Block-4 PROJECT MANAGEMENT PDF
Document Details
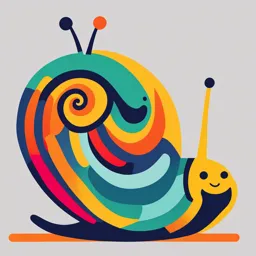
Uploaded by TimelyChrysoprase
Tags
Summary
This document provides an introductory overview of project management, focusing on project development, pre-investment, and investment phases. It highlights the importance of feasibility studies in project success.
Full Transcript
UNIT 12 PROJECTS : CONCEPT ANDPHASES Structure 12.1 12.2 12.3 12.4 12.5 Introduction (Objectives) Development of Projects 12.2.1 History and Projections 12.2.2 Some Cases of Monumental Project 12.2.3 General Causes of Overruns 12.2.4 Sound Management Practices Necessary to Combat Overruns Variou...
UNIT 12 PROJECTS : CONCEPT ANDPHASES Structure 12.1 12.2 12.3 12.4 12.5 Introduction (Objectives) Development of Projects 12.2.1 History and Projections 12.2.2 Some Cases of Monumental Project 12.2.3 General Causes of Overruns 12.2.4 Sound Management Practices Necessary to Combat Overruns Various Phases of the Projects 12.3.1 Project Identification 12.3.2 Pre-feasibility Report and its Clearance 12.3.3 Estimates and Techno-economic Feasibility Report 12.3.4 Detailed Project Report 12.3.5 Project Clearances 12.3.6 Project Financing 12.3.7 Technology Transfer and Foreign Collaboration 12.3.8 Appointment of Consultants Summary Answers to SAQs 12.1 INTRODUCTION A project is a set of activities related to the achievement of some planned objective, normally where the objective is unique or non-repetitive in nature. Thus, a project is usually distinguished from repetitive or continuous production processes by the characteristic of uniqueness, or the "one shot" nature of the objective. Here, this will not be out of the point to mention that in project to achieve the objectives planning and control are the major tools to combat the overruns, but to conceive a project rather before the start of construction activity, there are various activities involved to implement the project. The project development cycle comprises the pre-investment, the investment and the operational phases. Each of these three major phases is divisible into stages, many of which constitute important industrial activities. Several parallel activities take place within this phase and even overlap into succeeding investment phase. Thus, once the early stages of pre-investment studies have produced fairly dependable indications of a viable project, investment promotion and implementation planning are initiated leaving, however, the main thrust to the final evaluation stage and investment phase. Feasibility study is one of most important activity during the pre-investment phase. Complete and detailed feasibility studies covering all aspects of a project is a vital requirement for the success of the project. It should define and analyze the critical elements that relate to the production of a given product together with alternative approaches to such production. Such a study should provide a project of a defined production capacity at a selected location using a particular technology or technologies in relation to defined materials and inputs, at identified investment and production costs, and sales revenues yielding a defined return on investment. The feasibility study should describe the optimum process justify the assumptions made and the solution selected, and define the scope of the project as the integration of the selected partial alternatives, If, however, the project is not viable despite all alternatives reviewed, this should be stated and justified in the study. A feasibility study may be either market-orientedor based on material inputs, i.e. it derives its initiative from an assumed or existing demand or from available material inputs such as raw materials or energy. A feasibility study is not an end in itself, but, only a means to arrive at an investment decision that need not agree with the conclusions of the study. In fact, it would be rare to find investor. response so flexible as to fully conform to the results of such a feasibility study. Objectives The major objective of this unit is to give a better understanding of the various tasks under the pre-investment phase of an industrial project. However, after studying this unit, you should be able to describe various statutory requirement, prepare various reports and documents normally furnished. and interact with various authorities for clearing the projects. 12.2 DEVELOPMENT OF PROJECTS It is common knowledge that a country's economic development is achieved through various industrial and infrastructural development projects and that industrial growth depends on the country's infrastructure. In India, development process in the real sense, using science, technology, engineering and construction, began only in the year 1951, that is, with the First Five Year P1an. 12.2.1 History and Projections From 1951, till 1989-90, financial outlay totalling Rs. 787,591 crore has been invested in development projects. These huge sums have been distributed among the heads of development like Agriculture and Allied Activities, Energy, Industry and Minerals. Transport, Communication Science, Technology and Environment, Irrigation and Flood Control, Rural Development, Special Areas Programmes, Housing and General Economic Services. In the Eighth Plan (1992-97), out of a total outlay Rs. 798,000 crores. Investment in the public sector will be Rs. 434,100 crore, while the private and household sectors in various projects will account for the balance. India has, since independence, achieved substantial economic growth through industrial and infrastructural development projects. But, on a worldwide comparison, and when seen against the country's needs, the overall development achieved till date is negligible. 12.2.2 Some Cases of Monumental Project A few recent past examples of disastrous mismanagement of public sector projects, taken from different sectors and briefly discussed here, will help in a better perception of the prevailing situation. In the Atomic Energy Sector, the Narora Atomic Power Plant of 2 x 235 MW capacity at Bulandshahar in U.P. was approved by the Central Government in 2 January 1974 with, an estimated total cost of Rs. 209.89 crore, and the two units were to be commissioned before March 1982. The project has suffered more than 10 years delay and Rs. 535 crore cost overrun. It was a case of failure on the part of the owner and/or executing authority not to timely planning and integrated team management of all agencies involved. In the Coal Sector the Moonidih Underground Project of 2.1-million tonnes/year capacity was seven years of schedule and seventeen years of overrun, raising its cost from Rs. 15.49crore to Rs. 158.38 crore. This recordbreaking classic example of project failure is attributable to indecision and lack of coordinated efforts which led to delay in finalizing technology and equipment, with continued changes in the scope of the project. and delay in the supply of long wall face equipment. In Steel, the colossal overruns experienced by Vizag Steel Project with a time overrun of 56 months and cost overrun of Rs. 6,093 crore are the result of wrong estimates, had fund flow, inordinate delay in civil work and equipment supplies by public sector enterprise, and failure on the part of the State Government to provide water on time. The root causes of all this failure is the consultant's inadequate exercises at the formulation stage, in sufficient funding arrangements, and undeserved protection to the public sectors vendors and contractors. The four million tonne expansion projects of both Bokaro and Bhilai have overrun by8 years and 7 1/2 years respectively, with cost overruns of Rs. 1,251 and Rs. 1,350 crore, respectively their percentages being 132 and 144. In fact, simultaneously, Bokaro Steel's captive power plant work had also overrun and wasted over Rs. 80 crore additionally. Non-freezing of specifications. "go ahead" clearance without a final plan, delay in supplies,delayed dispatches by USSR and Poland and failure by public sector construction contractors are the main factors responsible for this. In Petroleum& Natural Gas, the delay of over 6 years and the cost overrun of 200 percent amounting to Rs. 106 crore in the construction of Polystaple Fibre Plant in Bongaigaon were caused by law and order problems and infrastructural inadequacy. In the Power Sector, Dulhasti project in J & K, and Panchat II and Koel Karo, both in Bihar,all hydroelectric projects, illustrate the inefficiency of power projects. Dulhasti with over44 months delay and cost overrun of Rs. 1572 crore over the estimated cost of Rs. 183crore: Panchat II with 128 month delay and cost overrun of Rs. 47 crore over the estimated cost of Rs. 16 crore; and Koel Karo with indefinite delay and cost overrun of Rs. 894 crore over the estimated cost of Rs. 445 crore, are among the bad examples of project management failures. Admitted causes are : delay in land acquisition, adverse geological conditions, tunnel failure, law and order problems and contractors' failure. The lapses of the owner and project authorities and the lack of involvement of State Governments have not been examined. 12.2.3 General Causes of Overruns The general causes of overruns that have become a common feature of Indian Projects at different phases, as revealed by a detailed research on several past and ongoing projects areas follows : 3 Pre-feasibility Study Phase Delay in land acquisition, forest clearance and environmental clearance. Delay in clearances from financial/regulatory bodies of the Government. Lack of infrastructural facilities. Failure in planning for important resources, facilities, tie-ins and inputs needed for timely construction and putting into operation. Selection of incompetent consultant. Evaluation Phase Inadequate project study, understatement of scope and underestimate of cost and resources, calling for subsequent changes in the scope of the project; non-freezing of specifications; and revision of budgets. Political influences in site selection. Consultants' and project authorities' inadequacies, leading to wrong economic studies and misleading fund flow statements and projections, causing financial impediments. Technology Selection and Engineering Phase Poor outdated technology acquisition. Technological tie-ups more on consideration of credit offered by the supplier rather than of technical necessitie. Starting of detail engineering and preparation of shopping lists before finalising process flow-sheets and line diagrams. Delay in completing detail engineering: lack of design data; delay in the freezing of design and specifications: absence of an engineering schedule, leading to delay in the release of drawings for procurement. Inefficient procedures for scrutiny, approval and transmittance of drawings and specifications. Contracting and Procurement Phase Delays, slipshod preparation of bid documents. Poor selection of vendors/manufacturers/fabricators/suppliers and contractors and preferential treatment to public sector enterprises, on the basis of Government's guidelines. Delayed placement of orders. The practice of accepting the lowest quotation, irrespective of the vendor qualities and/or contractor's competency. Delay in the issuance of import licenses, permits and various clearances. 4 Delay in the opening of letters of credit and issuance of various guarantees to foreign suppliers. Time-consuming procedures concerning the procurement of imported raw materials and high-tech components by Indian manufacturers of equipment. Inadequate expediting actions. Lack of integrated action plans closely involving suppliers and contractors. Delay in the supply of critical equipment. Lack of proper quality control arrangements - at various levels and in final stage, and consequent defects in equipment. Changes and modifications without cost-benefit analysis. Poor logistics planning. Construction Phase Very early starting of construction activities, before ensuring the availability of working drawings, storage and pre-assembly space, sequential supply of equipment and materials and adequate infrastructure. Delay and/or inadequacy in contractors' mobilisation. Poor planning by contractors. Lack of close co-ordination and owners' serious involvement. Failure to assure contractors of law and order in the project area. Contractor's low productivity and consequent financial problems. Inefficiency of contractors, in both the public and private sectors. Hold-up resulting from delays in interconnected activities. because of the absence of integrated management. Belated clearances. Indecision and delayed decision-making. Bad quality control. Lack of micro-level schedule control with reference to the macro plan to the project. Unfair treatment to contractors and suppliers. Delay in replacement supply. 12.2.4 Sound Management Practices Necessary to Combat Overruns The chief aim of project management is project success, with reference to time. Cost and quality. Project management is an integrated multidisciplinary function aimed at achieving project success through proper pluming, organizing, execution and control. 5 Total project management is the whole process of creating a productive wealth or a fixed asset, capable of producing goods or generating services. This process encompasses all functional disciplines of business management with their nuances peculiar to the special features of formulating, planning and implementing a project, and is therefore, multidisciplinary in character. It is usually a task force consisting of members from various functional department, viz. Planning, Design and Engineering, Operation and Maintenance, Finance, Procurement and Material Management, Construction, and Personnel &Genera1Administration. Components of Project Management The main components of project management are: A clearly defined project objective. An integrated project team, consisting of the representative of :- The owner and/or executing authority. The consultant. The main contractors. Suppliers of critical equipment. Funding institution and all agencies which have a major role in the project The central and state Government, where relevant. An integrated total project plan, broken down into tasks and activities, with daily targets. The necessary resources. An effective quick-hitting control system. Commitment on the part of the people involved. SAQ 1 a) How the project is distinguished from other type of production process ? b) What are the different phases of project development cycle ? c) What is importance of feasibility study ? d) What are the general causes of overruns ? e) Why do you think project management essential to achieve project success ? 12.3 VARIOUS PHASES OF THE PROJECTS UNIDO has divided project cycles into phases and stages as follows: (1) Pre-investment Phase (a) Identification of investment opportunity (Project Idea) (b) Preliminary selection stage (Pre-feasibility study). (c) Project formulation stage (Techno-economic feasibility study). 6 (d) Evaluation and decision stage (Evaluation report and Detailed Project Report). (2) Investment Phase (a) Negotiation and contracting stage. (b) Project design stage (c) Construction stage (d) Start-up stage (3) Operational Phase (a) Short-term views (b) Long-term views Regardless of the division made for the convenience of handling a large engineering and construction project goes through major activities of: (i) Analyzing social, financial. economic and technical cost-benefits and feasibility. (ii) Obtaining various clearances and approvals. (iii) Financial arrangements. (iv) Engineering and Design. (v) Procurement, contracting and construction. (vi) Commissioning and stabilizing the operation and maintenance. UNIDO's stage I (b). 1(c) and 1(d) coincide with the Government of India's practice of three stage project scrutiny, namely (i) pre-feasibility study, (ii) techno-economic feasibility study and (iii) detailed project report. 12.3.1 Project Identification When project idea occurs, you have to visualize and identify it as a wealthcreating and a goods producing or a service-generating enterprise or facility. Such identification has to be done with reference to the country's developmental strategies and long time economic policy, so that, when completed, it fits well into the total economic system or development networks, capable of being fully utilized. Every project that is identified for implementation, even if it is a private enterprise, must serve an economic and/or social need of country in general and society around it in particular, for a long time to come. The Central Government's Planning Commission and Developments of Economic Affairs and Industrial Development give guidance in these matters. Even State Government has industrial development organizations set up for guiding and assisting entrepreneurs. Opportunity study is aimed at identifying an and investment opportunity to take commercial advantage of natural resources and factors of production available in abundance at a place, with potential for conversion into goods or services. 12.3.2 Pre-feasibility Report and its Clearance 7 Project formulation report or project opportunity study report or pre-feasibility report is the document which elicits the preliminary sanction or the first stage clearance by the Government and/or the Board of Directors of the enterprise, for further feasibility study of a project. A clearer report will elicit a faster clearance. The objective of appraisals in the various stages of evolution and project decision is to ensure that the project is viable from the following angles: Market demand for the projects' end-product and plant capacity Materials and inputs. Location and site. Project engineering and investment costs. Plant organisation and overhead costs. Manpower. Implementation schedule. Financial and Economic evaluation. While it is true that one should expect a pre-feasibility report to contain precise details and accurate figures, it necessary that attempts are made to give even in the pre-feasibility report the best available information. Also, if any aspect, favourable or adverse, calls for special attention in making a decision, that aspect should be highlighted in sufficient detail. Particularly to be highlighted is the cost for any foreign process/technology to be acquired, its age and obsolescence and its Indiansation plan. Simultaneously, with the submission of PFR, you may go ahead with your action to obtain the other clearances required, which, depending on the type and location of the project, may include all or most of the clearances. A gross idea of cost components are also considered in pre-feasibility estimates. The Principal types of estimates follows : (i) (ii) (iii) (iv) Order of magnitude estimate : This is desired from the cost report of completed projects. Probability of this estimates accuracy is generally between (25 and 40 percent). Preliminary control estimate : This is prepared generally after the completion of the process design and major equipment listing. Accuracy of this estimate may he between (15 and 25 percent). Definitive estimate : This is prepared as soon as the basic engineering is completed, and bulk material take off sheets are made. Accuracy of this may range from (10 to 15 percent) Detailed estimated: This is prepared when design engineering and preparation of production drawing and final material lists have been completed and prices of all materials ascertained. This may improve the accuracy to 5 percent, leading to revision of provisional budgets. 12.3.3 Estimates and Techno-economic Feasibility Report Techno-economic feasibility Report is the second stage of the evolution phase where the project scope is described, its size and the methods determined suitability of the site, the required natural resources and raw materials 8 investigated and more accurate estimates made of process and non-procesess equipment, buildings, offsite facilities and other assets, their costs. etc. and the total feasibility of the proposal studied in-depth and cleared. Preparation of Techno-economic feasibility Report is an arduous task to be accomplished with a great deal of care and functional interface of your total organisation. The information and figures given in pre-feasibility report have to undergo a lot of refinement to find their places in Techno-economic feasibility report. The objective is to include enough data to enable a proper assessment of the technical, financial and economic feasibility of the proposed project. Information generally contained in the report are as follows : Project background and description. Market and plant capacity. Materials and input. Location and sites. Project engineering and investment cost. Plant organization and overhead cost. Manpower Implementation schedule. Financial and economic evaluation Estimating the project cost is an important activity for preparing the technoeconomic feasibility report. Although the estimate at this TEFR stage is still preliminary or pre-definitive and subject to further refinement at the 1ater definitive/detailed estimation, care must be taken to keep down the level of uncertainly by making the best use of process flow sheet and other available information sources. The usual practice to prepare capital cost estimates is as follows : Prepare detailed schedules tor every cost component, listing item description, quantities, rate or prices assumed and total amounts. Prepare a summary sheet for every component. Make a top sheet covering all components, providing separate columns for foreign exchange, local cost and total cost. The Industries and Commerce Department of several State Government offer incentives to the entrepreneurs for rapid industrial development. The incentives may include the following : Relief of sales tax or octroi or entry tax. Laid for setting up new units and for expansion of existing units Contribution towards the cost of feasibility and-project report. Subsidy on power. Financial assistance in the form of term loan or working capital loan. Housing scheme. Supply of raw materials, etc. 9 Export oriented units and unit set up in export processing zones which undertake to export their entire production of goods are eligible for the following incentives and concessions : Concessional rent for lease of industrial plots and standard design factory buildings/sheds allotted for the first three years. The International Price Reimbursement Scheme (IPRS) on the purchase of iron and steel, which will help the unit in pricing the endproduct competitively in the international market, without being affected by higher domestic price paid for iron and steel. Tax holiday by exemption from payment of corporate income tax for a block of five years in the first eight years of operation. Clubbing of Net Foreign Exchange (NFE) earned by the unit with the NFE of the parent/associate company in the Domestic Tariff Area (DTA) for purpose of according export house status' based on export earning. Concession in duty and taxes. Foreign equity participation upto 100%. Before deciding on investment. the total financial viability of the project is to be examined closely from the angles of : (i) Profitability or rate of return (ROR) (ii) Cash Flow (iii) Pay-back of investment. Profitability, cash flow and repayment capacity shall be computed and analysed and report from the angle of: Net present value of cash flow (NPV) Internal rate of return (IRR) Pay-back period (PBP) Simple rate of return] (SRR) Break-even point (BEP) Sensitivity analysis (SA) 12.3.4 Detailed Project Report This is the last and the most important stage of the pre-investment phase of any project. Detailed Project Report (DPR) should be undertaken only after obtaining the investment decision based on Techno-economic feasibility report, so that the expensive efforts involved in the preparation of DPR are not wasted. For preparing filmed-up estimates with about 15 percent accuracy to be submitted with DPR, and the documents like process design, layout drawings and construction data are necessary for DPR preparation. Although you have a time limit up to one year from the TEFR clearance for submission of DPR. The outline and the items of DPR are the same as of the TEFR. All the vital aspects of location and site costs, process/technology, market demand, plant capacity, product revenue, production costs, profitability, economic benefits, 10 etc. have to be gone into in greater detail and reported on. The basic difference is the level of accuracy. To develop DPR from TEFR, you have to : breakdown all project components, time-phase and schedule them with accurate cost estimates, by way of deviation from TEFR with explanations giving the improved basis of assumptions and calculations, develop baselines for controlling time and cost during the implementation of the project, and prove your preparedness with all the technical and resources requirement, to implement the project. All Detailed Project Report must indicate the parts components, etc. with approximate annual quantities proposed to be procured from, ancillary industries around the project for use in construction, operation and maintenance. This has to be supported by clearance from the Development Commissioner, Small Scale Industries of the area. While applying for grant of letters of intent and industrial license, where applicable, the items proposed to be procured from ancillary industries around project be spell out. Following documents and data are necessary for preparation of DPR : Process/System design. Raw Materials/feedstock arid project specification. License fee for technology. Engineering plan and Engineering Manpower curves. Final Flow diagrams. Heat and material balances. Piping and instrumentation diagrams for process and utilities. Layout plans for buildings equipment, utilities and off-sites. General Project Specification. Soil investigation report. Single Line Electrical Drawing. Construction Plan and Manpower Deployment Plan. Environmental Pral Protection Plan. Equipment List with specification and data sheet. Resource Schedules. Organisational Charts and manpower curves. Water and Power Supply Guarantee. 12.3.5 Project Clearances Besides the techno-economic and financial clearances, a good number of other clearances are necessary for project implementation. While some of them are 11 technical requirements, others are statutory - but all regulated by the Government. Various clearances for a project are given below: Soil investigation report Clearance under the Monopolies and Restrictive Trade Practices (MRTP) Act Industrial License/Letter of Intent Approval of foreign collaboration Approval for appointment of foreign consultant Foreign exchange clearances Import of capital goods Approval for setting up export oriented units Environmental/Pollution Control Clearances Clearance from the International Airport Authority Railway Clearance Electricity Clearance Explosives Clearance Forest Clearance State Industries Department Clearance 12.3.6 Project Financing Many project failures resulting from unplanned, untimely and insufficient financing, mainly attributable to commencement of implementation before making adequate funding and disbursement arrangements. Sources of financing are not common for the various public, joint and private sector project enterprises. Some of the sources available to the public sector are not available to the private sector, while some others available to the private sector are not available to the public sector. The main sources of project finance are as follows : Equity and Preference Share Capital Promoter group's contribution. State Government contribution. Public subscription. Seed capital assistance. Risk Capital and Technology Finance Corporation Ltd.'s assistance. Technology Development and Information Company of India's assistance. Share subscription by financial institutions and mutual funds. 12 Share subscriptions by NRIs. Employees stock exchange. Preference shares or Preferred stock. Central and state capital subsidies, sales tax loan and development assistance. Internal generation of funds Retained profit. Depreciation. Lease financing Public Sector Bonds Debentures Long-term rupee loans From all-India development banks and investment institutions. Sundry sources of long-term loans. Inter-corporate loans. Central Government budgetary support Foreign Currency Funds Free foreign exchange from FE dealers and loans from development banks. External commercial borrowings External aid Bilateral aid. Multilateral aid. Assistance from International Finance Corporation Investment from Oil Exporting Developing Countries (OEDCs) Collaborator's equity participation in foreign exchange Share subscription by overseas investors NRI and OCB Share subscription in foreign exchange Short term rupee funds for working capital From commercial banks. Public deposits. Debentures/Bonds. Suppliers' credits. SAQ 2 a) What are the major activities, a long engineering and construction project goes through ? 13 b) What are the three stages of project scrutiny which Govt. of India is adopting ? c) What are different factors for assessing the viability of a project ? d) What is Techno-economic Feasibility Report ? 12.3.7 Technology Transfer and Foreign Collaboration The success of the end-product of your project would depend almost entirely on the quality of the production technology or process know-how you have used and the efficiency of the production facility you have created. In fact, every project owner likes to use the state-of-the-art technology for his projects' best performance, productivity and profit, especially at the present time when there are rapid technological advances all around him. The technology policy of the Government aims at making the country technology self-reliant; but at the same time, as the country is not technologically self-sufficient, permitting transfer of advanced foreign technology to India. For local absorption, adaptation or Indianisation and further improvement, with due consideration to Indian economic objectives and natural resources. Besides conforming, in general, to the Government's industrial and technological policy, every technology transfer agreement should, in particular, be clear in regard to the nature and scope of the technology transfer. It should place at your use the collaboration technology- owner's (i) Knowledge, (ii) Experience, and (iii) Skill necessary to : (a) Set-up the sturdiest, but at the same time inexpensive, production which is easy to operate and maintain. (b) Produce the planned goods or services in a manner capable of capturing the local and foreign markets within the shortest period of time keeping within the national economic parameters. The level of sophistication of the technology should be determined with reference to the type of demand and the competition that your product is likely to face from others. The Government's Department of Industrial Development in the Ministry of Industry has a Technology Data Bank, which gives information on a wide choice of technologies and collaborators. The most appropriate technology should be chosen to suit your project in the Indian environment, which, for some more years to come will be labour-oriented and not highly sophisticated nor substantially automated. The factor relevant to Indian conditions is ne need to use local raw materials local infrastructure and other locally available inputs to the fullest possible extent. The environment in which the undertaking is set up and the type of equipment ,and production technique employed are interrelated. The national economic policy is also in favour of this inter-relation. Our developing economy has a certain level of technology absorption capacity. So it will be ideal if you choose a technology suited to that level, with the potential for improvement, keeping pace with the changes in our socioeconomic environment. The phases of Technology Transfer are sequentially as follows : Choosing 14 Source Searching Negotiation Contracting The principal forms of Technology Transfer are : Licensing. Outright Purchase. Joint venture with capital participation. Technology transfer with buy-back guarantee. Technology transfer with loan agreement. Technology transfer with plant operation and management contract. Technology transfer forming part of a consultancy contract. Technology transfer forming associated with equipment supply contract or turnkey contract. The technology absorbed by an enterprise has to attain maturity and keep improving in the Indian environment with continuous commercial exploitation, keeping pace with consumer demand. In a world faced with technology explosion, the challenge of avoiding the repetitive import of the same technology with all the latest development can he met only through continuous in-house R&D efforts. Foreign collaboration, envisage two types of participation by well established foreign companies in Indian projects in their specialized fields. They are : (a) Collaboration for technical participation under which an engineering and production technology passes onto the Indian side. (b) Collaboration for technical and financial participation in an Indian project by a foreign party. Foreign collaboration is a complex part of the total project management spectrum. Government's policy for foreign collaboration is based on national priorities. Foreign collaboration 1s permitted liberally in the certain groups of high priority industries and export-oriented units, and selectively in other cases. Foreign collaboration should generally aim at integrating our industry into global/economy. The policy is guided by the following objectives: Attaining technological competence and self-reliance, to reduce vulnerability, particularly in strategic and critical areas, making the maximum use of indigenous resources. Providing maximum gainful and satisfying employment to all strata of society with emphasis on employment of woman and weaker section of society. Using traditional skills and capabilities, making them commercially competitive. Ensuring maximum development with minimum capital outlay. Identifying obsolescence of technology in use and then arrange for modernisation of both equipment and technology. Developing technologies, which are internationally competitive, particularly those with export potential. Reducing demand in energy, particularly energy from non-renewable sources. 15 Improving production speedily through greater efficiency and fuller utilization of existing capabilities, 'and enhancing the quality and reliability of performance and output. Ensuring harmony with the environment, preserving the ecological balance and improving the quality of the habitat. Recycling waste material and making full utilization of byproducts. 12.3.8 Appointment of Consultants You will find that most of the project owners use the services of a consultant an individual consultant or a consulting firm, or a captive consulting organisation, throughout the project duration. Even when the owner has a competent project team, a consultant may he appointed for the following reasons : The functional experts of various disciplines who are members of the project team will have many other responsibilities, which are bound to divert their attention from the particular project. A multi-disciplinary consultant's deep knowledge, rich experience and concentrated attention to all important aspects of a project will, no doubt, boost its efficiency, justifying the consultancy cost. An independent consultant will view all matters in an unbiased manner. General issues concerning the appointment of a project consultant in the Indian conditions are the following : (a) Determination of the consultant's role in the project. (b) Types of consultant. (c) The role of domestic consultant. (d) Selection and appointment. (e) Terms of preference. (9 Actual use of consultant. (g) Co-ordination procedure. (h) Professional liability. Generally, the selection process comprises the following steps : 16 Determination of the consultant's role. Determination of pre-qualification criteria. Estimation of the expendable consultancy cost. Short-listlng or pre-qualification of consultants. Determination of final selection criteria. Determination of selection procedure and designing of forms for consultant's work proposals, bio-data arid consulting experience of his firm as a whole or of the members individually proposed to be employed on the project. Invitation of work proposals and bids from the short-listed ones. Evaluation of capabilities on the basis of the work proposals, data and bids received. Selection of one or more consultant for the whole project or for different assignment or work package. Negotiation on terms of conditions. Appointment. The principal types of appointments are given below : Consulting firms retained by owners, with the lending institute's approval, following the selection procedure prescribed or agreed to by the lending institute. Consulting firms retained by the lending institutes playing the role of executing agency. Consulting firm engaged as Engineering firm, acting alone or in joint venture with one or more other agencies, to provide total turnkey packages comprising all services and supplies. Individual consultants retained by owners. SAQ 3 a) What are the incentives offered by the Industries and Commerce Department of several State Governments ? b) What are the other incentives for which export oriented units are eligible ? c) What arc the different project clearances which are necessary for project implementation ? d) What are the main resources of project finance ? e) What are the objectives behind foreign collaboration ? f) Why does a project owner feel the requirement of consultants in his project success ? 12.4 SUMMARY Project is a set of activities related to the achievement of some planned objective. In a project object is normally unique and/or non-repetitive in project planning and control are the major tools to combat the overruns. The study of unit provides better understanding of the various tasks under the preinvestment phase of an industrial project. Unit also described some cases of monumental projects in India which are delayed and overruns. Root causes are analysed. For achieving project success, requirement of Project Management is felt. Components of Project Management are explained in detail. Unit tells about various phases of the projects and Government of India's practice of their scrutiny. Pre-Investment, investment and operational phases are three phases of projects. Pre-feasibility study, Estimates and Techno-economic feasibility study and Detailed Project Report are three stages, Government of India practices for scrutiny. Under Techno-economic feasibility a detail description of various incentives and concessions for industry is given. Under Detailed 17 Project Report a list of documents and data necessary for preparation of DPR is given. Various project clearances which are necessary for project implementation are listed. Unplanned and insufficient finance always results into project failure. Main source of project finance are given in the unit. The success of the end product of project depends on the quality of the production technology. In many cases, country is not technologically selfsufficient, therefore, one may use the collaboration with technology knowledge, experience and skill. The principal forms of Technology transfer are listed. The project owner always appoints a consultant to have use of deep knowledge, rich experience and concentration attention of consultant. General issues concerning appointment of a project consultant in the Indian condition are pointed out along with selection process. 12.5 ANSWERS TO SAQs Refer the relevant preceding text in the unit or other useful books on the topic listed in the section "Further Reading" to get the answers of the SAQs. 18 UNIT 13 PROJECT MANAGEMENT Structure 13.1 13.2 13.3 13.4 13.5 13.6 13.7 13.8 Introduction Objectives Project Planning and Organising 13.2.1 Development of Project Plan Objectives 13.2.2 Programming and Scheduling 13.2.3 Project Budget and Fund Flow Status 13.2.4 Project Organisation CPM and Other Project Planning Techniques 13.3.1 Origin of Bar Chart and CPM/PERT 13.3.2 Detailed Study of CPM 13.3.3 Precedence Network 13.3.4 CPM 13.3.5 Line of Balance (LOB) Procurement and Materials Management Contracting and Construction Management 13.5.1 Contracting Approach 13.5.2 Contractors' Role 13.5.3 Types of Contract 13.5.4 Contracting Procedure 13.5.5 Objective of Construction Management 13.5.6 Definition of CM's Scope Project Control 13.6.1 Time and Cost Control Tools and Techniques 13.6.2 Decision Making as a Control Function 13.6.3 Time crashing Economy Analysis 13.6.4 Information Reporting System 13.6.5 Risk Management as a Control Function Summary Answers to SAQs 13.1 INTRODUCTION Management is a process concerned with achievement of goals or objectives. Project Management involves the coordination of group activity wherein the manager plans, organizes staff, directs, and controls to achieve an objective with constraints on time, cost and performance of the end product. It is appropriate at this point to elaborate on the term project. A project is a set of tasks or activities related to the achievement of some planned objective, normally objective is unique or non-repetitive in nature. Thus, a project is usually distinguished from repetitive or continuous production process by the characteristic of uniqueness or the 'one shot' nature of the objective. Projects may involve routine procedures where project planning techniques are useful for detailed analysis and optimization of the operating plan. Planning is the process of preparing for the commitment of resources in the most effective fashion. Controlling is the process of making events conform to schedules by coordinating the action of all functions of the organisation according to the plan established for attaining the objective. It can also be said that project management is a blend of art and science : the art of getting, things done through and with people in formally organised groups; and the science of handling large volume of data to plan and control so that project duration and cost are balanced and excessive and disruptive demands on scare resources are avoided. In order to accomplish the project goal or objective, the manager must plan and schedule largely on the basis of his experience with similar projects, applying his judgment to the particular conditions of the project at hand. During the course of the project, he must continually replan and reschedule because of unexpected progress, delays or technical conditions. Until the advent of critical plan methods there was no generally accepted formal procedure to aid in the management of project. Each manager had his own scheme, which often involved limited use of bar charts - a useful tool in production management but inadequate for the complex interrelationships associated with contemporary project management. The development of network based planning methods in the late fifties provided the basis for a more formal and general approach toward a discipline of project management. Critical path methods involve both a graphical portrayal of the interrelationships among the elements of a project, and an arithmetic procedure which identifies the relative importance of each element in the overall schedule. Since their development, critical path methods have been applied with notable success to research and development programs, all types of construction work, equipment and plant maintenance and installation, introduction of new products or service or changeovers to new models, developments of major transportation and energy related systems, strategic long term planning, management information systems developments production planning, emergency planning and even the production of motion pictures, conduct of political campaigns and complex surgery. All of these activities are classed as projects. In all of these projects, management is concerned with developing a optimum and workable plan of the activities that make up the project including a specification of their interrelationships. Also management is interested in scheduling these activities in an acceptable time scale, considering the manpower and other resources required to carry out the program as it progresses in time. Management is also concerned with monitoring the expenditure of time and money in carrying out the scheduled program, as well as the resulting output, quality or performance, for cases where achievement of the project objective(s) can be measured on a continuous or ordinal scale(s). The ultimate objective of planning is timely and economical implementation of project. A well managed project should have a proper integration in both planning and implementation efforts, commitment on the part of people engaged on implementation and involvement by the top management in the monitoring of projects and trouble-shooting. Engineering contract, commissioning and start-up services which translate a project concept into a goods producing or service generating facility should be very well planned, organised, implemented and controlled for the success of the project. The owner of the project must closely monitor all the functions and ensure that its various activities are on schedule and they are enabling other project activities like procurement, contracting, construction and commissioning to proceed as per schedule, without hold-up. A well designed performance reporting system and a good data management system are vital requirement for an efficient Project Management Function. Objectives After studying this unit, you should be able to 20 understand the various aspects of project management, discuss various techniques of project planning implementation, enumerate various project procurement and materials management functions, describe various controlling tools and techniques to combat project overruns, develop a computer system for preparing computerised network based project planning, identify the critical path of a project, and define risk management as a control function. 13.2 PROJECT PLANNING AND ORGANISING Planning is the formation of a detailed scheme for proper arrangement of the necessary actions, steps and means for achieving the project objectives. The planning exercise should be guided initially by the overall time schedule and cost estimate given in the Detailed Project Report. In the planning stage, the project is broken down into many manageable elements fixes into a time frame within the overall time schedule, with an allotment f resources within the overall project cost, and released for execution. An achievable. Realistic plan, fitting in which the overall project time and project cost is the essential requirement for a project’s success. Performance guidelines and a controlling system to evaluate, and modify the performance as required, shall form part of the plan. Between the formulation of preliminary plan in the Detailed Project Report stage and the finalisation of plan for implementation, the planning has to be subjected to iteration for a possible reformation of the preliminary plan. 13.2.1 Development of Project Plan Objectives It is a universal practice to define the scope of the plan before drawing of a detailed plan. A clear understanding of the plan objectives is a requirement for the plan's success. Ensure that the objectives are achievable, measurable, simple to understand and consistent with the resources levels fixed (and assumptions made) in the Detailed Project Report estimates. Apart from estimates, the planner will require all key information about the project. While Detailed Project Report contains such information, efforts must be made to refine them before using them for planning, thus reducing the level of inaccuracy to the minimum. Planning aims at achieving the projects completion making the most effective use of time and resources. This is normally done by preparing a questionnaire and fill it up before sitting down to do the planning, so that once the planning activity is started there Is no hold up for want of right kind of resources. 13.2.2 Programming and Scheduling Programme is the forerunner of schedule. It is form, a programme of action, that the schedule is prepared. In the section we are dealing with the definition of tasks and the strategy to accomplish them. Various steps of programming are briefly illustrated below : Listing of Work 21 List the tasks and the activities under each tasks, showing main work elements of the total projects by functions/discipline/skills/crafts. These lists will form the foundation of the subsequent steps of a more detailed definition of work. This list can be simple, tabular statement with columns for task code, task description, task duration, etc. Definition of Work Here define the listed work elements in greater detailed for clear understanding. These definition should remove uncertainties, if any, contained in detailed project reports. Work Breakdown Structure and Codification of Tasks Simultaneous efforts and specialists attention in several fronts are necessary for the efficient implementation of a project. Besides, the volume of work allotted to a team should be of a controllable size only. It is for these reasons that work breakdown structure (WBS) is made. WBS is a function of programming. Break down the total project work into manageable self contained and independently executable work packages and the down-the-line activities, area wise or function wise, or crafts wise,or process stage wise. Codification of tasks and related projects accounts facilitate effective management aid control. It is a useful practice in large projects to use structured codes for identification, reference, accounting, integration and computerisation of drawings and technical documents, WBS contains, costs, purchase orders, budget commitments, equipment and materials, schedules, off-sites and infrastructural facilities, manpower and other inputs, contracts, bills, progress reports, performance evaluation, income and expenditure, assets and liabilities etc. Coding can be done either numerically or alphabetically and combined alpha-numerically. The structure of codification would depend on the size, type and accounting needs of the project and the enterprise. Modeling the Work Make graphic models of the main segments and important elements of the work. These models will help you to understand the variables you have to handle in translating the plans into a reality. The models shall indicate the various angles of the type and magnitude of the work to be put in, and the technical, functional and logical relationship of the various activities involved in the work. Addition of time duration to every model with a beginning and an end is done here. As calendar dating may be impossible at this stage, the time is fixed in time of project months or project days, starting from the zero date which is the first milestone of the project. Fixation of Sequence and Priority A project is an integrated whole unit into which hundreds of tasks and thousands of work elements are integrated. So, work programming has to be done if the interrelationship of work in mind. Interfacing of the models will establish the, interrelationship. It must be possible to carry out many work elements independently upto their assembly stage, but in a project with a few hundred thousands identifiable work elements, one cannot afford to leave half of them executed out-of-sequence and wait for mass finishing assembly, connections and testing towards the end of the project. That would cause a lot of confusion, wastage, lock up of money and in most cases remobilisation and even some re-works. Moreover, in a large project, different work packages 22 may have different phased-out commissioning dates for technical and financial results, necessitating a corresponding phased-out completion of work. Besides, for economic or technical reasons, some segments may have to he accomplished on priority over others. For these reasons, sequence and priority have to be given due consideration while programming. Fixation of Activity Duration Every activity shall be allotted a realistically estimated time duration so that the sum total of all such durations minus the net overlapping would be equal to the project duration. In actual practice the time duration is fixed on the basis of the previous on-the-job experience of the planners and the line managers. It is usual to fix a shorter than permitted duration, keeping a few days up one’s - sleeve as a "Buffer Time" for any possible slippage. This provision is contingency time. Scheduled completion time plus contingency time is the target time. Identification of Critical Activities In total project model placing individual segments models end-to-user or drawing a time phased master bar chart, plotting all the important segments with the indication of their interrelationships, it can be found some items have fairly long floats or slack time between starting and finishing, as their finishing does not hold up other activities, but at the same time some other items are so critical that the preceding items tie in and start of succeeding items are dependent on their finishing .These latter items have to be separately identified and listed for special management attention towards their completion, in the interest of timely completion of the project. Scheduling is a substantial improvement on programming. Scheduling is principally the exercise of laying out and integrating time, resources, and the main work elements of engineering, procurement and construction in the most efficient manner to achieve the project objectives. Resources availability and their economic levels of distribution, time duration for individual activities and for the total project, the estimated costs are interrelated through the scheduling exercise. Various steps of scheduling are enumerated below: Forward and Backward Scheduling Forward and backward scheduling is a scheduling strategy used for keeping down the level of resources deployment and the making the optimum use of them by taking advantage of their floats. Forward schedule starts as soon as working front clearance is available for an activity and it often finishes before the required due date. The philosophy here is "finish every activity as early as possible". Backward schedule starts backwards from the required due date of finishing the activity and arrives at a required starting date. The starting date so arrived at will be the latest starting date. The guiding philosophy here is ''finish economically when required". Resources Assessment and Matching Every project owner's resources have some limitations for reasons of economy and previous commitments. So, what is usually done in scheduling is as follow: 23 (a) Take stock of the total Available Resources (AR) that can be mobilised during the activity time, after previous commitments if any. (b) Assess the most economic quantity of Resources Requiremenr (RR) for finishing the activity within the time duration. (c) If the RR is more than AR, try to revise the activity duration using the Forward and Backward scheduling technique and adjust the volume of activities to suit the available resources, taking advantage of floats, but with due consideration to dependencies of activities and overall project completion target, and then calculate the Reassessed Requirements of Resources (KKR). (d) Make provision for procurement of the difference between RRR and AR. (e) Make a master bar chart schedule of the activities with starting and finishing dates and corresponding tabular schedule of time phased allocation of all resources. It must be remembered that the contractors who are awarded jobs will also bring in their resources as per contract stipulation for use in the project. Master Schedule and Master Budget A corresponding master schedule of resources should list the requirements of major resources of men, equipment and materials for the same work packages in a matching time phase with considerations for procurement time and mobilisation time, to enable timely work execution. A corresponding master budget shall ensure financial allocation and the project fund flow. The master resources schedule and master fund flow statement shall be based on the project cost estimate and project investment cost distribution schedule and their subsequent refinement based on firmed up project data and engineering details. Construction Schedule As the construction schedule has a definite impact on other schedules, and as construction activities consume most of the man power employed in the project, including the entire field labour, the construction schedule should be finalised first, among all individual schedules, and particularly before manpower scheduling is taken up. Important points to be borne in mind while scheduling construction work areavailability of construction drawings and materials and the possibility of mobilising economically the required workforce. What is particularly important in construction scheduling is the integration of construction schedule into other schedules for overall success. Manpower Schedules Master manpower planning is required for : (a) Project management, for the project duration, (b) Construction, till the completion of construction, (c) Operation and maintenance, permanent, and (d) Management and control, permanent. 24 In the interest of timely planning and implementation of the project, you must ensure availability of the required number of the right type of staff and workmen for the project management and construction, suiting the overall project schedule. For assessing and fixing the manpower requirement with reference to programmed quantity of work, usually the same norms are used as were used for Detailed Project Report or historical figures of the enterprise and/or the industry average, checked and confirmed by experienced executives. One should always keep in mind following points while preparing the Manpower Schedule : Uneconomical peaks and valleys in the employment levels. Levels of supervisory and administrative staff in proportion to the levels of workforce. Usage of rare skills. Once the manpower schedule is finalised, action shall be initiated for time phased recruitment and training so that according to the demand of the work, the required number of men of the right type are available. Construction Equipment Usage Schedule Normally, a large project will need a large number of construction equipment of different types and capacities for material handling and construction. So a schedule for their proper usage with reference to the schedule of the project work bifurcating it between "to be provided by the owner" and "to be provided by contractors" and then initiate steps for their deployment. Ordering and Delivery Schedule for Incorporated Equipment and Materials For all equipment and materials including bulk materials that go into the project, separate exhaustive lists should be prepared first. for guidance in scheduling their ordering and r