Hazard Control - Spring 2024/25 Training PDF
Document Details
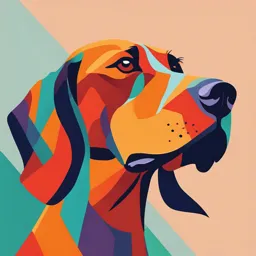
Uploaded by almaha
2024
Tags
Related
- Bioenvironmental Engineering Apprentice Block IV: Chemical Controls PDF
- Advanced Safety Concepts PDF
- RMS-C-2: Introduction to Safety (PDF)
- Occupational Health and Safety Practices in Tourism and Hospitality Industry PDF
- Risk Management and Hazard Control Process PDF
- Workplace Environmental Health Issues PDF
Summary
This presentation covers hazard control, including objectives to eliminate or minimize hazardous incidents at the workplace. It discusses the hazard control hierarchy, inherent safety, engineering controls like pressure relief valves and alarm systems, and administrative controls for hazard management. The presentation also covers personal protective equipment (PPE).
Full Transcript
Hazard Control Spring 2024/25 Introduction to Hazard Control The main objectives of hazard control is to eliminate or minimize the adverse effects of the identified hazardous incidents at the workplace. Once the hazards have been identified and evaluated, then the safety and process e...
Hazard Control Spring 2024/25 Introduction to Hazard Control The main objectives of hazard control is to eliminate or minimize the adverse effects of the identified hazardous incidents at the workplace. Once the hazards have been identified and evaluated, then the safety and process engineers can determine what can be done to protect the workers, the environment, and the surrounding community from these hazards. Engineers will determine if they can eliminate the hazards. Sometimes, the hazards cannot be eliminated due to cost and lack of technology. Introduction to Hazard Control Engineers will typically follow the hazard control hierarchy: Inherent Safety Apply engineering controls, which are equipment-related methods of control; Apply administrative control, which are documented rules and procedures Require personal protective equipment (PPE) Introduction to Hazard Control Inherent Safety Can a less toxic or non-toxic chemical be used instead of the currently 1.0 highly toxic chemical? Engineering Hazard Control Hierarchy If a less toxic chemical cannot be found, can the system be designed Control Consider a 2.0 (add-on system: e.g relief valve, alarm system) to greatly reduce or situation where make non-existent the risk of exposure to personnel? you are planning to mitigate hazards in a Administrative reaction system Control If exposure is still possible, what procedures need to be in place to 3.0 further reduce the exposure? Equipment Protective Personal What PPE is required by workers to protect them from exposure? 4.0 Inherent Safety An inherently safe plant relies on chemistry and physics to prevent accidents rather than on control systems, interlocks, redundancy, and special operating procedures. An inherently safer design of a process plant is one that avoids hazards instead of controlling them, particularly by reducing the amount of hazardous material and the number of hazardous operations in the plant. Inherent Safety Principles: Elimination, Minimization, Substitution, Attenuation, Limitation of Effects, Simplification Engineering Controls Engineering Control Engineering controls in process safety refer to physical interventions or design measures implemented to eliminate or reduce hazards associated with chemical processes, machinery, or operations. They aim to either prevent hazardous incidents from occurring or mitigate their consequences if they do occur. Safety Instrumented Systems (SIS): Automated shutdown systems. Emergency shutdown (ESD) valves. Pressure Relief Devices: Example of Pressure safety valves (PSV). Engineering Pressure Relief Valve. Controls Containment and Isolation: Double-walled tanks. Leak-proof piping and isolation valves. Ventilation and Extraction Systems: Local exhaust ventilation to remove toxic gases or vapors. Explosion-proof ventilation systems. Pressure Relief Valve Opens gradually and proportionally to the increase in system pressure. As pressure rises slightly above the set point, the valve opens just enough to relieve the excess. Typically designed with a spring-loaded mechanism that adjusts based on system pressure. Set pressure point is typically close to the operating pressure, so it can respond to minor pressure fluctuations without causing full system shutdown. Pressure Safety Valve A Pressure Safety Valve (PSV) is a type of valve used to quickly release gasses from equipment in order to avoid over pressurization and potential process safety incidents. PSVs are activated automatically when pressure exceeds prescribed pressure limits in order to return equipment pressure to a safe operating level. Automatic Detection and Alarm Systems: Gas, smoke, fire, or leak detectors integrated with alarms and automatic actions. Example of Process Control and Automation: Engineering Distributed control systems (DCS) to maintain safe Controls operational parameters. Redundant control systems and interlocks. Emergency Containment Structures: Dikes or bunds around chemical storage tanks. Secondary containment areas. Gas Detectors Gas detectors are critical for monitoring and ensuring safety by detecting hazardous gases that could pose health, explosion, or environmental risks Flammable gas detectors are essential safety devices used to detect the presence of combustible gases in various environments, especially where gases like methane, propane, butane, hydrogen, or other flammable gases are used or stored Toxic gas detectors are crucial safety devices designed to detect hazardous gases in the environment to prevent health risks or fatalities. Engineering Controls: Fail Safe Design Fail safe designs use a system (usually a computer) that notices when process variables are about to enter undesirable ranges and which then defaults into a fail-safe state. Automatic shutdown devices (fail safes) are activated by temperature, pressure, flow, level, and process composition values. This put the system in the safest possible state where it waits for the user to intervene or reset the system. Engineering Controls: Redundancy Systems should be designed to function normally even when a single instrument or control functions or prime movers (e.g. pumps, compressors) fail. This is achieved with redundant controls and equipment, including two or more measurements, processing paths and actuators that ensure system operates safely and reliably. Redundancy is based upon how critical an unwanted event is to worker safety or process continuation or the potential economic losses Engineering Controls: Weak-Link A weak link is one designed to fail at a certain level of stress in order to minimize and control any possibility of a more serious failure or accident. Weak links have been used in electrical, mechanical and structural systems for safety purposes. The most common use of a weak link has been electrical fuses, which have been designed to fail before more valuable parts are damaged. Engineering Controls: Alarms Alarms are devices that alert the process engineer to an abnormal or out-of-specification condition. There are usually audible (buzzer or horn) and visual (flashing symbol or colour on a computer screen). Types of Alarm Process Alarms Safety Alarms Equipment Alarms High/Low Alarms: Triggered when Emergency Shutdown (ESD) Mechanical Failure Alarms: Alert a process variable (like Alarms: Initiate an emergency operators to potential or actual temperature, pressure, or flow) shutdown of the process when a mechanical faults in equipment, exceeds or drops below a preset critical condition is detected to such as pumps, motors, or limit. prevent catastrophic failures. compressors. Rate of Change Alarms: Activated Fire and Gas Alarms: Detect Power Failure Alarms: Signal loss when a process variable changes smoke, flames, or gas leaks and of power to critical equipment or too quickly, indicating a possible alert personnel to evacuate or systems, enabling operators to fault or abnormal condition. take immediate action. take corrective actions. Deviation Alarms: Triggered when Leak Detection Alarms: Used for Vibration Alarms: Detect unusual there is a significant difference detecting leaks in pipes, vessels, levels of vibration in rotating between a setpoint and the actual or other containment systems, equipment, which could indicate value, often used in systems with often important in hazardous bearing wear or imbalance. setpoint tracking. material handling. Engineering Controls: Process Upset Control System Flare Flares are basically a safety relief system used to burn waste gases and for the emergency dumping of gases from an upset unit. Toxic and flammable gases cannot be vented to the atmosphere because of safety, health and environment concerns. Vented gases empty into a flare header and are swept into the flare and burned. Pressure Relief PRVs protect pressure vessels or piping from becoming overpressured. They open when excessive pressure threaten a vessel. The material released is normally vented to a line that empties into a flare header. Engineering Controls: Process Upset Control System Explosion Suppression Explosion suppression system usually are walls designed to contain explosions. e.g blast proof control room The walls are called blast walls and may be built around a particular unit or vessel that contains very unstable materials or reactive chemicals. Bundall and Dikes Bund wall and Dikes are simple structures (devices) to contain and/or direct spills to a safe location. Encircle storage tanks and should be able to contain the entire contents of the ruptured or leaking tank. Bund Wall Example of Bund wall Engineering Controls: Isolation, Lockouts, Lockins and Interlocks Isolation, lockouts, lockins and interlocks are some of the most commonly used safety measures built on three basic principles or else on combinations of the first two, which are: 1. Isolating a hazard once it has been recognized. 2. Preventing incompatible events from: a) occurring, b) occurring at the wrong time, c) occurring in the wrong sequence. 3. Providing a release after suitable and correct action has been taken. Administrative Control Administrative Control Administrative controls are procedures put into place to limit employee exposure to hazards. Their function is to influence worker behaviour. Enforcement of these procedures may involve penalties that vary in severity and can include termination of employment. Administrative controls can be divided down into two broad categories: 1. Programs: Programs are the written documents that explain how hazards are to be controlled 2. Activities: Activities are the programs put into action Administrative Control Item Program Activities Training   Housekeeping  Permit System  Safety Inspection  Safety Audits  Safety Investigations HAZOP   Safe work observation  Fugitive Emission Monitoring  Administrative Control Administrative programs are the written documents that explain how hazards are to be controlled. Often, these documents are put in frames and displayed at strategic locations for employees and visitors to read (e.g. evacuation plans during a fire). New employees are given copies of the administrative programs during their orientation and training so that they can learn and embrace the requirements as set out in the documents. Administrative Controls A partial list of the more common administrative control programs includes: ✓Policy Statements, which in effect are a business’s guiding principles. ✓Principles, which are set of rules or standards. ✓Rules, which are statements of how to do something or what may or may not be done. ✓Plans, which are methods prepared in advance for carrying out actions. ✓Procedures, which are step-by-step instructions for accomplishing a task. Administrative Programs Evacuation and Accountability Plans Evacuation and accountability plans are established procedures that outline the evacuation routes and assemble areas for prompt evacuation and accounting of personnel in the event of an emergency. Manufacturing plants have evacuation routes and primary and alternative assembly areas. The assembly area chosen depends on the wind direction and how close the hazard is to the assembly area. Once personnel gather at the assembly area, an accounting (head count) is made to verify everyone has exited the unit or building Administrative Programs Cardinal Rules Cardinal rules are very important rules, that if broken, have severe disciplinary consequences, such as time off (suspension) without pay or termination. A violation of a cardinal rule can cause a major safety or environmental incident Cardinal rules are not required by any regulatory agency but are considered a best management practice in the process industry. Administrative Programs Cardinal Rules The following are examples of some of the cardinal rules in use throughout most industries: No alcoholic beverages can be brought to or consumed at the workplace. Using drugs or being under the influence of drugs within the company’s boundaries is prohibited. Possessing firearms within the boundary of the plant site, either the personnel’s vehicle on his/her body, is prohibited. Workers are not allowed to fight with or threaten other employees with violence. Possessing matches or lighters and smoking are prohibited in restricted areas Administrative Programs Mutual Aids Agreements Mutual aid agreements are agreements between each manufacturing site managers and local government agencies to render aid in case of need. All manufacturing plants of significant size that deal with hazardous materials should have their own fire departments and trained first-aid personnel. Where two or more of these type of plants fairly close together, each site’s emergency response coordinators should develop a mutual aid agreement to render aid in the event of a release or other hazardous situation. If one site has a large fire and the site’s fire fighting department has only one fire truck, a radio call can bring more trucks and firefighters from other sites or from the nearest municipality (Bomba) to help control and douse the fire. Administrative Programs Buddy System Some tasks in a chemical process plant are so hazardous that lone individuals should never attempt to do them on their own. The buddy system is employed to monitor and safeguards persons who undertake hazardous operations. There are two common buddy system methods: 1. Two persons constitute a buddy pair and are subjected to the same hazard at the same time and under the same conditions. Each must look out for the well-being of the other, monitoring the other’s activities and providing assistance when required. 2. Only one of the pair is exposed to the hazard. The other’s sole duty is to protect and assist the person in danger, should the need arise. Administrative Programs Hazard Communication (HAZCOM) The intent of the hazard communication or HAZCOM program is to ensure that information concerning the hazards of all chemicals produced as: the final commercially valuable product or intermediates or wastes or imported raw materials or Solvents are made known to employees. A written HAZCOM program is a blueprint that describes how a company will achieve the goals set by authorities. Types of Labels NFPA Diamonds and HMIS Bars are Color & Number Coded with Hazard Information DOT Symbols Are Usually Found on Shipping Cartons 35 NFPA Diamond NFPA 704: STANDARD SYSTEM FOR THE IDENTIFICATION OF THE HAZARDS OF MATERIALS FOR EMERGENCY RESPONSE Red - Flammability Blue Health Yellow -instability / reactivity White – Special notes NFPA Diamond NFPA Diamond HMIS Bars HMIS - Hazardous Materials Identification System Blue Health Red - Flammability Orange –physical hazard White – personal protection HMIS Bars Blue Health 4. Life-threatening, major or permanent damage may result from single or repeated overexposures (e.g., hydrogen cyanide). 3. Major injury likely unless prompt action is taken and medical treatment is given. 2. Temporary or minor injury may occur. 1. Irritation or minor reversible injury possible. 0. No significant risk to health. HMIS Bars Red - Flammability 4. Flammable gases, or very volatile flammable liquids with flash points below 73 °F (23 °C), and boiling points below 100 °F (38 °C). Materials may ignite spontaneously with air (e.g., Propane). 3. Materials capable of ignition under almost all normal temperature conditions. Includes flammable liquids with flash points below 73 °F (23 °C) and boiling points above 100 °F (38 °C), as well as liquids with flash points between 73 °F and 100 °F. 2. Materials which must be moderately heated or exposed to high ambient temperatures before ignition will occur. Includes liquids having a flash point at or above 100 °F (38 °C) but below 200 °F (93 °C) (e.g., Diesel fuel). 1. Materials that must be preheated before ignition will occur. Includes liquids, solids and semi solids having a flash point above 200 °F (93 °C) (e.g., Canola oil). 0. Materials that will not burn (e.g., Water). HMIS Bars Orange – Physical Hazard 4. Materials that are readily capable of explosive water reaction, detonation or explosive decomposition, polymerization, or self-reaction at normal temperature and pressure 3. Materials that may form explosive mixtures with water and are capable of detonation or explosive reaction in the presence of a strong initiating source. Materials may polymerize, decompose, self-react, or undergo other chemical change at normal temperature and pressure with moderate risk of explosion. 2. Materials that are unstable and may undergo violent chemical changes at normal temperature and pressure with low risk for explosion. Materials may react violently with water or form peroxides upon exposure to air. 1. Materials that are normally stable but can become unstable (self-react) at high temperatures and pressures. Materials may react non-violently with water or undergo hazardous polymerization in the absence of inhibitors. 0. Materials that are normally stable, even under fire conditions, and will not react with water, polymerize, decompose, condense, or self-react. Non-explosives. HMIS Bar Yellow Reactivity / Instability Administrative Program Safety Signage 5.3 Administrative Controls 5.3.2 Administrative Activities Administrative activities in hazard control are the administrative programs put into action. Administrative hazard control activities can consist of any of the following: Training – providing instruction on job tasks, skills, and knowledge. Housekeeping – maintaining a clean, neat, orderly, and safe workplace. Permit system – preparing a job site to ensure conditions are safe for a specific task to begin. Safety inspection – conducting regular, scheduled checks to 45 ensure a safe and healthy KR4743 workplace. 45 5.3.2 Administrative Activities Safety audits – conducting regular and scheduled checks for compliance with safety, health and environmental regulations and procedures. Safety investigations – taking action to determine the cause or causes of an incident or accident. HAZOP – conducting a hazard and operability study to identify any possible flaws in a system, operation, or piece of equipment that could lead to an accident. Fugitive emissions monitoring – taking samples around operating equipment to determine if toxic or hazardous substances are present at unacceptable levels that are dangerous to workers and polluting to the environment. 46 KR4743 46 5.3.2 Administrative Activities Safe work observations – looking at selected work practices on a regular basis and providing feedback on the safe and potential unsafe acts observed. Safety activities require management support and commitment of budget. Expenses include: Overtime costs for people in training; Expended material costs, such as refilling fire extinguishers after fire training, providing respirators, etc.; Consultant or special schooling fees, such as sending emergency response members to firefighting schools. 47 KR4743 47 Personal Protective Equipment (PPE) Personal Protective Equipment Personal protective equipment (PPE) is the equipment persons wear for protection against an accident. Though most employees understand the need for PPE, many neglect the use of it due to laziness, because they are willing to take a risk, or because they consider the PPE too uncomfortable to wear. Management must have a proactive program and enforce this method of hazard control. The need of PPE can be divided into three categories: 1. For a scheduled hazardous operation, such as sample collecting, protective gloves and a respirator might be required. 2. For investigative and corrective purposes, it may be necessary to determine whether an environment has become dangerous because of chemical leak. The chemical might be toxic. An air pack (breathing apparatus) and chemical suit might be required in this instance. 3. For accidents, which may be severest requirement, the first few minutes after an accident occurs may be the most critical reaction time in which to suppress or control any injury or damage. Because of this, PPE must be simple, i.e. easy to wear and operate. Personal Protective Equipment