Quality Control and Quality Assurance (PDF)
Document Details
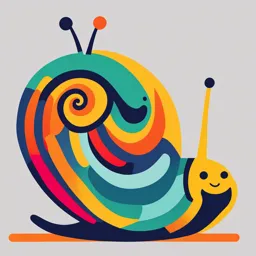
Uploaded by AdvancedRhinoceros
STI
Tags
Summary
This document details quality control and quality assurance, including different types of services, such as business, professional, personal, and social services. It introduces the concept of Total Quality Management (TQM) in service operations and its benefits, including improved customer satisfaction and sustained business growth, along with potential challenges to TQM implementation in service-oriented companies.
Full Transcript
BM2408 QUALITY CONTROL AND QUALITY ASSURANCE Establishing and maintaining high-quality assurance and control are among the most important components of a successful operation across various industries, whether in manufacturing or service-oriented businesses. Ensuring and preser...
BM2408 QUALITY CONTROL AND QUALITY ASSURANCE Establishing and maintaining high-quality assurance and control are among the most important components of a successful operation across various industries, whether in manufacturing or service-oriented businesses. Ensuring and preserving the quality of goods and services is essential for customer satisfaction and retention (Tarlengco, 2024). TQM in Service Operations Service businesses are of great significance as they provide vital support and assistance to individuals and other businesses. They address a wide range of needs and demands and play a pivotal role in fostering innovation and addressing evolving challenges in various industries (Davids, 2024). What is a Service? (George, 2024) William Edwards Deming asserts that service is a type of intangible product that customers receive in exchange for payment. Unlike physical offerings, services are non-physical and encompass a broad range of activities, such as professional assistance and task performance. They are prevalent in sectors such as healthcare, finance, education, and transportation. Services differ from goods in that they are often consumed immediately upon production and cannot be stored or resold. Examples of service offerings include consulting, repair, maintenance, hospitality, banking, and entertainment. The quality of a service is shaped by factors such as customer experience, satisfaction, and the ability to meet customers' needs and expectations. Classification of Services (Shafer, 2024) As Shafer emphasizes in his book, the role of every business is to ensure the high quality of their market offerings, optimize resource utilization, maximize efficiency, and maintain quality control. Services are categorized into different types to make them easier to understand and manage efficiently. This classification facilitates better communication and understanding among service providers, consumers, and regulatory agencies. Business services: These are services that cater to the needs of businesses, such as consulting, accounting, and legal services. McKinsey, a leading management consulting firm in the Philippines, provides advice and expertise to help businesses improve their operations. Professional services: These services are performed by professionals who have specialized knowledge and skills, such as doctors, lawyers, accountants, and architects. Philippine General Hospital is an example of this, offering healthcare services provided by doctors and other healthcare professionals. Personal services: These services are aimed at fulfilling individual needs and include services like personal grooming, fitness training, and home cleaning. A good example is a spa that offers massage and beauty treatments or a Beauty Salon that offers different haircare treatments and make-up services for various occasions. Social services: These services are geared towards enhancing the well-being of individuals and communities, including services like childcare, elder care, and community development programs. Bahay Tsinoy Foundation, a nonprofit organization that provides shelter for homeless individuals, is an example of this service. Another one is the Philippine Social Welfare and Development Agency, 05 Handout 1 *Property of STI Page 1 of 8 BM2408 which serves as the primary government institution responsible for social protection and poverty alleviation programs in the country. Financial services: These services include banking, insurance, and investment services. For instance, a commercial bank like BDO, Metrobank, and Unionbank provides various financial services, such as savings accounts, loans, and credit cards. Hospitality services: These services are related to the tourism and hospitality industry, such as hotels, restaurants, and travel agencies. For instance, Shangri-la Hotel and Astoria Plaza in Boracay offer accommodation, dining, and concierge services to travelers. Transportation services: These services involve the movement of people or goods from one place to another, such as airlines, taxi services, and shipping companies. A courier service that delivers packages and documents like J&T, Lalamove, and Air21 are examples of these services. Communication services: These services facilitate the exchange of information, such as telecommunications, internet providers, and media companies. The best examples are Globe and Smart Telecommunications, the two leading mobile phone network providers in the Philippines, which offer voice and data communication services to their customers. Education services: These services are related to the field of education, including schools, colleges, and tutoring services. For instance, STI College provides learning classes to students. Entertainment services: These services offer leisure and entertainment options, such as movie theaters, amusement parks, and event management companies. A concert venue that hosts live performances is an example of an entertainment service. Benefits of TQM in the Service Operation (Besterfield, 2024) In the service industry, the implementation of Total Quality Management (TQM) fosters a proactive approach to problem-solving. This approach emphasizes prevention rather than correction, enabling service organizations to achieve elevated levels of quality and productivity such as: Improved customer satisfaction: Quality value in the service industry ensures that customers receive services that meet or exceed their expectations. For instance, luxury hotel chains like Okada Manila focus on providing exceptional services, such as personalized greetings, customized amenities, and 24/7 concierge assistance, which elevate the overall experience and leave a positive, lasting impression on customers. Increased customer loyalty and retention: By consistently delivering high-quality services, companies can build trust and loyalty, encouraging customers to return in the future. Apple is renowned for its commitment to quality in its electronic products, creating a loyal customer base that eagerly awaits their new releases and often becomes repeat buyers. Enhanced reputation and brand image: Quality value contributes to building a strong reputation and a positive brand image. For example, Amazon has established itself as a leader in the e-commerce industry by prioritizing quality in its vast product range and ensuring timely delivery, leading to a reputation for reliability and excellent customer service. Competitive advantage: Offering superior quality services can give a company a competitive edge over its rivals. Philippines Airlines differentiates itself by providing exceptional customer service, on- time performance, and overall satisfaction, positioning itself as a preferred choice for air travel compared to other airlines in the highly competitive industry. Operational efficiency and cost savings: Quality value focuses on streamlining processes and eliminating inefficiencies, which can result in cost savings for the company. McDonald's introduced 05 Handout 1 *Property of STI Page 2 of 8 BM2408 the “Self-service Kiosk” to improve the speed and efficiency of their food preparation, leading to cost savings and faster service for customers. Employee satisfaction and productivity: Empowering employees to deliver high-quality services boosts their job satisfaction and can lead to increased productivity. Tobys, a famous multi-brand sports retailer, places great emphasis on employee satisfaction and empowerment, resulting in a workforce that goes above and beyond to provide exceptional customer service. Continuous improvement and innovation: Quality value encourages a culture of continuous improvement and innovation, pushing companies to evolve and stay ahead. Tesla, for example, has revolutionized the electric vehicle industry by continuously improving its products, expanding charging infrastructure, and introducing innovative features to provide customers with top-quality electric cars. Customer advocacy and referral: When customers experience quality value in the service industry, they become advocates and are more likely to recommend the company to others. Apple's dedicated fan base serves as a powerful marketing tool, as satisfied customers often refer their friends and family to purchase Apple products. Reduced customer complaints and returns: By delivering services of high quality, companies can minimize customer complaints and returns, saving time and resources. Uniqlo, a fast-fashion retailer, has a stringent quality control process that ensures its products meet the desired standards, reducing the likelihood of customer dissatisfaction or returns. Sustainable business growth: Quality value contributes to the overall growth and success of a business. Toyota's strong focus on quality, displayed through its "Toyota Production System," has allowed the company to become one of the largest and most profitable automakers globally, ensuring sustained growth and success Hindrances to Quality Service (Davis, 2024) Implementing Total Quality Management (TQM) may appear deceptively effortless, but it poses numerous challenges. The application of TQM in service-oriented enterprises encounters obstacles that necessitate substantial cultural and organizational transformations. These shifts can prove to be challenging to accomplish within the framework of service businesses: Lack of employee training and development: When employees are not adequately trained and developed, they may lack the skills and knowledge needed to provide high-quality service. This can result in mistakes, delays, and poor customer experiences. Solution: Implement regular training programs and provide opportunities for employees to enhance their skills and knowledge. Inadequate communication: Miscommunication or insufficient communication between employees and customers can lead to misunderstandings and dissatisfaction. If a customer's request is not clearly understood by an employee, it can result in a wrong product or service being delivered. Solution: Implement effective communication channels and encourage open and transparent communication between employees and customers. Poor leadership and management: When leaders and managers do not prioritize and emphasize the importance of quality service, it can trickle down to the employees, affecting their motivation and attitude toward delivering excellent service. Solution: Ensure strong leadership and management support, where quality service is set as a priority and actively promoted among employees. 05 Handout 1 *Property of STI Page 3 of 8 BM2408 Inefficient systems and processes: Outdated or inefficient systems and processes can hinder the delivery of quality service. If a customer must go through a lengthy and complicated process to get their issue resolved, it can lead to frustration and dissatisfaction. Solution: Regularly review and optimize systems and processes to ensure they are streamlined and customer-friendly. Lack of customer feedback and evaluation: Without input from customers, businesses may not be aware of areas where their service falls short. A restaurant that does not actively seek customer feedback may not realize that their service speed is too slow, resulting in customers leaving unsatisfied. Solution: Establish mechanisms to gather customer feedback, such as surveys or suggestion boxes, and use the feedback to identify areas for improvement. Insufficient employee empowerment: When employees do not have the authority or autonomy to make decisions or resolve customer issues, it can hinder the delivery of quality service. If a customer complaint goes through multiple levels of approval, it can lead to delays and frustration. Solution: Empower employees by providing them with the necessary authority and resources to resolve customer issues promptly. Lack of consistent standards and guidelines: Inconsistency in service delivery can lead to confusion and dissatisfaction among customers. A hotel that has different interpretations of cleanliness standards across its various branches may result in varying customer experiences. Solution: Establish and communicate clear standards and guidelines for service delivery to ensure consistency across all touchpoints. Failure to adapt to changing customer needs: If a business fails to understand and adapt to evolving customer needs and preferences, it can result in outdated and irrelevant service offerings. Solution: Regularly conduct market research and engage with customers to stay informed about their changing needs and modify service offerings accordingly. Lack of emphasis on employee satisfaction: Disengaged or dissatisfied employees are less likely to provide quality service. A retail store that does not provide sufficient incentives or recognition for its employees may lead to a lack of enthusiasm for serving customers. Solution: Prioritize employee satisfaction by implementing initiatives such as rewards and recognition programs, employee surveys, and a positive work environment. Failure to resolve customer complaints effectively: Inability to address and resolve customer complaints can damage the reputation of a business and lead to customer loss. A company that mishandles customer complaints may face negative reviews and decreased customer loyalty. Solution: Establish a robust system for handling customer complaints promptly and effectively, ensuring that customers feel heard, and their issues are resolved to their satisfaction TQM in Manufacturing Operations What is Manufacturing? According to Jacobs (2024), Manufacturing is the process of converting raw materials, components, or parts into finished goods on a large scale using machinery, labor, and various production techniques. It involves a series of steps, such as design, engineering, production, and quality control, to create a final product that can be sold to consumers or other businesses. This industry encompasses a wide range of sectors, including automotive, electronics, food and beverage, pharmaceuticals, and more. The goal of manufacturing is to efficiently produce goods that meet market demand while ensuring high quality and cost-effectiveness. 05 Handout 1 *Property of STI Page 4 of 8 BM2408 Classifications of Manufacturing (Shafer, 2024) Manufacturing operations are classified to establish a structured and comprehensive approach to organizing and comprehending the various types of manufacturing activities. Grouping these activities facilitates analysis, comparisons, and decision-making processes, as well as enables the identification of shared characteristics, trends, and challenges within similar manufacturing sectors. Job Order Manufacturing: This involves producing customized products in small quantities according to specific customer requirements. In the Philippines, Jeepney manufacturing creates unique designs based on client orders. Batch Manufacturing: This method involves producing a specific quantity of items before moving on to the next batch. A good example is the production of packaged food items like dried mangoes, which are made in batches to meet market demand. Mass Production: This involves manufacturing large quantities of standardized products in an assembly-line fashion. One notable example is the production of consumer goods like canned sardines, which are manufactured in huge volumes. Continuous Manufacturing: This method involves the uninterrupted production of goods, often using automation. For instance, the production of cement by companies like Holcim Philippines, where the process runs continuously to meet market demands. Process Manufacturing: This entails the production of goods through a systematic series of steps. Companies producing beverages, like San Miguel Corporation, utilize process manufacturing to create beverages such as beer and soft drinks Benefits of TQM in Manufacturing Operations (Besterfield, 2024) The integration of Total Quality Management (TQM) in manufacturing operations fosters a culture of constant improvement and active employee involvement. This approach facilitates enhanced problem-solving abilities and promotes innovation, contributing to superior process control, waste reduction, and more effective decision-making. Improved quality: TQM focuses on continuously improving product quality to meet customer expectations and reduce defects. For example, Toyota's implementation of TQM has led to higher- quality vehicles and increased customer satisfaction. Cost reduction: By identifying and eliminating waste and inefficiencies, TQM helps manufacturing operations reduce costs while maintaining or improving product quality. For instance, Samsung saw significant cost savings after implementing TQM in its manufacturing processes. Enhanced customer satisfaction: TQM aims to meet or exceed customer expectations, resulting in higher customer satisfaction and loyalty. General Electric implemented TQM to improve customer satisfaction and gain a competitive edge. Increased productivity: TQM involves focusing on process improvements and employee involvement, leading to increased productivity. Ford's successful implementation of TQM resulted in significant productivity gains in its manufacturing operations. Employee involvement and empowerment: TQM encourages involving and empowering employees to contribute to continuous improvement and innovation. Philippine Airlines is known for its TQM approach, which includes employee involvement and empowerment and has resulted in improved operational efficiency. Better decision-making: TQM emphasizes data-driven decision-making, leading to better overall decision-making in manufacturing operations. San Miguel Corporation's use of TQM has improved decision-making and problem-solving within its manufacturing processes. 05 Handout 1 *Property of STI Page 5 of 8 BM2408 Competitive advantage: TQM can provide a competitive advantage by differentiating a company through higher quality, lower costs, and greater customer satisfaction. As a result of TQM implementation, Shein has achieved a competitive advantage in its manufacturing operations. Continuous improvement: TQM promotes a culture of continuous improvement, ensuring that manufacturing operations are always striving to enhance processes and products. For instance, Apple has successfully implemented TQM to achieve continuous improvement in its manufacturing operations of Apple products to meet customer demands worldwide. Supplier relationships: TQM involves working closely with suppliers to ensure high-quality inputs, leading to improved overall product quality. Japanese car brands like Toyota, Suzuki, and Honda’s TQM approach have resulted in strong supplier relationships, ensuring high-quality components in its manufacturing operations. Enhanced communication: TQM encourages open communication within manufacturing operations, leading to better coordination, problem-solving, and innovation. Procter & Gamble has used TQM to improve communication and collaboration within its manufacturing operations. Hindrances to Quality Manufacturing (Davis, 2024) Implementing Total Quality Management (TQM) may seem deceptively simple; however, it presents numerous challenges. TQM's application in manufacturing businesses requires significant cultural and organizational transformations, leading to various obstacles. Lack of Skilled Workforce: When employees lack the necessary skills and knowledge, it hampers the manufacturing process and reduces the quality of products. Some business companies may struggle to find workers with specialized technical skills required for certain manufacturing processes. Solution: Offer specialized training programs and partnerships with educational institutions to develop a skilled workforce. Poor Infrastructure: Inadequate infrastructure and outdated facilities can lead to manufacturing inefficiencies and affect product quality. A company might face issues such as unreliable power supply or outdated machinery. Solution: Invest in modernizing infrastructure, upgrading machinery, and ensuring a stable power supply. Inconsistent Supply Chain: Fluctuations in the supply chain, including delays or shortages in raw materials or components, can disrupt manufacturing and compromise product quality. A company might experience delays in receiving raw materials from suppliers due to transportation issues or supply chain disruptions. Solution: Strengthen supplier relationships, establish backup suppliers, and consider implementing just-in-time inventory management systems. Inadequate Quality Control Processes: Insufficient quality control measures, such as lack of proper inspections and testing, can result in defective products reaching the market. A company might have limited quality control checks and fail to identify product defects before shipment. Solution: Implement robust quality control processes, conduct regular inspections, and invest in testing equipment to ensure product quality. Cultural Barriers: Differences in work culture and communication styles can impact manufacturing quality, especially in multinational companies. A company collaborating with foreign partners may face challenges due to cultural differences affecting coordination and understanding of quality requirements. 05 Handout 1 *Property of STI Page 6 of 8 BM2408 Solution: Promote cross-cultural training, encourage effective communication practices, and foster a collaborative work environment. Lack of Standardization: Inconsistent manufacturing practices and lack of standardized operating procedures can lead to variations in product quality. A company might have different manufacturing processes across different production lines, resulting in inconsistent product quality. Solution: Establish standardized operating procedures, implement quality management systems, and conduct regular audits to ensure adherence to quality standards. Insufficient Investment in Research and Development: Lack of investment in research and development limits innovation and the ability to improve product quality. A company may struggle to allocate resources for research and development, hindering improvements in manufacturing techniques and product quality. Solution: Allocate resources for research and development activities, promote innovation, and collaborate with research institutions to enhance manufacturing processes and product quality. Regulatory Compliance Challenges: Adhering to complex and evolving regulatory requirements can be a hindrance to quality manufacturing. Some companies must comply with local and international regulations, which can affect manufacturing processes and quality control. Solution: Stay updated with regulations, invest in compliance management systems, and ensure adherence to all applicable standards and certifications. Lack of Continuous Improvement Culture: Without a focus on continuous improvement, manufacturing companies may face complacency and fail to address emerging quality issues. A company may resist implementing changes to improve manufacturing processes, resulting in quality stagnation. Solution: Foster a culture of continuous improvement, encourage employee involvement in identifying improvement opportunities, and implement lean manufacturing principles. Inadequate Data Management: Poor data management practices can hinder decision-making and compromise product quality. A company may face challenges in collecting, analyzing, and utilizing manufacturing data effectively to identify quality improvement opportunities. Solution: Develop robust data management systems, implement data analytics tools, and ensure data-driven decision-making processes to improve product quality. Quality Measurements and Metrics What is Quality Measurement? Guevara (2023) defined quality measurement as “the fundamental process of assessing and evaluating the characteristics and properties of a product, service, or process against established standards and criteria.” Through the systematic gathering and analysis of data, quality measurement permits an objective assessment of performance, adherence to requirements, and customer satisfaction. In essence, quality measurements serve to identify areas that require enhancement, monitor progress, and make well-informed decisions regarding potential changes or interventions. They play a vital role in monitoring and controlling quality, ensuring consistency, and meeting customer expectations. Across diverse industries and domains, an array of instruments and methodologies, including metrics, key performance indicators, surveys, and audits, are employed to conduct quality measurements. This comprehensive approach provides valuable insights into a system's effectiveness and efficiency, enabling organizations to drive continuous improvement and elevate overall performance. 05 Handout 1 *Property of STI Page 7 of 8 BM2408 Metrics Used to Conduct Quality Measurements (Guevara, 2023) Customer Satisfaction: This metric measures customers' satisfaction with products or services. An example is the Net Promoter Score (NPS), which gauges customers' likelihood of recommending a company's product or service. NPS is based on a simple question: "On a scale of 0-10, how likely are you to recommend our product/service to a friend or colleague?" Respondents are then classified into three categories: Promoters (scoring 9-10), Passives (scoring 7-8), and Detractors (scoring 0-6). To calculate the NPS, the percentage of Detractors is subtracted from the percentage of Promoters. The resulting score can range from -100 to +100. A positive NPS indicates that the majority of customers are satisified and will recommend the product, while a negative score indicates unsatisfied customers that will not recommend the product. Return on Investment (ROI): ROI measures the profitability of an investment and is used to assess the financial returns relative to the investment's cost. Example: Calculating the ROI of a marketing campaign to determine its effectiveness. Customer Retention Rate: This metric measures the percentage of customers that a business has retained over a specific period. Example: A company with a high customer retention rate indicates that its products or services are meeting customer needs effectively. Employee Productivity: This metric evaluates the output of employees in relation to the resources expended. Example: Measuring the sales generated per employee to assess productivity. Defect Rate: Defect rate measures the number of defective products or services produced. Example: A manufacturing company monitoring the defect rate in its products to ensure quality. Net Profit Margin: This metric assesses the profitability of a business by measuring the percentage of revenue that translates into profit. Example: Analyzing the net profit margin to evaluate a company's efficiency in cost management. Market Share: Market share measures a company's sales in relation to the total market. Example: Tracking the market share of a company's product to assess its competitiveness. On-time Delivery Performance: This metric evaluates how often a business delivers products or services on time. Example: A logistics company tracking on-time deliveries to ensure customer satisfaction. Cost of Quality (COQ): COQ measures the costs associated with ensuring product quality. Example: Assessing costs related to quality control, prevention, and appraisal activities. Employee Satisfaction: This metric measures the contentment and engagement level of employees. Example: Using employee surveys to gauge satisfaction levels within the organization References Besterfield, D. (2024) Total Quality Management. Pearson Davis, S. (2024). Total Quality Management: An Integrated Approach. Butterworth-Heinemann Publications George, S. (2024) Total Quality Management: Strategies and Techniques Proven Today’s Most Successful Companies. Wiley LLC Guevara, P. (2023). What are Quality Metrics? https://safetyculture.com/topics/quality-metrics/. Jacobs, R. (2024). Operations and Supply Chain Management. McGraw-Hill Education Shafer, M. (2024). Operations Management for MBAs. Wiley Publications. Tarlengco, J. (2024). Quality Assurance and Quality Control. https://safetyculture.com/topics/quality-assurance-and-quality-control/ 05 Handout 1 *Property of STI Page 8 of 8 BM2408 QUALITY OPERATIONS STRATEGY The changing business environment, characterized by an increasingly high-velocity service and fast-growing product demand, underscores the growing importance of capacity planning and management. In a high- velocity service delivery environment, the need for accurate and real-time capacity planning becomes imperative, given the high levels of concurrent projects. Companies must refrain from guesswork in capacity planning, especially as they strive to scale and diligently meet customer needs. Whether in the engineering or consulting sector, the intricate planning and organizational tools required for maximizing customer experience highlight the vital role of capacity planning in creating tangible business value and ensuring positive customer experiences (Woodgate, 2023). Capacity Planning What is Capacity Planning? According to the definition provided by Jacobs (2024), Capacity planning is the process of determining and managing the resources required to meet the demand for goods or services effectively. By evaluating current and future needs across production, businesses can optimize resource allocation, drive efficient operations, and make informed decisions. Accurate forecasting aligned with available capacity is key in preventing resource underutilization or overutilization, thereby enhancing cost efficiency and improving customer satisfaction, making the audience feel efficient and effective. Capacity Planning also allows businesses to proactively identify potential bottlenecks or constraints in their production processes and take proactive measures to eliminate them. This enables enterprises to scale their operations to accommodate growth or changes in market conditions, thereby maintaining a competitive edge. Types of Capacity Planning (Laoyan, 2024) There are various approaches to capacity planning that businesses can employ in different scenarios to optimize production capacity. A. Lead capacity planning. Also known as a lead strategy, involves expanding production capacity in preparation for anticipated high demand. For instance, a retailer might require a surge of seasonal employees during the holidays, whether that be for an entire season or just a temporary sales event. By anticipating increased customer footfall, the retailer can effectively recruit additional staff to meet the demand within a short timeframe. B. Lag strategy planning. Lag strategy planning involves carefully strategizing to ensure that production capacity can be increased in response to real-time demand. This approach is commonly utilized in fields such as medical care, social work, or the restaurant industry, particularly in situations where individuals are "on call." Depending on the workload, a manager may call additional team members to ensure ample availability of resources, thereby guaranteeing that all customer or client needs are met effectively. C. Match strategy planning. It involves a strategic combination of proactive capacity planning and reactive resource allocation. This process necessitates a gradual increase in capacity through small increments until optimal resource utilization is achieved. For instance, consider the restaurant industry: A manager might have multiple employees on call for the evening shift. When faced with an unexpectedly large party, he may opt to summon additional servers to accommodate the surge until the crowds subside. 06 Handout 1 *Property of STI Page 1 of 8 BM2408 Capacity Planning Process (Laoyan, 2024) The process of capacity planning involves the following five (5) main stages to ensure the availability of resources required when needed: Step 1. Forecast anticipated demand. When one becomes aware of an upcoming project, it is wise to engage in a well-informed assessment of the tasks that need to be completed. This evaluation will provide valuable insight into the necessary skills and abilities required to execute the project successfully. As a result, it becomes possible to compare this capacity with the existing available resources. Step 2. Determine required capacity. Based on the initial estimates, it is important to approximate the capacity needed to complete the forecasted work. A common unit of measurement, such as hours, or a project estimation tool can be utilized for this purpose. For instance, engineering managers base their capacity planning on the number of hours required to finish a project. Step 3. Calculate the resource capacity of the current team. To ensure that the team is not overwhelmed and at risk of burnout, it is imperative to assess their capacity before introducing another project. This can be accomplished by considering that an average person is typically able to dedicate approximately 30 hours per week. To determine available capacity within a week, one must subtract the total number of hours they are currently occupied with existing projects from the average of 30 hours. Step 4. Measure the capacity gap. Based on the capacity needed for a specific project and considering the expected level of demand, evaluate and analyze how the existing resources align with the anticipated requirements, considering the potential constraints and limitations that may impact the overall capacity assessment. Step 5. Align capacity with the demand. Consider analyzing the previous gap in capacity and subsequently optimize the current and available capacity to achieve a balanced state. If the team is presently operating at full capacity and unable to accommodate additional tasks to complete the project, a short-term solution could involve adding team members to expedite project completion. And should there be an excess of capacity, it may be best to integrate another project to optimize the available resources effectively. Key Considerations for Successful Capacity Planning To remain competitive and ensure an over-arching positive brand and customer experience, businesses should gain insight into the maximum number of customers they can accommodate over a specific period based on their current projects (Tagetik, 2022): Accurate demand forecasting: This involves predicting future demand for products or services. For example, Jollibee Foods Corporation, a fast-food company in the Philippines, uses sales data and market trends to forecast demand for its menu items. This allows it to plan its capacity accordingly. Flexibility and scalability: Companies need to be able to adapt to changes in demand and scale their operations up or down as needed. Philippine Airlines demonstrates this by adjusting its flight schedules and fleet size based on seasonal demand fluctuations and market conditions. Efficient resource utilization: Maximizing the use of available resources, such as labor, equipment, and facilities, is crucial. San Miguel Corporation, a diversified conglomerate in the Philippines, optimizes its production processes to ensure efficient utilization of its manufacturing facilities. Risk management and contingency planning: It is important to anticipate and mitigate potential risks that could impact capacity. A property developer like Ayala Land in the Philippines conducts risk assessments to identify and plan for possible disruptions in its construction projects. 06 Handout 1 *Property of STI Page 2 of 8 BM2408 Technology integration: Leveraging technology to enhance capacity planning processes and improve operational efficiency. Globe Telecom, a leading telecommunications company in the Philippines, uses advanced network management systems to optimize its network capacity based on data usage patterns. Collaboration and communication: Effective communication and collaboration among different departments and stakeholders are essential. A retail giant like SM Supermalls coordinates with its tenants to align capacity planning efforts with expected foot traffic and customer demand. Long-term strategic alignment: Capacity planning should align with the company's long-term strategic goals and growth plans. Energy Development Corporation in the Philippines aligns its capacity expansion initiatives with the country's renewable energy targets and its sustainability commitments. Regulatory compliance: Ensuring that capacity planning adheres to relevant laws and regulations. A pharmaceutical company like Universal Robina Corporation follows strict regulatory guidelines in its production capacity planning to meet quality and safety standards for its products. Organizing Resources What is Resource Planning? According to Gupta (2023), Resource Planning, also known as Resource Management, involves the identification, forecasting, and allocation of optimal resources, including human resources, equipment, assets, and facilities, among others, to projects at the appropriate time and cost. Its objective is to ensure the efficient and effective utilization of resources throughout the organization. In essence, resource planning is a strategic process designed to maximize the use of resources based on their capacity and availability while delivering each project within specified time and budget constraints. Difference Between Resource Planning and Capacity Planning (Laoyan, 2024) Although the two (2) are at times used interchangeably, capacity planning and resource planning are similar yet distinct project planning strategies Capacity planning is a strategic process that allows teams to anticipate and effectively manage any upcoming increase in demand. It involves carefully evaluating the supply and demand dynamics of a business's resources. The key to a successful capacity plan lies in its ability to accurately predict and prepare for situations where the business experiences a significant surge in demand, requiring additional resources. By proactively allocating and provisioning resources, a well-executed capacity plan ensures that the business is fully equipped to meet the needs of its customers and maintain optimal operational efficiency. Resource planning is a crucial process that empowers teams to effectively allocate their available resources to the areas where they are most needed. The primary goal of resource planning is to strategically identify and make the best use of the resources currently possessed by the business, as well as to determine the optimal allocation of these resources. In addition, resource capacity planning entails a merging of both resource planning and foresight, as it involves anticipating and preparing for the future requirement of additional resources. Resource Planning Process (McConnel, 2024) The process of resource planning involves following four (4) main stages to ensure the stability of the bottom line and access to available resources when needed. This is also referred to as the resource management life cycle. 06 Handout 1 *Property of STI Page 3 of 8 BM2408 Step 1. Evaluate Available Resources. After assessing the situation and determining the key objectives, select the most suitable strategy and accurately estimate the resources required to achieve the set goal. The process of resource forecasting must be approached with utmost efficiency and cost- effectiveness in mind. These resources include labor, materials, equipment, and facilities, as well as administrative support and subcontractors, among others. Step 2. Procure Resources. Begin assembling the team based on the necessary skills and experience prescribed by the project. Take the initiative to acquire the required equipment and secure reliable contractors. This stage of resource planning entails the development of team roles, procurement, contractual arrangements, budget allocation, performance evaluation methods, and the implementation of policies and procedures to optimize resources. Step 3. Manage Resources. The roles and responsibilities of the team members must be clearly defined, along with everyone’s specific tasks. The roles of subcontractors should also be clear. If tools and equipment are being rented for the project, it is essential to ensure that they are returned in a condition that meets the requirements of the contract. Step 4. Control Resources. It involves actively monitoring performance during implementation to ensure that they are producing the anticipated outcomes. An important aspect of this step is the measurement of the resource utilization rate, which assesses the effectiveness of using the resource. In cases where the utilization rate is insufficient, it is necessary to initiate corrective measures, including conducting a cost-benefit analysis. Continuous evaluation of results is essential to maintain alignment with objectives. Key Considerations for Successful Resource Planning (McConnel, 20224) Resource management plans can vary across projects, as organizations often choose different levels of complexity. However, at a basic level, a resource plan should include the following essential components. All the Resources Necessary to Complete the Project: Ensure to include all essential elements, ranging from personnel to machinery and even office space, to create a comprehensive list. Dedicate an ample amount of time to this task, as the level of completeness in the list will directly impact the accuracy of the schedule. Timeframes For the Planned Effort of Each Resource: Carefully assessing the time needed for each resource and making a precise projection of the project schedule. The Number of Each Resource Needed Per Day/Week/Month: Break down the project's resource requirements on a daily, weekly, and monthly rotation to gain a more comprehensive understanding of what is needed and when. It is recommended to utilize a resource histogram to facilitate this process. Quantity of Resource Hours Required Per Day/Week/Month: Ensure that the workload for each resource is evenly distributed over the specified time by allocating the appropriate number of hours for each resource. Assumptions and Constraints: Assumptions represent potential truths, while constraints encompass factors such as schedule, cost, and scope of projects. It is essential to understand both assumptions and constraints and their potential impact on the project plan. Resource Constraints: In addition to the traditional project management constraints that affect how to manage resources, there are other specific limitations on resource availability to be considered, such as required skill sets, geographical location, or even the availability of certain equipment. 06 Handout 1 *Property of STI Page 4 of 8 BM2408 Quality Management and Control What is Quality Management? According to an article published by CFI Team (2023), Quality management is the essential practice of supervising various activities and tasks within an organization to ensure the consistency and excellence of both products and services. Its purpose is to achieve and uphold a desired standard of quality throughout the entire organization. What is a Quality Management System? A quality management system (QMS) is a well-defined framework of processes and responsibilities that ensures the smooth functioning of your business. Every organization has its own set of QMS, which includes a formal set of policies, processes, and procedures designed to enhance customer satisfaction. A QMS serves as a guiding force for organizations as they streamline and improve quality controls in areas such as manufacturing, service delivery, and other crucial business processes. The core benefits of a QMS include: Enhanced process and output consistency and standardization Reduced waste, lessened errors, and improved resource utilization Improved customer loyalty and retention by consistently delivering high-quality products and services. Continuous evaluation and improvement of organizational operations What is an ISO? (Davis, 2024) ISO stands for International Organization for Standardization. It is an independent, non-governmental international organization that develops and publishes international standards. These standards are designed to ensure that products, services, and systems are safe, reliable, and of good quality. ISO standards cover a wide range of areas, including technology, manufacturing, food safety, healthcare, and environmental management. They provide a benchmark for organizations to follow, helping to improve efficiency, reduce waste, and enhance customer satisfaction. ISO certification is often sought by companies to demonstrate their adherence to these standards and to gain a competitive advantage in the market. The ISO 9000: The International Standard for Quality Management Systems (ASQ, 2023) The ISO 9000 is a family of standards and guidelines. It sets the requirement for quality assurance and management’s involvement. The main objective of ISO 9000 is for the organizations to implement the following standard requirements: Improve customer satisfaction by fulfilling customer requirements. Achieve continual improvement of organizational performance and competitiveness. Continually improve organizational processes, products, and services. Comply with regulatory requirements. How ISO 9000 is Applied to Organizations An online article published by ASQ (2023) stated that an organization must develop and use Quality Management Systems (QMS) conforming to the strict standards and guidelines of ISO 9001 to secure registration to ISO 9000. 06 Handout 1 *Property of STI Page 5 of 8 BM2408 The quality management system must include the following documentation: A quality policy. It refers to a statement that describes how the organization approaches quality. The quality manual. It refers to a collection of guiding policies that address each clause of the ISO 9001 standard. It typically includes an organizational chart that illustrates management's responsibility for operating the quality system. Quality objectives. It refers to the goals related to quality and must be in harmony with the quality policy of the company. Quality procedures. It refers to a step-by-step method that describes how the company meets the quality policy. Forms and records. It refers to the proof of activities that will support the quality procedures. Benefits of ISO 9000 (Hayes, 2024) The following are the benefits associated with ISO 9000 certification: Increased marketability. ISO 9000 certification provides businesses with heightened credibility to current and prospective clients. An ISO-certified company denotes a consumer perception that the company brings quality to its customers, which helps increase customer retention and acquisition. Reduced operational expenses. ISO 9000 registration exposes significant shortcomings in various operational areas of the business, which can be improved to save the company time and financial resources. Better management control. ISO 9000 registration process results in a realization of the company’s overall direction since the certification requires self-assessment of the business process. Increased customer satisfaction. ISO 9000 registration uncovers areas in which the quality of the final product can be improved, resulting in continual improvement in the outputs, which eventually leads to higher levels of customer satisfaction. Improved internal communication. The ISO 9000 registration process emphasizes self-analysis and operations management issues, encouraging various departments of a company to interact with one another in hopes of gaining a complete understanding of the needs and desires of their internal customers. Improved customer service. ISO 9000 registration refocuses company priorities on pleasing customers in all respects, including customer service. Reduction of product-liability risks. ISO 9000 certification limits the chance of a company being charged with product liability lawsuits because of the established ISO standards incorporated in their processes. Attractiveness to investors. ISO 9000 certification increases a company's likelihood of securing funding from venture capital firms. ISO 9000 Versions/Updates (ASQ, 2023) The various updates to ISO 9000 are summarized as follows: ISO 9000:1987. This initial version of the ISO 9000 standard emphasizes conformance with procedures rather than the overall process of management. It contains three (3) models for quality management systems as follows: ISO 9001:1987. Quality assurance in design, development, production, and installation services ISO 9002:1987. Quality assurance in production, installation, and servicing ISO 9003:1987. Quality assurance in final inspection and test 06 Handout 1 *Property of STI Page 6 of 8 BM2408 ISO 9000:1994. This version emphasizes quality assurance by enforcing preventive actions instead of conforming to the procedures and checking the final product. However, it still requires comprehensive evidence of compliance with properly documented procedures. ISO 9001:2000. This version combined ISO 9001, 9002, and 9003 into one (1) document that is ISO 9001. It sought to create a radical change in the concept of process management by monitoring and optimizing the company’s activities to achieve quality improvement. In addition, it also emphasizes the contribution of upper executives in integrating quality into the business system. It also gives emphasis on enforcing performance metrics as a numerical measurement of the effectiveness of the different tasks and activities of a company. Also, it highlights continual process improvement and tracking customer satisfaction. The established requirements of this version for ISO certification were the following: Approved documents before distribution Provided correct version of documents at points of use Presented company records to prove that requirements have been met Developed a procedure to control company records ISO 9001:2008. This version is not substantively different from ISO 9001:2000, but several important requirements were added as follows: The quality policy must be a formal statement from upper management that is linked to the organization’s business and management plan. The quality policy must be understood and used by all personnel at all levels. Each member of the personnel must have a measurable work objective. The quality system must be audited regularly for conformance and effectiveness. Decisions about the quality system must be based on recorded data. Records must trace problems directly to its source. Records must include where and how raw materials were processed. The organization must have a comprehensive system for communicating with customers about any aspects of the relationship. Product development must have planned stages with testing at every stage, and test results must be documented to indicate whether the product meets all applicable requirements. Organizational performance must be regularly reviewed. The organization must have documented procedures for dealing with nonconformance. ISO 9001:2015. This version is constructed around the seven (7) quality management principles, such as customer focus, leadership, engagement of people, process approach, improvement, evidence- based decision making, and relationship management. This ISO version emphasizes measuring and properly assessing the input and output of processes. It encourages risk-based thinking by employing risk analysis to determine the challenges in the business process of an organization. In addition, the concept of stakeholders in the business is also extended from customers to suppliers, personnel, shareholders, legislative bodies, society, and internal customers. This version recommends that organizations must be aware of the importance of these stakeholder’s changing requirements and standards. 06 Handout 1 *Property of STI Page 7 of 8 BM2408 References ASQ Org. (2023). What is the ISO 9000 Standards Series? https://asq.org/quality-resources/iso-9000 CFI Team. (2023). Quality Management. https://corporatefinanceinstitute.com/resources/management/quality-management/ Davis, S. (2024). Total Quality Management: An Integrated Approach. Butterworth-Heinemann Publications Gupta, O. (2023). What is Resource Planning and Why is it Important? https://www.saviom.com/blog/what-is-resource-planning-and- why-is-it-important/ Hayes, A. (2024). ISO 9000 Standard: Benefits and How to Achieve. https://www.investopedia.com/terms/i/iso-9000.asp Jacobs, R. (2024). Operations and Supply Chain Management. McGraw-Hill Education Laoyan, S. (2024). What is Capacity Planning? Tips to Apply the Right Strategy. https://asana.com/resources/capacity-planning# McConnel, S. (2024). Resource Plan: The Ultimate Guide to Resource Planning. https://www.projectmanager.com/guides/resource- management Tagetik. (2022). Capacity Planning for Service Organizations: The Value of Scaling Your Business. https://www.wolterskluwer.com/en/expert-insights/the-value-of-capacity-planning-process Woodgate, Z. (2023). Why is Capacity Planning Important? https://www.precursive.com/post/why-is-capacity-planning-important 06 Handout 1 *Property of STI Page 8 of 8 BM2408 QUALITY IMPLEMENTATION AND REVIEW Quality implementation and review are essential components of operations management, ensuring that products and services meet or exceed customer expectations. In today's business landscape, where consumers demand high-quality products and services, quality assurance has become more critical than ever. Many industries have specific quality standards or regulations that businesses must adhere to. Failure to comply with these standards can result in fines, penalties, or even legal action. (Davis, 2024). Supply Chain Management (Besterfield, 2024) What is a Supply Chain? A supply chain constitutes a complex network of organizations engaged in the creation and delivery of products or services to customers. This network encompasses all stages, from the extraction of raw materials to the final delivery of the product. The fundamental components of a supply chain include: Suppliers: Entities that furnish raw materials, components, or services to other organizations within the chain. Manufacturers: Businesses that convert raw materials or components into finished products. Distributors: Companies responsible for transporting and storing products to ensure they reach retailers or customers. Retailers: Businesses that sell products directly to consumers. Customers: The end-users of the product or service. What is Supply Chain Management? Supply chain management involves the strategic oversight and coordination of all activities necessary to produce and deliver a product or service to customers. This comprehensive process starts with sourcing raw materials and culminates in the delivery of the final product. Key focal points within supply chain management include: A. Supplier Relationship Management: Cultivating strong partnerships with suppliers to guarantee a consistent and cost-effective supply of materials and components. B. Demand Planning: Accurately forecasting future product or service demand to ensure that supply aligns with market needs. C. Inventory Management: Optimizing inventory levels to strike the right balance between the costs associated with stockouts and excessive inventory. D. Project Management: Organizing and managing resources to achieve specific goals within a defined scope, schedule, and budget. E. Performance Measurement: Monitoring and assessing key performance indicators (KPIs) to gauge the effectiveness of the supply chain. Using KPIs to measure supply chain management is vital for businesses to maintain a competitive edge, lower costs, enhance customer satisfaction, and improve overall operational efficiency. Objectives of Supply Chain Management Well-executed supply chain management offers numerous objectives, such as: 07 Handout 1 *Property of STI Page 1 of 12 BM2408 Reduced Costs: By streamlining processes and minimizing waste, companies can lower expenses throughout the supply chain. Improved Customer Satisfaction: An effectively managed supply chain ensures timely delivery of products in excellent condition, which significantly enhances customer satisfaction. Increased Competitiveness: A healthy supply chain allows businesses to stand out from competitors and gain a market edge. Enhanced Risk Management: By identifying and addressing potential risks, companies can bolster their resilience and reduce disruptions. Forecasting and Demand Management What is Forecasting? (Jacobs, 2024) Forecasting refers to the systematic process of predicting forthcoming events, trends, or outcomes by utilizing historical data and employing statistical models. This methodology involves the analysis of past patterns, the identification of underlying relationships, and the calculation of these insights to make informed predictions. Forecasting is used to: Predict future needs: Companies can predict sales, customer trends, and market requirements to produce more leanly with minimal inventory and pricing capacity. Better financial planning: Businesses can more accurately predict revenue, expenses, and profitability, which in turn boosts better financial projections and strategic resource allocation. Risk management: Forecasting can help spot risks or opportunities that would otherwise go unnoticed and plan or act accordingly. Informed decisions: By being aware of future trends, businesses are better equipped to make strategic choices in product development or market expansion and investments. Different Ways to Forecast A. Qualitative Approach: Qualitative styles entail expert opinion, survey, and other related subjective methods. Delphi method: This method gathers insights from a panel of industry experts, such as healthcare professionals, technology experts, and industry analysts. Market Research: Surveys, interviews, and focus groups can provide valuable insights into consumer preferences and market trends. Scenario Planning: Creating hypothetical scenarios can help to identify potential risks and opportunities. B. Quantitative Approach: Utilize statistical models and historical data to make predictions. Time series analysis: This technique analyzes data such as monthly, quarterly, or yearly sales figures collected over time to forecast sales. Regression Analysis: This method can be used to predict a dependent variable (e.g., sales) based on independent variables (e.g., market spending, economic indicators). Causal Modeling: This approach identifies cause-and-effect relationships between variables (e.g., market spending, economic indicators) to forecast future outcomes (e.g., sales). Simulation Modeling: It involves creating a representation of a real-world system to simulate different scenarios and assess potential outcomes. 07 Handout 1 *Property of STI Page 2 of 12 BM2408 C. Hybrid Approach: A hybrid method integrates both qualitative and quantitative methods to provide a more accurate forecast. Combining Qualitative and Quantitative Methods: Combining methods like the Delphi method (qualitative) with time series analysis (quantitative) can provide a comprehensive view of future trends. Ensemble Forecasting: Combining multiple forecasting models can reduce bias and improve accuracy Forecasting Challenges (Shafer, 2024) Forecasting is an important function for businesses, as it helps them plan, make informed decisions, and allocate resources more efficiently. However, forecasting is not without its challenges. Here are some common challenges: Incomplete or Inaccurate Information: Companies often lack the information needed to make accurate forecasts. Data can be missing, outdated, or inaccurate, resulting in unreliable forecasts. For example, a retail company may not have incomplete sales data for a product or region, making it difficult to forecast future demand. Data Noise: Data can be contaminated by noise, which can obscure trends and underlying processes. For example, a sudden spike in sales due to one-off promotions can distort overall sales, making it difficult to forecast future sales accurately Unforeseen Issues: Businesses often face unexpected issues that can significantly affect their forecasts. Economic downturns, natural disasters, political instability, and technological disruption can all disrupt operations and make it difficult to predict future results. Market Flexibility: Markets can be highly volatile, with rapid changes in consumer preferences, competitive landscape, and economic conditions. These variables can make it difficult to predict future sales or market share accurately. For example, the popularity of certain products or services may change rapidly as a result of technological advances or changes in consumer tastes. Overfitting: The forecast model may be too complex and fit historical data too closely. This results in poor efficiency with new data. This can happen when too many variables are included in the model or are not properly validated. For example, a forecast model that matches too much historical sales data may not be able to predict sales accurately predict the future in the face of changing market conditions. Incorrect Model Specification: Selecting the wrong forecast model can lead to inaccurate forecasts. For example, using a linear model to predict a nonlinear trend can cause Important errors are possible. Human Judgment: Prophecy is often a human judgment influenced by biases and assumptions. For example, a sales manager may be overly optimistic about future sales, inflating the forecasts. Groupthink: When a group of people work together to make a forecast, there may be more opportunities to follow the opinion of the majority, even if it's not correct. This can lead to biased predictions. Rapid Change: Businesses operate in a dynamic environment that is constantly changing. New technologies, competitors, and regulations may emerge, making it difficult to predict future trends. For example, the rise of e-commerce has affected Traditional retail business. This makes forecasting future sales a challenge. 07 Handout 1 *Property of STI Page 3 of 12 BM2408 Demand Management (George, 2024) Demand Management is the process of planning and controlling the level of demand for a product or service to align it with business objectives and supply capabilities. It consists of a wide range of activities related to customer demand, such as pricing strategies, promotions, product availability, and customer education. Objectives of Demand Management Balance Supply and Demand: In this way, the product or service, the quantity of which is demanded, is ensured to be in direct relation to the inventory, avoiding excessive or insufficient supplies and sales. Optimize Revenue: Identify such products or services from demand data and then set the selling price in accordance with customer needs and preferences to bring in the highest possible revenue. Improve Customer Satisfaction: Maintain the customers' trust by letting them know they will get the products or services they want at the time and place they want them. Reduce Costs: The unnecessary costs related to production overages, stockouts, or missed sales should be minimized Demand Management Strategy (Jacobs, 2024) A. Pricing: Adjusting prices to influence demand. For example, increasing prices at peak demand by offering discounts or promotions to stimulate demand during slow periods. B. Promotion: Use a marketing advertising campaign to create awareness and interest in a product or service. C. Product Availability: Ensure that products or services are available when customers need them. This may include managing inventory levels. Delivery channel and order fulfillment processes D. Customer education: Provide information about products or services to customers to help them make informed purchasing decisions. E. Demand Forecasting: Use data analysis and forecasting techniques to predict future demand levels. By managing demand effectively. Intersection of Forecasting and Demand Management (Jacobs, 2024) Forecasting and demand management are intricately linked, serving as essential elements of effective business planning and operations. Forecasting establishes the groundwork for demand management, while strategies in demand management can shape future forecasts. Demand Shaping: Demand management techniques, including pricing strategies and promotions, can significantly affect demand levels and therefore influence future forecasts. For instance, an effective marketing campaign may boost demand, whereas a price hike might diminish it. Feedback Loop: There exists a continuous feedback loop between forecasting and demand management. Forecasts guide demand management decisions, and the results of these decisions refine future forecasting accuracy. Optimize Inventory Levels: Accurate demand predictions allow for the maintenance of optimal inventory levels, minimizing costs related to overstocking or stockouts. Enhance Customer Satisfaction: Effective demand management increases customer satisfaction by ensuring product availability aligns with customer needs. Improve Supply Chain Efficiency: Aligning supply with demand enhances supply chain efficiency, reducing costs while improving lead times. 07 Handout 1 *Property of STI Page 4 of 12 BM2408 Support Strategic Decision-Making: Reliable forecasting and demand management provide crucial insights for strategic decisions, including new product development, market expansion, and resource allocation. Risk Assessment: It also assists in identifying potential risks, such as shortages or overstock situations, allowing for the development of contingency plans to address these challenges. Inventory Management (Davis, 2024) What is Inventory Management? Inventory management is an essential process that encompasses the planning, organization, and control of acquiring, storing, and distributing inventory. Its primary goal is to ensure that the right quantity of inventory is available at the appropriate time and location to fulfill customer demands while keeping costs to a minimum. Objectives of Inventory Management Balancing Supply and Demand: Ensuring that inventory levels are sufficient to meet customer needs without resulting in overstock. Minimizing Costs: Lowering expenses related to inventory maintenance, such as storage fees and risks of obsolescence. Enhancing Customer Satisfaction: Guaranteeing product availability to meet customer needs promptly. Optimizing Cash Flow: Strategically managing inventory levels to prevent excessive capital from being tied up in stock. Inventory management techniques and strategies A. Economic Order Quantity (EOQ): A mathematical formula designed to identify the most efficient order quantity that minimizes total inventory costs, balancing ordering and holding expenses. For example, a retail store might determine the optimum number of units to order for its best-selling item. B. Just-in-Time (JIT): A strategy focused on reducing inventory levels by having supplies delivered precisely when needed for production. For instance, a car manufacturer may arrange for components to be delivered right to the assembly line, minimizing the need for large stockpiles. 3. C. ABC Analysis: This is a classification method for inventory items based on their value and usage, helping companies prioritize management efforts. A grocery store, for example, might categorize items into "A" (high-value, high-usage), "B" (medium-value, medium-usage), and "C" (low-value, low- usage), dedicating more resources to the "A" items. D. Safety Stock: An additional reserve of inventory kept to compensate for unforeseen spikes in demand or supply interruptions. For example, a restaurant could maintain a safety stock of popular dishes to avoid shortages during busy periods. E. Inventory Turnover: A metric indicating the efficiency of inventory usage and replenishment. A high turnover rate signifies that products are selling quickly, reflecting positively on sales performance. 07 Handout 1 *Property of STI Page 5 of 12 BM2408 F. Reorder Point: The specific inventory level that triggers a reorder to replenish stock. For example, a bookstore may establish a reorder point for a bestselling title, prompting a new order as soon as the stock falls below that threshold. G. Vendor-Managed Inventory (VMI): A collaborative approach where suppliers take responsibility for managing their products’ inventory levels at a client’s location. For instance, a beverage supplier may oversee stock replenishment at a grocery store to ensure consistent availability. H. Demand Forecasting: The process of leveraging historical data and statistical analysis to project future product demand. A clothing retailer might apply this method to predict seasonal trends and adjust inventory levels accordingly. Inventory Management Challenges While inventory management may appear straightforward, it presents various challenges that can significantly impact business operations. Here are some prevalent issues and their consequences: Demand Uncertainty: Accurately forecasting future demand is challenging, particularly for new products or seasonal items. A fashion retailer may struggle to predict demand for a new trend, resulting in stockouts or surplus inventory. Supply Chain Disruptions: Delays, quality concerns, or even supplier bankruptcies can hinder inventory flow. For example, a manufacturing company might encounter production delays due to a supplier’s labor strike. Rapid Technological Changes: Products can quickly become outdated, especially in fast-paced industries like electronics or fashion. A smartphone manufacturer may observe declining interest in older models as new versions emerge. Inventory Costs: The expenses related to storing inventory can be substantial, particularly for large or perishable items. A grocery store may face elevated costs from storing perishable food items with limited shelf life. Stockouts: Running out of stock can lead to missed sales opportunities and customer dissatisfaction. A customer looking for a popular tool at a hardware store may leave empty-handed, opting instead to purchase from a competitor. Carrying Costs: Holding onto excess inventory can tie up capital and incur increased storage fees. A retailer may overstock a seasonal product that fails to sell, resulting in elevated storage costs and potential markdowns. Data Accuracy: Mistakes in inventory data can lead to stockouts, overstock situations, and financial losses. A warehouse with incorrect product quantity records may experience unforeseen stockouts or excess inventory. Demand Fluctuations: Businesses selling seasonal products must effectively manage inventory levels to meet peak demand while avoiding excess stock in off-peak times. For example, a toy retailer needs to adjust inventory levels accordingly to prepare for increased demand for holiday gifts. Project Management 07 Handout 1 *Property of STI Page 6 of 12 BM2408 What is Project Management? (Besterfield, 2024) Project management is the discipline of organizing and managing resources to achieve specific goals within a defined scope, schedule, and budget. It involves planning, organizing, motivating, and controlling resources (people, equipment, and materials) to achieve a specific project objective. Objectives of Project Management The primary objective of project management is to deliver a project successfully by: Achieving project goals: Ensuring that the project meets its defined objectives and delivers the desired outcomes. Satisfying stakeholders: Meeting expectations of all stakeholders involved in the project, including customers, sponsors, and team members. Increased Efficiency: It helps streamline processes and optimize resource allocation, leading to improved efficiency and productivity. Improved Decision-Making: By simply providing data-driven insights and risk assessments, project management enables informed decision-making. Enhanced Stakeholder Satisfaction: Effective project management ensures that projects are delivered on time, within budget, and to the desired quality, leading to satisfied stakeholders. Risk Mitigation: Project management helps organizations avoid costly mistakes and delays by proactively identifying and addressing potential risks. Competitive Advantage: Successful project management can differentiate organizations from their competitors by enabling them to deliver innovative products and services faster and more efficiently. Project Management Process (Jacobs, 2024) Project management involves several key components: Step 1: Initiation: Defining the project's purpose, scope, and goals. Example: A software development company wants to create a new mobile app for their customers. They define the app's features, target audience, and desired outcomes. They identify stakeholders such as the CEO, product manager, developers, and designers. They create a project charter that outlines the app's scope, timeline, and budget. Step 2: Planning: Developing a detailed plan outlining tasks, resources, and timelines. For example, a construction company creates a project plan for building a new office building, including timelines for each phase of construction. Example: The software development company creates a detailed project plan, breaking down the project into tasks such as requirements gathering, design, development, testing, and deployment. They identify dependencies between tasks, such as the need to complete the design before starting development. They create a communication plan outlining how team members will communicate and provide updates. They identify potential risks, such as delays in obtaining necessary approvals or changes in requirements, and develop contingency plans to address them. Step 3: Executing: Carrying out the planned activities and managing the project team. For example, a marketing team executes a product launch campaign, including advertising, public relations, and event planning. 07 Handout 1 *Property of STI Page 7 of 12 BM2408 Example: The software development team assigns tasks to developers, designers, and testers. They use project management software to track the progress of each task and identify any potential delays. They ensure that resources such as hardware, software, and personnel are available as needed. They address any issues or problems that arise, such as bugs in the code or changes in requirements. Step 4: Monitoring and Controlling: Tracking progress, identifying issues, and taking corrective actions. For instance, a project manager monitors the progress of a website development project using project management software and adjusts as needed. Example: The project manager regularly reviews the project's progress against the plan and identifies any variances, such as tasks that are behind schedule or over budget. They take corrective action, such as reallocating resources or adjusting the timeline. They provide regular updates to stakeholders, including the CEO, product manager, and other interested parties. Step 5: Closing: Completing the project, evaluating results, and documenting lessons learned. An example of this can be a construction company that closes a project by conducting a final inspection, obtaining necessary permits, and documenting the project's outcomes. Example: The software development team completes the app and delivers it to the product manager. They evaluate the project's success against the original goals and objectives. They document any lessons learned, such as the importance of early involvement of stakeholders or the effectiveness of certain project management tools. They obtain formal approval from the CEO and product manager to officially close the project. Essential Tools and Techniques in Project Management (Shafer, 2024) Project management encompasses a diverse range of tools and methodologies that empower organizations to plan, execute, and monitor projects with efficacy. Below are some of the most prevalent techniques, accompanied by examples and explanations: A. Work Breakdown Structure (WBS): This tool organizes a project into a hierarchical structure of smaller, manageable tasks. In a software development project, tasks may include requirements gathering, design, coding, testing, and deployment. Figure 1: Work Breakdown Structure Source: https://www.blog.ganttpro.com B. Gantt Chart: A visual timeline illustrating a project schedule, including task durations and dependencies. For instance, a construction project may utilize a Gantt chart to display the sequence and timing of tasks such as foundation work, framing, roofing, and finishing. 07 Handout 1 *Property of STI Page 8 of 12 BM2408 Figure 2: Gantt Chart Source: https://www.blog.ganttpro.com C. Program Evaluation and Review Technique (PERT): This probabilistic method estimates project duration by analyzing optimistic, pessimistic, and most likely scenarios for each activity. In software development, PERT can project the duration of coding tasks, factoring in code complexity and developer experience. Figure 3: Program Evaluation and Review Technique (PERT) Source: www.geeksforgeeks.com D. Risk Response Planning: Strategies are developed here to mitigate, avoid, transfer, or accept risks. A manufacturing business development project may draft a contingency plan to address possible delays by earmarking additional resources. 07 Handout 1 *Property of STI Page 9 of 12 BM2408 Figure 4: Risk Response Planning Source: https://www.slideteam.net E. Project Charter: This formal document establishes the project's scope, objectives, and deliverables. A marketing campaign could be initiated with a project charter that delineates the target audience, key messages, and expected outcomes. Figure 5: Project Charter Source: https://www.techno-pm.com 07 Handout 1 *Property of STI Page 10 of 12 BM2408 Project Management Challenges (Shafer, 2024) Several factors can hinder effective project management: Lack of Clear Goals: If project goals are not clearly defined and communicated, it can lead to confusion and misalignment among stakeholders. Inadequate Resource Allocation: Insufficient resources (e.g., budget, personnel, equipment) can delay project progress and compromise quality. Scope Creep: Uncontrolled changes to the project's scope can increase costs, delay, and decrease quality. Poor Communication: Ineffective communication among stakeholders can result in major confusion, misunderstandings, conflicts, and delays. Risk Management Failures: Failure to identify and address potential risks can lead to unexpected challenges and project failures. Lack of Leadership: A weak or ineffective project leader can hinder the team's motivation and productivity. Process Review and Improvement (Besterfield, 2024) What is Process Review and Improvement? Process review and improvement is a structured methodology for analyzing and optimizing business processes to boost efficiency, effectiveness, and quality. It involves pinpointing areas that need enhancement, implementing necessary changes, and assessing the outcomes. Objectives of Process Review and Improvement The fundamental goal of process review and improvement is to refine business processes by: Identifying Opportunities: Highlighting areas ripe for enhancement in efficiency, effectiveness, and quality. Implementing Changes: Executing essential modifications to processes to reach the desired outcomes. Measuring Results: Evaluating the impact of changes on performance indicators. Fostering Continuous Improvement: Building a culture of perpetual process enhancement. Increased Efficiency: Streamlining processes and eliminating waste allows organizations to enhance their overall productivity significantly. Enhanced Quality: Optimized processes often yield superior products or services, leading to heightened customer satisfaction and loyalty. Reduced Costs: Identifying and removing inefficiencies can lower operational costs, including expenses related to materials and labor. Competitive Advantage: Process improvement enables organizations to distinguish themselves from competitors by delivering exceptional value to customers. Key Steps of Process Review and Improvement Step 1: Process Identification: Determining which processes will be reviewed. A manufacturing firm may select production, quality control, and logistics for evaluation. 07 Handout 1 *Property of STI Page 11 of 12 BM2408 Step 2: Process Analysis: Assessing the status of the process, including inputs, outputs, activities, and decision points. A customer service team may examine the workflow for addressing inquiries and assessing steps, response times, and satisfaction levels. Step 3: Process Improvement Identification: Recognizing potential enhancements, such as eliminating superfluous steps, reducing cycle times, or elevating quality. For example, a retail store may observe long checkout lines and introduce self-checkout stations to cut wait times and enhance satisfaction. Step 4: Process Improvement Implementation: Making changes to address identified shortcomings. For example, a manufacturing firm might adopt new technology to automate certain production tasks, decreasing manual labor and boosting efficiency. Step 5: Process Measurement and Evaluation: Assessing the effects of changes on performance metrics and the overall efficacy of the improvements. A customer service department may track satisfaction levels pre-and post-implementation of alterations in inquiry handling. Challenges to Process Review and Improvement Several obstacles can impede effective process review and improvement, including: Resistance to Change: A manufacturing plant employees may hesitate to adopt new technology Lack of Resources: A small business might lack the budget to engage consultants or invest in new software. Poor Communication: Ineffective inter-departmental communication can cause misunderstandings and delays, as seen when the sales team is unaware of production modifications. Lack of Data: Without necessary data, such as customer satisfaction metrics, a customer service team may struggle to identify improvement areas. Short-Term Focus: Some companies favor quick profits over sustainable process improvements, avoiding long-term investments. Lack of Leadership Support: A deficiency in executive backing for improvement initiatives can hinder employee buy-in and resource allocation. Complexity of the Process: Complicated processes with numerous interdependent steps can obscure improvement opportunities. Fear of Failure: Employees might resist suggesting changes or new approaches out of fear of adverse repercussions. Successfully overcoming these hurdles is vital for effective process review and improvement. Organizations must cultivate a culture of continuous improvement, provide adequate resources, foster transparent communication, and promote innovative experimentation. References Besterfield, D. (2024) Total Quality Management. Pearson Davis, S. (2024). Total Quality Management: An Integrated Approach. Butterworth-Heinemann Publications George, S. (2024) Total Quality Management: Strategies and Techniques Proven Today’s Most Successful Companies. Wiley LLC. Jacobs, R. (2024). Operations and Supply Chain Management. McGraw-Hill Education Shafer, M. (2024). Operations Management for MBAs. Wiley Publications 07 Handout 1 *Property of STI Page 12 of 12