Wind Energy Technologies PDF
Document Details
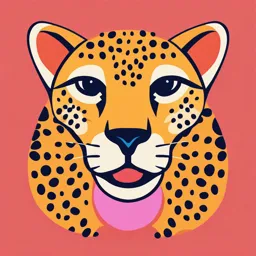
Uploaded by LuxuriousLagoon
Università degli Studi di Padova
D. Del Col
Tags
Summary
This document provides an overview of wind energy technologies, including different types of wind rotors and generators. It also discusses the statistical distribution of wind speeds, which determines the energy production capacity of a wind turbine.
Full Transcript
UNIVERSITẦ DEGLI STUDI DI PADOVA LM Energy engineering Renewable Energy Technologies WIND ENERGY D. Del Col Sources: J. A. Duffie, W. A. Beckman. Solar Engineering of Thermal Processes. J. Wiley and Sons, chapter 24 Wind ener...
UNIVERSITẦ DEGLI STUDI DI PADOVA LM Energy engineering Renewable Energy Technologies WIND ENERGY D. Del Col Sources: J. A. Duffie, W. A. Beckman. Solar Engineering of Thermal Processes. J. Wiley and Sons, chapter 24 Wind energy. https://onlinelibrary.wiley.com/doi/epub/10.1002/9781119540328 Erich Hau, Wind Turbines. Fundamentals, Technologies, Application, Economics, Springer G. L. Johnson, Wind Energy Systems, Electronic Edition The sun irradiates the earth with 1.74 1014 kWh of energy every hour, of which 1.22 1014 kW is absorbed. About 1-2% of the energy from the sun is converted into wind energy, which is about 50-100 times greater than the energy converted into biomass by all the plants on our planet. The principle of operation of wind rotors is the same as for windmills: the wind that pushes the blades. But in the case of wind turbines, the rotational movement of the blades is transmitted to a generator that produces electricity. We talk about aeromotors when the movement of the turbine is directly transmitted to the user as mechanical energy: this is an example of the water lifting pumps still present in the North American plains. A typical 600 kW wind turbine has a rotor with a diameter of 43-44 m, corresponding to a swept area of the rotor of 1500 square meters. Consider a cylindrical "slice" of air, 1 meter thick, that moves passing through the 1500 m2 rotor of a typical 600 kW wind turbine: each cylinder weighs 1.9 tons The kinetic energy of a moving body is proportional to its mass. The kinetic energy of the wind therefore depends on the density of the air p 288,15 B 1, 225 T [K] is absolute temperature, Ra T T 1013,3 B [mbar] is barometric pressure Reference: international standard atmosphere of ICAO (International Civil Aviation Organization). It accounts for the temperature and pressure variation: it assumes 15 °C and 101325 Pa at sea level, with vertical thermal gradient (initially) equal to -6,5 °C/(1000 m) z z 1, 225exp 10262 If we account for air humidity 1 x p x (mass of vapor per unit of mass of dry air) is the specific humidity Ra xRv T of air, Rv is the gas constant for water vapor (= 461,5 J kg-1 K-1) 1 1 Available Power & v1 A v1 v12 0,5 A v13 P0 m 2 2 2 4000 3500 ρ=1,225 kg m-3 3000 2 power (W/m ) 2500 2000 potenza 1500 1000 500 0 0 2 4 6 8 10 12 14 16 18 velocità (m/s) velocity A is the area of the actuator disc (area swept by the rotor) A first family of wind motors / generators is the one with a vertical axis rotor, acronym VAWT, Vertical Axis Wind Turbines. These rotors, rotating with respect to a vertical axis, do not need to change orientation as the direction of the wind varies, and this certainly constitutes a great operational simplification. These rotors, with the exception of the Savonius type, do not start spontaneously in the presence of wind, but require external starting (this is not a problem for generators connected to the general electrical network). A further observation on the vertical axis rotors concerns the type of dynamic action of the wind on the rotor used to obtain useful energy; in the Savonius rotor the drag opposed to the wind by the rotor is exploited, while in the Darrieus or H rotors the lift action induced by the wind on the rotating blades is mainly exploited, which in fact, in the vast majority of cases, have an aerodynamic profile. It can be shown that lift rotors are much more efficient than drag rotors. Other types of wind generator belong to the horizontal axis family, acronym HAWT, Horizontal Axis Wind Turbines. The most common is a modern three-blade wind turbine. This same family of wind motors / generators includes turbines with one, two or three blades, the so-called Dutch four-blade turbines (derived from the historic windmills) and the so-called American turbines with large numbers of blades (called multi-blade). They are all lift rotors, generally with the possibility of self-starting; they all commonly operate in the windward position (to limit the disturbing action on the wind operated by the nacelle and the support tower). They need a mechanism to get oriented in the direction of the wind. DRAG ROTOR LIFT ROTOR lift portanza F low pressure bassa pressione corda del pro filo drag resistenza angolo di attac co velocità indisturbata relative velocity velocità relativa alta highpressione pressure Some italian terminology Componenti nella Mozzo del Navicella (o Gondola) rotore e controllo calettamento Pala del rotore Albero rotore e Moltiplicatore giri ad ingranaggi cuscinetti Freno rotore Mozzo del rotore e controllo calettamento Generatore elettrico Cavidotti di potenza Quadro elettrico e sistema di controllo Pala del rotore Basamento Sistema controllo imbardata Torre Cavidotti di potenza Connessione alla rete Fondazione 1. Pale 2. Rotore 3. Passo della pala 4. Freno 5. Albero bassa velocità 6. Moltiplicatore giri 7. Generatore 8. Controllo 9. Anemometro 10. Banderuola 11. Gondola (navicella) 12. Albero alta velocità 13. Comando imbardata 14. Motore imbardata 15. Torre Wind generator, 2008, Emdem, Germania Nominal power 6 MW Rotor diameter 126 m / Height 135 m There are wind generators with nominal power 8 MW (rotor diam 164 m) Evolution of dimensions of wind rotors in HAWT Union Pacific Railroad Laramie, 1868 Rotor Savonius Rotor Darrieus Rotor H-Darrieus Vertical axis wind rotors Wind Turbine Darrieus Diameter 19 m Nominal power 170 kW Wind Turbine with H rotor Diameter 35 m Nominal power 300 kW Aerogenerator X. Vertical axis wind generator with a nominal power of 10 MW under development in the UK (Arup), for off-shore applications on a semi- submersible platform; distance between the tips of the blades 275 m. First installations initially planned for 2014. Chimney height 200 m Chimney diameter 10 m Solar roof diameter 250 m Project to be carried out in the Australian desert, now shelved. Solar tower EnviroMission New project to be built in the Arizona desert, USA, with expected production start date in 2015 (but construction has not yet begun in 2014) Nominal power 200 MW Tower height 800 m Area of the circular greenhouse on the ground about 40 km2 Estimated cost 750 M$ How can we characterize the available wind resource? WINDINESS – Wind speed statistics The speed of the wind is continuously changing, making it desirable to describe the wind by statistical methods If we have a set of measured wind speeds vi , which is measured every time interval i , the average speed can be calculated as If we consider only the time intervals when we measure vi we can obtain the Probability p(vi ) of the discrete wind speed vi being observed: it is equal to the ratio of these time periods divided by the total time of observation in other terms it is equal to the proportion of total time characterized by speed vi p(vi ) = Weibull statistical distribution Probability density function k v k 1 v k D v exp s is scale parameter, k is shape parameter ss s Probability to have a speed between v1 and v2 v2 v k v k v k vv12 v1 D v d v exp exp 1 exp 2 v2 s s s v1 Cumulative distribution function v v k v k v v0 v D v dv exp 1 exp 0 s s 0 Weibull statistical distribution Maximum available energy speed probability density scale factor shape factor median speed average speed probability distribution scale factor median speed shape factor Maximum available energy speed average speed velocity Weibull statistical distribution Probability to have a wind speed between v1 and v2 v2 v k v k v k vv12 v1 D v d v exp exp 1 exp 2 v2 s s s v1 Probabilità to have a wind speed between v and v+dv D v dv = proportion of total time with speed between v and v+dv Median speed v v k v k v v0 v D v dv exp 1 exp = 0,5 0 s s 0 vˆ k 1 Velocità mediana : exp 0,5 vˆ s ln 2 k s Average wind speed Average wind speed 1 Velocità media v v d v v D v dv 0 1 v s Γ 1 k x1 exp y dy Funzione function : x y gammaGamma 0 y is the integration variable, while x is the argument of the gamma function Ratio scale factor / average speed Shape factor Weibull statistics Maximum available energy speed probability density scale factor shape factor median speed average speed probability distribution scale factor median speed shape factor Maximum available energy speed average speed velocity When the shape factor is 2 (k = 2) the Weibull distribution is referred to as the Rayleigh distribution, a situation which is very often taken as a reference to define the generic performance of a wind turbine (without referring to a particular application site). In this case, the characteristic parameters of the statistical distribution can be written as: 1 v 1 k s 2 v v 2 D v 2 exp 2v 4 v v 2 0 v 1 exp v 4 v Dimensionless expressions Velocità speed v* v / v normalizzata Normalized Densità di Probabilità Probability della Velocità density of normalized Normalizzata speed k * * k k D v k v exp v * v k 1 v s s D v k 1 * 1 k v * k 1 exp k 1 1 v * k It is only a function of k k k D v* v D v D v dv D v dv * * CumulativeCumulata Probabilità probability distribution della of normalized Velocità Normalizzata : speed v* k v * v* 0 v D v* dv* exp k 1 1 v * k 1 exp 1 1 * k 0 k 0 k Probability distribution Normalized probability density Normalized speed Weibull statistics Together with the shape parameter, the value of the scale factor determines the average wind speed, and is therefore an index of the windiness of the site. The statistical distribution of wind speed naturally varies from place to place, depending on the local climatic conditions, the altitude considered, the conformation of the site and the characteristics of the surface. Therefore the Weibull distribution can vary both in the shape and in the values of the other characteristic parameters. It should be noted that the Weibull model is only a mathematical tool, with which we try to approximate the results of measurements on the windiness of a site carried out in appropriate time intervals (to have a complete view of the situation, it is necessary to extend the evaluation to a whole year; even better if the surveys, at a suitable height from the ground, are available for longer times and therefore data on the typical year can be obtained). The Weibull distribution is not always able to approximate the measurements satisfactorily, for example in the case of two-peak probability density, characteristic of areas with a strong prevalence of seasonal phenomena; in this circumstance one can often use distributions obtained from the composition of two distinct Weibull functions, or the Weibull distribution with more than two parameters. The practical values that the shape parameter can take are between 0.5 and 4, depending on the irregularity of the wind; its value is quite homogeneous in similar climatic areas; it assumes values around 1.5 in mountain areas, around 2 in temperate climates and coastal areas, and around 3 in trade wind-monsoon areas. As regards the Italian situation, the surveys of the various anemometric stations scattered throughout the territory show values of the shape parameter between 0.5 and 2.3, with average speed values up to 8 m/s. Available instant wind 1 : P0 Av1 3 power 2 1 1 Available Energia energy : Ed A v d A v33 winddisponibile eolica 3 2 2 1 1 3 1 3 speed : v3 v d v3 s 1 3 3 Velocità media Mean cubiccubica k Ed 1 Available Potenza mean media power : Pd disponibile Av33 2 3 1 3 1 v3 k Fluctuationdicoefficient Coefficiente : kf fluttuazione v 1 1 k mean speed / scale factor fluctuation coefficient Ratios Fluctuation coefficient Ratio cubic mean speed / scale factor Ratio mean speed / scale factor Shape factor 3 1 1 3 3 v 1 Coefficiente di 3fluttuazione k 3 1 k v s Γ 1 v3 s 1 f k k v 1 1 k 1 1 Available Energia eolicaenergy in disponibile : Ed A v3 d D A v v d 3 v 3 the time interval Δ 2 2 1 Ed A v3 D v dv 2 0 We can search the wind speed that maximizes the function v3 D v 𝜕(𝑣 3 𝐷 𝑣 ) =0 𝜕𝑣 We find the speed value that provides the maximum contribution to energy availability (in the case of the Weibull statistical distribution): 1 k 2 k vmax E s k This speed value is always higher than both the average speed and the cubic average speed, and also higher than the value of the scale factor of the Weibull distribution. In defining the operating parameters of a wind turbine, it is important that the wind speed range around this value is exploited to the maximum degree. cubic mean mean Ratio Speed of maximum available energy / Mean speed Ratio Speed of maximum available energy / Scale factor Ratios Ratio Speed of maximum available energy / Cubic mean speed Shape factor 1 1 2 v2 v d 2 Quadratic mean speed 1 2 for Weibull distribution v2 s 2 1 k In the case of k=2 (Raileigh) , we obtain 2 1 and thus v2 s 1/ 2 2 1/ 2 1 v22 v 2 k R 1 v v 2 Relative standard deviation 2 1 1 It depends only on k k Approximate empirical expressions, always in case of Weibull statistics: 1/ k v 0, 433 R k 0,9208 0,568 s k Low k means high variability Again, it is confirmed that the value of the shape factor k is indicative of the variability of the wind speed around the average value: high values of k (3 or higher) indicate a site where the wind speed (these are values averaged in intervals of the order of 10 min - 1 hour) varies little around the average annual value (such as in the trade wind band*), while low values of k (such as 1) indicate wind of high variability. (*) trade wind = venti alisei The wind speed values obtained from measurements in a given site are generally evaluated at a fixed height above the ground, and are commonly averaged in the short term: the IEA and IEC standards establish an average period of 10 min. The wind speed values considered previously refer to this situation: they therefore mediate instantaneous speed fluctuations (turbulence) and short-term fluctuations (gusts); these data are considered suitable for evaluating the annual energy generation of a wind generator. The energy calculations for a wind rotor refer to the wind speed at the center line of the device: the average height of the rotating surfaces for a vertical axis rotor; the median dimension of the hub for a turbine rotor with a horizontal axis. It must therefore be taken into account that in the vicinity of the ground, and significantly up to 100 m above sea level where wind rotors generally operate, the wind speed is affected by friction with the surface; only at altitudes above 1000 m the wind speed profile can be considered not disturbed by the ground. A model generally used in the wind industry to evaluate the variation of wind speed with altitude is the logarithmic Prandtl model, which is based on the general theory of the dynamic boundary layer: ln( z / m) v z v0 m is roughness coefficient and depends on the ln( z 0 / m) class of ground Roughness coefficient, m Class m [m] Description 0 0,0002 Still water surface 0,5 0,0024 Terreni completamente aperti con superficie liscia (piste di aeroporto, prati falciati etc.) 1 0,03 Aree agricole aperte senza recinzioni e siepi e con edifici molto radi; colline a declivio dolce roughness 1,5 0,055 Terreni agricoli con qualche casa e filari di recinzione alti 8 m a distanza media di 1250 m 2 0,1 Terreni agricoli con qualche casa e filari di recinzione alti 8 m a distanza media di 500 m 2,5 0,2 Terreni agricoli con molte case, arbusti e piante, o filari di recinzione di 8 m a circa 250 m 3 0,4 Villaggi, piccoli paesi, terreni agricoli con molte o alte siepi, foreste e terreni molto scabri ed irregolari 3,5 0,8 Grandi città con edifici alti 4 1,6 Metropolis with tall buildings and skyscrapers Wind speed profile as function of height Class of ground Height from ground, ln( z / m) v z v0 ln( z 0 / m) Ratio The following relationship is also often used to express the variation of wind speed with height from the ground vz z v0 z0 If we do not have more information on the type of ground, we can take: 1/ 7. In addition to the statistical distribution of speed, it is useful to have the wind rose of a site (see figure in next slide). It essentially shows, in polar representation, the statistical distribution of the direction of origin of the winds usually over the year. The particular wind rose in the figure divides the entire round angle into twelve sectors, each of 30°. The three polar representations, all normalized with respect to the maximum value that is represented with the maximum coordinate of the diagram, provide: a- the relative frequency of origin of the wind in the twelve sectors, i.e. the percentage of the total time in which the wind blows from the direction considered; b- the above data, multiplied by the average wind speed in the considered direction, and this allows to determine how much each directional sector contributes to the average wind speed; c-the data referred to in a- multiplied by the cube of the average cubic wind speed in each sector, and this allows to determine how much each directional sector contributes to the total energy availability of the wind. The wind rose of a particular site allows, for example, to ascertain the nature of any obstacles present in the most favorable directions for energy production, or to plan the location of the various turbines on a wind farm. N Wind rose c W E a- the relative frequency of origin of the wind in the twelve sectors, i.e. the percentage of the total time in which the wind a blows from the direction considered; b b- the above data, multiplied by the average wind speed in the considered direction; S c- the data referred to in a- multiplied by the cube of the average cubic wind speed in each sector. European Wind Atlas W/m2 Finally, it must be considered that wind systems, even if not in operational conditions, must still be able to structurally resist extreme wind conditions, even if these are likely to occur very rarely. In this regard, the international standard IEC 61400 - part I (Wind Turbines - Design requirements) specifies the essential requirements in the design of wind turbines, in order to ensure an adequate level of protection against damage from all kinds of risks over the lifetime of the turbine. The standard considers all the subsystems of a wind turbine, such as protection and control devices, internal electrical systems, mechanical systems and support structures. The standard classifies wind turbines into four classes, for three of which a reference wind speed vref is specified, which is five times the average annual wind speed in the considered location. The extreme speed with a recurrence of 50 years is then defined, equal to 1.4 vref at the height of the hub; the wind speed is considered variable with the height according to a law proportional to the power 0.2 of the height; the extreme wind speed with annual frequency is finally considered equal to 0.75 vref. Finally, for each class three levels of turbulence are defined; A designates the turbulence level of extreme characteristics, B that of intermediate characteristics and finally C that of more reduced characteristics; Iref indicates the respective levels for the intensity of turbulence at 15 m s-1 (ratio between the standard deviation of the speed with respect to the average value over the time of 10 min, and the value of the speed itself). With reference to these values and operating conditions, the standard defines a number of transient events to which the turbine must resist. The wind speeds of the four classes of wind turbines are set as follows in the standard IEC 61400-Part 1: Class of wind turbine I II III S Reference speed vref [m s-1] 50 42,5 37,5 Values Yearly average speed v [m s-1] 10 8,5 7,5 specified A Iref [-] 0,16 by B Iref [-] 0,14 design C Iref [-] 0,12 The aforementioned standard does not apply to offshore wind turbines, which are instead the subject of the IEC 61400-3 standard; it is instead applied in conjunction with the IEC 61400-2 standard for small turbines (area swept by the rotor less than 200 m2). The entire set of IEC 61400 standards (also CEI EN 61400) is dedicated to wind turbines and its components). UNIVERSITẦ DEGLI STUDI DI PADOVA LM Energy engineering Renewable Energy Technologies WIND ENERGY Part 2 D. Del Col Source Erich Hau, Wind Turbines. Fundamentals, Technologies, Application, Economics, Springer Power output from an ideal turbine: one dimensional wind turbine model The kinetic energy of the wind is exploited; the wind is slowed down! In 1926 Betz published a paper that is the basis of the analysis presented here. Although the model is considerably simplified, it provides a basis for understanding the characteristics of wind turbines. The major assumptions are as follows: -Incompressible and frictionless steady flow -An ideal rotor (i.e., an infinite number of blades with uniform flow and forces over the rotor) -A non-rotating wake -Static pressure in the stream tube far upstream and downstream of the rotor that is equal to the undisturbed static pressure One dimensional wind turbine model Betz theory does not refer to any specific device for capturing wind power; we will refer to an actuator disk, intended as a generic conversion device, which is functionally assimilated to a surface with permeability to the flow of air. The assumptions underlying Betz theory are the following: 1. The current tube that passes through the actuator disc does not interact with the remaining portion of fluid that surrounds it. 2. In each section of the flow tube there is a permanent, uniform and one-dimensional velocity distribution in the axial direction. The fluid deceleration on the actuator disc is evenly distributed over the disc section. 3. In the infinitely upstream and downstream sections it is possible to consider a fluid dynamic situation undisturbed by the presence of the machine, that is, we have the atmospheric pressure of the external environment, just like in the free jet condition. 4. The wind flow encounters no obstacles beyond the turbine, neither upwind nor downwind. 5. The wind is stationary and of constant intensity with altitude. 6. There is no spinning effect of the wake due to momentum "extraction". 7. The compressibility of the air is neglected, ie the density is considered constant. The fluid flow, characterized upstream (section 1) by an undisturbed speed v1, reaches the rotor blades and is slowed down - before and after the rotor - until it reaches a speed v2 in section 2 section 2 v A v1 A1 v2 section 1 A2 From the equation of mass conservation From conservation of momentum v1 A1 = v2 A2 = m The thrust T is the axial force of the wind on the turbine T = m (v1 − v2 ) v12 − v22 P = T v = v m (v1 − v2 ) P = m 2 v = ( v1 + v2 ) / 2 It is convenient to introduce the axial induction factor a as the fractional reduction of the wind velocity at the rotor a: axial induction factor a = 1 – v / v1 = ( v1 – v ) / v1 v = v1 ( 1 - a ) v2 = v1 (1-2a) Therefore the power can be written as a function of the axial induction factor 1 P= Av13 4a( 1 − a )2 2 1 Whereas the available wind power is P0 = Av13 2 TURBINE POWER COEFFICIENT It is the ratio of the turbine power to the power of the wind 1 P 2 Av13 4a (1 − a ) 2 CP = = = 4a (1 − a ) 2 P0 1 Av13 2 P and CP display maximum values when the axial induction factor a=1/3 Cp max = 16/27 0.59 2 CP = P/P0 = (1/2) (1 - v2 / v1 ) (1 + v2 / v1) Ratio of areas Relative variation of kinetic energy Power coefficient Speed ratio POWER COEFFICIENT: ratio of the turbine power to the power of the wind 1 P 2 Av13 4a(1 − a) 2 CP = = = 4a (1 − a ) 2 P0 1 Av13 2 The power coefficient is not strictly speaking an efficiency, for the definition of which the correct reference should be the kinetic power possessed by the flow rate actually processed by the actuator disk P* 1 1 1 P* = & v12 = Av v12 = Av13 (1 − a ) m m 2 2 2 P CP = = 4 a (1 − a ) = At maximum power: η=8/9=0,889 P* (1 − a) Comment regarding the concept of efficiency of a wind rotor. The energy of the wind, in the short time, has an unpredictable and casual character, but it is free in nature. A 20% efficiency defect between two axial turbine rotors can be compensated, by the less efficient rotor, with a 10% increase in diameter. The concept of efficiency therefore loses in this case the decisive role it has in other cases of exploitation of primary energy sources (fossil fuels, but also in many cases the hydraulic source) while other evaluation parameters have more importance (plant cost and management, specific annual production,...). THRUST TORQUE 1 T = Av12 4a(1 − a) Mr = P 2 THRUST COEFFICIENT TORQUE COEFFICIENT T drag Mr CT = e CM = 1 1 Av1 2 force of wind Av1 R 2 2 2 CT = 4a(1 − a) Tip-speed ratio CM = CP = 4a(1 − a)2 U R = = v1 v1 Real performance of wind rotors Pmec ideale(Betz) < Pmec While remaining in the ideal range of inviscid flow (i.e. neglecting the viscosity of the air) , and with specific reference to a rotor with horizontal rotation axis, it must be considered that a rotating converter necessarily imparts a rotary motion to the wake air flow; for the conservation of tangential momentum, the helical motion imparted to the air flow will have the opposite direction of rotation to that of the rotor itself. The existence of a tangential velocity component reduces the kinetic energy variation induced by the rotor compared to what is calculated by Betz's theory. As a consequence, the power coefficient of the rotor is reduced, depending on the ratio between the energy component of the rotary motion and that of the axial translation motion. U R = = v1 v1 2 RN g U= ; = v1 60 2 RN g 2 N g 2 U= ; = ; = 60 60 2 RN g 2 N g 2 RN g U= ; = ; = 60 60 60v1 limit with wake rotation (Betz limit) At low values of the tip speed ratio, even in otherwise optimized conditions, the losses of kinetic energy due to the vorticosity of the wake can be high; only when λ tends to infinity, such losses tend to zero (the rotationality of the flow decreases) and the power coefficient tends to the ideal Betz value. The wake losses decrease rapidly as λ increases, tending to cancel out for λ → ∞. - for a specified undisturbed wind speed, the power recovered by each rotor blade can be expressed as the product of the useful torque on the blade by the blade rotation speed; Mr = P - as the speed of rotation increases (and therefore as λ increases), a lower torque (and therefore a lower tangential force) is required to obtain the same power 2 RN g 2 N g 2 RN g U= ; = ; = 60 60 60v1 - a lower tangential force corresponds to a lower tangential velocity value impressed to the air flow, and therefore a lower wake loss To be able to obtain adequate information, no longer referring to idealized situations of the behavior of a real rotor in capturing wind energy, it is necessary to consider the total aerodynamic actions (lift and drag) exerted by the wind on a blade element of a wind rotor. torque L S TO TF -r vr v TH thrust blade element of a wind rotor coppia utile Lift and drag on a translating airfoil The chord line is the straight line connecting the leading and trailing edges of an airfoil The pitch angle is the angle between the chord line of the blade and the plane of rotation The plane of rotation is the plane in which the blade tips lie as they rotate. The blade tips actually trace out a circle which lies on the plane of rotation. Full power output would normally be obtained when the wind direction is perpendicular to the plane of rotation. The pitch angle is a static angle, depending only on the orientation of the blade. Another important blade parameter is the angle of attack , which is the angle between the chord line of the blade and the relative wind or the effective direction of air flow. It is a dynamic angle, depending on both the speed of the blade and the speed of the wind. Lift and drag on a translating airfoil lift portanza F low pressure bassa pressione corda del pro filo drag resistenza angolo di attac co velocità indisturbata velocitàvelocity relative relativa alta highpressione pressure D L CD = ; CL = 1 1 Ap vr2 Ap vr2 2 2 STALL flow detachment, with Set value of Reynolds the formation of vortices on the leeward side of number the airfoil D L CD = ; CL = 1 1 Ap vr2 Ap vr2 2 2 α [°] L CL E= = Indicates airfoil efficiency D CD L CL E= = Indicates airfoil efficiency D CD In the previous figure, the maximum value of the airfoil efficiency is identified at an angle of attack just above 0°, with an efficiency of the airfoil that exceeds the value 200; it represents the optimal operating situation of the airfoil Dependence of the aerodynamic coefficients on the Reynolds number (and thus on the magnitude of the inertia forces compared to the viscous ones) -on average the drag coefficient CD increases as the Reynolds number decreases, -this increase is drastic below the critical value of Re, when the boundary layer becomes totally laminar; -the effect of Re on the coefficient of lift CL is most important on the value of the stall angle, which increases as Re increases; -since the lift coefficient varies approximately linearly with the angle of attack for values lower than the stall angle, even the maximum value of the lift coefficient increases as the Reynolds number increases. Furthermore, the coefficients depend on the surface quality; in particular the drag coefficient increases with the roughness of the surface. Ф v1 (angolo di calettamento) (angolo di attacco) Ф = α+θ The tangential force that produces useful torque derives from the lift of the profile = + angle of attack + pitch angle S = L sin − D cos Tangential force T = L cos + D sin Axial thrust Tangential force coefficient CS CS = CL sin − CD cos Axial thrust coefficient CT CT = CL cos + CD sin 1 1 S = CS Ap vr2 T = CT Ap vr2 1 M r = S r = CS Ap vr2 r 2 2 2 Rotor torque Local tangential velocity of the blade u=ωr varies from blade root to blade tip Blades are twisted - the twist locally necessary to keep the angle of attack α constant along the entire blade depends on the value of the ratio between the tip speed of the blade and the local wind speed v - the optimization of the blade geometry therefore is done for the nominal operating conditions - in the other operating conditions, the twisting of the blade is not optimized, and this inevitably leads to efficiency losses The whirling impulsive theory assumes complete absence of resistant action by the blades, and therefore the use of an ideal blade profile for which the lift / resistance ratio L / D → ∞ It has already been discussed how the action of the resistance (which derives from the variation of momentum of the wind flow when interacts with the blades) leads, in lift rotors, to the generation of a torque contrary to the useful rotary motion, and how it therefore reduces the wind power captured by the rotor. Furthermore, the impulsive theories take into consideration a generic actuator disk, and the results are based on the entire flow rate passing through this device; in practice, the possibility of capturing a higher or lower fraction of this power also depends, for a wind turbine, on the number and shape of the blades, as well as on their speed of rotation. Impulsive theories therefore consider, in all circumstances, a number of blades, with idealized behavior, B → ∞ Whirling impulsive theory Effect of number of blades with the same wind speed, a finite number of blades can interact more completely with the entire flow of air passing through the surface swept by the rotor when the rotation speed is higher (i.e. λ is higher). Effect of blade drag as the lift / drag ratio (L / D) decreases, the power coefficient that can be achieved decreases. The airfoils, in the design conditions, work with efficiency values of around 50 – 100, while the curved plate blade profiles operate, always in optimal conditions, around efficiency values 10 – 15. The optimal point of the power coefficient shifts towards lower values of λ as the efficiency of the blade airfoil decreases (the efficiency decreases because of the drag losses). At high values of L / D (≈100), the optimal value of the tip speed ratio λ is high, and the number of rotor blades is not so important for the value of the achievable power coefficient. On the other hand, when the efficiency of the blade airfoil is low (L / D ≈ 10), the achievable values for the power coefficient are considerably lower, they can be obtained at low values of the tip speed ratio λ, and the number of blades becomes very important. High speed rotors (high λ) can have excellent performance with a limited number of blades, but the blade profile is of great importance in this case. (Betz) It is evident the superiority of the modern HAWT rotors with aerodynamic profile blades, operating at high values of tip tangential speed, compared to the old slow (in terms of the value of the parameter λ) traditional rotors (Dutch, American). With the latter it is difficult to achieve, under optimized operating conditions, rotor power coefficient values of 0.3, while modern rotors can reach values around 0.5, therefore not excessively far from the ideal Betz limit. The different types of wind rotors show optimal operation around different values of the tip speed ratio λ: while the American multi-blade rotors have optimal operation around λ = 1, the fast single-blade rotors operate effectively in a wider range of λ, around the value λ = 15. The different types of rotors are characterized in fact by different values of the solidity parameter σ, defined, for HAWT rotors, as the ratio of the frontal area of the rotor blades to the total area swept by the rotor in its motion. Three- Two- Single Dutch multi-blade blade blade blade Solidity (loose) correlation between rotor Bc Z solidity and optimal value of the = design tip speed ratio R2 American multi-blade Tip speed ratio Bc Z B number of blades = Rotor solidity c (average) chord of the airfoil R2 Z lenght of the blade A low solidity value produces a broad and rather flat CPR - λ curve; this means that CPR changes little over a wide range of values of the tip speed ratio, but the maximum value of CPR is low due to the high resistance losses of the blade profile. A high solidity value produces a tight CPR - λ curve with a pronounced peak, making the rotor performance very sensitive to variations in the tip speed ratio; if the solidity value is too high, the maximum CPR value is low, due to losses due to rotationality of the wake. An optimal solidity value (also from an economic point of view) is achieved with three-blade HAWT wind rotors (typical solidity values around 0.035), but the two-blade solution can be an acceptable alternative because the CPR curve - λ is flatter Mr CP Rotor torque coefficient CM = = v12 AR 2 CM Torque The difference between slow multi-blade rotors and fast ones with a low number of blades is evident; in particular, at the start (λ = 0) the former can produce high torque even with modest wind speeds, unlike the latter. It is easy to understand the unsuitability of rotors with a limited number of blades to produce high starting torque: when stationary they can interact only very limitedly with the total flow of wind that passes through the swept area. Hence the suitability of multi-blade rotors to operate as aeromotors, for example with the rotor directly mechanically connected to volumetric pumps for lifting water (as for classic American multi-blade aircraft) or connected to millstones (Dutch windmills). For wind turbines (rotors for electricity production), apart from the need for a minimum wind speed value to operate (cut-in speed), the low torque value constitutes an advantage for the sizing of any revolutions multiplier of connection between the slow rotor axis and the fast axis of the electric generator. Number of rotor blades The smaller the number of blades of a rotor, the faster it must rotate (other conditions being equal) to compensate for the disadvantage of a smaller coverage of the physical area of the actuator disc The optimal range of design values of the tip speed ratio varies as a function of the number of rotor blades When switching from one to two blades, the increase in the maximum rotor power coefficient is substantial (see next slide) In passing from three to four blades, this increase is only 1 or 2%, which generally does not justify the higher cost These curves in the figure represent the envelope of the characteristic curves of the power coefficients of modern rotors as the pitch of the blades varies (see next figure). Three-blade rotor WKA-60. The CPR - λ curve depends on the pitch angle of the blade; modern rotors with variable pitch of the blades in motion can in theory adapt the pitch angle by optimizing it in different operating conditions (therefore at different values of the tip speed ratio λ), while rotors with fixed blade pitch must operate along a single curve characteristic CPR - λ. For wind turbines, connected to the general electricity grid and built about twenty years ago (operating at a fixed rotation speed), being able to operate at high rotation speeds was a concrete advantage. The lower multiplication ratio necessary between the slow rotor axis and the fast axis of the generator (which had to directly produce electricity at grid frequency) led to significant advantages in terms of weight and cost for the gear multiplier. Currently, due to the progress in the conception and construction of speed multipliers, and to the possibility of operating even without a speed multiplier with rotors with variable rotation speed, the design rotor rotation speed is no longer a problem, and therefore this cancels out one of the reasons for preferring two-blade or even single-blade fast rotors. Furthermore, one of the negative environmental aspects in the exploitation of wind energy is the generation of noise from wind turbines. To reduce the sound power of the wind rotors it is necessary to limit the value of the tip speed of the blade; an empirical limit value in this regard is U=70 m/s. For large modern rotors, the three-blade are favored in this respect over the two- blade or single-blade. Nowadays it is possible to work with lower rotation speed, therefore less advantage of the two-blade rotors Furthermore, there is the constraint due to noise (U=70 m/s) CM Shape of the blade airfoils As a general design constraint, the lift coefficient of the blade profile is chosen so that, at the design value of the tip speed ratio λD, the blade operates at the maximum efficiency value (lift / drag ratio). With commonly used airfoils, the corresponding angle of attack is several degrees below the critical value (of maximum lift), thus leaving an appropriate margin with respect to stall conditions; in these conditions, the indicative value of the lift coefficient is around 1. The maximum value of the rotor power coefficient CPR is reached at the chosen design value of λD. This, however, requires achieving an aerodynamically optimal distribution for the chord trend of the blade profile along its length. The optimal trend provides for a hyperbolic distribution of the size of the chord as a function of the radius. The next figure shows the result of the aerodynamic optimization of the blade profiles, for rotors with different number of blades and different design tip speed ratio; the figure refers to a well-determined airfoil (NACA 4415). Chord The inapplicability of some solutions can be immediately noticed, however, outside the optimal limits already considered. For example, the aerodynamically optimal blade profile for a three-blade rotor with a design tip speed ratio of 15 is too elongated and thin to be able to satisfy the necessary structural and stiffness mechanical constraints. Often, for reasons of constructive simplicity, the hyperbolic planar profile, which corresponds to the optimal aerodynamic condition, is approximated with trapezoidal or semitrapezoidal trends with rectilinear traces of the leading edge and trailing edge, with a modest penalty on the value of the rotor power coefficient. It has already been observed that the part of the blade close to the hub has less importance, as regards the capture of wind energy, than the outermost part. For this reason the part of the blade closest to the hub is shaped giving greater importance to structural and stiffness requirements rather than to aerodynamic requirements. On the other hand, the tip of the blade mainly responds to aerodynamic needs, also to reduce the intensity of the extremity eddies, a further phenomenon that penalizes the power coefficient achievable due to the increase of the drag action. Nominal power and energy yield The wind turbines are characterized by the rated (nominal) power value Pn, which is the maximum electrical power that can be produced by the electric generator. The corresponding value of rotor power PRn is higher, due to the effect of mechanical losses (supports and mechanical seals of the slow axis, possible speed multiplier) and electrical losses (generator, possible inverter) in the energy transmission chain from the rotor to the electric grid. An indicative value, for modern wind turbines, of the global mechanical losses is around 4%; the efficiency of a generator is around 0.96 - 0.97, and that of a frequency converter 0.97 - 0.98. For economic reasons, the rated power of a wind turbine is somewhat lower than the power value it could produce at maximum operating wind speeds. When the wind has a speed between the nominal value v1n and the maximum speed at which the rotor is operated (cut-out speed), it is necessary to control the rotor power output constantly at the PRn value (or lower values). For wind speed values lower than the nominal value v1n the rotor will operate in partial yield conditions. The nominal speed value v1n and therefore the choice of the nominal power value responds to technical-economic optimization criteria, and represents a fundamental design choice for a wind generator. WIND GENERATORS WITH VARIABLE PITCH IN MOTION - wind generators connected to the general electricity grid, and put into operation up to ten years ago, are of the type with an electric generator directly connected to the grid - they must operate with a rotor at a constant rotation speed, apart from modest variations resulting from the sliding of any conventional asynchronous generator - the rotation speed is determined by the grid frequency, by the number of pole pairs of the electric generator, and of course by the multiplication ratio of the speed variator between the slow rotor axis and the fast axis of the generator - this prevents adapting the value of the tip-speed ratio to the value of the wind speed; only for a value of the wind speed the rotor can operate at the maximum value of the power coefficient. wind generator cut-out Rotor power, nominal speed generator cut-in wind speed, Three-blade real aerogenerator (WKA-60) Electric nominal power 1200 kW (at rotor 1342 kW), rotor diameter D = 60 m Speed range: cut-in – cut-out 6 – 24 m s-1, nominal wind speed v1n = 12 m s-1, Fixed rotation speed Ng = 23 giri/min. Total energy production vcut −out E= P d E = P v D v dv vcut −in POWER DENSITY Wind turbine WKA-60, statistics distribution of wind speed according to Weibull with k = 2 and s = 7,9 m s-1 Annual energy yield : MWh/year Energy available in the wind : 9943 MWh/anno Maximum energy that can be captured (according to Betz): 5892 MWh/year MWh/anno Energy captured by the rotor : 3414 MWh/year MWh/anno Specific rotor production HR (ratio of production to the rated power): 3414000 ore hours HR = = 2544 1342 anno year Distribuzione di Weibull, k = 2, s = 7,9 m s-1 Weibull distribution, max according to available in the wind Betz theory Specific power density , captured by the rotor median speed average speed cut-in wind speed, cut-out VARIABLE ROTATION SPEED WIND TURBINES - use of a synchronous electric generator with permanent magnets with a high number of pole pairs (up to over one hundred) and converter - this electronic power device transforms the variable frequency current generated by the generator into direct current, and subsequently (inverters and electronic switches) into alternating current suitable for powering the network The advantage of this solution is the elimination of the speed multiplier, with its direct and indirect costs (due to the considerable mass). Turbina eolica WKA-60 variable rotation speed Rotor power, constant rotation speed wind speed, Turbina eolica WKA-60 variable rotation speed Specific power density , constant rotation speed average speed Weibull distribution median k = 2, s = 7,9 m s-1 speed cut-in wind speed, Weibull distribution, variable ω available in the wind Specific power density , cut-in speed 4,5 m s-1 ; 6 m s-1 max that can be captured (Betz) speed average median fixed ω wind speed, FIXED PITCH WIND TURBINES - the connection of the blades to the hub is fixed; they generally work with direct connection of the generator to the general electricity grid - they must therefore operate at a constant rotation speed - as the wind speed varies, the tip speed ratio of the rotor therefore varies - the power coefficient follows the trend of the rotor characteristic with constant pitch Rotor power coefficient CPR Rotore tripala Three-blade Fixed pitchfisso Calettamento Tip-speed ratio λ Rotore tripala Three-blade Fixed pitchfisso Calettamento Rotor power coefficient CPR Tip-speed ratio λ Rotore tripala D = 60 m Three-blade Calettamento Fixed pitchfisso Rotor power coefficient CPR 15 25 30 Ng = 10 rpm 20 wind speed, Three-blade Rotore tripala D = 60 m Fixed pitchfisso Calettamento 25 Rotor power, Ng = 20 rpm 15 wind speed, Maximum power is limited by passive stall of the blades The rated power is chosen from the maximum value of the rotor (and generator) power ATTENTION The power delivered by the rotor in stall conditions (beyond the nominal wind speed corresponding to the maximum power value) is fluctuating and cannot be accurately predicted. In these conditions the rotor is subjected to unstable dynamic actions: it is important to avoid the occurrence of fatigue damage. The design rotation speed drastically affects the power delivered by the turbine. If the design rotation speed is low, the power reaches its maximum value at low wind speeds, and at higher wind speeds it is necessary to operate in stall conditions and therefore inefficiently. A turbine operating at high rotation speed, at moderate wind speeds operates inefficiently due to drag losses The annual production increases with the rotation speed, and then decreases. The maximum value for annual energy production can be used, with reference to a defined windiness, to choose the design rotation speed Passive Stall Control with Fixed Blade Pitch This passive self-regulating mechanism for controlling the power input of the rotor gives stall control its practical significance, especially for small turbines which in most cases do not have blade pitch adjustment. At higher wind velocities, the rotor power is only limited by the aerodynamic stall occurring at the rotor blades. Using this type of passive stall control requires carefully designed rotor blade geometry and carefully selected rotor speed. To ensure that at a certain wind speed the flow does indeed separate, so that an increase in power is effectively prevented, the rotor must be generally operated at a speed below the aerodynamically optimum rotational speed. Three-blade Rotore tripala D = 60 m Calettamento fisso Fixed pitch Specific rotor power density , 40 20 30 Ng = 10 rpm Wind speed v1 Power control Goals: - Limit the power captured by the wind turbine to values not exceeding the nominal power of the electric generator Pn - Keep the rotor rotation speed controlled, at a constant value or within well- defined limits. Example: dramatic problem in case of loss of voltage on the part of the network to which the generator is connected: the resistant torque suddenly fails, and the rotation speed would increase rapidly, with possible destruction of the wind generator Aerodynamic means can be used to control the captured power and possibly the speed of rotation 1 Variation of yaw angle (angolo di imbardata) – only for small power aerogenerators Reducing the aerodynamically effective rotor swept area, i.e. turning the rotor out of the wind (furling), is only practicable with very small rotors Power Control by Rotor Blade Pitching By far the most effective way of influencing the aerodynamic angle of attack, and thus the input power, is by mechanically adjusting the rotor blade pitch angle (next figure). For this purpose, in general, the rotor blade is turned about its longitudinal axis with the aid of actively controlled actuators. In principle, power control by changing the aerodynamic angle of attack of the rotor can be achieved by two methods. The conventional approach is by adjusting the angle of attack of the blade to a smaller angle in order to reduce power input. Conversely, increasing the angle of attack increases the power input. The other possibility is to change the blade pitch angle to a larger angle of attack up to the so-called "critical aero- dynamic angle of attack", at which point the airflow separates at the surface of the rotor blades, thus limiting the aerodynamic power input. This effect is known as stall. The advantage of this method is that the necessary turning angle for pitching the blade is smaller. Medium and large turbines: variation of angle of attack Controlling the rotor input power by pitching the blade towards feather or towards stall The methods used are basically three: - passive stall - pitch control (passo avanti) - active stall (passo indietro – stallo attivo) 1. Passive is the method of limiting the captured power typical of wind turbines with fixed pitch blades (it concerns machines with fixed rotation speed, at most double speed). It occurs spontaneously by entering the stall area, which depends on the relative angle of incidence of the wind on the blades, which depends on the wind speed. 2. The pitch control (adjustment of the pitch towards feather): when the nominal wind speed is exceeded, the pitch angle is rotated (counter-clockwise), so as to reduce the angle of attack α to a value lower than the optimal one , and keep the captured power constant by reducing the lift coefficient (and at the same time also the drag coefficient). 3. The active stall (pitch adjustment towards stall): with winds speed higher than the nominal value, the blades rotate clockwise in order to overcome the critical angle of attack and enter the stall zone, adjusting in thus the captured power. Methods 2 and 3: for wind speed values above the cut-out value, the blades can be oriented in line with the wind. Comparison among methods Practical experience has shown that method 2 (continuously controlled blade pitch angle settings towards feather) leads to a much steadier operation which is why almost all the larger wind turbines have this type of power control. Using continuous blade pitch control, the electrical output power can be kept at a constant level at wind speeds from rated wind speed up to cut-out wind speed. The continuous adjustment of the blade pitch angle towards the feathered position provides for an effective and precise control of the output power and, if necessary, also of the rotor speed over a wide range of wind velocities. Control of the rotor speed is of importance when the electrical generator is not connected to a fixed-frequency grid which would otherwise govern the rotor speed. This mode of operation has to be used while the rotor accelerates up to the speed of synchronization with the grid frequency and when the wind turbine is operated in isolation (stand-alone mode). Adjusting the pitch angle towards the feathered position offers further advantages. As power control takes effect above the rated wind speed, rotor thrust drops markedly, while this is hardly the case with stall-regulated rotors. In addition, the rotor blades can be feathered completely when wind speeds are extremely high, thus greatly reducing the wind loading on the rotor blades and on the entire turbine. Active stall control with a number of blade pitch angles in operation and in standstill EXERCISE A three-blade horizontal axis wind turbogenerator, with rotor diameter 2R = 80 m, operates at constant rotation speed Ng = 14 rpm, with the following characteristic speed values: vc-i=4 m s-1, vc-o=25 m s-1, v1n=12,5 m s-1. The rotor power characteristic (CPR rotor power coefficient as a function of the tip speed ratio λ) is that shown in the attached figure. The power control for wind speed higher than the nominal value is obtained by adjusting the pitch of the blades. With reference to a site whose annual windiness can be represented in terms of Weibull probability density with two parameters, with shape factor k = 2 and scale factor s = 7.9 m s-1, constant reference density of the air ρ = 1.225 kg m-3, it is requested to evaluate the annual specific rotor production of the device. EXERCISE, cont Rotor power coefficient CPR Tip-speed ratio λ EXERCISE, cont EXERCISE, cont Now let us divide the speed range in intervals v1 = 0,5 m/s. For each interval, we make the calculation for the average speed in that interval. In the following the calculation is reported for the interval v1 = 10-10,5 m/s EXERCISE, cont EXERCISE, cont Δv1 v1 λ CPR P* P D DP* DP -1 ms - - kW (m s-1)-1 -1 -1 kW (m s ) 4↔4,5 4,25 13,798 0,2814 67 67 0,1020 6,78 6,78 4,5↔5 4,75 12,346 0,3514 116 116 0,1060 12,29 12,29 5↔5,5 5,25 11,170 0,3945 176 176 0,1082 19,01 19,01 5,5↔6 5,75 10,198 0,4237 248 248 0,1085 26,90 26,90 6↔6,5 6,25 9,383 0,4435 333 333 0,1071 35,70 35,70 6,5↔7 6,75 8,688 0,456 432 432 0,1042 45,01 45,01 7↔7,5 7,25 8,088 0,4643 545 545 0,1001 54,52 54,52 7,5↔8 7,75 7,567 0,4682 671 671 0,0949 63,65 63,65 8↔8,5 8,25 7,108 0,4693 811 811 0,0888 72,07 72,07 8,5↔9 8,75 6,702 0,4684 966 966 0,0822 79,43 79,43 9↔9,5 9,25 6,340 0,4659 1135 1135 0,0753 85,43 85,43 9,5↔10 9,75 6,014 0,4618 1318 1318 0,0681 89,76 89,76 10↔10,5 10,25 5,721 0,4558 1511 1511 0,0610 92,19 92,19 10,5↔11 10,75 5,455 0,4489 1717 1717 0,0541 92,84 92,84 11↔11,5 11,25 5,213 0,4402 1930 1930 0,0474 91,56 91,56 11,5↔12 11,75 4,991 0,4291 2143 2143 0,0412 88,33 88,33 12↔12,5 12,25 4,787 0,4156 2352 2352 0,0355 83,39 83,39 12,5↔13 12,75 4,599 0,3995 2549 2549 0,0302 77,00 76,99 13↔13,5 13,25 4,426 0,3802 2723 2549 0,0255 69,39 64,96 13,5↔14 13,75 4,265 0,3596 2878 2549 0,0213 61,31 54,30 14↔14,5 14,25 4,115 0,3386 3016 2549 0,0176 53,21 44,97 14,5↔15 14,75 3,976 0,3165 3127 2549 0,0145 45,26 36,90 15↔15,5 15,25 3,845 0,2928 3197 2549 0,0118 37,62 30,00 15,5↔16 15,75 3,723 0,2682 3226 2549 0,0095 30,59 24,17 16↔16,5 16,25 3,609 0,2441 3225 2549 0,0076 24,41 19,30 16,5↔17 16,75 3,501 0,2217 3208 2549 0,0060 19,21 15,27 Δv1 v1 λ CPR P* P D DP* DP EXERCISE, cont m s-1 - - kW (m s-1)-1 kW (m s-1)-1 4↔4,5 4,25 13,798 0,2814 67 67 0,1020 6,78 6,78 4,5↔5 4,75 12,346 0,3514 116 116 0,1060 12,29 12,29 5↔5,5 5,25 11,170 0,3945 176 176 0,1082 19,01 19,01 5,5↔6 5,75 10,198 0,4237 248 248 0,1085 26,90 26,90 6↔6,5 6,25 9,383 0,4435 333 333 0,1071 35,70 35,70 6,5↔7 6,75 8,688 0,456 432 432 0,1042 45,01 45,01 7↔7,5 7,25 8,088 0,4643 545 545 0,1001 54,52 54,52 7,5↔8 7,75 7,567 0,4682 671 671 0,0949 63,65 63,65 8↔8,5 8,25 7,108 0,4693 811 811 0,0888 72,07 72,07 8,5↔9 8,75 6,702 0,4684 966 966 0,0822 79,43 79,43 9↔9,5 9,25 6,340 0,4659 1135 1135 0,0753 85,43 85,43 9,5↔10 9,75 6,014 0,4618 1318 1318 0,0681 89,76 89,76 10↔10,5 10,25 5,721 0,4558 1511 1511 0,0610 92,19 92,19 10,5↔11 10,75 5,455 0,4489 1717 1717 0,0541 92,84 92,84 11↔11,5 11,25 5,213 0,4402 1930 1930 0,0474 91,56 91,56 11,5↔12 11,75 4,991 0,4291 2143 2143 0,0412 88,33 88,33 12↔12,5 12,25 4,787 0,4156 2352 2352 0,0355 83,39 83,39 12,5↔13 12,75 4,599 0,3995 2549 2549 0,0302 77,00 76,99 13↔13,5 13,25 4,426 0,3802 2723 2549 0,0255 69,39 64,96 13,5↔14 13,75 4,265 0,3596 2878 2549 0,0213 61,31 54,30 14↔14,5 14,25 4,115 0,3386 3016 2549 0,0176 53,21 44,97 14,5↔15 14,75 3,976 0,3165 3127 2549 0,0145 45,26 36,90 15↔15,5 15,25 3,845 0,2928 3197 2549 0,0118 37,62 30,00 15,5↔16 15,75 3,723 0,2682 3226 2549 0,0095 30,59 24,17 16↔16,5 16,25 3,609 0,2441 3225 2549 0,0076 24,41 19,30 16,5↔17 16,75 3,501 0,2217 3208 2549 0,0060 19,21 15,27 17↔17,5 17,25 3,399 0,2005 3168 2549 0,0047 14,89 11,98 17,5↔18 17,75 3,304 0,181 3116 2549 0,0037 11,38 9,31 18↔18,5 18,25 3,213 0,1634 3058 2549 0,0028 8,60 7,17 18,5↔19 18,75 3,128 0,147 2983 2549 0,0021 6,41 5,48 19↔19,5 19,25 3,046 0,132 2899 2549 0,0016 4,72 4,15 19,5↔20 19,75 2,969 0,1179 2796 2549 0,0012 3,42 3,11 20↔20,5 20,25 2,896 0,1048 2679 2549 0,0009 2,44 2,32 20,5↔21 20,75 2,826 0,0932 2564 2549 0,0007 1,72 1,71 21↔21,5 21,25 2,760 0,0824 2434 2434 0,0005 1,19 1,19 21,5↔22 21,75 2,696 0,0724 2293 2293 0,0004 0,82 0,82 22↔22,5 22,25 2,636 0,0636 2157 2157 0,0003 0,55 0,55 22,5↔23 22,75 2,578 0,056 2030 2030 0,0002 0,37 0,37 23↔23,5 23,25 2,522 0,0499 1931 1931 0,0001 0,25 0,25 23,5↔24 23,75 2,469 0,046 1897 1897 0,0001 0,17 0,17 24↔24,5 24,25 2,418 0,0435 1910 1910 0,0001 0,12 0,12 24,5↔25 24,75 2,369 0,0422 1970 1970 0,0000 0,09 0,09 EXERCISE, cont Without power control Δv1 v1 λ CPR P* P D DPS* DPS m s-1 - - kW (m s-1)-1 W m-2/(m s-1) 4↔5 4,5 13,03 0,321 90 90 0,104 1,867 1,867 5↔6 5,5 10,66 0,411 210 210 0,109 4,541 4,541 6↔7 6,5 9,02 0,451 381 381 0,106 8,025 8,025 7↔8 7,5 7,82 0,467 606 606 0,0976 11,770 11,770 8↔9 8,5 6,90 0,469 887 887 0,0856 15,108 15,108 9↔10 9,5 6,17 0,464 1226 1226 0,0717 17,479 17,479 10↔11 10,5 5,59 0,453 1613 1613 0,0575 18,452 18,452 11↔12 11,5 5,10 0,435 2036 2036 0,0443 17,933 17,933 12↔13 12,5 4,69 0,408 2454 2454 0,0328 15,993 15,993 13↔14 13,5 4,34 0,370 2804 2454 0,0233 13,013 11,387 14↔15 14,5 4,04 0,328 3076 2454 0,0160 9,790 7,809 15↔16 15,5 3,78 0,280 3213 2454 0,0106 6,759 5,162 16↔17 16,5 3,55 0,233 3222 2454 0,0067 4,321 3,291 17↔18 17,5 3,35 0,191 3145 2454 0,0041 2,594 2,024 18↔19 18,5 3,17 0,155 3023 2454 0,0025 1,481 1,202 19↔20 19,5 3,01 0,125 2858 2454 0,0014 0,803 0,689 20↔21 20,5 2,86 0,098 2609 2454 0,0008 0,406 0,382 21↔22 21,5 2,73 0,078 2376 2376 0,0004 0,198 0,198 22↔23 22,5 2,61 0,059 2079 2079 0,0002 0,090 0,090 23↔24 23,5 2,50 0,048 1905 1905 0,0001 0,041 0,041 24↔25 24,5 2,39 0,043 1939 1939 0,0001 0,020 0,020 Δv1, m s-1 2 1 0,5 0,2 0,1 0,01 ER, MWh/anno 6386 6372 6371 6369 6368 6368 We can see how the choice Δv1 = 1 m s-1 would lead to satisfactory results for engineering purposes. Effect of rotation speed Annual rotor energy, MWh/year Rotation speed, rpm