MSENSE® VAM Monitoring System Operating Instructions PDF
Document Details
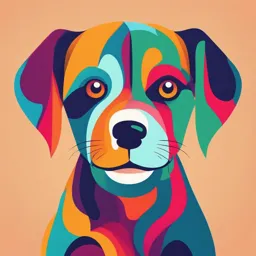
Uploaded by FunnyTriumph
Tags
Related
Summary
This document provides operating instructions for the MSENSE® VAM Monitoring system. It details safety procedures, installation, and operational guidelines, along with general information about the product.
Full Transcript
THE POWER BEHIND POWER. Operating instructions MSENSE® VAM. Monitoring system 8459861/04 EN © All rights reserved by Maschinenfabrik Reinhausen Dissemination and reproduction of this document and use and disclosure of its content are strictly prohibited unless expressly permitted. Infringements w...
THE POWER BEHIND POWER. Operating instructions MSENSE® VAM. Monitoring system 8459861/04 EN © All rights reserved by Maschinenfabrik Reinhausen Dissemination and reproduction of this document and use and disclosure of its content are strictly prohibited unless expressly permitted. Infringements will result in liability for compensation. All rights reserved in the event of the granting of patents, utility models or designs. The product may have been altered since this document was published. We reserve the right to change the technical data, design and scope of supply. Generally the information provided and agreements made when processing the individual quotations and orders are binding. The product is delivered in accordance with MR's technical specifications, which are based on information provided by the customer. The customer has a duty of care to ensure the compatibility of the specified product with the customer's planned scope of application. The original operating instructions were written in German. Table of contents 1 Introduction................................................. 5 6.3 Connecting the ISM® assemblies.............................. 42 1.1 Manufacturer................................................................. 5 6.3.1 Cable recommendation.................................. 42 1.2 Completeness............................................................... 5 6.3.2 Notes on the screw terminal tightening 1.3 Safekeeping................................................................... 5 torque............................................................. 43 1.4 Notation conventions.................................................. 5 6.3.3 Information about connecting serial 1.4.1 Hazard communication system....................... 5 interfaces RS232 and RS485 (with 9-pin 1.4.2 Information system........................................... 6 data cable)..................................................... 43 1.4.3 Instruction system............................................. 6 6.3.4 Information about connecting analog 1.4.4 Typographic conventions................................. 7 sensors........................................................... 45 6.3.5 Electromagnetic compatibility....................... 45 2 Safety........................................................... 8 6.3.6 Information about laying fiber-optic 2.1 Appropriate use............................................................ 8 cable............................................................... 47 2.2 Inappropriate use......................................................... 8 6.3.7 Connecting the vibration sensor to the 2.3 Fundamental safety instructions................................ 9 control cabinet.............................................. 48 2.4 Personnel qualification............................................... 10 6.3.8 Connecting the motor-drive unit 2.5 Personal protective equipment................................. 11 controller to the monitoring system............ 51 6.3.9 Connecting the temperature sensor.............. 51 3 IT security................................................... 12 6.3.10 Connecting additional leads (optional)........ 51 3.1 General......................................................................... 12 6.3.11 Connecting the power supply...................... 52 3.2 Commissioning............................................................ 12 6.4 Checking functional reliability................................... 53 3.3 Operation..................................................................... 12 3.4 Interfaces..................................................................... 13 7 Commissioning.......................................... 54 3.5 Encryption standards.................................................. 13 7.1 Establishing connection to visualization.................. 54 7.2 Setting the language.................................................. 56 4 Product description.................................... 15 7.3 Downloading the operating instructions................. 57 4.1 Variants........................................................................ 15 7.4 Setting date and time................................................ 57 4.2 Scope of delivery......................................................... 15 7.5 Commissioning wizard.............................................. 57 4.3 Function description................................................... 16 7.6 Name plate................................................................. 58 4.4 Performance features................................................ 17 7.6.1 Enter the name plate data.............................. 59 4.5 Design.......................................................................... 18 7.6.2 Displaying the name plate.............................. 59 4.5.1 VS 1 sensor assembly....................................... 19 7.7 Setting the control system protocol (optional)....... 60 4.5.2 Control cabinet................................................. 19 7.8 Performing tests......................................................... 60 4.6 Main screen................................................................ 25 7.8.1 Checking measured values and status of 4.6.1 Standalone version......................................... 25 digital inputs and outputs............................ 60 4.6.2 Integration solution........................................ 26 7.8.2 Performing function tests.............................. 60 4.7 Operating concept..................................................... 27 7.8.3 Electrical high-voltage tests on the transformer.................................................... 60 5 Packaging, transport and storage............... 31 7.8.4 Ground test...................................................... 61 5.1 Suitability...................................................................... 31 7.8.5 Dielectric tests on transformer wiring........... 63 5.2 Markings....................................................................... 31 5.3 Transportation, receipt and handling of 8 Operation.................................................. 64 shipments................................................................ 32 8.1 System......................................................................... 64 5.4 Storage of shipments................................................ 33 8.1.1 General.............................................................. 64 5.5 Unpacking shipments and checking for 8.1.2 Configuring the network................................. 65 transportation damages......................................... 33 8.1.3 Setting the device time................................... 67 8.1.4 Configuring syslog.......................................... 69 6 Mounting.................................................... 35 8.1.5 SCADA.............................................................. 70 6.1 Installing the Cap rail modules / control cabinet..... 35 8.1.6 Name plate....................................................... 83 6.1.1 Installing the cap rail modules........................ 35 8.1.7 Displaying measured value recorder 6.1.2 Integration solution in the ETOS® ED (optional)........................................................ 84 motor-drive unit............................................ 38 8.1.8 Linking signals and events.............................. 86 6.1.3 Fitting the control cabinet to the 8.1.9 Configuring digital inputs and outputs......... 89 transformer.................................................... 38 8.1.10 Configuring analog inputs and outputs 6.2 Mounting the vibration sensor.................................. 41 (optional)......................................................... 91 8.1.11 Event management....................................... 94 8459861/04 EN Table of contents 3 8.1.12 User administration....................................... 96 8.1.13 Hardware...................................................... 100 8.1.14 Software....................................................... 102 8.1.15 Import/export manager.............................. 102 8.1.16 Transformer Personal Logic Editor (TPLE)............................................................ 107 8.1.17 Linking to the visualization of external devices.......................................................... 118 8.2 On-load tap-changer................................................. 121 8.2.1 Displaying VAM analysis................................ 121 8.3 Active part................................................................. 124 8.3.1 Temperature monitoring.............................. 124 8.4 On-load tap-changer................................................ 125 8.4.1 Vibro-acoustic monitoring of the on-load tap-changer (VAM)....................................... 125 8.4.2 OLTC data...................................................... 128 8.4.3 Changing tap position designation (optional)....................................................... 129 9 Inspection and maintenance..................... 131 9.1 Care............................................................................. 131 9.2 Inspection.................................................................. 131 9.3 Maintenance.............................................................. 131 10 Fault elimination..................................... 132 10.1 General faults........................................................... 132 10.2 Event messages....................................................... 132 10.3 Human-machine interface...................................... 132 10.4 Other faults.............................................................. 133 11 Disassembly............................................ 134 12 Disposal................................................... 135 13 Technical data......................................... 136 13.1 Control cabinet standalone version....................... 136 13.1.1 Connection terminals.................................... 138 13.2 Power supply QS3.241............................................ 139 13.3 CPU (central processing unit) II.............................. 139 13.4 DIO 28-15 digital inputs and outputs..................... 141 13.5 AIO 2 analog inputs and outputs.......................... 143 13.6 VI 4 vibration sensor input module...................... 143 13.7 VS 1 vibration sensor.............................................. 144 13.8 Sensor cable............................................................ 144 Glossary....................................................... 145 List of key words........................................ 146 4 Table of contents 8459861/04 EN 1 Introduction This technical file contains detailed descriptions on the safe and proper installa- tion, connection, commissioning and monitoring of the product. It also includes safety instructions and general information about the product. This technical file is intended solely for specially trained and authorized person- nel. 1.1 Manufacturer Maschinenfabrik Reinhausen GmbH Falkensteinstraße 8 93059 Regensburg Deutschland +49 941 4090-0 [email protected] reinhausen.com MR Reinhausen customer portal: https://portal.reinhausen.com. Further information on the product and copies of this technical file are available from this address if required. 1.2 Completeness This technical file is incomplete without the supporting documents. The following documents are considered supporting documents: – Operating instructions – Connection diagrams 1.3 Safekeeping Keep this technical file and all supporting documents ready at hand and accessi- ble for future use at all times. 1.4 Notation conventions 1.4.1 Hazard communication system Warnings in this technical file are displayed as follows. 1.4.1.1 Warning relating to section Warnings relating to sections refer to entire chapters or sections, sub-sections or several paragraphs within this technical file. Warnings relating to sections use the following format: 8459861/04 EN Introduction 5 WARNING Type of danger! Source of the danger and outcome. Action Action 1.4.1.2 Embedded warning information Embedded warnings refer to a particular part within a section. These warnings apply to smaller units of information than the warnings relating to sections. Em- bedded warnings use the following format: DANGER! Instruction for avoiding a dangerous situation. 1.4.1.3 Signal words in warning notices Signal word Meaning DANGER Indicates a hazardous situation which, if not avoided, will result in death or serious injury. WARNING Indicates a hazardous situation which, if not avoided, could result in death or serious injury. CAUTION Indicates a hazardous situation which, if not avoided, could result in mi- nor or moderate injury. NOTICE Indicates measures to be taken to prevent damage to property. Table 1: Signal words in warning notices 1.4.2 Information system Information is designed to simplify and improve understanding of particular procedures. In this technical file it is laid out as follows: Important information. i 1.4.3 Instruction system This technical file contains single-step and multi-step instructions. Single-step instructions Instructions which consist of only a single process step are structured as fol- lows: Aim of action Requirements (optional). Step 1 of 1. Result of step (optional). Result of action (optional). Multi-step instructions Instructions which consist of several process steps are structured as follows: 6 Introduction 8459861/04 EN Aim of action Requirements (optional). 1. Step 1. Result of step (optional). 2. Step 2. Result of step (optional). Result of action (optional). 1.4.4 Typographic conventions Typographic convention Purpose Example UPPERCASE Operating controls, switches ON/OFF [Brackets] PC keyboard [Ctrl] + [Alt] Bold Software operating controls Press Continue button …>…>… Menu paths Parameter > Control parameter Italics System messages, error messages, sig- Function monitoring alarm triggered nals [► Number of pages] Cross reference [► Page 41]. Dotted underscore............................................. Glossary entry, abbreviations, definitions, Glossary entry........................ etc. Table 2: Typographic conventions used in this technical file 8459861/04 EN Introduction 7 2 Safety – Read this technical file through to familiarize yourself with the product. – This technical file is a part of the product. – Read and observe the safety instructions provided in this chapter. – Read and observe the warnings in this technical file in order to avoid func- tion-related dangers. – The product is manufactured on the basis of state-of-the-art technology. Nevertheless, risks to life and limb for the user or impairment of the product and other material assets due to the function may arise in the event of im- proper use. 2.1 Appropriate use The product is a monitoring system for monitoring on-load tap-changers on power transformers/reactors. You can use the product to detect time and am- plitude anomalies in the progression of the vibro-acoustic signal sent by the on- load tap-changer and receive event messages when anomalies are detected. The product is designed solely for use in electrical energy systems and facilities. It may only be used in compliance with the requirements and conditions listed in this technical file as well as the warnings in this technical file and the warn- ings posted on the product. This applies throughout the service life of the prod- uct, from delivery, installation and operation to removal and disposal. The following is considered appropriate use: – Only use the product with the on-load tap-changer and the motor-drive unit specified in the order. – Only use the product for on-load tap-changers that have not already been damaged. – Operate the product in accordance with this technical file, the agreed-upon delivery conditions and the technical data. – Ensure that all necessary work is performed by qualified personnel only. – Only use the equipment and special tools included in the scope of delivery for the intended purpose and in accordance with the specifications of this technical file. – Only use the product on transformers with insulated add-on parts after ap- proval by Maschinenfabrik Reinhausen GmbH (special version required). – Only operate the product in industrial areas. Observe the notices in this tech- nical file regarding electromagnetic compatibility and the technical data. 2.2 Inappropriate use – The product is not suitable for extending the permitted service life of the on- load tap-changer specified by the on-load tap-changer manufacturer. – The product is not a protective device. Do not use it to handle safety-related functions. – Risk of explosion and fire from highly flammable or explosive gases, vapors, or dusts. Do not operate the product in areas at risk of explosion. 8 Safety 8459861/04 EN – The product is not intended for use in environments subject to strong corro- sion effects. – Unauthorized or inappropriate changes to the product may lead to personal injury, material damage and operational faults. Only modify the product after consultation with Maschinenfabrik Reinhausen GmbH. 2.3 Fundamental safety instructions To prevent accidents, malfunctions and damage as well as unacceptable ad- verse effects on the environment, those responsible for transport, installation, operation, maintenance and disposal of the product or parts of the product must ensure the following: Personal protective equipment Loosely worn or unsuitable clothing increases the danger of becoming trapped or caught up in rotating parts and the danger of getting caught on protruding parts. This poses a danger to life and limb. – Wear appropriate personal protective equipment such as a helmet, work gloves, etc. for the respective activity. – Never wear damaged personal protective equipment. – Never wear rings, necklaces, or other jewelry. – If you have long hair, wear a hairnet. Work area Untidy and poorly lit work areas can lead to accidents. – Keep the work area clean and tidy. – Make sure that the work area is well lit. – Observe the applicable laws for accident prevention in the relevant country. Working during operation The product may only be operated in a sound, operational condition. Otherwise it poses a danger to life and limb. – Regularly check the operational reliability of safety equipment. – Comply with the inspection work, maintenance work and maintenance inter- vals described in this technical file. Securing the motor-drive unit If you open the motor-drive unit during operation, there is a danger of electric shock due to live components behind the swing frame. – Secure the motor-drive unit against unauthorized opening during operation by using a padlock. – The motor-drive unit may only be opened by an electrically skilled person. Safety markings Warning signs and safety information plates are safety markings on the prod- uct. They are an important aspect of the safety concept. – Observe all safety markings on the product. – Make sure all safety markings on the product remain intact and legible. – Replace safety markings that are damaged or missing. Ambient conditions To ensure reliable and safe operation, the product must only be operated under the ambient conditions specified in the technical data. – Observe the specified operating conditions and requirements for the installa- tion location. 8459861/04 EN Safety 9 Modifications and conversions Unauthorized or inappropriate changes to the product may lead to personal in- jury, material damage and operational faults. – Only modify the product after consultation with Maschinenfabrik Reinhausen GmbH. Spare parts Spare parts not approved by Maschinenfabrik Reinhausen GmbH may lead to physical injury, damage to the product and malfunctions. – Only use spare parts that have been approved by Maschinenfabrik Rein- hausen GmbH. – Contact Maschinenfabrik Reinhausen GmbH. 2.4 Personnel qualification The person responsible for assembly, commissioning, operation, maintenance and inspection must ensure that the personnel are sufficiently qualified. Electrically skilled person The electrically skilled person has a technical qualification and therefore has the required knowledge and experience, and is also conversant with the applicable standards and regulations. The electrically skilled person is also proficient in the following: – Can identify potential dangers independently and is able to avoid them. – Is able to perform work on electrical systems. – Is specially trained for the working environment in which (s)he works. – Must satisfy the requirements of the applicable statutory regulations for acci- dent prevention. Electrically trained persons An electrically trained person receives instruction and guidance from an electri- cally skilled person in relation to the tasks undertaken and the potential dangers in the event of inappropriate handling as well as the protective devices and safety measures. The electrically trained person works exclusively under the guidance and supervision of an electrically skilled person. Operator The operator uses and operates the product in line with this technical file. The operating company provides the operator with instruction and training on the specific tasks and the associated potential dangers arising from improper han- dling. Technical Service We strongly recommend having maintenance, repairs and retrofitting carried out by our Technical Service department. This ensures that all work is per- formed correctly. If maintenance is not carried out by our Technical Service de- partment, please ensure that the personnel who carry out the maintenance are trained and authorized by Maschinenfabrik Reinhausen GmbH to carry out the work. Authorized personnel Authorized personnel are trained by Maschinenfabrik Reinhausen GmbH to carry out special maintenance. 10 Safety 8459861/04 EN 2.5 Personal protective equipment Personal protective equipment must be worn during work to minimize risks to health. – Always wear the personal protective equipment required for the job at hand. – Never wear damaged personal protective equipment. – Observe information about personal protective equipment provided in the work area. Protective clothing Close-fitting work clothing with a low tearing strength, with tight sleeves and with no protruding parts. It mainly serves to protect the wearer against being caught by moving machine parts. Safety shoes To protect against falling heavy objects and slipping on slip- pery surfaces. Safety glasses To protect the eyes from flying parts and splashing liquids. Visor To protect the face from flying parts and splashing liquids or other dangerous substances. Hard hat To protect against falling and flying parts and materials. Hearing protection To protect against hearing damage. Protective gloves To protect against mechanical, thermal, and electrical haz- ards. Table 3: Personal protective equipment 8459861/04 EN Safety 11 3 IT security Observe the following recommendations to operate the product safely. 3.1 General – Ensure that only authorized personnel have access to the device. – Only use the device within an ESP (electronic security perimeter). Do not connect the device to the Internet in an unprotected state. Use mechanisms for vertical and horizontal network segmentation and security gateways (fire- walls) at the transition points. – Ensure that the device is only operated by trained personnel who are familiar with IT security. – Check regularly whether software updates are available for the device and perform the updates. 3.2 Commissioning Observe the following recommendations for device commissioning: – User IDs must be unique and assignable. Do not use a "Group account" func- tion or the "Auto login" function. – Activate the "Auto logout [►Section 8.1.1.2, Page 65]" function. – Restrict the rights of the individual user groups as much as is feasible; this helps avoid errors during operations. A user with the "Operator" role, for ex- ample, should only perform operations and should not be able to change any device settings. – Delete or disable the default "admin" user ID. This requires first creating a new user account with the "Administrator" role. You can then use it to delete or disable the default "admin" account. – Deactivate service user access. – Enable SSL/TLS encryption [►Section 8.1.1, Page 64]; access to the device is then only possible using the SSL/TLS protocol. In addition to encrypting communication, this protocol also checks the authenticity of the server. – Integrate the device into a public key infrastructure. Create your own SSL cer- tificates for this if necessary and then import them. – Connect the device to a central log server by using the syslog interface [►Section 8.1.4, Page 69]. – Media converter with managed switch (assembly SW 3-3): – Change user account and password. – Disable unnecessary services. 3.3 Operation Observe the following recommendations during device operation: – Change the password at regular intervals. – Export the security log [►Section 8.1.15.2, Page 104] at regular intervals. – Check the log files regularly for unauthorized system access and other secu- rity-related events. 12 IT security 8459861/04 EN – Media converter with managed switch (assembly SW 3-3): Check at regular intervals whether the manufacturer Belden/Hirschmann has released an up- date for the product “EES 25” and, where necessary, perform a firmware up- date. 3.4 Interfaces The device uses the following interfaces for communication: Figure 1: Assembly SW 3-3 interfaces Interface Protocol Port Description ETH 2.3, TCP 22 SSH 1 ETH 2.4 23 Telnet 1 80 HTTP for web-based visualization 1 443 HTTPS for web-based visualization 1 UDP 161 SNMP 1 Table 4: Interfaces and open ports of the SW 3-3 assembly 3.5 Encryption standards The device supports the following TLS versions: – TLS 1.2 – TLS 1.3 The device uses the following cipher suites for a TLS-secured connection: 1 Port is closed if the corresponding service is disabled. 8459861/04 EN IT security 13 The device uses the SHA256 hash function to save passwords. The SW 3-3 assembly supports the following TLS version: – TLS 1.2 The assembly uses the following cipher suites for a TLS-secured connection: Key exchange Authentication Encryption Key length Operating Hash function mode TLS ECDHE RSA WITH AES 128 GCM SHA265 DHE CBC SHA Table 5: Cipher suite The device uses the following encryption standards in accordance with techni- cal directive TR-02102-4 from Germany's Federal Office for Information Secu- rity: – Key agreement: – diffie-hellman-group1-sha1 – diffie-hellman-group14-sha1 – diffie-hellman-group16-sha512 – diffie-hellman-group18-sha512 – diffie-hellman-group-exchange-sha256 – ecdh-sha2-nistp256 – Server authentication: – ssh-rsa – rsa-sha2-512 – rsa-sha2-256 – Encryption algorithms: – aes128-ctr – [email protected] – [email protected] – MAC protection: – hmac-sha1 – hmac-sha2-256 – [email protected] – [email protected] – Compression: – None – [email protected] – Zlib Also refer to 2 TLS version [► 67] 14 IT security 8459861/04 EN 4 Product description 4.1 Variants The device is available in the following versions: – MSENSE® VAM: – Standalone version in the control cabinet – ETOS® ED/TD with MSENSE® VAM function: – Integration solution in the motor-drive unit – ETOS® IM with MSENSE® VAM function: – Integration solution in the customer control cabinet (pluggable modules) – MSENSE® BM with MSENSE® VAM function 4.2 Scope of delivery Please note the following: – Check the shipment for completeness using the shipping documents. – Store the parts in a dry place until installation. Depending on the product version, the following MSENSE® VAM monitoring system assemblies are included in the scope of supply. Depending on the order, additional ETOS® modules that are not listed in these instructions may also be used. Also observe the corresponding operating instructions. MSENSE® VAM: Standalone version in the control cabinet – VI 4 vibration sensor input module – VAM sensor assembly (including VS 1 vibration sensor, adapter screw and kick guard) – Sensor cable for VS 1 vibration sensor – Analog AIO 2 or AIO 4 inputs/outputs – G1 PULS DIMENSION QS3.241 power supply – Digital DIO 28-15 or DIO 42-20 inputs/outputs – CPU II (central processing unit) – Control cabinet – Optional: MC 2-2 media converter – Optional: SW 3-3 media converter with managed switch – Optional: Display – Optional: PT100 for OLTC oil temperature (temperature pocket must be available in the on-load tap-changer head cover)1) ETOS® ED/TD with MSENSE® VAM option: Integration solution in the motor-drive unit – VI 4 vibration sensor input module – VAM sensor assembly (including VS 1 vibration sensor, adapter screw and kick guard) – Sensor cable for VS 1 vibration sensor – Optional: MC 2-2 media converter – Optional: SW 3-3 media converter with managed switch – Optional: Display – Optional: PT100 for OLTC oil temperature (temperature pocket must be available in the on-load tap-changer head cover)1) 8459861/04 EN Product description 15 ETOS® IM with MSENSE® VAM option: Integration solution in the cus- tomer control cabinet (pluggable modules) – VI 4 vibration sensor input module – VAM sensor assembly (including VS 1 vibration sensor, adapter screw and kick guard) – Sensor cable for VS 1 vibration sensor – Analog AIO 2 or AIO 4 inputs/outputs – G1 PULS DIMENSION QS3.241 power supply – Digital DIO 28-15 or DIO 42-20 inputs/outputs – CPU II (central processing unit) – Optional: MC 2-2 media converter – Optional: SW 3-3 media converter with managed switch – Optional: Display – Optional: PT100 for OLTC oil temperature (temperature pocket must be available in the on-load tap-changer head cover)1) 1) Oil temperature recording is a prerequisite for the self-learning of the yellow limit value curve. As an alternative to recording the OLTC oil temperature, the top-oil temperature can be used. 4.3 Function description The product is a monitoring system for monitoring vibro-acoustic signals from on-load tap-changers. You can use the product to detect time and amplitude anomalies in the vibro-acoustic signal progression and receive event messages when anomalies are detected. The on-load tap-changer is equipped with measuring equipment that records the vibro-acoustic signal in the system throughout the entire tap change se- quence and analyses it immediately upon completion. In addition, the system determines the changed tap position and the oil temperature in the on-load tap- changer. Using the implemented algorithms, the monitoring system can reliably detect any potential anomalies that occur in the vibro-acoustic signal progression, tak- ing the temperature variations of the on-load tap-changer oil into account. 16 Product description 8459861/04 EN Status message The MSENSE® VAM monitoring system produces a 3-stage status message: Status Device/visualization display SCADA/digital output re- mote signaling Normal OK message through blue No remote signaling status message Warning The first and the second No remote signaling anomalies in an evaluation cluster are indicated via a yellow status message in the VAM analysis (Information menu). Alarm A third anomaly arising in an This event message is trans- evaluation cluster or the mitted to a connected third successive anomaly SCADA system. triggers an additional event In addition, it can also be message (Events menu). sent to a digital output. 4.4 Performance features The MSENSE® VAM monitoring system monitors the vibro-acoustic signals from on-load tap-changers and has the following : – Monitoring on-load tap-changers/reactors in accordance with the technical specification in the order confirmation – Suitable for on-load tap-changers with oil-switch and vacuum-switch technol- ogy – Recording of the vibro-acoustic signals during on-load tap-changer operation via automatic triggering – Evaluation of the vibro-acoustic signal progression with regard to time and amplitude anomalies – Self-learning limit value at an oil temperature above 15 °C, which moves to- wards the signal progression with increasing tap-change frequency Approxi- mately 5 tap-change operations per evaluation cluster (e.g. 5x from step 1 to step 2 in reverse tap-change operation) are necessary before the first limit value curve is displayed. The signals are also evaluated below 15 °C, but the limit value is not adjusted. – Display and recording of the measured and calculated values – Status messages via digital outputs – Web-based visualization – SCADA – IEC 60870-5-101 – IEC 60870-5-103 – IEC 60870-5-104 – IEC 61850 (edition 1 and edition 2) – Modbus (RTU, TCP, ASCII) – DNP3 8459861/04 EN Product description 17 4.5 Design This chapter contains an overview of the design of the monitoring system: Figure 2: Design, example of single-column application 1 On-load tap-changer head cover 2 Vibration sensor with kick guard 3 Control cabinet 4 Sensor cable 5 Transformer 18 Product description 8459861/04 EN 4.5.1 VS 1 sensor assembly Figure 3: VAM sensor assembly 1 Sensor cable 2 Kick guard 3 Vibration sensor 4 Adapter 4.5.2 Control cabinet Depending on the order, the electronic assemblies are either already installed in a control cabinet or are supplied as individual components for mounting on a cap rail. The following two figures show a design example for the standalone version. 8459861/04 EN Product description 19 4.5.2.1 Display elements and operating controls The control cabinet contains the following display elements and operating con- trols: Figure 4: Display elements and operating controls (example) 1 Indicator lamp H1: yellow = "Anomaly 2 Indicator lamp H2: green = "No anom- detected" alies" 3 Service interface 20 Product description 8459861/04 EN 4.5.2.2 Control cabinet layout The following figure shows an example layout in the control cabinet with the most important electronic assemblies for the MSENSE® VAM. The order-specific details can be found in the connection diagram provided. Figure 5: Control cabinet layout (example) A10 CPU II (central processing unit) A22 VI 4 vibration sensor input module A18 Analog AIO 2 or AIO 4 inputs/outputs G1 Voltage supply X19 Plug socket F13 Miniature circuit breaker for heating F14 Miniature circuit breaker for control F25 Residual current circuit breaker plug system A19 Digital inputs/outputs DIO 28-15 The functions of the device's individual assemblies are described in the follow- ing section. You can find more information about these assemblies in the Tech- nical data [►Section 13, Page 136] section. 4.5.2.2.1 Power supply QS3.241 The PULS DIMENSION QS3.241 assembly supplies power to the ISM® assem- blies. Figure 6: PULS DIMENSION QS3.241 assembly 8459861/04 EN Product description 21 4.5.2.2.2 CPU II The CPU II assembly is the central computing unit for the device. It contains the following interfaces: – Internal system interface RS232 (COM1) – Serial interface RS232/485 (COM2) – 3x Ethernet (ETH 1, ETH 2.1, ETH 2.2) – USB (USB 2.0) – 2x CAN bus (CAN 1, CAN 2) CPU RUN INIT 9 9 9 COM 1 CAN 1 CAN 2 ERR 2 4 6 0 8 L 1 1 1 E C A 2 4 6 8 H C A TEST 9 PROG COM 2 RUN USB2.0 1 24V DC ETH 1 ETH 2.1 ETH 2.2 + - Figure 7: CPU assembly 4.5.2.2.3 DIO 28-15 digital inputs and outputs The DIO 28-15 assembly makes 28 inputs and 15 outputs (6 N/O contacts, 9 change-over contacts) available. Figure 8: DIO 28-15 assembly Warning of a danger point. Read the information given in the product operating instructions. Warning of dangerous electrical voltage. Table 6: Safety-relevant symbols on the assembly 22 Product description 8459861/04 EN 4.5.2.2.4 Analog inputs and outputs (AIO 2) The AIO 2 assembly provides 2 channels for analog inputs and outputs. In ac- cordance with the device configuration, the AIO assembly supports one of the following signal types: Input Output Voltage Current Voltage Current 0 to 10 V 0...20 mA 0 to 10 V 0...20 mA 4...20 mA 4...20 mA Resistance measurement (e.g. PT100, resistor contact series) Table 7: Signal types supported by the AIO assembly Figure 9: AIO 2 assembly 4.5.2.2.5 Vibroacoustics VI 4 The VI 4 assembly records the vibration sensor signals via an IEPE interface. The abbreviation IEPE refers to an industry standard for piezo-electrical sensors (IEPE = Integrated Electronics Piezo Electric). Figure 10: Assembly VI 4 The measured signals are processed with evaluation algorithms. 4.5.2.2.6 System networking MC 2-2 The MC 2-2 assembly is a media converter, which converts 2 electrical connec- tions (RJ45) to one fiber-optic cable connection each. Each is converted inde- pendently of the other. The following interfaces are available: – 2x RJ45 (ETH12, ETH22) – 2x Duplex-LC (SFP module) (ETH11, ETH21) 8459861/04 EN Product description 23 The media converter is designed to be transparent for the network and i does not have its own IP address. Figure 11: MC 2-2 assembly 4.5.2.2.7 System networking SW 3-3 The assembly SW 3-3 is a media converter with managed switch. It combines two independent functions and provides you with the following interfaces: – A media converter converts an electric connection (RJ45) into a fiber-optic cable connection – RJ45 (ETH12) – Duplex-LC (SFP module) (ETH11) – Managed switch with redundancy function (PRP or RSTP) – 2x RJ45 (ETH23, ETH24), device-internal connection – 2x Duplex-LC (SFP module) (ETH21, ETH22), redundancy connection The following redundancy functions are available to you according to your or- der: – PRP (standard setting) – RSTP Figure 12: SW 3-3 assembly 24 Product description 8459861/04 EN 4.6 Main screen The visualization start screen of the MSENSE® VAM monitoring system varies depending on the product version. Their is a difference between the following product versions: 4.6.1 Standalone version On the start screen of the standalone version, the vibro-acoustic signal progres- sion of the last recorded and evaluated on-load tap-changer operation is shown in blue. Clicking on the Home button always returns you to this screen. Once the recording of a tap-change operation is complete, the calculation and evaluation is performed. With complex switching sequences and a high switch- ing frequency, it may take a few minutes before the latest tap-change operation is displayed. Figure 13: Start screen The upper curve in yellow indicates the self-learned limit value. In addition, the corresponding properties of the tap-change operation are shown: – Type of OLTC tap-change operation (e.g. reverse tap-change operation) – Start and end position of the tap-change – Date and time of the tap-change operation – Oil temperature of the on-load tap-changer – Number of OLTC tap-change operations registered until now – Status display with the following color code: Color code Meaning Blue No anomalies: Plausibility criteria met and limit values not exceeded Yellow Limit value was exceeded Gray The evaluation could not be carried out 8459861/04 EN Product description 25 4.6.2 Integration solution Figure 14: Main screen 1 Display area 2 Secondary navigation 3 Primary navigation 4 Status bar Click on the on-load tap-changer in the graphic to enter the overview screen for the vibro-acoustically measured tap-change operations of the on-load tap- changer (OLTC). Primary navigation The primary navigation on the right edge of the screen is always structured the same way, regardless of the product version. The buttons of the primary navi- gation have the following functions: Button Function Home Switch to the start screen Events Switch to the display of events detected Information Switch to the display of information on: – Installed hardware – OLTC – Tap-change operation statistics – OLTC oil temperature curve – VAM analysis Recorder Switch to the display of statistics for tap position and oil tem- perature 26 Product description 8459861/04 EN 4.7 Operating concept You can operate the device using the controls on the front panel or using the web-based ISM™ Intuitive Control Interface visualization on a PC. The scope of function and structure of both options is virtually identical. User rights and user roles The device is equipped with a rights system and a roles system. The display and access rights to device settings or events can therefore be controlled at the user level. You can configure the rights system and roles system to meet your require- ments. You will find more information on user rights in the User administration [►Section 8.1.12, Page 96] section. You can only modify the device settings or parameters if you have the nec- i essary user rights. Logging on, logging off and changing users The control of access rights to device settings and parameters is user-based. Various users can log in at the same time (e.g. via the visualization) and access the device. If you want to operate the device via the controls and visualization at the i same time, you have to log in on the device and via the visualization. 1. Select the LOGIN or CHANGE button in the status line. 2. Enter your user name and password and select the OK button. The name of the logged-in user appears in the status line. To log out as a user, proceed as follows: Press the LOGOUT button in the status line. Navigation If you are operating the device using the controls on the front panel, you can use the rotary knob to navigate through the entire menu. The menu currently selected has a blue border. To open the highlighted menu, you have to press the key. Pressing the key returns you to the previous menu level. If you are operating the device using the web-based visualization, you can navi- gate by clicking on the appropriate buttons. Example 1. Go to Settings. 2. Go to Parameters. 3. Go to System. 4. Go to Time synchronization. 5. Select Time. In these operating instructions, the path for navigating to a parameter is always shown in an abridged form: Go to Settings > Parameters > System > Time syn- chronization. Setting parameters There are various ways to configure the settings, depending on the parameter. 8459861/04 EN Product description 27 Selecting from a list To select a list entry, proceed as follows: 1. Use the rotary knob to navigate to the list and press the key. Figure 15: Select an entry from a list 2. Use the rotary knob to highlight the list entry and press the key. 3. Press the Accept button to save the modified parameter. Entering a value To enter a value, proceed as follows: 1. Use the rotary knob to select the value field and press the key. If operating via the front panel, the numerical keypad appears. Figure 16: Entering a value 2. Enter the desired value and confirm with. 3. Press the Accept button to save the modified parameter. 28 Product description 8459861/04 EN Entering text 1. Use the rotary knob to select the text box and press the key. If operating via the front panel, the keyboard appears. Figure 17: Entering text 2. Enter the desired text and confirm with. 3. Press the Accept button to save the modified parameter. Parameter search You can use the quick search function in the parameter menu to search for a parameter. Enter the name of the desired parameter in the Search entry field. Figure 18: Quick search 8459861/04 EN Product description 29 Expert mode The device has an expert mode for entering the parameters. You can enter the parameters directly on the overview screen of the respective menu in this mode. Figure 19: Expert mode 1. Go to Settings > Parameters. 2. Select the Expert mode checkbox. Expert mode is active. Hiding/showing parameters Depending on how you set the parameters, the device will hide or show addi- tional parameters related to this function. 30 Product description 8459861/04 EN 5 Packaging, transport and storage 5.1 Suitability NOTICE Property damage due to incorrectly stacked crates! Stacking the crates incorrectly can lead to damage to the packaged goods. The outer marking on the packaging states if, for example, the on-load tap- changer or selector has been packed upright. Never stack these crates. General rule: Do not stack crates above a height of 1.5 m. For other crates: Only stack up to 2 equally sized crates on top of one an- other. The packaging is suitable to ensure undamaged and fully functional means of transportation in compliance with local transportation laws and regulations. The packaged goods are packed in a sturdy crate. This crate ensures that, when in the intended transportation position, the packaged goods are stabilized to prevent impermissible changes in position, and that none of the parts touch the loading surface of the means of transport or touch the ground after unloading. Sealed packaging surrounds the packaged goods with plastic foil on all sides. The packaged goods are protected from humidity using a desiccant. The plastic foil was bonded after the desiccant is added. 5.2 Markings The packaging bears a signature with instructions for safe transport and correct storage. The following symbols apply to the shipment of non-hazardous goods. Adherence to these symbols is mandatory. Protect against Top Fragile Attach lifting Center of mass moisture gear here Table 8: Shipping pictograms 8459861/04 EN Packaging, transport and storage 31 5.3 Transportation, receipt and handling of ship- ments WARNING Danger of death or severe injury! Danger of death or serious injuries due to tipping or falling load. Only transport the crate when closed. Do not remove the securing material used in the crate during transport. If the product is delivered on a pallet, secure it sufficiently. Only trained and authorized persons may select the sling gear and secure the load. Do not walk under the suspended load. Use means of transport and lifting gear with a sufficient carrying capacity in accordance with the weight stated on the delivery slip. In addition to oscillation stress, jolts must also be expected during transporta- tion. In order to prevent possible damage, avoid dropping, tipping, knocking over and colliding with the product. If a crate tips over, falls from a certain height (e.g. when slings tear) or experi- ences an unbroken fall, damage must be expected regardless of the weight. Every delivered shipment must be checked for the following by the recipient be- fore acceptance (acknowledgment of receipt): – Completeness based on the delivery slip – External damage of any type The checks must take place after unloading when the crate or transport con- tainer can be accessed from all sides. Visible damage If external transport damage is found upon receipt of the shipment, proceed as follows: – Immediately record the identified transport damage in the shipping docu- ments and have this countersigned by the carrier. – In the event of severe damage, total loss or high damage costs, immediately notify the manufacturer and the relevant insurance company. – After identifying damage, do not modify the condition of the shipment fur- ther and retain the packaging material until an inspection decision has been made by the transport company or the insurance company. – Record the details of the damage immediately on site together with the car- rier involved. This is essential for any claim for damages. – Photograph damage to packaging and packaged goods. This also applies to signs of corrosion on the packaged goods due to moisture inside the packag- ing (rain, snow, condensation). – NOTICE! Damage to packaged goods due to damaged sealed packaging. If the product is delivered in sealed packaging, check the sealed packaging im- mediately. If the sealed packaging is damaged, do not under any circum- stances install or commission the packaged goods. Either re-dry the dried packaged goods as per the operating instructions, or contact the manufac- turer to agree on how to proceed. – Identify the damaged parts. Hidden damage When damages are not determined until unpacking after receipt of the ship- ment (hidden damage), proceed as follows: – Make the party responsible for the damage liable as soon as possible by tele- phone and in writing, and prepare a damage report. – Observe the time periods applicable to such actions in the respective coun- try. Inquire about these in good time. 32 Packaging, transport and storage 8459861/04 EN With hidden damage, it is very hard to make the transportation company (or other responsible party) liable. Any insurance claims for such damages can only be successful if relevant provisions are expressly included in the insurance terms and conditions. 5.4 Storage of shipments Packaged goods dried by Maschinenfabrik Reinhausen Upon receipt of the shipment, immediately remove the packaged goods dried by Maschinenfabrik Reinhausen from the sealed packaging and store air-tight in dry insulating fluid until used if the packaged goods were not supplied in insu- lating fluid. Non-dried packaged goods Non-dried packaged goods but with a functional sealed packaging can be stored outdoors when the following conditions are complied with. When selecting and setting up the storage location, ensure the following: – Protect stored goods against moisture (flooding, water from melting snow and ice), dirt, pests such as rats, mice, termites and so on, and against unau- thorized access. – Store the crates on timber beams and planks as a protection against rising damp and for better ventilation. – Ensure sufficient carrying capacity of the ground. – Keep entrance paths free. – Check stored goods at regular intervals. Also take appropriate action after storms, heavy rain or snow and so on. Protect the packaging foil from direct sunlight so that it does not disintegrate under the influence of UV rays, which would cause the packaging to lose its sealing function. If the product is installed more than 6 months after delivery, suitable measures must be taken without delay. The following measures can be used: – Correctly regenerate the drying agent and restore the sealed packaging. – Unpack the packed goods and store in a suitable storage space (well venti- lated, as dust-free as possible, humidity < 50% where possible). 5.5 Unpacking shipments and checking for trans- portation damages – NOTICE! Transport the packaged crate to the place where the packaged goods are to be installed. Do not open the sealed packaging until just before installation. Otherwise, damage to the packaged goods may occur due to in- effectively sealed packaging. – WARNING! When unpacking, check the condition of the packaged goods. Place the packaged goods in an upright crate and protect it from tipping out. Otherwise, the packaged goods may become damaged and serious injuries may result. – Check the completeness of the accessories kit using the delivery slip. 8459861/04 EN Packaging, transport and storage 33 Attachment points for lifting gear WARNING Danger of death and damage to property! Danger of death and damage to property due to tipping or falling load! Only trained and authorized persons may select the sling gear and secure the load. Do not walk under the suspended load. Use means of transport and lifting gear with a sufficient carrying capacity in accordance with the weight stated in the Technical data [►Section 13, Page 136] section. – WARNING! Serious injuries and damage to the control cabinet due to fall- ing load. Attach the lifting gear such that the cable angle is always less than 45° in relation to the vertical. Figure 20: Maximum permissible cable angle for the lifting-gear limit stop of the control cabi- net – WARNING! Serious injuries due to the control cabinet tipping and dam- age to the cable gland if the control cabinet is set down, transported or stored upright. Only set down, transport and store the control cabinet on its back. – Only remove the control cabinet from the crane once it has been fully con- nected to the transformer. 34 Packaging, transport and storage 8459861/04 EN 6 Mounting This chapter describes how to correctly mount and connect the device. Note the connection diagrams provided. DANGER Electric shock! Risk of fatal injury due to electrical voltage. Always observe the following safety regulations when working in or on electrical equipment. Disconnect the equipment. Lock the equipment to prevent an unintentional restart. Make sure all poles are de-energized. Ground and short-circuit. Cover or cordon off adjacent energized parts. NOTICE Damage to the device! Electrostatic discharge may cause damage to the device. Take precautionary measures to prevent the build-up of electrostatic charges on work surfaces and personnel. 6.1 Installing the Cap rail modules / control cabi- net 6.1.1 Installing the cap rail modules With the MSENSE® VAM product version as an integration solution in the cus- tomer control cabinet, the cap rail modules must be installed in a suitable con- trol cabinet, taking the EMC standards into consideration. This section does not apply for other product versions. 6.1.1.1 Minimum distances NOTICE Damage to the device! Insufficient circulation of ambient air can result in damage to the device due to overheating. Keep the ventilation slots clear. Ensure sufficient distance to neighboring components. Only mount device in horizontal position (ventilation slots are at the top and bottom). Reliable operation of the device in the permitted temperature range requires that you maintain the following minimum distances to the control cabinet and to neighboring components: Minimum distance To the floor of the control cabinet 88.9 mm (3.5 in) Corresponds to 2 RU To the roof of the control cabinet Between assemblies on the bus bar and assemblies on the remote cap rail Table 9: Minimum distances in the control cabinet 8459861/04 EN Mounting 35 Figure 21: Example depiction of the minimum distances in a control cabinet For other installation types, contact Maschinenfabrik Reinhausen GmbH. 6.1.1.2 Fastening the cap rail The cap rail is required to mount a bus bar or a device's remote assemblies in a control cabinet. Only use the following types of cap rails in accordance with IEC 60715: – TH 35-7.5 – TH 35-15 The cap rail may not be painted or lacquered. WARNING Electric shock! Risk of fatal injury due to electrical voltage if the cap rail is not connected to the protective ground. Connect the cap rail to the protective ground securely (e.g. with a protec- tive conductor line-up terminal). Ensure that the cap rail is connected securely to the protective ground via a ground test after installation. NOTICE Damage to screw terminals! Tightening the screws too tightly can damage the screw terminals. When fastening the screw terminals, make sure that the tightening torque is 0.4 Nm. 36 Mounting 8459861/04 EN Fasten the cap rail to the rear panel of the switch cabinet using screws and contact washers or lock washers. The distance between the screws may be no more than 10 cm (3.94 in). in) 94 (3. m 0c ≤1 i n) 94 (3. m 0c ≤1 in) 94 (3. cm ≤ 10 Figure 22: Fastening the cap rail 6.1.1.3 Installing the bus rail on the cap rail The bus rail connects assemblies, such as the CPU, UI and AIO, to each other mechanically and electrically. The bus bar can contain different assemblies ac- cording to your order. WARNING! Mount the bus rail on the cap rail, ensuring that the bus rail engages correctly. Otherwise, it can result in electric shock due to a faulty connection to the protective ground. Figure 23: Hooking the bus rail into position 6.1.1.4 Installing the assembly at a distance on the cap rail The assemblies VI 4, CPU II and AIO 2/AIO 4 are delivered pre-mounted on the bus rail. The following optional assemblies must be mounted with an offset on a cap rail: – DIO 28-15 or DIO 42-20 – MC 2-2 – SW 3-3 – G1 (PULS) 8459861/04 EN Mounting 37 Cap rail fastened to the rear panel of the cabinet [►Section 6.1.1.2, Page 36]. WARNING! A faulty connection to the protective ground can lead to an electric shock in the event of faults. Hook the assembly onto the cap rail at the specified location, ensuring that the assembly engages correctly. Figure 24: Example: Hooking on DIO and SW assemblies 6.1.2 Integration solution in the ETOS® ED motor-drive unit With this product version, proceed in accordance with the ETOS® ED operating instructions and follow the safety information and warnings they contain when mounting the control cabinet on the transformer. Once mounted, continue in accordance with the section "Mounting the vibration sensor" [►Section 6.2, Page 41] in these instructions. 6.1.3 Fitting the control cabinet to the transformer This section describes how to mount the control cabinet of the stand-alone ver- sion to the transformer. The special design with vibration dampers must be used on transformers i where the control cabinet is subject to vibration. 38 Mounting 8459861/04 EN The control cabinet has four fixing attachments on the rear to secure it. To mount the control cabinet on the transformer, proceed as follows: 1. Attach four stud bolts (not supplied by MR) to the transformer tank. Figure 25: Fastening the stud bolts 2. Use the fixing attachments to attach the control cabinet to the stud bolts and align it vertically on the transformer tank. Figure 26: Attaching the control cabinet 8459861/04 EN Mounting 39 3. NOTICE! Secure the control cabinet without subjecting it to mechanical ten- sion. Otherwise, the control cabinet may be damaged. Figure 27: Fastening the control cabinet 4. Connect the grounding cable to the control cabinet and transformer tank, holding it against the control cabinet using a wrench of size 36. Figure 28: Connecting the grounding cable to the control cabinet 40 Mounting 8459861/04 EN 6.2 Mounting the vibration sensor When selecting the mounting position, ensure that there is the greatest i possible clearance to the drive motor, drive shafts and pipelines to reduce the disruptive effect on the vibro-acoustic recording to a minimum. To mount the VAM sensor, proceed as follows: 1. Remove one bolt from the on-load tap-changer cover. Reuse the washer that is present. Figure 29: Removing bolt 8459861/04 EN Mounting 41 2. NOTICE! Incorrect mounting can destroy the vibration sensor. Only apply a tool with wrench size 17 to the lower hexagon of the adapter to attach the sensor assembly. Place the washer over the open tapped hole and screw in the sensor assembly (vibration sensor with adapter and kick guard) with a torque of 34 Nm. Figure 30: Mounting the vibration sensor 6.3 Connecting the ISM® assemblies WARNING Electric shock! Risk of fatal injury due to connection errors. Ground the device using the grounding screw on the housing. 6.3.1 Cable recommendation Please note the following Maschinenfabrik Reinhausen recommendation when wiring the device. Excessive line capacitance can prevent the relay contacts from interrupting i the contact current. In control circuits operated with alternating current, take into account the effect of the line capacitance of long control cables on the function of the relay contacts. If you want to route Ethernet connections from a control cabinet or build- ing, we recommend the use of fiber-optic cables (in accordance with the IEC 61850-90-4 recommendation). The sensor cable is included in the scope of delivery and is oil-resistant and UV- resistant. 42 Mounting 8459861/04 EN Use oil-resistant versions for all connection cables outside of control cabi- i nets and versions also with additional UV resistance for those outside of buildings. Cable Assembly Cable type Conductor cross-section Max. length 2 Signal inputs DIO 28-15, Shielded 1.5 mm 400 m ( System > General > Language. Figure 45: Setting the language 2. Select the desired language from the list field. 3. Press the Accept button to save the modified parameter. The "Restart device" dialog appears. 4. Restart the device to apply the changed language setting. 56 Commissioning 8459861/04 EN 7.3 Downloading the operating instructions Download the operating instructions from the device to start device commis- sioning and parameterization. Select in the status line. The operating instructions will be downloaded. The document is also available for download in the MR Customer Portal and on our website www.reinhausen.com. 7.4 Setting date and time You can set the date and time in the following ways: – Manually – Time synchronization via control system (SCADA) – Time synchronization via SNTP time server If you are using a control system, the device automatically synchronizes the date and time with the control system. If you would like to use an SNTP time server, you must set the required parameters. For more information, refer to the information in the section Setting the device time [►Section 8.1.3, Page 67]. 7.5 Commissioning wizard If you want the device to help when setting the relevant parameters, you can use the commissioning wizard. The commissioning wizard provides a selection of parameters that you can configure in order. A detailed description of each of the parameters can be found in the Operation [►Section 8, Page 64] chapter. To call up the commissioning wizard, you will need the necessary access i rights [►Section 8.1.12, Page 96]. 8459861/04 EN Commissioning 57 To set the parameters with the help of the commissioning wizard, proceed as follows: 1. Log in as a user with the necessary access rights. 2. Go to Settings > Commissioning wizard. Information Commissioning wizard Home Welcome to the commissioning wizard Please select your language English Events If you change the language, a restart is necessary in order to apply the change. The commissioning assistant will continue automatically after the restart. Information Recorder Accept EN LOGOUT REBOOT admin 2023-11-13 14:39 MR Settings Figure 46: Commissioning wizard 3. Press the Accept button to launch the commissioning wizard. 4. Follow the on-screen instructions. Once you have entered all of the parameters relevant to commissioning, con- tinue with the function test. 7.6 Name plate You can enter the data of the nameplates from the transformer, on-load tap- changer and motor-drive unit and display it later. When operating devices with the MSENSE® VAM option, you must enter i the correct serial number for every on-load tap-changer. This entry is nec- essary to ensure the correct assignment of the vibro-acoustic records in the external database. 58 Commissioning 8459861/04 EN 7.6.1 Enter the name plate data You can enter the name plate data for the transformer, the on-load tap-changer and the motor-drive unit. Figure 47: Nameplate Go to Settings > Parameter > System > Name plate. 7.6.2 Displaying the name plate You can display the nameplate data for the transformer, on-load tap-changer, and motor-drive unit. Figure 48: Transformer nameplate Go to Information > System > Name plate > On-load tap-changer/Motor. 8459861/04 EN Commissioning 59 7.7 Setting the control system protocol (optional) If you need a control system protocol, you must set the parameters required for this. More information on this (e.g. data points) is to be found in the provided supplement for the control system protocol. You do not need to set additional parameters for commissioning. 7.8 Performing tests Please contact Maschinenfabrik Reinhausen GmbH (MR) if any aspect of i the tests is not clear. 7.8.1 Checking measured values and status of digital inputs and outputs Upon commissioning the device, check whether the measured values and sta- tus of digital inputs and outputs are plausible. To do so, use an additional mea- suring device if necessary to check the individual measured values. To display the measured values and status of the digital inputs and outputs, proceed as follows: 1. Go to Information > Hardware. 2. Select the individual assemblies one after another and check the individual measured values or the status of digital inputs and outputs. 3. If errors arise, check the measurement path and the wiring. 7.8.2 Performing function tests To ensure that the monitoring system functions seamlessly, you have to check the communication with the sensor and the automatic triggering function after each installation or maintenance action as follows: 1. Check that the wiring of the sensor and the signal feedback is in accordance with the supplied circuit diagram. 2. Perform a few on-load tap-changes for all positions and in both directions and check the plausibility of the signal progression including the envelope curve in the monitoring system. 3. Check that the signals are being recorded and saved correctly. 4. Optional: Check the control system. The monitoring system is ready to function. 7.8.3 Electrical high-voltage tests on the transformer It is essential that you ensure only trained, instructed expert personnel who are familiar with and comply with the pertinent safety and technical regulations, who are aware of the potential risks, and who consistently use the occupational safety equipment provided to prevent injury and property damage are assigned to perform such a transformer test. 60 Commissioning 8459861/04 EN Note the following points before performing high voltage tests on the trans- former: – Check that the ground connections on the control cabinet and the control cabinet fixings are free of paint. – Only perform a high voltage test with the control cabinet door closed. – Disconnect the sensor cable and other external connections to electronic components in the control cabinet to prevent damage through overvoltage. – When connecting