Document Details
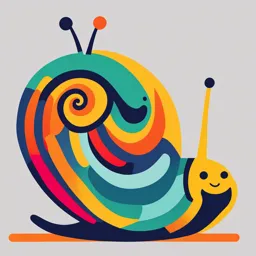
Uploaded by PatriIllumination
Full Transcript
te: Presence of hazardous gases or vapors might also necessitate sealing of underground conduits or raceways entering buildings. Article 310 Conductors for General Wiring ENHANCED CONTENT Collapse Conductors rated over 2000 volts are now located in Article 315, Medium Voltage Conductors,...
te: Presence of hazardous gases or vapors might also necessitate sealing of underground conduits or raceways entering buildings. Article 310 Conductors for General Wiring ENHANCED CONTENT Collapse Conductors rated over 2000 volts are now located in Article 315, Medium Voltage Conductors, Cable, Cable Joints, and Cable Terminations. Part I. General 310.1 Scope. This article covers general requirements for conductors rated up to and including 2000 volts and their type designations, insulations, markings, mechanical strengths, ampacity ratings, and uses. These requirements do not apply to conductors that form an integral part of equipment, such as motors, motor controllers, and similar equipment, or to conductors specifically provided for elsewhere in this Code. 310.3 Conductors. (A) Minimum Size of Conductors. The minimum size of conductors for voltage ratings up to and including 2000 volts shall be 14 AWG copper or 12 AWG aluminum or copper-clad aluminum, except as permitted elsewhere in this Code. Conductor Material. Conductors in this article shall be of copper, aluminum, or copper-clad aluminum, unless otherwise specified. Aluminum and copper-clad aluminum shall comply with the following: Solid aluminum conductors 8, 10, and 12 AWG shall be made of an AA-8000 series electrical grade aluminum alloy conductor material. Stranded aluminum conductors 8 AWG through 1000 kcmil marked as Type RHH, RHW, XHHW, XHHN, XHWN, THW, THHW, THWN, THHN, service-entrance Type SE Style U, and SE Style R shall be made of an AA-8000 series electrical grade aluminum alloy conductor material. For copper-clad aluminum conductors, the copper shall form a minimum 10 percent of the cross-sectional area of a solid conductor or each strand of a stranded conductor. The aluminum core of a copper-clad aluminum conductor shall be made of an AA-8000 series electrical grade aluminum alloy conductor material. Copper-clad aluminum conductor material shall be listed. ENHANCED CONTENT Collapse This section correlates with the UL listing requirements for testing terminations — such as copper-aluminum, revised (CO/ALR) devices and other connectors — suitable for use with aluminum conductors. The electrical industry has developed AA-8000 series aluminum alloy materials and the connectors suitable for use with aluminum conductors to provide for safe and stable connections. Connections suitable for use with aluminum conductors are also generally listed as suitable for use with copper conductors and are marked accordingly, such as AL7CU or AL9CU. Numbers 7 and 9 identify the temperature ratings of 75°C and 90°C, respectively, for these terminations. Copper-clad aluminum conductors are manufactured so that copper forms a minimum of 10 percent of the cross-sectional area of a solid conductor or of each strand of a stranded conductor. Stranded Conductors. Where installed in raceways, conductors 8 AWG and larger shall be stranded, unless specifically permitted or required elsewhere in this Code to be solid. ENHANCED CONTENT Collapse Large-size conductors are required to be stranded for greater flexibility. This requirement does not apply to conductors outside of raceways, such as busbars and the conductors of Type MI metal-sheathed cable. Special applications elsewhere in the NEC may require or permit different requirements for stranded conductors. For example, the bonding conductors of a permanently installed swimming pool are required to be solid copper conductors of 8 AWG or larger, according to 680.26(B). Insulated. Conductors not specifically permitted elsewhere in this Code to be covered or bare shall be insulated. Informational Note: See 250.184 for insulation of neutral conductors of a solidly grounded high-voltage system. Part II. Construction Specifications 310.4 Conductor Constructions and Applications. Insulated conductors shall comply with Table 310.4(1) and Table 310.4(2). Informational Note: Thermoplastic insulation may stiffen at temperatures lower than −10°C (+14°F). Thermoplastic insulation may also be deformed at normal temperatures where subjected to pressure, such as at points of support. Table 310.4(1) Conductor Applications and Insulations Rated 600 Volts Trade Name Type Letter Maximum Operating Temperature Application Provisions Insulation Thickness of Insulation AWG or kcmil mm mils Outer Covering1 Fluorinated ethylene propylene FEP or FEPB 90°C Dry and damp locations Fluorinated ethylene propylene 14–10 0.51 20 None (194°F) 8–2 0.76 30 200°C (392°F) Dry locations — special applications2 Fluorinated ethylene propylene 14–8 0.36 14 Glass braid 6–2 0.36 14 Glass or other suitable braid material Mineral insulation (metal sheathed) MI 90°C Dry and wet locations Magnesium oxide 18–163 0.58 23 Copper or alloy steel (194°F) 16–10 0.91 36 250°C For special applications2 9–4 1.27 50 (482°F) 3–500 1.40 55 Moisture-, heat-, and oil-resistant thermoplastic MTW 60°C Machine tool wiring in wet locations Flame-retardant, moisture-, heat-, and oil-resistant thermoplastic (A) (B) (A) (B) (A) None (140°F) (B) Nylon jacket or equivalent 90°C Machine tool wiring in dry locations. 22–12 0.76 0.38 30 15 (194°F) 10 0.76 0.51 30 20 8 1.14 0.76 45 30 Informational Note: See NFPA 79-2021, Electrical Standard for Industrial Machinery. 6 1.52 0.76 60 30 4–2 1.52 1.02 60 40 1–4/0 2.03 1.27 80 50 213–500 2.41 1.52 95 60 501–1000 2.79 1.78 110 70 Paper 85°C For underground service conductors, or by special permission Paper Lead sheath (185°F) Perfluoro-alkoxy PFA 90°C Dry and damp locations Perfluoro-alkoxy 14–10 0.51 20 None (194°F) 8–2 0.76 30 200°C Dry locations — special applications2 1–4/0 1.14 45 (392°F) Perfluoro-alkoxy PFAH 250°C Dry locations only. Only for leads within apparatus or within raceways connected to apparatus (nickel or nickel-coated copper only) Perfluoro-alkoxy 14–10 0.51 20 None (482°F) 8–2 0.76 30 1–4/0 1.14 45 Thermoset RHH 90°C Dry and damp locations 14-10 1.14 45 Moisture-resistant, flame-retardant, nonmetallic covering1 (194°F) 8–2 1.52 60 1–4/0 2.03 80 213–500 2.41 95 501–1000 2.79 110 1001–2000 3.18 125 Moisture-resistant thermoset RHW 75°C Dry and wet locations Flame-retardant, moisture-resistant thermoset 14–10 1.14 45 Moisture-resistant, flame-retardant, nonmetallic covering (167°F) 8–2 1.52 60 1–4/0 2.03 80 RHW-2 90°C 213–500 2.41 95 (194°F) 501–1000 2.79 110 1001–2000 3.18 125 Silicone SA 90°C Dry and damp locations Silicone rubber 14–10 1.14 45 Glass or other suitable braid material (194°F) 8–2 1.52 60 1–4/0 2.03 80 200°C For special application2 213–500 2.41 95 (392°F) 501–1000 2.79 110 1001–2000 3.18 125 Thermoset SIS 90°C Switchboard and switchgear wiring only Flame-retardant thermoset 14–10 0.76 30 None (194°F) 8–2 1.14 45 1–4/0 1.40 55 Thermoplastic and fibrous outer braid TBS 90°C Switchboard and switchgear wiring only Thermoplastic 14–10 0.76 30 Flame-retardant, nonmetallic covering (194°F) 8 1.14 45 6–2 1.52 60 1–4/0 2.03 80 Extended polytetra-fluoro-ethylene TFE 250°C Dry locations only. Only for leads within apparatus or within raceways connected to apparatus, or as open wiring (nickel or nickel-coated copper only) Extruded polytetra-fluoroethylene 14–10 0.51 20 None (482°F) 8–2 0.76 30 1–4/0 1.14 45 Heat-resistant thermoplastic THHN 90°C Dry and damp locations Flame-retardant, heat-resistant thermoplastic 14–12 0.38 15 Nylon jacket or equivalent (194°F) 10 0.51 20 8–6 0.76 30 4–2 1.02 40 1–4/0 1.27 50 250–500 1.52 60 501–1000 1.78 70 Moisture- and heat-resistant thermoplastic THHW 75°C Wet location Flame-retardant, moisture- and heat-resistant thermoplastic 14–10 0.76 30 None (167°F) 8 1.14 45 6–2 1.52 60 90°C Dry location 1–4/0 2.03 80 (194°F) 213–500 2.41 95 501–1000 2.79 110 1001–2000 3.18 125 Moisture- and heat-resistant thermoplastic THW 75°C Dry and wet locations Flame-retardant, moisture- and heat-resistant thermoplastic 14–10 0.76 30 None (167°F) 8 1.14 45 90°C Special applications within electric discharge lighting equipment. Limited to 1000 open-circuit volts or less. (Size 14-8 only as permitted in 410.68.) 6–2 1.52 60 (194°F) 1–4/0 2.03 80 213–500 2.41 95 501–1000 2.79 110 1001–2000 3.18 125 THW-2 90°C Dry and wet locations (194°F) Moisture- and heat-resistant thermoplastic THWN 75°C Dry and wet locations Flame-retardant, moisture- and heat-resistant thermoplastic 14–12 0.38 15 Nylon jacket or equivalent (167°F) 10 0.51 20 8–6 0.76 30 4–2 1.02 40 THWN-2 90°C 1–4/0 1.27 50 (194°F) 250–500 1.52 60 501–1000 1.78 70 Moisture-resistant thermoplastic TW 60°C Dry and wet locations Flame-retardant, moisture-resistant thermoplastic 14–10 0.76 30 None (140°F) 8 1.14 45 6–2 1.52 60 1–4/0 2.03 80 213–500 2.41 95 501–1000 2.79 110 1001–2000 3.18 125 Underground feeder and branch-circuit cable — single conductor (for Type UF cable employing more than one conductor, see Part II of Article 340). UF 60°C See Part II of Article 340. Moisture-resistant 14–10 1.52 605 Integral with insulation (140°F) 8–2 2.03 805 1–4/0 2.41 955 75°C Moisture- and heat-resistant (167°F)4 Underground service-entrance cable — single conductor (for Type USE cable employing more than one conductor, see Part II of Article 338). USE 75°C See Part II of Article 338. Heat- and moisture-resistant 14–10 1.14 45 Moisture-resistant nonmetallic covering (See 338.2.) (167°F)4 8–2 1.52 60 1–4/0 2.03 80 213–500 2.41 95 6 501–1000 2.79 110 1001–2000 3.18 125 USE-2 90°C Dry and wet locations (194°F) Thermoset XHH 90°C Dry and damp locations Flame-retardant thermoset 14–10 0.76 30 None (194°F) 8–2 1.14 45 1–4/0 1.40 55 213–500 1.65 65 501–1000 2.03 80 1001–2000 2.41 95 Thermoset XHHN 90°C Dry and damp locations Flame-retardant thermoset 14–12 0.38 15 Nylon jacket or equivalent (194°F) 10 0.51 20 8–6 0.76 30 4–2 1.02 40 1–4/0 1.27 50 250–500 1.52 60 501–1000 1.78 70 Moisture-resistant thermoset XHHW 90°C Dry and damp locations Flame-retardant, moisture-resistant thermoset 14–10 0.76 30 None (194°F) 8–2 1.14 45 75°C Wet locations 1–4/0 1.40 55 (167°F) 213–500 1.65 65 501–1000 2.03 80 1001–2000 2.41 95 Moisture-resistant thermoset XHHW-2 90°C Dry and wet locations Flame-retardant, moisture-resistant thermoset 14–10 0.76 30 None (194°F) 8–2 1.14 45 1–4/0 1.40 55 213–500 1.65 65 501–1000 2.03 80 1001–2000 2.41 95 Moisture-resistant thermoset XHWN 75°C Dry and wet locations Flame-retardant, moisture-resistant thermoset 14–12 0.38 15 Nylon jacket or equivalent (167°F) 10 0.51 20 8–6 0.76 30 XHWN-2 90°C 4–2 1.02 40 (194°F) 1–4/0 1.27 50 250–500 1.52 60 501–1000 1.78 70 Modified ethylene tetrafluoro-ethylene Z 90°C Dry and damp locations Modified ethylene tetrafluoro-ethylene 14–12 0.38 15 None (194°F) 10 0.51 20 150°C Dry locations — special applications2 8–4 0.64 25 (302°F) 3–1 0.89 35 1/0–4/0 1.14 45 Modified ethylene tetrafluoro-ethylene ZW 75°C Wet locations Modified ethylene tetrafluoro-ethylene 14–10 0.76 30 None (167°F) 8–2 1.14 45 90°C Dry and damp locations (194°F) 150°C Dry locations — special applications2 (302°F) ZW-2 90°C Dry and wet locations (194°F) Note: Conductors in Table 310.4(1) shall be permitted to be rated up to 1000 volts if listed and marked. 1 Outer coverings shall not be required where listed without a covering. 2 Higher temperature rated constructions shall be permitted where design conditions require maximum conductor operating temperatures above 90°C (194°F). 3 Conductor sizes shall be permitted for signaling circuits permitting 300-volt insulation. 4 The ampacity of Type UF cable shall be limited in accordance with 340.80. 5 Type UF insulation thickness shall include the integral jacket. 6 Insulation thickness shall be permitted to be 2.03 mm (80 mils) for listed Type USE conductors that have been subjected to special investigations. The nonmetallic covering over individual rubber-covered conductors of aluminum-sheathed cable and of lead-sheathed or multiconductor cable shall not be required to be flame retardant. Table 310.4(2) Thickness of Insulation for Nonshielded Types RHH and RHW Solid Dielectric Insulated Conductors Rated 2000 Volts Conductor Size (AWG or kcmil) Column A1 Column B2 mm mils mm mils 14–10 2.03 80 1.52 60 8 2.03 80 1.78 70 6–2 2.41 95 1.78 70 1–2/0 2.79 110 2.29 90 3/0–4/0 2.79 110 2.29 90 213–500 3.18 125 2.67 105 501–1000 3.56 140 3.05 120 1001–2000 3.56 140 3.56 140 1Column A insulations shall be limited to natural, SBR, and butyl rubbers. 2Column B insulations shall be materials such as cross-linked polyethylene, ethylene propylene rubber, and composites thereof. ENHANCED CONTENT Collapse Table 310.4(1) includes conductor applications and maximum operating temperatures for insulations rated 600 volts. Some conductors with dual ratings are listed for dry, damp, and wet locations. Type XHHW is rated 90°C for dry and damp locations and 75°C for wet locations; Type THW is rated 75°C for dry and wet locations and 90°C for special applications within electric-discharge lighting equipment. Types RHW-2, XHHW-2, and other types identified by the suffix “2†are rated 90°C for dry and wet locations. Additional detailed wire classification information for sizes 14 AWG through 2000 kcmil is available in standards and directories such as those published by Underwriters Laboratories Inc. 310.6 Conductor Identification. (A) Grounded Conductors. Insulated or covered grounded conductors shall be identified in accordance with 200.6. Equipment Grounding Conductors. Equipment grounding conductors shall be identified in accordance with 250.119. Ungrounded Conductors. Conductors that are intended for use as ungrounded conductors, whether used as a single conductor or in multiconductor cables, shall be finished to be clearly distinguishable from grounded conductors and equipment grounding conductors. Distinguishing markings shall not conflict in any manner with the surface markings required by 310.8(B)(1). Branch-circuit ungrounded conductors shall be identified in accordance with 210.5(C). Feeders shall be identified in accordance with 215.12(C) Exception: Conductor identification shall be permitted in accordance with 200.7. ENHANCED CONTENT Collapse Ungrounded conductors with white or gray insulation are permitted if the conductors are permanently reidentified at termination points and are visible and accessible. Common methods of reidentification include colored tape, tagging, or paint. Other applications where white conductors are permitted include flexible cords and circuits less than 50 volts. A white conductor used in single-pole, 3-way and 4-way switch loops also requires reidentification (a color other than white, gray, or green) if it is used as an ungrounded conductor. See 200.7(C)(2) for more information about reidentification of grounded conductors. 310.8 Marking. (A) Required Information. All conductors and cables shall be marked to indicate the following information, using the applicable method described in 310.8(B): (1) The maximum rated voltage. The proper type letter or letters for the type of wire or cable as specified elsewhere in this Code. The manufacturer’s name, trademark, or other distinctive marking by which the organization responsible for the product can be readily identified. The AWG size or circular mil area. Informational Note: See Chapter 9, Table 8, Conductor Properties, for conductor area expressed in SI units for conductor sizes specified in AWG or circular mil area. Cable assemblies where the neutral conductor is smaller than the ungrounded conductors shall be so marked. Method of Marking. Surface Marking. The following conductors and cables shall be durably marked on the surface: Single-conductor and multiconductor thermoset and thermoplastic-insulated wire and cable Nonmetallic-sheathed cable Service-entrance cable Underground feeder and branch-circuit cable Tray cable Irrigation cable Power-limited tray cable Instrumentation tray cable The AWG size or circular mil area shall be repeated at intervals not exceeding 610 mm (24 in.). All other markings shall be repeated at intervals not exceeding 1.0 m (40 in.). Marker Tape. Metal-covered multiconductor cables shall employ a marker tape located within the cable and running for its complete length. Exception No. 1: Type MI cable shall not require a marker tape. Exception No. 2: Type AC cable shall not require a marker tape. Exception No. 3: The information required in 310.8(A) shall be permitted to be durably marked on the outer nonmetallic covering of Type MC, Type ITC, or Type PLTC cables at intervals not exceeding 1.0 m (40 in.). Exception No. 4: The information required in 310.8(A) shall be permitted to be durably marked on a nonmetallic covering under the metallic sheath of Type ITC or Type PLTC cable at intervals not exceeding 1.0 m (40 in.). Informational Note: Included in the group of metal-covered cables are Type AC cable, Type MC cable, and lead-sheathed cable. (3) Tag Marking. The following conductors and cables shall be marked by means of a printed tag attached to the coil, reel, or carton: (1) Type MI cable Switchboard wires Metal-covered, single-conductor cables Type AC cable Optional Marking of Wire Size. The information required in 310.8(A)(4) shall be permitted to be marked on the surface of the individual insulated conductors for the following multiconductor cables: Type MC cable Tray cable Irrigation cable Power-limited tray cable Power-limited fire alarm cable Instrumentation tray cable Suffixes to Designate Number of Conductors. A type letter or letters used alone shall indicate a single insulated conductor. The letter suffixes shall be indicated as follows: D — For two insulated conductors laid parallel within an outer nonmetallic covering M — For an assembly of two or more insulated conductors twisted spirally within an outer nonmetallic covering Optional Markings. All conductors and cables contained in Chapter 3 shall be permitted to be surface marked to indicate special characteristics of the cable materials. These markings include, but are not limited to, markings for limited smoke, sunlight resistant, and so forth. ENHANCED CONTENT Collapse Cable insulations that have special characteristics are permitted to carry surface markings that indicate their characteristics. For example, limited-smoke cables are permitted to be marked “LS†or “ST1.†Other characteristics permitted to be marked include sunlight resistance and low corrosiveness. For a detailed list of optional wire and cable marking, see the UL Wire Marking Guide. Part III. Installation 310.10 Uses Permitted. The conductors described in 310.4 shall be permitted for use in any of the wiring methods covered in Chapter 3 and as specified in their respective tables or as permitted elsewhere in this Code. Dry Locations. Insulated conductors and cables used in dry locations shall be any of the types identified in this Code. Dry and Damp Locations. Insulated conductors and cables used in dry and damp locations shall be Types FEP, FEPB, MTW, PFA, RHH, RHW, RHW-2, SA, THHN, THW, THW-2, THHW, THWN, THWN-2, TW, XHH, XHHW, XHHW-2, XHHN, XHWN, XHWN-2, Z, or ZW. Wet Locations. Insulated conductors and cables used in wet locations shall comply with one of the following: Be moisture-impervious metal-sheathed Be types MTW, RHW, RHW-2, TW, THW, THW-2, THHW, THWN, THWN-2, XHHW, XHHW-2, XHWN, XHWN-2 or ZW Be of a type listed for use in wet locations Locations Exposed to Direct Sunlight. Insulated conductors or cables used where exposed to direct rays of the sun shall comply with one of the following: Conductors and cables shall be listed as being sunlight resistant. Conductors and cables shall be covered with insulating material, such as tape or sleeving, that is listed as being sunlight resistant. Direct-Burial Conductors. Conductors used for direct-burial applications shall be of a type identified for such use. Corrosive Conditions. Conductors exposed to oils, greases, vapors, gases, fumes, liquids, or other substances having a deleterious effect on the conductor or insulation shall be of a type suitable for the application. ENHANCED CONTENT Collapse Nylon-jacketed conductors, such as Type THWN, are suitable for use where exposed to gasoline. The UL Guide Information for Electrical Equipment states in the category for Thermoplastic- Insulated Wire (ZLGR) in part: THWN — wire that is suitable for exposure to mineral oil, and to liquid gasoline and gasoline vapors at ordinary ambient temperature, is marked “Gasoline and Oil Resistant I†if suitable for exposure to mineral oil at 60°C, or “Gasoline and Oil Resistant II†if the compound is suitable for exposure to mineral oil at 75°C. Gasoline-resistant wire has been tested at 23°C when immersed in gasoline and is considered inherently resistant to gasoline vapors within the limits of the temperature rating of the wire type. Before a wire-pulling compound is used, it should first be investigated to determine compliance with 310.10(F). Conductors in Parallel. General. Aluminum, copper-clad aluminum, or copper circuit conductors for each ungrounded conductor, grounded conductor, or neutral conductor shall be permitted to be connected in parallel (electrically joined at both ends) only in sizes 1/0 AWG and larger and shall be installed in accordance with 310.10(G)(2) through (G)â (4). Exception No. 1: Conductors in sizes smaller than 1/0 AWG shall be permitted to be run in parallel to supply control power to indicating instruments, contactors, relays, solenoids, and similar control devices, or for frequencies of 360 Hz and higher, provided all of the following apply: (1) They are contained within the same raceway or cable. (2) The ampacity of each individual conductor is sufficient to carry the entire load current shared by the parallel conductors. (3) The overcurrent protection is such that the ampacity of each individual conductor will not be exceeded if one or more of the parallel conductors become inadvertently disconnected. Exception No. 2: Under engineering supervision, 2 AWG and 1 AWG grounded neutral conductors shall be permitted to be installed in parallel for existing installations. Informational Note: Exception No. 2 can be used to alleviate overheating of neutral conductors in existing installations due to high content of triplen harmonic currents. ENHANCED CONTENT Collapse Conductors connected in parallel are treated by the NEC as a single conductor with a total cross-sectional area of all conductors in parallel. The use of parallel conductors is a practical and cost-effective means of installing large-capacity feeders or services. Using conductors larger than 1000 kcmil in raceways is neither economical nor practical unless the conductor size is governed by voltage drop. The ampacity of larger sizes of conductors would increase very little in proportion to the increase in