Document Details
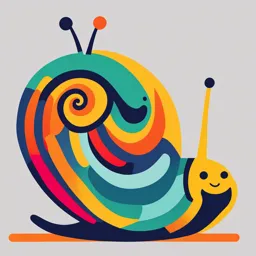
Uploaded by PatriIllumination
Full Transcript
l-mounted control devices or (2) located at a customary wall switch location and equipped with a manual override that will allow the sensor to function as a wall switch. ENHANCED CONTENT Collapse Lighting outlets are permitted to be controlled by wall switches and other wall- mounted control devices...
l-mounted control devices or (2) located at a customary wall switch location and equipped with a manual override that will allow the sensor to function as a wall switch. ENHANCED CONTENT Collapse Lighting outlets are permitted to be controlled by wall switches and other wall- mounted control devices, including occupancy sensors. A controlled receptacle outlet is not permitted to serve as the required lighting outlet in kitchens, laundry areas, or bathrooms. A switched receptacle is not considered one of the receptacle outlets required by 210.52. Occupancy sensors are permitted to be used for switching lighting outlets in habitable rooms, kitchens, and bathrooms, provided they are equipped with a manual override or are used in addition to regular switches. (2) Additional Locations. Additional lighting outlets shall be installed in accordance with the following: * (1) At least one lighting outlet controlled by a listed wall-mounted control device shall be installed in hallways, stairways, attached garages, detached garages, and accessory buildings with electric power. * (2) For dwelling units, attached garages, and detached garages with electric power, at least one exterior lighting outlet controlled by a listed wall- mounted control device shall be installed to provide illumination on the exterior side of outdoor entrances or exits with grade-level access. A vehicle door in a garage shall not be considered as an outdoor entrance or exit. Exception to (2): For an outdoor, grade-level bulkhead door with stairway access to a sub- grade-level basement, the required lighting outlet that provides illumination on the stairway steps shall be permitted to be located in the basement interior within 1.5 m (5 ft) horizontally of the bottommost stairway riser. This interior lighting outlet shall be permitted to be controlled by a listed wall-mounted control device or by a unit switch of the interior luminaire or interior lampholder. * (3) Where lighting outlets are installed for an interior stairway with six or more risers between floor levels, there shall be a listed wall-mounted control device at each floor level and at each landing level that includes a stairway entry to control the lighting outlets. Exception to (1), (2), and (3): Remote, central, or automatic control of lighting shall be permitted in hallways, in stairways, and at outdoor entrances. * (4) Dimmer control of lighting outlets installed in accordance with 210.70(A)(2)(3) shall not be permitted unless the listed control devices can provide dimming control to maximum brightness at each control location for the interior stairway illumination. (B) Guest Rooms or Guest Suites. In hotels, motels, or similar occupancies, guest rooms or guest suites shall have at least one lighting outlet controlled by a listed wall-mounted control device installed in every habitable room and bathroom. Exception No. 1: In other than bathrooms and kitchens where provided, one or more receptacles controlled by a listed wall-mounted control device shall be permitted in lieu of lighting outlets. Exception No. 2: Lighting outlets shall be permitted to be controlled by occupancy sensors that are (1) in addition to listed wall-mounted control devices or (2) located at a customary wall switch location and equipped with a manual override that allows the sensor to function as a wall switch. ENHANCED CONTENT Collapse A lighting outlet is required in every habitable room (the hotel room or rooms in a suite) and in bathrooms. The lighting outlet must be operated through a wall-mounted control device. Kitchens are required to have at least one lighting outlet controlled by a wall-mounted control device. Rooms other than bathrooms and kitchens can have switched receptacles to meet this lighting requirement. Exception No. 2 permits the use of occupancy sensors to control the lighting outlet, provided it is in the typical switch location and can be manually controlled. (C) All Occupancies. For attics and underfloor spaces, utility rooms, and basements, at least one lighting outlet containing a switch or controlled by a wall switch or listed wall- mounted control device shall be installed where these spaces are used for storage or contain equipment requiring servicing. A point of control shall be at each entry that permits access to the attic and underfloor space, utility room, or basement. Where a lighting outlet is installed for equipment requiring service, the lighting outlet shall be installed at or near the equipment. Article 215 Feeders 215.1 Scope. This article covers the installation requirements, overcurrent protection requirements, minimum size, and ampacity of conductors for feeders not over 1000 volts ac or 1500 volts dc, nominal. Informational Note: See Part III of Article 235 for feeders over 1000 volts ac or 1500 volts dc. 215.2 Minimum Rating and Size. (A) General. Feeder conductors shall have an ampacity not less than the larger of 215.2(A)(1) or (A)(2) and shall comply with 110.14(C). (1) Continuous and Noncontinuous Loads. Where a feeder supplies continuous loads or any combination of continuous and noncontinuous loads, the minimum feeder conductor size shall have an ampacity not less than the noncontinuous load plus 125 percent of the continuous load. Exception No. 1: If the assembly, including the overcurrent devices protecting the feeder(s), is listed for operation at 100 percent of its rating, the ampacity of the feeder conductors shall be permitted to be not less than the sum of the continuous load plus the noncontinuous load. Exception No. 2: Where a portion of a feeder is connected at both its supply and load ends to separately installed pressure connections as covered in 110.14(C)(2), it shall be permitted to have an ampacity not less than the sum of the continuous load plus the noncontinuous load. No portion of a feeder installed under this exception shall extend into an enclosure containing either the feeder supply or the feeder load terminations, as covered in 110.14(C)(1). Exception No. 3: Grounded conductors that are not connected to an overcurrent device shall be permitted to be sized at 100 percent of the continuous and noncontinuous load. ENHANCED CONTENT Collapse Exception No. 2. This exception addresses installations where feeders are installed in multiple segments. Feeders installed under this scenario comprise three segments: two segments at the terminations - supply and load - and an intervening segment. The allowable ampacity of the intervening segment is permitted to be calculated without applying 125 percent to the continuous load. The two segments at the terminations of the feeder are sized to accommodate the effects of continuous loading on the termination devices. Their ampacities are selected and coordinated to not exceed the lowest temperature rating of any connected termination, conductor, or device, as covered in 110.14(C)(1). The intervening segment must terminate in enclosures at the feeder source and destination. This segment is sized in accordance with the ampacity requirements for the conductor specifically to provide wiring that will accommodate the maximum current, whether or not any portion of that current is continuous. The ampacity of this intervening segment is limited only by the ampacity parameters that apply over the length of the intervening segment and the ampacity at the listed and identified temperature rating of the pressure connector, as covered in 110.14(C)(2). The following exhibit shows a 400-ampere load supplied by a feeder comprising three segments. The segments at the overcurrent device and load terminate on terminals rated at 75øC and connect to the intervening load with pressure connectors rated at 90øC. A 600-kcmil, Cu THHN, Type MC cable is used at the supply and load ends. A 500-kcmil, Cu THHN, Type MC cable is used for the intervening segment. Exception No. 3. Feeder grounded/neutral conductors that do not connect to the terminals of an overcurrent protective device are not required to be sized based on 125 percent of the continuous load. For example, if the maximum unbalanced load on a feeder neutral is calculated per 220.61 to be 200 amperes and the load is considered to be continuous, the use of a 3/0 AWG, Type THW copper conductor is permitted as long as the conductor terminates at a neutral bus or terminal bar within the electrical distribution equipment. (2) Ampacity Adjustment or Correction Factors. The minimum feeder conductor size shall have an ampacity not less than the maximum load to be served after the application of any adjustment or correction factors in accordance with 310.14. Informational Note No. 1: See Informative Annex D for Examples D1 through D11. Informational Note No. 2: Conductors for feeders, as defined in Article 100, sized to prevent a voltage drop exceeding 3 percent at the farthest outlet of power, heating, and lighting loads, or combinations of such loads, and where the maximum total voltage drop on both feeders and branch circuits to the farthest outlet does not exceed 5 percent, will provide reasonable efficiency of operation. Informational Note No. 3: See 210.19, Informational Note for voltage drop for branch circuits. ENHANCED CONTENT Collapse Informational notes are not mandatory, as outlined in 90.5(C). Where circuit conductors are increased due to voltage drop, 250.122(B) requires an increase in circular mil area for the associated equipment grounding conductors. The resistance or impedance of conductors can cause a substantial difference between voltage at service equipment and voltage at the point-of- utilization equipment. Excessive voltage drop impairs the starting and the operation of electrical equipment. Undervoltage can result in inefficient operation of heating, lighting, and motor loads. An applied voltage of 10 percent below rating can result in a decrease in efficiency of substantially more than 10 percent - for example, fluorescent light output would be reduced by 15 percent, and incandescent light output would be reduced by 30 percent. Induction motors would run hotter and produce less torque. With an applied voltage of 10 percent below rating, the running current would increase 11 percent, and the operating temperature would increase 12 percent. At the same time, torque would be reduced 19 percent. In addition to resistance or impedance, the type of raceway or cable enclosure, the type of circuit [alternating current (ac), direct current (dc), single-phase, 3-phase], and the power factor should be considered to determine voltage drop. This basic formula can be used to determine the voltage drop in a 2-wire dc circuit, a 2-wire ac circuit, or a 3-wire ac single-phase circuit, all with a balanced load at 100 percent power factor and where reactance can be neglected: where: VD = voltage drop (based on conductor temperature of 75øC) L = one-way length of circuit (ft) R = conductor resistance in ohms (ê) per 1000 ft (from Chapter 9, Table 8) I = load current (amperes) For 3-phase circuits (at 100 percent power factor), the voltage drop between any two phase conductors is 0.866 times the voltage drop calculated by the formula. Voltage-drop tables and calculations are available from various manufacturers. See also Table 9 of Chapter 9 and its enhanced content for an example of voltage-drop calculation using ac reactance and resistance. (B) Grounded Conductor. The size of the feeder circuit grounded conductor shall not be smaller than the equipment grounding conductor size required by 250.122, except that 250.122(F) shall not apply where grounded conductors are run in parallel. Additional minimum sizes shall be as specified in 215.2(C) under the conditions stipulated. ENHANCED CONTENT Collapse Using 250.122 to establish the minimum size grounded conductor in a feeder circuit provides a relationship between the grounded conductor and the feeder circuit overcurrent protective device that is the same as that used for sizing equipment grounding conductors. It provides an adequate fault current path in the event of a fault between a phase conductor and the grounded conductor. See also 235.202 for sizing requirements of the grounded feeder conductor for feeder circuits over 1000 volts ac or 1500 volts dc, nominal. See 220.61 and 310.10(G) for determining the minimum grounded conductor size for feeder circuits installed in parallel in separate raceways or cables. (C) Ampacity Relative to Service Conductors. The feeder conductor ampacity shall not be less than that of the service conductors where the feeder conductors carry the total load supplied by service conductors with an ampacity of 55 amperes or less. ENHANCED CONTENT Collapse According to Table 310.16, a 3/0 AWG, Type THW copper conductor has an ampacity of 200 amperes. However, for a 3-wire, single-phase dwelling unit service, as shown in the exhibit below, 310.12 permits a service conductor (or a main power feeder conductor) with an ampacity of 83 percent of the service rating. This permits a minimum of 2/0 AWG, Type THW copper conductors or 4/0 AWG, Type THW aluminum conductors for services or a main power feeder rated at 200 amperes. 215.3 Overcurrent Protection. Feeders shall be protected against overcurrent in accordance with Part I of Article 240. Where a feeder supplies continuous loads or any combination of continuous and noncontinuous loads, the rating of the overcurrent device shall not be less than the noncontinuous load plus 125 percent of the continuous load. Exception: Where the assembly, including the overcurrent devices protecting the feeder(s), is listed for operation at 100 percent of its rating, the ampere rating of the overcurrent device shall be permitted to be not less than the sum of the continuous load plus the noncontinuous load. 215.4 Feeders with Common Neutral Conductor. (A) Feeders with Common Neutral. Up to three sets of 3-wire feeders or two sets of 4-wire or 5-wire feeders shall be permitted to utilize a common neutral. (B) In Metal Raceway or Enclosure. Where installed in a metal raceway or other metal enclosure, all conductors of all feeders using a common neutral conductor shall be enclosed within the same raceway or other enclosure as required in 300.20. ENHANCED CONTENT Collapse If ac feeder conductors, including the neutral conductor, are installed in metal raceways, the conductors are required to be grouped together to avoid induction heating of the surrounding metal. If it is necessary to run parallel conductors through multiple metal raceways, conductors from each phase plus the neutral must be run in each raceway. For requirements associated with conductor grouping of feeder circuits, see 250.102(E), 250.134, 300.3, 300.5(I), and 300.20. A 3-phase, 4-wire (208Y/120 or 480Y/277) system is often used to supply both lighting and motor loads. The 3-phase motor loads typically are not connected to the neutral and, thus, will not cause current in the neutral conductor. The maximum current on the neutral is due to lighting loads or circuits where the neutral is used. On this type of system (3-phase, 4-wire), a demand factor of 70 percent is permitted by 220.61(B) for that portion of the neutral load in excess of 200 amperes. For example, if the maximum possible unbalanced load is 500 amperes, the neutral would have to be large enough to carry 410 amperes (200 amperes plus 70 percent of 300 amperes, or 410 amperes). No reduction of the neutral capacity for that portion of the load consisting of electric-discharge lighting is permitted. Section 310.15(E) points out that a neutral conductor must be counted as a current-carrying conductor if the load it serves consists of harmonic currents. The maximum unbalanced load for feeders supplying clothes dryers, household ranges, wall-mounted ovens, and counter-mounted cooking units is required to be considered 70 percent of the load on the ungrounded conductors. For other systems in which the 70-percent demand factor can be applied, see 220.61(B). 215.5 Diagrams of Feeders. If required by the authority having jurisdiction, a diagram showing feeder details shall be provided prior to the installation of the feeders. Such a diagram shall show the area in square feet of the building or other structure supplied by each feeder, the total calculated load before applying demand factors, the demand factors used, the calculated load after applying demand factors, and the size and type of conductors to be used. 215.6 Feeder Equipment Grounding Conductor. Where a feeder supplies branch circuits in which equipment grounding conductors are required, the feeder shall include or provide an equipment grounding conductor, to which the equipment grounding conductors of the branch circuits shall be connected. Where the feeder supplies a separate building or structure, the requirements of 250.32 shall apply. 215.7 Ungrounded Conductors Tapped from Grounded Systems. Two-wire dc circuits and ac circuits of two or more ungrounded conductors shall be permitted to be tapped from the ungrounded conductors of circuits having a grounded neutral conductor. Switching devices in each tapped circuit shall have a pole in each ungrounded conductor. 215.9 Ground-Fault Circuit-Interrupter Protection for Personnel. Feeders shall be permitted to be protected by a listed ground-fault circuit interrupter installed in a readily accessible location in lieu of the provisions for such interrupters as specified in 210.8 and 590.6(A). ENHANCED CONTENT Collapse Ground-fault circuit-interrupter (GFCI) protection of the feeder circuit protects all branch circuits supplied by that feeder. This type of GFCI installation is permitted in lieu of the branch-circuit GFCI requirements of 210.8. GFCI protection in the feeder can also be used to protect construction site receptacles, as covered in 590.6(A), provided the feeder supplies no lighting branch circuits. Although it may be more economical or convenient to install GFCIs for feeders, consideration should be given to the possibility that a GFCI might be monitoring several branch circuits and will de-energize all branch circuits in response to a line-to-ground fault from one branch circuit. 215.10 Ground-Fault Protection of Equipment. Each feeder disconnect rated 1000 amperes or more and installed on solidly grounded wye electrical systems of more than 150 volts to ground, but not exceeding 1000 volts phase-to-phase, shall be provided with ground-fault protection of equipment in accordance with 230.95. Informational Note: See 517.17 for buildings that contain health care occupancies. Exception No. 1: This section shall not apply to a disconnecting means for a continuous industrial process where a nonorderly shutdown will introduce additional or increased hazards. Exception No. 2: This section shall not apply if ground-fault protection of equipment is provided on the supply side of the feeder and on the load side of any transformer supplying the feeder. Exception No. 3: If temporary feeder conductors are used to connect a generator to a facility for repair, maintenance, or emergencies, ground-fault protection of equipment shall not be required. Temporary feeders without ground-fault protection shall be permitted for the time period necessary but shall not exceed 90 days. ENHANCED CONTENT Collapse Exception No. 1. Prior to this requirement, an unusually high number of burndowns on feeders and services operating in this voltage range were reported. Solidly grounded systems operating at 480Y/277 volts were the primary focus of this requirement when it was first introduced in the NEC, but other solidly grounded, wye-connected systems operating over 150 volts to ground and not more than 600 volts phase-to-phase are covered by this requirement. Each ground-fault protection system must be performance tested and documented according to the requirements of 230.95(C) before being put into service. Ground-fault protection of feeder equipment is not required if protection is provided on an upstream feeder or at the service. However, additional levels of ground-fault protection for feeders might be preferred so that a single ground fault does not deenergize the whole electrical system. See also 230.95 and its enhanced content for more on ground-fault protection of services. See 517.17, which requires an additional level of ground-fault protection for health care facilities. For the different ground-fault protection requirements for emergency feeders covered within the scope of Article 700, see 700.31. Exception No. 2. Ground-fault protection installed in equipment supplying the primary of a transformer will not function to protect equipment supplied by the secondary of the transformer. If the equipment supplied by the secondary of the transformer meets the parameters under which ground-fault protection of equipment (GFPE) is required by 215.10, protection must be installed to protect the equipment supplied by the secondary of the transformer. 215.11 Circuits Derived from Autotransformers. Feeders shall not be derived from autotransformers unless the system supplied has a grounded conductor that is electrically connected to a grounded conductor of the system supplying the autotransformer. Exception No. 1: An autotransformer shall be permitted without the connection to a grounded conductor where transforming from a nominal 208 volts to a nominal 240-volt supply or similarly from 240 volts to 208 volts. Exception No. 2: In industrial occupancies, where conditions of maintenance and supervision ensure that only qualified persons service the installation, autotransformers shall be permitted to supply nominal 600-volt loads from nominal 480-volt systems, and 480-volt loads from nominal 600-volt systems, without the connection to a similar grounded conductor. 215.12 Identification for Feeders. (A) Grounded Conductor. The grounded conductor of a feeder, if insulated, shall be identified in accordance with 200.6. (B) Equipment Grounding Conductor. The equipment grounding conductor shall be identified in accordance with 250.119. (C) Identification of Ungrounded Conductors. Ungrounded conductors shall be identified in accordance with 215.12(C)(1) or (C)(2), as applicable. ENHANCED CONTENT Collapse Parallel with the requirement for ungrounded branch-circuit conductors in 210.5(C), 215.12(C) requires identification of ungrounded feeder conductors by system and phase where there is more than one nominal voltage supply system to a building, structure, or other premises. For ac circuits, the identification scheme is not specified, but whatever is used is required to be consistent throughout the premises. A permanent legend or directory indicating the feeder identification system for the premises is required to be posted at each point in the distribution system from which feeder circuits are supplied, or the identification scheme is to be described in a facility log or other documentation and made readily available. Below is an example of the use of different colors to identify each ungrounded line or phase of a nominal voltage system. (Courtesy of AFC Cable Systems, a Part of Atkore International) (1) Feeders Supplied from More Than One Nominal Voltage System. Where the premises wiring system has feeders supplied from more than one nominal voltage system, each ungrounded conductor of a feeder shall be identified by phase or line and system at all termination, connection, and splice points in compliance with 215.12(C)(1)(a) and (C)(1)(b). * (a) Means of Identification. The means of identification shall be permitted to be by separate color coding, marking tape, tagging, or other approved means. * (b) Posting of Identification Means. The method utilized for conductors originating within each feeder panelboard or similar feeder distribution equipment shall be documented in a manner that is readily available or shall be permanently posted at each feeder panelboard or similar feeder distribution equipment. (2) Feeders Supplied from Direct-Current Systems. Where a feeder is supplied from a dc system operating at more than 60 volts, each ungrounded conductor of 4 AWG or larger shall be identified by polarity at all termination, connection, and splice points by marking tape, ta