Configuration Management User Guide - Ramco Aviation Solution PDF
Document Details
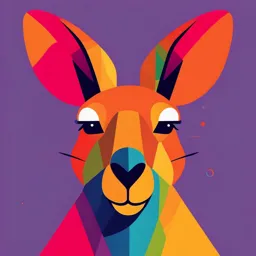
Uploaded by TruthfulHarp
Anna University
2022
Tags
Related
- Chapter 8 - 06 Configuration Management Fundamentals PDF
- Chapter 8 - 06 - Understand the Fundamentals of CM and Asset Management PDF
- NAVAIR SOP 00-25-300 Chapter 2 PDF
- Introduction to Software Maintenance & Configuration Management (SCM) PDF
- Software Configuration Management CSE2552 PDF
- CSE2552 Software Configuration Management PDF
Summary
This document is a user guide for Ramco Aviation Solution, version 5.9. It provides an overview of configuration management processes and functions in the aviation industry. The guide covers aircraft and component configuration management, technical record management, and various tasks like defining aircraft entities, managing parts, and building configurations. It's intended for users new to the solution.
Full Transcript
RAMCO AVIATION SOLUTION VERSION 5.9 USER GUIDE CONFIGURATION MANAGEMENT ©2022 Ramco Systems Limited. All rights reserved. All trademarks acknowledged. This document is published by Ramco Systems Ltd. without any warranty. No part of this document may be reproduced or transmitted in any form or by...
RAMCO AVIATION SOLUTION VERSION 5.9 USER GUIDE CONFIGURATION MANAGEMENT ©2022 Ramco Systems Limited. All rights reserved. All trademarks acknowledged. This document is published by Ramco Systems Ltd. without any warranty. No part of this document may be reproduced or transmitted in any form or by any means, electronic or mechanical, for any purpose without the written permission of Ramco Systems Limited. Improvements and changes to this text necessitated by typographical errors, inaccuracies of current information or improvements to software programs and/or equipment, may be made by Ramco Systems Limited, at any time and without notice. Such changes will, however, be incorporated into new editions of this document. Any hard copies of this document are to be regarded as temporary reference copies only. The documentation has been provided for the entire Aviation solution, although only a part of the entire solution may be deployed at the customer site, in accordance with the license agreement between the customer and Ramco Systems Limited. Therefore, the documentation made available to the customer may refer to features that are not present in the solution purchased / deployed at the customer site. Ramco Aviation Solution 3 | Configuration Management ABOUT THIS MANUAL This manual briefly describes the basic processes and functions in Ramco Aviation Solution. WHO SHOULD READ THIS MANUAL This manual is intended for users who are managing the Aviation industry processes and are new to Ramco Aviation Solution. This manual assumes that the user is familiar with the Aviation Industry nomenclatures and systems based software. HOW TO USE THIS MANUAL Ramco Aviation Solution provides extensive Online Help that contains detailed instructions on how to use the application. Users are suggested to use this manual for specific references, along with the Online Help. This manual contains enough information to help the users perform the basic tasks and points toward the Online Help for more detailed information. HOW THIS MANUAL IS ORGANIZED The User Guide is divided into 2 chapters and index. Given below is a brief run-through of what each chapter consists of. Chapter 1 provides an overview of the entire Configuration Management business process. The sub processes are explained in the remaining chapters. Chapter 2 focuses on the Aircraft & Component Configuration Management sub process. Chapter 3 dwells on the Technical Record Management sub process. The Index offers a quick reference to selected words used in the manual. DOCUMENT CONVENTIONS The data entry has been explained taking into account the "Create" business activity. Specific references (if any) to any other business activity such as "Modify" and "View" are given as "Note" at the appropriate places. Boldface is used to denote commands and user interface labels. Example: Enter Company Code and click the Get Details pushbutton. Italics used for references. Example: See Figure 1.1. The icon is used for Notes, to convey additional information. REFERENCE DOCUMENTATION This User Guide is part of the documentation set that comes with Ramco Aviation Solution. The documentation is generally provided in two forms: The Documentation CD in Adobe® Systems’ Portable Document Format (PDF). Context-sensitive Online Help information accessible from the application screens. WHOM TO CONTACT FOR QUERIES Please locate the nearest office for your geographical area from www.ramco.com for assistance. Ramco Aviation Solution 4 | Configuration Management contents 1 INTRODUCTION........................................................................................................................7 1.1.1 INTRODUCTION................................................................................................................................7 2 AIRCRAFT & COMPONENT CONFIGURATION MANAGEMENT..................................................................................................................................9 2.1 SETTING UP COMMON MASTERS FOR AIRCRAFT AND COMPONENT CONFIGURATION MANAGEMENT............................................................................................................. 10 2.1.1 Defining regulatory authority codes.................................................................................................10 2.2 DEFINING AIRCRAFT ENTITIES.......................................................................................................... 11 2.2.1 Defining quick codes.........................................................................................................................11 2.2.2 Creating manufacturer.....................................................................................................................11 2.2.3 Creating parameters.........................................................................................................................12 2.2.4 Setting base parameters...................................................................................................................13 2.2.5 Creating formula for consumption and range parameters...............................................................14 2.2.6 Creating aircraft model.....................................................................................................................16 2.2.7 Attribute Parameters........................................................................................................................17 2.2.8 Creating zones..................................................................................................................................18 2.2.9 Creating ATA chapter........................................................................................................................19 2.2.10 Managing Cabin Configuration.......................................................................................................19 2.2.11 Mapping Cabin Configuration.........................................................................................................21 2.2.12 Maintaining Cabin equipment........................................................................................................21 2.3 Defining configuration entities........................................................................................................ 23 2.3.1 Creating configuration class.............................................................................................................23 2.3.2 Creating deferral category................................................................................................................24 2.4 Managing effectivity of parts........................................................................................................... 25 2.5 Managing Recommended Spare Parts List........................................................................................ 27 2.6 Building model and part configuration............................................................................................. 29 2.6.1 Building aircraft model configuration...............................................................................................29 2.6.2 Building part configuration...............................................................................................................37 2.7 Maintaining flight log parameters.................................................................................................... 41 2.8 Inducting aircraft and components.................................................................................................. 43 2.8.1 Maintaining maintenance information for part...............................................................................43 2.8.2 Creating part model..........................................................................................................................48 2.8.3 Defining component.........................................................................................................................50 2.8.4 Updating component condition........................................................................................................58 Ramco Aviation Solution 5 | Configuration Management 2.8.5 Defining aircraft................................................................................................................................58 2.8.6 Changing aircraft registration number.............................................................................................65 2.8.7 Creating aircraft group.....................................................................................................................66 2.8.8 Managing Part Maint. Level Definitions...........................................................................................66 2.9 Building component and aircraft configuration................................................................................ 67 2.9.1 Building component configuration...................................................................................................67 2.9.2 Building aircraft configuration..........................................................................................................71 2.10 Recording aircraft readiness log details.......................................................................................... 80 2.11 Activating aircraft record............................................................................................................... 82 2.12 Updating status and condition for aircraft records......................................................................... 83 2.13 Approving configurations............................................................................................................... 85 2.13.1 Approving model and aircraft configuration..................................................................................85 2.13.2 Canceling model and aircraft configuration...................................................................................86 2.13.3 Approving part and component configuration...............................................................................86 2.13.4 Canceling part and component configuration................................................................................88 2.13.5 Viewing part usage information.....................................................................................................88 2.14 Managing Thrust Ratings & Performance based Life Limits............................................................. 89 2.15 Generating serviceable certificate.................................................................................................. 91 2.16 Reviewing component / receipt records......................................................................................... 92 2.17 Managing part restrictions............................................................................................................. 94 2.18 Correcting the parameter value..................................................................................................... 95 2.19 Viewing maintenance log details for the component or aircraft...................................................... 98 2.19.1 Viewing maintenance log details....................................................................................................98 3 TECHNICAL RECORD MANAGEMENT................................................................................103 3.1 FLEET OVERVIEW............................................................................................................................. 105 3.1.1 Inquiring aircraft fleet.......................................................................................................................105 3.1.2 Aircraft Details section.....................................................................................................................106 3.1.3 Engine Details section.......................................................................................................................107 3.1.4 Parameter Details section................................................................................................................107 3.1.5 Due and Overdue tasks.....................................................................................................................107 3.1.6 Creating aircraft................................................................................................................................108 3.2 Managing aircraft / component records........................................................................................... 110 3.2.1 Managing aircraft / component configuration.................................................................................111 3.2.2 Managing aircraft / component program.........................................................................................114 3.2.3 Managing parameter values.............................................................................................................118 3.2.4 Managing task compliance...............................................................................................................119 3.3 Record Mode................................................................................................................................... 121 Ramco Aviation Solution 6 | Configuration Management contents 3.4 Correction & Deletion / View Mode................................................................................................. 123................................................................................................................................................................ 124 Index....................................................................................................................................................... 125 Ramco Aviation Solution 7 | Configuration Management 1 INTRODUCTION 1.1.1 INTRODUCTION Aircraft life cycle management In the aviation industry, entities for which maintenance activities have to be planned, monitored and analyzed, or for which qualitative and quantitative performance attributes need to be tracked, can be identified as one of the following types: i) Aircraft ii) Component The aircraft is the primary entity defined in the system to which components can be attached, whereas components are the building blocks for the systems in the aircraft. Induction of these maintainable entities necessitates: i) Identifying Parameters, the indicators that help in monitoring the condition or usage of the assets. ii) Defining Aircraft Model, a type or design of aircraft. iii) Defining Zones, the areas depicting the three dimensional identification of each location in the aircraft. iv) Identifying ATA chapters, the categorization of aircraft systems as identified by the Air Traffic Association. Ramco Aviation Solution 8 | Configuration Management Configuration management and control ‘Configuration’ essentially refers to the structure of an aircraft. It represents the various components present in the aircraft and the positions where these can be fitted. Aircraft are composite objects constituted by innumerable major assemblies, sub-assemblies and components. The original configuration of an aircraft or a major assembly can undergo modifications during its operating life. Adequate control over the configuration of an aircraft and component is extremely important in achieving the designed operating efficiency and reliability of the overall system. Configuration Management is the business process that aims at defining and managing configuration of maintenance assets. Aircraft & Component Configuration Management, the sub process covers the induction of the component and configuration control requirements for both aircraft as well as for components. The Technical Record Management sub process provides a centralized hub which facilitates Tech Records personnel to easily manage Technical records document information like Configuration, Program and Compliance from a single screen. This simplifies the aircraft induction process and reduces the processing time for induction and maintenance of aircraft / component records. The sub process enables the user to perform Straight Through Processing (STP) whereby user can quickly Create Part Information, Update Effectivity Information and Define Alternate Information for the part without navigating away from Technical Record interface, based on user role access rights. Ramco Aviation Solution 9 | Configuration Management 2 AIRCRAFT & COMPONENT CONFIGURATION MANAGEMENT The airline industry is characterized by the prevalence of a large number of similar maintainable assets – large fleets of identical aircraft (model and make), and similar components, which can be interchanged across models. ‘Configuration’ essentially refers to the structure of an aircraft. It represents the various components present in the aircraft and the positions where these can be fitted. The configuration control and management process enable you to i) Induct an aircraft and all its sub-assemblies or components ii) Build up respective configurations and approve them iii) Revise the approved configurations Aircraft business component enables you to define aircraft and its components in the organization. Also, the various entities associated to the aircraft and components such as ATA chapters, Zones and Parameters can be identified. Configuration business component enables you to define configuration for the aviation assets such as aircraft and components. It also aids in defining position-based rules for the part numbers and identifying MEL or CDL items for configuration. Ramco Aviation Solution 10 | Configuration Management 2.1 SETTING UP COMMON MASTERS FOR AIRCRAFT AND COMPONENT CONFIGURATION MANAGEMENT Regulatory authorities are statutory bodies responsible for the laying down, implementing and monitoring of standards regarding airworthiness of the aircraft, safety operations of the aircraft, certification of air operators and formulation of aviation legislation. The “Common Master” business component allows you to define regulatory authorities, which can be associated to the aircraft. 2.1.1 Defining regulatory authority codes 1. Select Create Regulatory Authority Codes under Common Master business component. 2. Provide a unique code for the Regulatory Authority and Description. 3. Furnish the Address and Country details. 4. Click Create Reg. Auth. Record pushbutton Ramco Aviation Solution 11 | Configuration Management 2.2 DEFINING AIRCRAFT ENTITIES You can create the various entities associated with aircraft such as aircraft model, manufacturer, zones and ATA chapters. In addition to this, you can define various parameters that help in monitoring the life of aircraft and components. The various possible values that a parameter can assume, is also identified during parameter definition. 2.2.1 Defining quick codes Quick codes act as additional qualifiers for a business entity or document. Quick codes can assume user provided values, which can be used to categorize or group an entity or document. You can define quick codes to satisfy your organization’s specific needs, especially with respect to unique characteristics of aircraft or components. For example, the usage of aircraft can be categorized as “Passenger”, “Cargo” and “Combi” etc. These categories are called Quick Codes. Similarly, you can categorize aircraft, model, aircraft group, manufacturer and other aircraft and component details. These quick codes are typically useful in viewing summary details and report generation. 1. Select Create Quick Codes under Aircraft business component. The Create Quick Codes page appears. See Figure 2. 1. Figure 2.1 Creating aircraft quick codes 2. Use the Quick Code Type drop-down list box to select the type of quick code to be created. You can define quick codes of the type “Aircraft Group category”, “Aircraft Type”, “Aircraft Status”, “Model Type”, “Usage Type”, "Aircraft Details - 1", "Aircraft Details - 2", "Component Details - 1", "Component Details - 2", "Component Details - 3", “Manufacturer Category”, “Mod Category”, “Mod Classification”, “Lower Landing Minimum” and “User Status”. 3. Enter unique quick codes for the selected type, in the Quick Code field in the multiline. 4. Enter the Description for the quick code. 5. Click the Create Quick Codes pushbutton. Note: The system assigns the "Active" status to the quick codes entered in the multiline. 2.2.2 Creating manufacturer You can define the details of the manufacturer of the aircraft and components. The manufacturer can also be defined in “Supplier” business component. 1. Select Create Manufacturer Information under Aircraft business component. The Create Manufacturer Information page appears. See Figure 2. 2. Ramco Aviation Solution 12 | Configuration Management Figure 2.2 Creating manufacturer information 2. Provide a unique identifier for the manufacturer in the Manufacturer # field. 3. Enter Manufacturer Name. 4. Enter SPEC 2000 Code assigned to the manufacturer. 5. Select the category of the manufacturer from the Manufacturer Category drop-down list box. 6. Enter the contact details such as address, phone number of the registered office and website of the manufacturer in the Address, Phone # and URL fields. 7. Enter Contact Person, Work Phone and Email fields to specify the name, phone number and email address of the contact person. 8. Enter the contact details of the manufacturer which includes Address, City, State, Country and Zip Code. 9. Enter Phone #, URL, Contact Person, Work Phone and Email of the contact person. 10. Click Create Manufacturer Information pushbutton. 2.2.3 Creating parameters There are certain attributes for each of the maintainable entity, which help in monitoring its condition or usage. These attributes, which can be either quantitative or qualitative, are defined as parameters and identified through a unique code. The parameter(s) can be associated to aircraft or components. The parameters can be of type “Consumption”, “Range”, “Technical” or “Attribute”. 1. Select Create Parameters under Aircraft business component. The Create Parameters page appears. See Figure 2. 3. Select the unit of Select this link to define measurement for the the parameter values for parameter attribute parameters Figure 2.3 Creating parameters 2. Provide a unique identifier for the parameter in the Parameter field. 3. Use Parameter Type drop-down list box to select the type of the parameter, which could be “Attribute”, “Consumption”, “Range” or “Technical”. 4. Enter the Parameter Description. Ramco Aviation Solution 13 | Configuration Management 5. Enter the formula to be associated to the ‘consumption’ or ‘range’ parameter in the Formula # field. For more details, refer “Formula Builder” Online Help. 6. Select the Unit of Measurement for the parameter. 7. Specify the Time Display Option as ‘Decimal Format’ or ‘HHMM Format’. 8. Click Create Parameter pushbutton. To enter values for the parameter of type “Attribute”, Select Edit Attribute Parameter Values link. Specifying values for attribute parameter You can identify the various values that an “Attribute” parameter takes. 1. Select Edit Attribute Parameter Values link in the Create Parameters page or Edit Parameter page. The Edit Attribute Parameter Value page appears. See Figure 2. 4. Figure 2.4 Entering values for an attribute parameter 2. Enter the value for the attribute parameter in the Parameter Value field. 3. Click the Edit Attribute Parameter Value pushbutton. 2.2.4 Setting base parameters The system displays the base parameters such as flying hours, flying cycles, block hours, landing cycles, engine hours, engine cycles, APU hours, APU cycles, aircraft weight, aircraft moment and position formula by default. You can associate the equivalent parameter defined in the system to each of these predefined parameters, so that the present value of the parameters is suitably updated. For example, if the parameter for Flight Hour is defined as FH in the “Create Parameters” page, then FH should be specified as parameter for the Base parameter Flight Hours. 1. Select Set Base Parameters under Aircraft business component. Set Base Parameters page appears. See Figure 2. 5. Ramco Aviation Solution 14 | Configuration Management Select this link to identify parameters that will inherit base parameter Figure 2.5 Setting base parameters The system lists all the base parameters in the multiline. 2. Enter the Parameter code that you wish to associate to the base parameter. For more details on base parameters setting, refer “Aircraft” Online Help. Note: The parameter type of base parameters is commonly set to “Consumption”. However, an exception to this are base parameters “Aircraft Weight”, , “Aircraft Moment”, “Oil Consumption Rate” and “Fuel Consumption/Hour”, which can also be of type “Range” or “Technical”. 3. Click Set Base Parameters pushbutton. To provide further information, Select Identify Inheritable Parameters link to identify the inheritable parameters. Identifying inheritable parameters Inheritable parameters are the parameters that that must be updated during parameter value update. 1. Select Identify Inheritable Parameters link in the Set Base Parameters page. 2. Enter the Parameter that will be inherited or updated during parameter value update. The parameter value update takes place when the flight log gets updated. 3. Click Update Parameter List pushbutton. 2.2.5 Creating formula for consumption and range parameters A formula is an independent entity that can be associated to dependent quantitative parameters. The formula contains the participating parameters and the relationship between them specified in the form of mathematical expressions. 1. Select Create Formula under Formula Builder business component. The Create Formula page appears. See Figure 2. 6. Ramco Aviation Solution 15 | Configuration Management The consumption and range parameters defined in the system Figure 2.6 Creating formula 2. Provide a unique identifier for the formula in the Formula # field. 3. Enter the Description for the formula. 4. Enter the actual content of the formula in the Formula Content field. 5. Select the relevant parameter from the Parameter Details multiline. 6. Click Transfer Parameter pushbutton to transfer the selected parameter to the Formula Content field. 7. Click Create Formula pushbutton. Ramco Aviation Solution 16 | Configuration Management 2.2.6 Creating aircraft model The aircraft model provides for the definition of the aircraft models present with the operator. You can define an aircraft model and associate aircraft to it. 1. Select Create Aircraft Model under Aircraft business component. The Create Aircraft Model page appears. See Figure 2. 7. Select the Aircraft Model to copy aircraft model details Figure 2.7 Creating aircraft model 2. Provide a unique number for the aircraft model in the Aircraft Model # field. 3. Enter Description for aircraft model. 4. Use Model Type drop-down list box to select the type of the aircraft model. 5. Enter Manufacturer # field. 6. Enter the type certificate number given for the aircraft model in the Type Certificate # field. To copy the aircraft model details 7. Use the Aircraft Model # drop-down list box to specify the aircraft model from which the details must be copied. 8. Select an appropriate option in the Copy Options drop-down list box, to copy the zone, work area, access panel, parameter or the entire details of the aircraft model. 9. Click the Create Aircraft Model pushbutton. To provide further information for aircraft model Select Edit Aircraft Model link at the bottom of the page to edit the aircraft model details. Select Edit Technical & Attribute Parameters link to define the technical and attribute parameter details for aircraft model. Select Edit Consumption & Range Parameters link to define the consumption and range parameter details for aircraft model. Defining technical and attribute parameters for aircraft model You can define different types of parameters at the aircraft model level, which will be inherited by the aircraft when they are associated to the model. Technical Parameters These parameters provide static information about the maintainable entity like the make, power rating, capacity, weight, dimensions, etc. These parameters primarily describe the specifications of the aircraft or component. Ramco Aviation Solution 17 | Configuration Management 2.2.7 Attribute Parameters Qualitative attributes, which take values from a pre-defined set, are identified as ‘Attribute Parameters’. For example, the color of the engine oil might be clear, brown or black. 1. Select Edit Technical & Attribute Parameters link in the Create Aircraft Model page. See Figure 2. 8. For an attribute parameter, this value must be already defined in the system Figure 2.8 Defining technical and attribute parameters for aircraft model 2. Enter the technical or attribute parameter that you wish to associate to the aircraft model, in the Parameter field. 3. Select the source of parameter inheritance from the Parameter Source drop-down list box. The parameter source could be “Calculated”, “Flight Log”, “Manual” or “Parent”. For more details, refer the “Aircraft” Online Help. 4. Specify the Value of the parameter. 5. Click the Edit Parameters pushbutton. Defining consumption and range parameters for aircraft model You can define consumption and range parameters for an aircraft model. Consumption Parameters: These are the attributes of an aircraft/component that increase in value on usage. Attributes like the flight hours and flight cycles fall under this type. Planned maintenance activities are triggered based on the values of these parameters. The life of an aircraft/component can also be expressed in terms of one or more consumption parameters. Range Parameters: These are parameters whose value falls in a specified range. Range parameter values are indicative of the entity’s condition; an actual value outside the specified range can indicate malfunctioning. 1. Select Edit Consumption & Range Parameters link in the Create Aircraft Model page. See Figure 2. 9. Figure 2.9 Defining consumption and range parameters for aircraft model 2. Enter the consumption or range parameter that you wish to associate to the aircraft model in the Ramco Aviation Solution 18 | Configuration Management Parameter field. 3. Use the Life Parameter drop-down list box and set the field to “Yes”, to set the parameter as a life parameter. Note: Life Parameter is a parameter that needs to be tracked for knowing the remaining life of a component. 4. Select the source of parameter inheritance from the Parameter Source drop-down list box. The parameter source could be “Calculated”, “Flight Log”, “Manual” or “Parent”. For more details, refer the “Aircraft” Online Help. 5. Enter the minimum and maximum range of values in the Range: From and Range: To fields for the range parameter. 6. Enter the Average Daily Utilization or Forecast Factor for the consumption parameter. Based on the average daily utilization or the forecast factor, the maintenance activity is forecasted. 7. Enter the Ultimate Life Value of the component, if you have set the consumption parameter as Life Parameter. 8. Enter the formula to be associated to the consumption parameter in the Formula # field. 9. Use the Warranty Tracking drop-down list box to specify whether the warranty tracking on the aircraft is based on this parameter value. 10. Specify whether the parameter update is mandatory or not, by selecting the appropriate option from the Parameter Update drop-down list box. 11. Select the parameter update mode from Update Mode drop-down list box, which could be “Delta” or “New”. 12. Click the Edit Parameters pushbutton. 2.2.8 Creating zones You can define various zones of the aircraft, which depicts the three-dimensional identification of each location in the aircraft. The zones help in locating a specific component which might have several instances of it attached in different parts of the aircraft. 1. Select Create Zones under Aircraft business component. The Create Zones page appears. See Figure 2. 10. 2. Use the Aircraft Model # drop-down list box to select the aircraft model to which the zone belongs. Figure 2.10 Creating zones 3. Provide a unique number for the zone in the Zone # field. 4. Enter Description for zone. 5. Enter Category field to categorize the zone. 6. Click the Create Zones pushbutton. Ramco Aviation Solution 19 | Configuration Management 2.2.9 Creating ATA chapter The Air Transport Authority chapter numbers define and describe the systems in the aircraft. ATA grouping of part numbers helps in easy trouble shooting as well as system-wise reliability analysis. 1. Select Create ATA Chapter under Aircraft business component. The Create ATA Chapter page appears. See Figure 2. 11. Figure 2.11 Creating ATA chapters 2. Provide a unique number for the ATA chapter in the ATA # field. 3. Enter Chapter Description. 4. Click the Create ATA Chapters pushbutton. Maintaining manufacturer ATA details 1. Select Edit ATA Chapter under Aircraft business component. Select Maintain Manufacturer ATA# Details link in the Edit ATA Chapter page. The Maintain Manufacturer ATA# Details page appears. See Figure 2. 12. The code identifying the manufacturer’s ATA code The code identifying the aircraft manufacturer Figure 2.12 Maintaining manufacturer ATA details 2. In the Manufacturer ATA# Details group box, enter the Manufacturer #, Manufacturer ATA #, Manufacturer ATA Chapter Description, Status and Remarks fields 2.2.10 Managing Cabin Configuration This activity enables tracking of the entire cabin configuration which includes all the items associated within an aircraft cabin, the seats, doors, galleys and passenger facilities, equipment like the Inflight entertainment system, oxygen tanks and so on. As such this activity enables the tracking of defects or discrepancies occurring inside the aircraft cabin and provides a visual model to aide in management of such defects/discrepancies. 1. You can record comprehensive configuration details of cabin sections for a specific aircraft or an aircraft model. For an aircraft model, cabin configuration is defined for Config. Class and Maint. Operator # combination. For an aircraft, if cabin configuration is not available, the system derives the same from the model of the aircraft. If no maintenance operator is tagged to the aircraft, the cabin configuration is derived from that of the aircraft model and Config. Class. Ramco Aviation Solution 20 | Configuration Management 2. Select Manage Cabin Configuration activity under the Configuration business component. The Manage Cabin Configuration page appears. See Figure 2. 13. Figure 2.13 Managing cabin configuration 3. Use the Cabin Layout for drop-down list box to indicate whether you wish to record the configuration details for an aircraft model or a specific aircraft. The drop-down list box displays the following: Aircraft Model # or Aircraft Reg. #. 4. If you have selected Aircraft Model # in the Cabin Layout for drop-down list box, enter Aircraft Model #, Configuration Class and Maint. Operator # to retrieve the specific model. 5. If you have selected Aircraft Reg. # in the Cabin Layout for drop-down list box, enter Aircraft Reg. # for the specific aircraft: 6. In the Aircraft Details group box, enter the Aircraft Model #, Configuration Class and Customer for whom the aircraft is flying and click the Get Details pushbutton. 7. In the Deck Details group box, specify whether the cabin is defined in two different sections in the Double Deck? drop down list box. From the Deck drop down list box specify whether you wish to define configuration for the main or upper deck and enter the number of column of seats required in the Max Column Layout field. 8. In the Cabin Sections multiline, enter Section Name and Section Description. 9. Use the Section Class drop-down list box to select the class to which the section belongs. 10. Use the Seat Section? drop-down list box to indicate whether the section comprises of only seats. The drop-down list box displays the following: Yes or No. Select: Yes, if the section has only seats; and No, if the section has both seats and equipment/gadget 11. Enter Column Layout and Row Count. Note: It is mandatory that you enter a positive integer, if Seat Section? is ‘Yes’ in both the above- mentioned fields. Do not enter a value in this field, if Seat Section? is ‘No’. 12. Enter Starting Row # and Ending Row # for the section. Note: It is mandatory that you enter a positive integer, if Seat Section? is ‘Yes’ in both the above- mentioned fields. Do not enter a value in this field, if Seat Section? is ‘No’. 13. Enter Seq # of the section in the cabin. 14. Enter Non-Seat Count. Ramco Aviation Solution 21 | Configuration Management Note: This field is mandatory, if “Seat Section?” is selected as Yes. 15. Enter Unique identifiers for the non-seat item. 16. Use the Has Exit? drop-down list box to indicate whether an exit is present in the section. 17. Click the Save pushbutton to save cabin configuration details for the given Aircraft Model – Configuration – Customer combination. To map cabin configuration, Select the Map Cabin Configuration link at the bottom of the page to map cabin configurations. 2.2.11 Mapping Cabin Configuration This activity enables you to map the defined sections based on their set up configurations to their positions in the aircraft. 1. Select the Map Cabin Configuration link at the bottom of the Manage Cabin Configuration activity under the Configuration business component See Figure 2. 14. Figure 2.14 Mapping cabin configuration 2. In the Cabin Details, select the item for which position is to be mapped from the Cabin Item drop- down list box. 3. In the multiline, enter the Standard Part # for which configuration is not tracked and provide the other details. 4. Use the Equipment Category drop-down list box to select the category of the equipment that can be attached to the cabin position #. 5. Select the Save pushbutton to save mapping of the sections and the items to the aircraft configuration. 2.2.12 Maintaining Cabin equipment This activity enables you to specify and categorize equipment categories and cabin equipment under specific equipment group, such as In-Flight Entertainment (IFE) and Global Communication Satellite (GCS). An equipment category typically identifies the version or model or brand of cabin equipment (such as Monitor, Harness Assembly, ADB, ADB Ports, Wi-Fi, File Servers) that is attached to a designated position code in the cabin layout of an aircraft. Cabin equipment are attached to the designated cabin positions in accordance with the cabin layout defined for an aircraft model / aircraft. 1. Select Maintain Cabin Equipment List activity under the Configuration business component. The Maintain Cabin Equipment List page appears. See Figure 2. 15. Ramco Aviation Solution 22 | Configuration Management Figure 2.15 Maintaining Equipment Category 2. Use the Equipment Group drop-down list box to select the equipment group to which you want to tag the cabin equipment / equipment category. The drop-down list box displays the Active quick codes defined under the quick code type “Equipment Group” in the Create Quick Code activity of Aircraft. In addition, the drop-down list box also displays “Not Applicable”. You can select “Not Applicable”, if you do not wish to associate a cabin equipment / equipment category to any equipment group. However, if no equipment group has been defined in Active status, the drop-down list box the only option: “Not Applicable”. 3. Select the Equipment Category List tab to associate equipment categories to the selected equipment group. See Figure 2.13. 4. Enter Equip. Category Code and Equip. Category Desc. 5. Use the Status drop-down list box to indicate whether the equipment category is Active or Inactive. 6. Select the Cabin Equipment List tab to associate cabin equipment to the selected equipment group. See Figure 2. 16 Figure 2.16 Maintaining Cabin Equipment list 7. Enter Cabin Equipment and Cabin Equipment Desc. 8. Use the Status drop-down list box to indicate whether the cabin equipment is Active or Inactive. 9. Select the Save pushbutton to save the details. Ramco Aviation Solution 23 | Configuration Management 2.3 Defining configuration entities The key data entities such as configuration class and deferral category can be defined in the system before venturing into the configuration building. 2.3.1 Creating configuration class Configuration class is the code that denotes a particular type of configuration or structure of the aircraft. A configuration class can be associated to entities like aircraft models and aircraft registration numbers. Configuration Class and Aircraft Model number is a unique identifier for the aircraft configuration. Multiple configuration classes can be associated to an Aircraft Model, but at any point of time only one Configuration Class or Model combination can be associated to an aircraft registration number. 1. Select Create Configuration Class under Configuration business component. The Create Configuration Class page appears. See Figure 2. 17. Select the type of Select the type of usage of landing gear for the the aircraft, attached to the configuration class configuration class Any user-defined detail regarding configuration class Figure 2.17 Creating configuration class 2. Provide a unique identifier for the Configuration Class and Description. 3. Check ETOP box to apply ETOP configuration for the configuration class. For more details, refer “Configuration” Online Help. Note: The aircraft associated to this configuration class will inherit ETOP configuration if this box is checked. To define Configuration Class Attributes 4. Select appropriate aircraft group from Aircraft Group # drop-down list box to associate to the configuration class. Note: The system leaves this field blank, by default. 5. Use the Aircraft Type drop-down list box to specify the type of the aircraft, which you wish to attach to the configuration class. Note: The system leaves this field blank, by default. 6. Enter the No. of Engines, No. of APUs and Maint. Operator #, you wish to define for the configuration class. To define model effectivity for configuration class, 7. In the Model Effectivity Details multiline, enter the Aircraft Model # field to specify the aircraft model number for which the configuration class is applicable. Ramco Aviation Solution 24 | Configuration Management 8. Click Create Configuration Class pushbutton. 2.3.2 Creating deferral category All MEL/CDL items are deferred based on certain norms set by the aviation authority. Deferral category defines the deferment limits of the MEL/CDL items and the parameters on which it depends. An MEL/CDL item is associated to a deferral category, and it derives its deferment schedule from that of the deferral category. 1. Select Create Deferral Category under Configuration business component. The Create deferral Category page appears. See Figure 2. 18. 2. Provide a unique identifier for the Deferral Category and Deferral Category Desc. 3. Select the type of deferral limit associated to deferral category, from the Limit Type drop-down list box. The limit types could be “Infinite”, “Time Limited”, “Usage Limited” or “Time and Usage Limited”. For more details, refer “Configuration” Online Help. 4. Select the Limit Basis for the time and usage based deferral. The options are “Whichever is earlier” and “Whichever is later”. Note: Leave this field blank, if the “Limit Type” is “Time Limited” or “Usage Limited”. The duration for which the MEL item number can be deferred The parameters based on which the MEL item number will be deferred Figure 2.18 Creating deferral category 5. Enter the duration or period for which the MEL/CDL item number can be deferred, in the Deferral Duration field. Note: Leave this field blank, if the “Limit Type” field is set to “Usage Limited”. 6. Enter the value of the parameter based on which the MEL/CDL item number is deferred, in the Deferral Limits field in the multiline. Note: Leave this field blank, if the “Limit Type” field is set to “Time Limited. 7. Click the Create Deferral Category pushbutton. Ramco Aviation Solution 25 | Configuration Management 2.4 Managing effectivity of parts Effectivity of a part is set for aircraft model/aircraft/part/component. Effectivity defines the compatibility of a part for an aircraft/component. To make a part effective to all aircraft models/aircraft/parts/components, do not define effectivity for the part in this activity You can set the effectivity of a part by choosing one of the following statuses as explained below: Effective: You can make a part suitable for an aircraft model/aircraft/part/component by setting its Effectivity Status to “Effective”. When a part is made effective for an aircraft model, it implies that the part is compatible for all the aircraft of the aircraft model. It also means that the part is incompatible for all other models of aircraft. You can also make a part effective for a specific aircraft, which means the part is not suitable for any other aircraft. Similarly, if you make a part effective for a NHA (parent) part/component, the system automatically makes all other parts/ components unsuitable for the part. Conditional Effective: You may make a part effective for an aircraft model/aircraft/part/component under certain flying conditions or for specific maintenance/usage parameters. This is achieved when you set Effectivity Status to “Conditional Effective”. This makes the part incompatible to other aircraft models/aircraft/parts/components. Not Effective: You make a part invalid for an aircraft model/aircraft/part/component when you set the Effectivity Status to “Not Effective”. This makes the part effective to all other aircraft model/aircraft/part/component. The effectivity definition that you define in this activity forms the basis for attachment of parts during component replacement and aircraft maintenance 1. Select the Manage Part Effectivity link under the Aircraft business component. The Manage Part Effectivity page appears. See Figure 2. 19. Note: In this page, the Part # and related fields are displayed or available for input only if the “Enable Manufacturer Part # control in transaction" parameter is set to ”No” in the Set Inventory Process Parameters activity of the Logistics Common Master component. Conversely, the Mfr. Part # and Mfr. # related fields are displayed/available for input only if the “Enable Manufacturer Part # control in transaction" parameter is set to ”Yes” in the Logistics Common Master' business component, in the Set Inventory Process Parameters activity of the Logistics Common Master component.. Enter the following in the Search Criteria group box: 2. Use the Search Entity drop-down list box the entity for which you want to record the effectivity details. Enter the following in the Default Details group box: 3. Use the Effectivity Status drop-down list box to indicate effectivity status of part. 4. Use the Effectivity Level drop-down list box to specify the effectivity level of the part. The system lists the values “Direct” and “Alternate” 5. Specify any additional information on the effectivity or suitability of the part to aircraft or component in the Effectivity Notes field. Ramco Aviation Solution 26 | Configuration Management Figure 2.19 Managing part effectivity Enter the following in the Effectivity Details multiline. 6. Use the Job Type drop-down list box to specify the job type. The system lists the values “Aircraft”, “Component” and “Others” 7. Specify the Part # for which you want to record effectivity details. 8. Use the Effectivity Level drop-down list box to specify the effectivity level of the part. 9. Enter Primary Part # of the effective part. 10. Use the Effectivity Rule drop-down list box to specify the effectivity rule of the part. The drop-down system lists the values “One Way” and “Two Way”. 11. Use the Effectivity Status drop-down list box to indicate the effectivity of the part. 12. Enter Aircraft Model # and Aircraft Reg # for which the part is effective. 13. The NHA Part # and NHA Serial # for which the part is effective. Note: You must specify Aircraft Model # and/or Aircraft Reg. # or NHA Part # and/or Serial #. However, if you have entered the serial #, you must also specify the part #. 14. Enter Effectivity Notes, if the Effectivity Status is set to “Conditional Effective”. 15. The Ref. Doc. Type, the Ref. Doc. # and the Ref. Doc. Rev # of the document that affirms the effectivity or suitability of the part to aircraft or component. 16. Click the Update Effectivity pushbutton to save effectivity details. Ramco Aviation Solution 27 | Configuration Management 2.5 Managing Recommended Spare Parts List In the aviation industry, OEMs will provide the list of spare parts that has to be maintained at Aircraft Model level. Based on the recommended spare parts list provided by OEM, the inventory float gets computed. In this activity, recommended spare Part List for a given Aircraft Model can be defined and maintained. This activity also maintains the Aircraft Models for which a part serves as the spare along with additional RSPL Information. 1. Select Manage Recommended Spare Parts List activity under Aircraft business component. The Manage Recommended Spare Parts List screen appears. See Figure 2. 20. Mean time between unscheduled removals for the part Figure 2.20 Managing Recommended Spare Parts List 2. Enter the A/C Model # for which the spare parts are to be defined. 3. Use the RSPL Rev. # drop-down list box to specify the revision number of the RSPL document. The system lists all the available revisions for the specified Aircraft Model. In the “Spare Parts List” multiline, 4. Enter the Part # and specify the Part Classification of the spare part for the Aircraft Model. 5. Use the Essentiality Code drop-down list box to specify whether the aircraft is permitted to fly with or without the spare part specified by the OEM. The system lists the following values: No-Go - Indicates that the aircraft can fly without the spare part for a limited period, without any specific conditions. Go-If - Indicates that the aircraft can fly without the spare part for a limited period, with specific conditions. Go - Indicates that the aircraft cannot fly without the spare part. 6. Enter the MTBUR and Unit of the Mean Time Between Unscheduled Removals for the spare part #. 7. Enter the Mean Shop Processing Time and MSPT UOM for the spare part #. 8. Enter the QPA to specify the spare part per aircraft and the UOM of QPA. 9. Use the BFE drop-down list box to specify whether the spare part is Buyer Furnished Equipment. 10. Use the Power Plant Part? drop-down list box to specify whether the spare part is power plant part (Engine). 11. Enter the NHA Part # to specify the parent part effective for the spare part and the Qty / NHA. 12. Use the Source Doc. Type to specify the type of source document. The system lists the following values: Ramco Aviation Solution 28 | Configuration Management IPC - Indicates that the source document is an Illustrated Parts catalogue. Eng. Doc – Indicates that the source document is an Engineering Document. Others – Indicates that the source document could be any document other than “IPC” and “Eng. Doc". 13. Enter the Part Description, Part Type and Part Planning Group of the spare part. 14. Click the Save pushbutton to save the entered details. The system generates the Recommended Spare Parts List in ‘Fresh’ status with Revision # as 0. If the details are already available in ‘Active’ status, the system generates Revision # by incrementing 1 value if any value is modified / deleted and latest revision # will be in ‘Fresh’ status. The old revision #s status will be updated as ‘Revised’. 15. Click the Confirm pushbutton to confirm the recommended Spare Parts List. The system updates the status of RSPL Revision # for Aircraft Model # as ‘Active’. To proceed, carry out the following Select the Maintain Alternate Part Nos link at the bottom of the screen to update the alternate part numbers for the spare part. Select the Upload Documents link at the bottom of the screen to upload the associated documents. Select the View Associated Doc. Attachments link at the bottom of the screen to view the associated documents. Ramco Aviation Solution 29 | Configuration Management 2.6 Building model and part configuration Building configuration essentially involves defining the position codes and identifying sub- assemblies, components and piece parts for the maintainable entity. You can define Generic configuration for an aircraft model or part number, which can be inherited across associated aircraft or components. Entity specific configuration, which enables the tracking of aircraft or component specific variations from the generic structure. As a part of the configuration definition, you can identify various position codes in which the parts can be fitted, categorize positions, define the interchangeability rules and identify MEL and CDL list for the aircraft model. The following sections give you a bird’s eye view of the configuration definition and management process. 2.6.1 Building aircraft model configuration The first level of the configuration is defined as the Model Configuration. The position based configuration rules like part interchangeability rules, part intermixing rules and ETOP twin positions can be defined for the model configuration. Also the MEL and CDL items are identified for the aircraft model. You can build aircraft model configuration, which can be inherited to the associated aircrafts. 1. Select Build Model Configuration under Configuration business component. The Select Model page appears. 2. Provide filter criteria to search for Aircraft Model # for building model configuration. 3. Select Build Model Configuration link to define configuration details for the selected aircraft model. The Build Model Configuration page appears. See Figure 2. 21. 4. Use the Config. Status drop-down list box to set the status of the model configuration.. The system lists the following: Fresh – When the model configuration is created or modified. Cancel – When the model configuration is cancelled. Select this option if you wish to disable this model configuration from future reference in other activities. 5. Use the Config. Control Basis drop-down list box to indicate the basis for attaching a part to the aircraft of the aircraft model during maintenance. The drop-down list displays the following: Part Effectivity and Config. Rules. If you select; Config. Rules, the system allows you to attach only those parts to the position code that satisfy specific configuration rules (interchangeability, intermixing, ETOPS Twin position and permitted serial #) as well as the condition set for the Part Effectivity option as explained next. Part Effectivity, the system allows you to attach only those parts that are effective for the aircraft model to the position code. (Note that the part effectivity must be pre-defined in the Maintain Part Effectivity page.) 6. Enter the Seq # for the position code. 7. Specify Datum Point that is the origin point or an imaginary point in the aircraft model from which the distance of the component / part is calculated. Enter Position Code field to identify the position of the part number in the model configuration. 8. Specify Arm that is the length between the Datum point and the component/part in the aircraft model. 9. Set the status of position code in Position Code Status field. You can activate or inactivate the position code by assigning “Active” or “Inactive” status. 10. Enter the part number to be associated to the model configuration in the Part # field. Ramco Aviation Solution 30 | Configuration Management 11. Select the type of the position code from the Position Type field, which could be “APU”, “Engine”, “Landing Gear” or “Others”. 12. Use the Component Mandatory drop-down list box to indicate whether a component must be fitted to the position code or not. 13. Use the Weight Mandatory drop-down list box to indicate whether the component/part attached at the position code to be considered for Weight & Balance analysis of the aircraft model. 14. Set the Cargo drop-down list box to “Yes” to indicate that the part can be used in the cargo aircraft. 15. Set the RVSM drop-down list box to “Yes” to indicate that the part can be used in the aircraft, which fly in the Reduced Vertical Separation Minimum limit. For more details, refer “Configuration” Online Help. 16. Enter Zone #, Position Formula #, ATA # fields to specify the zone, position formula and ATA chapter details for the position code. 17. Use the Equipment Category drop-down list box to select the category of the equipment that can be attached to the position code in the aircraft of the selected model. 18. Specify the drawing details of the part by entering Drawing # and File Name fields in the multiline. To copy model configuration details The status of the model configuration Click the Re-Number pushbutton to rearrange the existing rows in the ascending order of the sequence number. The type of the position code to which the part is fitted Check this box to apply model configuration changes to aircraft configuration Figure 2.21 Building model configuration 19. Enter the remarks of the configuration in the Remarks field. 20. Click the Build Model Configuration pushbutton. To provide further details for model configuration, Select Edit Conf 46iguration Deviation List link to identify the configuration deviation list for model configuration. Select Edit Minimum Equipment List link to identify the minimum equipment list for model configuration. Select Edit Piece Part List for Model link to identify the piece part list for model configuration. Select Edit Notes link to enter notes for model configuration. Ramco Aviation Solution 31 | Configuration Management Select Edit Configuration Rules link to define model configuration rules. Select Build Part Configuration link to build part configuration. Defining model configuration rules You can define rules for the position codes to govern the part numbers that can be fitted to it, the relationship of the position codes and the part numbers associated to it across the model configuration. 1. Select Edit Configuration Rules link in the Build Model Configuration page. The Edit Position Attributes page appears. See Figure 2. 22. 2. Provide filter criteria in Display Filter group box, to define configuration rules for the position code for the aircraft model. 3. The system displays the aircraft configuration details in the form of a tree structure. Enter filter criteria to retrieve the position codes for defining configuration rules Indicates the level of configuration Figure 2.22 Defining model configuration rules 4. Set the Cargo drop-down list box to “Yes” to indicate that the position code is in the cargo aircraft. 5. Set the RVSM drop-down list box to “Yes” to indicate that the position code is in the aircraft, which fly in the Reduced Vertical Separation Minimum limit. 6. Enter Zone #, Position Formula #, ATA # fields to specify the zone, position formula and ATA chapter details for the position code. 7. Click Edit Position Attributes pushbutton. To enter further information, Select Edit Part Intermixing Rules link to define part intermixing rules for the position code for the aircraft model. Ramco Aviation Solution 32 | Configuration Management Select Edit Part Interchangeability Rules link to define part interchangeability rules for the position code for the aircraft model. Select Edit ETOP Twin Positions link to identify ETOP twin positions for the position code for the aircraft model. Select Maintain Part Program link to modify the part program details. Select Maintain Position Based Schedules link to modify position based schedules for the part. Defining part intermixing rules for model configuration The intermixing rule defines the list of dependent position codes and the dependent part numbers for the reference position code and the reference part number. The intermixing rule states that, whenever the reference part number is fitted in the reference position code, the dependent position codes must have the associated dependent part numbers fitted in them. 1. Select Edit Part Intermixing Rules link in the Edit Position Attributes page. The Edit Part Intermixing Rules page appears. See Figure 2. 23. The reference position code The reference part number The position code of the part, that is Indicate whether the intermixing dependent on the reference The part number that must be fitted rule is reversible or not position code and reference part to the dependent position code, number when the reference part number is fitted to the reference position code. Figure 2.23 Defining part intermixing rules for model configuration 2. Select the Reference Part # for whose position code, the dependent position codes must be defined. 3. Click the Get Details pushbutton to retrieve the intermixing part details that are already defined for the reference part number. 4. Enter Dependent Position Code and Dependent Part # fields. 5. Click the Edit Part Intermixing Rules pushbutton. Defining part interchangeability rules for model configuration The parts interchangeability rule defines the list of alternate part numbers that can be placed in the reference position code, in place of the reference part number, if the reference part number is not available. 1. Select Edit Part Interchangeability Rules link in the Edit Position Attributes page. The Edit Part Interchangeability Rules page appears. See Figure 2. 24. Ramco Aviation Solution 33 | Configuration Management The reference position code The reference part number The part that can be fitted in place of the reference part number, to the reference position code Figure 2.24 Defining part interchangeability rules for model configuration 2. Enter Interchangeable Part # field. 3. Enter Order of Preference, the preferred order in which the interchangeable part must be considered for fitting in the reference position code. 4. Click Edit Part Interchangeability Rules pushbutton. To proceed, Select View Alternate Part No link to view the alternate part details for the interchangeable part. Identifying ETOP twin positions for parts in model configuration ETOP twin position codes are the position codes that are parallel to a reference position code. This rule restricts any maintenance activity being carried out simultaneously in the reference position code and the twin position code. This is required to govern the reliability of aircraft while performing ETOP. 1. Select Edit ETOP Twin Positions link in the Edit Position Attributes page. The Edit ETOP Twin Positions page appears. See Figure 2. 25. The reference position code for which the twin position code must be defined The reference part number The code identifying the twin position for ETOP aircraft Figure 2.25 Defining ETOP twin position codes for model configuration 2. Enter Twin Position Code field. This is the position code that is parallel to the reference position code. For more information, refer “Configuration” Online Help. 3. Enter the part number associated to the twin position code in the Part # field. 4. Click the Edit ETOP Twin Positions pushbutton. Ramco Aviation Solution 34 | Configuration Management Identifying Configuration Deviation List for model configuration You can identify Configuration Deviation List (CDL), which is the list of secondary parts of the airframe and engine, which do not affect the flying of the aircraft. This list denotes that the aircraft can still fly without these parts, or with these parts in defective condition. 1. Select Edit Configuration Deviation List link in the Build Model Configuration page. The Edit Configuration Deviation List page appears. See Figure 2. 26. A unique number identifying the Deferral item Figure 2.26 Defining configuration deviation list for model configuration 2. Provide a unique number and description for the Deferral item in the Deferral Item # and Deferral Item Desc fields. 3. Specify the Deferral Category of the CDL item. 4. Specify the CDL Quantity, which is the quantity of part to be included in the configuration deviation list. 5. Enter minimum quantity of the CDL, in the Minimum CDL Quantity field. Minimum quantity refers to the total quantity that can be under CDL at any given point of time. 6. Set the status of CDL item to “Active” or “Inactive” in the Item Status drop-down list box. 7. Enter the task performed during the first scheduled maintenance to ensure that the deferred task is completed, in the Deferral Task # field. 8. Enter the task performed during the second scheduled maintenance to ensure that the deferred task is completed, in the Deferral Rev. Task # field. 9. State the Maintenance Procedures and Operational Procedures of flying the aircraft without the secondary part or with the secondary part in defective condition. 10. Use the Placard drop-down list box to indicate whether a placard must be posted at the location of the CDL item. The options are “Required” and “Not Required”. 11. Enter Placarding Instructions. 12. Click the Edit Configuration Deviation List pushbutton. Identifying Minimum Equipment List for model configuration You can identify Minimum Equipment List (MEL), the list of equipment approved by the aviation authority, which may remain in an unserviceable state under certain operating conditions, but still provide an acceptable level of safety in the operation of the aircraft. Ramco Aviation Solution 35 | Configuration Management 1. Select Edit Minimum Equipment List link in the Build Model Configuration page. The Edit Minimum Equipment List page appears. See Figure 2. 27. A unique number The textual identifying the description of the Deferral item Deferral item Figure 2.27 Defining minimum equipment list for model configuration 2. Enter MEL Item # and MEL Item Desc fields. 3. If the MEL item is defined as a part in the “Part Administration” business component, enter Part # field. 4. Specify the Deferral Category. 5. Set the status of MEL item to “Active” or “Inactive” in the Item Status drop-down list box. 6. Specify the MEL Quantity, which is the quantity of part to be included in the minimum equipment list. 7. Enter minimum quantity of the part that can be under MEL at any given point of time, in the Number Required field. 8. Set the Conditional? drop-down list box to “Yes” to indicate that the usage of the part in an unserviceable state is based on certain conditions. Enter Conditions. 9. Enter the task performed during the first scheduled maintenance, to rectify a deferred discrepancy which would have occurred during a maintenance activity, in the Deferral Task # field. 10. Enter the task performed during the second scheduled maintenance, in case of further deferment in the discrepancy rectification, in the Deferral Rev. Task # field. 11. State the Maintenance Procedures and Operational Procedures of flying the aircraft with the part in an unserviceable state. 12. Use the Placard drop-down list box to indicate whether a placard must be posted at the location of the MEL item. The options are “Required” and “Not Required”. Enter Placarding Instructions. 13. Click the Edit MEL pushbutton. To define position code details for MEL items, for which the MEL quantity is less than the total MEL quantity defined per aircraft, Select Edit MEL Position Details link. Ramco Aviation Solution 36 | Configuration Management Defining position details for MEL item number You can define the position code details only for a MEL item number that is ‘position based’. A MEL item becomes ‘position based’ when the MEL quantity is less than the total MEL quantity defined for the aircraft. For example, if the total MEL quantity identified for an aircraft is 5, and the MEL quantity (the MEL items that can be deferred) is 3, then the MEL item is said to be ‘position based’. You can define the position code details for the MEL items that will be deferred. 1. Select Edit MEL Position Details link in the Edit Minimum Equipment List page. The Edit MEL Position Information page appears. See Figure 2. 28. 2. Use the MEL drop-down list box and set the field to “Yes”, if you wish to include the part associated to the position code in the minimum equipment list. 3. Set the Conditional? drop-down list box to “Yes” to indicate that, the part associated to the position code can remain in an unserviceable state, based on certain conditions. Enter Conditions. 4. State the Maintenance Procedures and Operational Procedures flying the aircraft with the part placed in the position code in an unserviceable state. 5. Use the Placard drop-down list box to indicate whether a placard must be posted at the position of the part. The options are “Required” and “Not Required”. 6. Enter Placarding Instructions. The position code details for the MEL item are displayed Select “Yes” to include the part associated to the position code in the MEL Figure 2.28 Defining MEL position details for model configuration 7. Click the Edit MEL Positions pushbutton. Identifying piece part list for model configuration Among the various part numbers associated or fitted to the aircraft, certain parts are identified as piece parts. Some of these piece parts need to be tracked for various reasons such as their high value in terms of their price, warranty requirements and to identify parts that are fitted on a trial basis. You can identify the piece parts for the model configuration including the quantity per piece part. 1. Select Edit Piece Part List for Model link in the Build Model Configuration page. The Edit Piece Part List for Model page appears. See Figure 2. 29. 2. Enter the piece part number in the Piece Part # field. 3. Specify the Quantity of the piece part identified for model. Ramco Aviation Solution 37 | Configuration Management Select this link to define positions for piece part Figure 2.29 Defining piece part list for model configuration 4. Enter Zone # field to specify the zone to which the piece part belongs. 5. Indicate whether the piece part must be tracked in the Trackable field. High value pieces can be marked as trackable. 6. Enter the prefix for piece part position in the Prefix for Position # field. 7. Click the Edit Piece Parts List pushbutton. To enter position details for the piece part, Select Edit Piece Part Position Information link. Defining piece part positions for model configuration You can identify the position codes to which the piece parts must be fitted, in the model configuration. 1. Select Edit Piece Part Position Information link in the Edit Piece Part List for Model page. 2. Enter the position code to which the piece part must be fitted in the Position Number field. 3. Activate or inactivate the position code by selecting appropriate option from the Status drop-down list box. 4. Click the Edit Position Details pushbutton. 2.6.2 Building part configuration A set of identical components may be grouped into a single addressable group called “Part”. You can define the configuration details for a selected part, which can be inherited to the components associated to it. Note: The part # is available/displayed only if the Enable Manufacturer Part # control in transaction" parameter is set to ”No” in the Logistics Common Master' business component, in the Set Inventory Process Parameters activity of the Logistics Common Master component. Conversely, the manufacturer part # and manufacturer # fields are available/displayed only if the Enable Manufacturer Part # control in transaction" parameter is set to ”Yes” in the Logistics Common Master' business component, in the Set Inventory Process Parameters activity of the Logistics Common Master component. 1. Select Build Part Configuration under Configuration business component. The Select Part page appears. 2. Provide filter criteria to search for Part # for building part configuration. 3. Select the Build Part Configuration link in the Select Part page or click the hyperlinked part number in Ramco Aviation Solution 38 | Configuration Management the same page, to define configuration details. The Build Part Configuration page appears. See Figure 2. 30. 4. Enter the Part # in the Part Details group box for which you wish to create configuration or modify existing configuration details. 5. Use the Mfr. Part #/ Mfr. # drop-down list box to specify manufacturer part # and manufacturer # of the part for which you wish to create configuration or modify existing configuration details. 6. Click the Get Details pushbutton. The system displays the part configuration details in the form of a tree structure. The configuration details such as Position Code, Part #, Part Description, Part Serial # and Component ID are displayed for the part. On selection of a node in the tree structure, the system automatically retrieves the corresponding part details in the Part Details group box, and the child part details in the Next Level Details multiline. 7. Enter the Seq # of the position code. 8. Enter Position Code field to identify the position of the part number in the part configuration. 9. Set the status of position code in Position Code Status field. You can activate or inactivate the position code by assigning “Active” or “Inactive” status. 10. Enter the Part # identifying the child part to be associated to the position code Mandatory. 11. Enter the Mfr. Part # and Mfr. # of the child part to be associated to the position code. You must specify the manufacturer part # of the child part as it is mandatory. 12. Select the type of the position code from the Position Type field, which could be “APU”, “Engine”, “Landing Gear” or “Others”. 13. Set the RVSM drop-down list box to “Yes” to indicate that the part can be used in the aircraft, which fly in the Reduced Vertical Separation Minimum limit. For more details, refer “Configuration” Online Help. 14. Set the Cargo drop-down list box to “Yes” to indicate that the part can be used in the cargo aircraft. 15. Enter ATA # field to specify the ATA chapter to which the position code belongs. 16. Use the Reqd. for Test drop-down list box to specify if it is mandatory for the part to be attached to the position code for testing the component/engine. 17. Use the Equipment Category drop-down list box to select the category of the equipment that can be attached to the position code in the part. 18. Specify the drawing details of the part by entering Drawing # and File Name fields in the multiline. 19. Use the Component Mandatory drop-down list box to indicate whether a component must be fitted to the position code or not. 20. Click Previous Level and Next Level pushbuttons to traverse across configuration levels. 21. Click the Build Part Configuration pushbutton. Ramco Aviation Solution 39 | Configuration Management The part number for which the configuration must be defined The status of the part configuration Click this pushbutton to rearrange the existing rows in the ascending order of the sequence number Click these buttons to traverse across configuration levels The type of the position code to which the part is fitted Check this box to apply part configuration changes to component configuration Figure 2.30 Building part configuration To provide further details for part configuration, Select Edit Notes link to enter notes for part configuration. Select Edit Piece Part List link to identify the piece part list for part configuration. Identifying piece part list for part configuration 1. Select Edit Piece Part List link in the Build Part Configuration page. The Edit Piece Part List page appears. See Figure 2. 31. Ramco Aviation Solution 40 | Configuration Management Enter the reference part number Figure 2.31 Defining piece part list for part configuration 2. Enter the Seq # for the reference part. 3. Enter the Position # corresponding to the reference part, if Reference Part # is duplicated. 4. Enter the Reference Part # in the piece part configuration. You cannot modify the reference part. 5. Use the Reqd. for Test drop-down list box to specify if it is mandatory for the part to be attached to the position code for testing the component/engine. 6. Enter the Ref. Quantity indicating the quantity of reference parts identified for the Piece Part configuration. 7. Select the Position Type indicating the status of the position code of the reference part as ‘Others’. 8. Select the Position Status of the reference part as ‘Active’ or ‘Inactive’.2 9. Use the Equipment Category drop-down list box to select the category of the equipment that can be attached to the position code in the part. 10. Click the Re-Number pushbutton to insert Seq # in the multiline and rearrange the existing rows in the ascending order of the Seq #. 11. Click the Edit Piece Parts List pushbutton. Ramco Aviation Solution 41 | Configuration Management 2.7 Maintaining flight log parameters The flight log is created after the accomplishment of a flight by an aircraft. You can record the leg-wise parameters and oil uplift details for specific aircraft model and configuration class combinations. 1. Select Maintain Flight Log Parameters link under the Aircraft business component. The Maintain Flight Log Parameters page appears. In the Aircraft Details group box, 2. Select the Aircraft Model # for which the leg-wise parameter information is to be recorded. 3. Select the Configuration Class. 4. Click the Get Details pushbutton. 5. Select the Maintain JL Parameter Details tab. See Figure 2. 32. Enter the following details of leg wise-parameters in the multiline, 6. Enter the Position Code for which the parameter is reported. 7. Enter the Parameter reported at the specified position code. Figure 2.32 Maintaining leg-wise parameters 8. Select the Maintain Oil Uplift Details tab. See Figure 2. 33. Enter the following details of oil uplift parameters in the multiline, 9. Enter the Item #, Item Description, Item Type and Part #. 10. Enter Position Code, UOM, Maximum Capacity, Status and Mandatory? Ramco Aviation Solution 42 | Configuration Management Figure 2.33 Maintaining oil uplift parameters 11. Click the Maintain Flight Log Info. pushbutton. Ramco Aviation Solution 43 | Configuration Management 2.8 Inducting aircraft and components You can induct aircraft and components once the logical configuration of model and part are available. The induction process involves defining component, aircraft and other sub-assemblies. 2.8.1 Maintaining maintenance information for part For defining components, the part numbers of type “Component” in the inventory are identified. You can define maintenance information for the part number, which will be inherited by the components generated using the part number. You can also define maintenance activities for non-component parts in this sub-process. 1. You can specify the classification, administrative and operational details of the part along with the component ID generation mode, which could be “Auto” or “Manual”. You can also specify whether multiple maintenance tasks for a part can be consolidated and executed through a single shop work order. Select Maintain Maintenance Info. for Part under Aircraft business component. The Select Part page appears. 2. Provide filter criteria to search for a part for updating maintenance information for the part of type Component. 3. Select the Part # in the multiline. 4. Select the Edit Part Information link to update maintenance information for the part. The Maintain Maintenance Info. for Part page appears. See Figure 2. 34. To specify classification details for the part, 5. Enter the Part Model # field to specify the part model to which you wish to associate the part. 6. Click Get Details pushbutton to retrieve the details of the part model entered. 7. Select the Component Type to which the part belongs. 8. Select the appropriate option from Part Classification drop-down list box to classify the part. The part can be classified as “Controllable”, “Repairable” or “Rotable”. If the part is of type other than “Component”, th