Ceramic Lecture PDF
Document Details
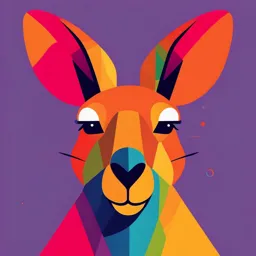
Uploaded by VivaciousVerism
Tags
Summary
This lecture provides an overview of the ceramic industry, covering various aspects of ceramic manufacturing, chemistry, and applications. It discusses the historical context, bonding, structures, and manufacturing techniques. It further touches upon advanced ceramics use in different domains.
Full Transcript
1 The ceramic industry is a vast and multifaceted field that combines elements of chemistry, material science, and engineering to produce a wide range of products with applications in various sectors, including construction, electronics,...
1 The ceramic industry is a vast and multifaceted field that combines elements of chemistry, material science, and engineering to produce a wide range of products with applications in various sectors, including construction, electronics, healthcare, and consumer goods. This article delves into the manufacturing processes, the underlying chemistry, and the significant developments within the ceramic industry. Introduction to Ceramics Ceramics are non-metallic, inorganic materials that are typically crystalline in nature. They are composed of metal and non-metal elements bonded together by ionic and covalent bonds. The term “ceramic” encompasses a broad category of materials, including traditional ceramics like pottery and bricks, as well as advanced ceramics used in cutting-edge technologies. Historical Perspective The use of ceramics dates back thousands of years, with early human civilizations using clay to create pottery, tiles, and other functional items. The development of high-temperature kilns and the discovery of glazing techniques were significant milestones that expanded the utility and aesthetic appeal of ceramic products. Over time, advancements in materials science and engineering have led to the development of advanced ceramics with superior properties, including high strength, thermal resistance, and electrical conductivity. Chemistry of Ceramics The chemistry of ceramics is fundamental to understanding their properties and manufacturing processes. Ceramics are primarily composed of oxides, carbides, nitrides, and borides. Common ceramic materials include alumina (Al₂O₃), zirconia (ZrO₂), silicon carbide (SiC), and silicon nitride (Si₃N₄). Bonding in Ceramics Ceramic materials are characterized by strong ionic and covalent bonds. In ionic ceramics, such as alumina, there is a transfer of electrons from metal atoms to non-metal atoms, resulting in positive and negative ions. This ionic bonding gives ceramics their high melting points and hardness. In covalent ceramics, such as silicon carbide, atoms share electrons, leading to strong directional bonds that contribute to high stiffness and thermal stability. Crystal Structure The properties of ceramics are heavily influenced by their crystal structures. Ceramics can exhibit various crystalline structures, including cubic, hexagonal, and tetragonal. For instance, zirconia can exist in multiple phases (monoclinic, tetragonal, and cubic), each with distinct properties. The ability to control these phases through doping and thermal treatments is crucial in tailoring the properties of ceramic materials for specific applications. Manufacturing Processes 2 The manufacturing of ceramics involves several key processes, including raw material preparation, forming, drying, firing, and finishing. Each stage plays a critical role in determining the final properties of the ceramic product. Raw Material Preparation The first step in ceramic manufacturing is the preparation of raw materials. This involves the selection of high-purity raw materials and the blending of various components to achieve the desired composition. Common raw materials include clays, feldspar, silica, and alumina. These materials are often processed to remove impurities and achieve a fine particle size, which is essential for uniformity and quality in the final product. Forming Forming is the process of shaping the raw material into the desired geometry. There are several forming techniques, each suited for different types of ceramic products: 1. Pressing:Pressing involves compacting the ceramic powder in a mold under high pressure. This method is commonly used for producing dense, uniform products such as tiles and bricks. 2. Extrusion: Extrusion is used to create long, continuous shapes with a constant cross-section, such as pipes and rods. The ceramic material is forced through a die to achieve the desired shape. 3. Slip Casting: In slip casting, a slurry of ceramic particles (known as slip) is poured into a porous mold. The liquid portion of the slip is absorbed by the mold, leaving a solid layer that conforms to the mold’s shape. This technique is widely used for making complex shapes, such as sanitary ware and decorative items. 4. Injection Molding: Injection molding involves injecting a mixture of ceramic powder and binder into a mold. This process is suitable for producing intricate and detailed shapes, often used in advanced ceramic applications. Drying After forming, the ceramic material must be dried to remove excess moisture. This step is crucial because uneven drying can lead to warping, cracking, or other defects. Drying can be performed at room temperature or in controlled drying chambers, where humidity and temperature are carefully regulated. Firing Firing is the most critical stage in ceramic manufacturing, where the formed ceramic body is heated to high temperatures in a kiln. This process, also known as sintering, causes the ceramic particles to bond together, resulting in a dense, solid material. The firing temperature and duration depend on the type of ceramic material and the desired properties. For example, traditional ceramics like bricks and pottery are typically fired at temperatures ranging from 800°C to 1200°C, while advanced ceramics may require temperatures above 1600°C. During firing, several chemical and physical changes occur, including: Dehydration: Removal of chemically bound water from the ceramic material. 3 Phase Transformation: Changes in the crystalline structure, which can affect the material’s properties. Densification: Reduction of porosity and increase in density, leading to improved mechanical strength and durability. Finishing The final stage of ceramic manufacturing involves finishing processes such as glazing, polishing, and machining. Glazing involves applying a glassy coating to the ceramic surface to enhance its appearance, impermeability, and resistance to chemical attack. Polishing and machining are used to achieve precise dimensions and smooth surfaces, particularly for advanced ceramics used in technical applications. Advanced Ceramics Advanced ceramics, also known as engineering ceramics or technical ceramics, represent a significant evolution from traditional ceramics. These materials exhibit exceptional mechanical, thermal, and electrical properties, making them suitable for high-performance applications. Types of Advanced Ceramics 1. Oxide Ceramics:Oxide ceramics, such as alumina and zirconia, are known for their high hardness, chemical stability, and wear resistance. Alumina is widely used in cutting tools, electrical insulators, and biomedical implants. Zirconia is valued for its high fracture toughness and is used in applications such as dental implants and thermal barrier coatings. 2. Non-Oxide Ceramics:Non-oxide ceramics include carbides, nitrides, and borides. Silicon carbide and silicon nitride are notable examples, used in applications that require high temperature and wear resistance, such as turbine blades, armor, and cutting tools. 3. Composite Ceramics: Composite ceramics combine different ceramic materials or ceramics with metals to achieve a balance of properties. For instance, ceramic matrix composites (CMCs) are reinforced with fibers to enhance toughness and thermal shock resistance, making them suitable for aerospace and defense applications. Applications of Ceramics Ceramics have a wide range of applications across various industries, driven by their unique properties. Construction In the construction industry, ceramics are used for structural components such as bricks, tiles, and sanitary ware. Their durability, aesthetic appeal, and resistance to weathering make them ideal for building materials. Electronics Ceramics play a critical role in electronics, where their electrical insulating properties are essential. They are used in capacitors, insulators, piezoelectric devices, and substrates for electronic circuits. 4 Healthcare In healthcare, bioceramics such as alumina and zirconia are used for medical implants, including hip and knee replacements, dental implants, and bone grafts. Their biocompatibility and mechanical properties make them suitable for long-term use in the human body. Aerospace and Defense Advanced ceramics are used in aerospace and defense applications for their high-temperature stability and wear resistance. Examples include thermal protection systems for spacecraft, armor plating, and components for jet engines and gas turbines. Consumer Goods Ceramics are also found in everyday consumer goods, such as cookware, decorative items, and household appliances. Their heat resistance and aesthetic qualities make them popular choices for various consumer products. Future Trends and Developments The ceramic industry continues to evolve with advancements in materials science and technology. Key trends and developments include: 1. Nanotechnology: The incorporation of nanomaterials into ceramics is leading to the development of nanoceramics with enhanced properties, such as increased strength, toughness, and electrical conductivity. 2. 3D Printing: Additive manufacturing techniques, such as 3D printing, are revolutionizing ceramic manufacturing by enabling the production of complex shapes and customized products with reduced material waste. 3. Sustainable Manufacturing: There is a growing emphasis on sustainable manufacturing practices, including the use of recycled materials, energy-efficient processes, and environmentally friendly additives. 4. Functional Ceramics: Research is ongoing into the development of functional ceramics with specific properties, such as magnetic, optical, and catalytic functionalities, for advanced technological applications. Conclusion The ceramic industry is a dynamic and multifaceted field that integrates chemistry, materials science, and engineering to produce a diverse array of products. From traditional pottery and construction materials to advanced ceramics used in cutting-edge technologies, the industry continues to innovate 5 and adapt to meet the demands of modern society. As research and development efforts progress, the future of ceramics holds promise for even more sophisticated and high-performance materials that will drive advancements across various industries.