Process Measurement Level Sensing & Measuring Devices PDF
Document Details
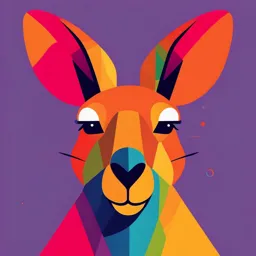
Uploaded by Reusl
Tags
Summary
This document provides an introduction to various types of level sensing and measuring devices used in process applications. It explains single and continuous monitoring, as well as direct and indirect measurement methods. Key devices discussed include gauge glasses, magnetic float gauges, and float-type systems.
Full Transcript
Introduction to Process Measurement • Chapter 2 Objective 2 Describe the types of level sensing and measuring devices. Level Measurement Power Engineers regularly monitor and record important levels, including boiler water level, fuel tank level, storage tank level, and others. Some instruments, s...
Introduction to Process Measurement • Chapter 2 Objective 2 Describe the types of level sensing and measuring devices. Level Measurement Power Engineers regularly monitor and record important levels, including boiler water level, fuel tank level, storage tank level, and others. Some instruments, such as gauge glasses, only indicate level. Other level sensing instruments transmit signals to remote indicators and control systems. Liquid level sensing may be categorized as: • Single point level detection • Continuous level monitoring In single point level detection, the presence of the process material is detected at predetermined levels. Depending on the process, single point detection can be used to start or stop pumps, open or close control valves, trip off equipment, or to sound alarms. For uninterrupted level measurement, continuous level monitoring is used. In this case, the level of the process material is constantly monitored. A level signal may then be transmitted for monitoring, recording, or control purposes. Level measurements can be direct or indirect. A direct measurement might involve placing a float on the process fluid surface and tracking its motion. Indirect methods may involve inferring level based upon pressure changes due to changes in height of process fluid. Direct Level Measurement Gauge Glasses The gauge glass is the simplest and most common level indicator used in industry. It provides direct visual indication of the process fluid level. Power Engineers will find them installed on refrigeration system liquid receivers, boiler steam drums, lube oil tanks, expansion tanks, and steam separators, to name a few. If the gauge glass is installed on a pressurized container, a container under vacuum, or a sealed vessel containing toxic, volatile or flammable materials, it will be installed with gasketed leak-tight connections at both ends (Figure 18 (a)). The top of the gauge glass will be installed to the vapour space of the vessel, and the bottom to the liquid space. If the vessel is an open tank, only the bottom of the gauge glass needs to be connected (Figure 18 (b)). The top may be left exposed to the atmosphere. Figure 18 – Gauge Glass Applications 4th Class Edition 3 • Part A 2-17 Unit A-9 • Energy Plant Instrumentation and Controls Gauge glasses are equipped with valves to permit their isolation and replacement should they break. Some of the isolation valves contain mechanisms to automatically stop process liquid flow from a broken gauge glass. Most gauge glasses have protective shields or barriers to prevent their accidental breakage. Gauge glasses are available in a variety of styles for various pressure applications. Magnetic Float Gauge Certain toxic or corrosive materials attack conventional gauge glass gaskets. As well, certain process chemicals attack glass, making conventional gauge glasses unsuitable. In these situations, magnetic float indicators can be used. Figure 19 shows a magnetic float that is free to travel vertically in a tubular housing made of non-magnetic material, such as stainless steel. The non-magnetic tube is connected to the vapour space and liquid space of a vessel. This housing is sometimes called a stilling well because its isolation valves can be throttled to dampen wave action or level fluctuation in the process vessel. An indicator is magnetically coupled to the float and travels freely up and down an externally mounted scale, following the changes in the process vessel level. The level is read directly from the scale at the location of the magnetic indicator. The magnetic float can also be configured to operate level control or alarm switches. Figure 19 – Magnetic Float Float-Type Level Measurement Another direct level measurement and indication method commonly used in open tanks is shown in Figure 20(a). The float is attached to a weight by means of cables and pulleys. The float is located in the tank. The while the weight hangs outside, beside a scale marked in units of level. The float is heavier than the weight, but less dense than the process fluid being measured. 2-18 4th Class Edition 3 • Part A Introduction to Process Measurement • Chapter 2 Figure 20 – Float-Type Level Measurement and Control Scale Pivot Weight Inlet Valve Float Float Level Measurement Level Control (a) (b) Figure 20(b) shows a float-type level control system where a float positions an inlet valve through a linkage arrangement. By moving the pivot to the left, a greater change in level is required to produce the full range of valve motion. When it is not practical to have a float in a vessel or tank, a float cage (Figure 21) is mounted on the outside, with the bottom part connected to the liquid space, and the top to the vapour space. If the level in the vessel increases, the float rises to open the control valve further so more liquid will flow from the vessel. Note that the cage will be under the same pressure as that in the vessel. Similar float arrangements can be connected to a boiler drum where the float may operate a switch to start and stop a feedwater pump, and to operate a low water-level fuel cut-off in case the boiler water becomes dangerously low. Figure 21 – Float Cage Unit Upper Connection Float Turnbuckle Lower Connection Double Ported Valve 4th Class Edition 3 • Part A 2-19 Unit A-9 • Energy Plant Instrumentation and Controls Ultrasonic Transducers Ultrasonic transducers can be used to provide direct, continuous, or single-point level measurements. Their advantage is that they do not need to physically contact the process fluid. This is especially important in applications that contain process fluids that are corrosive, contain suspended solids, or may create troublesome coatings on instruments. Ultrasonic level transducers (Figure 22) may be used to measure level, volume, or open-channel flow. Figure 22 – Ultrasonic Level Transmitter The level measurement is made by emitting an ultrasonic pulse from the transducer, then measuring the time required for the echo to reflect from the liquid surface and return to the transducer. Sophisticated electronics measure the time of the round trip pulse and, by knowing the speed of sound, calculate the distance. Since speed of sound is temperature dependent, the transducer also measures the temperature in the vessel to compensate for changing temperature. By inputting the type and geometry of the vessel, the intelligent electronics can calculate the liquid volume in the vessel. In a similar operation, the ultrasonic level sensor can perform open channel flow measurement by converting the level reading into units of volume per time. Common tank, flume, and weir shapes can be stored in the device’s software. Conductance (Conductivity) Probes Conductivity sensors work on the principle that many process fluids (including boiler water) conduct electricity. The probes can be thought of as poles of a switch, and the process fluid as the blade that opens or closes the switch. As levels change, probes of various lengths become submerged consecutively in conductive process fluid. If the level drops below the bottom of a probe, the current flow will be interrupted, and the circuit will open. The circuit will close again when the level rises above the bottom of the probe. Conductivity probes may also be used to generate a digital process control signal, based on the process fluid level. These probes are ideal for point level detection of conductive liquids such as water, caustic soda, and sulfuric acid. Conductivity probes provide reliable service where point level detection or control is desired. The voltage used with these probes is selected based on the conductivity of the process fluid. Higher liquid conductivity requires lower voltage than liquids with lower conductivity. If the vessel is made of conductive material, such as steel, the vessel itself can be used as one of the sensing probes. 2-20 4th Class Edition 3 • Part A Introduction to Process Measurement • Chapter 2 Figure 23 – Conductive Level Probe System 1 2 3 Steam line Normal Operating Range (level) 1 High Probe - shuts down feedwater pump 2 Low Probe - starts feedwater pump Water line 3 Low-Low Probe - trips boiler Water Column Level Probes (Conductivity) Conductivity level sensors or probes may be used to start and stop feedwater pumps on small boilers, signal process alarms, or instigate process equipment trips. Figure 23 shows conductance probes installed in the water column of a steam boiler where the operating level is kept between the two upper conductance probes. If the level drops below the lowest probe, the boiler burner circuit opens, shutting the boiler fuel valves. Conductivity probes used with corrosive liquids are manufactured from special metals. Conductance probes have not historically been used in the chemical processing industry, because they may release sparks when approached by conductive fluids. Recently, though, solid-state designs have been made for intrinsically safe service. Radar or Microwave Transducers Radar (or microwave) level sensors work similarly to ultrasonic sensors (Figure 24). Instead of using ultrasonic signals, though, they transmit electromagnetic waves with a frequency of around 10 GHz. These waves reflect back to the sensor when they reach the surface of the process fluid being measured. The time taken for the wave to travel to the liquid surface and back to the transducer indicates the level in the vessel. 4th Class Edition 3 • Part A 2-21 Unit A-9 • Energy Plant Instrumentation and Controls Figure 24 – Radar or Microwave Level Detection System Microwave Transducer Emitted Pulse Storage Vessel Reflected Pulse Process Liquid Non-invasive Radar Level Measurement Radar level measurement is highly accurate. It does not require direct contact with the process fluid. Radar transducers are not affected by dust, vapours, or moisture. Unlike ultrasonic transducers, radar transducers can operate in a vacuum. Indirect Level Measurement Bubblers The simplest way to indirectly measure liquid level is to measure the pressure of the liquid at the base of the vessel. To do this, a supply of clean air (or inert gas) is forced through a submerged tube near the base of a vessel. For this method to work the vessel must remain at atmospheric pressure; therefore, its use is restricted to vented or open vessels. Figure 25 shows a simple bubbler system. Figure 25 – Bubbler Air is fed into the air line with only enough pressure to cause bubbles to exit the end of the submerged tube. A pressure gauge mounted on the air line reads the hydrostatic pressure of the liquid above the bubble tube opening. If the density of the liquid is known, the pressure can be converted to height (or depth) in metres. Some pressure gauge dials are directly calibrated in liquid depth. 2-22 4th Class Edition 3 • Part A Introduction to Process Measurement • Chapter 2 Diaphragm-Type Differential Pressure Level Indicator Figure 26 shows a level indicator that can be placed in a remote location when a boiler steam drum is higher than the operating floor, and the level gauge (gauge glass) on the steam drum is not visible from the operating floor. This indicator has a large diaphragm with the upper side connected to the steam space, and the lower side to the water space of the boiler. A condensing pot at the boiler drum maintains a fixed head of water or pressure on the upper side of the diaphragm. The lower side is subjected to a varying hydrostatic head as function of the water level in the boiler. The difference in pressure due to the liquid head between the two sides of the diaphragm is balanced by a spring, so the diaphragm moves in accordance with the water level. As the water level rises in the drum, the pressure under the diaphragm increases causing it to rise, moving the indicator upwards. Full boiler pressure is exerted on both sides of the diaphragm, so the boiler pressure has no effect on the movement of the indicator. The equalizer pipe ensures that if either the steam connection or the water connection isolation valves are shut, pressure imbalance will not damage the differential pressure assembly (diaphragm, spring, and linkages). Figure 26 – Remote Water-Level Indicator 4th Class Edition 3 • Part A 2-23 Unit A-9 • Energy Plant Instrumentation and Controls Differential Pressure Level Measurement Figure 27 shows a small vessel that has a water level in the lower section and steam above the water. A gauge glass indicates the water level to the operator. As well, there is a differential pressure sensor (DP-cell), with a transmitter that provides level information to a controller. The “High Side Transmitter Connection” is filled completely with water, and provides a constant head (or reference head) to the DP-cell. The “Low Side Transmitter Connection” pressure varies with the level in the vessel. A diaphragm inside the DP-cell moves with changes in level and varies the transmitter output signal. Figure 27 – Differential Pressure Level Measurement Isolating Valve Vessel Operating Level Gauge Glass High Side Transmitter Connection Level Transmitter Isolating Valve Low Side Transmitter Connection dp cell If a DP-cell transmitter is used to measure level in an open tank, then one side of the DP-cell bellows is connected to the bottom of the tank, and another port is left open to the atmosphere. This setup will accurately detect and measure the liquid level as function of the hydrostatic head in an atmospheric vessel. 2-24 4th Class Edition 3 • Part A