Procedimientos de Fabricación TI1-T6.1 PDF
Document Details
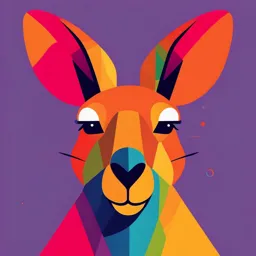
Uploaded by DaringKhaki9129
Tags
Summary
Este documento proporciona una introducción a los procedimientos de fabricación, incluyendo técnicas como moldeo, sinterizado y deformación. Explica diferentes métodos a través de ejemplos y se centra en diversos tipos de procesos de fabricación.
Full Transcript
TI1-T6.1-Procedimientos de fabricación: Técnicas y procedimientos de fabricación Procedimientos de fabricación: Técnicas y procedimientos de fabricación Tecnología Industrial 1º Bachillerato...
TI1-T6.1-Procedimientos de fabricación: Técnicas y procedimientos de fabricación Procedimientos de fabricación: Técnicas y procedimientos de fabricación Tecnología Industrial 1º Bachillerato Contenidos Procedimientos de fabricación Técnicas y procedimientos de fabricación La fabricación de productos consiste en la obtención de productos artificiales a partir de los distintos materiales. Probablemente se trate del proceso técnico más trascendente de la humanidad. Los procesos de fabricación son procesos complejos que requieren un elevado número de operaciones con un importante grado de dificultad. Estos procesos se vienen realizando desde tiempos remotos y las técnicas de ejecución se han ido depurando y mejorando con el paso del tiempo. Imagen de FJ Martínez en INTEF. Licencia CC Fue a partir de la segunda mitad del siglo XVII cuando la sociedad sufre una profunda transformación, que se dio en llamar Revolución Industrial. A partir de ese instante se produjo el desarrollo o mejora en muy corto espacio de tiempo de un elevado número de técnicas de fabricación. Esto hizo que aumentara de forma muy importante el número y calidad de elementos fabricados por la mano del hombre, lo que a su vez provocó un importante cambio en la estructura social de la época, dando paso a que la sociedad campesina empezase a convertirse en obrera. La población fue abandonando el campo y empezó a reunirse alrededor de la fábrica que se convirtió en el nuevo núcleo de la sociedad. A lo largo de este tema vamos a estudiar los diferentes métodos de fabricación más importantes en la actualidad. 1. Fabricación sin pérdida de masa Encontramos las siguientes técnicas de fabricación: Moldeo o fundición: proceso de fabricación de piezas, metálicas o de plástico, consistente en elevar la temperatura de un material hasta que funde e introducirlo en un molde, con la forma que deseamos obtener, donde solidifica. Colada Imagen de AB5602 en Wikimedia. CC Sinterizado: Proceso de fabricación en el que se parte de una materia prima en forma de polvo fino. El polvo inicial se compacta para darle la forma determinada, y a continuación se calienta a una temperatura inferior a la de fusión de la mezcla. Esto hace que se incremente la fuerza y la resistencia de la pieza, al crearse enlaces fuertes entre sus partículas. Por deformación:En todos los procesos de fabricación de este tipo, la masa del material y su volumen permanecen constantes. En todos ellos se modifica la forma de la pieza al aplicar fuerzas externas.Las ventajas más significativas de estos métodos de conformación son el que no se pierde material y se pueden obtener piezas con formas muy diversas, el proceso se puede llevar a cabo en frío o en caliente. Encontramos la laminación, la estampación, el trefilado y la extrusión. Forja Imagen en INTEF. CC 1.1 Conformación por moldeo El método de trabajo parte de la obtención de un modelo de cera, yeso o madera de la pieza que se quiere fabricar. Sobre este modelo se construye un molde, que será de arena o de metal. Cuando la pieza original es hueca, se necesita también fabricar machos, que son las piezas que ocupan los huecos interiores en el molde. Al construir el molde hay que diseñar los conductos por los que se tiene que verter el material fundido, (bebederos) y los conductos por los que debe evacuarse el posible material sobrante (mazarotas). El proceso de vertido del material fundido en el molde se denomina colada. Ésta puede producirse por gravedad, cuando el material ocupa el molde por su propio peso, o por presión cuando el llenado del molde ocurre por la acción de un elemento que inyecta el material con presión. Una vez solidificado el material se procede a extraer la pieza del molde o desmoldeo. Elaboración propia Los métodos de conformación por moldeo se clasifican según el material del cual esté elaborado el molde. Moldeo en arena Moldeo en arena: consiste en la confección de un molde elaborado con arena que es un material refractario muy abundante, mezclada con arcilla, con lo que adquiere cohesión y moldeabilidad sin perder la permeabilidad que posibilita evacuar los gases del molde cuando se vierte el metal fundido. Por este método se obtienen pequeñas series de piezas complejas, y pueden ser moldeados materiales con elevada temperatura de fusión. Imagen en Pixabay. CC0 Moldeo en coquilla Moldeo en coquilla, en este caso los moldes son fabricados con materiales metálicos (acero), llamados coquillas, con lo que es posible reutilizarlos un elevado número de veces, aunque con el uso van perdiendo los perfiles y es necesario sustituirlos, este proceso es muy barato y se consiguen altos ritmos de producción, se emplea cuando es necesario producir grandes series de piezas sencillas, y se debe emplear con materiales que tengan una temperatura de fusión significativamente más baja que la coquilla. Imagen en Pixabay. CC0 Existen dos tipos de proceso de moldeo que cabe citar por sus características especiales. Fundición centrífuga Fundición centrífuga: Consiste en depositar una capa de material fundido en un molde que gira a la velocidad adecuada como para que la fuerza centrífuga provoque que el material fundido se desplace hacia las paredes del molde entonces solidifica el material por enfriamiento continuo del molde o coquilla. Por este método se fabrican un gran número de piezas como tuberías, objetos de joyería,… Moldeo a la cera perdida Moldeo a la cera perdida: Es un procedimiento escultórico de muy antigua tradición, empleado para obtener figuras de metal (generalmente bronce) por medio de un molde, obtenido a partir de un modelo fabricado con cera. Este modelo previo es rodeado de una gruesa capa de material blando que solidifica; después se introduce en un horno, que derrite la cera, escurriendo ésta por unos orificios creados al efecto, en el hueco que ha quedado se inyecta el metal fundido, que adopta la forma exacta del modelo. Es necesario romper el molde para extraer la pieza final. Con esta técnica de vaciado, se pueden obtener piezas con detalles que sería imposible lograr por otros medios. Enlace a recurso reproducible >> https://www.youtube.com/embed/MSqazcApFTk?rel=0 Técnica de fundición en bronce a la cera perdida Técnica de moldeo a la cera perdida Vídeo de MemorANDA alojado en Youtube Las piezas obtenidas por moldeo pueden ser de muy diversos materiales. Un material será apto para fabricar una pieza por moldeo cuando cumpla dos condiciones. El material sometido a moldeo ha de presentar buena colabilidad, o aptitud de un material que en estado fundido rellena todas las cavidades del molde en que es vertido y adopte su forma. En el caso de productos poliméricos, este método se puede utilizar con plásticos termoestables, pero sobre todo con termoplásticos. En el caso de materiales metálicos se utiliza con aceros y fundiciones de los que se fabrican un diverso tipo de piezas, levas, pistones, cigüeñales, bancadas,… Fusibilidad o la aptitud de un material de pasar de sólido a líquido por efecto del calor, se caracteriza por la temperatura de fusión. A través de estos métodos se obtienen piezas de bronce y latón como herrajes, hélices de barcos, campanas, grifería, esculturas,…y también de plomo, aleaciones de aluminio,… Comprueba lo aprendido Lee el siguiente párrafo y completa los huecos con la palabra adecuada. El material fundido entra en el proceso de al interior del molde por unos conductos llamados. Es necesario dejar unos conductos por los que pueda escapar el material sobrante, estos conductos reciben el nombre de. 1.2. Conformación por sinterizado Este método se utiliza para fabricar grandes series de piezas pequeñas con gran precisión y para controlar el grado de porosidad de las piezas. Presenta importantes ventajas: Se aprovecha todo el material. Gran precisión y buen acabado Altos ritmos de producción. Piezas con una porosidad imposibles de obtener por otros medios. Imagen de M. Ayuso en INTEF. Licencia CC Aunque también tiene inconvenientes: Elevado coste de las matrices empleadas. Peores características mecánicas debido a la porosidad de las piezas. Entre las piezas fabricadas por este método destacan las herramientas de corte, rodamientos, filtros, árboles de levas, bielas, segmentos de pistones,... El proceso para la fabricación de una pieza sinterizada consta de las siguientes etapas: Obtención del polvo: Se produce por dos posibles métodos: Triturado y molido del mineral, aunque los granos obtenidos de este modo no son demasiado homogéneos. Deposición electrolítica del material, haciendo que éste se comporte como ánodo en una cuba electrolítica donde se produce su deposición en forma de polvo fino, que posteriormente puede ser tratado, este método es el empleado cuando se requiere obtener piezas de gran calidad. Preparación del polvo: El polvo obtenido se acondiciona para procesos sucesivos. Para ello se mezcla con los elementos aleantes precisos, se añaden lubricantes y otros aditivos, lo que proporciona al material una mejor maquinabilidad y compresibilidad. Compactación: Tras colocarlo en la matriz con la forma deseada se introduce en una prensa para que adquiera la forma deseada Sinterización: Se eleva la temperatura y se mantiene durante el tiempo necesario en función de las dimensiones de la pieza a obtener, manteniendo la presión. El proceso se debe realizar en ambientes inertes para evitar la oxidación de la pieza debido a las altas temperaturas alcanzadas. Acabado de la pieza: Las piezas así obtenidas presentan un buen nivel de acabado y no suele ser necesario someterlas a ningún otro proceso, aunque en algunos casos es necesario aplicar procedimientos de mejora del acabado. 1.3. Conformación por deformación Encontramos las siguientes técnicas: Laminación Laminación: Método de conformación basado en la deformación plástica que sufren metales o aleaciones al hacer pasar la pieza entre unos cilindros. Es el método más barato y eficiente para fabricar productos alargados de sección transversal constante a lo largo de todo el producto. Se puede realizar en frío o en caliente. En frío es necesaria más energía para realizar la deformación, ya que el material en frío no se deforma con facilidad, pero las propiedades de los materiales deformados en frío son significativamente mejores que en caliente, y además el grado de acabado superficial en la Imagen de Wizard191 en Wikimedia. Licencia CC deformación en frío es significativamente mejor que en caliente, tal es así que las piezas laminadas en frío no suelen tener que sufrir un proceso de acabado en cambio las laminadas en caliente suelen requerir un acabado final. En el proceso de laminado en caliente el lingote colado, las palanquillas o tochos se calientan a una temperatura entre los 900°C y los 1.200°C, con el fin de proporcionar ductilidad y maleabilidad para facilitar la reducción de área a la que se va a someter. A continuación se hace pasar el material entre una serie pares de rodillos metálicos superpuestos, que giran en sentido contrario y lo comprimen dándole la forma y tamaño deseados. Estampación Estampación: Proceso de conformación, también llamado embutición, que se basa en someter a un metal a un esfuerzo de compresión entre dos moldes de acero, llamados matrices o estampas. Los componentes fundamentales de la estampación son una prensa que puede tener distinta potencia, forma y tamaño, y una matriz, que lleva grabado la forma que se desea acuñar en la chapa, y que al dar un golpe seco sobre la misma queda grabada en ella. Cuando además de modificar la forma del material la prensa va provista de punzones Cuando además de modificar la forma del material, la prensa va provista de punzones que provocan cortaduras sobre la chapa de material, entonces al proceso se le llama troquelado. La estampación permite un óptimo nivel de automatización del proceso para producir grandes cantidades de piezas y a un elevado ritmo de trabajo. Las piezas obtenidas presentan un nivel de acabado superficial aceptable no siendo necesario someterlas a ninguna operación posterior. La forja por estampación en caliente se aplica a los metales, y consiste en darles forma sometiéndolos a esfuerzos violentos de compresión, que pueden ser repetitivos o continuos. En este proceso el tocho del material de partida se sitúa en la matriz con la forma de la pieza que se desea obtener. Sobre la parte superior que cierra la matriz y se golpea, manual o neumáticamente, cuando los esfuerzos tienen que ser muy grandes manualmente es imposible ejecutarlos, se produce la deformación permanente de la pieza que va ocupando todo el hueco de la matriz. Imagen en INTEF. Licencia CC Al extraer la pieza de la matriz, en general el grado de acabado no es satisfactorio y la pieza suele presentar rebabas que se tienen que recortar, también suele ser necesario someter a las piezas a procesos posteriores de acabado. Con este procedimiento se suelen fabricar componentes mecánicos, como bielas, ejes,… La forja manual es uno de los métodos más antiguos de trabajar el metal. El proceso consiste en calentar el metal al rojo vivo en una fragua. La fragua es un hogar construido con ladrillo refractario, que recibe el aire forzado desde un fuelle, para avivar la combustión del combustible, generalmente carbón de coque o vegetal. A continuación se coloca el metal sobre un yunque y se golpea para darle forma con pesados martillos llamados machos. Además de martillos, se emplean otras herramientas en las diferentes operaciones de forja. Trefilado Trefilado: El método consiste en reducir progresivamente la sección inicial de un producto metalúrgico (una barra de metal dúctil, o alambrón laminado…) haciéndolo pasar, mediante tracción, por unos orificios calibrados llamados hileras, de sección inferior a la de la pieza que se va a trabajar. Este procedimiento se utiliza sobre todo en la fabricación de alambre. Las piezas donde están situadas las Las piezas donde están situadas las hileras debe estar fabricadas de un material que soporte elevadas temperaturas y grandes esfuerzos de fricción con el mínimo desgaste posible, carburo de tungsteno, y deben ser lubricadas y refrigeradas mediante materiales en polvo. A cada paso del material por hileras de sección cada vez inferior, éste va ganando resistencia a la tracción, a costa de perder resistencia a la flexión y de aumentar su acritud. El diámetro del cabo del alambre para Imagen de Jahj en Wikimedia. Licencia CC estirar está reducido en una máquina sacapuntas. Este lado de alambre con diámetro afilado se enhebra por la boquilla de la primera máquina trefiladora y se fija en el tambor por un elemento que traccionará del alambre para empezar el estirado, un tambor va girando y enrollando el alambre. Éste debe pasar por varios procesos de trefilado hasta alcanzar el diámetro requerido. Cuando un rollo de alambrón para trefilar está próximo a terminarse, se suelda al principio de otro rollo para poder seguir con el proceso de trefilado. Extrusión Extrusión: Procedimiento de conformación con desplazamiento de material que permite obtener piezas de sección compleja aprovechando la plasticidad de ciertos materiales cuando son sometidos a esfuerzos de compresión o de choque. El proceso consiste en introducir el material a trabajar en un depósito en el que hay un émbolo que le empuja. La acción del émbolo obliga a fluir al material por un orificio, boquilla o hilera, con la forma de la sección que se desea obtener. Debido a los grandes esfuerzos de fricción las hileras sufren desgastes. Este fenómeno se reduce cuando se eleva la temperatura, ya que de este modo aumenta la deformación plástica de los materiales. Sin embargo los productos obtenidos presentan un mejor acabado, características y propiedades si el proceso ha tenido lugar en frío. Dependiendo del sentido en que el material fluya por la boquilla, la extrusión puede ser: Directa: Cuando el material fluye en el mismo sentido que la fuerza de compresión. Inversa: Cuando el flujo se produce en sentido contrario al de la fuerza de Inversa: Cuando el flujo se produce en sentido contrario al de la fuerza de compresión. Proceso de extrusión Imagen en Wikimedia. Dominio público Por este procedimiento se trabajan materiales con tendencia a presentar baja acritud y capacidad para deformarse plásticamente, como son los polímeros, el plomo, el estaño, el zinc, el aluminio, el cobre. Ejercicio resuelto Calcula la longitud final de un alambre de acero trefilado de 10 mm de diámetro, si su longitud inicial era 6000 mm y tenía un diámetro de 30 mm. Se considera al alambre como un cilindro. En el proceso de trefilación su volumen permanece constante. El volumen de un cilindro viene dado por la expresión: Donde d es el diámetro y h la altura. Como el volumen se mantiene constante podemos igualar Donde i representa el estado inicial y f el estado final. Simplificando los términos comunes: Despejando la altura final: Dando valores: 2. Fabricación con arranque de material Estos métodos de fabricación se realizan arrancando el material sobrante en forma de virutas o pequeñas partículas, con el fin de obtener la pieza diseñada. Se caracterizan por que hay una gran pérdida de material, lo que encarece el producto final; se debe utilizar un material inicial, obtenido mediante forja, laminación o cualquier otro proceso de los explicados en el tema de conformación por deformación, con una preforma de dimensiones ligeramente mayores que las definitivas. Imagen de David English en Wikimedia. Licencia CC En el mecanizado por arranque de viruta se dan procesos de desbaste (eliminación de mucho material con poca precisión) y de acabado (eliminación de poco material con mucha precisión) Estas operaciones de arranque de material conocidas como mecanización, son realizadas por medio de máquinas-herramientas. En ellas se dan dos tipos de movimientos: el de corte, por el que la herramienta penetra en el material, y el de avance, por el que la herramienta encuentra nuevo material para cortar. Cada uno de ellos lo puede realizar la pieza o la herramienta según el tipo de mecanizado. Importante Las máquinas herramientas se caracterizan por los siguientes parámetros comunes a todas ellas: Velocidad de corte, es la velocidad de un punto común a la arista cortante y a la pieza. Cuando la pieza se mueve y la herramienta permanece fija, es llamada velocidad de corte lineal, vc expresada en (m/min). Donde: es el diámetro de la pieza, expresado en (mm). n es la velocidad de giro de la pieza expresada en (rpm) revoluciones por minuto. Si se mueve la herramienta mientras permanece fija la pieza, entonces se habla de la velocidad angular de corte, se expresa en (rpm). Siendo la ecuación: Velocidades muy rápidas desgastan la herramienta pero mecanizan muy deprisa, en cambio velocidades bajas alargan la vida de la herramienta, pero fabrican muy lentamente, se debe encontrar una solución de compromiso entre ambas. Avance (a), es el desplazamiento de la herramienta o de la pieza por cada pasada o por cada vuelta, se expresa en (mm/min), o en (mm/vuelta), según que la herramienta se traslade o gire. Profundidad de pasada (p), es el espesor del material arrancado en una pasada, se mide en mm. Tiempos de fabricación, (t) es el tiempo que tarda en realizarse el mecanizado expresado en (min). Donde: L es la longitud mecanizada, expresada en mm. a es el avance en cada vuelta, expresado en mm/vuelta. n es la velocidad de giro, expresada en (rpm). Fuerza de corte, es la fuerza necesaria para arrancar una determinada sección de material. Potencia de corte, es la potencia necesaria en la herramienta para el avance y el desprendimiento de material. Reflexiona ¿Cúales son los parámetros comunes que caracterizan a todas las máquina herramientas? Velocidad de Corte Avance Profundidad de pasada Tiempos de Fabricación Fuerza de Corte Potencia de Corte 2.1. Torno Importante Es una máquina-herramienta que se utiliza para fabricar piezas de revolución, es decir, piezas cuya sección transversal tiene forma circular. La herramienta de corte será de un material que soporte las condiciones de trabajo sin desgastarse ni deformarse, dependiendo del material sobre el que se trabaje, podrá ser de acero al carbono, acero rápido al cobalto, widia, cerámica, diamante; siempre será más dura y resistente que el material a mecanizar. Si la operación lo requiere se suele utilizar un fluido (taladrina) que lubrica y refrigera la zona de trabajo. Enlace a recurso reproducible >> https://www.youtube.com/embed/p16Bn0tPi7I?rel=0 Torneado Vídeo alojado en Yotube Movimientos de trabajo en la operación de torneado Movimiento de corte: lo realiza la pieza que gira sobre su eje principal. Este movimiento lo produce un motor eléctrico que arrastra a un husillo, que tiene acoplado en su extremo un sistema de fijación (platos de garras) que sujetan la pieza a mecanizar. Movimiento de avance: se produce por el desplazamiento longitudinal de la herramienta sobre la pieza que se está trabajando, en combinación con el giro del husillo, determina el espacio recorrido por la herramienta por cada vuelta que da la pieza. Profundidad de pasada: se determina por la maquinabilidad del material que se trabaja, la velocidad de corte y la potencia de la máquina. Con el torno se pueden realizar operaciones de, cilindrado, mandrinado, refrentado, rasurado, roscado, moleteado… mediante diferentes tipos de herramientas y útiles intercambiables con diversas formas. Los carros del torno llevan incorporado unos nonios en forma de tambor graduado, donde cada división informa del desplazamiento del carro, ya sea el longitudinal o el transversal; los tornos de control numérico, CNC, no llevan nonios ya que las dimensiones de la pieza se programan y se consiguen automáticamente. Para saber más El moleteado Es un proceso de conformado en frío del material mediante unas moletas que presionan la pieza mientras da vueltas. Esta deformación incrementa el diámetro original de la pieza. El moleteado se realiza en piezas que se tengan que manipular a mano, para evitar que resbalen con el sudor o la grasa, como podría suceder en caso de tener la superficie lisa. Un ejemplo de moleteado es el que tienen los granetes en su superficie, o algunos bolígrafos. Imagen en Wikimedia. Licencia CC 2.2. Fresadora Importante Es una máquina que debido al movimiento de una herramienta rotativa, de varios filos de corte, denominada fresa, mecaniza piezas que se desplazan con movimiento rectilíneo bajo la herramienta, pudiendo obtener diversos trabajos. Son las máquinas herramientas más polivalentes dada la gran variedad de mecanizados que realizan y las opciones que permiten en los procesos de fabricación. Los elementos que configuran una fresadora son: 1: base. 2: columna. 3: consola. 4: carro transversal. 5: mesa. 6: puente. Imagen de HUB1 en Wikimedia. Licencia CC 7: eje portaherramientas En el siguiente vídeo podemos ver cómo funciona una fresadora industrial: Enlace a recurso reproducible >> https://www.youtube.com/embed/Y46X5WzOfuo?rel=0 CNC Fräsen Milling "Nockenwellenrad" UVA UNVERZAGT Vídeo de AWTLG alojado en Youtube Importante Movimientos: Movimientos de la herramienta El principal movimiento de la herramienta es el giro sobre su eje, en algunas es posible modificar la inclinación de la herramienta. Movimientos de la mesa La mesa de trabajo se puede desplazar, arrastrando a la pieza, de forma manual o automática pudiendo tener los siguientes movimientos: Movimiento longitudinal, corresponde habitualmente al movimiento de trabajo. Para facilitar la sujeción de las piezas la mesa tiene unas ranuras que permiten la fijación de mordazas y puede inclinarse para permitir tallar ángulos. Movimiento transversal, se utiliza para ubicar la herramienta sobre la pieza en la posición correcta. Movimiento vertical, corresponde al desplazamiento vertical de la mesa de trabajo, determina la profundidad de corte del fresado. Se pueden dar varias combinaciones de movimientos entre la fresa y la pieza. Se pueden dar varias combinaciones de movimientos entre la fresa y la pieza Imagen 17. wikipedia. Lic. Creative Commons Curiosidad Sabías que... La widia es un material descubierto en 1927 y su conocimiento provocó un enorme avance en el campo de las herramientas de arranque de material. Su nombre proviene de las palabras alemanas wi (como) diamant (diamante), debido a que presenta una dureza muy próxima a la del diamante, está compuesta por carburo de tungsteno, titanio, vanadio y cobalto, se fabrica por sinterización, las herramientas de este material soportan trabajar a temperaturas de hasta 800ºC sin desafilarse. 2.3. Taladro Importante Es la máquina herramienta que mecaniza la mayoría de los orificios que se hacen sobre las piezas en los talleres mecánicos, son máquinas de muy fácil manejo. Tienen un movimiento de rotación de la herramienta (broca), producido por un motor eléctrico que a través de una caja de velocidades por poleas y engranajes permite seleccionar la velocidad adecuada en función del tipo de material sobre el que se trabaja, y el movimiento de penetración de la broca, que puede realizarse de forma manual sensitiva o de forma automática, se incorpora un piñón-cremallera para hacerlo. Se llama taladrar a la operación de mecanizado que produce orificios cilíndricos sobre cualquier material, utilizando como herramienta una broca, que será de un material capaz de soportar las condiciones de trabajo y según sobre el material que trabaje, podrá ser de acero aleado para garantizar su dureza, de widia,… La operación de taladrar se puede llevar a cabo con un taladro portátil, con una máquina taladradora, en un torno, en una fresadora, en un centro de mecanizado CNC. La imagen muestra un taladro manual. Imagen de M. Haggstrom en Wikimedia. Licencia CC Ej i i lt Ejercicio resuelto Ejercicio ¿Cuál será la velocidad de giro de una broca de 12 mm de diámetro si debe alcanzar una velocidad de corte de 41 m/min? Despejamos n Sol. n=1088 rpm Ejercicio ¿Cuál será la velocidad de corte de una broca de 16 mm de diámetro que gira a una velocidad de 500 rpm? Sol. vc=25,12 m/min. Ejercicio ¿Qué tiempo se tardará en perforar un orificio de 12mm de diámetro sobre una pieza de 33 mm de espesor, si el avance de la broca es de 0,3 mm /vuelta y la broca gira a una velocidad de 425 rpm? Sol. t=0,259min=15,53s Ejercicio Un taladro de columna desarrolla una fuerza de 5000 N y su velocidad de corte es de 37 m/min. Si el motor eléctrico que lo arrastra tiene unas pérdidas del 12 %. Calcula la potencia del taladro expresada en kw y en CV. P=F(N)·v(m/s)=5000·(37/60)= 3083 W hace falta Como se pierde un 12%: 3083*0,12 =370 W Ptotal = 3083+370 = 3453 W aprox. 3,5 kW Sol. P = 3,5 kW = 4,76 CV Para saber más Escariado, es una operación de mecanizado para conseguir un acabado fino y de precisión en orificios que han sido previamente realizados con broca a un diámetro ligeramente inferior. La mayoría de escariadores son cilíndricos, pero también los hay cónicos y para dimensiones especiales existen escariadores extensibles, que permiten escariar agujeros a dimensiones fuera de las normales. El escariado puede realizarse a mano, en un torno, en una fresadora o en una taladradora. Escariador Imagen de Graibeard en Wikimedia. Licencia CC 2.4. Limadora, aserrado y abrasión Limadora Limadora La limadora es una máquina que mediante el movimiento horizontal alternativo de la herramienta va produciendo una superficie plana, o bien va generando ranuras paralelas sobre la pieza a trabajar. La mesa que sujeta la pieza realiza un movimiento de avance transversal, para facilitar el trabajo de mecanización, también se pueden desplazar verticalmente ambas, manual o automáticamente, para aumentar la profundidad de pasada. La limadora mecánica permite el mecanizado de piezas pequeñas y medianas, es la máquina de elección para la generación de superficies planas de menos de 800 mm de longitud, por su fácil manejo y su bajo consumo energético. Imagen de Silberwolf en Wikimedia. Dominio público Las herramientas suelen ser de acero al carbono o acero rápido, ya que la máquina no alcanza grandes velocidades, por lo que no es necesario emplear herramientas extraduras. Aserrado Aserrado Es la operación que consiste en cortar el material a la longitud adecuada como paso previo a otras operaciones de fabricación, se lleva a cabo mediante diversas herramientas o máquinas con diferentes tipos de hoja de sierra y formas: de arco, de cinta, circular. En ocasiones los dientes de la hoja de sierra se inclinan alternativamente a derecha e En ocasiones los dientes de la hoja de sierra se inclinan alternativamente a derecha e izquierda al objeto de facilitar la rectitud del corte y para refrigerar la zona de corte ya que no rozan lateralmente con la pieza continuamente, entonces, los dientes se dicen que están triscados. Es un método rápido y continuo, dejando las superficies lisas y con muy pocas rebabas, por lo que se ahorran procesos posteriores. En carpintería además de estas sierras se suelen emplear sierras de calar y serruchos de mano que presentan distintos tipos dependiendo del trabajo a realizar, universal, de costilla, de punta, de metal. Serrucho universal Serrucho de costilla Serrucho de punta Imagen de MdeVicente en Wikimedia. Imagen de MdeVicente en Wikimedia. Imagen de MdeVicente en Wikimedia. Licencia CC Licencia CC Licencia CC Abrasión Abrasión La abrasión consiste en desgastar la pieza, desprendiendo partículas de material, se realiza por la acción de una muela, que está formada por partículas de material abrasivo muy duro unidas por un aglutinante. Esta forma de eliminar material, rayando la superficie de la pieza, necesita menos fuerza que el arranque de viruta, por lo que se puedan dar pasadas de mucho menor espesor. La precisión que se obtiene por abrasión y el acabado superficial son muy buenos, aunque los tiempos de fabricación se alargan. Muela abrasiva Imagen de Grailberard en Wikimedia. Licencia CC Este tipo de trabajo lo suele realizar la esmeriladora, sus movimientos son muy parecidos a los de una fresadora horizontal, este procedimiento genera superficies planas empleándose una esmeriladora cilíndrica de eje horizontal planas, empleándose una esmeriladora cilíndrica de eje horizontal. Elimina cantidades reducidas de material (metal) lográndose buenos acabados y trabajos de gran precisión. Esmeriladora Imagen en INTEF. Licencia CC Cuando se requieren trabajos de gran precisión se recurre a la rectificadora, se utilizan para mejorar los acabados superficiales de las piezas y obtener las mejores tolerancias posibles. Tiene una gran desproporción entre el tamaño de la máquina y la pieza, para evitar vibraciones. La herramienta gira a muy alta velocidad. (n>10000 r.p.m.). El movimiento de avance de la pieza es muy rápido (metros/minuto). Los esfuerzos de corte son muy reducidos, del orden de 1 kg/cm2. Rectificadora Imagen de en Wikimedia. Licencia CC 2.5. Centro de mecanizado CNC Importante Todas las máquinas mencionadas hasta ahora desarrollan trabajos específicos, pero generalmente para fabricar una pieza es necesario que concurran varios de estos procesos, por lo que las piezas deben pasar de máquina en máquina, encareciendo el producto final y dando lugar a la posible aparición de errores debidos a los operarios. Para paliar todo esto, se pensó en crear un centro de mecanización que ejecutase secuencialmente todos los trabajos incorporando el control informático del proceso, para tratar de reducir las probabilidades de error. Así surgió el CNC, o Control Numérico Computerizado, llamado de este modo por que las órdenes que reciben las máquinas están codificadas numéricamente. Estas máquinas herramientas están constituidas por un ordenador que gobierna la posición y la velocidad de giro de distintos motores, de modo que las herramientas o las piezas pueden realizar movimientos que serían impensables de realizar manualmente, como formas tridimensionales complejas. El paso previo al proceso de fabricación será programar la máquina, introduciendo todos los datos necesarios en el ordenador que la controla, para posteriormente desarrollar todo el trabajo secuenciado sin necesidad de que ningún operario intervenga en el proceso. Imagen de G. Mckechnie en Wikimedia Commons. Licencia CC Actualmente se emplean tres métodos de programación de CNC: Programación manual, el programador debe indicar mediante un programa toda la secuencia de movimientos de pieza y herramienta, cambio de ésta,… es un proceso largo y reiterativo. Programación asistida, el programador elige la operación que debe realizar la máquina y esta le va pidiendo los datos que necesita para llevar a cabo el proceso. Programación CAD/CAM, utilizan programas informáticos, que minimizan los posibles errores, agilizan la producción y permiten modificaciones rápidas de las dimensiones de las distintas piezas. En primer lugar, se dibuja con el programa CAD la pieza que se tiene que fabricar en dos o tres dimensiones (2D, 3D). Posteriormente el programa CAM procesa esta información y establece la ruta de corte que debe seguir la herramienta para ejecutar la pieza, se redacta el programa de CNC, es capturado por la máquina herramienta y es ejecutado sin necesidad de introducir ningún otro tipo de dato o de código numérico. Son especialmente recomendables cuando hay que producir series muy largas de producción, ya que de este modo se consigue amortizar el elevado coste de los equipos. Máquina CNC Biesse Máquina CNC en funcionamiento 3. Fabricación por unión entre piezas Las estructuras y las máquinas están constituidas, generalmente, por elementos mecánicos y piezas unidas entre sí. A veces es necesario poder desmontar las piezas de un conjunto sin que éstas sufran ningún daño, mientras que en otras ocasiones las uniones deben mantenerse permanentemente. Durante el desarrollo de este tema desglosaremos los distintos tipos de uniones, las fácilmente desmontables y las permanentes, diferenciando las características de cada una de ellas y conociendo los distintos métodos de realización de las uniones. Imagen en Wikimedia Commons. Dominio público Imagen en Pxhere. Licencia CC 3.1. Uniones fácilmente desmontables En ocasiones los elementos y las piezas que constituyen una máquina se deben poder desunir por diferentes motivos. En ese caso es necesario que los elementos que mantenían la unión permitan esta función con facilidad, dejando las piezas en las mismas condiciones que antes de haber sido unidas. Este tipo de uniones fácilmente desmontables se pueden realizar de distintas formas: UNIONES DESMONTABLES UNIONES ROSCADAS UNIONES NO ROSCADAS Tornillos/tuercas Pasadores Tirafondos Chavetas Autorroscantes Lengüetas Bulón Guías Tornillo de unión Botones/velcro/corchetes Prisioneros Espárragos Pernos Importante Una unión roscada la constituye un tornillo o un tornillo-tuerca del mismo tipo de rosca. UNIONES ROSCADAS A continuación se detallan cada una de ellas. Tornillos/tuercas Importante Un tornillo es un elemento mecánico cilíndrico, generalmente metálico, dotado de una cabeza y una caña roscada, y que se emplea para fijar unas piezas con otras. Aplicándole una fuerza de torsión en su cabeza con la herramienta apropiada se introduce en un orificio roscado o atraviesa piezas para acoplarse a una tuerca. Imagen en Wikimedia. Lciencia CC Las roscas pueden ser de distintos tipos: métrica (la más común), withworth, sellers, trapezoidal, ACME... Para identificar a un tornillo, basta con indicar el tipo de rosca, el diámetro exterior y su paso. Del siguiente modo: Además de estos valores, que están prefijados, se tiene que escoger el tipo de cabeza, que dependerá del lugar donde se vaya a fijar y del tipo de trabajo que vaya realizar el conjunto. Imagen 8. Wikipedia. Creative Commons En esta imagen vemos distintas formas de cabezas para los tornillos: hexagonal (a), redonda (b), cilíndrica (d, g), avellanada (c, e, f); combinadas con distintos sistemas de apriete: hexagonal (a) o cuadrada para llave inglesa, ranura o entalla (b, c, d) y Phillips (f) para destornillador, agujero hexagonal (e) para llave Allen, moleteado (g) para apriete manual, etc. Importante Una tuerca es la pieza, roscada interiormente, que se acopla al tornillo para formar una unión roscada. Imagen en Wikimedia. CC Para que tornillo y tuerca encajen deben tener el mismo tipo de rosca y el mismo paso. Pueden presentar formas diversas: hexagonal, ciega, mariposa, autoseguro, soldable, almenada..., aunque las más habituales son las hexagonales. Imagen 10. Wikipedia. Creative Commons. La manera de identificar las tuercas es similar a los tornillos indicando su tipo de rosca, su diámetro y su paso. Tirafondos TIRAFONDOS Se utilizan para pared y madera. Para instalarlos en pared se perfora ésta al diámetro adecuado, se inserta un taco de plástico y a continuación se introduce el tornillo que rosca a presión el taco, quedando así fuertemente sujeto al soporte. También se utiliza para el atornillado de elementos de madera. Imagen 13. deu ferretería. Copyright. Imagen 14. deu ferretería. Copyright. Autoroscantes AUTORROSCANTES Se les denominan autorroscantes porque abren su propio camino. Se usan en láminas o perfiles metálicos, porque permiten unir metal con madera, metal con metal, metal con plástico o con otros materiales. Imagen 15. Wikipedia. Creative Commons. Tienen la mayor parte de su caña cilíndrica y el extremo en forma cónica. Pueden tener distintas formas de cabeza. La rosca es delgada, con su fondo plano, para facilitar el “agarre”. Estos tornillos están completamente tratados (desde la punta hasta la cabeza) y sus bordes son más afilados que el de los tornillos para madera. Imagen 16. Wikipedia. Creative Commons. Bulón BULÓN Es un tornillo de gran tamaño que se enrosca en una tuerca y que sólo está roscado en el extremo de su caña. Las piezas que une un bulón no van roscadas y para que éste pueda ser introducido en ellas sin Imagen 17. Isftic. Creative Commons. dificultad, tienen un diámetro ligeramente superior al del bulón. Se manipulan mediante llaves especiales, y se usan con maquinaria pesada, vías férreas,... Suelen ir provistos de arandelas, que son delgados discos perforados, de metal o de plástico, utilizados para soportar aprietes. Tornillo de unión TORNILLO DE UNIÓN El tornillo de unión es semejante a los bulones, pero no se rosca a una tuerca sino que la pieza más alejada de la cabeza del tornillo hace la función de tuerca, por lo que tiene que estar roscada. Se emplea este tipo de unión cuando se tiene que unir piezas de poco espesor a otras de gran grosor. Prisionero PRISIONERO El prisionero es un tornillo que se rosca en una pieza y se alojan en el hueco practicado en la otra. Se usan, sobre todo, cuando es necesario que una pieza permanezca fija sobre otra, sin desplazamientos ni giros. Imagen 18. Importper. Copyright. Espárrago ESPÁRRAGO Es una varilla cilíndrica roscada en ambos extremos y con la parte central sin roscar. Se emplean para unir piezas grandes y costosas con otras más sencillas que requieren ser desmontadas con regularidad. La utilización del espárrago nos permite desmontar sólo la pieza sencilla y así preservar la rosca de la pieza costosa. Imagen 19. Isftic. Creative Commons. Perno PERNO El perno es un elemento cilíndrico largo, con cabeza redondeada por un extremo, y que en el otro extremo se asegura por medio de un pasador, una chaveta o una tuerca. Se emplean para unir varias piezas y pueden desarrollar funciones de apoyo, de articulación y de anclaje. Imagen 20. Isftic. Creative Commons. Imagen 21. Wikipedia. Creative Commons. UNIONES NO ROSCADAS En ocasiones se recurre a otro tipo de unión desmontable que no precisa de elementos roscados. Las más comunes quedaron presentadas en el punto 1 del tema y ahora las vamos a ver un poco más detalladas: Pasadores PASADORES Son vástagos cilíndricos o cónicos que van a unir piezas pasando a través de ellas. Además de sujetar, sirven para mantener la posición relativa entre piezas. Suelen ser de acero. Imagen elaboración propia Imagen elaboración propia Chavetas CHAVETAS Son piezas metálicas en forma de cuña cuya altura va en disminución y que se alojan en unas hendiduras longitudinales llamadas chaveteros. Son lo suficientemente robustas como para unir piezas y transmitir esfuerzos entre ellas. Pueden ser transversales o longitudinales. En las imágenes siguientes se muestra un dibujo de una chaveta en su chavetero y un eje con su chaveta para evitar que se produzca un movimiento relativo del eje y del agujero en el que va acoplado. Imagen 27. Wikipedia. Creative Commons. Imagen 28. Wikipedia. Creative Commons. Lengüetas LENGÜETAS Como las chavetas, son cuñas metálicas alojadas en chaveteros, pero éstas tienen todas sus caras paralelas. Su función es permitir que la pieza a sujetar tenga un cierto desplazamiento longitudinal sobre la pieza que sujeta la lengüeta. Guías GUÍAS Permiten el desplazamiento longitudinal de una pieza respecto a otra. Imagen 29. Isftic. Creative Common Son empleadas en las máquinas herramientas para desplazar herramientas y carros. Botones, velcro, corchetes... BOTONES, VELCRO, CORCHETES... Son distintos elementos que se emplean habitualmente en el ámbito textil. Los botones, se fabrican de resina, plástico, madera, nácar,… Para realizar la unión son introducidos por un ojal. El velcro es un sistema de apertura y cierre rápido. Son dos tiras contrapuestas en un lado con unos ganchos más o menos deformables que se agarran a una tira de fibras enmarañadas, produciendo una adhesión parcial que se desmonta estirando de ambas. Los corchetes son una especie de broches, fabricados de metal o de plástico, y constituidos por un macho y una hembra, que cuando se presionan uno sobre otro produce la unión entre las prendas. Imagen 30. Isftic. Creative Commons. Imagen 31. Isftic. Creative Commons. Imagen 32. Isftic. Creative Commons. Comprueba lo aprendido Responde verdadero o falso a las siguientes afirmaciones sobre los tipos de unión no roscados. Una lengüeta es una chaveta de mayor tamaño. Verdadero Falso Falso La diferencia no tiene nada que ver con el tamaño, sino con la forma. Una chaveta tiene forma trapezoidal y la lengüeta tienen sus caras paralelas. Las chavetas no permiten ningún movimiento entre el eje y el agujero al que va acoplado. Verdadero Falso Verdadero La función de las chavetas es no permitir ningún movimiento relativo entre las piezas que une. El carro de un torno puede desplazarse porque está montado sobre una guía. Verdadero Falso Verdadero La función de una guía es precisamente esa, permitir el desplazamiento longitudinal de una pieza sobre la otra. Una cremallera no es un tipo de unión porque lo que une son tejidos. Verdadero Falso Falso Es un tipo de unión, no en el ámbito industrial, pero si en el textil. 3.2. Uniones fijas: remaches, roblones, adhesivos y ajuste a presión Por lo general, las máquinas y mecanismos se diseñan de modo que sus componentes deben estar permanentemente unidos, ya que no se prevé su desmontaje. Por eso se recurre a uniones fijas o difícilmente desmontables, de estas los métodos más empleados son: Remaches Importante Remachar consiste en unir dos o más piezas con elementos metálicos cilíndricos que se deforman. Remaches Imagen en Wikimedia. CC En el siguiente vídeo se muestra cómo se coloca un remache con una remachadora Enlace a recurso reproducible >> https://www.youtube.com/embed/J06VYN_nhAs?rel=0 Cómo colocar remaches con una remachadora manual Vídeo de Miguel Ángel Vadillo alojado en Youtube Los remaches se usan en el fuselaje de los aviones o en los cascos de los barcos Los remaches se usan en el fuselaje de los aviones o en los cascos de los barcos donde pueden verse casos de piezas unidas por remaches. También son muy utilizados en estructuras metálicas de construcción civil. Como curiosidad, decir que en el proceso del montaje de la Torre Eiffel se emplearon más de dos millones y medio de remaches. Roblones Curiosidad Los roblones son remaches cuyo diámetro es superior a 10 mm. Imagen de Miaow Miaow en Wikimedia. Imagen de G. Slickers en Dominio público Wikimedia. CC Adhesivos Importante Otra técnica de unión de materiales consiste en interponer entre las superficies a unir una película de material con elevado poder de adherencia, denominado adhesivo o pegamento. Esta técnica se está imponiendo gracias al desarrollo de nuevos adhesivos. Imagen de Babi en Wikimedia. Licencia CC ¿Cómo utilizar un adhesivo? Primero hemos de elegir convenientemente el adhesivo adecuado y para ello hemos de considerar una serie de factores: materiales a unir condiciones de trabajo humedad humedad temperatura esfuerzos soportados vibraciones También deberemos tener en cuenta otros aspectos: tiempo de secado forma de aplicación: pistola, rodillo, brocha Antes de proceder al pegado de dos superficies se debe asegurar la limpieza de éstas, para eliminar el polvo, la suciedad e incluso pequeños espesores de óxido que han podido formarse sobre la superficie de las piezas a unir. La resistencia de la unión no sólo depende del pegamento utilizado, sino también de la interfase del adhesivo con cada uno de los materiales, por lo que, contra lo que vulgarmente se piensa, el exceso de pegamento nunca es bueno. Es muy importante leer las instrucciones de uso, ya que la manipulación de algunos adhesivos puede resultar peligrosa. ¿Qué adhesivos existen? Hay muchos tipos de adhesivos, pero los más comunes y menos peligrosos son: la cola de carpintero, la cola de contacto, el pegamento termofusible y los pegamentos sintéticos. Estos tipos de adhesivos se detallan en el epígrafe siguiente Ajuste presión Importante Ajustar una pieza consiste en acoplarla o encajarla dentro de otra. Será necesario, pues, que la relación entre sus medidas esté determinada previamente. Se suelen identificar a las piezas a unir como eje y agujero (pieza contenida y pieza continente respectivamente). En los procesos de fabricación es prácticamente imposible que dos piezas tengan la misma medida por lo que se pueden dar los siguientes casos: AJUSTE MÓVIL O LIBRE AJUSTE FIJO O FORZADO dD Se denomina JUEGO a la diferencia de Se denomina APRIETO a la diferencia de Se denomina JUEGO a la diferencia de Se denomina APRIETO a la diferencia de los diámetros los diámetros JUEGO = D - d APRIETO = d - D D= diámetro del agujero d= diámetro del eje Importante Un ajuste recibe el nombre de ajuste a presión cuando se ejecuta mediante un ajuste forzado, es decir cuando el diámetro del eje es mayor que el del agujero donde se desea colocar. Cuando se trabaja con ajustes a presión, para poder introducir el eje en el agujero (de menor diámetro) se necesita calentar la pieza donde se ubica éste, para que se dilate y poder introducir el eje fácilmente. De este modo, cuando se reduce su temperatura, la unión entre ambos se consolida. En ocasiones no es necesario el calentamiento y la unión se realiza mediante apriete manual o por medio de prensas. Como es imposible que las piezas fabricadas tengan las medidas exactas, introduciremos el concepto de tolerancia, que se define como el margen de medidas límites que puede tener una pieza para que sea válida en las aplicaciones a las que se destina. Es decir la tolerancia, T, será la diferencia entre la cota máxima permitida, CM y la cota mínima permitida, Cm. T = CM - Cm Soldadura Este contenido se desarrolla en el apartado 3.3. Uniones fijas: Soldadura TIPOS DE ADHESIVOS COLA DE CARPINTERO Es un líquido pastoso y blanco que proporciona una unión resistente con maderas, papeles y derivados. El inconveniente de la cola de carpintero es que tarda mucho tiempo en secar, y hay que mantener las piezas presionadas durante ese tiempo mediante gatos u otras herramientas. Imagen de Babi en Wikimedia. Elaboración propia Dominio público COLA DE CONTACTO Es una disolución de caucho que se utiliza con todo tipo de materiales. Se debe aplicar una capa muy fina sobre las dos partes a unir y esperar hasta que no se adhiera al dedo al tocarla. Después se mantienen presionadas las piezas a unir durante unos segundos. Imágenes de Babi en Wikimedia. Dominio público PEGAMENTO TERMOFUSIBLE Son barras de silicona sólida a temperatura ambiente que al aplicarles calor funden. Esa masa fundida es utilizada como elemento de unión, y como el enfriamiento es rápido, las piezas pegadas se pueden utilizar rápidamente. Para la utilización de este tipo de adhesivos es necesario utilizar una pistola, capaz de mantener caliente de forma continua el pegamento que se desea aplicar. Imagen enWikimedia. Dominio público. ADHESIVO SINTÉTICO ADHESIVO SINTÉTICO Existen un gran número de adhesivos sintéticos que cada vez tienen más aplicación en la industria, desde simples masillas hasta pegamentos de dos componentes, pasando por el conocido "Super Glue". Adhesivo de dos componentes Imagen en INTEF. Licencia CC Comprueba lo aprendido Responde a estas cuestiones de verdadero o falso para asentar tus conocimientos sobre los adhesivos. Los adhesivos son materiales con alto poder de adherencia. Verdadero Falso Verdadero Su propio nombre lo indica. Los adhesivos tiene mucha adherencia. El adhesivo se usa poniendo una capa generosa de éste entre los materiales a unir. Verdadero Falso Falso No tiene por qué ser necesario una gran cantidad; en algunos caso es casi al contrario. Los adhesivos son muy cómodos de usar porque se secan enseguida y podemos utilizar muy pronto las piezas unidas. Verdadero Falso Falso Hay adhesivos de muchos tipos, y unos secan rápido y otros no. Los pegamentos de dos componentes son pegamentos sintéticos de gran aplicación en la industria. Verdadero Falso Verdadero Aunque creamos que los pegamentos no son uniones fiables a nivel industrial, sí lo son, y cada vez más. 3.3. Uniiones fijas: Soldadura Importante La soldadura es un proceso de unión de materiales, generalmente metales o termoplásticos, por medio del calor. Consiste en caldear el material hasta que funde, y una vez unidas las piezas, se dejan enfriar. Imagen de W.M.Plate Jr en Wikimedia. Dominio público Si en el proceso de soldadura se utiliza un material que se aporta a la unión, se dice que es una soldadura con material de aportación, y si no interviene ningún material externo, entonces se dice que es una soldadura sin material de aportación o autógena. Si el material de aportación y los materiales a unir son de la misma naturaleza, se llamará soldadura homogénea y en caso contrario heterogénea. En la soldadura se pueden utilizar diferentes formas de caldeo del material: una llama de gas, un arco eléctrico, un láser, un rayo de electrones, procesos de fricción o ultrasonido. Puede ser realizada en diferentes ambientes al aire libre, en atmósfera inerte, bajo el agua o en el espacio. Imagen en Wikimedia Commons. Imagen de Spangineer en Wikimedia. Dominio público Dominio público Como curiosidad aquí tienes un vídeo interesante sobre la soldadura bajo el agua. Enlace a recurso reproducible >> https://www.youtube.com/embed/ZTj4jHCT1Wc Video de Soldanet AR alojado en Youtube La soldadura puede realizarse: a tope, en la que los dos extremos que se pretenden soldar están situados en el mismo plano. Cuando se suelda a tope, el cordón debe ser continuo a todo lo largo de la unión y con completa penetración. En uniones de fuerza el cordón de soldadura debe realizarse por ambas caras. Es la posición más usual y recomendable. a solape, realizando el cordón a lo largo de dos juntas solapadas. Se le llama también soldadura con recubrimiento. El material de aportación debe tener una temperatura de fusión inferior a la de las piezas a soldar e incluso en algunas ocasiones hay que aportar una presión junto con el calor para que se realice la soldadura. Habitualmente se emplea también un producto llamado borax con el que se impregnan las superficies a soldar. Éste cumple la doble función de actuar como desoxidante de las zonas donde se aplica y como fundente, es decir, reduciendo la temperatura de fusión. A continuación vamos a conocer los distintos tipos de soldaduras. Imagen de Aisart en Wikimedia. Licencia CC Soldadura blanda SOLDADURA BLANDA Se emplea para unir componentes electrónicos y montar circuitos impresos. Para realizarla se utiliza un soldador que es una herramienta con aspecto de "lápiz". En la punta tiene una barra de cobre recubierta con hierro, níquel y cromo y cuando se conecta a la red alcanza temperaturas superiores a 230ºC (dependiendo de su potencia). Si necesitamos deshacer una soldadura o eliminar el exceso de metal de aportación, utilizamos el desoldador que es un instrumento con un mecanismo succionador que absorbe el material fundido. Utiliza como material de aportación una aleación formada por 60% de estaño y 40% de plomo debido a su buena conductividad eléctrica, a su bajo punto de fusión (232ºC) y a su precio competitivo, aunque en ciertas aplicaciones especiales se usan aleaciones con plata u oro. Este material es tubular y su alma es de una resina que al fundirse, desengrasa y desoxida los metales a soldar, lo que asegura que los elementos a soldar deben estar limpios de grasa, óxido, lo que hace que la soldadura sea eficaz. Soldador Imagen de Inductiveload en Wikimedia. Imagen de Norro en Wikimedia. Dominio público CC Soldadura oxiacetilénica o autógena SOLDADURA OXIACETILÉNICA O AUTÓGENA Se utiliza para soldar distintos materiales: acero, cobre, latón, aluminio, magnesio, fundiciones y sus respectivas aleaciones. No necesita material de aportación. Para lograr la fusión rápida del material se utiliza un soplete que combina oxígeno (como comburente) y acetileno (como combustible). La mezcla se produce en una boquilla hueca de la que sale acetileno rodeado por el oxígeno. La llama que Imagen de Neutrality. Dominio público se produce es muy delgada y de color celeste, y alcanza una temperatura de 3050 ºC. Si se van a unir dos chapas metálicas se colocan una junto a la otra, se calienta hasta alcanzar el punto de fusión sólo en la zona de la unión y por unión de ambos materiales se produce una costura. El enfriamiento es más lento que con el arco eléctrico, lo que provoca mayores tensiones residuales y distorsión de soldadura. El oxígeno y el acetileno se almacenan en botellas de acero, a una presión de 15 kp/cm² el acetileno y de 200 kp/cm² el Imagen en Mediateca. CC oxígeno y ambas van montadas en un carrillo desplazable. Un proceso similar, el oxicorte, se emplea para cortar metales. Curiosidad La llama producida en el soplete oxiacetilénico presenta varias zonas: Zona de mezcla, donde se mezclan ambos gases. Dardo, se calienta la mezcla hasta la temperatura de inflamación, pero todavía no ha ardido es de un color verdoso. Zona de inflamación, se produce una elevación muy brusca de temperatura. Zona de temperatura máxima, es la que se emplea durante la soldadura. Penacho, es la zona exterior de la llama, donde se produce la segunda fase de la combustión. En el siguiente vídeo tienes una muestra de cómo se realiza la soldadura oxiacetilénica. Enlace a recurso reproducible >> https://www.youtube.com/embed/EfGhi27euoA?rel=0 Soldadura Oxiacetilénica Vídeo de Urisei alojado en Youtube Soldadura por arco SOLDADURA POR ARCO Actualmente es un método muy comúnmente empleado, por su reducido coste, fácil aplicación, buenos ritmos de fabricación, y la facilidad para soldar un amplio número de metales. El proceso consiste en provocar la fusión de las piezas a unir debido al calor producido por un arco eléctrico (alcanza una temperatura de unos 3500ºC). Los bordes fundidos de las piezas se mezclan íntimamente con el material de aportación (que se desprende de un electrodo), dando lugar, al enfriarse, a una unión homogénea y resistente. Imagen de J. Barrios en Wikimedia. CC Se deben fijar las piezas a soldar a una mesa de trabajo de material refractario, inmovilizándolas durante el proceso. Se debe ir eliminando la escoria que se va produciendo, recubriendo el cordón de soldadura, con una picoleta. Hay que mantener el electrodo inclinado unos 15º y desplazarlo en un movimiento de zigzag relativo, para tratar de que el material que se desprende de él se distribuya homogéneamente entre las piezas a soldar. Los electrodos tienen una parte central o alma, y un revestimiento exterior (metálico o de carbón; según los empleados se identifican distintas técnicas de soldadura). Las sustancias del revestimiento tienen diversas misiones: añadir material a la soldadura, proteger el metal fundido durante la fusión, aumentar la ionización del aire, dirigir el arco y las gotas de metal fundido y formar escorias que ascienden a la superficie de la soldadura. Durante el proceso de la soldadura hay que protegerse los ojos con un vidrio muy oscuro, ya que la luminosidad del arco podría dañar los ojos. Soldadura por resistencia SOLDADURA POR RESISTENCIA Se basa en el efecto Joule, es decir, en aprovechar el calor generado cuando una corriente eléctrica atraviesa una resistencia que colocamos en la zona de unión de dos superficies de metal para fundir el material. Se puede diferenciar varios tipos de soldadura por resistencia: Soldadura por puntos Soldadura por costura Soldadura TIG Soldadura aluminotérmica Soldadura por puntos SOLDADURA POR PUNTOS Se utiliza para soldar chapas de metal solapadas, de hasta 5 mm de espesor. Dos electrodos aprietan las chapas de metal y se hace pasar una corriente, de elevado valor, a su través, lo que proporciona el calor suficiente para fundir el material. Presenta indiscutibles ventajas: uso eficiente de la energía escasa deformación de las piezas elevados ritmos de producción, fácil automatización no necesita material de aportación y aunque la fuerza en la unión es inferior que con otros métodos de soldadura, está especialmente indicada en la industria del automóvil. Un coche actual lleva varios miles de puntos de soldadura ejecutados por robots soldadores. Imagen de Trident en Wikimedia. CC Imagen de albertollopisrosa en Wikimedia. CC Soldadura por costura SOLDADURA POR COSTURA Los electrodos tienen forma de rueda y van girando, describiendo una trayectoria por la zona a soldar y haciendo posible costuras de soldadura largas y continuas. Antes se usaba en la fabricación de latas de bebidas, ahora sus usos son más reducidos. SOLDADURA TIG (Tungsten Inert Gas) Caracterizada por la utilización de un electrodo permanente de tungsteno. Como el punto de fusión del tungsteno es muy elevado (3410ºC) y se trabaja en presencia de atmósferas inertes, generalmente gas argón o helio, el electrodo apenas sufre desgaste tras usos prolongados. Imagen en Mediateca. CC Soldadura aluminotérmica Es un procedimiento utilizado en raíles de vías férreas y está basado en la reducción del óxido de hierro por el aluminio que se produce según una reacción altamente exotérmica, alcanzándose temperaturas superiores a 2000º C. Fe2O3 + 2 Al = Al2O3 + 2 Fe + calor La soldadura se ejecuta en un molde refractario acoplado en los extremos de los raíles a unir, dentro del que se vierte el acero fundido producto de la reacción, que se inicia con un fósforo. Una vez iniciada la reacción el proceso es muy rápido y el material fundido fluye dentro del molde, quedando el acero entre los extremos a soldar. Imagen de Skatebiker en Wikimedia. Dominio Imagen de LosHawlos en Wikimedia. CC público Curiosidad Hay constancia histórica de que hace más de 2000 años en China, ya se realizaban soldaduras heterogéneas. El historiar romano Plinio hace referencia a la soldadura con estaño, como método habitual empleado por los orfebres, para fabricar adornos con metales preciosos. Durante el siglo XV se empezó a emplear el borax como fundente en los procesos de soldadura. Para saber más Si quieres aprender un poco más sobre soldaduras mira este video documental sobre soldadura. Es un poco largo pero merece la pena. Documental sobre soldaduras Comprueba lo aprendido La soldadura es un método de unión basado en: La fusión de los materiales por medio de calor. La fusión de los materiales por el efecto Joule. La fusión de los materiales por medio de reacciones exotérmicas. Solución. Correcto. Incorrecto. Incorrecto Los raíles de las vías férreas se sueldan con soldadura: TIG Aluminotérmica Oxiacetilénica Solución. Incorrecto. Correcto. Incorrecto Para soldar chapas solapadas y de poco espesor se utiliza la soldadura. Por puntos y por costura. Por puntos y por arco. Sólo por puntos. Solución. Correcto. Incorrecto. Incorrecto El material de aportación de la soldadura oxiacetilénica es: El acetileno. El acetileno y el oxígeno. No utiliza material de aportación. Solución. Incorrecto. Incorrecto. Correcto En la soldadura blanda se usa estaño : Como material de aportación. Para desengrasar los elementos a soldar. Para desoxidar los elementos a soldar. Solución. Correcto. Correcto. Correcto Resumen Descarga aquí la versión imprimible de este resumen: >> Documento de descarga (pdf - 1419,72 KB) 1 / 16 Imprimible Descarga aquí la versión imprimible de este tema. Si quieres escuchar el contenido de este archivo, puedes instalar en tu ordenador el lector de pantalla libre y gratuito NDVA. Aviso Legal Las páginas externas no se muestran en la versión imprimible http://www.juntadeandalucia.es/educacion/permanente/materiales/index.php?aviso#space