UG Cable Notes PDF
Document Details
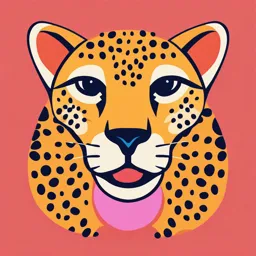
Uploaded by SeamlessOcean
KMCT
Tags
Summary
This document provides a detailed overview of underground cables, covering their construction, materials, types, joints, and testing procedures. It is geared towards professionals in the electrical field.
Full Transcript
Electrical Related Theory for Exercise 1.3.30 - 1.3.33 Electrician - Wires - Joints - Soldering - UG cables Under ground (UG) cables - construction - materials - types - joints - testing Objectives: At the end of this lesson you shall be able to define UG cable explain...
Electrical Related Theory for Exercise 1.3.30 - 1.3.33 Electrician - Wires - Joints - Soldering - UG cables Under ground (UG) cables - construction - materials - types - joints - testing Objectives: At the end of this lesson you shall be able to define UG cable explain the construction of UG cables list and state the insulating materials used in cables list out and state the types of UG cables used for 3 phase service state the types of cable joints and laying methods expalin the faults and testing procedures of cables. Under Ground (UG) cables at high voltage transmission of electric power for same moderate distances. “A cable so prepared that it can withstand pressure and can be installed below the ground level and normally two General construction of UG cables or more conductors are placed in an UG cablewith sepa- An underground cable essentially consists of one or more rate insulation on each conductor” conductors covered with suitable insulation and surrounded by a protecting cover. Electric power can be transmitted (or) distributed either by over-head lines system or by underground cable system. Necessity requirements for cables The underground cable system have several advantage, In general, a cable must fulfill the following necessary such requirements. Advantages i The conductor used in cables should be tinned stranded Less chance to damage through storms or lightning. copper or aluminum of high conductivity. (Strands of cable gives flexibility and carry more current). Low maintenance cost. ii The size of the conductor should be selected, so that the Less chances of fault. cable carries the desired load current without overheating Not affected by man- made problems like sabotage, and limits the voltage drop to a permissible value. strike etc. iii The cable must have proper thickness of insulation to Voltage regulation in UG cables system is much ensure the safety and reliability for the designed voltage. better, because they have less inductive losses. General construction of UG cables Better general appearance of area compared to O.H iv The cable must be provided with suitable mechanical lines. protection so that it may withstand the rough use in Disadvantages laying it. However, their major draw back / disadvantages are v The materials used in cables should be with complete chemical and physical stability throughout. Initial cost of UG cable system is heavy. The cost of joints are more. Introduce insulation problems at high voltages compared with O.H lines. For these reasons UG cables are employed where it is impracticable to use O.H lines like (i) thickly populated areas, where municipal authorities prohibit O.H lines for the reason of safety. ii Around plants iii In Substations, iv Where maintenance conditions do not permit the use Construction of Cables of O.H construction. Fig 1 shows the general construction of a 3-core cable. The UG cable were used many years for distribution of The various parts are: electric power in congested urban areas to low and medium voltages. Then with improvement and development i) Cores or conductors: A cable may have one or more of design, the manufactures have made it possible to use than one core (conductor) depending upon the type of service for which it is intended. For instance, the 3- 128 Copyright Free under CC BY Licence conductor cable shown in Fig 1 is used for 3-phase In case the insulating material is hygroscopic, it must service. The conductors are made of tinned copper or be enclosed in a waterproof covering like lead sheath. aluminium and are usually stranded in order to provide v) Non-inflammable flexibility to the cable and having high conductivity. vi) Low cost compared to O.H. system. ii Insulation: Each core or conductor is provided with a suitable thickness of insulation, the thickness of layer vii) Unaffected by acids and alkalies to avoid any chemical depending upon the voltage to be withstood by the action. cable. The commonly used materials for insulation The type of insulating material to be used depends upon are impregnated paper, varnished cambric or rubber the purpose for which the cable is required and the quality mineral compound. Petrolium jelly is applied to the of insulation to be aimed at. layers of the cambric to prevent damage. The principal insulating materials used in cables are iii Metallic sheath: In order to protect the cable from moisture, gases or other damaging liquids (acids or (i) Rubber alkalies) in the soil and atmosphere, a metallic sheath (ii) Vulcanized India rubber of lead or aluminium is provided over the insulation as shown in Fig 1. The metallic sheath is usually a lead (iii) Impregnated paper or lead alloy. (iv) Varnished cambric and iv Paper Belt: Layer of imprignated paper tape is wound (v) Polyvinyl chloride. round the grouped insulated cores. The gap in the cores is filled with fibrous insulating material (jute etc.) 1 Rubber: Rubber may be obtained from milky sap of tropical trees or it may be produced from oil products. It v Bedding: Over the metallic sheath is applied a layer of has relative permittivity varying between 2 and 3, dielectric bedding which consists of a fibrous material like jute strength is about 30 KV/mm and resistivity of insulation is or hessian tape. The purpose of bedding is to protect 1017 Ω cm. the metallic sheath against corrosion and from mechanical injury due to armouring. It suffers from some major drawbacks viz readily (i) absorbs moisture vi Armouring: Over the bedding, armouring is provided which consists of one or two layers of galvanized steel (ii) maximum safe temperature is low (about 380 C) wire or steel tape. Its purpose is to protect the cable (iii) soft and liable to damage due to rough handling from mechanical injury while laying it and during the and ages when exposed to light. course of handling. Armouring may not be done in the case of some cables. Therefore, pure rubber cannot be used as an insulating material. vii Serving: In order to protect armouring from atmospheric conditions, a layer of fibrous material (like jute) similar 2 Vulcanised Indian Rubber (V.I.R.) : It is prepared by to bedding is provided over the armouring. This is known mixing pure rubber with mineral matter such as zinc oxide, as serving. red lead etc. and 3 to 5% of sulphur. The compound so formed is rolled into thin sheets and cut into strips. The It may not be out of place to mention here that bedding, rubber compound is then applied to the conductor and is armouring and serving are only applied to the cables for heated to a temperature of about 150°C. The whole, the protection of conductor insulation and to protect the process is called vulcanization and the product obtained metallic sheath from mechanical injury. is known as Vulcanized Indian Rubber. Insulating materials for cables Advantages: Vulcanised India rubber has greater mechanical strength, durability and water resistant property The satisfactory operation of a cable depends to a great than pure rubber. extent upon the characteristics of insulation used. Therefore, the proper choice of insulating material for cables Disadvantages: Its main drawback is that sulphur reacts is of considerable importance. In general, the insulating quickly with copper. So, cables using VIR insulation must material used in cables should have the following properties: have tinned copper conductor. The VIR insulation is generally used for low and moderate voltage cables. i) High insulation resistance to avoid leakage current. 3 Impregnated paper: It consists of chemically pulped ii) High dielectric strength to avoid electrical breakdown paper made from wood chippings and impregnated with of the cable. some compound such as paraffinie or naphthenic material. iii) High mechanical strength to withstand the mechanical Aadvantages: handling of cables. (i) Low cost iv) Non-hygroscopic i.e. it should not absorb moisture from (ii) Low capacitance air or soil The moisture tends to decrease the insulation (iii) High dielectric strength and resistance and hastens the breakdown of the cable. (iv) High insulation resistance. Electrical : Electrician (NSQF LEVEL - 5) - Related Theory for Exercise 1.3.30 - 1.3.33 129 Copyright Free under CC BY Licence Disadvantages: A cable may have one or more than one core depending (i) The paper is hygroscopic and even if it is impregnated upon the type of service for which it is intended. It may be with suitable compound (i) single-core (ii) two-core (iii) three-core (iv) four-core etc. For a 3-phase service, either 3-single core cables or three- (ii) It absorbs moisture and thus lowers the insulation core cable can be used depending upon the operating resistance of the cable. voltage and load demand. For this reason, paper insulated cables are always provided Fig 2 shows the constructional details of a single-core low with some protective covering and are never left unsealed. tension cable. The cable has ordinary construction because If it is required to be left unused on the site during laying, the stresses developed in the cable for low voltages (upto its ends are temporarily covered with wax or tar. 6600 V) are generally small. It consists of one circular Since the paper-insulated cables have the tendency to core of tinned stranded copper (or aluminium) insulated absorb moisture, they are used where the cable route has by layers of impregnated paper. The insulation is a few joints. For instance, they can be profitably used for distribution at low voltages in congested areas where the joints are generally provided only at the terminal apparatus. However, for smaller installations, where the lengths are small and joints are required at a number of places, VIR Cables will be cheaper and durable than paper insulated cables. 4 Varnished cambric: It is a cotton cloth impregnated and coated with varnish. This type of insulation is also known as empire type. The cambric is lapped on to the conductor in the form of tape and its surface is coated with petroleum jelly compound to allow for the sliding of one turn over another as the cable is bent. As the varnished surrounded by a lead sheath which prevents the entry of cambric is hygroscopic, therefore, such cables are always moisture into inner parts. In order to protect the lead sheath provided with metallic sheath. Its dielectric strength is from corrosion, an overall serving of compounded fibrous about 4 KV/mm and permittivity is 2.5 to 3.8. material (jute etc.) is provided. Single-core cables are not usually armoured in order to avoid excessive sheath losses. 5 Polyvinyl chloride (PVC): This insulating material is The principal advantages of single-core cables are simple a synthetic compound. It is obtained from the construction and availability of large copper section. polymerization of acetylene and is in the form of white powder. For obtaining this material as a cable insulation, Cables for 3-Phase Service it is compounded with certain materials known as In practice, underground cables are generally required to plasticiser which are liquids with high boiling point. deliver 3-phase power. For the purpose, either three-core cables or three single core cables may be used. For Advantages: voltages upto 66 KV, 3-core cable (i.e. multi-core (i) It has high insulation resistance construction) is preferred due to economic reasons. The following types of cables are generally used for 3-phase (ii) Good dielectric strength service. (iii) Mechanical toughness over a wide range of temperature. 1. Belted cables – upto 11 KV This type of insulation is preferred over VIR in extreme 2. Screened cables – from 22 KV to 66 KV environmental conditions such as in cement factory or chemical factory. 3. Pressure cables – beyond 66 KV Classification of cables 1. Belted cables Cables for underground service may be classified in two ways according to (i) the type of insulating material used in their manufacture (ii) the voltage for which they are manufactured. However, the later method of classification is generally preferred as (i) Low-tension (L.T) cables – upto 1100 V (ii) High-tension (H.T) cables – upto 11,000 V (iii) Super-tension (S.T cables – from 22 KV to 33 KV (iv) Extra high-tension (E.H.T) cables – from 33 to 66 KV (v) Extra super voltage cables – beyond 132 KV 130 Electrical : Electrician (NSQF LEVEL - 5) - Related Theory for Exercise 1.3.30 - 1.3.33 Copyright Free under CC BY Licence These cables are used for voltages upto 11 KV but in The S.L type cables have two main advantages over H- extraordinary cases, their use may be extended upto 22 type cables. KV. Fig 3 shows the constructional details of a 3-core a) The separate sheaths minimize the possibility of core- belted cables. The cores are insulated from each other to-core breakdown. by layers of impregnated paper. b) Bending of cables become easy due to the elimination Another layer of impregnated paper tape called paper belt of overall lead sheath. is wound round the grouped insulated cores. The gap between the insulated cores is filled with fibrous insulating The disadvantage is that the three lead sheaths of S.L. material (jute etc.) The belt is covered with lead sheath to cable are much thinner than the single sheath of H-cable protect the cable against ingress of moisture and mechanical injury. The belted type construction is suitable only for low and medium voltages as the electrostatic stresses developed in the cables for these voltages are more or less radial i.e. across the insulation. However, for high voltages (beyond 22 KV), the tangential stresses also become important. 2. Screened cable These cables are meant for use upto 33 KV but in particular cases their use may be extended to operating voltages upto 66 KV. Two principal types of screened cables are H-type cable and S.L. type cables. Limitations of solid type cables (i) H-type cables. This type of cable was first designed All the cables of above constructions are referred to as by H. Horchstadter and hence the name. Fig 4 shows the solid type cables because solid insulation is used and no constructional details of a typical 3-core, H-type cable. gas or oil circulates in the cable sheath. The voltage limit Each core is insulated by layers of impregnated paper. for solid type cables is 66 KV due to the following reasons: The insulation on each core is covered with a metallic screen which usually consists of a perforated aluminium a. As a solid cable carries the load, its conductor foil. temperature increases and the cable compound (i.e. insulating compound over paper) expands. This action stretches the lead sheath which may be damaged. b. When the load on the cable decreases, the conductor cools and a partial vacuum is formed within the cable sheath. If the pinholes are present in the lead sheath, moist air may be drawn into the cable. The moisture reduces the dielectric strength of insulation and may eventually cause the breakdown of the cable. c. In practice, voids are always present in the insulation of a cable. Modern techniques of manufacturing have resulted in void free cables. However, under operating conditions, the voids are formed as a result of the differential expansion and contraction of the sheath and The cable has no insulating belt but lead sheath, bedding, impregnated compound. armouring and serving follow as usual. As all the four screens (3 core screens and one conducting belt) and the 3. Pressure cables lead sheath are at earth potential. For voltages beyond 66 KV, solid type cables are unreliable Advantages: because there is a danger of breakdown of insulation due to the presence of voids. When the operating voltages are The posibility of air pockets or volds in the dielectric is greater than 66 KV, pressure cables are used. In such eleminated cables, voids are eliminated by increasing the pressure of The metalic screen increase the heat dissipating power compound and for this reason they are called pressure of the cable cables. Two types of pressure cables viz oil filled cables and gas pressure cables are commonly used. (ii) S.L. type cables Fig 5 shows the constructional details of 3-core S.L (separate lead) type cable. It is (i) Oil filled cables. In such type of cables, channels of basically H-type cable but the screen round each core ducts are provided in the cable for oil circulation. The oil insulation is covered by its own lead sheath. There is no under pressure (it is the same oil used for impregnation) overall lead sheath but only armouring and serving are is kept constantly supplied to the channel by means of provided. Electrical : Electrician (NSQF LEVEL - 5) - Related Theory for Exercise 1.3.30 - 1.3.33 131 Copyright Free under CC BY Licence external reservoirs placed at suitable distances (say 500 m) along the route of the cable. Oil under pressure compresses the layers of paper insulation and is forced into any voids that may have formed between the layers. Due to the elimination of voids, oil- filled cables can be used for higher voltages, the range being from 66 KV upto 230 KV. Oil-filled cables are of three types viz. (i) Single-core conductor channel (ii) Single-core sheath channel and Advantages (iii) Three-core filler-space channels. (a) Formation of voids and ionization are avoided. (i) Single-core Conductor channel (b) Allowable temperature range and dielectric strength Fig 6 shows the constructional details of a single-core are increased. conductor channel, oil-filled cable. The oil channel is formed at the centre by stranding the conductor wire around a (c) If there is leakage, the defect in the lead sheath is at hallow cylindrical steel spiral tape. The oil under pressure once indicated and the possibility of earth faults is is supplied to the channel by means of external reservoir. decreased. As the channel is made of spiral steel tape, it allows the Disadvantages oil to percolate between copper strands to the wrapped insulation. (a) High initial cost and complicated system of laying The oil pressure compresses the layers of paper insulation (ii) Gas pressure cables. The voltage required to set up and prevents the possibility of void formation. The ionization inside a void increases as the pressure is disadvantage of this type of cable is that the channel is at increased. Therefore, if ordinary cable is subjected to a the middle of the cable which is at full voltage w.r.t earth, sufficiently high pressure, the ionization can be altogether so that a very complicated system of joints is necessary. eliminated. At the same time, the increased pressure produces radial compression which tends to close any voids. This is the underlying principle of gas pressure cables. Fig 9 shows the section of external pressure cable designed by Hockstadter, Vogal and Bowden. The construction of the cable is similar to that an ordinary solid type except that it is of triangular shape and thickness of lead sheath is 75% that of solid cable. The triangular section reduces the weight and gives low thermal resistance but the main reason for triangular shape is that the lead sheath acts as a pressure membrane. The sheath is protected by a thin (ii) Single-core sheath channel (Fig 7) metal tape. The cable is laid is a gas-tight steel pipe. In this type of cable, the conductor is solid similar to that of solid cable and is paper insulated. However, oil ducts are provided in the metallic sheath. The pipe is filled with dry nitrogen gas at a pressure of 12 to 15 atmospheres. The gas pressure produces radial compression and closes the voids that may have formed between the layers of paper insulation. Advantages: In the 3-core oil-filled cable shown in Fig 8, the oil ducts are located in the filler space. These channels are a) Cables can carry more load current composed of perforated metal-ribbon tubing and are at b) Operate at higher voltages than a normal cable. earth potential. 132 Electrical : Electrician (NSQF LEVEL - 5) - Related Theory for Exercise 1.3.30 - 1.3.33 Copyright Free under CC BY Licence c) Maintenance cost is small and the nitrogen gas helps in quenching any flame. Disadvantages: The overall cost is very high. Further the cables are also classified according to their insulation system as under: PVC insulated cables (Poly vinyl chloride) MI cables (Mineral insulation) PILC cables (Paper insulated lead covered) XLPE cables (Cross linked poly ethylene) PILCDTA cables (Paper insulated lead covered double tape armoured) The specification of underground cables The cables shall carry the following information either labelled or stenciled on the reel or drum or container. 1 Reference to the Indian Standard; for example Ref. IS 694-1977. 2 Manufacturer’s name, brand name or trademark. The choice of any of the systems given above depends on 3 Type of cable and voltage grade. (i) The actual installation conditions 4 Number of cores. (ii) Inital cost of laying 5 Nominal cross-sectional area of conductor. (iii) Maintenance and repair charges 6 Cable code. (iv) Deisred care in replacement of any cable or adding 7 Colour of cores (in case of single core cables) new cables for the future. 8 Length of cable on the reel, drum or coil As far as the possible cable should be laid along the roads 9 Number of lengths on the reel, drum or coil (if more and streets. Power and communication cables should than one). cross at right angles. 10 Direction of rotation of drum (by means of arrow). During the preliminary stages of laying the cable, consideration should be given to a proper location of the 11 Approximate gross weight. joints position so that when the cable is actually laid, the 12 Country of manufacturing. joints are made in the most suitable places. 13 Year of manufacture. As far as possible water logged locations, carriage ways, pavements, proximity to telephone cables, gas or water Fig 10 shows the paper insulated 3 phase 3 ½ core cable. mains in accessible places, ducts pipes, racks etc shall be avoided for joint position. UG cables laying method The reliability of the underground cable (UG) installation depends upon the proper laying and attachment of fittings (i.e) cable and boxes, joints, branch connectors etc. Methods of laying of UG cables The following are the methods of laying underground cables 1 Laying direct in ground 2 Laying in ducts 3 Laying on racks in air. 4 Laying on racks inside a cable tunnel. 5 Laying along buildings or structures. Electrical : Electrician (NSQF LEVEL - 5) - Related Theory for Exercise 1.3.30 - 1.3.33 133 Copyright Free under CC BY Licence Laying direct in ground: For cable of rating This method involves digging a trench in the ground and Ref. Upto 1.1 kV Exceeding 1.1 kV laying cable(s) on a bedding of minimum 75 mm riddled soil A 75 120 or sand at the bottom of the trench, and covering it with additional riddled soil or sand of minimum 75 mm and A1 (75+n1x30) (120+n1x30) protecting it by means of tiles, bricks or slabs. B 8 8 Depth: The desired minimum depth from ground surface to C 17 17 the top of cable is as follows: D 35 35 a) High voltage cables, 3.3 KV to 11 KV rating : 0.9 m. D1 (30+n2x20) (30+n2x20) b) High voltage cables, 22 KV, 33 KV rating : 1.05 m. E 15 15 c) Low and medium voltage and control cables : 0.75 m. n1 = Number of additional cables in vertical formation. d) Cables at road crossings : 1.00 m. n2 = Number of additional cables in horizontal formation. e) Cables at railway level crossings (measured from bottom of sleepers to the top of pipe) : 1.00 m. For road crossings cast iron, or 2nd class RCC pipes or M.S/G.I. Pipe of medium class having an appropriate Width: The width of a trench for laying a single cable should diameter should be laid during construction of the road to be minimum 35 cm. When more than one cable is laid in avoid damage to the road later on. The top surface of the the same trench in horizontal formation, the width of the pipe should be at a minimum depth of 1m. Pipes provided trench shall be so increased that the inter-axial spacing for entry to a building shall slope upward to prevent entry of between two cables is 20 cm. water into the building. After laying of the cable they should Clearance from the terminal cable to the sides of a trench be sealed. should be 15 cm. Advantages Cable is protected by sand or layer of brick as shown in 1 It is a simple and less costly method. Fig 1a. Bricks should be second class bricks of a size not less than 20 cm x 10 cm x 10 cm and laid for full length for 2 It gives the best conditions for dissipating the heat one cable (bricks to be laid breadthwise). generated in the cables. When more than one cable is to be laid in the same trench, 3 It is a clean and safe method as the cable is invisible and this protective covering shall extend atleast 5 cm. over the free from external disturbances. sides of the end cables. An alternative to this covering can Disadvantages be earth ware or R.C.C. or fire-bricks of peaked covers section as shown in Fig 1b. 1 The extension of load is possible only by a complete new excavation which may cost as much as the original work. 2 The alterations in the cable network cannot be made easily. 3 The maintenance cost is very high. 4 Localisation of fault is difficult. 5 It cannot be used in congested areas where excavation is difficult. Drawing the cables into duct pipes: When drawing the cables through ducts, lack of space in the drawing pits usually restricts the distance from the cable drum to the duct mouth. It is essential that the direction of curvature of the cables is not reversed as it enters the duct. If the cable drum is on the same side of the drawing pit, as shown in Fig 2, this condition is fulfilled. It is good practice to leave about 3 metres of cable spare in a loop formation near poles and joints, so that in case joint fails, this additional cable comes to rescue. Cable should be laid 0.4 metre away from water and power mains. 134 Electrical : Electrician (NSQF LEVEL - 5) - Related Theory for Exercise 1.3.30 - 1.3.33 Copyright Free under CC BY Licence Precautions while handling cables 1 Prevent the cable from dragging on the floor. Advantages 2 Prevent kinking of the cable. 1 Reparis, alterations or additions to the cable network 3 After laying the cable in the ducts it should be can be made without opening the ground. immediately covered or suspended. 2 As the cables are not armoured, therefore, joints Cable jointing methods: This process consists of the become simpler and maintenance cost is reduced following steps. considerably. a) Exact measurement of the cable for insulation removal. 3 There are very less chances of fault occurrence due to strong mechanical protection provided by the system. b) Removal of insulation. Disadvantages c) Replacing of the original insulation with high grade tapes and sleeves. 1 The initial cost is very high. d) Dressing the cable ends and conductor joints through 2 The current carrying capacity of the cables is reduced sleeves/split sleeves. due to the close grouping of cables and unfavourable conditions for dissipation of heat. e) Providing separators between cables. This method of cable laying is suitable for congested areas f) Fixing a cast iron or any other protective shell around where excavation is expensive and inconvenient, for once the joint and filling the joint boxes with molten bitumen the conduits have been laid, repairs or alterations can be compound. made without opening the ground. This method is generally g) Plumbing metallic sleeves or brass glands to the lead used for short length cable routes such as in workshops, sheath of the cable to prevent moisture from entering road crossing where frequent digging is costlier or impossible. the joint in case of cast iron joint boxes or tape Laying cables on racks in air: Inside buildings, industrial insulation in case of cast resin kit joint boxes. plants, generating stations, substations and tunnels, cables Straight through joints are generally installed on racks fixed to the walls or supported from the ceiling. Racks may be ladder or The emphasis should be laid on quality and selection of perforated type and may be either fabricated at the site or proper cable, cable accessories, proper jointing techniques. pre-fabricated. Considerable economy can be achieved by The quality of joint in cable should be such that, it does using standard factory made racks. The necessary size of not add any resistance to the circuit. The material and the racks and associated structure has to be worked out techniques employed in joining the cables should give taking into consideration the cable grouping and permissible adequate mechanical and electrical protection to the joint bending radii. Fig 3 shows the method of laying cables under all service conditions. The joints should further be inside a tunnel on racks. resistant to corrosion and other chemical effects. Laying cables along buildings or structures: Cables For PILC cable: For paper insulated lead sheathed can be routed inside the building along with structural cables, straight joints are made either by using sleeve elements or with trenches under floor ducts or tunnels. The joints or crimping joints up to voltage grade 11 KV. Above route of the proposed cable should be such that intersection 11 KV, compound filled copper or brass sleeves, along with with other cables will be minimum. The route should not cast iron, fibre glass protection boxes are used. subject these cables to any vibrations, damage due to heat Fig 4 shows such a joint. or other mechanical causes. All adequate precautions should be taken to protect the cables. Electrical : Electrician (NSQF LEVEL - 5) - Related Theory for Exercise 1.3.30 - 1.3.33 135 Copyright Free under CC BY Licence a) High electrical strength b) High resistance to moisture Compounding process: Heat the compound in a special bucket on firewood or charcoal fire, stir with a clean metal rod to have even melting of the compound. Check the temperature with a thermometer and heat the compound up to 180° to 190°C. Heat the sealing box to 70oC with a blow torch. Open all air The cast iron protection boxes used up to 11 KV or moulds escape plugs. Fit a heated funnel to the pouring hole. Pour used for 1.1 KV joints in cast resin joints should conform the compound carefully and evenly in 2 or 3 stages with an to the relevant Indian Standard. Above 11 KV cast resin interval between them to allow the compound to solidify. system is not yet standardized. Take care that no air bubble is trapped inside. Tee joint: These joints are to be restricted up to 11 KV. Cold pouring compound: Cold pouring is used by using These joints are made either using cast resin kits or C.I. cast resin system for PVC cable jointing. This has been boxes with or without sleeves for PILC cables and cast developed for application up to 11 KV grade cables. The resin kits for PVC and XLPE cables. (Fig 5) compound consists of a resin base and a polyamino hardener. The two component liquids are mixed at the site in accordance with the recommendation of the manufacturer. Typical epoxy straight joint for PVC cable: In this system of jointing the insulation is removed and conductors are joined. The core joints in the case of LV/MV cables should be kept apart to avoid any flash over between them. Spacers are provided between the cores for H.V. cables. No insulation is applied over the core joints. A cover earth ring is placed tight over the two cut ends of the armour and soldered to the armour wires. The two rings are then jointed Tri-furcating end connections: In order to connect UG by a copper wire and the cut ends of the armouring are bent cables to the air break switches etc. tri-furcating boxes are over the rings to have continuity of armour as earth used. They can be either cast resin type up to 1.1 KV or conductor. cast iron type for 11 KV and above. This type of box is shown in Fig 6. Sandpaper is applied to the inner sheath surface and is cleaned by using methyl chloride. The joint is enclosed by plastic mould, which is in two parts, whose ends are duly cut to match the size of cable. PVC tape is wrapped at the two places where the mould will touch the cables. The two halves are pasted together and kept clamped to avoid any air gap. The mould ends are enclosed with putty which is supplied in the joint kit. The expiry date of resin is checked and the hardener added to resin. The mixture is churned thoroughly for about 15 to 20 minutes till the colour of the mixed compound becomes grey. The mix is poured slowly into the mould taking care to avoid formation of air bubbles till the mould is filled and it comes out at the risers. Allow the joint to set for a minimum of three hours till it Method of preparing and filling compounds becomes a solid mass before charging the cable. The – Hot pouring mould may be removed, if desired. – Cold pouring Normally all the components required for joints are supplied Hot pouring compounds: A bituminous compound of as kits for various sizes of cables. melting temperature 90°C and pouring temperature 180°C Fig 7 illustrates a typical straight through and outdoor - 190°C is used for hot pouring. termination of PVC cable with epoxy resin respectively. Properties: The bituminous compound has the following properties. 136 Electrical : Electrician (NSQF LEVEL - 5) - Related Theory for Exercise 1.3.30 - 1.3.33 Copyright Free under CC BY Licence Types of cable faults and testing procedure The common faults which are likely to occur in cables are: 1. Ground fault. The insulation of the cable may breakdown causing a flow of current from the core of the cable to the lead sheath or to the earth. This is called “Ground Fault”. 2. Short circuit fault. If the insulation between two conductors is faulty, a current flows between them. This is called a “short circuit fault”. Methods for locating ground and short circuit faults. The methods used localizing the ground and short circuit faults differ from those used for localizing open circuit faults. Where (R+X) is total loop resistance formed by the sound cable and the faulty cable. When the conductors have In the case of multi core cables it is advisable, first of all, the same cross-sectional area and the same resistivity, to measure the insulation resistance of each core to earth the resistance are proportional to lengths. If l1 represents and also between cores. This enables us to sort out the the length of the fault from the test end and ‘l’ is the length core that is earthed in-case of ground fault; and to sort out of each cable. Then the cores that are shorted in case of a short circuit fault. Loop tests are used for location of ground short circuit Q faults. These tests can only be used if a sound cable I =. 2I 1 P+Q runs along with the faulty cable or cables. The loop tests work on the principle of a Wheatstone bridge. The above relation shows that the position of the fault may The advantage of these tests is that their setup is such be located when the length of the cable is known. Also, that the resistance of fault is connected in the battery the fault resistance does not alter the balance condition circuit and therefore does not effect the result. However, if because its resistance enter the battery circuit hence the fault resistance is high, the sensitivity is adversely effects only the sensitivity of the bridge circuit. However, affected. In this section only two types of tests viz., Murray if the magnitude of the fault resistance is high, difficulty and Varley loop tests are being described. may be experienced in obtaining the balance condition on account of decrease in sensitivity and hence accurate Murray Loop Test. The connection for this test are shown determination of the position of the fault may not be in Fig 8a relates to the ground fault and Fig 8b relates to possible. the short circuit fault. In such a case, the resistance of the fault may be reduced In both cases, the loop circuit formed by the cable by applying a high direct or alternating voltage, in conductors is essentially a wheatstone bridge consisting consistence with the insulation rating of the cable, on the of resistances P, Q, R and X. G is a galvanometer for line so as to carbonize the insulation at the point of the indication of balance, fault. The resistors P, Q forming the ratio arms may be decade Varley loop test. In this test we can determine resistance boxes or slide wires. experimentally the total loop resistance instead of Under balance conditions : calculating it from the known lengths of the cable and its resistance per unit length. The necessary connections for the ground fault are shown in Fig 9a and for the short X Q X Q circuit fault in Fig 9b. The treatment of the problem, in = or = R P R+X P+Q both cases, is identical. Q A single pole double throw switch A is used in this circuit. ∴X = (R + X) Switch K is first thrown to position ‘I’ and the resistance P+Q ‘S’ is varied and balance obtained. Electrical : Electrician (NSQF LEVEL - 5) - Related Theory for Exercise 1.3.30 - 1.3.33 137 Copyright Free under CC BY Licence At balance R P = X+S Q 2 R+X+S P+Q (R + X) Q − S P 2 2 = or X = X+S Q P+Q 2 Hence, X is known from the known value of P, Q, S2 from this equation and R+X (the total resistance of 2 cables) as determined from Eqn. knowing the value of X, the position of the fault is determined. Now X I X 1 = or I = 2I R+X 2I 1 R+X Where I1= length of fault from the test end and Measurement of resistance l = total length of conductor. Let the value of S for balance be S. The four arms of the Equations for murrary loop test and varley loop test are Wheatstone bridge are P, Q, R + X, S1 at balance: valid only when the cable sections are uniform throughout the loop. Corrections must be applied in case the cross- R+X P sections of faulty and sound cables are different or when = the cross-section of the faulty cable is not uniform over its S Q 1 entire length. Since temperature affects the value of resistance, This determines R + X i.e. the total loop resistance as P, corrections must be applied on this account if the Q and S1 are known. temperatures of the two cables are different. Corrections The switch K is then thrown to position ‘2’ and the bridge may also have to be applied in case the cables have a is rebalanced. Let the new value of S for balance be S2. large number of joints. The four arms of the bridge now are P, Q, R, X + S2. 138 Electrical : Electrician (NSQF LEVEL - 5) - Related Theory for Exercise 1.3.30 - 1.3.33 Copyright Free under CC BY Licence