Document Details
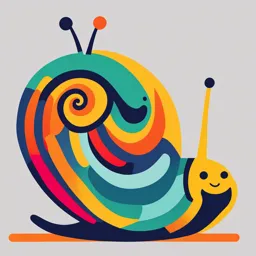
Uploaded by PatriIllumination
Full Transcript
the cable core, installed in conduit, shall be sealed in the Class I, Division 1 location after the jacket and any other coverings have been removed so that the sealing compound can surround each individual insulated conductor or optical fiber tube and the outer jacket. Exception: Multiconductor cab...
the cable core, installed in conduit, shall be sealed in the Class I, Division 1 location after the jacket and any other coverings have been removed so that the sealing compound can surround each individual insulated conductor or optical fiber tube and the outer jacket. Exception: Multiconductor cables with a gas/vaportight continuous sheath capable of transmitting gases or vapors through the cable core shall be permitted to be considered a single conductor if the cable is sealed in the conduit within 450 mm (18 in.) of the enclosure and the cable end is sealed within the enclosure by an approved means to minimize the entrance of gases or vapors and prevent the propagation of flame into the cable core, or by other approved methods. If both requirements are met, the shielding material shall not be required to be removed and the twisted pairs of shielded cables and twisted pair cables shall not be required to be separated. ENHANCED CONTENT Collapse In addition to the conduit seal, the cable within the conduit also must be sealed to prevent gases from passing through the cable. A single conduit seal can serve both purposes, sealing the conduit and sealing the cable. Cables Incapable of Transmitting Gases or Vapors. Each multiconductor cable installed in conduit shall be considered as a single conductor if the cable is incapable of transmitting gases or vapors through the cable core. These cables shall be sealed in accordance with 501.15(A). Cable Seals, Class I, Division 2. In Division 2 locations, cable seals shall be located in accordance with 501.15(E)(1) through (E)(4). Exception: Cables with an unbroken gas/vaportight continuous sheath shall be permitted to pass through a Division 2 location without seals. Terminations. Cables entering enclosures that are required to be explosionproof shall be sealed at the point of entrance into the enclosure. The sealing fitting shall comply with 501.15(B)(1) or be explosionproof. Multiconductor or optical multifiber cables with a gas/vaportight continuous sheath capable of transmitting gases or vapors through the cable core that are installed in a Division 2 location shall be sealed with a listed fitting after the jacket and any other coverings have been removedsuch that the sealing compound surrounds each individual insulated conductor or optical fiber tube to minimize the passage of gases and vapors. Multiconductor or optical multifiber cables installed in conduit shall be sealed in accordance with 501.15(D). Exception No. 1: Cables leaving an enclosure or room that is permitted to use general-purpose equipment as a result of Type Z pressurization and entering a Division 2 location shall not require a seal at the boundary. Exception No. 2: Removal of shielding material from shielded cables and separation of twisted pair cables shall not be required if the conductors are sealed in accordance with instructions provided with the listed fitting to minimize the entrance of gases or vapors and prevent propagation of flame into the cable core. (2) Cables That Do Not Transmit Gases or Vapors. Cables that have a gas/vaportight continuous sheath and do not transmit gases or vapors through the cable core in excess of the quantity permitted for seal fittings shall not be required to be sealed except as required in 501.15(E)(1). The minimum length of such a cable run shall not be less than the length needed to limit gas or vapor flow through the cable core, excluding the interstices of the conductor strands, to the rate permitted for seal fittings [200 cm3/hr (0.007 ft3/hr) of air at a pressure of 1500 pascals (6 in. of water)]. ENHANCED CONTENT Collapse The ability of a cable to transmit gases or vapors through the core (primarily between insulated conductors) depends not only on how tightly packed the conductors are within the outer sheaths and the location and composition of fillers but also on how the cable has been handled and the geometry of the cable run. If any concern that the cable run is capable of transmitting gases or vapors through the core exists, a seal fitting should be installed. See also 501.15, Informational Note No. 2, and its enhanced content for more on seal fittings. Cables Capable of Transmitting Gases or Vapors. Cables with a gas/vaportight continuous sheath capable of transmitting gases or vapors through the cable core shall not be required to be sealed except as required in 501.15(E)(1), unless the cable is attached to process equipment or devices that may cause a pressure in excess of 1500 pascals (6 in. of water) to be exerted at a cable end, in which case a seal, a barrier, or other means shall be provided to prevent migration of flammables into an unclassified location. Cables Without Gas/Vaportight Sheath. Cables that do not have a gas/vaportight continuous sheath shall be sealed at the boundary of the Division 2 and unclassified location in such a manner as to minimize the passage of gases or vapors into an unclassified location. Drainage. ENHANCED CONTENT Collapse Pictured below is a seal designed for use in a vertical run of conduit to provide drainage for any condensation trapped above the enclosure by the seal. Any accumulation of water runs down over the surface of the sealing compound, flowing through an explosionproof drain. A combination drain and breather fitting is shown below. This fitting is specifically designed to permit the escape of accumulated water through its drain and to allow the continuous circulation of air through the breather, preventing condensation of moisture that could be present while still providing explosionproof protection. (Images Courtesy of AppletonTM, Emerson Electric Co.) Control Equipment. Where there is a probability that liquid or other condensed vapor may be trapped within enclosures for control equipment or at any point in the raceway system, approved means shall be provided to prevent accumulation or to permit periodic draining of such liquid or condensed vapor. Motors and Generators. Where liquid or condensed vapor may accumulate within motors or generators, joints and conduit systems shall be arranged to minimize the entrance of liquid. If means to prevent accumulation or to permit periodic draining are necessary, such means shall be provided at the time of manufacture and shall be considered an integral part of the machine. 501.17 Process Sealing. Process-connected equipment, including, but not limited to, canned pumps, submersible pumps, and flow, pressure, temperature, or analysis measurement instruments, shall be sealed with process seals. A process seal shall be a device that prevents the migration of process fluids from the designed containment into the external electrical system. Process-connected electrical equipment that incorporates a single process seal, such as a single compression seal, diaphragm, or tube to prevent flammable or combustible fluids from entering a conduit or cable system capable of transmitting fluids, shall be provided with an additional means to mitigate a single process seal failure. The additional means might include, but are not limited to, the following: (1) A suitable barrier meeting the process temperature and pressure conditions that the barrier will be subjected to upon failure of the single process seal. There shall be a vent or drain between the single process seal and the suitable barrier. Indication of the single process seal failure shall be provided by visible leakage, an audible whistle, or other means of monitoring. A listed Type MI cable assembly, rated at not less than 125 percent of the process pressure and not less than 125 percent of the maximum process temperature (in degrees Celsius), installed between the cable or conduit and the single process seal. A drain or vent located between the single process seal and a conduit or cable seal. The drain or vent shall be sufficiently sized to prevent overpressuring the conduit or cable seal above 6 in. water column (1493 Pa). Indication of the single process seal failure shall be provided by visible leakage, an audible whistle, or other means of monitoring. An add-on secondary seal marked “secondary seal†and rated for the pressure and temperature conditions to which it will be subjected upon failure of the single process seal. Process-connected electrical equipment that does not rely on a single process seal or is listed and marked “single sealâ€, “dual sealâ€, or “dual seal without annunciation†shall not be required to be provided with an additional means of sealing. Process-connected electrical equipment marked “single seal — install conduit or cable seal†shall be sealed in accordance with 501.15. Informational Note: See ANSI/UL 122701, Requirements for Process Sealing Between Electrical Systems and Flammable or Combustible Process Fluids, for construction and testing requirements for process sealing of listed and marked single seal, dual seal, or secondary seal equipment. ENHANCED CONTENT Collapse In addition to the primary seal provided with canned pumps and other process equipment that operate above atmospheric pressure, 501.17 requires a second means to prevent fluid from entering the electrical conduit or cable system if the primary seal fails. The method employed is not limited to the four common techniques described. 501.20 Conductor Insulation, Class I, Divisions 1 and 2. Where condensed vapors or liquids may collect on, or come in contact with, the insulation on conductors, such insulation shall be of a type identified for use under such conditions; or the insulation shall be protected by a sheath of lead or by other approved means. ENHANCED CONTENT Collapse Type THWN conductors are commonly used in areas where they could be exposed to gasoline because of their ease of handling. Not all Type THWN conductors are suitable where they could be exposed to gasoline. THWN wire suitable for exposure to liquid gasoline and gasoline vapors at ordinary ambient temperature is marked ‘‘Gasoline and Oil Resistant I’’ (or “GR1â€) or ‘‘Gasoline and Oil Resistant II’’ (or “GR2â€). See the UL Guide Information for Electrical Equipment for further information on these cables. 501.25 Uninsulated Exposed Parts, Class I, Divisions 1 and 2. There shall be no uninsulated exposed parts, such as electrical conductors, buses, terminals, or components, that operate at more than 30 volts (15 volts in wet locations). These parts shall additionally be protected by a protection technique according to 500.7(E), (F), or (G) that is suitable for the location. ENHANCED CONTENT Collapse The intrinsically safe or nonincendive techniques listed in 500.7 limit the circuit’s energy to a level incapable of causing ignition in the hazardous area. 501.30 Grounding and Bonding. Regardless of the voltage of the electrical system, wiring systems and equipment shall comply with 501.30(A) and (B). Grounding. Wiring systems and equipment shall be grounded in accordance with Part I and Part VI of Article 250, as applicable. Bonding. Bonding shall comply with Part I and Part V of Article 250, as applicable, and 501.30(B)(1) and (B)(2). Specific Bonding Means. Bonding shall comply with 501.30(B)(1)(a) and (B)(1)(b). The locknut-bushing and double-locknut types of contacts shall not be depended on for bonding purposes, but bonding jumpers with identified fittings or other approved means of bonding shall be used. These bonding means shall apply to all metal raceways, fittings, boxes, cable trays, and enclosures, and other parts of raceway systems between Class I locations and the point of grounding for service equipment or point of grounding for a separately derived system. Metal struts, angles, or channels provided for support and mechanical or physical protection as permitted in 335.4(5), 336.10(7)(c), or 722.135(C) shall be bonded in accordance with 250.102. Where the branch-circuit overcurrent protection is located on the load side of the disconnecting means, the specific bonding means shall be permitted to end at the nearest point where the grounded circuit conductor and the grounding electrode conductor are connected together on the line side of the building or structure disconnecting means as specified in 250.32(B). ENHANCED CONTENT Collapse The specific bonding methods mentioned in this section are intended to provide a mechanical/electrical connection that is low impedance and free from accidental arcing due to loose connections; they apply to raceways and raceway-to-enclosure connections both inside and outside the hazardous location. Section 250.100 specifies this enhanced level of bonding for all raceways and enclosures, and the requirement is not contingent on the circuit voltage. This includes metal raceways and enclosures containing signaling, communications, or other power-limited circuits. Section 250.100 clarifies that the installation of a wire-type equipment grounding conductor (EGC) in a metal raceway does not negate the special raceway and enclosure bonding requirements. The electrical continuity of raceways and raceway-to-enclosure connections must always be ensured through compliance with 250.100 and 501.30(A), regardless of whether a wire-type EGC has been installed in the raceway. Section 501.30(B)(1)(b) covers the grounding and bonding requirements that are specific to hazardous locations where the installation occurs at a multibuilding or multi-structure setting. If the service equipment and the electrical equipment supplying the hazardous location are not located in the same building or structure, applying the bonding requirement of 501.30(A) from the hazardous location back to the service equipment is not required. It is necessary only to apply the bonding requirement from the hazardous location back to the grounding electrode connection to the grounded conductor on the line side of the building or structure disconnecting means. Flexible Metal Conduit and Liquidtight Flexible Metal Conduit. Flexible metal conduit and liquidtight flexible metal conduit shall comply with 501.30(B)(2)(a) and (B)(2)(b). Flexible metal conduit and liquidtight flexible metal conduit shall include an equipment bonding jumper of the wire type in accordance with 250.102. In Class I, Division 2 locations, the bonding jumper shall not be required where all of the following conditions are met: Listed liquidtight flexible metal conduit 1.8 m (6 ft) or less in length, with fittings listed for grounding, is used. Overcurrent protection in the circuit is limited to 10 amperes or less. The load is part of a meter, instrument, or relay circuit. 501.35 Surge Protection. (A) Class I, Division 1. Surge arresters, surge-protective devices, and capacitors shall be installed in enclosures identified for Class I, Division 1 locations. Surge-protective capacitors shall be of a type designed for specific duty. Class I, Division 2. Surge arresters and surge-protective devices shall be nonarcing, such as metal-oxide varistor (MOV) sealed type, and surge-protective capacitors shall be of a type designed for specific duty. Enclosures shall be permitted to be of the general-purpose type. Surge protection of types other than described in this paragraph shall be installed in enclosures identified for Class I, Division 1 locations. ENHANCED CONTENT Collapse In Class I, Division 2 locations, only spark-producing types of surge arresters require installation in an enclosure identified for the location. Nonarcing, sealed, and solid state–type surge-protective devices (SPDs) are permitted where installed in a general-purpose-type enclosure. Surge arresters can also be installed in oil-filled enclosures or have the arcing or sparking contacts enclosed in hermetically sealed chambers. Part III. Equipment 501.100 Transformers and Capacitors. (A) Class I, Division 1. In Class I, Division 1 locations, transformers and capacitors shall comply with 501.100(A)(1) and (A)(2). Containing Liquid That Will Burn. Transformers and capacitors containing a liquid that will burn shall be installed only in vaults that comply with 450.41 through 450.48 and with (1) through (4) as follows: There shall be no door or other communicating opening between the vault and the Division 1 location. Ample ventilation shall be provided for the continuous removal of flammable gases or vapors. Vent openings or ducts shall lead to a safe location outside of buildings. Vent ducts and openings shall be of sufficient area to relieve explosion pressures within the vault, and all portions of vent ducts within the buildings shall be of reinforced concrete construction. Not Containing Liquid That Will Burn. Transformers and capacitors that do not contain a liquid that will burn shall be installed in vaults complying with 501.100(A)(1) or be identified for Class I locations. Class I, Division 2. In Class I, Division 2 locations, transformers shall comply with 450.21 through 450.27, and capacitors shall comply with 460.3 through 460.28. 501.105 Meters, Instruments, and Relays. Class I, Division 1. In Class I, Division 1 locations, meters, instruments, and relays, including kilowatt-hour meters, instrument transformers, resistors, rectifiers, and thermionic tubes, shall be provided with enclosures identified for Class I, Division 1 locations. Enclosures for Class I, Division 1 locations include explosionproof enclosures and purged and pressurized enclosures. Informational Note: See NFPA 496, Standard for Purged and Pressurized Enclosures for Electrical Equipment. (B) Class I, Division 2. In Class I, Division 2 locations, meters, instruments, and relays shall comply with 501.105(B)(2) through (B)(6). General-Purpose Assemblies. Where an assembly is made up of components for which general-purpose enclosures are acceptable as provided in 501.105(B)(1), (B)(2), and (B)(3), a single general-purpose enclosure shall be acceptable for the assembly. Where such an assembly includes any of the equipment described in 501.105(B)(1), 501.105(B)(2), and 501.105(B)(3), the maximum obtainable surface temperature of any component of the assembly that exceeds 100°C shall be clearly and permanently indicated on the outside of the enclosure. Alternatively, equipment shall be permitted to be marked to indicate the temperature class for which it is suitable, using the temperature class (T Code) of Table 500.8(C)(4). Contacts. Switches, circuit breakers, and make-and-break contacts of pushbuttons, relays, alarm bells, and horns shall have enclosures identified for Class I, Division 1 locations in accordance with 501.105(A). Exception: General-purpose enclosures shall be permitted if current-interrupting contacts comply with one of the following: (1) Are immersed in oil (2) Are enclosed within a chamber that is hermetically sealed against the entrance of gases or vapors (3) Are in nonincendive circuits (4) Are listed for Division 2 locations ENHANCED CONTENT Collapse This exception identifies the conditions under which general-purpose enclosures are permitted for certain equipment in Class 1, Division 2 locations. Although gasketed seals can be very effective, depending on the gasket material used, gasket materials can be damaged and deteriorate rapidly if exposed to atmospheres that contain solvent vapors. In accordance with the definition in Article 100 of hermetically sealed, such enclosures cannot be used to satisfy those requirements in which hermetic sealing is recognized as a protection technique. This does not mean that the entire enclosure or circuit is required to qualify as being protected by one of these techniques, only that the contacts need such protection. Resistors and Similar Equipment. Resistors, resistance devices, thermionic tubes, rectifiers, and similar equipment that are used in or in connection with meters, instruments, and relays shall comply with 501.105(A). Exception: General-purpose-type enclosures shall be permitted if such equipment is without make-and-break or sliding contacts [other than as provided in 501.105(B)(2)] and if the marked maximum operating temperature of any exposed surface will not exceed 80 percent of the autoignition temperature in degrees Celsius of the gas or vapor involved or has been tested and found incapable of igniting the gas or vapor. This exception shall not apply to thermionic tubes. (4) Without Make-or-Break Contacts. Transformer windings, impedance coils, solenoids, and other windings that do not incorporate sliding or make-or-break contacts shall be provided with enclosures. General-purpose-type enclosures shall be permitted. Fuses. Where general-purpose enclosures are permitted in 501.105(B)(2) through (B)(4), fuses for overcurrent protection of instrument circuits not subject to overloading in normal use shall be permitted to be mounted in general-purpose enclosures if each such fuse is preceded by a switch complying with 501.105(B)(2). Connections. To facilitate replacements, process control instruments shall be permitted to be connected through flexible cord and attachment plug and receptacle if all of the following conditions apply: The attachment plug and receptacle are listed for use in Class I, Division 2 locations and listed for use with flexible cords. Exception No. 1 to (1): A Class I, Division 2 listing shall not be required if the circuit involves only nonincendive field wiring. Exception No. 2 to (1): In restricted industrial establishments, the Class I, Division 2 listing shall not be required if the requirements of 501.105(B)(6)(2), (B)(6)(3), and (B)(6)(4) are satisfied and the receptacle carries a label warning against plugging or unplugging when energized. The flexible cord does not exceed 900 mm (3 ft), is of a type listed for extra-hard usage, or is listed for hard usage and protected by location. Only necessary receptacles are provided. Unless the attachment plug and receptacle are interlocked mechanically or electrically, or otherwise designed so that they cannot be separated when the contacts are energized and the contacts cannot be energized when the plug and socket outlet are separated, a switch complying with 501.105(B)(2)is provided so that the attachment plug or receptacle is not necessary to interrupt current. Exception to (4): The switch shall not be required if the circuit is nonincendive field wiring. 501.115 Switches, Circuit Breakers, Motor Controllers, and Fuses. (A) Class I, Division 1. In Class I, Division 1 locations, switches, circuit breakers, motor controllers, and fuses, including pushbuttons, relays, and similar devices, shall be provided with enclosures, and the enclosure in each case, together with the enclosed apparatus, shall be identified as a complete assembly for use in Class I locations. ENHANCED CONTENT Collapse The explosionproof panelboard shown below consists of an assembly of branch-circuit devices enclosed in a cast metal explosionproof housing. Explosionproof panelboards are provided with bolted access covers and threaded conduit-entry hubs designed to withstand the force of an internal explosion. A cylindrical-type (spin-top) combination motor controller, motor control starter, and circuit breaker in an explosionproof enclosure in shown below. The top and bottom covers are threaded for quick removal for installation and servicing. The following is an example of a standard toggle switch in an explosionproof enclosure. (Images courtesy of AppletonTM, Emerson Electric Co.) Class I, Division 2. Switches, circuit breakers, motor controllers, and fuses in Class I, Division 2 locations shall comply with 501.115(B)(1) through (B)(4). Type Required. Circuit breakers, motor controllers, and switches intended to interrupt current in the normal performance of the function for which they are installed shall be provided with enclosures identified for Class I, Division 1 locations in accordance with 501.105(A), unless general-purpose enclosures are provide