Paper Production and Properties PDF
Document Details
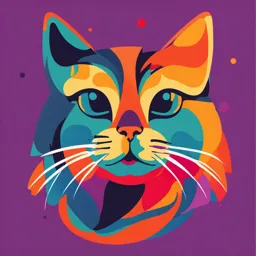
Uploaded by EnjoyableArgon
Tags
Summary
This document provides an overview of the paper production process, from the initial gathering of raw materials to the final product. It covers different types of paper, including softwood and hardwood pulps, and the various processes involved.
Full Transcript
Paper A thin material produced by pressing together most fibers of cellulose pulp derived from wood, rags, grasses, and drying them into flexible sheets Who has the biggest paper market share? Packaging - 50% When and where was the first paper making process documented? China - A.D 105 What is paper...
Paper A thin material produced by pressing together most fibers of cellulose pulp derived from wood, rags, grasses, and drying them into flexible sheets Who has the biggest paper market share? Packaging - 50% When and where was the first paper making process documented? China - A.D 105 What is paper derived from? Papyrus, Ancient Greek for the Cyperus papyrus plant Paper consists of? Pulp: mechanical pulp, chemical pulp, recovered pulp Additives: bleaching agents, fillers, sizing agents Colourants: dyes and inks Pulp A lignocellulosic fibrous material prepared by chemically or mechanically separating cellulose fibres from wood, fiber crops, waste paper, or rags Wood pulp Cellulose (40-50%)- source of fibre, what we want to extract from wood pulp for papermaking Lignin (15-30%)- what we want to remove from wood pulp for papermaking Hemicellulose (15-25%) Cellulose fiber Fibres made with ethers or esters of cellulose The most abundant organic polymer on Earth Lignin Makes wood stiff and trees stand upright Acts as a glue to bind the cellulose fibres together Helps to protect the wood from pests and other damage What happens to paper with lignin when exposed to air and sunlight? Eventually turns paper yellow because of oxidation The exposure of lignin to air and sunlight is what turns paper yellow Softwood (Needle Wood) Pulp Larch, red pine, spruce, and etc 35% Softwood Softwood fiber is long & thin (more preferable) Hardwood pulp (Broadleaf Wood) Pulp Birch, maple, oak and etc 65% Hardwood Hardwood fiber is short & thick (more cheaper) Lignin content of hardwood is less than softwood Paper character of softwood pulp Good flexibility, high folding strength, good tensile strength, and printability Paper character of hardwood pulp Loose, with strong absorptivity and high opaqueness, high thickness high stiffness What is more expensive? Softwood or hardwood Softwood Mechanical pulp Have short fibers and produces weak paper The mechanical pulping does not remove the lignin The lignin causes the paper produced to turn yellow and become brittle over time The yield is very high (>95%) Types of mechanical pulp Groundwood pulp and Thermomechanical pulp Chemical pulp (also known as wood-free papers) To make pulp from wood, chemical pulping process separates lignin from cellulose fibers Preserves the length of the cellulose fibers Do not contain lignin (or very low amount), which deteriorates over time Types of chemical pulp Kraft pulp, Sulfite pulp, and Soda pulp Recycled pulp Created from paper that was recovered for recycling Depending on the final product, the recovered paper may be further process to remove inks, coatings sizing adhesives or other impurities (process called de-inking) Recovered paper pulp can be used to produce new products (made entirely of recovered content or from a blend of recovered paper pulp & pulp from wood chips) Bleaching agents (chlorine, hydrogen peroxide or sodium peroxide) Used to get precise shade of white that manufacturer wants In the production of white paper, the wood pulp is bleached to remove any colour from the trace amounts of lignin that was not extracted in the chemical pulping process Fillers (china clay, chalk, calcium, etc) Added to increase mass of the paper and give it a stronger structure Used to lower the consumption of more expensive binder material Used to improve some properties of the paper such as brightness and opacity Sizing agents Used to reduce the paper's tendency when dry to absorb liquid Provide water resistance Added to make the structure firm and stronger Provide a more consistent, precise printing surface and better printability smoothness, abrasiveness and creasibility Internal sizing Applied directly into the pulp in the papermaking process External sizing Applied externally (also called surface, or tub sizing), after the paper has to be formed, pressed, and dried Wet-strength additives (Polyamide-epichlorohydrin (PAE), paraformaldehyde (UF), or melamine formaldehyde MF) Wet strength additives ensure it retains its strength when it gets wet E.g coffee filter paper-contain wet strength polymer so to withstand hot water soaking Colourants - Dyes and Inks Used to create paper of specific colour Paperboard Thick paper-based material Generally thicker overm (0.3mm) than paper Paper with a grammage above 250g/m2 (ISO 2018), but there are some exceptions Single or multi-ply Certain superior attributes such as foldability, and rigidity Commonly used in the packaging industry; but not in the publishing industry What does the ISO 216 do? Determines the dimensions of various Paper Sizes Outside North America (commonly) What are ISO A and ISO B- most common for? ISO A and ISO B- the most common in general for commercial printing Typically have the same aspect ratio (1 to 1.41), from the largest to smaller size ANSI format compared to ISO The 'letter' size is 8.5" x 11" (215.9mmx 279.4mm) and is slightly shorter and wider than the ISO's A4 size (8.27"x11.69"(210mmx297mm) Caliper Paper thickness Measures in either Micron or Points Typical paper caliper in publishing 0.0025~0.012 inches Consistency of caliper Variations in caliper within a single paper roll cause problems in feeding web offset presses and can cause web breaks North American/Imperial measurement of paper - M Weight Weight in pounds of 1000 sheets of a specified size (given size) North American/Imperial measurement of paper - Basis Weight Weight in pounds of 500 sheets (a ream) of basic size Metrics Grammage: weight in grams per 1m² gsm Apparent density Basis weight divided by the caliper (or, grammage divided by the paper thickness) Paper Bulk Bulk is the inverse of paper density The ratio of paper caliper to its weight A measurement of paper that often determines what type of printers can handle it In book production, bulk is a factor in determining book size Machine Direction (MD) (horizontal) The direction that is parallel to the direction of the movement of the forming wire on a paper making machine It is the forward movement of the forming paper web on the forming wire that induces the paper's grain Cross Machine Direction (CD) (vertical) The direction perpendicular to the machine direction is known as the cross-machine direction, or the cross-grain direction Grain Long The grain runs parallel to the long edge of the paper Grain Short The grain runs parallel to the short edge of the paper Tearing Test The tear pattern will be straight when parallel to the grain and jagged across the grain Bending Test (slump test) Parallel to the grain direction the resistance is far less than against the grain Moisture Test The curl indicating the paper grain direction Folding It will fold easier parallel to the grain direction than against the grain Paper Stiffness The ability for a sheet of paper to resist bending Influenced by the thickness and basis weight of the sheet Stiffness can vary from machine direction (MD) to cross machine direction (CD) Typically stiffer across the grain due to the resistance of the paper fibers to bend across themselves Type of paper stiffness tester Gurly stiffness tester (TAPPI T543) Tensile Strength The ability of the paper to resist tear when a tensile load (a load parallel to the paper) is applied Greater in machine direction than in cross direction Type of tensile strength test Tensile strength test (TAPPI T494) To find out how resistant paper is to a web break Calculated with the force per unit width and express as N/m Factors affecting to the tensile strength of paper Length and bonding of fiber Degree of fiber refining Direction of the fiber Paper formation Refers to the uniformity and distribution of the fibers within a sheet of paper How is paper formation measured? Measures that uniformity of the sheet structure and orientation of fibers using an optical test Ex. Poor basis weight uniformity, thick and thin spots, equals poor formationn Two main factors that affect paper formation Quality of the wood pulp and "ingredients" used Speed of the moving wire Good Formation: uniform fiber alignment Poor Formation:c fibers are blotchy and uneven Opacity The degree to which light is prevented from travelling through a paper How well a paper prevents the image on the backside of a sheet showing through to the front How can opacity be increased? Increased with fillers, pigments, or even coatings When is opacity important? Very important when projects require thinner paper stocks and both sides of the sheet are being printed Brightness and whiteness Internally whiteness is the most commonly used measure as defined by the CIE (Internally Commission on Illumination) (i.e CIE D65 Illumination) In North America the most commonly seen measure in Brightness as defined by the TAPPI (Technical Association of the pulp and paper industry) (i.e. TAPPI T452) Paper whiteness Measures the reflective properties of the paper across the entire visible spectrum of light (approximately 380nm-720nm) A perfect reflecting, non-fluorescent white material measures 100 whiteness Paper Brightness Measures the amount of light reflected from the surface of paper at one specific wavelength (457nm) in the blue region of the spectrum Effect of UV brighteners (obstacle brightening agents, OBAs) Roughness and Smoothness Refers to the amount of evenness the surface of the paper possesses What can enhanced smoothness do? key word: productivity !! - Reduces the amount of abrasion that is caused when it passes through the printing device - Cause fewer printer jams, resulting in less productivity - Allows to print more pages on the same cartridge - Provides better ink receptivity Gloss Gloss measures the amount of light reflected from the sheet surface at an angle equal to the incident light Glossier paper Most significant portion of the incident light is reflected directly Only a small part is reflected diffusely Gloss - TAPPI T480 Measuring the specular gloss of paper at 75 degree angle (15 from the plane of paper) Suitable for low-to-high glossy paper Gloss - TAPPI T653 Measuring the specular gloss of paper at 20 degree angle Suitable for highly varnished, waxed paper Coated paper A coated paper is produced at the paper mill with a smooth surface A coated paper can have a range of reflectively values including dull, matte, silk, satin or glossy Coating Finishes A coating finish is a clear layer applied after the ink is printed on the paper It is used to enhance the visual appeal of printed graphics or to add durability and protection to the printing Paper coating is used to influence paper in regards to: Image clarity and ink absorbency Brightness Colour Smoothness and Roughness Structure Resistance to dirt and moisture Types of coating Matte: Works well with handwriting and multicolor printing, but may not look good enough with color photos Silk/Dull coat: Also known as suede or velvet Gloss Coat: Best for reproducing images of hard or shiny objects Types of coating pigments Clay Titanium Dioxide Satin White Calcium Carbonate Plastic Pigments Talc Pigments - Clay Smoothness , gloss, ink holdout Pigments - Calcium Carbonate Opacity, brightness, ink absorbency Pigments - Titanium dioxide Brightness and opacity Binders Added to increase the adhesion of the particles of pigment to each other and to the paper fibers Natural Sources: Starch Synthetic Sources: styrene-butadiene and vinyl acrylic lattices Printability The extent to which materials used in printing and contribute to the required or expected level of quality - thus Print Quality! A term describing the interrelationships of paper properties that result in accurate, high quality printed images Factors affecting printability - Surface Properties Smoothness Ink Absorbency Cleanliness Gloss Finish Factors affecting printability - Structural Properties Thickness Weight Dimensional stability Runnability The extent to which materials used go through a given printing process without causing problems, stoppages, or delays - thus Productivity! Considerations of a paper's runnability - Cleanliness of the surface Loose fibers cause problems such as piling on the blanket Considerations of a paper's runnability - How well particles of fillers and coatings remains bonded to the paper Loose filler and coating particles can contaminate the chemistry of an offset printing press Considerations of a paper's runnability - How well a paper maintains its dimensional stability Changes in size due to changes in moisture content can affect not only the quality of the printed image, but also cause feeding problems Ex. Curling, wavy edges, and chemical composition Moisture contents of paper Most papers are designed to be 45%-55% in a 72F environment Regardless the type of printer, humidity affects paper Low humidity can do what to paper? May cause static electricity = leads to jams and misfeeds High humidity can do what to paper? Dampens the paper = causes jams as well as diminished print quality End Use The extent to which materials used in printing conform to unique or specific requirements of the end user or end use application Considerations for end use Grammage Caliper Brightness Opacity Glossy Smoothness Printing Methods Sustainability Non-fibrous substrates - Synthetic paper Look similar to paper, but made of a plastic Usually made of polyester plastic No fibre No grain direction High strength, smoothness Ink Holdout Dimensional stability Suitable for security applications I.e Kimdura, Yupo, Tvek (remember this !!) Non-fibrous substrates - Film Extruded from plastic Polyester, polypropylene, polyethylene, polyvinyl chloride Large-format, inkjet printing, flexography Non-fibrous substrates - Foils Think membranes of metal (aluminum) Metal laminated to plastic Used for premium adhesive labels, food, packages Excellent barrier properties Ink A liquid or paste containing dyes and pigments Printing inks may be: Paste inks (offset litho, letterpress) Liquid pourable inks (flexo, gravure, screen) Specialty inks Why do we need to know about printing ink? Inks transforms paper into print Beautiful and special effects Ink can have a significant cost Colour is critical in most jobs, → and ink creates colour Problems are often due to ink, and we need to be able to anticipate and solve problems Pigments Finely ground solid particles which give ink its colour. May be organic or inorganic. (Difference between pigments and dyes) Vehicles (AKA.Binder) The liquid portion of the ink which holds and carries the pigment. Vehicle provides workability and drying products, and binds the pigments to the substrate. Driers Salts of cobalt and manganese (both metals) which speed oxidation and drying Additives Includes dryers and other additives which affect tack, viscosity, setoff, rub resistance of other properties Body Consistency, stiffness or softness of inks Ink consistency vary widely from very stiff inks for letterpress to very soft, fluid inks for newsprint and flexo Viscosity Measure of the flow characteristics of soft or fluid inks Stiff inks have a false body that is called thixotropy Different types of viscometers are necessary for different viscosity ranges of inks Ex. liquid (flexo) vs paste (litho) ink