Indian Railway Rolling Stock Code PDF
Document Details
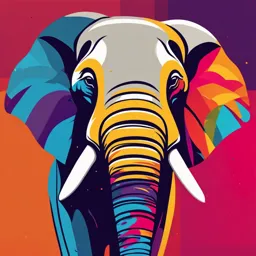
Uploaded by PatriElf
Indian Institute of Management Indore
2022
R.N.Singh
Tags
Summary
This document is the Indian Railway Rolling Stock Code, published in October 2022. It details the organization of rolling stock production and maintenance departments, including procedures for costing, employee duties, and materials management. The code covers various aspects of operations within the Indian Railway system.
Full Transcript
MINISTRY OF RAILWAYS (RAILWAY BOARD) INDIAN RAILWAY ROLLING STOCK CODE OCTOBER 2022 PREFACE The State Railway Code for the Mechanical Department was first published provisionally in March, 1940, and its first Reprint Edition was broug...
MINISTRY OF RAILWAYS (RAILWAY BOARD) INDIAN RAILWAY ROLLING STOCK CODE OCTOBER 2022 PREFACE The State Railway Code for the Mechanical Department was first published provisionally in March, 1940, and its first Reprint Edition was brought out in 1944. Subsequently, four editions were brought out in 1950, 1970, 1974 and 1991 as Indian Railway Code for the Mechanical Department (Workshops) incorporating correction Slips up to No. 7 of 2008. This code was further updated in 2016 with the introduction of new techniques and concepts in manufacturing and maintenance of rolling stocks, introduction of Group Incentive Scheme, Bio-metric Attendance System, Environment Management, Factory Act provisions, Enterprise Resource Planning, introduction of Information Technology etc. and renamed as “Indian Railway Rolling Stock Code". Now, this code has been further revised incorporating the inputs from IRIMEE and Railway officers on important issues like, linkage of Bio-metric attendance with wages, costing and incentive, domain consultancy by the workshops, implementation of Workshop Information System, Umbrella works for PH-41 and many more. This code supersedes all existing rules and orders issued by the railway board on the subject dealt within it. Unless any contrary intention is expressed or implied in the wording of the existing rules, the provisions of this code are mandatory and binding. For any deviation, the sanction of the‘ Railway Ministry should be obtained. Any errors or omissions, which may be found in this edition, may be brought to the notice of the undersigned. Equally welcome are comments and suggestions. ( R.N.Singh ) Secretary, Railway Board New Delhi Dated.10.2022 CHAPTER 1 Organization of Rolling Stock Production & Maintenance Department 101-Corporate Objectives 102-Mission Areas for Rolling Stock Vertical 103- Organisation 104-Railway Board and RDSO 105-Production Units 106-Zonal Railways 107-Rolling Stock Maintenance Organization in Zonal Railways: 108-Zonal Railway workshops 109-Chief Workshop Manager (CWM) 110-Chemist and Metallurgist 111-Workshop Personnel Officer 112- Environment and Safety Manager (EnSM) 113 Workshop Civil Engineer 114-Workshop Electrical Engineer 115 Dy. Chief Mechanical Engineer (Dy.CME) / Workshop Manager (WM) 116-Workshop Accounts Officer 117- Dy. Chief Material Manager (Dy.CMM)118-Production Engineer 119-Important duties of the Production Engineer 120-Production Engineer’s office 121-Planning and Production Control 122- Chief/Deputy Chief Mechanical Engineer (Information Technology)-CME/Dy.CME(IT)123-24 Workshop Security Officer (WSO) 123 (A) Workshop Health unit/Hospital 125-26-Workshop Supervisors 127 Duties of Supervisors 128-29- Categorisation of shops 130 Maintenance and Inspection of Boilers 131 Maintenance of weigh bridges and weighing scales 132 Classification of staff in Workshops 133-134-Staff strength 135- Agility 136-137-Open Line divisions 138-139-Customer orientation 140 Empowering Coach Maintenance & Disaster Management Wings 141- unitary Command and Control 142 - Acts relevant to Rolling Stock Production & Maintenance Department 143-Important Codes and Manuals of Indian Railways Annex 1.1-Mid life rehabilitation (MLR): Chapter 2 Production Units 201-General 202-03-Organization 204-05-Costing in Production Units of Indian Railways 206-07 - Process Costing System: 208 - Batch Costing System: 209 - Features of Batch Costing System: 210 - Batch size 211-Work Orders 212 - Cost Classification 213-14 - Materials 215 - Pairing of Issue Notes and Advice Note of Returned Stores 216 - Finished Parts Stores Depot: 217 - Component Costing: 218 - Assembly Costing 219 Collection of cost under Groups and Assemblies 220 Overheads 221- Allocation and Apportionment of Overheads 222-23 - Quarterly Review 224 - Job Costing 225 - Workshop General Register: 226 - Completion Certificate: 227-28 - Drawl Books 229 - Batch Cost Report: 230 - Transfer of Final Cost to Railway Board 231 - Cost Report to GM 232 - Managerial Statements 233 - Development Suspense 234 - Transfer Price 235 - Guidelines for Rolling stock manufacture by repair workshop CHAPTER 3 Employees' Duties and Responsibilities 301-Hours of Work 302-04-Working Hours 305-“Gate Attendance System” 306- Deliverables of a modern “Gate Attendance System” 307-Modernization of “Gate Attendance” system using smart card and biometrics 308-Biometric System of “Gate Attendance” 309-Time Office 310-Opening and closing of workshop gates 311-12-Late Attendance 313-Work during meal hour and on Sundays 314- Attendance of Supervisory Staff 315-Working Hours of Shop Clerks 316-318 Employee’s Biometric Identity Number (BIN) 319-Leaving shops during working hours 320-323 Duty Certificate 324-Night Shift 325-326 Overtime Requisition 327- Overtime Register 328-329 Overtime Allowance 330-331Material Gate Passes 332- 334-Muster Roll cum Labour Pay Sheet 335-Deductions for Absence 336-Chart of Labour Charges 337 Extract Pay Sheet 338- Inter-shop Transfers 339-Staff Register 340-Hours of work 341-Exemptions to limitation of hours of work 342-Remaining on duty 343-“Attendance in LCDs” 344-Modern Gate Attendance System for LCDs” 345-Disaster Management 346-Accident Relief & Medical Equipment Train 347- Accident Relief Trains 348-Breakdown staff 349-Accident checklist 350- Reprovisioning in ART/ARME Annexure3.1-Important procedure of hour of work and period of rest Rules-2005 CHAPTER 4 Administration's Duties and Responsibilities to workers 401-Introduction 402-Features of the Chittaranjan Scheme 403-Prerequisites for introduction of Incentive Scheme 404-Allowed Time 405-Timing of Operation 406- Time Study 407-Synthetic Times 408-Rating 409-Normalizing 410-Preparational Time (PT) 411-Extra Time 412-Job cards/Squad Cards 413-Out-turn 414- Simplification of time taken with computerised GA 415-Time Saved/Time Lost 416- Material scrap 417-Guaranteed Basic wages 418-Incentive Bonus Rates and Ceiling on profits in CLW Scheme 419-Abnormal Profits 420-Losses 421-Incentive Bonus to essential indirect workers and Junior Supervisors 422-Incentive Bonus to Senior Supervisors 423-Payment of incentive bonus 424-Incentive to staff in the service shops 425-Workers booked on Incentive and day work systems 426-Overtime working in Incentive sections 427-Idle time 428-Deduction from supervisors for idle time 429-Allocation of bonus 430-Extension/ Contraction Proposals 431-Capping on IW and EIW strength 432-Checking of Job Cards 433-Group Incentive scheme 434- Main Features 435-Special Management responsibility in incentive schemes 436- Training 437-Categories of Employees 438-Training of new comers 439-Multi-skilling 440-Designing of courses and employee involvement 441-Improving trainee Participation 442-Salary Payment Ann. 4.1-Managerial and Exception Statements to be generated by the system Ann. 4.2-Comparison between Chittaranjan and Group Incentive Scheme Ann 4.3 Administration responsibilities on industrial safety Ann 4.4 Administration responsibilities on Environment Management CHAPTER 5 Materials Management in Railway Workshops 501—Introduction 502--Sources from which Materials are obtained by shops and maintenance depots 503--Demands for materials to match with budget 504—Workshop Inventory Management - stock and non-stock items 505--Raw material norms 506-- Sub Stores 507-508--Pairing of Issue Notes 509--Provisional Adjustment of Issue Notes 510--Main Stores Sub-ledger 511--Adjustment of cost of stores received from depots 512-517--Stores Purchased Direct 518--Stores Sub-ledger for Credits 519-521--Stores Sub-ledger for Out-turn of Process shops 522-523--Stores Charges Write-back Order 524--Other Miscellaneous Charges 525--Miscellaneous stores sub ledger 526-530-- Summary sub ledger Annex. 5.1-5.3--Labour & Stores sub ledger Chapter 6 Costing in Workshops 601-Introduction 602-603-Costing in Workshops of Indian Railways 604-Job Costing System 605-Features of Job Costing System 606-607-Planning 608-Process Sheets 609-Revision of Control Work Order Series 610-Recoupment of Stock 611-Issue of Production Documents 612-Route Card 613-14-Work order System in Workshops 615-Prime Cost 616-Direct Labor 617-Direct Material/Stores 618-Accountal of Material cost for costing 619-Overheads/on costs 620-621-Shop & General On Costs 622-623-Quarterly Review of on-costs 624-628-Costing of POH of Rolling Stock 629- Reconciliation and merger of Costing records with financial records 630-Managerial Statements 631-Use of costing data Annex. 6.1-Revised Costing System CHAPTER 7 Execution of works in Workshops/PUs 701-Works undertaken in Workshops 702-03-Estimates 704-06-Estimates for Rolling Stock additions & workshop M&P Items for Workshops & Sheds 707-11-Estimates for Renewals and Replacements 712-713-Estimates of work for outside agencies 714-Charges for preparation of estimates 715-Interest Charges 716-Sanction for works to be executed in Workshops 717-Verification of Estimates 718-719-Certificate of Accounts Verification 720-Sanction to Estimates 721-Record of all Estimates 722- Currency of Sanction 723-725-Postal Vans 726-729 -Saloon carriages & other vehicle reserved for exclusive use of other deptt./Ministries 730 POH of Rolling Stock hired to/owned by defence deptt. 731 Loaning/Hiring charges for Rolling Stock loaned/hired to Outside parties and Government Departments 732-Loaning/hiring charges of the Rolling Stock 733-Hire charges for Plant & Machinery let out to Contractors 734-Sale of Heritage Rolling Stock 735-Sale of In-service MG rolling Stock 736-Methodology for sale 737-739-Execution of Works 740-Analysis of expenditure 741-742-Work-order system 743-Revenue Standing Work orders 744- Other Standing work orders 745-On-cost Work orders 746-Raw material stock work orders 747-Manufacturing work orders or Division work orders 748-Part, Group and repair work orders 749-751-Work order Register 752-Advice of Completion 753- Monthly Statement of completed work orders Compilation of the Workshop Manufacture Suspense Account 754-Work shop Manufacture Suspense Account 755-Workshop General Register 756-Check sheet 757-Calculation of On-cost Charges 758-767-Out-turn Statement 768-Workshop Deposit Schedule 769-770- Workshop Account Current 771-Workshop Manufacture Suspense Account Journal Entries 772-Up-to-date totaling of Workshop General Registers 773-Review of Workshop General Registers 774-Irregular booking of charges 775-Workshop Subsidiary Balance Register 776-Labour Book 777-Reconciliation with the General Books 778-780-Review of Balance under “Workshop Manufacture Suspense Account” 781-782-Completion Reports 783-785-Completion Report Register 786- Adjustment of charges and Credits reported on completed works 787 - Productivity Review Annexure 7.1 -Flow of data for WGR & WMS account current Chapter 8 Information Technology Workshop Information System (WISE) 0801-Introduction 0802-Workshop Information System (WISE) 0803-Brief Scope 0804-WISE Infrastructure 0805-Benefits Accrued 0806-Training 0807-System Security 0808- WISE 0809-Business Process Flow 810- Workshops covered under WISE 811- Integration with other Applications Annex. 8.1-WISE Architecture Annex. 8.2- Management Dashboard and Reporting for Workshops Annex. 8.3- List of Abbreviations used CHAPTER 9 QUALITY 901-Quality – Definition 902 - Quality & Process 903 - Quality Management Techniques: 904 - Quality Standards 905 - Origins of Defects 906 - Defective design 907 - Quality of Inputs 908 - Defective Workmanship 909 - Process Defects 910 - Management Commitment to Quality 911 - In process audit 912 - Inspection and quality of output 913 - Inspection and Measurement of Quality 914 - Inspection by 3rd Party 915 - Certification of Laboratories 916 - Quality enforcement of outsourced work 917 - Product Inspection 918 -Inspection Vs Process Control 919 - Quality enforcement through warranty obligation 920 - Accountability for Defects Annexure 9.1 Quality assurance in shops and maintenance depots CHAPTER 10 Investment Planning 1001-Planning: 1002-04-Goals for investments: 1005-06-Advance Planning for Rolling stock: 1007-Codal Life and Condemnation: 1008-Normal condemnation of Rolling stock: 1009-Underage condemnation: 1010-Overaged stock on line: 1011- Accident Damaged Rolling Stock: 1012-13-Officers authorized to condemn Rolling stock: 1014-Sale of Rolling Stock: 1015-Scope of the Rolling Stock Programme. 1016-Capital/Unit exchange spares 1017-Estimation of requirements - New acquisitions 1018-Itemized Rolling Stock Program (IRSP): 1019-Machinery and Plant (M&P) Program: 1020-Nomenclature of M&P and T&P: 1021-Codal Life of Machines: 1022-Creation of new assets: 1023-Replacement proposals: 1024-Utilization of Workshop Space and Layout considerations: 1025-Plan Head “41” 1026-Works in Progress (WIP) : 1027-Monetary Ceiling for Preliminary M & P Programme: 1028- Format and Presentation of Proposals: 1028(A) M&P proposals under umbrella work 1029-Budgeting for M&P: 1030-Review of M&Ps under procurement 1031-Category of M&Ps & agency for procurement 1032-Cost and time overruns: 1033-End-loaded expenditure booking: 1034-Budgetary Reviews: 1035-Machine maintenance and Annual Maintenance Contracts (AMCs) 1036-Disposal of condemned and surplus machines: 1037-Maintenance of asset Register: 1038-39-Proposals under Plan Head 42 1040-Standards for Maintenance Facilities 1041-Expansion Programs to meet capacity shortfalls: 1042-Checklist for proposals under Plan head 42: 1043- Head of allocation: 1044-Powers for sanction and compilation of Approved Works 1045-Work Register & Reconciliation 1046-Direction and General Charges. 1047- Cost and time overruns 1048-Maintenance of civil infrastructure in sheds and workshops:- Ann. 10.1-Rolling stock Programme- New Acquisitions Ann. 10.2-Codal life of machines CHAPTER 11 Capacity Optimization and Product Development 1101 - Background. 1102-Multi skilling tasking and Inter-shop transfers 1103- Outsourcing – need to outsource 1104-Outsourcing to units outside the workshops. 1105-06- Outsourcing or contracting for works within the Railway Premises. 1107- ERP based production Management 1108- RDSO’ s role in vendor approval and product inspections 1109-Innovation 1110-Strategies for innovation 1111-Utilization of surplus shop capacity 1112-Process of procuring outside orders. 1113- Profitability: 1114-Annual Maintenance Contracts for M&P 1115-General CHAPTER 1 Para No. Title (Ctl + Click on Para no.) 101 Corporate Objectives Organization of 102 103 Mission Areas for Rolling Stock Vertical Organisation Rolling Stock 104 Railway Board and RDSO 105 Production Units Production & 106 Zonal Railways Maintenance 107 Rolling Stock Maintenance Organization in Zonal Railways: Department 108 Zonal Railway workshops 109 Chief Workshop Manager (CWM) 110 Chemist and Metallurgist 111 Workshop Personnel Officer 112 Environment and Safety Manager (EnSM) 113 Workshop Civil Engineer 114 Workshop Electrical Engineer 115 Dy. Chief Mechanical Engineer (Dy.CME) / Workshop Manager (WM) 116 Workshop Accounts Officer 117 Dy. Chief Material Manager (Dy.CMM) 118 Production Engineer 119 Important duties of the Production Engineer 120 Production Engineer’s office 121 Planning and Production Control 122 Chief/Deputy Chief Mechanical Engineer (Information Technology)-CME/Dy.CME(IT) 123-24 Workshop Security Officer (WSO) 123 (A) Workshop Health unit/Hospital 125-26 Workshop Supervisors 127 Duties of Supervisors 128-29 Categorisation of shops 130 Maintenance and Inspection of Boilers 131 Maintenance of weigh bridges and weighing scales 132 Classification of staff in Workshops 133-134 Staff strength 135 Agility 136-137 Open Line divisions 138-139 Customer orientation 140 Empowering Coach Maintenance & Disaster Management Wings 141 unitary Command and Control 142 Acts relevant to Rolling Stock Production & Maintenance Department 143 Important Codes and Manuals of Indian Railways Annex Mid life rehabilitation (MLR): 1.1 101. Corporate Objectives: The corporate objectives of Indian Railways are: a. To provide rail transport for both passenger and goods adequate to meet demand in areas where Railway operation confers optimum benefit to the economy, having due regard to the Government's policy of development of backward areas; b. To provide such rail transport at the lowest cost consistent with i. requirements of the Railway users and safety operations, ii. adequate provision for replacement of assets and some provision for development of business and iii. the least amount of pollution of the environment ; c. To work in association with or utilize other modes of transportation, such as pipelines and road transport, and to engage in ancillary activities necessary to sub-serve the above two objectives ; d. To establish a corporate image of the Railways as being an up-to-date business Organization With the interest of the public and of the nation as its prime objectives ; and e. To develop organizationally effective personnel with pride in their work and faith in the management. (Para 219 of the Indian Railway Code for Administration and Finance) 102. Mission Areas for Rolling Stock Vertical Note: The term Rolling Stock means Coaches, Wagons, Locomotives, EMU, DEMU, Trainset, MEMU, Tower Cars, Power Car, SPART, ART, ARMV, other special purpose coaches & wagons and rolling stocks. Rolling Stock Vertical is primarily assigned with the responsibility for Design, Manufacture, deploy and maintain the Rolling Stock of Indian Railways. The mission areas for this activity are: a. Evolving optimal designs for Rolling Stock, choosing the most economical option on a “life cycle costing basis” b. Manufacture of the rolling stock at Production units or external Manufacturing Units to stringent standards in a cost effective manner c. Maintaining the moving assets ensuring that they give optimal operational efficiency and safety throughout their full codal life. d. Planning, procurement and maintenance of Machinery & Plant. e. Ensuring realization of the full potential of the assets. f. Adopting and maintaining the best practices in the industry with excellence in all areas of operation. g. Arranging relief and rescue in any unlikely event of Railway disasters. While pursuing the above mission, the orientation of Rolling Stock, Production/Maintenance Vertical should remain in complete consonance with Corporate Objectives of Indian Railways. 103. Organisation: The organizational structure of the Rolling Stock, production/maintenance Vertical is driven by the manufacture and maintenance philosophy of rolling assets and is shown in the chart below: Area of responsibility: - EDME(Chg.) – Responsible for all activities from design of new coaches to condemnation of coaching stock. - EDME(Frt.) – Responsible for all activities from design of new wagons to condemnation of freight stock. - PED(W&D) – Responsible for all activities of railway workshops and for development/ introduction of new/advanced/improved technologies in rolling stock. - EDME(EnHM & Projects) – Responsible for all activities of cleaning/house- keeping of passenger carrying rolling stock and is nodal officer on GCC services. In addition, EDME (EnHM&Proj.) is also responsible for execution of project work related to rolling stock. - CAO(COFMOW) – Responsible for all activities for procurement of M&P and other technological items for Zonal railways and PUs. - CAO(WPO) – Responsible for all activities for establishing new infrastructural establishment for Rolling Stock. While the manufacturing practices in the Workshops are shaped by the strategies that characterize the internationally acclaimed World class industries, the maintenance philosophy balances between the two extremes of – a. Corrective maintenance: running the assets non-stop and attend only when they break down- thus enhancing availability at the cost of reliability. b. Preventive maintenance: withdrawing from traffic for frequent and prolonged maintenance attention, enhancing reliability at the cost of availability. Choosing a mid course between the two, Indian Railways contain the ineffective hours within the stipulated targets by restricting frequency and duration of preventive maintenance schedules. Emerging technologies with fit and forget components, enhanced quality conscience and principles of predictive maintenance further help in reducing the quantum of preventive maintenance with higher and higher levels of availability. Activities Function of Evolve specifications and designs a. of the rolling stock and choosing Railway Board and RDSO the most economical option on a “life cycle costing basis”. b. Manufacture Production Units, Zonal Railway Workshops and external manufacturers Periodical major overhauls and c. mid life rebuilds (MLRs) (see Zonal Railway Workshops and MLR shops annexure 1.1) Locomotive sheds, Distributed Power Top overhauls and minor Rolling stock (DPRS) Shed and the d. schedules, Intermediate and carriage, EMU, MEMU,Train set and routine overhauls Wagon depots Locomotive sheds, Distributed Power Rolling stock (DPRS) Shed and the Cleaning, topping up supplies, e. carriage and Wagon, EMU, MEMU, Train yard or pit line examination set depots, fuel pads and outstation attention depots. 104. Railway Board and RDSO: Complete rolling stock vertical reports to MTRS. AMs - ME, PU, Traction & RS report to him. Various directorates in Railway Board in charge for specific areas of rolling stock Workshops & Development functions, not only stipulate the philosophy for manufacture and maintenance, but also keep a close watch on the performance of the Railways. The motive power, PS & EMU, Carriage, wagon and testing directorates in the RDSO act as the depository of all technical knowledge in their respective domains and issue technical directives to the Production Units and zonal Railways, balancing between maintainability and ease of manufacturing. 105. Production Units: Production units are headed by General Managers/Chief Administrative Officers (CAO) assisted by Heads of Departments in Mechanical, Electrical, Accounts, Engineering, Security, Stores and Personnel Departments at appropriate level. Since design and quality are very important, there shall also be Chief Design Engineers. Other broad organizational set up of Workshops as discussed in Paragraphs 108 to 133 below will apply mutatis-mutandis, to Production Units. 106. Zonal Railways: The General Manager of Zonal Railway is the head of the administration and the organization. In discharge of his duties he is, assisted by a number of Principal Officers who are departmental heads of their respective departments. 107. Rolling Stock Maintenance Organization in Zonal Railways: The Principal Chief Mechanical Engineer (PCME) is the Principal Head of the Mechanical Department reporting directly to the General Manager. His important function is maintenance of the rolling stock and other mechanical equipment of the Railway in good repair, as on this depends the safety and reliability of railway transportation to a very large extent. To enable him to carry out this duty, Rolling Stock Vertical of the Railways have within their control one or more workshops, in which Rolling Stock are periodically examined, repaired and overhauled before being placed back on the line. Day to day maintenance of the rolling stock is done in sheds for various Rolling stock Locomotive Sheds, Distributed Power Rolling stock (DPRS) Shed, Coaching Depots, freight depots or other outstation maintenance points, all forming part of the divisional set up. The PCMEs assisted by heads of departments as shown below: a. Chief Workshop Engineer (CWE): The direct control on the affairs of the workshops in the Zonal Railway is exercised by the "Chief Workshop Engineer" who is the administrative head of the department for workshops and responsible for total planning of workshops including coordination with stores department for all workshop matters. In all matters relating to policy formulation which concerns workshops in general and the Rolling Stock Vertical in particular, the CWE issues instructions in consultation with the PCME, who is the Principal Head of the Vertical. Responsibility for budgetary controls in the workshop rests with the CWE. b. Chief Rolling Stock Engineers/Coaching (CRSE/Chg.) – CRSEs/Chg. exercises technical control over the coaching depots and other coaching activities in yards/ outstations CRSEs/Chg. will ensure that: i. Availability and reliability of the coaching stock are above the levels fixed by Board from time to time. ii. MLR, POH and other preventive maintenance schedules on the coaching stock including EMU/MEMU/ Train-sets are carried out in time and to the prescribed quality. iii. Ready availability of spare parts and supplies for coaching stock in coaching depots and outstation depots. iv. Rake links are made to maximize utilization without jeopardizing maintenance and safety. v. Cadre management for maintenance staff including timely recruitment and training. c. Chief Rolling Stock Engineers/Freight (CRSE/Frt) – CRSE/Frt exercises technical control over the freight depots and other freight activities in yards and outstations. CRSE/Frt will ensure that: i. Availability and reliability of the freight stock are above the levels fixed by Board from time to time. ii. POH, ROH and other preventive maintenance schedules on the freight stock are carried out in time and to the prescribed quality. iii. Ready availability of spare parts and supplies for freight stock in freight depots and outstation depots iv.To ensure maximum utilization of freight stock without jeopardizing maintenance and safety. v. Cadre management for maintenance staff including timely recruitment and training. d. Chief Electrical Service Engineers (CESE) – CESE exercises technical control on the department of electrical general service including passenger reservation system. CESE will ensure that: i. Availability and reliability of Train lighting and Air conditioning in coaches. ii. Planning, maintenance and periodic overhauling of Train lighting and Air conditioning in coaches. iii. Maintain liaison with division and state electricity board for uninterrupted power supply. iv. Ensure electrical power supply to railway residential, service building, stations and passenger amenities items. i. He also assists PCEE for overall works of general services. e. Chief Electrical Engineers/Rolling Stock (CEE/RS) – CEE/RS exercises technical control on the maintenance and operation of EMU/MEMU. CEE/RS will ensure that: i. Availability and reliability of the EMU/MEMU stock are above the levels fixed by Board from time to time. ii. Monitoring material availability, RSP items and procurement of stock items for EMU/MEMU. iii. All planning works and coordination with workshop for EMU/MEMU POH. iv. Cadre management for maintenance staff including timely recruitment and training. i. f. Chief Mechanical Engineer (Planning) – The CME (Planning) assists the PCME in all matters pertaining to Investment Planning i.e. requirements of Rolling Stock, Machinery and Plant and infrastructure creation under Works Program CME(Planning) will be the nodal officer for execution of all works under PH21, PH41 & PH42 of Demand No 16 and the planning process is elaborated in Chapter 11. g. Chief Motive Power Engineer/ Diesel & R (CMPE/D&R) – CMPE/D&R will assist PCME in management of ARMEs/ ARTs/ SPART and 140 T Cranes and other items of Disaster management. h. Chief Environment & House Keeping Manager (CEnHM) – CEnHM will be responsible for the following: i. All activity related to environmental and housekeeping management. ii. Monitoring of EnHM activities of stations, depot, colony etc. iii. NGT works and compliance iv. Monitoring of waste Management, ETP, CTS, OBHS etc., over Zonal Railways. These HODs are assisted by Dy.CMEs, EMEs/SMEs & AMEs in Headquarters. Note: In addition to above, additional designations can be assigned by PCMEs to additional posts like CME(EnHM), CME(IT), CTO, CAO(Project) etc. 108. Zonal Railway Workshops The Zonal Railway may have one or more workshop for repair and periodic overhauling of Rolling stocks based on the requirements and constraints of location. In the same workshop, repair and maintenance of different types of rolling stock and locomotives can be taken up. In addition to the repairs and reconditioning of rolling stocks and of plant and machinery, and manufacture of the spare parts for the repair thereof, these workshops may carry out work of the nature shown below: — a. Construction and assembly of - i. Locomotives. ii. Coaching Vehicles, iii. Goods Vehicles. iv. Distributed Power Rolling stock (DPRS) b. Manufacture of articles required by other departments of the Railways. c. Manufacture or repair of rolling stock (conventional as well as DPRS) or components for— i. Other Government Department. ii. Other zonal Railways/Production units, iii. Others. Any other activity, as specified by the PCME. 109. Chief Workshop Manager (CWM) The Chief Workshop Manager is posted as the officer in charge of the workshop. All the officers posted in the workshop will be under his direct administrative control analogous to that Divisional Railway Managers. CWMs (in SAG) of Workshop are given Financial as well as Administrative power at par with DRMs in Open line so far as areas within the Jurisdiction of CWM are concerned. 110. Chemist and Metallurgist In one or more of its workshops, each Railway zone shall have a specialized Central Material Technology (CMT) Laboratory with expertise on the following aspects: a. Testing and quality control (TQC): Testing chemical, physical, and mechanical properties of materials. The TQC should have adequate infrastructure such as metrology, hardness testers, organic and inorganic lab, testing of oils and fuels, optical microscope with image analyzer, UTM etc b. Technical investigations including failure analysis (TIFA): Expertise in fracture metallurgy and tribology; ability to differentiate between service and process failures and suggest preventive measures. c. Non destructive testing (NDT): To undertake testing and certification- keep abreast of NDT technologies and maintain documentation. d. New materials technology (NMT): Develop facilities and knowledge to test the new materials such as polymers, composites, ceramics, additives, amorphous metals, insulating materials, etc. and to help the shed or shop exploit their special qualities to upgrade the materials and processes. The officers (Chemists and Metallurgists) working in these specialized laboratories in Workshops and those working in the running sheds and depots aid in quality control in manufacturing and maintenance, involving special knowledge of modern chemical and metallurgical techniques. They will also help in failure analyses. The Chemist and Metallurgist who is in overall command of the Laboratory will report to the CWM or the officer in charge of the shed or depot, as the case may be. 111. Workshop Personnel Officer The open line workshops have an establishment branch under a Personnel Officer (at an appropriate level decided by the Principal Chief Personnel Officer) working under the direct control of Chief Workshop Manager in matters of day to day working, but taking policy directives from Principal Chief Personnel Officer of the Railway. One of his main duties is to attend to all affairs regarding staff and workshop labour. He is responsible to the workshop for all matters relating to establishment such as recruitment, payment of wages and overtime, grant of leave and passes, complaints, discharges, payment of provident fund, gratuity and compensation, maintenance of service registers and other such records. Staff welfare activities like canteen, management of railway quarters, railway schools, supports & cultural activities are also handled by him. 112. Environment and Safety Manager (EnSM) In 1986, the parliament enacted the Environment Protection Act. (EP Act.) for protection and improvement of environment, which includes water, air and land and also the inter relationship that exists among and between water, air and land and human beings, other living creatures, plants, micro-organism and property. Provision of safety officers in Workshops has been separately mandated in the Factories Act. Creating a work place safe not just for the employees, but the entire neighborhood in an environmentally responsible manner is a specialized activity of the Environment and Safety Manager (EnSM). The EnSM should be fully conversant with these Acts: The water- Prevention and Control of pollution Act 1974 The Air- Prevention and control of pollution Act 1981 The Environment (Protection) Act. 1986 The Hazardous Waste (Management, Handling and Trans Boundary Movement) Rules 2008 Factories Act,1948 Municipal Solid Waste (Management and Handling) Rules 2000. (These acts are reckoned in EMS 14001 and OSHAS 18001) The responsibilities of the Environment & Safety Managers (EnSM) inter alia, are listed in Annexure 5.3 & 5.4 as Administration’s duties & Responsibilities to workers. He will report to the Chief Workshop Manager and will oversee/inspect/control the activities of various departments on the subjects of environment protection & industrial safety. Industrial safety and adherence to the legislations like pollution act, factory act etc and assisting the CWM in his duties as the factory occupier are his functions. Based on the strength of staff, required number of safety officers to work under ENSM will be provided. For environment protection and industrial safety, a similar but smaller and lower level organization can be provided in bigger open line establishments like Loco sheds/Coaching Depots (conventional as well as DPRS) , as the impact of these subjects will be going up in the years to come. 113. Workshop Civil Engineer Each workshop shall have an exclusive civil engineering department headed by an appropriate level officer, to ensure construction and maintenance of various fixed assets of the Workshops like sheds, buildings, roads, permanent way, pillars and gantries, toilets & washrooms, drainage & water supply systems and other civil infrastructure He shall work under the administrative control of CWM & technical control of PCE. The Civil Engineer shall be suitably empowered to finalize tenders also. A separate budget shall be provided for Civil engineering maintenance of workshops. 114. Workshop Electrical Engineer Electrical Engineers in Workshops work under administrative control of Chief Workshop Manager. They are under the technical control of the Principal Chief Mechanical Engineer. Apart from rolling stock related maintenance, duties of Electrical Engineers include supply and distribution of electrical energy, the maintenance of electrical plants and machinery in the workshop. 115. Dy. Chief Mechanical Engineer (Dy.CME) / Workshop Manager (WM) For workshops exclusively/largely meant for repair and rehabilitation of rolling stock, Dy.CME/WM is (are) posted under the administrative control of Chief Workshop Manager and technical control of Principal Chief Mechanical Engineer. The Dy.CME/WM is in charge of mechanical repairs of rolling stock and other typical mechanical engineering functions. 116. Workshop Accounts Officer The workshops have an accounts and finance branch under an Accounts Officer at an appropriate level decided by the Principal Financial Adviser (PFA) and. Workshop Accounts Officer is under the direct control of Chief Workshop Manager in matters of day to day working. He is in charge of all the costing and accounting of the workshops and is the Financial Adviser to the Head of the Workshops and is responsible for rendering him all the assistance and cooperation related to Finance function that may be required by the later. He may take policy & professional directives from PFA. 117. Dy. Chief Material Manager (Dy.CMM) The workshops have a stores branch under a Dy. Chief Material Manager (Dy.CMM). He is responsible for the custody, replenishment and distribution of workshop stores. The Officer is under the direct control of Chief Workshop Manager in matters of day to day working and his exclusive charge will be supply management of the workshop in the most efficient manner possible and to maintain all records for the correct and prompt procurement/accountal of all stores/stores transactions. He may take policy directives from the PCMM. 118. Production Engineer (PE) PE reports to CWM and is responsible for the work of the following sections: a. Drawing office — Design b. Drawing office — Plant c. Drawing office — Jigs and Tools d. Planning and rate fixing e. Progress office f. Tool Room g. Inspection For those workshops, which are under Group Incentive Scheme, PE reports to CWM and is responsible for the work of Industrial Engineering Department having the following sections: a. Drawing b. Tender section c. General Section d. Electronic Data Processing center /Computer center e. ISO cell f. Material Control Cell g. Customer Service Cell h. Incentive cell i. Planning j. Budget Cell k. M&P cell l. RSP cell 119. Important duties of the Production Engineer a. Plan and ensure most economical and the best method of Production and the most economical use of machines; b. Determine the standard time for each operation by following the analytical method of fixing rates; and c. Design machines and tools to suit the needs of works passing through the shops. d. Conduct work study whenever changes in work is necessary on account of introduction of new rolling stock, changes in schedule maintenance works, introduction of new machineries/higher productivity machineries, introduction of new method of works etc in group incentive workshops. 120. Production Engineer’s office a. Prepares design drawings and specifications for new standard parts and for the necessary jigs and tools; b. Prescribes the nature and sequence of operations to be performed: c. Inspects all manufactured parts: and d. On completion of any series of operations, compares the times actually taken with those originally estimated by it, investigates all important differences and reports as to the causes thereof and remedies therefore. 121. Planning and Production Control The efficiency of a Railway Workshop or a Production Unit is largely dependent on an efficient planning and production control organization. The broad functions of this department comprise of: a. Pre-planning: Study of drawings and specifications, preparation of cost and details Books for each component; drawing up of lists of raw material or component requirements for ensuring its availability; maintenance of data for installed capacity; booked load; spare capacity, etc. for each machine group etc. b. Drawing office: Scrutiny of drawings received; preparation of part drawings to facilitate manufacturing operations, designing various jigs and fixtures, templates, gauges, etc. for economical manufacture of components; maintenance of drawings for standard cutting tools etc., placing manufacturing orders on Tool Room, when required, etc. c. Planning: This office plans the activities connected with production to ensure fullest use of the plant and other means of production; It makes all arrangements to work as smoothly and efficiently as possible. The functions of this office are broadly divided as under: i. Processing: The functions include preparation of scroll process sheets indicating sequence of operation, quantity of material to be used, the section or load centre where the operation is to be carried out, the requirement of machine groups, jigs, fixture and gauges, etc. ii. Rate fixing: The functions include maintenance of synthetic data for fixing rates (time) for individual operation, indicating allowed time in the process sheet for each of the operation involved; to scrutinize all completed piece work cards, issue of excess time cards etc. iii. Efficiency: This section deals with matters of general efficiency of the shops. Its activities comprise of review of existing practices, suggest improvement, keeping constant watch on off cuts and rejected materials lying on the shop floor or stores scrap yard in order to suggest suitable usage of that materials etc. e. Production control: Release of work orders for components assemblies etc. well in advance of the schedule of production; preparation of production schedule and distribution thereof in advance to all concerned for their guidance, arranging with stores departments for reservation of required material before actual release of work orders etc. f. Progress office: This office keeps constant watch of Production of components, assemblies, erection etc. as per schedules laid down, preparation of monthly report of production and their deliveries, keeping liaison with shops and stores departments in the drawal of raw material and finished parts. Intersection and inter-shop movement of components; maintenance of records for number of orders received, orders completed for each batch etc. g. Inspection: To inspect components, assemblies etc. on completion of each operation to ensure conformity to drawings and specifications, bringing to the notice of concerned authorities of deviation from drawings; and specifications for rectification and rejection; certification on the job card, and Route cards regarding quantities passed or rejected in respect of each operation etc. Inspectors are also deployed where ever required in checking materials or assemblies received from suppliers, for conformity to drawings and specifications. 122. Chief/Deputy Chief Mechanical Engineer (Information Technology)- CME/Dy.CME(IT) With the introduction of Information Technology (IT) in workshops, each workshop shall have a CME/Dy.CME(IT) for Enterprise Applications and Industrial Automation (EA&IA) with a CORE team for implementation, change management and user support as a part of the production control organization in the workshops and PUs. Production Units to have CME/Dy.CME(IT) under administrative control of PCME. Cadre of data entry operators for handling various IT applications like WISE, UDM, IMMIS, IREPS etc. will be under IT Manager in PUs/ Workshops. CME/Dy.CME(IT) will support Production Engineer in the rolling out of IT module. 123. Workshop Security Officer (WSO) Each workshop shall have a security officer from the Railway Protection Force (RPF) at an appropriate level, as decided by the Principal Chief Security Commandant of the Railway; He will work under the direct control of Chief Workshop Manager in matters of day to day working, taking policy directives from the Principal Chief Security Commandant. 123 (A). Workshop Health unit/Hospital Each workshop shall have a health unit/hospital depending upon staff strength. Adequate number of doctors at an appropriate level and para medical staff shall be posted, as decided by the Principal Chief medical director of the Railway; health unit/hospital will work under the direct control of Chief Workshop Manager in matters of day to day working, taking policy directives from the Principal Chief medical director. 124. As an officer entrusted with the Industrial security, the WSO is expected to a. Protect the railway premises and to safeguard railway property; ensure that the shop gates are kept under continuous watch, perimeter walls are robust and properly lit in the nights and adequately patrolled and the shops are free from thefts b. Gather crime intelligence and take security arrangements to protect Railway Property so as to insure that shops remain sterilized and impervious to terrorists and thieves at all times; and free from intrusion by unauthorized persons, especially those with criminal intents or mala-fide intentions of theft of technology secrets. c. Put in a system of screening and recording of all incoming and outgoing vehicles and materials d. Equip the CWMs with intelligence reports, in real time, on emerging labour problems with a potential to manifest into works stoppages or disruptions and to assist the shop administration during strikes and lockouts. e. Provide assistance to the shop officers particularly in conducting auctions or in matters pertaining to law and order by liaising with the local police officers, etc. 124a. The identified locations of workshop have to be covered under CCTV. 125. Workshop Supervisors Along with officers as listed above, supervisors are posted in different grades. Each workshop is sub-divided into 'Shops' and sub-divisions and is supervised by Senior Section engineers (SSEs) and Junior engineers (JEs). Supervisors are technically qualified “Shop Floor Managers” acting as an interface between management and the workmen. 126. Assisted by the other supervisors and clerks, the senior most supervisor of a shop (generally an SSE) exercises overall command of the affairs of the shop. He ensures that his shop remains current in paperwork and achieves the desired outturn and quality. SSEs have a special responsibility to instill discipline and resolve conflicts; and hence they have to remain neutral and unbiased and equidistant from the staff unions/Associations. 127. Duties of Supervisors The shop supervisors have a definite function in enforcing/ overseeing/ supervising the under-mentioned aspects: a. Allocation of work and deployment of Staff & supervisors b. Verification of timely and proper opening and closing of job cards c. Enforcing quality through Supervision of work and stage inspections d. Ensuring availability of tools and materials & Material handling / housekeeping equipment. e. Ensure economy in use of raw materials. f. Ensure punctuality in attendance, discipline and also presence of workers at the work spot during duty hours. Supervise the electronic staff attendance punching, discipline and also presence of workers at the work spot during duty hours. g. Ensure supply of safety kits to workers and ensure adherence to safety regulations and safe work practices. h. Ensure timely completion of work as per target set by the management. i. Ensure proper up-keep and safety of Railway’s assets - both immovable and movable. j. Ensure cleanliness of work premises and ensure good house-keeping by eliminating trash, filth, and foreign matters creating a cleaner workplace. Inculcate cleaning as a form of inspection and establish a clean-up time every day. k. Ensure correct handling of material so that damage does not occur due to mishandling. l. Inculcate and maintain proper work culture amongst staff. m. Design and establish an efficient and neat layout so that one can always get just as much of what is needed and whenever needed. n. Design of workstations: Design an efficient layout and ensure proper storage of tools, jigs and fixtures, raw materials, spare parts and semi- finished and finished work; and to put things in order (or organize them) according to a specific rule or principle. o. Ergonomics: To optimize tasks and workstations form the point of view of common place postures and movements such as sitting, standing, lifting, pulling and pushing with least stress on ligaments, joints and muscles of the workmen; and modify them as needed with change of activity or workmen with different anthropometric background. p. Environment: To create a conducive work environment free from avoidable heat, noise, pollution, vibrations and lack of illumination. q. Ensure staff safety. r. Issue of gate pass as per shop requirement. s. Ensure staff welfare including sanction of leave, issue of privilege pass/PTO etc t. Conduct market survey, initiate procurement of non-stock materials as per requirement, issue of technical suitability and rate reasonability. u. Monitoring of availability of materials for day-today maintenance works. Responsible for implementation of instructions and regulations issued by his superior officers. 128. Categorization of Shops The Zonal Railway workshops have Process Shops (i.e. Manufacturing Shops) and Job Shops (i.e. Repair shops). Amongst the Process Shops are the foundries, Forge & Smithy, welding, fabrication shops etc. All the other shops are job shops. Each shop should be allotted a shop number by which it can be distinguished. Certain "Shops" may be sub-divided usefully into "sections" or sub- divisions and this should be done wherever possible. 129. The 'Shop' or 'Section' of a shop is the unit not only for purposes of technical control, but also for those of financial and cost control. The number of jobs in progress at any one point of time in any such compact unit is comparatively small and the margin of error in booking to each job the correct time and materials spent on it as low as practical. Any method of distributing overhead expenditure (on cost) attributable to such an unit amongst the jobs undertaken would give more reliable results than what would be the case if the distribution were made, either taking the workshop as a whole or as divided up into a few large units. 130. Maintenance and inspection of boilers Boilers are maintained in accordance with the relevant provisions in the Factories act of the concerned State as well as Indian Boiler Act. PCME of each zonal railways becomes the Chief Boiler Inspector of Indian Railways, bestowed with the authority for inspection of in use/new boilers. An inspectorial organization with required number of inspectors is made available in certain workshops with earmarked Railway jurisdiction to perform the duties of inspection and certification of Boilers in use in various Railway units. These inspectors are specially trained and may be working as a part of the Mechanical millwright/M&P maintenance organizations of such workshops. The authority of PCME as Chief Boiler Inspector will be exercised by an officer of not less than senior scale level, who is also in charge of M&P maintenance activities in such workshops. With steam locos having been removed from service in most of the Railways, the expertise for maintenance of boilers need to be sustained as a special skill/trade by exclusive training of selected supervisors & staff. A Headquarter organization of Chief Boiler Inspector should also be available functioning under the workshop organization of HQs reporting to CWE. He will oversee the functioning of Boiler maintenance organizations of workshops. He will invoke the powers of PCME as Chief Boiler Inspector to serve notices for non compliance based on the stipulated acts on maintenance of Boilers. 131. Maintenance of Weigh Bridges & Weighing Scales Weigh Bridges & Weighing Scales which are in commercial use in various Railway units have to be maintained in accordance with the relevant Acts on ‘Weights& Measures’, currently in vogue. In many Railways, Rolling Stock Vertical is given the responsibility for maintenance and certification of these Weigh Bridges & Weighing Scales. M&P maintenance organization of Railway Workshops are generally charged with this responsibility, either through their in-house expertise or through certified outside agencies. In some Zonal Railways, this responsibility is given to the Divisional Rolling Stock Vertical. 132. Classification of staff in Workshops The staff employed in Railway workshops, other than Ministerial staff, may be classified under the following broad categories: (i) Helper (ii) Technician. Gr III (iii) Technician Gr. II (iv) Technician Gr. I (v) Senior Technician (vi) Junior Engineer (JE) (vii) Senior Section Engineer(SSE) 133. Staff strength Maximum number of staff in each grade that may be employed on a shop, under normal conditions should be fixed by the General Manager. Any variation in the number so fixed will require appropriate sanction. Note: If the existing number of staff is in excess of the normal strength so fixed, vacancies shall not be filled up until the strength fixed for the workshop is reached. 134. Within the staff strength limits prescribed by the General Manager or any lower authority empowered to do so, the detailed distribution of staff under each trade category will be made by the CWM. This will be the sanctioned strength of each shop. The CWM should communicate to the Workshop Accounts Officer any variations made in the strength so fixed. 135. Agility The annual orders of rolling stock (conventional as well as DPRS) (both numbers and variety) placed on the Production Units is driven by the emerging traffic needs, and shall not be constrained or expanded to match the production capacity. Likewise POH workload on the workshops, number and types of locos or coaches based in sheds and depots will be customer driven and not capacity driven. In order to meet such fluctuations, Production units, workshops or sheds, must be agile like world class organizations i.e. capable of “quickly” adjusting to changing workload (such as product mix or product volumes) and thrive under conditions of constant and unpredictable change. Such agility is consciously built in by: a. Incorporating flexible production systems and creating flexible structures, b. Creating a strong base of multi skilled staff, cross trained to handle a variety of jobs. It shall be the endeavor of the Chief Workshop Managers to get every skilled artisan trained in more than one trade. After the employee passes the prescribed training course for the new skill, the same will be entered in the personal database of the employee. c. Instant mobility of staff between sections, made smooth and seam-less, without establishment hurdles or delays d. As the volume of work decreases or increases necessitating contraction or expansion of staff strength, fixing numbers in each shop with reference to the minimum requirements of the shop, making temporary additions for a limited period. Fall back plans to quickly outsource critical items of work when the demand exceeds capacity. 136. Open Line divisions Rolling Stock (both conventional as well as DPRS), on being inducted on line are allotted to loco sheds, Distributed Power Rolling stock (DPRS) Sheds, coaching, EMU, MEMU, Train set or freight car depots in open line divisions. Thereafter, the Home sheds or depots look after these assets during their entire codal life and keep them operational by- a. Ensuring availability of spares and supplies (fuel, sand water etc) for locomotives, Distributed Power Rolling stock (DPRS) and coaches. b. Undertaking preventive maintenance of locomotives, Distributed Power Rolling stock (DPRS) and ensuring their outage and deployment c. Maintenance of carriages, wagons and other items of rolling stock (both conventional as well as DPRS) keeping the ineffective stock to the minimum d. Safety examinations and unscheduled attention as necessary arising on line and at satellite sheds and outstation depots e. Timely withdrawal from traffic and dispatching to nominated workshops for Periodical Overhaul and Mid life rehabilitation to MLR shops f. Planning facilities for induction of additional assets or new trains 137. In addition, open line divisions have the following important functions: a. To ensure that punctuality of trains remains unaffected by defects in the rolling stock (both conventional as well as DPRS) or Locos b. Maintenance of crew booking points c. Proper maintenance of running rooms d. Ensuring coordinated disaster management and maintenance of rolling stock, (conventional as well as DPRS) and equipments needed for deployment in disasters e. Ensuring effective manpower planning f. Ensuring training of staff. g. Ensure passenger amenities in trains like proper cleaning, provision of good quality linen, pest control, watering etc., 138. Customer orientation Generally speaking, Passengers spend more time in coaches than in terminals. The need for making customer friendly coaches with all amenities cannot therefore be overstated. Likewise, freight once loaded has to reach destination without damages and en-route detachments. RDSO, PUs and the zonal workshops contribute greatly in this effort, but it is the Divisions that act as a window to the customer and it is their performance that ultimately decides customer satisfaction. 139. Some of the instances that provoke customer complaints are: a. Introduction of new or special trains without creation of supporting manpower and infrastructure, b. Failure of Coach or linen cleaning and watering contracts coupled without any separable departmental staff to take over, c. Failure of watering systems, d. Theft of amenity fittings and damages by miscreants etc., 140. Empowering Coach Maintenance & Disaster Management Wings In an environment of inelasticity in creation of posts (and placing in position skilled persons at short notice) it is necessary that the officers in the open line heading coaching depots/Operation (Running) are given adequate special powers for the following: a. Fall back options while designing cleaning and watering contracts in connection with maintenance/servicing of rolling stock b. Hiring of mobile crane, welders, bulldozers etc across the counter at accident sites. c. Execution of Composite contracts for Passenger amenity works Such empowerment has been recommended by Railway Safety Review Committee (RSRC) also. Schedule of Powers in Zonal Railways should have necessary provisions for empowering the field officers on the above. 141. Unitary Command and Control The unitary command & control of different wings/departments of loco sheds & mega coaching depots must function in manner similar to the practice in workshops as outlined in para 109. 142. Acts relevant to Rolling Stock Production & Maintenance Department Officers and staff of the Rolling Stock Vertical must be familiar with the following Acts which have a bearing on their day to day functioning. a. Factories Act b. Industrial Disputes Act c. Workmen's Compensation Act, 1923 d. The water - Prevention and Control of pollution Act 1974 e. The Air – Prevention and control of pollution Act 1981 f. The environment (Protection) Act , 1986 g. The hazardous waste (management, handling and trans boundary movement) Rules 2008 h. Municipal solid waste (Management and Handling) Rules 2000. i. Indian Boiler Act j. Weights and Measures Act k. The Electricity Act 2003, etc. Copy of Bare Acts can be downloaded from Government of India website ‘www.indiacode.nic.in’ 143. Important Codes and Manuals of Indian Railways Officers and senior supervisors of Rolling Stock vertical must also be conversant with the salient provisions in the following Manuals and Codes and abide by them in discharge of their duties: Annexure 1.1 Mid Life Rehabilitation (MLR): Except for the mainframe and superstructure of a Locomotive or rolling stock, rest of the components gets invariably renewed or repaired during Periodical overhauls (POHs) in workshops. Thus only the physical life of frame and structure has been central to decisions on codal life of the Locomotives or rolling stock, which once inducted, therefore stay for long years in service (25 to 40 years). But the technology moves on and today’s equipments come with many superior and cost effective features than that of yesteryears. Stand alone equipments are renewed piecemeal, whenever the renewal is warranted; however systems such as engine, propulsion or brake circuits, flooring and upholstery, wagon bodies etc are renewed en-block in line with latest technology in the middle of the codal life. Using this opportunity, the locomotive or rolling stock is also modernized, while getting a new lease of life. The Mid Life Rehabilitations are carried out either in exclusive MLR shops or in nominated Railway Workshops as decided by Board. Chapter 2 Para No. Title (Ctl + Click on Para no.) 201 General Production Units 202-03 Organization 204-05 Costing in Production Units of Indian Railways 206-07 Process Costing System: 208 Batch Costing System: 209 Features of Batch Costing System: 210 Batch size 211 Work Orders 212 Cost Classification 213-14 Materials 215 Pairing of Issue Notes and Advice Note of Returned Stores 216 Finished Parts Stores Depot: 217 Component Costing: 218 Assembly Costing 219 Collection of cost under Groups and Assemblies 220 Overheads 221 Allocation and Apportionment of Overheads 222-23 Quarterly Review 224 Job Costing 225 Workshop General Register: 226 Completion Certificate: 227-28 Drawl Books 229 Batch Cost Report: 230 Transfer of Final Cost to Railway Board 231 Cost Report to GM 232 Managerial Statements 233 Development Suspense 234 Transfer Price 235 Guidelines for Rolling stock manufacture by repair workshop 201. General To attain self-sufficiency for Rolling Stock and other components meant for Indian Railways from within the internal resources of the country, Railway Production Units have been set up at different parts of the country which are functioning as independent units under the control of the Railway Board. These are: a. Chittaranjan Locomotive Works at Chittaranjan for manufacture of various types of electric locomotives. b. Diesel Locomotive Works at Varanasi for manufacture of various types of Diesel Locomotives, Diesel engines, standby Generating sets and their spares. c. Integral Coach Factory at Perambur for manufacturing of coaching stocks of various types and their spares. d. Rail Wheel Factory at Yelahanka for manufacture of various types of wheels, axles and wheel sets. e. Rail Coach Factory at Kapurthala for manufacture of coaching stocks of various types and their spares. f. Diesel Modernization Works, Patiala for midterm rehabilitation and modernization of Diesel Locomotives and manufacture of critical spares. g. Rail Wheel Plant, Bela Distt Saran (Bihar) for manufacture of Wheeel. h. Modern Coach factory, Lalgang, Raebareli (UP) for manufacture of coaching stocks of various types and their spares. In addition to the above Indian Railways are in the process of adding new Production Units and Wheel and Wagon Manufacturing facilities at various locations. 202. Organization All the production units will be headed by General Managers/Chief Administrative Officers who will be assisted by Heads of Departments in Mechanical, Electrical, Accounts, Engineering, Stores and Personnel Departments at appropriate level. Since design and quality are very important, there shall also be Chief Design Engineers. Other broad organizational set up of Work-shops as discussed in Chapter I of this Code will also apply mutatis-mutandis, to these production units. 203. The contents of all the other Chapters of this code are also applicable mutatis mutandis in Production Units. The contents of this chapter will also apply to workshops in open line engaged in manufacture of rolling stock, only for that activity alone. Some guidelines for these workshops have been laid down in para 335. 204. Costing in Production Units of Indian Railways The basic purpose of costing in Railway production units is to arrive at the Cost of Manufacturing of each item of rolling stock so that decisions on acquisition of rolling stock can be made on a rational and scientific basis. This will be facilitated greatly after the introduction of ERP (Enterprise Resource Planning) systems in all the production units and workshops of IR. In order to enable introduction of ERP, Railway Board, Production units as well as Zonal Railways must have digitized database details of all assets right from the time of proposal for acquisition till their condemnation. Details of every expenditure on manufacturing and maintaining each asset of the mechanical department must be available on the system. Till ERP is fully introduced in all the railways, cost of manufacture of rolling stock will be worked out as described in the following paragraphs. 205. The system of costing will differ depending on the nature of work carried out. The systems to be adopted in Railway Production units are Process Costing System for wheel manufacture, Foundry Accounts and similar activities and Batch Costing System for Rolling stock production. Both the systems are explained in the following paragraphs. 206. Process Costing System This system of costing is used for arriving at unit cost of cast iron melt in Railway Foundry workshops. The relevant direct material and direct labour forming Prime Cost of the process and in addition, indirect materials and labour are also charged to arrive at total Cost of the process. The total cost so arrived at is then divided by good castings to finally arrive at the unit rate of cast iron melt. The rate so arrived at forms the basic raw material Cost while computing the unit rate of Brake blocks manufactured. This may be extended to wheel manufacture and other similar activities. 207. The main features of Process Costing System are explained below: A. The quantum of raw material used with rate is fed as input B. Indirect materials like Ferro Manganese, Ferro Silicon, Fire bricks, Fire clay, Meltax, River sand etc. used are also to be given as input with Quantity and value to arrive at cost of indirect material. C. Quantum of Coke utilized with rate also to be given for the month. D. Direct Labour charges engaged in Casting/ Melting process for the month are to be booked to the work order. E. Finally the indirect Labour expressed as a percentage of Direct Labour also should be booked to the work order meant for Casting. The Total of (A+B+C+D+E)/ Good Casting will be unit rate of Cast iron melt. Foundry outturn statement for…..month M.207 A INPUT OUTPUT C I Scrap ******* Good casting ****** Pig iron ****** Rejections ****** Runners ****** Runners ****** Wastage ****** Sculling ****** Total ******* Total ******* Note: The format is for guidance only and can be modified by the Pus/ Workshops depending upon actual inputs and outputs Process cost sheet for ……. Month M. 207B RECEIPTS BALANCE OPENING ISSUES Balance Closing PARTICULARS AMOUNT AMOUNT RATE RATE RATE AMT AMT QTY QTY QTY QTY A. Direct material CI Scrap Runners B. Indirect Material Ferro Manganese Ferro Silicon Fire Bricks Fire clay Steel Pipe Meltex River sand C. Coke D. Direct Labour E. On cost Total Cost (A+B+C +D+E) Rate/kg cost/Good castings Total Note: The format is for guidance only and can be modified by the PUs/ Workshops depending upon actual inputs and outputs 208. Batch Costing System Railway production units engaged in Rolling Stock manufacture activity will adopt Batch Costing System. The total cost incurred per batch is collected and divided by the number of items of rolling stock manufactured to arrive at the unit cost of items produced in that particular batch. On completion of the batch quantity Completion Report should be drawn within 6 months to arrive at the cost of production of the said batch and forwarded to Railway Board. 209. Features of Batch Costing System a Each batch is assigned one work order number b All elements of cost pertaining to that batch are collected and charged to that work order. c Total expenditure is then divided by number of rolling stock produced in that batch to arrive at unit cost of rolling stock production. d This enables unit cost comparison between two batches viz. current batch & previous batch. 210. Batch size Orders on production unit for manufacture of locomotives, coaches etc., will be placed by the Railway Board. The Production unit should obtain necessary drawings and specification from RDSO / design office for the purpose of manufacture and use bill of materials (BOM) to generate the quantities to be procured by Stores Department. Wherever direct correlation between batch requirement of an item and drawl from store is not possible, the assessment of quantity is done by using a suitable forecasting technique. The total number of locomotives, coaches etc., should be split to convenient batches with due regard to the installed capacity and economy in production. The batch content should be decided by the PHOD of PU’s. The production control should release the orders for manufacture of components, assemblies for different batch quantity of Rolling Stock. However, in cases where circumstances so warrant, orders may be released in split up batch quantities also. 211. Work Orders The expenditure incurred by various Shops and Departments are collected under system of Work Orders as in the case of Workshop. Work Orders are of two kinds:- (i) Production Work Orders for collection of cost of works / jobs undertaken in Shops; and (ii) Non-Production Work orders for collection of indirect expenses which constitute Overheads. The work order system on Production Units has been discussed in detail in Chapter VIII of this Code and will apply mutatis mutandis to Production units. 212. Cost Classification The expenditure of a Production Unit is classified as under:- (a) Direct Labor comprising of (i) cost of labor booked directly to Work Order / Batch Order based on the average hourly rate; and (ii) actual incentive bonus paid Work Order / Batch Order wise. (b) Direct Stores; and (c) Overheads 213. Materials The materials directly required for the production and consumables are stocked in Stores Depot attached to the Workshops. The receipt, custody and issue of materials are done by the Stores Department based on the Issue Voucher generated by the Production Control. The raw materials are drawn through Material Requisition by Crediting Stores Suspense and Debiting WMS. All finished components held in Stores Depot under Stores Suspense are drawn by the Shops on Workshop Issue Slips for assembly or final fitment on the coach. The consumable stores for repair and maintenance etc. are drawn on Requisition-cum- Issue Note (Form 1523 or as prescribed in Stores Code or on specific material requisition). The stores department in PUs deals with procurement of purchase, receipt, custody and the issue of materials, M&P, tools and consumables stores. They also deal with inventory management and disposal of scrap materials. It deals not only with items borne under stores suspense, but also functions as custody stock holder of charged off shop manufactured items pending their drawl by shops. Receipt of Materials. The methodology to be followed for receipt of materials from trade is indicated in store code. Materials when received in the receipt ward are checked with relevant purchase order and after inspection and acceptance by the inspecting officer, a receipt note is granted which shows the allocation as final head or stores suspense. The materials are then passed on to the ward keeper or the concerned department. Imported stores are verified with reference to the “advice of dispatch”. These vouchers are posted as receipts in the numerical and priced ledgers and accounted for by debit to “stores suspense” or the final head as the case may be, by contra credit to purchases. If in any month the receipt note is received before the actual receipt of the material the debit is held temporarily under the “Stores-in-transit” account till the materials are received. In case of imported stores, the value of materials as ascertained from Invoice Distribution statement together with sea-freight, port and custom charges etc. is debited to stores suspense (or final head of a/c) contra credit to purchases imported to the extent of prime cost and different standing work orders for sea freight, port charges, custom duty etc. The credit understanding work orders for sea-freight etc. are cleared on receipt of debits for these charges. Materials manufactured in shops are accounted for through material tags and priced at price list rates. The value of the material is debited to stores suspense by contra credit to workshop manufacture suspense account. Material no longer required by shops and offices are returned to stores depot on ‘Advice Note of Returned Stores’ and the value thereof is accounted for as debit to ‘stores suspense’ and credit to shops or departments concerned against specified work orders or final heads of accounts. Transfer of materials from one U.L. No. to another within the same Depot is made through Book transfer forms. Adjustments necessitated by stock verification are made through Departmental or Accounts stock verification sheets surpluses being shown as debit and deficiencies as credit to stores suspense by contra credit or debit to stock adjustment account as the case may be. Materials are sometimes supplied to outside firms or Railways for fabrication, reconditioning etc. These are done by placing a fabrication contract on such units. The issue of material for fabrication /reconditioning /repair and receipt of fabricated reconditioned /repaired material is done through suspense issue note and suspense receipt note respectively. Details of this process is available in store code. In these cases usual issue notes are prepared and the value debited to ‘miscellaneous Advances’. Where the materials are received back duly fabricated or reconditioned they are received on usual Receipt Notes which are valued at the original cost of materials plus fabrication charges and accounted for a debit to ‘stores suspense’ by contra credit to ‘Miscellaneous Advances’. The extra credit balance lying under ‘Miscellaneous Advances’ represents fabrication charges and is cleared on payment or adjustment as the case may be. Issue of Materials: Some of the various issue vouchers through which issue of stores is made and counted for are given below (Details are available under Store order: a. Material Requisition: Raw materials and semi finished goods required for manufacture in the shops are drawn through material Requisition. This form, duly printed by the Electronic Data Processing Section is released by the progress office and after necessary posting in the numerical and priced ledgers, is accounted for by debit to various work orders concerned and credit to stores suspense. b. Workshop Issue Slips: All finished components held in stores depot under ‘Stock suspense’ are drawn by the shops on workshop Issue slips for assembly of final fitment etc. This form shows, interalia, complete allocation including the reference to the Batch No. etc. for which materials is required. This form duly printed by the EDP Section, is released by the progress office. These are posted in Numerical and Priced Ledgers and accounted for by debit to various work orders and credit to stores suspense. c. Issue Notes for consumable stores etc: Consumable stores for repairs and maintenance etc. are drawn on Requisition-cum-issue Notes (Form S. 1523 or as prescribed in Stores Code) which after posting in numerical and priced ledgers, are accounted for as debit to various work orders concerned and contra credit to stores suspense. d. Issue Notes for Sales: Materials sold to outsiders, railways or employees are transacted through Issue Notes, (Form S-1314 or as prescribed in Stores Code) and accounted for by debit to sales and credit to ‘stores suspense’/W.M.S. Integrated System of Stores and Cost Accounting- The details of this available in store code. In brief Store Accounting has been mechanized in the various production units in a manner whereby on the one hand the Stores Accounts Section is able to obtain tabulations and summaries for the purpose of reconciliation and compilation of monthly Stores Accounts pertaining to transactions for purchase Workshop manufactured materials, returned stores, issue of stores, adjustment of debits and credits against departments etc. It enables the costing section to obtain tabulations and summaries work order-wise in separate series of production and non-production of work orders for compilation of workshop manufacture suspense account. The tabulations obtained for various purposes will be reconciled by the Electronic Data Processing Section with various control figures before they are released. 214. For the material issued from store depot, the value of the stores issued should be debited against the relevant batch orders. The summary of the issues made to the relevant batch orders are to be grouped and indicated in the main sub ledger. Stores overhead at the prevailing percentage are also to be added. 215. Pairing of Issue Notes and Advice Note of Returned Stores Copies of Requisition-cum-Issue Notes (S.1523 or as prescribed in Stores Code) are to be received electronically in Costing Section. Each of these Issue Notes is paired with the corresponding copy received electronically after pricing from the Stores Accounts Section to see that:- (i) the shop serial number (i.e. Requisition Number) of the Issue Notes for each shop are continuous and that the breaks in such continuity, if any, are satisfactorily explained; (ii) The Issue Notes are received strictly according to the schedule i.e. by evening of the day following the date of issue; (iii) The issue notes are correctly prepared according to instructions issued for the purpose; and (iv) The work order number as quoted and the quantity of stores shown as received tally with the quantity shown as Issued in the copy received from Stores Accounts Section. Similarly, copies of Advice Notes of Returned Stores (S-1539) received from the Shops are paired with corresponding copies received from the Stores Accounts Section to see in addition that there is no delay in affording credit and that there is no difference in quantities. This procedure has been dealt elaborately in Stores Code. 216. Finished Parts Stores Depot In Production Units Finished Parts Stores Depot is the depot which stocks final manufactured goods under 'stores in stock’. In some cases, store depot also provides warehousing to the finished goods without taking these into books. These are the custody stores for finished parts. In respect of custody stores only 'Bin cards' and Numerical Ledger Cards are maintained by the ward keepers. The Finished Parts stores maintain the stock of only finished, semi-finished and rough components or assemblies. Cost and Detail Nos. / Part Nos. assigned for individual components and assembly serves as pricelist number. In respect of Finished Parts Store manufactured in Production Shops, the materials, while delivering to the Stores Department, are to be priced at prevailing estimated rate as provided in the workshop voucher based on para 317 below. These final rates of components are to be worked out for pricing and on completion of the Work Order batch. The final rate of component thus worked out updates the cost of finished stores part. Any difference between the old and new rates, if required is done by debiting to WMS. 217. Component Costing This is to be done only for item borne in the stores suspense. In respect of the furnished part-stores, an estimate is to be prepared before authorization of the work order. Production work orders for manufacture of components are released by quoting the order and batch numbers and cost and detail numbers/Part Number. Stores and labor required for the work order are to be booked and the estimated cost is to be advised to the stores accounts office to enable pricing of the item at the time of handing over to stores depot. The finished materials sent from shop to stores is initially priced at the estimated cost by debiting stores and crediting the respective work order. On completion of the work order, the difference between the estimate and actuals has to be advised and necessary adjustment is to be carried out in the books. 218. Assembly Costing The manufacture of Rolling Stock should be conveniently split up into a few divisions called groups, each group being composed of several assemblies. Each assembly is composed of several components each of which is indicated by Cost and Detail members/Part Numbers, which facilitate ascertaining of costs of assemblies and components from same labour and material booking documents with the help of machines. Production work orders for manufacture of components etc. are released by quoting the order and batch numbers and cost and detail numbers/Part Number. All Production documents viz. Material Requisitions, Job Cards, Squad Cards, Workshop issue slips, Material Tags etc. shall bear the order and batch numbers and cost and detail numbers/Part number. The labour and material charges booked through these documents are punched with all necessary particulars including order and batch nos. and C & D Nos. Batch-wise tabulations of labour and material charges and direct man-hours are then taken out in the "Electronic Data Processing Centre". Charges/Credits booked through out turn statements, miscellaneous adjustment memo, Material tags, Advice of Returned Stores are also tabulated batch wise separately. These charges/ credits shall be posted in the Workshop General Register under different elements of cost from month to month and progressive totals cost. These charges so collected under a batch constitute progressive cost of manufacture of the batch. The punched cards are sorted out by batches and groups and also by batches and assemblies and tabulations—group-wise and assembly-wise made out. Since the charges are tabulated by batches, groups and assemblies from same punched cards the totals of labour, material, overheads and man-hours by assemblies should agree with the total of the relevant batch. This reconciliation should be ensured by the "Electronic Data Processing Centre" before releasing the various tabulations to Costing Section. 219. Collection of Cost Under Groups and Assemblies The charges/credits appearing in the tabulations by groups and assemblies should be posted in the cost sheets for the groups and assemblies under different elements of cost and direct man-hours from month to month, each monthly figure being reconciled with corresponding figure available by batches in the Workshop General Register. On receipt of the completion certificate for.a batch, the totals of each group and assembly to end of the last month of booking of charges should be struck under different elements of cost and direct man-hours. 220. Overheads Besides direct expenditure on labour and materials incurred on a job, there are certain expenditures which cannot be directly charged to jobs but included in the cost of production on certain equitable basic. These indirect expenditures are termed in production units as overheads. The overheads in a production unit are classified on commercial pattern into four categories to ensure proper control and equitable distribution of indirect expenses on cost of production. These are as under: a. Factory overhead b. Administrative overhead c. Township overhead d. Stores overhead Separate standing work orders are issued for collection of overhead expenditure in respect of each of the above classification. For facility of collection, analysis and control of overheads falling under the above categories, separate expense numbers are allotted. The vouchers containing a charge to overhead expenses should bear the appropriate allocation as under: S.W.O. No. Overhead Expense No. Shop/Department. Factory Overheads This should generally comprise of: a. All indirect expense of production shops. b. All indirect expenses of production-cum-service shops. c. Expenses of Apprentices attached to main shops d. Expenses of Dy.CME (W)/Work Manager’s office including planning and progress, preplanning, estimating etc. offices. e. Expenses of time keeping organization. f. Expenses of works canteens including meal sheds. g. Depreciation of Building, Plant and Machinery of shops and Departments mentioned above. h. Electric charges consumed by departments and shops mentioned above. i. Credit for return of materials, interest and profit earned for works done for outsiders etc. Administrative Overheads These include: a. Expenses of General Managers office and other general administrative offices. b. Electric charges, as consumed by various offices included in (a) above. c. Credits on account of return of materials, diet charges etc. Township Overheads These comprise of: a. Expenses of civil engineering depts. b. Expenses of water works, sanitation, horticulture etc. c. Electricity consumed by the above departments and township. d. Depreciation of Buildings, Plant and Equipments etc. of above Departments and Township. e. Credit for recovery of house rent, electricity and water charges from staff and outsiders and return of materials etc. by the Departments mentioned above. Stores Overheads These comprise of: a. Cost of stores department in headquarter or elsewhere. b. Depreciation of buildings and equipments of the various stores offices/Deptts. c. Inland handling and freight charges not allocated to stores directly. d. Clearance from Stock Adjustment Account. e. Cost of pattern supplied by the Administration to suppliers as per agreement. f. Cost of replacement and rectification of defective and deficient materials supplied by the stores departments and not recoverable from Firms. g. Credit for return of materials allocable to stores Depts. And for incidental, freight and departmental charges realised on sales. Chief Mechanical Engineer of every Production unit will arrange to issue in consultation with associated finance fresh work orders for Overheads required for their units and the same should be reviewed once in 5 years. 221. Allocation and Apportionment of Overheads Administrative and Township Overheads are levied on direct wages of Production Jobs including incentive bonus and overtime payment. The percentages of Factory Overhead are worked out separately shop-wise, while the Administrative and Township Overheads are worked out as a percentage for the entire Workshop. A single percentage rate should be worked out for Stores Overhead for levy on Direct Stores. Chief Mechanical Engineer and Controller of Stores of every Production unit will arrange to work out these percentage rates in consultation with associated finance based on the actual expenses of the previous year and budgeting. The overhead percentages should be revised after revised estimates are submitted. In the case of work done for Government departments other than Indian railways, Railway PSUs, other PSUs, Private parties and export, profit shall be charged over the total estimate cost as a percentage, as per the extant instructions of Railway Board. In order to be competitive in international markets, the General Manager of a zonal Railway/Production Unit/Chief Administrative Officer of Production unit shall with the concurrence of FA & CAO have the power to reduce the quantum of fixed over heads and profit for exports, in accordance with special instructions in vogue. (7) @ applicable rate on Cl.1 to 6 EXCISEDUTY PROFIT (8) Material (2) packing (9) Nature of Charges & Proforma Labor (1) SOH (6) TOH (5) AOH (4) FOH (3) Special Direct Direct Work Capital/ Yes Yes Yes Yes Yes Yes Yes NIL NIL RSP/DRF For other Indian Yes Yes Yes Yes Yes Yes Yes NIL NIL Railways Railway Public Sector Under Percentage of Yes Yes Yes Yes Yes Yes Yes Actuals takings & Govt. (1+2+3+4+5+6) Departments Private parties & other Public Yes Yes Yes Percentage of Yes Yes Yes Yes * Actuals sector Under * * * (1+2+3+4+5+6) takings Percentage of Yes Yes Yes Yes Exports Yes Yes Yes * (1+2+3+4+5+6) Actuals * * * * * * For exports, fixed components of these overheads and profit can be reduced by GM with the concurrence of FA & CAO. Proforma Charges.—Proforma charges mentioned in above table comprise of: (i) Dividend.—Dividend charges payable to General revenue for a year at the applicable rate should be calculated on Capital-at-charge to end of the previous year plus half of the (anticipated) capital outlay for the year and should be distributed over the number of locomotives coaches etc