3 Common Hand Tools PDF
Document Details
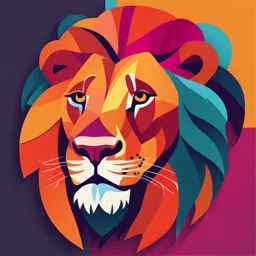
Uploaded by FaultlessMarsh8570
null
null
Tags
Summary
This document provides a comprehensive overview of various types of hacksaws, including junior hacksaws, coping saws, and piercing saws, used for different purposes in a metalworking or woodworking workshop. It also describes the function of tension files.
Full Transcript
Hacksaws The Hacksaw Hacksaw frames are usually adjustable in length to enable them to take blades of different lengths. Rectangular section steel tube is often used to make hacksaw frames. Handles may be of the pistol grip type or straight handled like the handle of a file. Blade tension is adjuste...
Hacksaws The Hacksaw Hacksaw frames are usually adjustable in length to enable them to take blades of different lengths. Rectangular section steel tube is often used to make hacksaw frames. Handles may be of the pistol grip type or straight handled like the handle of a file. Blade tension is adjusted by turning the wingnut at one of the blade attachment points. The blade must be under tension when the saw is in use to ensure a straight cut and lengthen the life of the blade. The attachment points are of square section and are mounted in square holes so that the blade can be mounted in line with the frame or at right angles to it. Blade tension should be released after use to unload the frame. Pistol grip hacksaw 2023-11-24 B-07b Maintenance Practices CASA Part 66 - Training Materials Only Page 74 of 498 Types of Hacksaws Junior hacksaw Junior hacksaw - for use with 6-in. blades with pinned ends. Used for general light work where a standard hacksaw is too clumsy. The blades are flexible, 6 in. × 32 TPI, and tension is applied either by the spring of the frame or by screwing up the hardwood handle. Coping saw and junior hacksaw Coping Saw Coping saws take pinned blades 6.25 in. long, with 14 TPI. They are used in a frame like the junior saw, but can be swivelled at any angle. Used for shaping soft materials such as wood. 2023-11-24 B-07b Maintenance Practices CASA Part 66 - Training Materials Only Page 75 of 498 Piercing Saw Piercing saws are similar in general shape to a coping saw, but the frames are deeper and sometimes adjustable for length. Serrated and hardened clamps ensure a firm grip on the blades, which are 5 in. long with TPI from 32 to 80. Used for fine sawing of intricate shapes in thin sheet. Piercing saw Tension files Tension files (e.g. Abrafiles) are made from a specially heat-treated flexible steel wire. They do not clog and will cut in any direction. Very useful for cutting intricate shapes or irregular holes in thin metal. Links enable the blades to be used in a standard hacksaw frame. Blades are available in three grades, fine, medium and coarse, and they are 8 in. long. Tension file (hacksaw) 2023-11-24 B-07b Maintenance Practices CASA Part 66 - Training Materials Only Page 76 of 498 Hacksaw Blades There are three factors that dictate which type of hacksaw should be used: the frame, the blade type and the blade length. Choosing the Blade The choice of blade depends on the type of material to be cut. Soft metals (e.g. brass, aluminium) require coarse-pitch blades. Hard metals (e.g. iron and steel) require fine-pitch blades. The shape and thickness of the material must also be considered. At least three teeth must be in contact with the material at any time. Therefore, fine blades must always be used for tubing and thin metals. The shape and size of the object will also determine the length of the blade required. The length of the blade is specified as the distance between the outside edges of the fixing holes. Blades for hand use are 10 or 12 in. long and 1/2 in. deep. A short blade may be useful where access is restricted. Blades for power tool use are 12–30 in. long and 5/8–2 1/2 in. deep. Blade Hardening A saw blade is usually supplied with all hard or flexible grade. The all-hard blade is very brittle and it is suitable for the skilful user only. The flexible grade is tough, so it can twist at an angle. It is suitable for cutting a curve or where the work piece must be cut easily with restricted access (i.e. not securely clamped in a vice). It is also suitable for beginners. High-carbon steel (HCS) anneals (softens) from the heat generated by fraction of cutting. Consequently, a HCS blade loses hardness quickly if it is used to cut an excessively hard work piece or if it cuts too fast. 2023-11-24 B-07b Maintenance Practices CASA Part 66 - Training Materials Only Page 77 of 498 The Blade Set The set in a saw refers to how much the teeth are pushed out in opposite directions from the sides of the blade. Changes the set enables the blade to make a cut wider than the thickness of the blade and prevents it from jamming in the cut (kerf). Fine blades have the teeth set in groups on each side, but coarse blades have alternate teeth set to left and right with sometimes every third tooth left straight to clear the cut of chippings. See the illustration below. Blade set (hacksaw) 2023-11-24 B-07b Maintenance Practices CASA Part 66 - Training Materials Only Page 78 of 498 Hacksaw Blade Types The section below describes a range of hacksaw blade types (TPI is teeth per inch) and their uses. As described above, there are two main categories: all-hard and flexible blades, which have unique compositions for slightly different uses. High-Carbon Steel Blade The high-carbon steel (HCS) blade is typically 18-32 TPI. It is designed for less rigorous use, high carbon steel blades are ideal for use on soft metals and plastics. Tungsten Carbide Blade A hacksaw blade with a tungsten carbide grit edge has, instead of teeth, carbide grains soldered in place (therefore TPI does not apply). This blade is for the cutting of awkward materials such as iron, steel, tile, brick, glass and for extremely hard materials that cannot be cut using normal saw blades. Flexible Bimetal HSS Blade The flexible bimetal high speed steel (HSS) blade features a HSS cutting edge, electron beam welded to a flexible alloy back. It is typically 18-32 TPI. This blade cuts all but the hardest steel with good resistance to breakage. Bimetal 8% Cobalt HSS Blade This blade is typically 18-32 TPI. Suitable especially for extra hard steels, stainless steel and similar materials. It is shatterproof and very long lasting. All Hard 3% Cobalt HSS Blade This blade is made from cobalt HSS strip-hardened at full cross-section. It's consistent hardness provides extreme rigidity, however the blade is not flexible. The blade ends are annealed to prevent cracks forming at clamping holes. This blade is suitable for firmly clamped material; very hard and remains sharp over a long period, but relatively brittle and expensive; cuts fast because the temper is resistant to being degraded by frictional heat; useful for cutting hard materials like annealed highcarbon steel. 2023-11-24 B-07b Maintenance Practices CASA Part 66 - Training Materials Only Page 79 of 498 Blade Terminology Work piece (work) is an object that is worked on by the saw blade. Chatter is the vibration of the saw blade or the workpiece, caused by insufficient rigidity of either, resulting in noise and an uneven finish to the cut (kerf). Kerf – the cut made by a saw. Hacksaw blades, 18, 24 and 32 TPI The pitch is graded according to the number of teeth per inch of blade (TPI or T). A coarse-pitch blade (18T) is most suitable for soft material and thick work pieces. A medium-pitch blade (24T) is suitable for steel pipe. A fine-pitch blade (32T) is suitable for thin metal sheet and thin copper pipe. For safety, always keep at least three teeth of the blade in contact with the workpiece. Use of the Hacksaw Choice of TPI is governed by: The material to be cut – The softer the metal, the coarser the pitch of the blade. The shape and thickness of the material to be cut – The teeth must never be allowed to straddle the material, so at least three consecutive teeth must always be in contact with the material. Therefore, fine blades must be used for tubing and thin metals. 2023-11-24 B-07b Maintenance Practices CASA Part 66 - Training Materials Only Page 80 of 498 Diameter of tube Hard metal (TPI) Soft metal (TPI) Up to 1/8 in. 32 32 1/8 to 1/4 in. 32 24 1/4 to 1/2 in. 24 18 1/2 to 1 in. 18 14 Relevant Youtube link: How to use a hacksaw (general use). Precautions for using a hand hacksaw: Choose a type of blade appropriate to the material to be cut (e.g. HCS, HSS or Cobalt HSS in bimetal or all hard form). Choose an appropriate pitch (TPI) for the size and material of the workpiece. Choose a shorter blade where access is restricted. Fit the blade to the frame with the teeth pointing away from the handle. Tension the blade correctly by taking up the slack and applying three full turns of the wingnut. Wherever possible, make sure the work piece is secured rigidly in the vice. Where feasible, fit the work in the vice so that the saw cut will be vertical and will come as close to the vice as possible to prevent chatter. If the work piece is irregular in shape, arrange it in the vice so that sawing does not start across a corner. Remember that the teeth must not straddle the work piece. At least three teeth must be in contact with the work piece. Use long, steady forward strokes while maintaining a steady downwards pressure. Do not exceed 60 strokes per minute for HSS blades – go slower for HCS. Release downwards pressure on the back stroke. This reduces frictional heating of the teeth, prolonging blade life. After use, release the tension on the blade. This unloads the frame of the hacksaw and prolongs the life of the frame. 2023-11-24 B-07b Maintenance Practices CASA Part 66 - Training Materials Only Page 81 of 498 Hacksaw technique Fault Causes Blade breakage Stroke out of line, excessive tensioning, insufficient tensioning, sawing against a sharp corner, material insecurely fixed, or the blade jamming in a cut. Rapid tooth wear HCS blade used instead of HSS blade, wrong tooth size, blade facing wrong way in frame, hard spot in material, insufficient or excessive pressure, pressure maintained during backstroke or excessive speed. Tooth breakage Wrong pitch, sawing against a corner or material insecurely fixed. Crooked cutting Insufficient tensioning, hard spot in the material, excessive pressure or the material was insecurely fixed. 2023-11-24 B-07b Maintenance Practices CASA Part 66 - Training Materials Only Page 82 of 498 Drills (Part 1) Twist Drill Bits Twist drills are the most commonly used and convenient method of producing a circular hole in a work piece. The quality and accuracy of the hole depend on proper selection of tools and equipment and the process used. The drill bit most often used in aircraft engineering workshops is the doublefluted twist drill bit. Drill bits are usually made from carbon steel, high-speed steel or steel alloys, and are available in four sets: fractional, number, letter and metric. Drill bits are comprised of three major parts: shank body point. The shank is the part by which driving force is applied to the drill. The two commonly used types of shank are straight and taper. Straight shanks are usually held in a drill chuck and are the most common types used in aircraft maintenance. On taper shanks, the taper is used to locate and drive the drill. These drills are usually turned by large drill presses in machine shops. They either fit directly into the tapered socket in the drilling machine spindle or, if there is a considerable size difference between a drill and the spindle, may be used with adaptor sleeves. The body of the drill bit includes the flutes, margins and lands. Spiral flutes are milled from the point to the shank. Chips and other swarf that are cut by the cutting edge are carried out of the hole through these flutes. In addition, lubrication can reach the point of the drill bit through them. The material between the flutes is known as the land. The land nearest the cutting edge is the full drill size and is known as the margin. Refer to the diagram below. 2023-11-24 B-07b Maintenance Practices CASA Part 66 - Training Materials Only Page 83 of 498 © Jeppesen Drill bit design The two most commonly used types of drill bits are the taper shank and parallel shank. Square shank drills are used in woodworking, and threaded shanks are employed in specialist applications, but neither are commonly encountered in aircraft maintenance. Taper shank drills fit directly into a female socket on the machine spindle. The tapers are called Morse tapers and are usually used on drills larger than 1/2-in. diameter because they are far more costly than parallel shank drills and breakages are frequent with drills of small diameter. Morse tapers have a taper of 5/8 in. (0.625 in.) per foot and run in sizes from 0 to 7, small drills having a smaller shank size than large drills. The drive is frictional by means of the taper fit, and the tang on the end of the taper serves no purpose other than for ejection. The tang fits into a slot in the machine spindle, and the drill is ejected by means of a steel drift. Remember to support the drill by hand when using the drift. To fit the drill firmly in the socket, push it in by hand and bring the drill down onto a block of wood or soft metal resting on the drill table. Morse taper sleeves enable a drill with a small-diameter Morse taper to be fitted in a machine carrying a large Morse taper. Morse taper shanks and sockets have to be treated with care at all times. They should be wiped clean before assembly and stored properly when not in use. Any treatment causing bruising, etc., will affect not only the accuracy of the rotation but the efficiency of the frictional drive. 2023-11-24 B-07b Maintenance Practices CASA Part 66 - Training Materials Only Page 84 of 498 Taper shank drill bit Parallel shank drills have cylindrical shanks which may be the same or different diameter than the body of the drill. They are designed for use in the chucks or collets of a wide variety of portable tooling. Chucks and collets must always be properly tightened with the correct tooling before use. 2023-11-24 B-07b Maintenance Practices CASA Part 66 - Training Materials Only Page 85 of 498 Parallel shank drill bit Advantages of parallel shank drills: Cheaper than taper shank drills. Can be used in a wide range of drilling machines, i.e. hand or power operated. Advantages of taper shank drills: Positive drive is given by the shank, the frictional grip increasing with the feed pressure; if shank and socket are well maintained, there is no risk of the drill slipping. More accurate than a chuck fitting. Quicker to assemble than a parallel shank drill. 2023-11-24 B-07b Maintenance Practices CASA Part 66 - Training Materials Only Page 86 of 498 Twist Drill Sizing Drill diameter sizes are usually marked on the shank and can be identified by the method used in their sizing. As stated previously, drill bits are available in four different ranges: fractional, number, letter and metric. Fractional range drill bits have a minimum size of 1/64-in. diameter, continuing by steps of 1/64 in. to 1 5/8-in. diameter, then by steps of 1/32 in. to 3-in. diameter. Most nominal size fastener drills are in fractions. Numbered range drill bits have a minimum No. 80 (0.0135-in. diameter) to No. 1 (0.228-in. diameter). The steps between successive sizes are irregular, ranging from 0.001 to 0.007 in. Most fastener clearance drills for aircraft work are number drills. Lettered range drill bits have a minimum size A (0.234-in. diameter) to size Z (0.413-in. diameter). The steps between successive sizes are irregular, ranging from 0.004 to 0.014 in. Metric range drill bits have a minimum size of 0.35 mm (0.0138 in.). The full range continues by steps of 0.5 mm to a 5-mm diameter and then by steps of 0.10 mm for larger sizes. The jobbers range of utility drills extends from 1 mm in diameter by steps of 0.5 mm. Metric drills are now superseding the lettered and numbered ranges for some purposes; a preferred selection from the full metric range gives a metric drill as a replacement for every drill in the obsolescent ranges. Number/letter/fraction range of drill sizes - Section 1 of 2 2023-11-24 B-07b Maintenance Practices CASA Part 66 - Training Materials Only Page 87 of 498 Number/letter/fraction range of drill sizes - Section 2 of 2 If the drill is too small to have the size stamped on the shank, then either a drill gauge or a micrometer should be used to establish its size correctly. 2023-11-24 B-07b Maintenance Practices CASA Part 66 - Training Materials Only Page 88 of 498 Twist Drill Materials Drills may be classed as solid, tipped or composite. Solid drills are made of the same material throughout, tipped drills have a cutting insert of harder material brazed or welded to a softer (cheaper) body, and the tips of composite drills are held by mechanical methods. The materials used are listed below: Carbon steel drills, in addition to iron and carbon, contain various amounts of manganese, silicon, sulphur and phosphorus. The letters CS may be found on the shanks of these drills. Carbon steel drills High-speed steel (HSS) drills contain a comparatively high percentage of tungsten (8%-12%), with a lesser percentage of chromium (5%) and smaller amounts of vanadium and possibly molybdenum added to the carbon and iron in this steel. HSS drills retain their hardness at low red heat and can thus be used at much higher speeds than carbon steel drills. This results in much less damage to the cutting edges, and although HSS drills are more expensive than CS drills, they can lower the cost of drill purchases over time. 2023-11-24 B-07b Maintenance Practices CASA Part 66 - Training Materials Only Page 89 of 498 High-speed steel (HSS) drills Cobalt steel drills contain up to 12% cobalt, with as much as 20% tungsten, 4% chromium, 1%–2% vanadium and traces of molybdenum combined with 0.8% carbon. These drills are normally used on stainless steels, titanium and other very hard metals. Being extremely hard, cobalt steel drills are also quite brittle. Because of this, the use of these drills can be very dangerous, and strict observance of the recommended cutting speeds is essential. Cobalt steel drill 2023-11-24 B-07b Maintenance Practices CASA Part 66 - Training Materials Only Page 90 of 498 Drill Speed and Feed The cutting speed of the drill is the rate at which the cutting edges pass through the material both radially and axially. Use of the wrong cutting speed causes friction and excessive heating, resulting in premature drill failure, poor hole quality and possibly damage to the work piece. Cutting speed is measured in feet per minute of the outer edge of the cutting surface. For practical purposes, it is convenient to separate the radial and axial elements. The radial element is sometimes expressed as surface feet per minute (SFPM) and determines the rotational speed in revolutions per minute (rpm). The axial element is feed in inches per revolution. Drill speed and feed rates The rpm and feed depend on: The material being cut The size of the drill The type of drill. Generally speaking, the harder the material being cut and the larger the drill, the lower the cutting speed. The harder the drill material, the higher the cutting speed. The table opposite gives cutting speeds and feed rates for a variety of common materials and drill sizes for standard HSS drills. It can be seen that surface cutting speed and feed are not directly related. For instance, the cutting speed for aluminium is much higher than that for titanium, but the feed rates are the same. To convert cutting speed into rpm, use the following formula: Cutting Speed (CS) × 4 RP M = Diameter of cutter (D) 2023-11-24 B-07b Maintenance Practices CASA Part 66 - Training Materials Only Page 91 of 498 Example: To drill a 3/8" hole in: Aluminium 250 × 4 RP M = 0.375 = 10000.375 = 2666 With a feed of 0.006" per revolution. Titanium 20 × 4 RP M = 0.375 80 = 0.375 = 213 With a feed of 0.006" per revolution. Drill bit RPM 2023-11-24 B-07b Maintenance Practices CASA Part 66 - Training Materials Only Page 92 of 498 Centre Punching and Centre Drilling When drilling small holes up to 6.0 mm (1/4 in.) in diameter, the depth of the centre punch mark usually accommodates the non-cutting, chisel-like point of the drill, keeping it on centre and guiding the drill until it is established in the metal. V. Ryan © 2008-2017 Centre punch for small diameter holes When a hole larger than 6.0-mm diameter is to be drilled, the centre punch mark is not large enough to accept the non-cutting point of the drill. In this instance, it is necessary to use a pilot drill to provide a guide for the larger drill. First, the centre of the hole is marked on the metal and care must be taken to accurately centre punch the metal. A small drill (the pilot drill), whose diameter is slightly larger than the non-cutting point of the finished size drill, is selected and a pilot hole is drilled in the metal (using the correct lubricant for the particular metal). The pilot drill is replaced by the finished size drill, which can then (and again using lubricant) be guided through the pilot hole to complete the hole to the appropriate size. 2023-11-24 B-07b Maintenance Practices CASA Part 66 - Training Materials Only Page 93 of 498 Pilot drilling practices 2023-11-24 B-07b Maintenance Practices CASA Part 66 - Training Materials Only Page 94 of 498 Drills (Part 2) Standard Drill The standard drill is machined from cylindrical bar. It is ground to a point at one end with an angle of 118° normally, although it may be between 90° for very soft materials and 150° for hardened materials. The sides of the cylinder are ground with two helical flutes which clear the swarf produced by the cutting edges, formed where the flutes meet the point. The cutting edges are offset from the centre line because of the thickness of the web between the flutes. The tip between these edges is ground to a chisel edge to prevent rubbing on the bottom of the hole. The angle of the cutting edge is determined by the helix angle of the flutes (measured at the periphery) and the lip relief or clearance angle of the flank, both of which are referred to as 'rake' angles, which causes some confusion. The helix angle is usually 22°–27° for normal work, but can vary from 0°–45° for special drills. The lip relief angle is normally in the range of 12°–15°, but may be increased to around 20° for very soft materials. To prevent friction within the hole, the outer sides of the drill are ground back towards the heel to produce body clearance, leaving a small extension of the land to guide the drill. Drill bit cutting edge 2023-11-24 B-07b Maintenance Practices CASA Part 66 - Training Materials Only Page 95 of 498 For most applications, a drill must be correctly ground to produce a good quality round hole. Almost all difficulties in drilling holes using twist drills can be attributed to improper grinding of the point. For most materials, the cutting edges are ground at an angle of 59° from the central axis of the drill, which gives an included angle of 118°. For drilling softer materials, such as plastics, wood and lead, the included angle can be much more acute, as much as 90°. For drilling harder materials, such as stainless steel or heat-treated steel, an angle as flat as 150° may be required. Drill bit included angle The chisel edge is on the axis of the drill, and considerable pressure is needed to force it through the metal being cut. Web thinning reduces the size of the chisel edge. On large drills, it lessens the pressure necessary to force the drill through the work. The depth of flute decreases from tip to shank (and hence web thickness increases) to give strength and rigidity. When a drill gets shorter by constant grinding or breakage, the chisel edge becomes thick and the drill should be web thinned. If this is not done, the drill will not centralise itself properly and as considerable force is needed to feed in the drill, the hole may be out of round or oversized. The actual size of the hole made by a drill depends on the diameter across the land at the very tips of the cutting edges, which is often difficult to measure accurately. A drill gauge is the most accurate way to check the diameter of a drill. 2023-11-24 B-07b Maintenance Practices CASA Part 66 - Training Materials Only Page 96 of 498 Drill gauge Drill Shanks The grip exerted on a self-centring chuck is adequate for smaller drills. A considerably stronger grip is required with larger drills and they usually have a Morse taper terminating in a flat tang. The Morse taper is 1 in 20, which engages directly with the tapered socket of the drilling machine or, where necessary, a Morse taper adaptor. A slot is provided in the machine or adaptor to remove the drill by inserting a wedge, which sits on top of the drill tang, and tapping the wedge with a hammer to free the drill. A square shank is provided on some drills to fit a drill brace fitted with a pair of jaws with a V seating, e.g. a carpenter’s brace. Morse taper drill shank 2023-11-24 B-07b Maintenance Practices CASA Part 66 - Training Materials Only Page 97 of 498 Countersinking Tools Stop and Press (Dimpling) Two special tools used during the riveting process are the stop countersinking bit and the press countersinking tool, more commonly known as the dimpling tool. Both of these tools have evolved as a result of the need for flush skins on high-performance aircraft. In order to have the rivet heads flush with the surface, the skin must be prepared either by cutting away a portion of the metal to match the taper of the rivet head or by indenting (by pressing) the edges of the hole to accept the rivet head. If the top sheet of the metal being joined is thicker than the tapered portion of the rivet head, then the material should be cut countersunk. While the standard countersink bit (or a twist drill twice the diameter of the rivet hole) can be used in a hand or power drill to form a countersunk hole, its lack of accuracy and consistency means it is only useful for small jobs and certainly should not be used where pressurised skins are concerned. Where a large number of holes need to be countersunk to a consistent depth, the stop countersink tool should be used. It can be adjusted to cut an exact countersink repeatedly, regardless of the force applied to the drill/tool combination. The pilots can be changed depending on the size of holes in the material, leaving the remainder of the tool to be used for all jobs unchanged. The stop may be held rigidly during cutting to avoid marking the surface. Press countersinking tool Press countersinking, or dimpling, is done where the aircraft skin is too thin to countersink, and without the attendant risk of enlarging the drilled hole. The edges of the hole are formed to accommodate the head of the rivet by using a set of dimpling dies, using either coin dimpling or radius dimpling methods. 2023-11-24 B-07b Maintenance Practices CASA Part 66 - Training Materials Only Page 98 of 498 Coin dimpling forces the sheets into the lower die, leaving a sharply defined and parallel-sided hole. This process also allows a number of sheets to be stacked together at the expense of a complex pair of tools and leaves a neat, clean dimpled hole with smooth sides. Radius dimpling uses a male die to drive the sheets into a female die. The sides of the formed holes are not as smooth as with the coin dimpling method, but this less precise operation is quicker and cheaper to achieve. With harder materials, such as magnesium and certain aluminium alloys, a process called hot dimpling is used. This method involves pre-heating the metal so that it forms more easily and is less likely to crack when shaping takes place. Dimpling Relevant Youtube link: Countersinking on aircraft 2023-11-24 B-07b Maintenance Practices CASA Part 66 - Training Materials Only Page 99 of 498 Straight-Fluted Drills Instead of having spiral flutes like a standard twist drill, straight-fluted drills have straight flutes. These give the drill zero rake, so the drill scrapes rather than cuts freely. Standard twist drills, when used for brass and particularly thin brass sheet, tend to bite excessively, screw themselves into the hole (due to the right-facing helix on the drill) and possibly jam. Because of the straight flutes, they drill brass more efficiently. However, the straight flutes do not clear the chippings as well as helical flutes, and the drills need frequent withdrawal when drilling deep holes. Straight-fluted drill 2023-11-24 B-07b Maintenance Practices CASA Part 66 - Training Materials Only Page 100 of 498 Step Drills Step drills have one or two straight flutes and multiple cutting edges along them, producing a range of different diameter holes. Due to the limited depth provided by each step, they are mainly used for sheet metal and reduce the need to change drill sizes regularly. They may also be used in conjunction with Eazi Out type stud extractors, where the steps provide multiple contact points for the extractor tool. Step drill 2023-11-24 B-07b Maintenance Practices CASA Part 66 - Training Materials Only Page 101 of 498 Centre, Combination or Slocombe Drill The centre drill is a twist drill and countersink combined. It is used for: Preparing work for mounting between lathe centres Spotting the centre for drilling in a lathe. Size ranges from 1/8-in. diameter upwards. The drill is always double-ended with an angle of 60° to correspond to the 60° angle of the lathe centres. The small pilot hole keeps the weight off the point of the centre and acts as a reservoir for grease. Usage: Speed – as for twist drills. Feed – relatively light. Heavy feeds result in drill breakage. When centre holes are required to a depth which uses half or more of the diameter of the countersink, i.e. deep centring, the drill should be withdrawn frequently to prevent chips choking the flutes. Always start the cut slowly. If the drill is bumped into the work, the pilot drill will fracture. Make sure the drill is securely held. Any slight movement will cause intermittent feed and subsequent breakage. Centre or slocombe drill 2023-11-24 B-07b Maintenance Practices CASA Part 66 - Training Materials Only Page 102 of 498 Special Drills Flat drills are sometimes used for cutting very thin material, like straight fluted drills, as they tend to scrape the hole rather than bite in. Quick helix drills are designed for drilling very soft materials like aluminium. The quick helix gives increased rake. Slow helix drills are designed for brass and bronze. The slow helix reduces the rake angle. Multi-flute drills are used for enlarging the size of holes already drilled. Masonry drills have brazed-in tips of tungsten carbide and are used for drilling brick, stone, etc. Flat drill 2023-11-24 B-07b Maintenance Practices CASA Part 66 - Training Materials Only Page 103 of 498 Countersink Drills Countersink drills are used to set flush countersink screws and for countersinking prior to riveting. They are made with an included angle of 60°–120°, depending on the head angle of the fastener to be installed. The rose countersink is usually made of HCS and is used chiefly for soft materials, e.g. wood. It is made with a square or round shank. The machine countersink is usually made of high-speed steel and is the type usually used on drilling machines and lathes. The piloted countersink is used in portable power drills and is available with pilots of varying size to suit the hole being countersunk. The stop countersink is used in the micro-stop type adjustable holder and cuts countersinks of consistent depth. The combined countersink consists of a drill bit with an integral countersink cutter and is again used in the micro-stop holder. Care is needed when using countersink drills as they cannot normally be sharpened. Countersink drills 2023-11-24 B-07b Maintenance Practices CASA Part 66 - Training Materials Only Page 104 of 498 Counterbores Counterbores are used to make a flat-bottomed recess, e.g. for a cheese-headed screw or cap screw, or a flat spot face on a casting. Using a pilot pin ensures that both drilled holes are concentric. The hole for the shank of the screw is made first using a standard drill and the counterbore, then used for the recessing or spot facing. The projecting pilot pin of the counterbore must fit the hole drilled for the shank of the screw. The pilot may be integral to the cutter or removable, which facilitates sharpening. Counterbores 2023-11-24 B-07b Maintenance Practices CASA Part 66 - Training Materials Only Page 105 of 498 Tank Cutters and Hole Saws Tank Cutter Tank cutters are used for cutting large holes in sheet material and are made with round or square shanks. The cutter is the end of an adjustable arm which can be lengthened or shortened to achieve the hole diameter required. The spindle is attached to the body and is concentric with the pilot, which may be a plain pin or a short drill bit. A pilot hole should always be drilled first. Tank cutter Fly Cutter A fly cutter is very similar to a tank cutter and can be used for cutting large holes in thin sheet, plate and solid material when mounted in a pillar drill or milling machine. The cutter is interchangeable for use in different depths and materials. When using a fly cutter, it is extremely important to back the metal being cut with scrap wood. This scrap wood is firmly clamped to the table of the drill press so that there is no danger of the cutter grabbing the metal and spinning it. Fly cutter 2023-11-24 B-07b Maintenance Practices CASA Part 66 - Training Materials Only Page 106 of 498 Hole Saw The hole saw is nonadjustable and consists of a toothed blade similar to that of a hacksaw, rolled or formed into a cylinder. The rolled type fits into the grooves of a holder which also has a spindle and drill bit attached. The formed type is fitted to an arbour. The drill bit centres the cutter on the pilot hole and guides the saw during the cut. The rolled type hole saw is often supplied with a number of alternative-sized blades which fit into the same holder. Hole saws 2023-11-24 B-07b Maintenance Practices CASA Part 66 - Training Materials Only Page 107 of 498 Drill Usage Sharpening Twist Drills To ensure correct cutting, the following rules need to be observed: The point angle needs to be correct; 118° is standard. The chisel edge must be at the right angle, which is 130°. The lip clearance must be correct for the size of drill. It is larger on small drills, averaging 10°– 12°. The two cutting edges should be the same length. The two cutting edges should be at the same angle to the drill axis. Effects of inaccurate grinding: Point angle too acute – lips become convex with loss of cutting efficiency. Point angle too obtuse – lips become concave with much loss of strength. Cutting edges at unequal angles – one lip does all the cutting, giving oversized holes. Insufficient lip clearance – drill rubs and does not cut cleanly. Excessive lip clearance – drill has weak cutting edges which chip and break easily. Cutting edges different sizes, point off centre – drill wobbles and cuts oversized hole. It is extremely difficult when grinding a drill, and particularly a small drill, by hand to ensure that all the angles are correct. A drill angle gauge can be made from steel plate and is useful for checking that the grinding of the point angle is correct. However, the lip relief or clearance angle is more difficult to measure. Drill angle gauge 2023-11-24 B-07b Maintenance Practices CASA Part 66 - Training Materials Only Page 108 of 498 Drill Grinding Machines The two types of drill sharpener or grinder fit on either a pedestal grinding machine or a standalone machine. The first type of drill sharpeners are jigs of varying complexity. The second type range from simple machines for home use to complex programmable machines for production line sharpening. Drill sharpening machines 2023-11-24 B-07b Maintenance Practices CASA Part 66 - Training Materials Only Page 109 of 498 Marking Out For Drilling A centre-punch mark must be made in order to position the drill. Without a centre-punch mark, the drill tends to wander, creating a hole that is misshapen and in the wrong place or causing the drill to skid off and damage the surface. This centre-punch mark must be: Accurate in position Large enough to take the chisel edge of the drill. Pilot drills, i.e. small drills used prior to a large one, are used for the following reasons: Large drills have a large chisel edge, requiring the centre-punch mark to be so large that it could not possibly be positioned accurately enough if it could be made large enough. The chisel edge is inefficient in cutting, and considerable pressure is needed to force it through the metal. The larger the drill, the larger the chisel edge and, consequently, the greater the pressure needed. This pressure can be relieved by drilling a pilot hole. The position for the hole is marked by intersecting lines, usually at right angles, and the point of intersection centre punched. If the hole need not be very accurate for position, it may now be drilled. Drill marking out process For accurate work and large holes, better methods are necessary because a drill started in a centrepunch mark does not necessarily drill a hole truly concentric with its original centre. 2023-11-24 B-07b Maintenance Practices CASA Part 66 - Training Materials Only Page 110 of 498 Method 1 Scribe a circle the exact diameter of the drill and centre punch the centre. Dot punch where the two lines intersect the circumference of the circle. These marks (pop marks) accurately fix the circumference of the circle, particularly as during drilling the circumference may be masked or obliterated with soluble oil, etc. Method 2 Use two circles: one the diameter of the finished hole and one smaller, both with pop marks. This is more accurate than Method 1. Correction Drilling is started and the work inspected before the drill has cut in very far. If the drill is running off true, it will be evident by its relative position to the intersecting lines and, if marked out by Method 2, by its position in relation to the inner circle as well. If it is off true, one or more grooves should be cut with a centre punch, half-round chisel or diamond point chisel in the opposite direction to which the drill has run. Drilling is restarted and the work again checked. If the hole is now concentric with the marking out, the drilling can be continued and a further check made when drilling approaches the circle. A further adjustment can then be made if necessary. Once the drill has started cutting its full diameter, it is impossible to make any correction. All adjustments must be made before the drill is cutting its full diameter. Drill marking out and correction method 2023-11-24 B-07b Maintenance Practices CASA Part 66 - Training Materials Only Page 111 of 498 Drilling Thin Sheet and Point Alteration All thin sheet, but particularly thin brass sheet, is difficult to drill with a standard twist drill. The holes are often out of round and roughly triangular in shape. The undersides of the holes are heavily burred. The drill tends to catch up badly and screw into the metal. A flat drill or straight-flute drill makes these holes more efficiently, particularly in brass sheet, because the rake angles are better suited to the material than the rake angle given by the helix of a standard twist drill. If neither of these drills is available, then modification of a standard drill is necessary. Alteration of Point Angle Heavy burning occurs and the drill tends to screw itself into the metal if the point of the drill breaks through on the underside before the full diameter of the drill has entered the work. These effects can be minimised if the point angle is altered to 140°, making it more obtuse. Alteration of Helix Angle The angle of the helix gives a tool angle that is much too acute for drilling brass. The angle can be altered by grinding in the flute to produce a rake angle of 15° or less. The cutting action then becomes similar to that of a straight-fluted drill. 2023-11-24 B-07b Maintenance Practices CASA Part 66 - Training Materials Only Page 112 of 498 Web or Point Thinning Web or point thinning can help produce a hole that is round. Drill angle alteration and point thinning Twist Drill Faults, Causes and Remedies There are a number of faults to look out for when drilling to ensure a quality final product. Drill bits are especially susceptible to damage and general wear and tear. The following is a list of some common defects, their causes and remedies. Broken or twisted tangs. Causes A bad fit between the shank and the socket causes a drive off the tang and not the taper. Morse taper shanks are self-driving, i.e. they are made to drive off the taper, not the tang. The tang is for ejection purposes only. Remedies Make sure the shank is a good fit in the socket. Shanks and sockets must be free of bruises, clean before inserting and stored carefully when not in use. 2023-11-24 B-07b Maintenance Practices CASA Part 66 - Training Materials Only Page 113 of 498 Splitting of the web. Causes 1. Striking the drill on the point with a hard object to ensure that it fits tightly into its socket. 2. Too much feed. 3. Careless ejection of the drill. 4. Excessive web thinning. 5. Too little lip clearances, necessitating excessive feed. Remedies 1. Use a soft-faced hammer or bring the drill down onto a block of wood. 2. Reduce the feed. 3. Hold the drill when ejecting to prevent it falling. 4. Reduce the web thinning. 5. Increase the lip clearance. Worn outer corners of cutting edge. Causes 1. Excessive speed for the material being cut. 2. Lack of a suitable cutting solution. Remedies 1. Reduce the speed. 2. Use the correct solution. Flaked outer corner of cutting edge. Causes This usually occurs when drilling thin section material which is not supported firmly enough. When the chisel edge breaks through, the material springs back and then snatches at the outer corner of the drill, causing them to chip. Remedies Examine the supports, and if it is necessary, fix them closer together. Alternatively, replace the support pieces with a solid supporting block. 2023-11-24 B-07b Maintenance Practices CASA Part 66 - Training Materials Only Page 114 of 498 Chipped cutting lips. Causes 1. Excessive lip clearance angles. 2. Too heavy a feed. Remedies 1. Re-grind and reduce the clearance angles. 2. Reduce the feed. Large chip from one flute, little or none from the other. Causes Unequal cutting edges causing one lip to do all the cutting. Remedies Re-grind, making cutting edges of equal length. Walls of drilled hole left rough. Causes 1. Drill is blunt. 2. Drill is badly ground. 3. No cutting solution. 4. Too much feed. Remedies 1. Re-grind. 2. Re-grind. 3. Use a cutting solution. 4. Reduce the feed. 2023-11-24 B-07b Maintenance Practices CASA Part 66 - Training Materials Only Page 115 of 498 Drill breakage. Causes 1. Incorrect grinding. 2. Too much feed. 3. Worn lands. 4. Flutes choked with chips. Remedies 1. Re-grind. 2. Reduce feed. 3. No remedy. Replace drill. 4. Withdraw the drill frequently to clear the flutes, especially with small drills and deep holes. Drill coloured blue. Causes 1. Speed too fast. 2. No cutting solution. 3. Worn lands. 4. No lip clearance. 5. Blunt drill. Remedies 1. Reduce speed. 2. Use cutting solution. 3. Replace drill. 4. Re-grind. 5. Re-grind. 2023-11-24 B-07b Maintenance Practices CASA Part 66 - Training Materials Only Page 116 of 498 Hole too large. Causes 1. Unequal cutting angles. 2. Unequal length of cutting edges. 3. Loose machine spindle. Remedies 1. Re-grind. 2. Re-grind. 3. Check the spindle bearing. Drill binds in the hole and squeaks. Causes Lands worn due to speed being too high or lack of cutting solution. Remedies Use a new drill. Reduce speed and use a cutting solution if the metal demands it. © Aviation Australia Twist drill parts (terminology) 2023-11-24 B-07b Maintenance Practices CASA Part 66 - Training Materials Only Page 117 of 498 Holding Work for Drilling Whenever metal parts have to be drilled, they should always be clamped securely whether drilling with fixed or portable equipment. When the work is not held properly, there is danger of: Damage to the hand or drill if the drill catches (injury) Damage to the work piece if the drill breaks through on the underside of the metal and tends to catch with consequent lifting and bending of the metal Drill breakage due to lack of rigidity. Holding by Hand For the above reasons, holding the work by hand should be avoided, but it is sometimes convenient to drill small holes with a pillar drill in long strip metal that is being held by hand. It is then advisable to use an extra stop, which is a block of metal bolted to the drill table through one of the bolting slots. The stop prevents rotation of the work, but does not prevent lifting of the work when the drill breaks through. Machine Vice The machine vice and hand vice are used for holding standard stock sections, particularly when extreme accuracy is not required. The machine vice should be bolted to the drill table except for the drilling of small holes. Machine vices vary in shape, size and cost, some having provision for swivelling the jaws to any desired angle. Machine vice 2023-11-24 B-07b Maintenance Practices CASA Part 66 - Training Materials Only Page 118 of 498 Clamping Plates Clamping plates are bolted to the work piece and held parallel to the drill table by packing pieces or adjustable stops. The clamping bolts fit either into T-slots or through bolting slots, whichever is provided on the drill table. The bolts must always be fitted so that they are nearer to the work piece than the packing; otherwise, the packing will be held more securely than the work piece. The packing must always be arranged so that the plate gives a parallel grip. The clamping plate can be made from rectangular steel strip, but drop-forged plates are stiffer with less likelihood of bending under pressure. Clamping plates 2023-11-24 B-07b Maintenance Practices CASA Part 66 - Training Materials Only Page 119 of 498 Vee Blocks The Vee Block Vee blocks are used to support round stock that has to be drilled, marked out or checked. When drilling rod diametrically, the set-up must be firm with no possibility of movement because: The drill might wander off the centre on the curved surface. The drill is inclined to bite fiercely when breaking through a curved surface. For diametric drilling, a centre line is needed on the end of the rod, which must be in a vertical position for drilling. Clamping plates are used to fix the vee blocks and work piece in position on the drill table. A vee block resting on its end supports the rod vertically for drilling. For light drilling, the rod and block may be held by hand, but for heavy and accurate drilling, the block and work must be clamped to the side face of the drill table. Vee block holding work for drilling 2023-11-24 B-07b Maintenance Practices CASA Part 66 - Training Materials Only Page 120 of 498 Vee block holding round stock vertically Angle Plates Angle plates are useful when awkward shapes or casting have to be drilled and when work needs clamping at right angles to the drill table. Angle plates When drilling thin plate and sheet metal, whether with a fixed drill or a portable one, a wooden or fibre backing block should be used to prevent distortion and reduce the risk of the drill snatching as it breaks through. When held in a bench vice for hand drilling, protective soft jaws should always be used to protect the work piece. 2023-11-24 B-07b Maintenance Practices CASA Part 66 - Training Materials Only Page 121 of 498 Drilling in a vice Avoid drilling parts in situ (i.e. fitted to the aircraft). Instead, parts should be marked in place, then removed and drilled at a bench. Where it is unavoidable, great care must be taken not to damage the work piece or the surrounding structure. Parts should be held securely with skin pins, G-clamps or hand vices as applicable and backed with wooden blocks to prevent distortion. It is important to ensure that the drill does not contact existing structure or fasteners as it breaks through. Drilling in situ When transferring holes from existing structure into new or repair material, a drill bush should be used to prevent enlargement of the original hole. The pilot hole produced guides the drill tip and reduces damage to the existing structure. Alternatively, a pattern of suitable material, such as acetate sheet, may be used to transfer hole positions to the new part. 2023-11-24 B-07b Maintenance Practices CASA Part 66 - Training Materials Only Page 122 of 498 Using a drill bush 2023-11-24 B-07b Maintenance Practices CASA Part 66 - Training Materials Only Page 123 of 498 Reamers The Reamer Drills cannot make holes with sufficient accuracy for certain applications. However, if a hole is drilled undersized and then reamed to a finished size, extremely accurate hole sizes are obtained. A reamer does not drill a hole but enlarges an existing hole, making it round, smooth and accurate in size. The purpose of reaming is to produce the required sized hole with a high degree of: accuracy finish concentricity. The accuracy of a reamer depends on its diameter, e.g. a 1/2-in. diameter reamer should be accurate to a limit of about 0.0005 in. A reamer only follows a previously drilled hole and does not alter that hole in relation to accuracy of position or direction. Machine reamers have a Morse taper shank and fit directly into the machine spindle, e.g. the lathe tail stock. Some have straight flutes, but more often the flutes form a left-facing helix or spiral. If the helix is right-facing, as in a twist drill, the reamer tries to screw itself into the metal. Hand reamers are used by hand in a tap wrench. They may have straight or helical flutes like machine reamers, and their extreme end is tapered slightly to give it a lead into the hole. Straight-fluted reamers are cheaper to produce but have a greater tendency to chatter. Reamers are used with a clockwise or rightwards rotation, and no backwards turns are necessary as with a tap. Cutting solutions must be used as for drilling. Reamer cross-section 2023-11-24 B-07b Maintenance Practices CASA Part 66 - Training Materials Only Page 124 of 498 Machine and hand reamers Taper reamers taper over their whole length and are used only for reaming taper holes, e.g. for fitting taper pins or cotters. Prior to reaming, the hole is normally step drilled, and great care must be taken that the steps do not exceed the taper as the hole quality will be damaged. 2023-11-24 B-07b Maintenance Practices CASA Part 66 - Training Materials Only Page 125 of 498 Taper reamer Adjustable and expanding reamers are used to ream holes to a non-standard dimension to accommodate a component which may be slightly worn. The expanding hand reamer can be varied in size to suit this type of work, but its range is very limited, usually a maximum of 1/16 in. It can be reground when blunt and then adjusted back to size. The simplest type of expanding reamer is similar to the ordinary straight-flute type, but has a hollow body, split to facilitate expansion. It is fitted with an internal bolt and a hardened conical nut that can be screwed into the hollow body to increase the cutting diameter. This reamer is easy to adjust while on the machine and, when worn, can be reground and re-adjusted to size again. The life of the expanding reamer is much longer than that of the solid type. 2023-11-24 B-07b Maintenance Practices CASA Part 66 - Training Materials Only Page 126 of 498 Expanding reamer The adjustable reamer has inserted blades which neatly fit into machined slots in the body of the reamer. They are made with either solid or hollow bodies and straight or angular blades. The bottom of each slot is tapered and the cutting blades are made with a corresponding taper. (The two tapered surfaces keep the cutting edges of the blades parallel.) The cutting blades are held in place with a nut at each end. The diameter is adjusted by moving the blades up or down the taper, tightening and loosening the nuts as appropriate. They are capable of considerable adjustment and the blades can be replaced when worn out or damaged. 2023-11-24 B-07b Maintenance Practices CASA Part 66 - Training Materials Only Page 127 of 498 Adjustable reamer Piloted chucking reamers are used in conjunction with air drills where a large amount of holes are to be produced and there is a requirement for a high degree of accuracy due to the pilot used. Piloted chucking reamers are produced in increments of 1/64 in. in varying types of fits, i.e. interference fit. The pilot is the same size as the final size of the previous sized reamer. 2023-11-24 B-07b Maintenance Practices CASA Part 66 - Training Materials Only Page 128 of 498 Reaming Practices Care of Reamers Reamers are expensive, high-precision cutting tools and need to be treated with extreme care. When blunted, they can be sharpened only by grinding in the flutes. This task requires a special tool and cutter grinder, and the number of re-grinds possible before the reamer becomes undersized is limited. Therefore, always ensure that the reamer is used correctly and that the drilled hole gives the correct allowance for reaming. Allowances for Reaming The amount of metal removed by the reamer is small. If too much is left for reaming, the reamer cuts inefficiently and deteriorates through excessive wear. The allowance for reaming depends on the size of the hole and type of metal being used. For holes up to 1/2-in. diameter, the allowance should be 0.003–0.005 in. For holes above 1/2-in. diameter, the allowance should be correspondingly larger. If the hole is too large, the reamer will slide rather than cut through the hole. When a reamer is turned in the hole rather than cutting, it dulls quickly. 2023-11-24 B-07b Maintenance Practices CASA Part 66 - Training Materials Only Page 129 of 498 Reaming Process Machine reaming should be done at about half the speed and twice the feed of the drilling process for the hole size. Hand reaming should be done at a constant speed and pressure to prevent chattering and scoring of the hole surface. The reamer should be turned in the same direction throughout the process, including during withdrawal. When taper reaming, great care must be taken not to oversize the hole. Expanding and adjustable reamers must be checked with a micrometer prior to use. Remember that the expanding reamer only reaches its full diameter for part of its length, and so must be passed through the full depth of the hole. Again, as with standard reamers, it should be turned in the same direction throughout the process, including during withdrawal. Aviation Australia Reamer sizing into metal 2023-11-24 B-07b Maintenance Practices CASA Part 66 - Training Materials Only Page 130 of 498 Thread Cutting Internal Screw Thread Cutting Taps Taps are used for hand cutting internal (female) screw threads of the common types, up to a maximum diameter of approximately 25.4 mm (1.0 in.). They are short, threaded bars of hardened and tempered steel which are fluted to give cutting edges, and the end of the shank is squared to facilitate turning with a wrench. Taps are normally made in sets of three, with the exception of the BA thread tap sets, which have only two taps to a set. A tap set, which all have the same maximum diameter, normally consists of a: Taper tap Intermediate tap Bottoming (plug) tap. Tap set The taper tap is used to start the thread-cutting process. It is tapered gradually from the point for about two thirds of the threaded length so it can enter the pre-drilled hole easily and assist in the correct alignment of the tap (which is very important) before cutting commences. The last third of its length has fully formed threads. 2023-11-24 B-07b Maintenance Practices CASA Part 66 - Training Materials Only Page 131 of 498 The second (or intermediate) tap is used, following the taper tap, to deepen the thread. This tap is tapered for the first two or three threads only and, where it is possible for the tap to pass the whole length through a hole, it is capable of cutting a fully formed thread. The Intermediate is the tap that is not available in BA thread tapping sets. The bottoming (or plug) tap has no taper and its purpose is to finish the threads in deep through holes or to cut threads to the bottom of ‘blind’ holes. Tap design 2023-11-24 B-07b Maintenance Practices CASA Part 66 - Training Materials Only Page 132 of 498 Preparing and Cutting Threads Before the thread can be cut, a hole must be drilled in the work piece. This hole must be of the correct size, and the drill that is selected (the tapping drill) must have the same diameter as the minor diameter of the thread needed to be cut. The correct tapping drill size can be obtained from workshop charts and reference books. Unfortunately, because taps are ‘glass hard’, they are also brittle and can be easily broken if due care is not given to their use. It is imperative that the tap’s location in the drilled hole be constantly confirmed and that its main axis is maintained in proper alignment with the corresponding axis of the hole. Adequate cutting fluid (as used in the drilling procedure) must be applied, and the arms of the wrench should be of an appropriate length (not too long) to minimise the possibility of the tap wobbling in the hole or of excessive turning force being applied to the tap (especially to smaller diameter taps). If a tap jams and snaps off in a hole, its removal can cause serious difficulties. After drilling of the correct sized hole, the tapping procedure involves ensuring that the workpiece is securely held (firmly attached to another component or clamped in a vice) and that the taper tap is attached to the correct size wrench. Taps, incidentally, may have right- or left-facing threads. There are two main types of tap wrenches. The T-handle wrench is used when working in a confined space. The bar handle is more commonly used and allows for good grip and control while tapping. Tap wrench types 2023-11-24 B-07b Maintenance Practices CASA Part 66 - Training Materials Only Page 133 of 498 With lubricant as required, the taper tap is inserted into the hole and its correct alignment verified (for example, with an engineer’s square), before it is rotated clockwise (for a right-facing thread), slowly and gently until the initial threads are established. Once the initial threads are established, the tap must not be rotated continuously, or the cuttings will not break off and the tap will jam in the hole and, if forced, will shatter. To this end, after each full turn, the tap is rotated backwards approximately one half to three quarters of a turn to break the cuttings off. The forward rotation is then continued, with subsequent cutting breaks, until the full thread portion of the tap has cut sufficient full threads in the hole. After the preliminary cut, the process is repeated using the second tap (if not a BA thread) and, if required, repeated again using the plug tap. The thread and each end of the hole (where accessible) should be cleaned out if burrs or swarf are present and, with blind holes, the swarf must be cleared out regularly to prevent the tap binding at the bottom of the hole. If a tap breaks in a hole, it may be necessary to resort to specialist procedures such as spark erosion for its removal without causing further, possibly expensive, damage to the component or work piece. Cutting Internal Threads The first step in producing a well-cut internal screw thread is drilling the hole to the correct tapping size. This should be the core diameter of the thread, but practically, the hole needs to be slightly larger to prevent the tap from binding and possibly breaking. To find the correct drill for use, consult an Engineer’s Pocket Book, which gives tapping drill sizes. If the book is not available, the correct drill size may be obtained by: Measuring the core diameter and taking the nearest size drill which is slightly larger than the core diameter. Selecting a drill which will just pass through a nut of the appropriate size. Having drilled a hole to the correct dimensions, ensure that the work is held rigidly in a vice. Enter the tap perpendicular to the face and turn in the cutting direction until the thread is just started. Test the tap for squareness using a fitter’s square. When satisfied that the tap is square, continue turning in the cutting direction for half a turn, then reverse the direction for a quarter turn. This continuous action will break the cutting into chips and prevent straining the taps. Continue cutting the thread as described until either the bottom of a blind hole has been reached or the full cutting length of the tap has been used. Change to the second or plug tap as required and continue until the thread has been properly cut. Lubricate the work using cutting oil for steel, copper and bronze, or paraffin for aluminium and aluminium alloys. 2023-11-24 B-07b Maintenance Practices CASA Part 66 - Training Materials Only Page 134 of 498 Brass and cast iron do not require a lubricant. Cutting internal threads 2023-11-24 B-07b Maintenance Practices CASA Part 66 - Training Materials Only Page 135 of 498 Tap Breakage Reasons for Tap Breakage Not using taps in the correct order. Undersize drilled hole. Blind hole not drilled deep enough to allow clearance for chippings. Chippings not being cleared out of blind hole. Bottoming tap in blind hole. Removing a Broken Tap If a sufficient amount of tap is projecting above the surface and not too great a length embedded in the hole, it is sometimes possible to remove the tap with a pair of pliers. Providing the melting point of the work is above the annealing temperature of the tap, anneal both the work and the tap. The tap can then be drilled out and the hole re-tapped. Large taps can often be unscrewed or broken into pieces with an old punch or chisel. Broken taps can be removed using an extractor. There are two types of extractor: 1. A screw extractor which has a left-facing thread. It requires the tap to be annealed and drilled. 2. For larger taps only, an extractor can be used that has a set of prongs which fit inside the flutes of the tap. No drilling or annealing is required. 2023-11-24 B-07b Maintenance Practices CASA Part 66 - Training Materials Only Page 136 of 498 External Screw Thread Cutting Dies Dies are used for hand cutting external (male) threads on round rods, bars or pipes of comparatively small diameters. While there are several designs of dies (depending on the diameter of the thread being cut), here we examine only the ‘split’ circular or button dies typically found in aircraft maintenance workshops and used by aircraft technicians to manufacture studs and similar items. Circular dies consist of an internally threaded (right- or left-handed) disc of hardened and tempered steel, which is fluted to form several cutting edges. Dies also need to be rotated (similarly to the previously mentioned taps) to cut threads, but unlike a tap and wrench, a die is rotated using a stock. Button die Die discs within the smaller diameter ranges have a standard outside diameter which allows a range of dies with different internal sizes to be used with the same standard stock. The discs are ‘split’ to allow for a degree of adjustment to the depth of the thread being cut. Die stock 2023-11-24 B-07b Maintenance Practices CASA Part 66 - Training Materials Only Page 137 of 498 The manufacturer’s name, thread type, diameter and number of threads per millimetre (or inch) are marked on the face of the die (taps, incidentally, are similarly marked on their shanks). A shallow taper, or chamfer, must be ground or filed onto the end of the rod to help locate the die before cutting commences, and the rod should be clamped firmly and, preferably, vertically in the bench vice with the tapered end uppermost. Once more, adequate lubrication must be used throughout the procedure, again, using the same lubricants as for drilling and tapping. Ensuring that the die is set to cut the maximum diameter, as described previously, the die should be placed squarely onto the taper of the rod and, with steady downwards hand pressure, carefully rotated (clockwise) to start the cut. The die must remain square to the rod at all times while cutting, continuing in a series of small arcs and reversing each time to sever the cuttings, as is done when using the taps. When enough thread has been cut, the die is removed and the thread checked using a finished nut. If the thread proves to be too tight, then, after backing off the centre adjusting screw and (carefully) turning the outer adjusting screws inwards, another cut is made with the die. The procedure is repeated as often as necessary until a satisfactory fit is achieved between the two mating threaded items. As the internal tapped thread is not adjustable, the internal thread should be cut first. The external thread, which can be slightly adjusted, should always be cut last to ensure the desired degree of fit between the respective threads. There are two types of die: Circular – generally used for cutting threads of a smaller size. Slight adjustment can be effected by the screws in the side of the stock. The die thread is tapered to allow an easier start. When fitting the die to the stock, the tapered side must always be away from the shoulder of the stock. AA Circular die 2023-11-24 B-07b Maintenance Practices CASA Part 66 - Training Materials Only Page 138 of 498 Rectangular – a two-piece die which is adjustable and is used for cutting larger diameter threads. Two or three cuts may be required to cut the full thread, the die being closed up after each cut. The die has tapered threads to allow easier starting. The engraved numbers on the two halves must be fitted on the same side. Rectangular - two piece die Cutting External Threads (Using Circular Die) 1. Secure the work in the vice. 2. Slightly taper the rod end to assist the start. 3. Slacken the two outer screws in the stock. Tighten the centre screw and re-tighten the outer screws. 4. Place the stock and die squarely on the rod and commence cutting the thread, using the same technique as for taps. 5. With the thread cut, try a nut on the new thread. 6. If further cutting is required, slightly loosen the centre screw of the stock, tighten the two outer screws and re-tighten the centre screw. 7. Repeat steps 4, 5 and 6 until the nut is a good fit on the thread. 2023-11-24 B-07b Maintenance Practices CASA Part 66 - Training Materials Only Page 139 of 498 Die Nuts Die nuts are made of high-quality chromium tool steel to exacting specifications. They are similar in shape to normal hexagon or square nuts. They are not intended for cutting threads, but are used for easing or restoring damaged threads on studs or bolts. They are turned by a suitably sized spanner. AA Die nuts - hexagonal Tap and Die Precautions Aviation Australia Tap and Die Precautions 2023-11-24 B-07b Maintenance Practices CASA Part 66 - Training Materials Only Page 140 of 498