Document Details
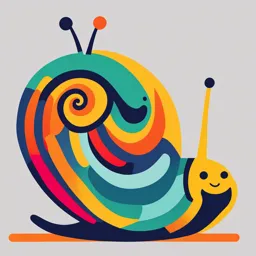
Uploaded by PatriIllumination
Full Transcript
tings should not be confused with short-circuit current ratings. 110.10 Circuit Impedance, Short-Circuit Current Ratings, and Other Characteristics. The overcurrent protective devices, the total impedance, the equipment short-circuit current ratings, and other characteristics of the circuit to be pr...
tings should not be confused with short-circuit current ratings. 110.10 Circuit Impedance, Short-Circuit Current Ratings, and Other Characteristics. The overcurrent protective devices, the total impedance, the equipment short-circuit current ratings, and other characteristics of the circuit to be protected shall be selected and coordinated to permit the circuit protective devices used to clear a fault to do so without extensive damage to the electrical equipment of the circuit. This fault shall be assumed to be either between two or more of the circuit conductors or between any circuit conductor and the equipment grounding conductor(s) permitted in 250.118. Listed equipment applied in accordance with their listing shall be considered to meet the requirements of this section. ENHANCED CONTENT Collapse Short-circuit current ratings are marked on equipment such as panelboards, switchboards, switchgear, busways, contactors, and starters. Listed products are subjected to rigorous testing as part of their evaluation, which includes tests under fault conditions. Therefore, listed products used within their ratings are considered to have met the requirements of 110.10. The purpose of overcurrent protection is to open the circuit before conductors or conductor insulation is damaged when an overcurrent condition occurs. An overcurrent condition can be the result of an overload, a ground fault, or a short circuit. OCPDs (such as fuses and circuit breakers) should be selected to ensure that the short-circuit current rating of the system components is not exceeded if a short circuit or high-level ground fault occurs. Wire, bus structures, switching, protection and disconnect devices, and distribution equipment all have limited short-circuit ratings and would be damaged or destroyed if those short-circuit ratings were exceeded. Merely providing OCPDs with sufficient interrupting ratings would not ensure adequate short-circuit protection for the system components. When the available short-circuit current exceeds the short-circuit current rating of an electrical component, the OCPD must limit the let-through energy to within the rating of that electrical component. Utility companies often determine and provide information on available short-circuit current levels to the service equipment. Application Example The short-circuit current rating of utilization equipment located and connected near the service equipment should be known because the available short-circuit currents near the service equipment are higher than elsewhere in the system. For example, HVAC equipment is tested at 3500 amperes through a 40-ampere load rating and at 5000 amperes for loads rated more than 40 amperes. For a typical one-family dwelling with a 100-ampere service using 2 AWG aluminum supplied by a 371/2 kilovolt-ampere transformer with 1.72 percent impedance located at a distance of 25 feet, the available short-circuit current would be approximately 6000 amperes. Where pad-mounted transformers are located close to a multimetering location of a multifamily building, available short-circuit current can be relatively high. For example, the line-to-line fault current values close to a low-impedance transformer could exceed 22,000 amperes. At the secondary of a single-phase, center-tapped transformer, the line-toneutral fault current is approximately one and one-half times that of the line-to- line fault current. 110.11 Deteriorating Agents. Unless identified for use in the operating environment, no conductors or equipment shall be located in damp or wet locations; where exposed to gases, fumes, vapors, liquids, or other agents that have a deteriorating effect on the conductors or equipment; or where exposed to excessive temperatures. Informational Note No. 1: See 300.6 for protection against corrosion. Informational Note No. 2: Some cleaning and lubricating compounds can cause severe deterioration of many plastic materials used for insulating and structural applications in equipment. Equipment not identified for outdoor use and equipment identified only for indoor use, such as “dry locations,” “indoor use only,” “damp locations,” or enclosure Types 1, 2, 5, 12, 12K, and/or 13, shall be protected against damage from the weather during construction. Informational Note No. 3: See Table 110.28 for appropriate enclosure-type designations. Informational Note No. 4: See NFPA 5000 -2015, Building Construction and Safety Code, the International Building Code (IBC), and the International Residential Code for One- and Two-Family Dwellings (IRC), for information for minimum flood provisions. ENHANCED CONTENT Collapse The flood-related requirements contained in Chapter 39 and elsewhere in NFPA 5000, Building Construction and Safety Code, provide methods to reduce flood damage to buildings and attendant systems. Chapter 32 of NFPA 70B, Recommended Practice for Electrical Equipment Maintenance, provides guidance to facilities, institutions, and businesses in the event of a disaster to help limit the recovery time, therefore getting them up and running sooner. The requirements in NFPA 5000 are based on years of collective experience and are consistent with the minimum requirements of the National Flood Insurance Program (NFIP). Fortunately, flood hazard information - which is necessary to implement the flood-related requirements - is readily available for most communities. While flood hazards have been mapped by a federal agency on a nationwide basis, floodplain management regulations are adopted and decisions are made at the local level. Communities that choose to participate in the NFIP must adopt local floodplain management regulations, which are no less stringent than minimum NFIP regulations. The flood-related requirements call for a number of actions, including the following: 1. Using available flood hazard information for the siting, design, and construction of buildings 2. Elevating buildings above the design flood elevation (DFE) 3. Designing and constructing structures to withstand anticipated flood loads during the design flood event 4. Using flood damage-resistant materials below the design flood elevation 5. In coastal areas, elevating buildings on a pile or column foundation and keeping areas below the elevated buildings free of obstructions, which could transfer flood loads to or otherwise damage the elevated portions of buildings during a flood Other aspects of flood-resistant design and construction covered in Chapter 39 of NFPA 5000 include determining the lowest floor elevation, designing foundations, selecting materials and systems, bringing existing buildings into compliance, and designing and building manufactured homes and temporary structures. 110.12 Mechanical Execution of Work. Electrical equipment shall be installed in a professional and skillful manner. Informational Note: See ANSI/NECA 1-2015, Standard for Good Workmanship in Electrical Construction, and other ANSI-approved installation standards for information on accepted industry practices. ENHANCED CONTENT Collapse The requirement for installations to be done in a “professional and skillful manner” is representative of pride in one’s work and is emphasized by persons involved in the training of apprentice electricians. A professional and skillful installation is also one that is easy to troubleshoot and is unlikely to have problems properly functioning. Installations that do not qualify as “professional and skillful” include exposed runs of cables or raceways that are sagging between supports or supported by improper methods; cables that are kinked, flattened, or incorrectly sized; or cabinets, cutout boxes, and enclosures that are not plumb or not properly secured. (A) Unused Openings. Unused openings, other than those intended for the operation of equipment, those intended for mounting purposes, or those permitted as part of the design for listed equipment, shall be closed to afford protection substantially equivalent to the wall of the equipment. Where metallic plugs or plates are used with nonmetallic enclosures, they shall be recessed at least 6 mm (1/4 in.) from the outer surface of the enclosure. (B) Integrity of Electrical Equipment and Connections. Internal parts of electrical equipment, including busbars, wiring terminals, insulators, and other surfaces, shall not be damaged or contaminated by foreign materials such as paint, plaster, cleaners, abrasives, or corrosive residues. There shall be no damaged parts that may adversely affect safe operation or mechanical strength of the equipment such as parts that are broken; bent; cut; or deteriorated by corrosion, chemical action, or overheating. (C) Cables and Conductors. Cables and conductors installed exposed on the surfaces of ceilings and sidewalls shall be supported by the building structure in such a manner that the cables and conductors will not be damaged by normal building use. Such cables and conductors shall be secured by hardware including straps, staples, cable ties, hangers, or similar fittings designed and installed so as not to damage the cable. The installation shall also conform with 300.4 and 300.11. Nonmetallic cable ties and other nonmetallic cable accessories used to secure and support cables in other spaces used for environmental air (plenums) shall be listed as having low smoke and heat release properties. Informational Note No. 1: See NFPA 90A-2021, Standard for the Installation of Air-Conditioning and Ventilating Systems, 4.3.11.2.6.5 and 4.3.11.5.5.6, for discrete combustible components installed in accordance with 300.22(C). Informational Note No. 2: Paint, plaster, cleaners, abrasives, corrosive residues, or other contaminants may result in an undetermined alteration of optical fiber cable properties. 110.13 Mounting and Cooling of Equipment. (A) Mounting. Electrical equipment shall be firmly secured to the surface on which it is mounted. Wooden plugs driven into holes in masonry, concrete, plaster, or similar materials shall not be used. (B) Cooling. Electrical equipment that depends on the natural circulation of air and convection principles for cooling of exposed surfaces shall be installed so that room airflow over such surfaces is not prevented by walls or by adjacent installed equipment. For equipment designed for floor mounting, clearance between top surfaces and adjacent surfaces shall be provided to dissipate rising warm air. Electrical equipment provided with ventilating openings shall be installed so that walls or other obstructions do not prevent the free circulation of air through the equipment. ENHANCED CONTENT Collapse The term ventilated is defined in Article 100. Ventilating openings in equipment are provided to allow the circulation of room air around internal equipment components. Blocking these openings can cause dangerous overheating. For example, a ventilated busway must be located where there are no walls or other obstructions that could interfere with the natural circulation of air and convection principles for cooling. The surfaces of some enclosures, such as panelboards and transformers, may also require normal room air circulation to prevent overheating. Proper placement of equipment requiring ventilation becomes enforceable using the requirements of 110.3(B). See also 430.14(A) and 430.16 for ventilation requirements for motors, and see 450.9 and 450.45 for ventilation requirements for transformers. 110.14 Electrical Connections. Because of different characteristics of dissimilar metals, devices such as pressure terminal or pressure splicing connectors and soldering lugs shall be identified for the material of the conductor and shall be properly installed and used. Conductors of dissimilar metals shall not be intermixed in a terminal or splicing connector where physical contact occurs between dissimilar conductors unless the device is identified for the purpose and conditions of use. Materials such as solder, fluxes, inhibitors, and compounds, where employed, shall be suitable for the use and shall be of a type that will not adversely affect the conductors, installation, or equipment. Connectors and terminals for conductors more finely stranded than Class B and Class C stranding as shown in Chapter 9, Table 10, shall be identified for the specific conductor class or classes. (A) Terminals. Connection of conductors to terminal parts shall ensure a mechanically secure electrical connection without damaging the conductors and shall be made by means of pressure connectors (including set-screw type), solder lugs, or splices to flexible leads. Connection by means of wire-binding screws or studs and nuts that have upturned lugs or the equivalent shall be permitted for 10 AWG or smaller conductors. Terminals for more than one conductor and terminals used to connect aluminum shall be so identified. (B) Splices. Conductors shall be spliced or joined with splicing devices identified for the use or by brazing, welding, or soldering with a fusible metal or alloy. Soldered splices shall first be spliced or joined so as to be mechanically and electrically secure without solder and then be soldered. All splices and joints and the free ends of conductors shall be covered with an insulation equivalent to that of the conductors or with an identified insulating device. Wire connectors or splicing means installed on conductors for direct burial shall be listed for such use. ENHANCED CONTENT Collapse Electrical connection failures are the cause of many equipment burnouts and fires. Many of these failures are attributable to improper terminations, poor workmanship, the differing characteristics of dissimilar metals, and improper binding screws or splicing devices. UL’s requirements for listing solid aluminum conductors in 12 AWG and 10 AWG and its requirements for listing snap switches and receptacles for use on 15- and 20-ampere branch circuits incorporate stringent tests that are intended to prevent termination failures. Screwless pressure terminal connectors of the conductor push-in type are for use only with solid copper and copper-clad aluminum conductors. See also 404.14(C) and 406.3(C) for further information regarding receptacles and switches using copper-aluminum, revised (CO/ALR) rated terminals. The electrical industry has developed new product and material designs that provide increased levels of safety for aluminum wire terminations. Aluminum Wire Terminations - New Installations The following commentary is based on a report prepared by the Ad Hoc Committee on Aluminum Terminations prior to publication of the 1975 NEC. This information is still pertinent today and is necessary for compliance with 110.14(A) when aluminum wire is used in new installations. New installation of aluminum conductors on 15- and 20- ampere branch circuits is not common, but many of these circuits continue to be in use. New Materials and Devices. For direct connection, only 15- and 20-ampere receptacles and switches marked “CO/ALR” and connected as follows should be used. The “CO/ALR” marking on the device mounting yoke or strap means the devices have been tested to stringent heat-cycling requirements to determine their suitability for use with UL-labeled aluminum, copper, or copper-clad aluminum wire. Listed solid aluminum wire, 12 AWG or 10 AWG, marked with the aluminum insulated wire label should be used. The installation instructions that are packaged with the wire should be followed. Installation Method. The following exhibit illustrates the correct method of connection: The freshly stripped end of the wire is wrapped two-thirds to three-quarters of the distance around the wire-binding screw post as shown in Step A. The loop is made so that rotation of the screw during tightening will tend to wrap the wire around the post rather than unwrap it. The screw is tightened until the wire is snugly in contact with the underside of the screw head and with the contact plate on the wiring device as shown in Step B. The screw is tightened an additional half-turn to provide a firm connection as shown in Step C. The wires should be positioned behind the wiring device to decrease the likelihood of the terminal screws loosening when the device is positioned into the outlet box. The next exhibit shows incorrect methods of connection. These methods should not be used. Existing Inventory. Marked 12 AWG or 10 AWG solid aluminum wire that does not bear the new aluminum wire label should be used with wiring devices marked “CO/ALR” and connected as described under the heading Installation Method. This is the preferred and recommended method for using such wire. For the following types of devices, the terminals should not be directly connected to aluminum conductors but may be used with copper or copper-clad conductors: 1. Receptacles and snap switches marked “AL-CU” 2. Receptacles and snap switches having no conductor material marking Receptacles and snap switches that have back-wired terminals or screwless terminals of the push-in type are for 14 AWG copper conductors only. Aluminum Wire Terminations - Existing Installations If examination discloses overheating or loose connections, the recommendations described under the heading Existing Inventory above should be followed. Splicing Wire Connectors. Splicing wire connectors are required to be marked for the material of the conductor and for their suitability where intermixed. Splicing wire connectors, such as twist-on wire connectors, are not suitable for splicing aluminum conductors or copper-clad aluminum to copper conductors, unless it is so stated and marked as such on the unit container or an information sheet supplied with the unit container. The required marking is “AL-CU (intermixed-dry locations)” where intermixing (direct contact) occurs. Other types of listed splicing wire connectors that are not rated for intermixing between the copper and the aluminum may also be used, as long as the conductors are not in direct physical contact. These connectors are just marked “AL- CU.” UL lists twist-on wire connectors that are suitable for use with aluminum-to-copper conductors, in accordance with UL 486C, Splicing Wire Connectors. The UL listing does not cover aluminum-to-aluminum combinations. However, more than one aluminum or copper conductor is allowed where used in combination. Suitable wire combinations are marked on the unit container or supplied on the information sheet with the unit container. These listed splicing wire-connecting devices are available for pigtailing short lengths of copper conductors directly to the original aluminum branch-circuit conductors as shown in the following exhibit. Also depicted is a similarly rated crimp splicing device that is also suitable for intermixing (direct contact). Primarily, these pigtailed conductors supply 15- and 20- ampere wiring devices. Pigtailing is permitted, provided suitable space is within the enclosure. (C) Temperature Limitations. The temperature rating associated with the ampacity of a conductor shall be selected and coordinated so as not to exceed the lowest temperature rating of any connected termination, conductor, or device. Conductors with temperature ratings higher than specified for terminations shall be permitted to be used for ampacity adjustment, correction, or both. (1) Equipment Provisions. The determination of termination provisions of equipment shall be based on 110.14(C)(1)(a) or (C)(1)(b). Unless the equipment is listed and marked otherwise, conductor ampacities used in determining equipment termination provisions shall be based on Table 310.16 as appropriately modified by 310.12. * (a) Termination provisions of equipment for circuits rated 100 amperes or less, or marked for 14 AWG through 1 AWG conductors, shall be used only for one of the following: o (1) Conductors rated 60øC (140øF). o (2) Conductors with higher temperature ratings, provided the ampacity of such conductors is determined based on the 60øC (140øF) ampacity of the conductor size used. o (3) Conductors with higher temperature ratings if the equipment is listed and identified for use with such conductors. o (4) For motors marked with design letters B, C, or D, conductors having an insulation rating of 75øC (167øF) or higher shall be permitted to be used, provided the ampacity of such conductors does not exceed the 75øC (167øF) ampacity. * (b) Termination provisions of equipment for circuits rated over 100 amperes, or marked for conductors larger than 1 AWG, shall be used only for one of the following: o (1) Conductors rated 75øC (167øF) o (2) Conductors with higher temperature ratings, provided the ampacity of such conductors does not exceed the 75øC (167øF) ampacity of the conductor size used, or up to their ampacity if the equipment is listed and identified for use with such conductors (2) Separate Connector Provisions. Separately installed pressure connectors shall be used with conductors at the ampacities not exceeding the ampacity at the listed and identified temperature rating of the connector. Informational Note: Equipment markings or listing information may additionally restrict the sizing and temperature ratings of connected conductors. ENHANCED CONTENT Collapse When equipment of 1000 volts or less is evaluated, conductors sized according to Table 310.16 are required to be used. The UL Guide Information for Electrical Equipment for Use in Ordinary Locations (AALZ) located on UL’s Product iQ(tm) database (productiq.ul.com) indicates that the 60øC and 75øC termination temperature ratings for equipment have been determined using conductors from Table 310.16 of the NEC. However, installers or designers who are unaware of the UL guide information might attempt to select conductors based on a table other than Table 310.16, especially if a wiring method is used that allows the use of ampacities such as those in Table 310.17, which can result in overheated equipment terminations. The ampacities shown in other tables could be used for various conditions to which the wiring method is subject (such as ambient or ampacity correction conditions), but the conductor size at the equipment termination must be based on ampacities from Table 310.16. Conductor terminations, as well as conductors, must be rated for the operating temperature of the circuit. For example, the load on an 8 AWG THHN, 90øC copper conductor is limited to 40 amperes where connected to a disconnect switch with terminals rated at 60øC. The same conductor is limited to 50 amperes where connected to a fusible switch with terminals rated at 75øC Not only do termination temperature ratings apply to conductor terminations, but the equipment enclosure marking must also permit terminations above 60øC. An example of termination temperature marking is shown below. (Courtesy of Siemens Industry, Inc.) (D) Terminal Connection Torque. Tightening torque values for terminal connections shall be as indicated on equipment or in installation instructions provided by the manufacturer. An approved means shall be used to achieve the indicated torque value. Informational Note No. 1: Examples of approved means of achieving the indicated torque values include torque tools or devices such as shear bolts or breakaway-style devices with visual indicators that demonstrate that the proper torque has been applied. Informational Note No. 2: See UL Standard 486A-486B, Standard for Safety-Wire Connectors, Informative Annex I for torque values in the absence of manufacturer’s recommendations.The equipment manufacturer can be contacted if numeric torque values are not indicated on the equipment or if the installation instructions are not available. Informational Note No. 3: See NFPA 70B-2019, Recommended Practice for Electrical Equipment Maintenance, Section 8.11 for additional information for torquing threaded connections and terminations. ENHANCED CONTENT Collapse Because the reliability and safety of terminations depend on proper connection, the use of an approved means is essential. Approved means include the use of a torque wrench, torque screwdriver, shear bolts, and breakaway devices. For wire connectors for which the manufacturer has not assigned a value appropriate for the design, Informative Anne