Total Quality Management (TQM) in the Clinical Laboratory PDF
Document Details
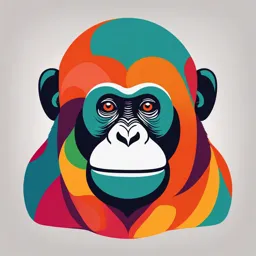
Uploaded by ExtraordinaryCosmos9683
University of Cape Coast
Tags
Summary
This presentation discusses Total Quality Management (TQM) in clinical laboratories at the University of Cape Coast, in Ghana. It covers the essential aspects, including laboratory systems, workflows, and the importance of quality management in medical settings.
Full Transcript
UNIVERSITY OF CAPE COAST Cape Coast, Ghana Cape Coast, Ghana Total Quality Management (TQM) in the clinical laboratory Essential to all aspects of health care are laboratory results that are ï‚§ accurate, ï‚§ reliable, and ï‚§ timely 2 How do we ach...
UNIVERSITY OF CAPE COAST Cape Coast, Ghana Cape Coast, Ghana Total Quality Management (TQM) in the clinical laboratory Essential to all aspects of health care are laboratory results that are  accurate,  reliable, and  timely 2 How do we achieve excellent performance in the laboratory? 3 Complexity of a Laboratory System Reporting Patient/Client Prep Sample Collection Personnel Competency Test Evaluations Data & Laboratory Management Safety Customer Sample Receipt and Service Accessioning Record Keeping Sample Transport Quality Control Testing 4 Path of Workflow THE PATIENT Test selection Sample Collection Preexamination Phase Sample Transport Laboratory Analysis Examination Phase Report Report Transport Creation Result Interpretation Postexamination Phase 5 WHY is the Path of Workflow essential to consider in health laboratories? The entire process of managing a sample must be considered:  the beginning: sample collection  the end: reporting and saving of results  all processes in between. 6 Laboratory tests are influenced by  laboratory environment  knowledgeable staff  competent staff  reagents and equipment  quality control  communications  process management  occurrence management  record keeping 7 Organization Responsibilities, Authorities Quality Policy Provision Communication of resources 8 Personnel  human resources  job qualifications  job descriptions  orientation  training  competency assessment  professional development  continuing education 9 Equipment  acquisition  installation  validation  maintenance  calibration  troubleshooting  service and repair  records 10 Purchasing and Inventory vendor qualifications supplies and reagents critical services contract review inventory management 11 Process Control quality control sample management method validation method verification Introduction Laboratory Quality Management 12 System-Module 1 Information Management  confidentiality  requisitions  logs and records  reports  computerized laboratory information systems (LIS) 13 Documents Records creation collection revisions and review review control and distribution storage retention 14 Laboratory Assessment Internal External Proficiency testing (EQA) Inspections Accreditations 15 Process Improvement Opportunities for improvement (OFIs) Stakeholder feedback Problem resolution Risk assessment Preventive actions Corrective actions 16 Facilities and Safety  Safe working environment  Transport management  Security  Containment  Waste management  Laboratory safety  Ergonomics 17 Twelve Quality System Essentials Organization Personnel Equipment set of coordinated activities that Purchasing Information Process function as & Inventory Control Management building blocks for Documents Occurrence quality & Records Management Assessment management Process Customer Facilities Improvement Service & Safety 18 Importance of High Quality Laboratory Service Accurate, reliable and timely laboratory results are essential to all aspects of health care 19 Mission of Health Laboratory Services Provide high quality services: in the right place in the right time in respect of the needs of – patients – community – health staff clinicians epidemiologists environmental sanitarians 20 Quality Management System Definition Coordinated activities to direct and control an organization with regard to quality (ISO,CLSI). All aspects of the laboratory operation need to be addressed to assure quality; this constitutes a quality management system. 21 How Do We Achieve Excellent Performance in the Laboratory? Importance of Quality Systems Different techniques and concepts have been developed to improve product or service quality ISO 9000 series of standards – widely used – outlines the systemic approach to quality 22 International Organization for Standardization (ISO) Non-governmental organization established in 1947 Worldwide federation of national standards bodies of 149 countries Develops voluntary consensus standards (and other types of document) 23 ISO 9000 Family Guidance for quality in manufacturing and service industries Has broad applicability, many kinds of organizations can use ISO 9001:2000, Quality management system – Requirements 24 ISO Documents - Laboratory ISO 15189:2007, Medical laboratories - Particular requirements to quality and competence Valuable compilation of statements to assist laboratory specialists in understanding and implementing quality management systems Has become the international foundation for medical laboratory accreditation 25 ISO 15189:2007: Content Management Technical Requirement Requirements Organization Quality management system Personnel authorities and Document control responsibilities Contract review Accommodation and Referral laboratories environmental conditions Supplier review Laboratory equipment Advisory services Pre-examination Complaint resolution Identification and control of procedures nonconformities Examination procedures Corrective actions Assuring quality of Preventive actions examination procedures Continual Improvement Post-Examination Quality and technical records procedures Internal audits Annexes Reporting of results Management review 26 National Committee for Clinical Laboratory Standards (NCCLS) in 2005 A committed forum for laboratory improvement through consensus, guidelines, and standardization. Today CLSI has approximately 2,200 members International in scope and participation – World Health Organization Collaborating Centre – Secretariat – ISO Technical Committee 212 Ten area committees addressing the full range of laboratory activities. 27 CLSI Quality Standards Guideline No. Title HS1-A2 A Quality Management System Model for Health Care  Describes quality system model, 12 essentials  Applicable to all health care systems,  Applies quality design consistent with ISO 9000 series GP 26-A3 Application of Quality Management System Model for Laboratory Services Laboratory application document for quality system Describes path of workflow Assists lab in improving processes relates to HS1-A2 and ISO 15189 28 ISO vs. CLSI Complimentary not conflicting roles ISO provides broad standard requirements CLSI provides detailed best practices, standards and practical guidance for implementation 29 Standards Organizations ISO CLSI International Organization Clinical and Laboratory for Standardization Standards Institute (formerly known as NCCLS) Guidance for quality in Standards, guidelines, and manufacturing and service best practices for quality in industries medical laboratory testing Broad applicability; used Detailed; applies by many kinds of specifically to medical organizations laboratories Uses consensus process in Uses consensus process in developing standards developing standards Introduction Laboratory Quality Management 30 System-Module 1 Quality System Organizational structure, resources, processes and procedures needed to implement quality management (ISO, CLSI) 31 Quality System Essentials Set of coordinated activities that function as building blocks for quality management 32 Application of a Quality System Approach Helps Ensure quality of overall process Detect and reduce errors, Improve consistency within and between laboratories Contain costs Ensure customer satisfaction 33 Who Is Responsible for Quality in the Laboratory? EVERYONE! 34 Implementing Quality Management does not But it detects guarantee errors that may an occur and ERROR-FREE prevents them Laboratory from recurring 35 Organizatio Personnel Equipment n Laboratories not Purchasing & Process Control Information Management implementing a Inventory quality management Documents Occurrence Assessmen system guarantees & Manageme t Records nt UNDETECTED ERRORS Process Customer Facilities Improvement Service & Safety 36 In summary Quality management is not new. Quality management grew from the good works of innovators who defined quality over a span of 80 years. Quality management is as applicable for the medical laboratory as it is for manufacturing and industry. 37