W20N Rheology PDF
Document Details
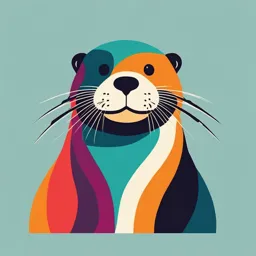
Uploaded by TimeHonoredSaxophone
Tags
Summary
This document provides an overview of rheology, covering learning outcomes, rheology and testing, viscometry, quality control, and rheology as a quality control tool. It includes definitions of terms, Newton's experiments, and viscoelasticity measurements. It's suitable for understanding the science of deformation and flow of matter, ideal for undergraduate study in materials science.
Full Transcript
Rheology Learning Outcomes Rheology and Rheological Testing Introduction to Viscometry Thixotropy shear-thinning and Yield Stress Oscillatory Rheological Testing Rheological Viscoelasticity Parameters Rheology The science of deformation and flow of mat...
Rheology Learning Outcomes Rheology and Rheological Testing Introduction to Viscometry Thixotropy shear-thinning and Yield Stress Oscillatory Rheological Testing Rheological Viscoelasticity Parameters Rheology The science of deformation and flow of matter - Viscosity is resistance to flow - Rheological properties affect a) Processing b) Drug product performance Viscometry Testing The measurement of a fluid’s resistance to flow The importance of rheology Characterisation & classification of materials - Rheological measurements describe the flow behaviour of liquids & semisolids ex) creams, ointments - Insights into viscosity, elasticity, viscoelasticity, to understand structure a) Raw materials b) Finished products Quality control - Physical stability, consistency in quality, patient compatibility, drug bioavailability - Differences could indicate contamination, poor mixing, variability - Adhesive performance of transdermal patches Process optimisation - By understanding how materials behave under stress and strain - Select suitable equipment Product development - Optimise flow, spreading, firmness, etc Predict behaviour - Under different conditions – e.g. temperature, pressure Research and Development - Explore molecular structure, interactions, new materials Rheology as a Quality Control Tool It can describe and quantify processing or application product characteristics or issues/problems: - Is it spreadable on the skin? - How well does it pour from the container? - The formulation has particle sedimentation during storage on the shelf - The patch detached from the skin – how adhesive is it on the skin surface? Newton’s Experiment Shear stress = force/area Velocity of top layer = displacement/time Shear strain = displacement/height Shear strain rate = velocity of top layer/height Viscometry – Definition of Terms Shear stress (σ) – the torsional force per area Applied Force / Area of top layer = N / m2 - The applied force per unit area is the shearing stress or SHEAR STRESS - 1 N/m2 = 1 Pa Shear Strain (g) – the resultant displacement divided by the sample height Strain = Displacement / Gap - Shear strain is normally abbreviated to strain - Dimensionless: use “% strain” or “milli strain” terms Shear (strain) rate (g’) – the change in strain in a certain time Shear Rate = Shear Strain / Shear Time - The rate of change of STRAIN is known as the shear strain rate or SHEAR RATE - Since strain has no units, the shear rate has units of reciprocal seconds (s-1) Viscosity (h) – shear stress divided by shear rate ratio of shear stress to shear rate Viscosity = Shear Stress / Shear Rate - Units; a) Pascal. Second Pas (SI) b) Poise P (CGS) - Dynamic viscosity h (Nm-2 s or Pas) generally used viscosity h = σ / g’ § A measure of the resistance of a fluid to flow (or move) - Kinematic viscosity n (m-2 s-1) regarding density ? n=h/ρ § Normalised value of viscosity § Velocity of the flow - The dynamic viscosity of a Newtonian liquid is 0.65 (Pas) and its density is 650 kg m-3. What is the kinematic viscosity of this liquid? (0.001 m-2 s-1) Newtonian Flow Easiest behaviour to describe – liquids have constant viscosity, regardless of applied shear stress (force per unit area acting parallel to the surface (as opposed to normally). So resistance to flow does not change with speed or force of flow. Follow Newton’s law - Rate of flow (shear rate, γ) is directly proportional to applied stress (shear stress, σ) Shear rate proportional to shear stress (slope = viscosity) Equipment for measuring Newtonian flow - Capillary viscometers - Falling Sphere viscometers (also called SINGLE POINT viscometers) Ostwald U-tube Falling Sphere viscometer viscometers - Tube filled with sample fluid (density = ρl) - Spherical ball of known density (ρs) and radius (r) is - Laminar flow of liquid under introduced to the tube the influence of gravity - Record time (t) for sphere to - Record time to flow from C to fall from mark A to mark B D under gravity Dynamic viscosity; - Determine viscosity using h=Kρt Stoke’s law; = Instrument constant x density x time a) V is velocity of sphere b) g is acceleration due to gravity Non-Newtonian Flow (Rotational Rheometer) Pharmaceutical systems tend to be non-Newtonian – because they are complex and heterogeneous Rate of flow (shear rate, g) is not directly proportional to applied stress (shear stress, σ) Three types of common behaviour; 1) Plastic 2) Pseudoplastic 3) Dilatant Plastic (or Bingham) flow Pseudoplastic flow Dilatant flow - Usually describes concentrated - Cannot define viscosity unless - Cannot define viscosity unless shear flocculated suspensions shear stress/rate specified stress/rate specified - When flocculated, weak bonds hold - Usually associated with - Usually associated with solutions of dispersed particles together concentrated deflocculated polymers, gums or pastes - When deflocculated, particles are suspensions and pastes a) sort of materials which have free to move independently - At low shear rates; particles are crosslinked networks - Flocculating agents may therefore separated, liquid acts as lubricant b) applied force is not sufficient to be used to change rheological - At high shear rates; particle break crosslinks, but will cause properties clump together, liquid no longer material to flow - Can also exhibit pseudoplastic flow lubricant and viscosity increases Studies of non-Newtonian Viscosity will change with applied stress Need an instrument that can apply variable stress and measure corresponding strain - Rheometer; to generate a stress/strain curve, rheometer must increase then decrease applied stress Upper mobile plate - Parallel plate (stainless steel, titanium, etc) - Cone plate Lower stationary plate Experimental settings - Size of plate (20nm, 40nm) - Gap size between plates - Temperature of plates Typical Rheology Instrumentation ¬ Cup and Bob ¬ Rotational Rheometer Typical measuring Geometries Factors that affect viscosity (η) 🌟 Temperature (T) Þ viscosity ¯ Pressure (P) Þ viscosity Time (t) - Thixotropic systems Shear stress (σ) - Newtonian systems Viscosity is shear rate (and shear stress) independent - Non-Newtonian systems viscosity changes depending on what we do Newtonian Fluids Newton’s Law of Flow: σ / g’ = constant - Flow curve (rheogram) is a linear plot, starting from zero / dy/dx = viscosity - Dynamic viscosity (η) is the proportionality constant Examples of Newtonian Fluids Ñ Non-Newtonian Fluids Shear stress dependent viscosity - Shear-thinning (pseudoplastic) flow (e.g. cream) a) Flow begins as soon as shear stress is applied b) Viscosity is high at low shear rates and vice versa c) Power Law equations: σ / η g’ where n < 1 d) Shear-thinning of polymer solutions (e.g. gels formulations) micelles + extra polymers quite thick - Shear-thickening (dilatant) flow (e.g. concentrated suspension corn starch, plaster) a) The opposite behaviour to shear-thinning behaviour pressure sensitive 어쩌구 b) Viscosity is high at high shear rates and vice versa c) Power Law equation: σ / η g’n where n > 1 increase stirring rate more aggregates formed increase viscosity - Bingham flow (e.g. toothpaste high yield stress thick/high viscosity, needs applied pressure to flow) a) Newtonian flow begins when yield stress 𝛔𝐲 is reached σ = 𝛔𝐲 + η g’ Time dependent viscosity - Thixotropic flow (e.g. bentonite, ketchup) Thixotropic behaviour ex. emulsion paint Thixotropy is time dependent shear-thinning (pseudoplastic) behaviour - When mixed up shake constantly viscosity decreases to the bottom point it becomes a liquid - But re-sets after application stop mixing thickens up again/behaves like a solid Hysteresis Loop (Thixotropic Loop) - Measured area gives an indication of how thixotropic a material is Yield stress - No flow until a certain shear stress is applied Viscoelasticity in Products Many materials exhibit visco-elasticity – i.e. they behave like viscous liquids in some processes and like elastic solids in others An example would be a concentrated suspension: - During storage, it needs to behave like a solid to prevent sedimentation - During application, it needs to behave like a fluid – e.g. so that it flows in the bristles of the brush and can be evenly painted Oscillation Principles Phase Angle (d) - For purely Elastic Material a) The stress and strain are exactly in phase b) Therefore the phase angle is zero - For purely Viscous Material a) The stress and strain are 1/4 of a cycle out of phase b) Therefore the phase angle is 90° - Phase Angle (d) is a measure of Elasticity a) The higher the phase angle, the more viscous b) The lower the phase angle, the more elastic Complex Modulus (G*) X Complex Modulus (Pa) = Stress / Strain - Mathematically derived from the ratio of the stress and strain amplitudes Calculated Parameters in Oscillation X - Loss (Viscous) Modulus, G’’ (Pa) = Stress / Strain x sin (d) ; can indicate the liquid-like nature of the sample - Storage (Elastic) Modulus, G’ (Pa) = Stress / Strain x cos (d) ; can indicate the solid-like nature of the sample - Dynamic viscosity, h’ (Pas) = G’’ / Frequency ; can be related to the shear viscosity if the sample obeys the Cox-Merz rule Test Modes Rotational rheometers have a range of test modes: - Viscometry (shear) - Oscillation - Creep and Recovery ‘Wet sponge model’ Dry = elastic solid (storage modulus) - If add water (inelastic, viscous/loss modulus) – complex viscoelastic behaviour (complex modulus – vector sum of moduli) - Soak with honey – higher complex modulus Rheological behaviour of cosmetic ingredients/finished products ㄴ semisolids creams, ointments (non-Newtonian, shear-thinning) Viscoelastic Behaviour Viscoelastic behaviour = viscous + elastic - Viscous behaviour: materials that flow – liquids - Elastic behaviour: structured materials that deform reversibly – solids - Viscoelastic behaviour: structured liquids which exhibit both viscous & elastic properties – e.g. polymer melts, polymer gels, creams Oscillation Measurement Types rheological measurement on suspension Amplitude sweep Two suspensions – one sample remains as a continuous phase and the other produces a supernatant layer A longer LVR enables the sample to ‘absorb’ a broader range of deformations before the structure breaks down Note that the magnitude of storage modulus is not necessarily related to product stability - Identify linear viscoelastic region - Measures inherent structure - Dispersion/suspension stability Frequency sweep - Unique fingerprint - Shows relative process time behaviour - When G’ > G’’ – elastically dominated + behaves like a solid - When G’ < G’’ – viscously dominated + behaves like a liquid - liquid soaps, gels, hydrogel films pressure sensitive adhesives X Temperature sweep Time experiment (e.g. thixotropic measurement) Viscoelasticity measurements – Creep test characterisation Application of constant stress (σ) over extended period of time t, and monitoring of the resulting strain Applied stress should be low so as not to destruct internal structure of material but high enough to cause movement Þ apply the stress take the stress out and see what happens The viscoelastic material stores some of the energy and dissipates (loses) the rest in the form of viscous flow. When stress is removed, the stored energy is recovered, in an attempt to restore the “rest state” Creep compliance J (Pa-1) = Strain / Stress J=g/s Creep compliance curve (creep compliance versus time) can be described by Burgers combined model Creep curve X - AB: immediate elastic response - BC: viscoelastic response - CD: steady state viscous (Newtonian) response - DE: elastic recovery = AB - EF: viscoelastic recovery = BC - Part of the structure cannot be recovered due to the lost energy during the viscous flow CD