Metal Casting History and Glossary PDF
Document Details
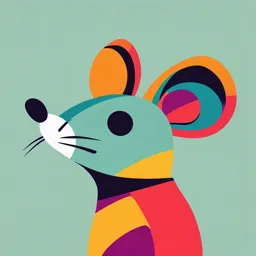
Uploaded by SuperbSuprematism
Tags
Summary
This document details the history of metal casting from 3200 B.C. to the late 20th century. It includes important milestones in the development of various casting processes and materials. A glossary of terms related to metal casting is also included, defining concepts such as blackheart iron, cold box process, crucible casting and more.
Full Transcript
History Origins of Metal Casting 3200 B.C. – A copper frog, the oldest known casting in existence, is cast in Mesopotamia. 2000 B.C. – Iron was discovered. 800–700 B.C. – First Chinese production of cast iron. 645 B.C. – Earliest known sand molding (Chinese). 233 B.C. – Cast iron plowshares are pou...
History Origins of Metal Casting 3200 B.C. – A copper frog, the oldest known casting in existence, is cast in Mesopotamia. 2000 B.C. – Iron was discovered. 800–700 B.C. – First Chinese production of cast iron. 645 B.C. – Earliest known sand molding (Chinese). 233 B.C. – Cast iron plowshares are poured in China. 500 A.D. – Cast crucible steel is first produced in India, but the process is lost until 1750 when Benjamin Huntsman reinvents it in England. Middle Ages to 1800 1455 – Dillenburg Castle in Germany is the first to use cast iron pipe to transport water. 1480 – Birth of Vannoccio Biringuccio (1480–1539), the "father of the foundry industry," in Italy. He is the first man to document the foundry process in writing. 1642 – Saugus Iron Works, America's first iron foundry (and second industrial plant), is established near Lynn, Massachusetts. The first American iron casting, the Saugus pot, is poured there. 1709 – Englishman Abraham Darby creates the first true foundry flask for sand and loam molding. 1720 – Rene Antoine de Reaumur develops the first malleable iron, known today as "European Whiteheart." 1730 – Abraham Darby is the first to use coke as fuel in his melting furnace in Coalbrookdale, England. 1750 – Benjamin Huntsman reinvents the process of cast crucible steel in England. This process is the first in which the steel is completely melted, producing a uniform composition within the melt. Since the metal is completely molten, it also allows for alloy steel production, as the additional elements in the alloy can be added to the crucible during melting. Prior steel production was accomplished by a combination of forging and tempering, and the metal never reached a molten state. 1776 – Foundrymen Charles Carroll, James Smith, George Taylor, James Wilson, George Ross, Philip Livingston, and Stephen Hopkins sign the American Declaration of Independence. 1794 – First use of the Cupola in iron founding. Invented by John Wilkinson of England, the original had metal-cladding and utilized a steam engine to provide the air blast. The 19th Century 1809 – Centrifugal casting is developed by A.G. Eckhardt of Soho, England. 1815 – The cupola is introduced in the United States in Baltimore, MD. 1818 – First cast steel produced by the crucible process in the U.S. at the Valley Forge Foundry. 1825 – Aluminum, the most common metal in the earth's crust, is isolated. 1826 – Seth Boyden of Newark, NJ, is the first to develop a process for and produce "blackheart" malleable iron. 1831 – In Cincinnati, OH, William Garrard establishes the first commercial crucible steel operation in the U.S. 1837 – First dependable molding machine is marketed and used by the S. Jarvis Adams company in Pittsburgh. 1845 – The open hearth furnace is developed. 1851 – Sir Henry Bessemer and William Kelly both invent a simple converter that uses blasts of air to burn out the impurities — silicon, manganese, and excess carbon — in pig iron. Although Kelly is the first to use a converter, Bessemer obtains the U.S. patents. Kelly proves patent priority in 1857. 1863 – Metallography, the etching, polishing, and microscopic evaluation of metal surfaces, is developed by Henry C. Sarby of Sheffield, England. It is the first process to physically examine the surface of castings for quality analysis. 1867 – James Nasmyth develops a gear-tilted foundry ladle, increasing worker safety and operational economy. 1870 – Sandblasting is first used to clean large castings by R.E. Tilghman of Philadelphia. 1880–1887 – The Sly tumbling mill is developed. It is the first cleaning machine for small castings. This mill greatly reduced the time needed for hand-cleaning operations and produced a finer finished product. 1896 – American Foundrymen's Association (renamed American Foundrymen's Society in 1948 and now called the American Foundry Society) is formed. 1897 – Investment casting is rediscovered by B.F. Philbrook of Iowa. He uses it to cast dental inlays. Early 20th Century 1906 – First electric arc furnace is used in the U.S. at Holcomb Steel Co. in Syracuse, NY. 1913 – First true stainless steel melted by Harry Brearley in Sheffield, England. 1913 – Crucible Steel Casting Co.'s Lansdown, PA plant installs the first low-frequency electric furnace for special melting. 1923 – Formation of the International Committee of Foundry Technical Associations in Zurich, Switzerland. 1924 – Dr. W.H. Hatfield invents 18/8 stainless steel (18% chromium, 8% nickel). 1930s – University of Michigan professors pioneer Spectrography for metal analysis. 1930 – First high-frequency coreless electric induction furnace in the U.S. is installed in the Lebanon Steel Foundry in Lebanon, PA. 1940 – Wood flour is introduced into foundry practice as a sand additive. 1947 – The Shell Process, invented by J. Croning of Germany during WWII, is discovered by U.S. officials and made public. 1948 – Development of ductile iron, a cast iron with a fully spheroidal graphite structure. 1949 – U.S. patent granted to K.D. Millis, A.P. Gagnebin, and N.B. Pilling of International Nickel Company for developing ductile iron. 1953 – The Hotbox system of making and curing cores in one operation is developed, eliminating the need for dielectric drying ovens. 1958 – H.F. Shroyer is granted a patent for the full mold process, the forerunner of the expendable pattern (lost foam) casting process. 1960s – Compactibility and methylene blue clay tests are developed for green sand control. Also developed at this time are high-pressure molding processes and fast-setting no bake binders for sand. 1964 – The first Disamatic molding machine is introduced. 1965 – The Scanning Electron Microscope is invented by the Cambridge University Engineering Department in England. 1965 – Cast metal matrix composites are first poured at International Nickel Company in Sterling Forest, NY, by Pradeep Rohatgi. 1968 – The Cold Box Process is introduced by L. Toriello and J. Robins for high-production core making. Late 20th Century Early 1970s – The Semi-Solid Metalworking (SSM) process is conceived at Massachusetts Institute of Technology. It combines aspects of casting with aspects of forging. 1971 – The Japanese develop V-Process molding. This method uses unbonded sand and a vacuum. 1971 – Rheocasting is developed at Massachusetts Institute of Technology. 1971 – U.S. Congress passes the Clean Air Act and OSHA, the Occupational Health and Safety Act. 1972 – The first production Austempered Ductile Iron (ADI) component is produced by Wagner Castings Company. 1974 – Fiat introduces the in-mold process for ductile iron treatment. 1976 – Compacted graphite iron (CGI), an iron with elongated graphite particles with rounded edges and roughened surfaces, is developed in the U.K. It has characteristics of both gray and ductile iron. 1982 – The Warm Box binder system is introduced. 1993 – First foundry application of a plasma ladle refiner (melting and refining in one vessel) occurs at Maynard Steel Casting Company in Milwaukee, WI. 1995 – Babcock and Wilcox, Barberton, OH, patent a lost foam vacuum casting process to produce stainless steel castings with low carbon content. 1996 – Cast metal matrix composites are first used in a production model automobile in the brake rotors for the Lotus Elise. 1997 – Electromagnetic casting processes developed by Argonne and Inland Steel Corporation. Electromagnetic edge containment greatly reduces cost and energy expenditures in steel production. Glossary Blackheart: American type of malleable iron. The normal fracture has a medium gray outer rim and a very black interior. Coke: Coal derivative resulting from the distillation of bituminous coal in the absence of air. The distillation process removes all of the volatile material from the coal so it can be used as a very intense source of fuel in cupola melting. Cold Box Process: A rapid core making process which does not require application of heat to cure the cores. Hardening of the cores is accomplished by chemical reaction rather than by conventional baking. A phenolic resin is added to the sand used to make the core. This resin reacts chemically when exposed to an accelerator (typically an active organic gas) and hardens very quickly, forming an organic bond in the core sand. This reaction occurs at room temperature and does not require special core boxes or equipment. Additionally, since the bond is organic, the sand collapses readily during shakeout and can be recovered easily from the casting. Crucible: A ceramic pot with refractory properties typically made of clay in which metal is melted for casting. Cupola: Vertically oriented, tube-shaped melting furnace in which the metal is melted in direct contact with the fuel. Ductile Iron: A type of iron in which the graphite content takes spherical rather than flake form. Ductile iron is produced by adding magnesium. The spherical form of the graphite provides greater tensile strengths and flexibility than other types of iron. Green Sand: Natural sands combined with water and organic additives (such as clay) to proper consistency for creating molds. Investment Casting: Method of casting using an expendable pattern of wax, plastic, or other material which is "invested" or surrounded by a molding medium in slurry or liquid form. After the molding medium has solidified, the pattern is removed by subjecting the mold to heat, leaving a cavity for reception of molten metal. Also called lost-wax molding. Malleable Iron: Iron that may be altered in shape by hammering or by the pressure of rollers without exhibiting fracture or brittleness. The majority of the carbon content is in the form of graphite nodules rather than flakes. Rheocasting: Also called flow casting. A metal forming process in which a semi-solid metal is used to make the casting. The solid metal is heated to a partly liquid, softened state and then pressed into the final form. The finished part has closer tolerances, better surface finish, higher strength, and lighter weight than a similar part made with traditional casting techniques. Shell Process: Process in which clay-free silica sand coated with a thermosetting resin or mixed with resin is placed on a heated metal pattern for a short period of time to form a partially hardened shell. The bulk of the sand mixture inside the resulting shell is removed for further use. The pattern and shell are then heated further to harden or polymerize the resin sand mix, and the shell is removed from the pattern. Frequently, shell cores are made using the hot box process. Warm Box Process: Core making method in which the corebox is warm when the core sand is introduced. The warmth of the corebox initiates curing but does not complete it. Cores finish curing outside the corebox (sometimes in a separate dryer), allowing for faster core production cycles than with the hot box process. Cores created using this process must be solid—they cannot be shell cores. Here is the text with spacing corrected and no modifications: Classification of Foundries Types of Foundries The foundry is a commercial or an establishment for producing castings in molten metal. The tendency is to act or process the act of founding or casting metal. A foundry may also be known as a collection of materials, fuel, fluxes, and tools to produce castings. It can be categorized according to the basis of production pattern and metals to be cast, which is shown below. Production Pattern Captive Foundry It is an integral part of some manufacturing organizations, where all the castings made are consumed mainly in the products being manufactured by that organization. Jobbing Foundry Normally produces a small number of castings of a given type for different customers. Such types of foundries may also have facilities for mass production. Production Foundry It is highly mechanized and can produce castings economically on a mass scale. Semi-Production Foundry It is a combination of jobbing foundry and a production foundry as regards its nature of work is concerned. Steel Foundry Steel foundry produces plain carbon steel, low and high alloy steels. Grey Cast Iron Foundry It is highly mechanized and can produce castings of grey color in nature. Malleable Iron Foundry It can produce castings to be hammered or pressed into shape and easy to influence. Ductile Iron Foundry It can produce castings to be drawn into fine standards and easily molded. Light Metals Foundry Aluminum and magnesium alloy foundry can produce light metals. Brass, Bronze, and Copper Foundry This type of foundry requires the alloys of germanium silver, aluminum phosphor, bronze, and manganese bronze brass to produce the metals. Lead, Tin, and Zinc Base Foundry This type of foundry requires the alloys of tin, antimony, copper zinc, solder, britannia metal, and bronze to produce the metals. In casting of metal, foundries can be classified as ferrous foundries and non-ferrous foundries. The iron group, which includes all irons and steels, are called ferrous metals (ferrous means iron), while the others are called non-ferrous. Ferrous Foundries may be further classified as:  Steel Foundry  Grey Cast Iron Foundry  Malleable Iron Foundry  Ductile Iron Foundry Non-ferrous Foundries may be classified as:  Light Metals Foundry  Copper, Brass, and Bronze Foundry  Lead, Tin, and Zinc Base Foundry Alloy materials play a crucial role in daily life. Types of Solid Solution:  Used in utensils, vehicles, computers, mobile phones, 1) Substitutional Solid Solution Strengthening: chairs, etc. Solute atom replaces solvent atoms in their lattice positions.  Various engineering, medical equipment, machinery, and Some alloying elements are only soluble in small amounts, while tools are made from alloys. others can form a solution over the entire range of binary How to make alloys: compositions.  Made by combining two or more metal elements while in 2) Interstitial Solid Solution: a molten state or by bonding metal powders. Solute atom is small enough to fit into interstitial sites Different alloys have different desired properties: between solvent atoms.Atoms crowd into interstitial sites, compressing the bonds of solvent atoms, causing deformation.  Strength Mixture of Solid Solution:  Visual attractiveness  Two crystalline solids mix to form a new crystalline solid  Malleability or lattice.  Hardness  Mixing occurs by melting the solids into liquids at high  Low melting points temperatures and then cooling, or by depositing vapors onto substrates to form thin films.  Magnetic or electrical characteristics  Mutual solubility depends on chemical properties and  High corrosion resistance crystalline structure. Properties of alloys: Mixed lattice can be:  The internal and external characteristics change during the  Substitutional: Atoms of one crystal replace those of alloy-making process. another.  Corrosion-resistant alloys can be formed and joined using  Interstitial: Atoms occupy normally vacant positions in conventional techniques. the lattice.  Solid solution alloy products are generally used in the annealed condition. The properties of the solid solution can vary continuously over the range of concentrations, allowing for tailoring properties for Age-hardenable alloys: specific applications.  Best fabricated in the annealed condition.  Can be directly aged or annealed and then aged for high Mixture of Pure Crystallite: strength.  Corrosion-resistant alloys typically formed at room  Solid solution strengthening improves the strength of temperature. pure metals by adding atoms of another element  Severe deformation may require multiple deformations (alloying element). with annealing between operations or heating to elevated temperatures for greater deformation.  The alloying element disrupts the lattice, making plastic deformation more difficult by impeding dislocation After hot forming: motion. Parts should be annealed to restore corrosion resistance.  Alloying beyond the solubility limit can form a second phase, leading to further strengthening (e.g., Cold-formed components: precipitation of intermetallic compounds). May be placed in service without annealing. If the environment could cause stress corrosion cracking, the cold-formed parts should be annealed. Age-hardened alloys: Not typically used in environments that induce stress corrosion cracking. Solid Solution:  A uniform mixture of substances in solid form.  Consists of two or more types of atoms or molecules sharing a crystal lattice (e.g., metal alloys).  Example: Steel is a solid solution of iron and carbon, where carbon atoms fit within iron's lattice and enhance its strength. Alloying Structure:  Four classes of alloy steel: structural steels, magnetic alloys, tool and die steels, and heat-resisting stainless  Substitutional Alloys: A second element replaces a metal steels. atom; form when the metals are similar in size.  Common in products like refrigerators, sinks, forks, and  Interstitial Alloys: A second element is much smaller knives. than the solvent element.  Heterogeneous Alloys: Components are not dispersed Steel Alloys: uniformly.  Combining iron and carbon creates various steel products.  Additional elements like molybdenum, nickel, silicon, boron, and manganese can be added to create different qualities. Super-Austenitic Stainless Steels Alloy (SASS Alloy):  Enhanced with higher nickel and nitrogen for improved strength and corrosion resistance.  Contains about 6% molybdenum and sufficient Common Types of Alloys: chromium for resistance to both reducing and oxidizing Aluminum Alloys: environments.  Not the strongest metal alone but combined with others Properties of Alloys: to create conductive, heat-resistant, and tarnish-resistant Alloys are generally: alloys.  Used in mechanical components like car engines,  Stronger and harder than the pure metal. airplane body panels, and boat hulls.  Less malleable and ductile.  More corrosion-resistant. Bearing Alloys: The strength of an alloy comes from the different atomic sizes  Used for accommodating pressure under sliding contact of the elements within it. Example: Bronze (made of copper and with another metal body (e.g., rotating shafts of motors, tin) is harder than copper and was historically used in the generators, vehicles, and propellers). "Bronze Age." Alloys are widely used across various fields and Corrosion-Resisting Alloys: industries for their improved properties over pure metals.  Made using noble metals to resist corrosion by forming a Composition, Properties, and Usage of Alloys: separation layer. Alloys are designed with specific properties in mind,  Examples: Stainless steel and aluminum alloys. such as improved strength, durability, or corrosion resistance, Gold Alloys: depending on their composition and intended application.  Gold used in jewelry is often an alloy because pure gold is too malleable.  Used in electronics for its conductivity. High-Strength Corrosion-Resistant Alloys:  Precipitation-hardenable versions of corrosion-resistant alloys offering more than twice the strength.  Can be fabricated before heat treatment and then heat- treated for high strength. Other Alloys:  Dental Alloy and Die-Casting Alloy: Widely used in daily life. Nickel Alloys:  React with specific chemicals to produce electricity, used in batteries and electric cars. Stainless Steel Products:  Made from iron and carbon; chromium and nickel are added to make stainless steel.