Document Details
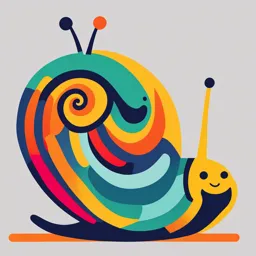
Uploaded by PatriIllumination
Full Transcript
riable, the conductor ampacity shall not be less than 125 percent of the phase converter nameplate single-phase input full-load amperes. Fixed Loads. Where the phase converter supplies specific fixed loads, and the conductor ampacity is less than 125 percent of the phase converter nameplate single-...
riable, the conductor ampacity shall not be less than 125 percent of the phase converter nameplate single-phase input full-load amperes. Fixed Loads. Where the phase converter supplies specific fixed loads, and the conductor ampacity is less than 125 percent of the phase converter nameplate single-phase input full-load amperes, the conductors shall have an ampacity not less than 250 percent of the sum of the full-load, 3-phase current rating of the motors and other loads served where the input and output voltages of the phase converter are identical. Where the input and output voltages of the phase converter are different, the current as determined by this section shall be multiplied by the ratio of output to input voltage. ENHANCED CONTENT Collapse Manufactured Phase Marking. The manufactured phase conductors shall be identified in all accessible locations with a distinctive marking. The marking shall be consistent throughout the system and premises. ENHANCED CONTENT Collapse The manufactured phase as defined in Article 100 is the phase that is created within the rotary or static equipment and is not solidly connected to the input conductors. Identification of the manufactured phase is necessary to help installers comply with 455.9, which does not permit single-phase loads to be supplied from the manufactured phase. The method of identification is not specified by the NEC; therefore, it could be by any means acceptable to the AHJ. While many phase converters are installed to supply a specific item of equipment such as a motor or heating equipment, the use of a 3-phase distribution equipment such as a panelboard supplied from the output of a phase converter is also acceptable and may be desirable as a central point from which to run branch circuits to equipment. Identification of the manufactured phase conductor at a central distribution point such as a panelboard provides the installer with visible indication of the phase conductor that cannot be used to supply any single-phase loads that have branch circuits originating from that equipment. 455.7 Overcurrent Protection. The single-phase supply conductors and phase converter shall be protected from overcurrent by 455.7(A) or (B). Where the required fuse or nonadjustable circuit breaker rating or settings of adjustable circuit breakers do not correspond to a standard rating or setting, a higher rating or setting that does not exceed the next higher standard rating shall be permitted. Variable Loads. Where the loads to be supplied are variable, overcurrent protection shall be set at not more than 125 percent of the phase converter nameplate single-phase input full-load amperes. Fixed Loads. Where the phase converter supplies specific fixed loads and the conductors are sized in accordance with 455.6(A)(2), the conductors shall be protected in accordance with their ampacity. The overcurrent protection determined from this section shall not exceed 125 percent of the phase converter nameplate single-phase input amperes. 455.8 Disconnecting Means. Means shall be provided to disconnect simultaneously all ungrounded single-phase supply conductors to the phase converter. Location. The disconnecting means shall be readily accessible and located in sight from the phase converter. Type. The disconnecting means shall be a switch rated in horsepower, a circuit breaker, or a molded-case switch. Where only nonmotor loads are served, an ampere-rated switch shall be permitted. Rating. The ampere rating of the disconnecting means shall not be less than 115 percent of the rated maximum single-phase input full-load amperes or, for specific fixed loads, shall be permitted to be selected from 455.8(C)(1) or (C)(2). Current Rated Disconnect. The disconnecting means shall be a circuit breaker or molded-case switch with an ampere rating not less than 250 percent of the sum of the following: Full-load, 3-phase current ratings of the motors Other loads served Horsepower Rated Disconnect. The disconnecting means shall be a switch with a horsepower rating. The equivalent locked rotor current of the horsepower rating of the switch shall not be less than 200 percent of the sum of the following: Nonmotor loads The 3-phase, locked-rotor current of the largest motor as determined from Table 430.251(B) The full-load current of all other 3-phase motors operating at the same time Voltage Ratios. The calculations in 455.8(C) shall apply directly where the input and output voltages of the phase converter are identical. Where the input and output voltages of the phase converter are different, the current shall be multiplied by the ratio of the output to input voltage. 455.9 Connection of Single-Phase Loads. Where single-phase loads are connected on the load side of a phase converter, they shall not be connected to the manufactured phase. 455.10 Terminal Housings. A terminal housing in accordance with the provisions of 430.12 shall be provided on a phase converter. Part II. Specific Provisions Applicable to Different Types of Phase Converters 455.20 Disconnecting Means. The single-phase disconnecting means for the input of a static phase converter shall be permitted to serve as the disconnecting means for the phase converter and a single load if the load is within sight of the disconnecting means. 455.21 Start-Up. Power to the utilization equipment shall not be supplied until the rotary-phase converter has been started. 455.22 Power Interruption. Utilization equipment supplied by a rotary-phase converter shall be controlled in such a manner that power to the equipment will be disconnected in the event of a power interruption. Informational Note: Magnetic motor starters, magnetic contactors, and similar devices, with manual or time delay restarting for the load, provide restarting after power interruption. 455.23 Capacitors. Capacitors that are not an integral part of the rotary-phase conversion system but are installed for a motor load shall be connected to the line side of that motor overload protective device. Article 460 Capacitors Part I. General 460.1 Scope. This article covers the installation of capacitors on electrical circuits. Surge capacitors or capacitors included as a component part of other apparatus and conforming with the requirements of such apparatus are excluded from these requirements. ENHANCED CONTENT Collapse Definitions. The following term has a definition in Article 100 that is unique to its use in Article 460: Safe zone 460.3 Enclosing and Guarding. (A) Containing More Than 11 L (3 gal) of Flammable Liquid. Capacitors containing more than 11 L (3 gal) of flammable liquid shall be enclosed in vaults or outdoor fenced enclosures complying with Article 110, Part III. This limit shall apply to any single unit in an installation of capacitors. Accidental Contact. Where capacitors are accessible to unauthorized and unqualified persons, they shall be enclosed, located, or guarded so that persons cannot come into accidental contact or bring conducting materials into accidental contact with exposed energized parts, terminals, or buses associated with them. However, no additional guarding is required for enclosures accessible only to authorized and qualified persons. Part II. 1000 Volts, Nominal, or Less 460.6 Discharge of Stored Energy. Capacitors shall be provided with a means of discharging stored energy. Time of Discharge. The residual voltage of a capacitor shall be reduced to 50 volts, nominal, or less within 1 minute after the capacitor is disconnected from the source of supply. Means of Discharge. The discharge circuit shall be either permanently connected to the terminals of the capacitor or capacitor bank or provided with automatic means of connecting it to the terminals of the capacitor bank on removal of voltage from the line. Manual means of switching or connecting the discharge circuit shall not be used. 460.8 Conductors. (A) Ampacity. The ampacity of capacitor circuit conductors shall not be less than 135 percent of the rated current of the capacitor. The ampacity of conductors that connect a capacitor to the terminals of a motor or to motor circuit conductors shall not be less than one-third the ampacity of the motor circuit conductors and in no case less than 135 percent of the rated current of the capacitor. ENHANCED CONTENT Collapse Capacitors are rated in reactive kilovolt-amperes (kilovars or kVAr) or kilovolt-amperes capacitive (kVAc). Both ratings are synonymous. The kVAr rating shows how many reactive kilovolt-amperes the capacitor will supply to cancel out the reactive kilovolt-amperes caused by inductance. For example, a 20-kVAr capacitor will cancel out 20 kVAr of inductive reactive kilovolt-amperes. The capacitor circuit conductors and disconnecting means must have an ampacity not less than 135 percent of the rated current of the capacitor. Capacitors are manufactured with a tolerance of zero percent to 15 percent, so a 100-kVAr capacitor can draw a current equivalent to that of a 115-kVAr capacitor. In addition, the current draw varies directly with the line voltage, and any variation in the line voltage from a pure sine wave form causes the capacitor to draw an increased current. Considering these factors, the increased current can amount to 135 percent of the rated current of the capacitor. The current corresponding to the kVAr rating of a 3-phase capacitor, ic, is computed from the following formula: The ampacity of the conductors and the disconnecting device is then determined by multiplying ic by 1.35. Where harmonic-producing loads are present, adding capacitors to the electrical system can place the system in a harmonic resonance condition. The harmonic loads can excite the electrical system at the harmonic resonance frequency and cause overcurrent and overvoltage conditions. If capacitors are to be placed on electrical systems with harmonic loads, an engineering study should be conducted that evaluates the size and placement of capacitors and the reactive impedance and load of the system. Capacitors may need a reactor placed in series with them to help detune the electrical system from a harmonic resonance condition. Overcurrent Protection. An overcurrent device shall be provided in each ungrounded conductor for each capacitor bank. The rating or setting of the overcurrent device shall be as low as practicable. Exception: A separate overcurrent device shall not be required for a capacitor connected on the load side of a motor overload protective device. ENHANCED CONTENT Collapse Unless the exception applies, the overcurrent device must be separate from the overcurrent device protecting any other equipment or conductor. The exhibit below shows two methods of connecting capacitors in induction motor circuit for power factor correction. Disconnecting Means. A disconnecting means shall be provided in each ungrounded conductor for each capacitor bank and shall meet the following requirements: The disconnecting means shall open all ungrounded conductors simultaneously. The disconnecting means shall be permitted to disconnect the capacitor from the line as a regular operating procedure. The rating of the disconnecting means shall not be less than 135 percent of the rated current of the capacitor. Exception: A separate disconnecting means shall not be required where a capacitor is connected on the load side of a motor controller. 460.9 Rating or Setting of Motor Overload Device. Where a motor installation includes a capacitor connected on the load side of the motor overload device, the rating or setting of the motor overload device shall be based on the improved power factor of the motor circuit. The effect of the capacitor shall be disregarded in determining the motor circuit conductor rating in accordance with 430.22. ENHANCED CONTENT Collapse Where a capacitor is connected on the load side of the motor overload relays, the line current will be reduced due to an improved power factor, which must be taken into account when selecting the rating of a motor overload device. A value lower than that specified in 430.32 should be used for proper protection of the motor. The most effective power factor correction is obtained where the individual capacitors are connected closest to the inductive load. Capacitor manufacturers publish tables in which the required capacitor value is obtained by referring to the speed and the horsepower of the motor. Those values improve the motor power factor to approximately 95 percent. To improve a plant power factor, capacitor manufacturers also publish tables to assist in the calculation of the total kVAr rating of capacitors required to improve the power factor to any desired value. 460.10 Grounding. Capacitor cases shall be connected to the equipment grounding conductor. Exception: Capacitor cases shall not be connected to the equipment grounding conductor where the capacitor units are supported on a structure designed to operate at other than ground potential. 460.12 Marking. Each capacitor shall be provided with a nameplate giving the name of the manufacturer, rated voltage, frequency, kilovar or amperes, number of phases, and, if filled with a combustible liquid, the volume of liquid. Where filled with a nonflammable liquid, the nameplate shall so state. The nameplate shall also indicate whether a capacitor has a discharge device inside the case. Part III. Over 1000 Volts, Nominal 460.24 Switching. (A) Load Current. Switches shall be rated for switching of capacitive loads. Capacitor switch operation shall open all ungrounded conductors and the switch shall be capable of the following: (1) Carrying continuously not less than 135 percent of the rated current of the capacitor installation Interrupting the maximum continuous load current of each capacitor, capacitor bank, or capacitor installation that will be switched as a unit Withstanding the maximum inrush current, including contributions from adjacent capacitor installations Carrying currents due to faults on capacitor side of switch Isolation. General. A means shall be installed to isolate from all sources of voltage each capacitor, capacitor bank, or capacitor installation that will be removed from service as a unit. The isolating means shall provide a visible gap in the electrical circuit adequate for the operating voltage. Isolating or Disconnecting Switches with No Interrupting Rating. Isolating or disconnecting switches (with no interrupting rating) shall be interlocked with the load-interrupting device or be provided with prominently displayed caution signs in accordance with 495.22 to prevent switching load current. Additional Requirements for Series Capacitors. The proper switching sequence shall be ensured by use of one of the following: Mechanically sequenced isolating and bypass switches Interlocks Switching procedure prominently displayed at the switching location 460.25 Overcurrent Protection. (A) Provided to Detect and Interrupt Fault Current. A means shall be provided to detect and interrupt fault current likely to cause dangerous pressure within an individual capacitor. Single Pole or Multipole Devices. Single-pole or multipole devices shall be permitted for this purpose. Protected Individually or in Groups. Capacitors shall be permitted to be protected individually or in groups. Protective Devices Rated or Adjusted. Protective devices for capacitors or capacitor equipment shall be rated or adjusted to operate within the limits of the safe zone for individual capacitors. 460.26 Identification. Each capacitor shall be provided with a permanent nameplate giving the manufacturer’s name, rated voltage, frequency, kilovar or amperes, number of phases, and the volume of liquid identified as flammable, if such is the case. 460.27 Grounding. Capacitor cases shall be connected to the equipment grounding conductor. If the capacitor neutral point is connected to a grounding electrode conductor, the connection shall be made in accordance with Part III of Article 250. Exception: Capacitor cases shall not be connected to the equipment grounding conductor where the capacitor units are supported on a structure designed to operate at other than ground potential. 460.28 Means for Discharge. (A) Means to Reduce the Residual Voltage. A means shall be provided to reduce the residual voltage of a capacitor to 50 volts or less within 5 minutes after the capacitor is disconnected from the source of supply. Connection to Terminals. A discharge circuit shall be either permanently connected to the terminals of the capacitor or provided with automatic means of connecting it to the terminals of the capacitor bank after disconnection of the capacitor from the source of supply. The windings of motors, transformers, or other equipment directly connected to capacitors without a switch or overcurrent device interposed shall meet the requirements of 460.28(A). ENHANCED CONTENT Collapse Means are required to drain off the stored charge in a capacitor after the supply circuit has been opened. Otherwise, a person servicing the equipment could receive a severe shock, or damage could occur to the equipment. In the following exhibit, diagram (a) shows a method in which capacitors are connected in a motor circuit so that they can be switched with the motor. In that arrangement, the stored charge drains off through the windings when the circuit is opened. Diagram (b) shows another arrangement in which the capacitor is connected to the line side of the motor starter contacts. An automatic discharge device and a separate disconnecting means are required. Capacitors often are equipped with built-in resistors to drain off the stored charge, pictured below. However, that type of capacitor is not needed where the connection is as shown in diagram (a) of the exhibit above. (Courtesy of GE Energy)Article 470 Resistors and Reactors Part I. General 470.1 Scope. This article covers the installation of separate resistors and reactors on electrical circuits. Exception: This article does not cover resistors and reactors that are component parts of other apparatus. ENHANCED CONTENT Collapse Resistors are made in many sizes and shapes and for different purposes. They can be wire, ribbon, form or edgewise wound, cast or punched steel grid, or box resistors. They can be mounted in the open or in ventilated metal boxes or cabinets, depending on their use and location. Because they give off heat, resistors must be guarded and located at safe distances from combustible materials. Where mounted on switchboards or installed in control panels, they are not required to have additional guards. Current-limiting reactors are installed to limit the amount of current in a circuit under short circuit conditions. Reactors can be divided into two classes: those with iron cores and those with no magnetic materials in the windings. Both types can be air cooled or oil immersed. Mechanical stresses exist between adjacent air-core reactors due to their external fields, and the manufacturer’s recommendations should be followed in spacing and bracing units and fastening supporting insulators. 470.2 Reconditioned Equipment. Resistors. Reconditioned resistors shall not be permitted. Reactors. Reconditioned reactors shall be permitted. Part II. 1000 Volts, Nominal, or Less 470.10 Location. Resistors and reactors shall not be placed where exposed to physical damage. 470.11 Space Separation. A thermal barrier shall be required if the space between the resistors or reactors and any combustible material is less than 305 mm (12 in.). 470.12 Conductor Insulation. Insulated conductors used for connections between resistance elements and controllers shall be suitable for an operating temperature of not less than 90°C (194°F). Exception: Other conductor insulations shall be permitted for the motor starting service. Part III. Over 1000 Volts, Nominal 470.20 General. (A) Protected Against Physical Damage. Resistors and reactors shall be protected against physical damage. Isolated by Enclosure or Elevation. Resistors and reactors shall be isolated by enclosure or elevation to protect personnel from accidental contact with energized parts. Combustible Materials. Resistors and reactors shall not be installed in close enough proximity to combustible materials to constitute a fire hazard and shall have a clearance of not less than 305 mm (12 in.) from combustible materials. Clearances. Clearances from resistors and reactors to grounded surfaces shall be adequate for the voltage involved. Temperature Rise from Induced Circulating Currents. Metallic enclosures of reactors and adjacent metal parts shall be installed so that the temperature rise from induced circulating currents is not hazardous to personnel or does not constitute a fire hazard. 470.21 Grounding. Resistor and reactor cases or enclosures shall be connected to the equipment grounding conductor. Exception: Resistor or reactor cases or enclosures supported on a structure designed to operate at other than ground potential shall not be connected to the equipment grounding conductor. 470.22 Oil-Filled Reactors. Installation of oil-filled reactors, in addition to the above requirements, shall comply with applicable requirements of Part II and Part III of Article 450. Article 480 Stationary Standby Batteries 480.1 Scope. This article applies to all installations of stationary standby batteries having a capacity greater than 3.6 MJ (1 kWh). Informational Note No. 1: See Article 706 for installations that do not meet the definition of stationary standby batteries. Informational Note No. 2: The following standards are frequently referenced for the installation of stationary batteries: (1) IEEE 484, Recommended Practice for Installation Design and Installation of Vented Lead-Acid Batteries for Stationary Applications (2) IEEE 485, Recommended Practice for Sizing Vented Lead-Acid Storage Batteries for Stationary Applications (3) IEEE 1145, Recommended Practice for Installation and Maintenance of Nickel-Cadmium Batteries for Photovoltaic (PV) Systems (4) IEEE 1187, IEEE Recommended Practice for Installation Design, and Installation of Valve-Regulated Lead-Acid Batteries for Stationary Applications (5) IEEE 1375, IEEE Guide for the Protection of Stationary Battery Systems (6) IEEE 1578, Recommended Practice for Stationary Battery Electrolyte Spill Containment and Management (7) IEEE 1635/ASHRAE 21, Guide for the Ventilation and Thermal Management of Batteries for Stationary Applications (8) UL 1973, Standard for Batteries for Use in Stationary, Vehicle Auxiliary Power, and Light Electric Rail (LER) Applications (9) UL Subject 2436, Outline of Investigation for Spill Containment for Stationary Lead Acid Battery Systems (10) UL 1989, Standard for Standby Batteries (11) UL Subject 1974, Standard for Evaluation of Repurposed Batteries (12) NFPA 855-2020, Standard for the Installation of Stationary Energy Storage Systems ENHANCED CONTENT Collapse The most common types of storage cells are the lead-acid type, the alkali (nickel-cadmium) type, and the lithium-ion type. A lead-acid cell consists of a positive plate, usually lead peroxide (a semisolid compound) mounted on a framework or grid for support, and a negative plate, made of sponge lead mounted on a grid. Grids generally are made of a lead alloy, such as lead calcium, lead antimony, or lead selenium. The electrolyte is sulfuric acid and distilled water. Lithium-ion batteries, which are used in a variety of consumer electronics products, use a variety of different chemistries. They are increasingly being used in large-scale applications because they have a very high energy density. Lead-acid cells can be of the vented or sealed (valveregulated) type. Under normal charging conditions, the vented type will liberate gases — hydrogen at the negative plate and oxygen at the positive plate. The valve-regulated type provides a means to recombine the gases, thus minimizing emissions from the cell. In the alkali, or nickel-cadmium, battery, the principal active material in the positive plate is nickelous hydroxide; in the negative plat