Amalgam Dental Materials PDF
Document Details
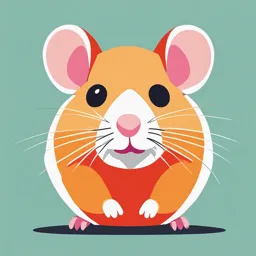
Uploaded by EnergyEfficientEpilogue
Dr.Masoun Suleman Aljebbeh
Tags
Summary
This document is a presentation on dental amalgam, covering its history, components, and properties. It discusses different types of amalgam alloys and their manufacturing processes, alongside handling characteristics and clinical aspects. The document explains different factors affecting amalgam, such as corrosion, creep, and dimensional change. It also touches on the safety considerations of using mercury in dental procedures.
Full Transcript
Amalgam Dr.Masoun Suleman Aljebbeh MSC in Operative Dentistry and Endodontics Amalgam is an alloy of mercury with one or more other metals. Dental amalgam alloy is an alloy that contains solid metals of silver ,tin ,copper and some times zinc. Dental amalgam is the alloy that results when mer...
Amalgam Dr.Masoun Suleman Aljebbeh MSC in Operative Dentistry and Endodontics Amalgam is an alloy of mercury with one or more other metals. Dental amalgam alloy is an alloy that contains solid metals of silver ,tin ,copper and some times zinc. Dental amalgam is the alloy that results when mercury is combined with the previously mentioned alloys to form a plastic mass. The mixing process of the alloy with the liquid mercury is called amalgamation or trituration. A mechanical device called an amalgamator or triturator. History 1819: A mercury-based dental amalgam filling was invented by the English chemist, Bell 1826: The dental amalgam mercury filling was first used in England and France. 1830: Crawcour brothers introduce amalgam to US– powdered silver coins mixed with mercury expanded on setting. 1840: The American Society of Dental Surgeons denounced the use of amalgams (the first amalgam war) 1859: the pro-mercury amalgam factions in America (ADA) (end of the first amalgam war) 1895: G.V. Black develops formula for modern amalgam alloy 67% silver, 27% tin, 5% copper, 1% zinc – overcame expansion problem. 1960’s: conventional low-copper lathe-cut alloys smaller particles – first generation high-copper alloys Dispersalloy (Caulk) – admixture of spherical Ag-Cu eutectic particles with conventional lathe-cut – eliminated gamma-2 phase 1970’s : first single composition spherical Tytin (Kerr) ternary system (silver/tin/copper) 1980’s: alloys similar to Dispersalloy and Tytin Why Amalgam? Inexpensive Ease of use Proven track record >100 years Familiarity Resin-free – less allergies than composite toughness and wear resistance amalgam has the ability to seal its margins Components in Amalgam Basic – Silver – Tin – Copper – Mercury Other – Zinc – Indium – Palladium Silver (Ag) – increases strength – increases expansion Tin (Sn) – decreases expansion – decreased strength – increases setting time Copper (Cu) – ties up tin reducing gamma-2 formation – increases strength – reduces corrosion reduces marginal corrosion. Mercury (Hg) – Hg activates reaction – Hg only pure metal that is liquid at room temperature. Other Components Zinc (Zn) decreases oxidation of other elements – sacrificial anode better clinical performance – less marginal breakdown delayed expansion with low Cu alloys – if contaminated with moisture during condensation. Indium (In) – decreases surface tension reduces amount of mercury necessary reduces emitted mercury vapor – reduces marginal breakdown – increases strength – must be used in admixed alloys. Palladium (Pd) – reduced corrosion – greater luster – example Valiant PhD (Ivoclar Vivadent) – 0.5% palladium The setting reaction of amalgam starts during trituration and progresses while condensation and carving take place. The working time of amalgam (the time that is needed to condense and carve) is not directly controlled by the dentist, as it is with light-activated composites. Amalgam is a direct restorative material that is held in place by mechanical retention. mechanical retention include undercuts and grooves. A silver-mercury matrix containing filler particles of silver-tin Filler (bricks) – Ag3Sn called gamma can be in various shapes – irregular (lathe-cut), spherical, or a combination Matrix – Ag2Hg3 called gamma 1 cement – Sn8Hg called gamma 2 voids Basic Setting Reactions Conventional low-copper alloys Admixed high-copper alloys Conventional Low-Copper Alloys Hg dissolves Ag and Sn from alloy Intermetallic compounds formed Ag3Sn + Hg Ag3Sn + Ag2Hg3 + Sn8Hg Gamma γ = Ag3Sn – unreacted alloy – strongest phase and corrodes the least – forms 30% of volume of set amalgam Gamma 1 (γ 1 ) = Ag2Hg3 matrix for unreacted alloy and 2nd strongest phase 10 µm grains binding gamma (γ) 60% of volume Gamma 2 (γ 2 ) = Sn8Hg – weakest and softest phase – corrodes fast – corrosion produces Hg which reacts with more gamma (γ) – 10% of volume – volume decreases with time due to corrosion Admixed High-Copper Alloys Ag enters Hg from Ag-Cu spherical particles Ag and Sn enter Hg from Ag3Sn particles Ag3Sn + Ag-Cu + Hg Ag3Sn + Ag-Cu + Ag2Hg3 + Cu6Sn5 Sn diffuses to surface of Ag-Cu particles – reacts with Cu to form (eta) Cu6Sn5 around unconsumed Ag-Cu particles Gamma 1 (γ 1 ) (Ag2Hg3 ) surrounds eta phase (Cu6Sn5 ) and gamma (γ) alloy particles (Ag3Sn) Classifications Based on copper(Cu) content Based on particle shape Copper Content Low-copper alloys – 4 to 6% Cu High-copper alloys – thought that 6% Cu was maximum amount due to fear of excessive corrosion and expansion – Now contain 9 to 30% Cu at expense of Ag BASED ON SHAPE OF ALLOY LATHECUT SPHERICAL ADMIXED The particles of the amalgam alloy may be formed by two methods. 1. The first method used to produce dental amalgam particles is grinding an ingot of metal to produce filings. Such amalgam alloys are called lathe-cut alloys 2. The second method used to produce dental amalgam particles is to spray molten metal into an inert atmosphere. The droplets cool as they fall, producing spherical alloys 3. Some products are a combination of both lathe-cut and spherical particles. These products are called admixed or blended alloys Particle Shape Lathe cut – low Cu New True Dentalloy – high Cu ANA 2000 Admixture – high Cu Dispersalloy, Valiant PhD Manufacturing Process Lathe-cut alloys – Ag & Sn melted together – alloy cooled – heat treat 400 ºC for 8 hours – grind, then mill to 25 - 50 microns – heat treat to release stresses of grinding Spherical alloys – melt alloy – atomize spheres form as particles cool – sizes range from 5 - 40 microns Trituration Mixing time – refer to manufacturer recommendations Overtrituration – “hot” mix sticks to capsule – decreases working / setting time – slight increase in setting shrinkage Undertrituration – grainy, crumbly mix Condensation Forces – lathe-cut alloys small condensers high force – spherical alloys large condensers less sensitive to amount of force vertical / lateral with vibratory motion – admixture alloys intermediate handling between lathe-cut and spherical Burnishing Pre-carve – removes excess mercury – improves margin adaptation Post-carve – improves smoothnes Handling Characteristics Spherical Advantages: easier to condense (around pins) hardens rapidly smoother polish disadvantages difficult to achieve tight contacts higher tendency for overhang Admixed – advantages easy to achieve tight contacts good polish – disadvantages hardens slowly – lower early strength Amalgam Properties Dimensional Change During amalgamation reaction, expansion and contraction occur simultaneously. Dissolution of γ particles contraction formation of γ-1 expansion. The overall dimensional change is therefore the sum of these two processes. Dimensional change is affected by many factors such as : o Moisture contamination o Particle size and shape o Type of the alloy o Manipulation : mercury/alloy, trituration and condensation. Dimensional Change: Delayed Excessive Expansion Zinc – containing alloy + Moisture Strength Amalgam restorations must resist the biting forces of occlusion. Dental amalgam has a high compressive strength, but the tensile and shear strengths are comparatively low. Therefore, amalgam should be supported by tooth structure for clinical success in the long term, which is approximately 10 to 20 years. Also, amalgam needs sufficient bulk. A thickness of 1.5 mm or more is needed to withstand occlusal forces. Creep Creep is a slow change in shape caused by compression. Creep of dental amalgam specimens is a common test and is included in the amalgam specification. It was once thought that creep provided a good indicator of clinical performance. However, when high copper amalgams were developed, creep became less of a predictor of clinical success. Tarnish is an oxidation that attacks the surface of the amalgam and extends slightly below the surface. It results from contact with oxygen, chlorides, and sulfides in the mouth. It causes a dark, dull appearance, but it is not very destructive to the amalgam Corrosion of Dental Amalgam Amalgam galvanically corrodes in much the same way that iron rusts. Galvanic corrosion occurs when two dissimilar metals exist in a wet environment. An electrical current flows between the two metals, and corrosion of one of the metals occurs. Corrosion occurs both on the surface and in the interior of the restoration. Surface corrosion discolors an amalgam restoration and may even lead to pitting. Surface corrosion also fills the tooth/amalgam interface with corrosion products, reducing microleakage An acidic environment promotes galvanic corrosion. Poor oral hygiene and a cariogenic diet will expose both teeth and restorative materials to a destructive environment. The same factors that promote caries will accelerate corrosion. Therefore, patient behavior can affect the longevity of amalgam and other restorations. Working and Setting Times Fast-set and slow-set versions of many brands are sold. The fastset version of a given product will set faster than does the regular-set version of that product. However, that same fast-set version may not be faster than the regular-set version of a different product. Mercury safety Safety should be considered for: – Patient – Operator – Environment How does mercury enter the human body – Skin contact – Vapor inhalation – Ingestion To protect the patient: – Use high volume suction – Rubber dam isolation Thank you