Engine Ops_Pump Op3 PDF
Document Details
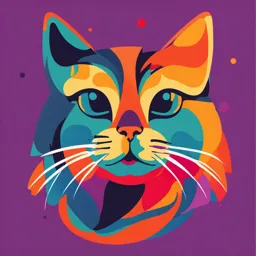
Uploaded by ProtectiveDaffodil
Tags
Summary
This document provides instructions on the operation modes of a pump, including Pressure Mode and RPM Mode. It details handling situations like running away from water, low water, or no water. The document also explains the switching between operating modes. It specifically covers the operation of a pump boss 400 pressure governor.
Full Transcript
OPERATION MODES The Pump Boss has two operating modes: o Pressure Mode o RPM Mode Click here to view Vector Solutions video on the Pump Boss PRESSURE MODE OPERATION In Pressure Mode, the governor maintains a constant pump discharge pressure. The discharge pressure is monitored and compared to the se...
OPERATION MODES The Pump Boss has two operating modes: o Pressure Mode o RPM Mode Click here to view Vector Solutions video on the Pump Boss PRESSURE MODE OPERATION In Pressure Mode, the governor maintains a constant pump discharge pressure. The discharge pressure is monitored and compared to the selected pressure setting; the engine RPM is varied to keep the discharge at the selected setting In Pressure Mode, the Pressure LED will be on. The governor maintains a constant discharge pressure within system capabilities by adjusting the engine RPM automatically to compensate for variations in pressure There is a max engine RPM programmed into the governor for Pressure Mode. If that RPM is reached, the message display flashes MAX RPM/OPERATOR, and the engine RPM is not allowed to go any higher RUNNING AWAY FROM WATER, LOW WATER, OR NO WATER There are situations during pump operations where there may be low or no supply water. This can be due to an empty water tank, a problem on the intake line, air in the pump, changing the water source, or an insufficient water supply The governor currently monitors the discharge pressure and compares it to the engine RPM. It is pre-programmed to limit RPM increases when conditions arise that fall outside normal operating parameters RUNNING AWAY FROM WATER If the discharge pressure starts dropping while operating in Pressure Mode, the governor increases the RPM and attempts to maintain the selected pressure setting. If the pressure drops and an increase in engine RPM does not bring the pressure back up, the governor recognizes this as a Running away from water condition. When this condition occurs, the governor switches to the RPM Limit Mode and controls the engine RPM accordingly RPM Limit Mode: When the RPM Limit mode is in effect, the Pressure LED stays on. To alert the operator, the RPM LED and the RPM DISPLAY flash, and the message display flashes OPERATOR/RPM LIMIT Second Edition 01/31/22 102 RUNNING AWAY FROM WATER CONT. In this mode, the pressure setting does NOT change and the PRESET button is DISABLED. If the pressure comes back up to the selected pressure setting, the RPM Limit Mode is cancelled, and the governor switches to normal operation in Pressure Mode at the selected pressure In some cases, the pressure may not come back up but remains at a level ABOVE 45 PSI. In the RPM Limit Mode the governor behaves like a manual throttle, and the operator can raise or lower the pressure by rotating the control knob. If the RPM is lowered to a point where the pump is no longer running away from water and the pressure is stable, the RPM Limit Mode is cancelled. The governor switches to normal operation in Pressure Mode with the current discharge pressure as the new pressure setting If the pump operator sets the engine to idle via the IDLE button, the governor comes out of the RPM Limit Mode and cancels the pressure setting LOW WATER CYCLE If the discharge pressure is less than 45 PSI, but stays above 15 PSI, the governor enters a Low Water Cycle and the message display flashes ATER The governor then sets the engine RPM to 1100 RPM. If the pressure does not rise above 45 PSI in seven seconds, the governor sets the engine RPM to IDLE The governor repeats the Low Water Cycle as long as the discharge pressure is between 15-45 PSI If the pressure rises above 45 PSI, the engine resumes normal operation (The RPM and PSI values for the Low Water Cycle are programmable) NO WATER SUPPLY If the discharge pressure is below 15 PSI, the governor sets the engine RPM to IDLE and the message display flashes NO WATER If the discharge pressure rises above 15 PSI within three minutes, the governor enters the Low Water Cycle mentioned above If the discharge pressure DOES NOT rise above 15 PSI within three minutes, the governor switches to IDLE MODE and cancels the pressure setting If the governor switches to IDLE Mode and cancels the pressure setting, the pump operator will have to take action to restart pump operations (press PRESET and/or rotate the control knob to select the pressure setting) Second Edition 01/31/22 103 RPM MODE OPERATION In RPM Mode, the governor maintains a constant RPM The pump discharge pressure can vary in RPM Mode; however, as a safety feature, the governor limits the increase in PSI to 30 PSI over the last established PSI value. As the discharge pressure approaches this limit, the governor automatically lowers the RPM to prevent a high-pressure surge The RPM LED blinks as the governor sets a lower RPM. This lower RPM will be the new operating RPM setting SWITCHING BETWEEN OPERATING MODES No variation in discharge pressure or RPM occurs when changing between Pressure Mode and RPM Mode When changing from Pressure Mode to RPM Mode, the RPM setting will be the RPM that the pump was operating at in Pressure Mode When changing from RPM Mode to Pressure Mode, the pressure setting will be the pressure that the pump was operating at in RPM Mode To switch between modes when the engine is at idle RPM: o Press the desired mode button, and the governor will change modes immediately To switch between modes when the engine RPM is above idle: o Press and hold the mode button for three seconds, and the governor will change modes. This is to avoid accidentally changing modes if the buttons get bumped Second Edition 01/31/22 104 OVERVIEW The discharge relief valve is a mechanical spring tensioned device designed to regulate the pump discharge pressure by rerouting excess discharge pressure back into the intake side of the pump COMPONENTS AND SPECIFICATIONS Made of two separate units o Pilot Valve mounted to the exterior of the pump panel; this pilot valve controls the operation of the relief valve o Relief Valve mounted between the intake and discharge sides of the pump Functional operating range is 75 PSI 300 PSI PILOT VALVE CONTROLS Pilot valve has two controls: o On/off switch o Pressure adjustment handle to adjust the relief valve operating pressure Open/Closed lights: o Amber light (Open) = On (relief valve engaged) o Green light (Closed) = Off (relief valve not engaged) The unit has a strainer designed to filter sand, grit, or other objects from the valve piping. The strainer should be serviced monthly (instructions on next page) Pressure adjustment handle increases or decreases the pressure required to open the relief valve o One turn is approximately 10 PSI o Turn counterclockwise to decrease pressure; turn clockwise to increase pressure The pressure adjusting spring on the pilot valve regulates the pressure needed to open the main relief valve located on the pump Second Edition 01/31/22 105 SETTING THE PRESSURE With water flowing, turn the pilot valve control on. The light should be green, indicating the relief valve is closed (not engaged) o If the light is amber, the pressure is set lower than the current discharge pressure and must be increased instead of decreased for capture The highest discharge pressure expected to be used based on the requirements of that as the target pressure Turn the pressure adjustment handle counterclockwise (decrease) in half turn increments. Pause between turns until mechanical and electronic capture is achieved o Mechanical capture = a reduction of PSI on the discharge gauge o Electronic capture = the light will change from green (closed) to amber (open) Note electronic capture will be delayed; mechanical capture will happen first Once mechanical and electronic capture have been achieved, turn the pressure adjustment handle one full turn clockwise to set it MONTHLY MAINTENANCE INSTRUCTIONS 1) Engage the pump and increase the pump discharge pressure to 150 PSI 2) With the pilot valve OFF, remove the strainer assembly by unscrewing it. Clean the strainer and the orifice in the end of the rod 3) Cover the strainer opening with one hand and slowly turn the pilot valve ON and OFF several times. In the ON position, water should flow from the strainer opening and the relief valve should open (amber light). In the OFF position, the water flow should stop and the relief valve should close (green light) 4) Check the strainer O-rings and replace if required. Screw the strainer assembly back in place (hand tight only) 5) With the pilot valve OFF, turn the pressure adjustment handle counterclockwise until it stops 6) Slowly turn the pilot valve ON. The relief valve should open (amber light) and the pump discharge pressure should decrease 7) Slowly turn the pilot valve OFF. The relief valve should close (green light) and the pump discharge pressure should rise back to 150 PSI 8) Repeat steps six and seven until the system responds quickly when turned ON and OFF 9) Reset the pressure adjustment handle to the desired pressure setting and decrease the engine speed to idle Second Edition 01/31/22 106 OVERVIEW Each CFD engine is outfitted with three separate intake relief valves. These relief valves operate similar to the Waterous discharge relief valves found on the older Ferrara engines. The relief valve has a spring mechanically tensioned to a set pressure; any excess pressure will be discharged if this setting is exceeded. Intake relief valves discharge the excess pressure onto the ground, rather than internally like the discharge relief valve. Mechanical discharge relief valves are no longer being installed on newer apparatus, due to the Pump Boss pressure governors. However, intake relief valves will continue to be a part of each new engine. The purpose of the intake relief valve is similar to that of the discharge relief valve to prevent surges in pressure from damaging supply hose or personnel. If crews are operating on a large incident and flowing large volumes of water, sudden changes in flow (generally the stoppage of flow due to closing a main intake valve or large master streams) could lead to a rapid rise in supply hose pressure, creating a potentially dangerous water hammer. The intake relief valve will regulate these pressure surges to prevent the supply hose from building to an excessive pressure. LOCATION When looking at the underside of the PVC drain piping directed toward the ground in several spots. Following this plumbing upward will lead to one of the three intake relief valves (red circle in left photo). The photo on the right shows a close up of one of the relief valves viewable with the cab tilted and the pump housing cover removed. operate independently of one another. They are both placed before the actual Main Intake Valve (MIV) butterfly valve. This means that the relief valve will activate with the MIV either open or closed. This allows the relief valve to still provide safety for the supply hose if the MIV is inadvertently closed, regardless which side the supply hose is attached to. For example, if the attack engine is being supplied by another engine and rapidly closes the MIV prior to having the this scenario, the relief valve would act hose, protecting the operator near the pump. Second Edition 01/31/22 107 The third intake relief valve is mounted in close proximity to the two previously mentioned intake relief valves. However, the third valve is plumbed in after the MIVs. This allows the relief activate anytime the pressure on the intake side of the pump exceeds its set pressure. The photo to the right shows the Intake Relief Valve exceeding the current setting. CHECKING INTAKE RELIEF VALVES Checking the current pressure setting of each intake relief valve is a relatively simple process. For the MIV relief valves, connect a short section adapter. The MIV should remain closed. Slowly increase discharge pressure on activates (indicated by water discharging onto the ground via the piping). There should be no pressure showing on the intake gauge with the MIV closed. found to be activating around 150 PSI. The same process can be completed for the officer side MIV to find out its setting. Second Edition 01/31/22 108 A second engine is required to check the s. Since this needs to be open to check it. Attempting to check it the same way as the MIVs above will not allow the intake pressure to build, since water is being discharged as fast as it can enter the pump. Connect two short sections of the engine having its relief valve checked. With the intake open on the engine receiving pressure, slowly increase discharge pressure on the supply engine until the relief valve activates. Use the intake gauge on the engine receiving water to determine what pressure the intake relief valve is currently set to. Either intake relief valve, since both sides are controlled by the same valve. ADJUSTING INTAKE RELIEF VALVES Normally no operator adjustment should be needed, as these valves are set prior to delivery to their respective fire houses. These intake valves are not intended to be adjusted like the older discharge relief valves are via the pilot handle at the pump panel. This absence of an external pilot handle that can be adjusted at the pump panel is another key difference between intake relief valves and discharge relief valves. Currently newer CFD Sutphen apparatus come with their intake relief valves set to 180 PSI on all three intake relief intakes set around 120 PSI, and the third intake relief valve set to around 165-180 PSI. However, it has been found that over time the tensioning nut can gradually loosen due to the normal vibrations of the truck. Some backup apparatuses have been found with their intake relief valves loosened to the point of activating around 70 PSI. This could lead to large amounts of undesirable ice forming during cold weather operations, potentially creating a hazard area around the pump for the operator. Also, if the attack engine requires higher intake pressure from a supply engine during series pumping (such as a high-rise operation with two single-stage pumps), the intake relief valve would limit the intake pressure available to the attack engine. Second Edition 01/31/22 109 If an intake relief valve is found to be discharging below the desired 180 PSI, it should be adjusted to the proper setting. The intake relief valves on newer CFD Sutphen engines can be accessed by tilting the cab and removing the pump housing cover. Older models of engines might only have access by crawling underneath the pump. The relief valve. It is only accessible from underneath by crawling under the pump. If there is a locking screw, it should be loosened one full turn prior to attempting to adjust the tensioning nut (right photo). This locking screw can be loosened with an Allen wrench. This locking screw might already be loose or missing (possibly a reason the tensioning nut has loosened). The large tensioning nut can then be loosened or crescent wrench. Loosen the tensioning nut until it is no longer in contact with the spring mechanism inside (indicated by the nut being able to be freely rotated by hand). From there, rotate the tensioning nut until it is in contact with the spring mechanism (you should start feeling the resistance of the spring). to begin increasing its operating pressure. The chart below shows the number of full turns required to reach the desired operating pressure. Number of 360° Turns from ZERO Opening Pressure PSI 0 1 2 3 4 5 6 7 8 9 75 103 126 148 170 191 209 230 250 269 Fully Down 281 Once it is tensioned, test the intake relief valve using the methods discussed previously to ensure it is activating at the desired pressure. Once the desired pressure is achieved, tighten the locking screw (if applicable). Obviously, performing this process on the scene of an emergency incident is not desirable. Crews should regularly flow water from a supply source through their pumps (not just recirculating tank water) especially if running with a backup apparatus. Second Edition 01/31/22 110 OVERVIEW Over time, engines will accumulate dirt and debris inside the pump housing This debris can come from soot, sand, corrosion, or damage to the water mains Rust and debris can also come from the interior of the pump itself It is important to periodically flush this debris out of the pump by back flushing the system WHAT IS BACK FLUSHING? Back flushing is the act of flowing water in reverse through the pump to clear debris A positive water source is hooked up to the pump discharge (backwards), and water is flowed out the remaining intakes and discharges The truck pump does not get engaged and the truck can be turned off. A positive water source is all that is needed Although the order in which the valves are opened is not critical, a systematic approach helps keep track of what has and has not been flushed yet. An example is shown below: o Driver and o o Driver and o uxiliary intakes o All remaining discharges o Do not include the pre-connects in the rear of the hose bed or cross lay. Since the pre-connects and the cross lay are elevated above the center of the pump housing, finding a large amount of sediment and debris there is unlikely Back flushing also gives crews a chance to operate all valves, service caps, fittings, and to repair broken screens if needed The following pages show a detailed step by step process of how to back flush a pump Second Edition 01/31/22 111 HOW TO BACK FLUSH THE PUMP Prior to back flushing the pump, contact the Support Services Apparatus Maintenance Captain and make sure replacement intake screens are available. Start by parking the engine close to a hydrant on the officer side. With the engine turned off, Storz fittings to expose the intake screens. Finally, remove all the discharge caps. These photos show the intake screens. The next step is to remove the screens so debris can pass through. intake screens, consider using two sets of needle nosed pliers to pull out the screen. Another option is feeding a piece of webbing through multiple areas of the screen and pulling outward. It is common for 5 screens to be corroded in place; it can take a little effort to remove them. intake screens, the gasket must be removed first, then pull out the screen. Intake screens are made to be designed to degrade and corrode so the inner workings of the pump do not. Older screens that have not recently been replaced can be very fragile, e hammering the screens or prying against them with a screwdriver. If the screen cracks or is already damaged, replace the screen. It may be difficult to keep from damaging older screens. Replacing the screens is normal maintenance that can be completed at the station level. Second Edition 01/31/22 112