Gulfstream G650ER Flap Control System PDF
Document Details
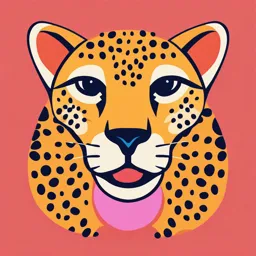
Uploaded by PhenomenalNumber
Tags
Related
- Gulfstream G650ER Aileron Interface and Control System Description Manual PDF
- Gulfstream G650ER Flap Actuation System PDF
- Gulfstream G650ER Flap Interface and Control PDF
- Gulfstream G650ER Flap System Electronics PDF
- Gulfstream G650ER Flap System Sensors and Indication PDF
- Gulfstream G650/G650ER Level A Question Bank PDF
Summary
This document describes the flap control system of a Gulfstream G650ER aircraft. It details the system's components, operation, and interfaces with other aircraft systems. The document covers flap actuation, sensors, and electronics.
Full Transcript
GULFSTREAM G650ER SYSTEM DESCRIPTION MANUAL FLAP CONTROL — SYSTEM DESCRIPTION 1. General A. Description The flap control system is a conventional system that provides electrical and mechanical control of the flaps, fault monitoring and annunciation. The flap control system interfaces with the follow...
GULFSTREAM G650ER SYSTEM DESCRIPTION MANUAL FLAP CONTROL — SYSTEM DESCRIPTION 1. General A. Description The flap control system is a conventional system that provides electrical and mechanical control of the flaps, fault monitoring and annunciation. The flap control system interfaces with the following aircraft systems: Aircraft hydraulic system Aircraft electrical DC power system Flight Control Computers (FCCs) Avionics Crew Alerting System (CAS) Central maintenance computer NOTE: The flap control system operates separately from the primary flight control system. The primary flight controls are ailerons, spoilers, elevators and rudders. The flaps are located on the trailing edges of each wing at Rear Beam Station (RBS) 109 - RBS 405. The flap system is comprised of a Fowler-type, single flap surface on the trailing edge of each wing. When extended, flaps increase wing aerodynamic lift and drag. This improves takeoff, approach and landing performance. Both left and right wing flap surfaces are simultaneously operated by the flap actuation system to extend or retract according to pilot input. The flap handle controls the flap position. The flap handle has four distinct detent positions that adjust the flap surfaces to UP (0°), 10°, 20° (T/O APP) and DOWN (39°). See Figure 1 and Figure 2. To compensate for pitch trim changes as the flaps are extended or retracted, the FCCs provide commands to the elevators. See Flight Controls, 27-00-00, System Description for more details. Closed loop feedback and position indication in the cockpit is provided by dual channel resolvers located on the left and right outboard flap actuators. flap handle inputs are sensed by two, single channel Rotary Variable Differential Transformers (RVDTs) in the flap handle. Position data is transmitted to the avionics system from each Flap Electronic Control Unit (FECU) lane. This data consists of flap position and flap handle position. The FECU runs several fault monitors and built-in test routines for the flap during actuator operation. 2. Subsystems Flap Interface and Control, 27-51-00, System Description Flap Actuation, 27-53-00, System Description Flap System Sensors and Indication, 27-54-00, System Description Flap System Electronics, 27-55-00, System Description 3. Subsystem Details A. Flap Interface and Control The flap interface and control includes the following: Flap control module with flap handle FECU Hydraulic Power Drive Unit (PDU) Hydraulic Control Module (HCM) Two actuators per flap surface Dual channel position sensors 27-50-00 Page 1 May 15/23 GULFSTREAM G650ER SYSTEM DESCRIPTION MANUAL Torque shafts and pillow blocks Quick disconnect switch The flap control module is installed in the pedestal located in the cockpit and contains the flap handle. The module interfaces with aircraft wiring through two electrical connectors and an edge lit panel. The edge lit panel lights up the module for low light operation. The flap PDU is located in the main landing gear wheel well. It converts hydraulic power into mechanical power through the use of one hydraulic motor and one gearbox. The PDU is connected to the flap inboard and outboard ballscrew actuators by torque shafts and pillow blocks. Flap torque shafts are located on each wing rear beam and are connected to the PDU. They transfer PDU torque to the flap actuators. Flap pillow blocks (bearing supports) are located in between the flap torque shafts. The motion of the left and right flap surfaces is mechanically synchronized by the flap PDU. The PDU simultaneously drives the left and right flap surfaces, through the torque shafts and flap surface actuators installed in both wings. The flap actuators contain mechanical force limiters that protect the flap actuators and flaps in the event of a mechanical jam or extension of flaps against excessive air loads. The PDU motor is hydraulically powered by the HCM. The HCM provides the motor with adequate control flow to move the flap surfaces at a specified rate. The HCM incorporates a Solenoid Operated Valve (SOV) and an Electro-hydraulic Servo Valve (EHSV) to provide control flow to the PDU motor. Both SOV and EHSV are electrically controlled by the FECU. The FECU monitors the flap position, speed and direction based on the feedback from the dual position sensors on the left and right outboard actuators. B. Flap Actuation The flap actuation system provides actuation and control of the flap surface on the left and right wing. In normal operation, the left 3000 psi hydraulic system, powered by the left engine-driven pump, provides hydraulic power to the hydraulic control module. The flap actuators extend and retract the two trailing edge flaps by converting rotary input torque into linear motion and force. Hydraulic actuation is driven by the FECU. The FECU provides command data to the flap HCM. The HCM provides the control of the hydraulic fluid to the PDU. The PDU is the control and power conversion element of the flap hydraulic actuation system. It consists of an hydraulic motor and a gearbox. The PDU is mounted transverse to the top of the torque box at FS 579, WL 48 and right BL 1. The SOV provides hydraulic power to the EHSV that ports hydraulic pressure for the PDU operation. C. Flap System Sensors and Indication Dual channel flap position sensor resolvers are installed on the outboard flap actuator on each wing and electrically bonded to the aircraft through a grounding strap. The flap position resolvers provides electrical feedback from the outboard flap actuator rotary inputs to the FECU. The position sensor provides the flap panel position and closes the positional control loop of the flap panel surface. The FECU provides excitation to the position sensor and converts the feedback to a flap position used to maintain flap positional accuracy, protect against asymmetry and provide the pilot flap position data. In addition to the flap position sensor resolvers, there are two electrically independent Rotary Variable Differential Transformer (RVDT) position sensors inside the flap control module. The flap control module interfaces with the FECU. In normal operation mode the FECU normal channel provides excitation to the flap position sensors and monitors the flap handle position. 27-50-00 Page 2 May 15/23 GULFSTREAM G650ER SYSTEM DESCRIPTION MANUAL D. Flap System Electronics The FECU is an electronic controller with a command / monitor architecture that provides control of the flap actuation system. The FECU interfaces with the flap control module, the flap HCM and position resolvers on the flap actuators and provides data to the FCCs using an Aeronautical Radio, Incorporated (ARINC) 429 bus. The FECU is electrically bonded to the aircraft structure through the FECU mounting tray. NOTE: The FCCs do not provide direct control data to the flaps. The flap HCM interfaces with the aircraft left hydraulic system and provides hydraulic system pressure and flow to the flap system PDU. The HCM responds to electrical commands received from the FECU and provides directional control, extend / retract and low / high speed rate control of the PDU. The HCM has one SOV and one EHSV and is installed in closed proximity to the PDU. The HCM contains an SOV, preloaded to the closed position, that stops hydraulic flow when not energized. The SOV opens when the solenoid coil is energized with 28 Vdc provided by the FECU. When open, the valve allows hydraulic system flow and pressure supply to the EHSV. The EHSV provides directional and flow control to the PDU. Flap surface deployment rate depends on the EHSV command current magnitude. 4. Operational Summary A. Flap Control The pilot manually adjusts the flap handle on the pedestal to position the left and right flap surfaces. If flap deployment is commanded at an airspeed higher than the flap placard speed for that position, the airspeed digits on the primary flight display turn red and an audible warning sounds. However, the FECU still tries to deploy the flaps. If the aircraft slows below flap placard speed for that flap position, the warning indications cease and flaps extend to the selected position. If the aircraft is sufficiently above flap placard speed, the force limiters in the flap actuators trip, stopping flap motion. Flap positions and system status are transmitted to the flightcrew from each lane of the FECU to the modular avionics units for display on the primary flight displays and the Aircraft Configuration synoptic page. System status and fault information is also recorded for later analysis and / or maintenance action. With the exception of an attempt to reverse the command and back out of an inferred symmetric lockup condition, the FECU will not permit further flap operation after the force limiters are tripped. If an attempt to back out of the symmetric flap lockout is successful, normal flap operation may be resumed. Otherwise, the FECU shuts down the flap system. If the flap handle is out of a detented position for more than 5 seconds, a message is displayed on CAS. This alerts the flightcrew to place the flap handle in a detented position. 27-50-00 Page 3 May 15/23