Production Factors Lecture Notes PDF
Document Details
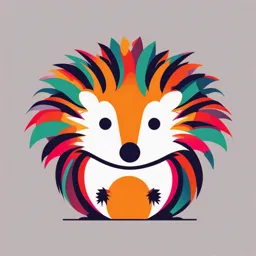
Uploaded by MerryHope2045
ACEC
2023
Tags
Summary
These lecture notes cover the production factors in an organization, including topics such as the use of management in an organization, division of power in managing an organization, economic theory versus business economics, and more. The document is part of a business or economics course for an undergraduate level.
Full Transcript
Production factors (dispositive work ≈ management) Content System of production factors in an organization The use of management in an organization Division of power in managing an organization Corporate governance Business and value chain Management approaches Economic theory vs bus...
Production factors (dispositive work ≈ management) Content System of production factors in an organization The use of management in an organization Division of power in managing an organization Corporate governance Business and value chain Management approaches Economic theory vs business economics theory Corporate economics – applied microeconomics Production factors differ. Economic theory Business-economic theory Labor Management labor Labor Executive labor Capital Material Capital Recently and added- Land knowledge, information,Long-term human assests capital, skills etc. Production factors in business theory Long-term tangible assets (depreciation, investment) Material (SCM, material time) Executive work (renumeration, salary – tools of management) Managerial work (today with link to productivity) System of production factors in an organization Production factors Elementary factors Managing factor Executiv Materia Long-term Original: decision making and e labor l assests goals setting Derived: planning organizing control Optimal combination of production factors goal Optimal combination of production factors What and how? Marginal product or marginal physical productivity Productivity and efficiency Productivity - is expressed as the ratio of output to inputs (factors of production) used in a production process, i.e. output per unit of input. Efficiency – productivity with valued units of inputs and outputs (importance by efficiency - how?) – balance sheet and profit/loss statement Productivity and efficiency Productivity and efficiency: relation between inputs and outputs Allocative (Pareto) efficiency: resources are so allocated that it is not possible to make anyone better off without making someone else worse off. Productive efficiency: no additional output can be obtained without increasing the amount of inputs, and production proceeds at the lowest possible average total cost. These definitions are not equivalent: a market or other economic system may be allocatively but not productively efficient, or productively but not allocatively efficient. There are also other definitions and measures. All characterizations of economic efficiency are encompassed by the more general engineering concept that a system is efficient or optimal when it maximizes desired outputs (such as utility) given available inputs. Productivity and efficiency Economic efficiency (used in microeconomics): Production of a unit of goods is economically efficient when that unit of goods is produced at the lowest possible cost. There are two concepts of efficiency: Technological efficiency (TE) occurs when it is not possible to increase output without increasing inputs. TE is an engineering approach. Given what is technologically feasible, something can or cannot be done. Economic efficiency (EE) occurs when the cost of producing a given output is as low as possible. EE depends on the prices of the factors of production. Something that is technologically efficient may not be economically efficient. But something that is economically efficient is always technologically efficient. System of production factors in an organization The above-mentioned breakdown of factors of production is typical for a manufacturing enterprise where there is a majority of long-term tangible assets and material. From the accounting point of view, the assets of an organization are divided into current assets (stocks of materials and goods, receivables, financial assets) and long-term assets (long-term tangible, intangible and financial assets) In the accounting view inputs - production factors (long-term assets and material or supplied goods) are being mixed with outputs (produced products, goods ready for distribution, receivables). Money is from the accounting point of view a special type of goods that mediate the economic activity of an organization - they are neither output nor input. What is the output? Money? Services? Products? Value chains Value creation – production function, SCM Value observations – controlling (managerial accounting or cost accounting) Value measurement – pricing function (part of 4P), margin Value chain model of company - Porter Porter´s value chain A value chain is a set of activities that a firm operating in a specific industry performs in order to deliver a valuable product or service for the market (Porter, 1985). Primary activities(Porter, 1985). Inbound Logistics: arranging the inbound movement of materials, parts, and/or finished inventory from suppliers to manufacturing or assembly plants, warehouses, or retail stores Operations: concerned with managing the process that converts inputs (in the forms of raw materials, labor, and energy) into outputs (in the form of goods and/or services). Outbound Logistics: is the process related to the storage and movement of the final product and the related information flows from the end of the production line to the end user Marketing and Sales: selling a product or service and processes for creating, communicating, delivering, and exchanging offerings that have value for customers, clients, partners, and society at large. Service: includes all the activities required to keep the product/service working effectively for the buyer after it is sold and delivered. Primary - Receipt of inputs (materials) - Storage Inbound Logistics - Stock Control - Internal Distribution of Inputs - Transformation of inputs into final product Operations - Use of Labour - Manufacturing Technologies Primary Activities - Distribution of finished goods Outbound Logistics - Stock Control & Inventory - Distribution of final product to buyers - Advertising Sales & Marketing - Promotional Activity - Persuading People to buy Porter´s value chain Support activities(Porter, 1985). Infrastructure: consists of activities such as accounting, legal, finance, control, public relations, quality assurance and general (strategic) management. Technological Development: pertains to the equipment, hardware, software, procedures and technical knowledge brought to bear in the firm's transformation of inputs into outputs. Human Resources Management: consists of all activities involved in recruiting, hiring, training, developing, compensating and (if necessary) dismissing or laying off personnel. Procurement: the acquisition of goods, services or works from an outside external source Support activities - Purchasing of Resources Procurement - Purchasing of inputs - Technology to support primary Technology Development activities & operations Support Activities - Leadership Structure/Management - Planning/processes Infrastructure - Finance - Information Systems - Recruitment - Selection Human Resource Management - Training - Reward & Motivation Construction of value chain of the company Creation of value chain according Magretta (2012) : To define the basic operations and actions, used within the industry to create value for the customer. Construction of value chain of the company Ikea value chain Marketin Inbound Operatio Outboun RandD g and Services logicstic ns d logistic sales Private Cabinet maker Marketin Inbound Operatio Outboun g and Services logicstic ns d logistic sales IKEA - suppliers Inbound Operatio Outboun Sales logicstic ns d logistic Material, information and money flow Material, information and money flow There are three different types of flow in supply chain management: In short, to achieve an efficient and effective supply chain, it is essential to manage all three flows properly with minimal efforts. It is a difficult task for a supply chain manager to identify which information is critical for decision-making. Therefore, he or she would prefer to have the visibility of all flows on the click of a button. Material Flow - includes a smooth flow of an item from the producer to the consumer. This is possible through various warehouses among distributors, dealers and Material, information and money flow Money flow - On the basis of the invoice raised by the producer, the clients examine the order for correctness. If the claims are correct, money flows from the clients to the respective producer. Flow of money is also observed from the producer side to the clients in the form of debit notes. Information/Data flow - comprises the request for quotation, purchase order, monthly schedules, engineering change requests, quality complaints and reports on supplier performance from customer side to the supplier. From the producer’s side to the consumer’s side, the information flow consists of the presentation of the company, offer, confirmation of purchase order, reports on action taken on deviation, dispatch details, report on inventory, invoices, etc. Order penetration point Business and value engineering A business (enterprise, a company or a firm) is an organizational, economical and legal entity and made up of an association of people involved in the provision of goods and services to consumers , in order to achieve specific declared goals.(Aaker, 2010, wikipedia.org) Business as an activity can be divided into(Appleby, 1987): People demanding goods and services - consumers People involved in obtaining, arranging and transforming basic materials into finished products – producers People involved in distribution the products to customers and others, or those involved in providing financial services. Prosumers? Photovoltaics - electricity Levels of management In the market economy system, the management decisions in an organization are either the owners (the founder) or the bodies created by them - the managers. Organizations can be divided into: owner's companies managerial companies Employees are (may be) involved in the decision-making process. If the „top“ management consists of several people, the way of making a decision is organized by using two principles: directorial principle participative principle collegial principle Link from owners to managers CG – Corporate governance = management of companies, which deals with the best possible distribution of managing rights (competence) for the successful management and control of an organization CG tasks: Ensure choice and establishment of competent management Set a strategic direction to business development Supervise high business performance Basic principles of CG: Personal responsibility of governing bodies (power division, motivation, up-to-date information) Transparency (transparent and complete information) Control (market, institutionalized) Keeping the chain together By management managerial work people. Management 1 The ultimate goal of an enterprise in a market economy is to achieve the highest possible value of the company (EVA MVA) by means of maximization of profit in the long run and in fulfilling certain secondary conditions. The top goals of public administration organizations can (and usually are) different (not profit- oriented). To achieve the goal, a unified enterprise management is created to plan the combination of production factors, organize their spending, and control the progress and results of business processes management labor (work). The role of managing an organization is to make (management) decisions. The main task in managing an organization is to set specific goals. (Specific = S.M.A.R.T.) To achieve these goals, resources (production factors) are used. The use of management in an organization can then be expressed in a sequence of steps in the management activities: decision making EVA – Economic value added setting targets (goals) EVA = NOPAT - C * WACC , - where: planning NOPAT - net operating profit after tax, realization (organization) C - long-term invested capital, WACC - cost of capital expressed as a discount rate control MVA – Market value added MVA = (Ps - Pp) * n , where: Ps - market price of the share, Pp - nominal share price, n - number of shares Management hierarchy Setting goals decision making planning implementing controlling decision making (organizing) (supervising) production investment procurement staff sales decision making Management 2 Goal setting is the starting point for the tasks of the managing factor. Its content is to define the desirable state that is sought. The goals of an organization are seen as a structured system. This system has: horizontal dimension = main and secondary goals vertical dimension = main goals, intermediate goals and sub-goals. Planning is a function of management of an organization, which focuses on finding alternative ways to achieve set goals. Decision making is placed behind planning Outputs of the planning process are variations of the plan. From the offered variants of paths to achieving the goal, one has to identify the one that best achieves the goal choosing one (optimal) plan variant. Management 3 Realization is carrying out of the selected plan variant. It includes the division of tasks and the organization of people, material resources and information in the intentions of the accepted plan. The content of the realization is not the implementation of individual tasks realization = organizing, resp. organization. Controlling is a function of business management that concludes basic explanation of managing factor tasks. Through the control, the managing factor gets information to which extent and how the set goals are achieved. The individual functions do not have to follow in the above order they mutually intertwine and combine there are mutual relationships and feedback between them. Management concepts Management is a way how to achieve your goal by hand of the others. Managerial concepts evolved through time, seeking and improving productivity in the employee activities. Efficiency and Productivity Productivity and management principles Principles of scientific management – F. W. Taylor Each worker should have a large, clearly defined, daily task. Standard condition are needed, to ensure the task is more easily accomplished. High payment to be made for successful completion of task. Workers should suffer loss when they failed to meet the standards laid down. ( Appleby, 1987) Based on the time and motion study, eliminating ‘false’, ‘slow’ and ‘useless’ movements of laborers. Results: fast and successful completion of task. This conception was also used by the Henry Ford - the system of work is known as Fordism – effective mass production. Productivity and management principles Human relations school – G. E. Mayo – Hawthorne experiment – psychological experiment at Hawthorne plant of the Western Electric Company. Attention focused on the components of job and work satisfaction on the part of employees. Result – The understanding of a person´s needs would enable a manager to use more accurate methods to motivate subordinates. Productivity and management principles Knowledge management - P. Drucker, I. Nonaka, H.Takeushi Forms of knowledge (Nonaka & Takeuchi, 1995): Explicit: information or knowledge that is set out in tangible form. Implicit: information or knowledge that is not set out in tangible form but could be made explicit. Tacit: information or knowledge that one would have extreme difficulty operationally setting out in tangible form. „Tacit" knowledge is Nonaka and Takeuchi's example of the kinesthetic knowledge that was necessary to design and engineer a home bread maker, knowledge that could only be gained or transferred by having engineers work alongside bread makers and learn the motions and the "feel" necessary to knead bread dough (Nonaka & Takeuchi, 1995). Source: researchgate.net Productivity and management principles TPS – Toyota production systems Principle 1: Base your management decisions on a long-term philosophy, even at Philosophy the expense of short-term financial goals. Principle 2: Create continuous process flow to bring problems to the surface. Principle 3: Use “pull” systems to avoid overproduction. Principle 4: Level out the workload (Heijunka). Principle 5: Build a culture of stopping to fix problems, to get quality right the first Process time. Principle 6: Standardized tasks are the foundation for continuous improvement and employee empowerment. Principle 7: Use visual control so no problems are hidden. Principle 8: Use only reliable, thoroughly tested technology that serves your people and processes. Principle 9: Grow leaders who thoroughly understand the work, live the philosophy, and teach it to others. Principle 10: Develop exceptional people and teams who follow your company’s People and Partners philosophy. Principle 11: Respect your extended network of partners and suppliers by challenging them and helping them improve. Principle 12: Go and see for yourself to thoroughly understand the situation (Genchi Genbutsu). Principle 13: Make decisions slowly by consensus, thoroughly considering all Problem solving options and then implement the decisions rapidly. Principle 14: Become a learning organisation through relentless reflection (Hansei) and continuous improvement (Kaizen) Benjamin Franklin (1706 - 1790) History The principles described by Benjamin Franklin since 1732 in the story Poor Richard or The Road to Prosperity - the core and foundations thus originated in the USA Developed and especially introduced on a larger scale in Japan after 1945 as Toyota production systems (since 1948) In the context of globalization, transferred to the whole world Named in 1988 as LEAN Production Avoiding MUDA (waste) Cost + Profit = Price changes to: Price - Cost = Profit 日 本 国 Waste MUDA Waste… MURA Imbalance, unevenness… MURI Inadequacy… (MUCHI ignorance (lack of knowledge) and MUSCHI ignorance) MUDA Muda means waste, vanity, futility or even pointlessness. This is the most famous evil in the production of the three. They are usually divided into seven types of waste. Transport Unnecessary movements Waiting Excess processing Defects and repairs Stocks Overproduction MURA Mura means unevenness, unevenness, imbalance, irregularity, imbalance or lack of uniformity. This is any unevenness or irregularity. And although it is often related primarily to material flow, it is a problem of many other cases outside the material flow. Below is a list of examples of when we may encounter mura and when it can cause problems. Uneven customer demand Inventory fluctuations - too much, too little Uneven production speed or change in production volumes Irregularities in the quality of good pieces Irregular work rhythm Unbalanced staff training Uneven distribution of workload MURI Muri means overloading resources, inadequacy, impossibility, exaggeration, beyond one's strength, excessive difficulty. Muri is any overloading and doing anything that is too difficult. The main focus here is, of course, on people. However, Muri can also apply to materials, machines and organizations. MURI People Work taking too long Lifting heavy objects Improper posture or insufficient ergonomics Noise Too demanding tasks Tasks too easy (can be boring or mentally tiring) Excessive stress Anything that leads to burnout, exhaustion, or repeated injury Lack of training Humiliation (possibly excessive praise) Organization We want the supplier to deliver what we want, whenever we want, without any signal from us that we want it Abuse of market power vis - à - vis suppliers or customers Machines and materials Driving the performance of machines and tools to the maximum limits of their capabilities, which leads to greater wear Skip maintenance (try to skip it, machines will definitely not like it) Improper handling of materials, storage of parts in unsuitable conditions Loading a truck or container beyond its weight limits Praxis Placement and marking Job placement history Shadow map Tool placement 5S Seiri - Divide - Go through and check the workplace and sort out unnecessary items. Seiton - Sort - Designation of items used in manufacture by a reasonable number or name. Seiso - Arrange - The logical arrangement of the items used in production as they follow in the sequential production process. Seiketsu - Document - Document and standardize all procedures. Shitsuke - Follow - Systematize and follow identified procedures and plans. Thank you…