Track Machine Manual PDF
Document Details
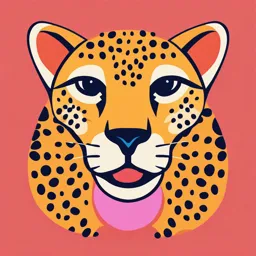
Uploaded by SolicitousOklahomaCity
Tags
Summary
This document provides details of monitoring, maintenance, and utilization of track machines. It includes data collection, reports, data entry, and validation procedures, as well as various parameters and schedules for monitoring the health and productivity of track machines.
Full Transcript
CHAPTER 11 MONITORING 1101 GENERAL - Track machines, being capital-intensive assets need track possession for working and shall be monitored on day-to-day basis at the level of division and headquarters. Both aspects of monitoring i.e. data collection & e...
CHAPTER 11 MONITORING 1101 GENERAL - Track machines, being capital-intensive assets need track possession for working and shall be monitored on day-to-day basis at the level of division and headquarters. Both aspects of monitoring i.e. data collection & entry and generation of alerts/reports have to be meticulously done to reduce the response time and ensure optimum utilization of track machines. In addition, a system of periodical meetings at different levels is required for bringing to fore the issues affecting the smooth functioning of track machines and its organization and to generate solutions to the issues. These interactions will also serve to have finger on the pulse of the organization. It is desirable to design TMS module keeping in mind above aspects so that relevant reports reach the concerning officials in the hierarchy at pre-decided times periodically. (1) Data Collection & Entry - This shall consist of creation of data for the following (a) Machine details. (b) Section wise availability of corridor blocks for each day of the week. (c) Manpower, their deployment and various competency certificates. (d) Target and deployment programme. (e) Daily machine utilization– duty hours, movement, block working and progress and important machine parameters. (f) Maintenance schedules including IOH and POH details, failures and repairs etc. (g) AMCs and other contracts, visits of service engineer. (h) Procurement of spares and consumables. (i) Issue and utilization of spares and consumables. (j) Details of unit assemblies and costly components like engines, tamping banks etc. (k) Inspections at various levels. (l) Frequency of maintenance operations like tamping, deep screening etc. (m) Costing of procurement of spares, consumables, maintenance, repair and operations. Data collection, entry and validation of different sets of data shall have authorization at various levels i.e. machine in-charge, engineering control in the division, satellite depot, zonal machine depot& its control, zonal headquarter & its track machine control and railway board. Scrutiny of data 295 entered, validation and authority for corrections at different levels has also to be designed so as to be an integral part of the data entry. (2) Generation of Reports and Alerts – The working of track machines shall be monitored by generation of various reports including exception reports and predefined alerts through software. This would consist of generation of - (a) Periodical Reports – Daily, weekly, monthly, yearly reports with an option of user specified period for a specific machine or machines types, for the jurisdiction of a SSE/AEN/DEN/division etc. including comparative positions for corresponding periods of previous spells/years. It should be possible to select the machines. (i) Stipulated and actual progress in tabular and graphical form. (ii) Blocks stipulated, demanded, granted and availed. (iii) Blocks granted within the specified corridor and outside the corridor. (iv) Position of AMCs and other contracts. (v) Maintenance and other schedules including IOH & POH and down time analysis. (vi) Utilization of consumables i.e. diesel, lube oil, hydraulic oil, grease etc. (vii) Utilization of spares and that of fast moving spares. (viii) Unit assembly and costly components. (ix) Expenditure on items like consumables, spares, unit assemblies, staff for operations, for spares and for depot working, IOH, POH etc. (x) Inspections in tabular and graphical form. (xi) Training details. (xii) Manpower detailed reports including medical and other competencies. (xiii) Costing per unit of work (fixed cost and variable costs). (xiv) Movement of machines –Intra and inter-divisional movement of machines as also inter railway movement. (xv) Health related data, service engineer visit details etc. (xvi) Deep screening chart and overdue deep screening chart. (xvii) Tamping chart and overdue tamping chart. The module shall be so designed to get these reports, machine wise, machine type wise, unit wise, division wise, and railway wise. 296 (b) Exception Reports for Management and Control at Various Levels (i) Data not entered (of different types like progress, maintenance etc.). (ii) Machines not available for work (for different reasons like schedule maintenance like IOH, POH, unit replacement, repair, movement etc.). (iii) Machines available but not worked (for different reasons like block not given, site not ready, track material not available, labour/staff not available, holiday, rest etc.). (iv) Overdue of maintenance operations like tamping, deep screening etc. (v) Overdue maintenance schedules of machines. (vi) Manpower issues such as overdue PME, refresher, competency, road learning. (vii) Repeat tamping or deep screening within user specified period. (c) Alerts on the Home page of TMS and/or Mobile based on Pre-decided Trigger Conditions (3) Periodical Meetings – Periodical review of the different aspects of machine working at appropriate levels is essential for keeping tab on the field situation and in turn for the proper functioning of system and to keep the staff informed and motivated. (a) Regular Meetings - shall be held at Zonal Depot/HQ level to monitor day-to-day progress, impediments etc. Daily meeting shall also be held at field level between machine staff and P. Way staff to avoid any communication gap and ensure quality work by the machines. It will also be useful to conduct pre-work inspection of work site by SSE/JE/TM, SSE/P.Way, SSE/TRD and SSE/S&T, as per need of the work. (b) Review Meetings (i) Fortnightly meetings of SSE/TM/I and machine staff with SSE/TM/SDI or SD (who is in-charge of fleet of machines) with his concerned staff, if any for the purpose of discussing about the health of the machine, failures of machines, safety issues etc. SSE/TM/SDI or SD will mostly hold these in the field generally during the field inspection. (ii) Monthly review meeting of SSE/SDIs with ZMD officials and respective AEN/TM/Lines with Dy.CE/TM/Line. Various issues of health of machine, progress, quality of work, failures, spares, consumables, staff, safety etc. will be discussed in this meeting, (iii) Quarterly meeting of Dy.CE/TM/Line and AEN/TM/Lines with CE/TM. Various issues of health of machine, progress, quality of work, failures, spares, consumables, staff, safety etc. will be discussed in 297 this meeting. The planning for AMC’s, procurement of spares, other proposals, infrastructural facilities, camping coaches etc. shall also be discussed. (iv) Periodic meetings should also be held by CE/TM and Dy.CE/TM with DRM and divisional officers of different departments as per the need and also at Zonal HQ with traffic officers to get co-operation for ensuring blocks, joint working, quality and progress of work. 1102 Organization for Monitoring - The offices of satellite depot, zonal maintenance depot and HQ will have a system of control set ups for data entry and communication of information for monitoring the working of the track machines. All these controls will function 24x7 as machines work in the field 24x7. (1) Track Machine Control at Headquarters– The track machine control office in the headquarter of railway shall function under the administrative control of JA Grade/Sr.Scale officer of the Track machine organization to have command and control over the units in the divisions and Zonal depot. This control office shall be manned round the clock on all 7 days of the week by staff not lower than Junior Engineer with suitable roster. EI roster shall be followed for the control staff. The control office shall be provided with railway telephone with STD facilities, DOT landline telephone with STD facilities, a fax machine, CUG mobile connection with smartphone instrument for effective communication with connected offices. A PC with printer and Internet connection (with wi-fi) for feeding of various details and monitoring, printing reports through TMS, as well as other than TMS, shall also be made available. (2) Track Machine Control at Zonal maintenance Depot (ZMD) Level – The track machine control office in the zonal maintenance depot shall function under the administrative control of JA Grade/Sr. Scale officer in-charge of the depot to co-ordinate with headquarter and other divisions, as also with the satellite depots and track machines in-charges. This control office shall be manned round the clock on all 7 days of the week by staff not lower than Junior Engineer with suitable roster. EI roster shall be followed for the control staff. Divisional control office shall be provided with Railway telephone with STD facilities, DOT landline telephone with STD facilities, a fax machine, CUG mobile connection with smartphone instrument for effective communication with connected offices. A PC with printer and Internet connection (with wi-fi) for feeding of various details and monitoring, printing reports through TMS, as well as other than TMS, shall also be made available. (3) Divisional Control – The day to day planning for deployment of machines, arranging blocks for the machines, monitoring progress of the machines and co-ordination with other departments for effective utilization of machines will be done by engineering control of the division. The present set-up of divisional control will serve this function, augmented by staff from track machine organization as required. 298 (4) Satellite Depot (SD) – An effective mechanism for SD to closely liaison with track machine in-charges and ZMD shall be put in place. Since the ZMD/SD have to respond on real time basis for any failure, breakdown etc., the officials shall have direct and real-time interaction with machine-in-charges and with ZMD and also with SD of other divisions of the zone. SD shall be provided with railway telephone with STD facilities, DOT landline telephone with STD facilities, a fax machine, CUG mobile connection with smart phone instrument for effective communication with connected offices. A PC with printer and internet connection (with wi-fi) for feeding/validating details and monitoring, printing reports through TMS, as well as other than TMS, shall also be made available. SD shall have a nominated official in the morning shift for liaison with zonal depot and machine in-charges. 1103 Functions of Divisional Control in respect of Track Machines (1) Advance planning of the daily machine works to be done. (2) Monitoring of grant of blocks for the machines. (3) To co-ordinate between the different departments in the control, machine in- charges, SD, ZMD as required; for effective utilization of machine. (4) Regular communication with engineering officers of the division. (5) Monitoring the work during the block for any unusual incidents and real-time reporting to the officials concerned. (6) Collecting the daily progress details (block hours, time of important events from machine being given ready to machine stabled in siding, location of work, break-up of time consumed in different operations in the block, output etc.) duly reconciled with SSE/P.Way and SSE/JE/TM along with reasons for less progress, if any. (7) Entering and validating track machine progress into TMS by SSE/JE/Control in the division through specific login id in addition to other entries. (8) Detention to traffic if any, and other factors, affecting train movement on account of working of machines. (9) Monitoring movement of track machines within the division including machines of other Zonal Railways. (10) Recording details of failures of machine, if any and getting failure reports. 1104 Functions of Track Machine Control at ZMD Level - The main functions of track machine control at ZMD level shall be: (1) Communication link between the machine in-charges, divisional control, satellite depots and headquarter. (2) Co-ordination for issues related to deployment of manpower etc. on different track machines. (3) Co-ordination for deployment of machines as per the programme issued. 299 (4) Co-ordination for movement of machine for deployment, major schedules like POH, IOH, replacement of major components and assemblies and repairs to be done in sheds. (5) Co-ordinate to ensure expeditious movement of spares for repairs. (6) Coordination for deputation of service engineer of OEM etc. (7) Obtaining and recording the details of unusual incidents and reasons affecting machine utilization. (8) Getting failure reports from the machine in-charges. (9) Regular interaction with HQ control in respect of above. (10) Providing feedback to HQ control regarding unusual, breakdown of machines etc. in real time. The information collected by the track machine control and instructions given should be recorded comprehensively in a logbook, which shall be scrutinized by the officials to ensure effective functioning. The functions of ZMD control have to be dovetailed in the TMS module for track machines. The systems evolved in different railway for distribution of roles and responsibilities between the HQ, ZMD, SD and divisional control may differ and will not be disturbed or modified if functioning satisfactorily. 1105 Functions of Track Machine Control at Headquarter Level - The main functions of track machine control at headquarter level shall be: (1) Ensuring feeding of track machine details including daily progress into TMS by respective officials at different levels and divisional controls. (2) Contacting the Divisional Controls for obtaining and recording the details of unusual incidents and other reasons affecting machine utilization. (3) Authorizing shifting of machines from one division to other. (4) Monitoring of unusual, failures and block bursting and recording assistance required. (5) Coordinate with Railway Board TMS cell for commissioning of new machines/shifting of machines to other Railways. (6) Monitoring deployment of the machines in the field as per the approved programme and bringing the deviations to the knowledge of HQ officials. (7) Communicating essential instructions from HQ to divisions/field units. (8) Generation of various reports at HQ for Railway Board, PCE, CTE, CE/TM etc. The information collected by the track machine control and instructions given should be recorded comprehensively in a logbook, which shall be scrutinized by the officials to ensure effective functioning. 300 1106 Monitoring Modules of Track Machines - The deployment and performance of Track machines is to be monitored very meticulously and desired reports extracted for an informed analysis of usage of track machines. The parameters shall be monitored broadly for two areas: - Working of machines affecting productivity and utilization, - Maintenance of machines affecting health. (1) Parameters for monitoring Productivity and Utilization of Machines (a) Productivity vis-à-vis Target - In the beginning of the year, railway wise targets for various types of machines are issued by Railway Board. These yearly/monthly targets should be broken into weekly targets and productivity monitored vis-a-vis assigned targets. The shortfall in productivity of machines should be made good by addressing issues such as health of machine, adequate traffic blocks etc. Efforts shall be made to achieve these targets and to ensure optimum productivity of track machines. (b) Adherence to Deployment Programme - The deployment programme issued for each machine in the beginning of the year shall be followed. It should be the endeavor of all concerned that no deviation in the issued programme is allowed. The performance shall be periodically reviewed to achieve the pre-decided deployment of machines in various sub- sections of division so as to complete the targeted work without any shortfall. It shall be the responsibility of track machine organization to make machine available to work in good fettle as per the requirement and deployment planning. Loss of time on account of schedule of the machine, major repairs, shifting etc. shall be minimized. The schedules of the machine i.e. 50 hrs, 100 hrs, 200 hrs, 500 hrs, 1000 hrs and also IOH, POH shall be meticulously planned and advance notice given to division for optimization of resources. The availability of each machine shall be worked out in terms of number of days machine is made available for work against total number of deployed days in each division. (c) Utilization of Machine – SBH, DBH and ABH - Railway Board has stipulated minimum block hours for each type of machine. All out efforts shall be made to operate traffic blocks equivalent to stipulated blocks hours thus making the Utilization ratio (granted blocks/stipulated blocks) as 1.0. Immediate steps for improving the traffic blocks for machines having utilization ratio less than 0.8 should be taken at appropriate level. (d) Performance of Machine in terms of rated output against achieved output - Rated output of machines per effective hour is stipulated for each type of machine. Ratio of actual output to rated output is a good 301 indicator of performance of machine. All out efforts shall be made to achieve performance ratio (actual output/rated output) as 1.0. Steps shall be taken to analyse and take corrective action for the machines having performance ratio less than 0.8. (2) Parameters for Monitoring Health of Machine (a) Monitoring of Prescribed Schedules of Machine - Prescribed schedules of machines as stipulated in relevant chapter of this manual, to ensure proper health of machines, shall be strictly adhered to and adequate time given for these maintenance works. Overlapping schedules shall be clubbed to reduce the down time of machine without compromising on quality of schedules. (b) Replacement Planning of Major Components/Assemblies - Major components/assemblies of machine shall be replaced in a planned manner and monitored at level of ZMD. These major components shall include: (i) Engine. (ii) Tamping unit. (iii) ZF and other gear boxes. (iv) Axles and wheels. (v) Pumps and motors. (vi) Other critical components as decided. All these important assemblies shall be serially numbered and performance of these components monitored in a centralized database for meaningful analysis and control. (c) Monitoring of consumption of oils and consumables - Consumption of consumables and various type of oils i.e. diesel oil, lube oil, hydraulic oil and gear oil are very essential to be kept under control. The daily/monthly reports shall form the basis and apart from cost aspect excess consumption will constitute a symptom, of ill health of a machine, indicating a need for corrective action. (d) Monitoring of consumption of Spares - While the consumption of mandatory spares requiring replacement at specified intervals will have to be on a set pattern, any excess drawl shall be critically reviewed. Similarly, case of spares consumed on repetitive basis, the root cause for such excess consumption should be analysed and corrective action to change the sub-assembly or going in for better quality of spares will have to be decided. The monthly reports will bring out the consumption forming the basis for this item. Issue of stores/spares at base depot shall be only with SSE/TM/ZD’s approval in the case of Imported spares and also when the stock is at a low level. 302 (e) Failure Analysis - Each failure of the machine or any of its components either during block or detected during maintenance shall be recorded and documented in the failure register. The failure analysis should be done machine type wise in following categories (i) Mechanical failure. (ii) Electrical failure. (iii) Hydraulic failure. (iv) Pneumatic failure. (v) Miscellaneous failure. Failure reports in the prescribed proforma shall begiven by SSE/TM/Line to SSE/TM/SDI and details along with remedial measures discussed during the monthly meeting held at the level of SSE/TM/SDI and Dy.CE/TM/Line. Failure reports of major nature and of those causing bursting of block shall be sent to HQ office also. Repeated failures and failure suspected on account of design shall be reported to RDSO for further study and analysis. Similarly, failures related to POH shall be reported to respective POH workshops. (f) Monitoring of Competencies of Staff and their validity - Track machine have to work in block section and accordingly staff have to in possession of various certificates such as PME, block competency, route learning, machine competency etc. This is to ensure that staff is fit to work in block section with track machine. A monitoring mechanism shall be put in place to ensure that all staff possess necessary fitness and certificates. Staff due for certification/examination shall be directed timely to the concerned authority for examination/training/certification. (g) Recording of machine parameters while working - Record of important machine parameters shall be kept by machine in charge while working. This may include various parameters such as squeezing pressure, squeezing time, tamping depth, vibration pressure in tamping machine, depth of cutting and lifting in BCM and SBCM. Monitoring of these parameters shall also ensure quality of the work done by the machine during block. Aim should be to develop such recording mechanism that records these parameters automatically while working. 1107 Reports and Documentation for Track Machines - The following reports/documents shall be used in monitoring of performance and other items in respect to working of machines: (1) Daily performance report – A daily performance report compiled by the track machine control based on the information/fed on-line or collected from all divisional engineering controllers/field staff. This will be a computer printout containing details of blocks demanded and actually made available, proportionate output achievable and actually achieved cumulative figures 303 for the month/year. Brief remarks for less output shall also be included for the information of CE/TM, CTE and PCE. A register shall be maintained by track machine control for serving as a “Master Record” for all relevant data till such time the information is computerised. (2) Daily log – A day wise report from the machine in charge to XEN/AEN/TM in charge of field incorporating block details, performance, schedules done/overdue, consumables/spares used, oil consumption, spares required for the machine, systems by passed/dummied in the machine, repair and failure shall be made out. A daily logbook shall be maintained by machine incharge as per the format given in Annexure 11.1. (3) Breakdown report – The machine in charge will submit a report to Dy.CE/XEN/TM/Line on every breakdown of the machine resulting in failures exceeding half an hour. The report will be submitted as per format given in Annexure 11.2. (4) Monthly appreciation report –Monthly appreciation reports from the machine in charge on performance furnishing: (a) Number of days worked. (b) Number of days not worked with reasons. (c) Block availed. (d) Target. (e) Output. (f) Reasons for less output. (g) Other remarks. (h) Consumables/spares used and cost thereof. (i) Failures/repairs with spares and cost particulars. (j) Details of service Engineer’s visit and copy of the reports. (5) Monthly summary – A summarized monthly performance report from XEN/AEN/TM/Line showing schedules of inspections done, health of machine, failure analysis, adequacy of allied track works etc. of the machines under their control to Headquarter and Dy.CE/TM/Line. (6) Record for 3 years –A summary of availability of each machine for a period of 3 years shall be maintained at the satellite depot and zonal depot showing at a glance the availability, breakdowns, schedule repairs and POH of machine. 1108 Track Management System (TMS) – Present Module - Track Management system (TMS) is web enabled multi user platform available for monitoring mechanized track maintenance inputs and their efficacy. Track machine module of TMS is an integral part of overall architecture of track maintenance system, generating various important reports, including deployment planning of a machine, 304 tamping chart etc. It should be the endeavor to switch over to TMS completely in a time bound manner so that paperless working can be achieved. Presently, only the progress related module is available in TMS. Statement of different kind of reports presently available in TMS is summarized in Annexure 11.3. 305 Annexure 11.1 TRACK MACHINES ORGANISATION Page No. WESTERN RAILWAY ENGINE LOG BOOK Machine No. Type Engine No. 1 Date ___/___/20__ 2 SSE/TM JE/TM Stabling Station Machine Movement STN FROM STN TO REMARKS Details Time From ________ To______________ Block Utilisation details Planned Availed Effective Location Attended Block Work No. of EQ length No From To From To From To STNF STNT LN KMF KMT in Km SL/ Turn out Block Time Lost Block Time Reason for loss of time No. Engine Meter Reading Start Close BF From prev. Total day Duration on date Engine No 1 Engine No 2 Name & Signature M/C. Incharge JE(P.Way) 306 Cotton Consumable Used HSD LUB HYD Gear Oil Waste Grease Others Spares Utilisation FIT/ Part Code New/ Description Unit Scheduled/ Repair cost Remarks Released Repaired Break down Schedule details Schedule Type Engine Meter Reading Cost Remarks Break down STN CODE From To In Block or Major/Minor Engine Meter Reading not details Remarks 307 Special Report Reasons /symptoms of likely Failure / Assistance Reason for not availing Block, ifany SSE/SE/JE/TM 308 Annexure 11.2 BREAKDOWN REPORT OF TRACK MACHINE (a) Report by Machine In charge 1. Machine No. ……………………….. Date of breakdown ………………………………..……….. 2. Block permitted from ………………… hrs. to……..………… hrs. 3. Block section …………………………..…………Division ………………………… 4. Time of breakdown……………………. hrs. to ………………… hrs. 5. Time of block cleared ……………..………………… 6. Detention to train if any …………………………… 7. Description of failure ………………………………………………………………… 8. Date of last POH/IOH: a) Machine …………… b) Engine ……………… 9. Date of last schedule maintenance ………………..………………………… And observations made …………………………….……………………………… 10. Rectification action ………………………………..……………………………… 11. Date and time M /c made fit ……………………..……………………………… 12. Report on failed part:- No. & description of part …………………………………………………………… Make of the part …………………………………………………..…………………… Date of fitment ……………………………………………….………………………… Part identification code ……………………..……………………………………… Spare part brought from …………………………………………………………… 13. Name of the machine I/c …………………………………………………………… 14. Officer/Supervisor at site …………………………………………………………… 15. Assistance required, if any, ……………..………………………………………… From XEN/TM/Line office 16. Action suggested to prevent ……………………………………………………… recurrence/reduce breakdown time Dated …………………… Signature …………………… (b) Report by Line Officer 1. Detailed description of failed part …………………………………………………………..……………… 2. Expected life of component …………………………………………………..……………….……………… 3. Period of service given by …………………………………………………….……………..………………… component at time of failure 4. If premature failure: a) Reason of failure …………………………………………………………………………………………………… b) Name of supplier & brand ……………………………………………………………..……………………… 5. Whether warranty period exists or not ……………………………………………………………………… 6. If mature failure reason for not changing component ……………………………………………………………………………………………………..………… 7. Whether failure was avoidable or unavoidable …………………………………………….…………… 8. Staff held responsible and action taken against ………………………………………………………… 9. Action suggested to prevent recurrence …………………………………………………………………… Dated ………………………… Copy to –Dy.CE/TM/Line; Dy.CE/TM/HQ 309 Annexure 11.3 TYPES OF REPORTS IN TMS – BLOCKS, AVAILABILITY & PROGRESS OF TRACK MACHINES SN Report Heading Period Report Content 1. Progress Specified Day wise block availed, time loss, progress, location, (Machine Wise) reason for tamping, design tamping, BCM site opened with speed for specified duration for single selected machine. 2. Progress Single Detailed report for whole railway/division either (Detailed) day machine wise or division wise with various times consumed/lost. 3. Progress Single Summary of machine holding, machines worked, (Summary 1) day progress and break up of reasons for not working, with summary of holding, worked in no. and % for all zonal railways. 4. Progress Single Summary of progress for whole railway /division for (Summary 2) day, the selected day, for the month up to the selected month day and for the financial year up to the selected day. and fin. year 5. Machine Idle Single Machine Idle – under repair/breakdown, under Day shifting, not planned as site not ready, depot work, machine under IOH/POH and stabled for condemnation – for a whole railway/division of any zone/division of Indian Railway. 6. Missing Data Specified Missing data entry for each machine worked in each Entry division giving dates of missing entry as well as total days– can be seen for railway, division for all machines or M/c type wise. 7. Missing Data Specified Missing data entry days division wise total – no break Summary up or details. This can be covered in SN- 6 8. Progress on Date Single Detailed report for a railway/division either machine day wise or division wise with progress, block and idling days for the month with timing of block in 24 hour format. 9. Progress in Mega Specified Progress and block details, date wise for each Block machine worked in mega block during the specified period. 10. Machine Progress Specified Machine availability for each machine for a & Availability railway/division with % ABH/SBH and machine days not worked break-up reason wise. 11. Machine Type Specified Machine wise cumulative block duration, days and 310 wise progress for whole railway/division/selected section for selected machine type(s) with sub-total. 12. Machine Specified % DBH/SBH, % ABH/DBH for whole railway/division – Utilization giving figures division wise for each machine type 13. Night Working Specified Total hours worked, worked in night in hours and % (19:00 to 05:00 hours) for whole railway/division, division wise, machine type wise. 14. Progress Target Specified Annual target, proportionate target, total and % Vs. Actual progress for whole railway/division, division wise machine type wise. 15. Yearly Summary Specified Day wise pictorial representation of specified machine worked and reasons for not worked for a specified period for whole railway/division. 16. Machine Under Single Machine under repair/breakdown and IOH/POH Repair day giving date since repair and reason for repair division wise on a given date. 17. Tamping Chart As on Track details, tamping details year wise for last 5 years, month wise for current year for a selected official for a selected line of a selected section (8 kms at a time). 18. Machine As on Average machine holding, average machine worked in Availability no. of units and % effective for the specified period of Summary this year as well as last year for selected/all Zonal Railways. 311