A330-200/300 Differences From A318/A319/A320/A321 Training Manual PDF
Document Details
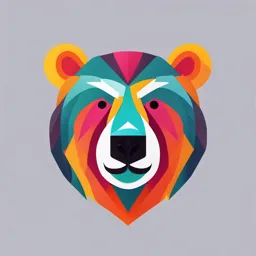
Uploaded by EminentAspen
UAntwerp
2019
Tags
Related
- ET-PP04 Aircraft Engine Inspection, Maintenance, Operation, and Troubleshooting PDF
- A330-200/300 Fuel System Training Manual PDF
- A330-200/300 Training Manual (CFM56/V2500) PDF
- A330-200/300 Fuel Inerting Training Manual PDF
- A330-200/300 Fuel System Training Manual PDF
- A330 RR Trent 700 Technical Training Manual PDF
Summary
This document provides detailed information on engine installation procedures for the A330-200/300 aircraft, including discussions on installing bootstrap systems and attaching engine transportation stands. The document outlines the connections for various systems like fuel, hydraulics, and electrical, covering crucial aspects of engine mounting and related configurations. It's part of a technical training guide.
Full Transcript
A330-200/300 DIFFERENCES FROM A318/A319/A320/A321 (CFM56/V2500) TRAINING MANUAL RR TRENT 700 THIS MANUAL IS FOR TRAINING PURPOSES ONLY AND SHOULD NOT BE USED FOR ANY OTHER PURPOSE THESE NOTES ARE NOT UPDATED B1/B2\_A330\_DIFF\_FR\_A320 REV. 1 DATE: 01.06.2019 DVIATION TRAINING SERVICES FO...
A330-200/300 DIFFERENCES FROM A318/A319/A320/A321 (CFM56/V2500) TRAINING MANUAL RR TRENT 700 THIS MANUAL IS FOR TRAINING PURPOSES ONLY AND SHOULD NOT BE USED FOR ANY OTHER PURPOSE THESE NOTES ARE NOT UPDATED B1/B2\_A330\_DIFF\_FR\_A320 REV. 1 DATE: 01.06.2019 DVIATION TRAINING SERVICES FOR TRAINING PURPOSES ONLY POWER PLANT (RR TRENT 700) GENERAL Power Plant Installation D/O (3)............................. 2 Nacelle D/O (3)......................................... 30 Engine D/O (3).......................................... 48 FUEL SYSTEM Engine Fuel System D/O (3)............................... 76 Engine Limit Protection D/O (3)........................... 106 FULL AUTHORITY DIGITAL ENGINE CONTROL (FADEC) FADEC Principle (3).................................... 116 FADEC D/O (3)........................................ 124 EIVMU Interfaces (3).................................... 158 FADEC Power Supply D/O (3)............................ 168 Power Plant RR Trent 700 Component Location (2)............ 174 Engine System Control & Indicating (2)..................... 206 IGNITION AND STARTING Ignition and Starting D/O (3).............................. 208 AIR SYSTEM Airflow Control System D/O (3)........................... 276 COOLING Engine Cooling System D/O (3)........................... 286 ENGINE CONTROLS Thrust Control D/O (3)................................... 296 Engine Master Control D/O (3)............................ 312 ENGINE INDICATING Vibration Monitoring System D/O (3)....................... 318 THRUST REVERSER Thrust Reverser System D/O (3)........................... 324 OIL SYSTEM Oil System D/O (3)...................................... 362 Engine System Operation, Control & Indicating (3)............ 408 MAINTENANCE PRACTICE Power Plant System Line Maintenance (2)................... 410 Engine Base Maintenance (3).............................. 440 MECHANICAL & AVIONICS COURSE - T1+T2 (LVL 2&3) 70 - POWER PLANT (RR Trent 700) TABLE OF CONTENTS Apr 18, 2013 Page 1 A330 RR Trent 700 TECHNICAL TRAINING MANUAL GCL13151 - GEHT0M0 B1/B2\_A330\_DIFF\_FR\_A320 REV. 1 DATE: 01.06.2019 DVIATION TRAINING SERVICES FOR TRAINING PURPOSES ONLY 1 POWER PLANT INSTALLATION D/O (3) BOOTSTRAP SYSTEM INSTALLATION The removal and installation of the engine requires the installation of a bootstrap system on the aircraft pylon. The bootstrap system is composed of two elements, to be installed at the front and at the rear of the pylon. Each element is used to attach at its ends the chain pulley blocks assembly and dynamometers that are used to lower or to lift the transportation stand attached to the engine. MECHANICAL & AVIONICS COURSE - T1+T2 (LVL 2&3) 70 - POWER PLANT (RR Trent 700) POWER PLANT INSTALLATION D/O (3) Apr 16, 2013 Page 2 A330 RR Trent 700 TECHNICAL TRAINING MANUAL GCL13151 - GEHT0M0 - FM70D9000000071 B1/B2\_A330\_DIFF\_FR\_A320 REV. 1 DATE: 01.06.2019 DVIATION TRAINING SERVICES FOR TRAINING PURPOSES ONLY 2 BOOTSTRAP SYSTEM INSTALLATION MECHANICAL & AVIONICS COURSE - T1+T2 (LVL 2&3) 70 - POWER PLANT (RR Trent 700) POWER PLANT INSTALLATION D/O (3) Apr 16, 2013 Page 3 A330 RR Trent 700 TECHNICAL TRAINING MANUAL GCL13151 - GEHT0M0 - FM70D9000000071 B1/B2\_A330\_DIFF\_FR\_A320 REV. 1 DATE: 01.06.2019 DVIATION TRAINING SERVICES FOR TRAINING PURPOSES ONLY 3 BOOTSTRAP SYSTEM INSTALLATION MECHANICAL & AVIONICS COURSE - T1+T2 (LVL 2&3) 70 - POWER PLANT (RR Trent 700) POWER PLANT INSTALLATION D/O (3) Apr 16, 2013 Page 4 A330 RR Trent 700 TECHNICAL TRAINING MANUAL GCL13151 - GEHT0M0 - FM70D9000000071 B1/B2\_A330\_DIFF\_FR\_A320 REV. 1 DATE: 01.06.2019 DVIATION TRAINING SERVICES FOR TRAINING PURPOSES ONLY 4 BOOTSTRAP SYSTEM INSTALLATION MECHANICAL & AVIONICS COURSE - T1+T2 (LVL 2&3) 70 - POWER PLANT (RR Trent 700) POWER PLANT INSTALLATION D/O (3) Apr 16, 2013 Page 5 A330 RR Trent 700 TECHNICAL TRAINING MANUAL GCL13151 - GEHT0M0 - FM70D9000000071 B1/B2\_A330\_DIFF\_FR\_A320 REV. 1 DATE: 01.06.2019 DVIATION TRAINING SERVICES FOR TRAINING PURPOSES ONLY 5 POWER PLANT INSTALLATION D/O (3) ENGINE TRANSPORTATION STAND ATTACHMENT POINTS The engine transportation stand, which is used for engine removal and installation, can be attached to the engine by four trunnions: \- two front trunnions attached onto the intermediate case, on the LH side and RH sides, \- two rear trunnions attached onto the tail bearing housing, on the LH side and RH sides. MECHANICAL & AVIONICS COURSE - T1+T2 (LVL 2&3) 70 - POWER PLANT (RR Trent 700) POWER PLANT INSTALLATION D/O (3) Apr 16, 2013 Page 6 A330 RR Trent 700 TECHNICAL TRAINING MANUAL GCL13151 - GEHT0M0 - FM70D9000000071 B1/B2\_A330\_DIFF\_FR\_A320 REV. 1 DATE: 01.06.2019 DVIATION TRAINING SERVICES FOR TRAINING PURPOSES ONLY 6 ENGINE TRANSPORTATION STAND ATTACHMENT POINTS MECHANICAL & AVIONICS COURSE - T1+T2 (LVL 2&3) 70 - POWER PLANT (RR Trent 700) POWER PLANT INSTALLATION D/O (3) Apr 16, 2013 Page 7 A330 RR Trent 700 TECHNICAL TRAINING MANUAL GCL13151 - GEHT0M0 - FM70D9000000071 B1/B2\_A330\_DIFF\_FR\_A320 REV. 1 DATE: 01.06.2019 DVIATION TRAINING SERVICES FOR TRAINING PURPOSES ONLY 7 POWER PLANT INSTALLATION D/O (3) ENGINE MOUNTS The engine is attached to the aircraft pylon by two mounts, which support the weight of the engine and transmit thrust loads to the aircraft structure. The engine front mount is installed on the top of the engine intermediate case and is attached to the aircraft pylon by four tension bolts. The front mount is designed with a failsafe feature and transmits vertical, side and thrust loads to the aircraft pylon. The engine rear mount is installed on top of the turbine exhaust case and is attached to the aircraft pylon by four tension bolts. This mount is also designed with a failsafe feature, and transmits vertical, side and torsion loads to the aircraft pylon. MECHANICAL & AVIONICS COURSE - T1+T2 (LVL 2&3) 70 - POWER PLANT (RR Trent 700) POWER PLANT INSTALLATION D/O (3) Apr 16, 2013 Page 8 A330 RR Trent 700 TECHNICAL TRAINING MANUAL GCL13151 - GEHT0M0 - FM70D9000000071 B1/B2\_A330\_DIFF\_FR\_A320 REV. 1 DATE: 01.06.2019 DVIATION TRAINING SERVICES FOR TRAINING PURPOSES ONLY 8 ENGINE MOUNTS MECHANICAL & AVIONICS COURSE - T1+T2 (LVL 2&3) 70 - POWER PLANT (RR Trent 700) POWER PLANT INSTALLATION D/O (3) Apr 16, 2013 Page 9 A330 RR Trent 700 TECHNICAL TRAINING MANUAL GCL13151 - GEHT0M0 - FM70D9000000071 B1/B2\_A330\_DIFF\_FR\_A320 REV. 1 DATE: 01.06.2019 DVIATION TRAINING SERVICES FOR TRAINING PURPOSES ONLY 9 POWER PLANT INSTALLATION D/O (3) FLUID CONNECTIONS The fluid connections between engine and aircraft pylon are located on the RH side of the fan case. The fluid connection line for the fuel system is the LP fuel supply line. The fluid connection lines for the hydraulic system are: \- the hydraulic pressure line and suction line of the green system, \- the hydraulic pressure line and suction line of the blue or yellow system, \- the hydraulic case drain of the green system, \- the hydraulic case drain of the blue or yellow system. MECHANICAL & AVIONICS COURSE - T1+T2 (LVL 2&3) 70 - POWER PLANT (RR Trent 700) POWER PLANT INSTALLATION D/O (3) Apr 16, 2013 Page 10 A330 RR Trent 700 TECHNICAL TRAINING MANUAL GCL13151 - GEHT0M0 - FM70D9000000071 B1/B2\_A330\_DIFF\_FR\_A320 REV. 1 DATE: 01.06.2019 DVIATION TRAINING SERVICES FOR TRAINING PURPOSES ONLY 10 FLUID CONNECTIONS MECHANICAL & AVIONICS COURSE - T1+T2 (LVL 2&3) 70 - POWER PLANT (RR Trent 700) POWER PLANT INSTALLATION D/O (3) Apr 16, 2013 Page 11 A330 RR Trent 700 TECHNICAL TRAINING MANUAL GCL13151 - GEHT0M0 - FM70D9000000071 B1/B2\_A330\_DIFF\_FR\_A320 REV. 1 DATE: 01.06.2019 DVIATION TRAINING SERVICES FOR TRAINING PURPOSES ONLY 11 POWER PLANT INSTALLATION D/O (3) THRUST REVERSER ISOLATION CONTROL UNIT (ICU) ELECTRICAL CONNECTION The Isolation Control Unit (ICU) of the Thrust Reverser system receives two electrical connectors for its control and monitoring. MECHANICAL & AVIONICS COURSE - T1+T2 (LVL 2&3) 70 - POWER PLANT (RR Trent 700) POWER PLANT INSTALLATION D/O (3) Apr 16, 2013 Page 12 A330 RR Trent 700 TECHNICAL TRAINING MANUAL GCL13151 - GEHT0M0 - FM70D9000000071 B1/B2\_A330\_DIFF\_FR\_A320 REV. 1 DATE: 01.06.2019 DVIATION TRAINING SERVICES FOR TRAINING PURPOSES ONLY 12 THRUST REVERSER ISOLATION CONTROL UNIT (ICU) ELECTRICAL CONNECTION MECHANICAL & AVIONICS COURSE - T1+T2 (LVL 2&3) 70 - POWER PLANT (RR Trent 700) POWER PLANT INSTALLATION D/O (3) Apr 16, 2013 Page 13 A330 RR Trent 700 TECHNICAL TRAINING MANUAL GCL13151 - GEHT0M0 - FM70D9000000071 B1/B2\_A330\_DIFF\_FR\_A320 REV. 1 DATE: 01.06.2019 DVIATION TRAINING SERVICES FOR TRAINING PURPOSES ONLY 13 POWER PLANT INSTALLATION D/O (3) FAN ELECTRICAL INTERFACE PANEL The fan electrical interface panel is used for the connections between the fan electrical harnesses and the pylon. It is installed on the LH side of the fan case upper part. MECHANICAL & AVIONICS COURSE - T1+T2 (LVL 2&3) 70 - POWER PLANT (RR Trent 700) POWER PLANT INSTALLATION D/O (3) Apr 16, 2013 Page 14 A330 RR Trent 700 TECHNICAL TRAINING MANUAL GCL13151 - GEHT0M0 - FM70D9000000071 B1/B2\_A330\_DIFF\_FR\_A320 REV. 1 DATE: 01.06.2019 DVIATION TRAINING SERVICES FOR TRAINING PURPOSES ONLY 14 FAN ELECTRICAL INTERFACE PANEL MECHANICAL & AVIONICS COURSE - T1+T2 (LVL 2&3) 70 - POWER PLANT (RR Trent 700) POWER PLANT INSTALLATION D/O (3) Apr 16, 2013 Page 15 A330 RR Trent 700 TECHNICAL TRAINING MANUAL GCL13151 - GEHT0M0 - FM70D9000000071 B1/B2\_A330\_DIFF\_FR\_A320 REV. 1 DATE: 01.06.2019 DVIATION TRAINING SERVICES FOR TRAINING PURPOSES ONLY 15 POWER PLANT INSTALLATION D/O (3) CORE ELECTRICAL INTERFACE PANEL The core electrical interface panel is used for the connections between the core electrical harnesses and the pylon. It is installed near to the engine front mount. MECHANICAL & AVIONICS COURSE - T1+T2 (LVL 2&3) 70 - POWER PLANT (RR Trent 700) POWER PLANT INSTALLATION D/O (3) Apr 16, 2013 Page 16 A330 RR Trent 700 TECHNICAL TRAINING MANUAL GCL13151 - GEHT0M0 - FM70D9000000071 B1/B2\_A330\_DIFF\_FR\_A320 REV. 1 DATE: 01.06.2019 DVIATION TRAINING SERVICES FOR TRAINING PURPOSES ONLY 16 CORE ELECTRICAL INTERFACE PANEL MECHANICAL & AVIONICS COURSE - T1+T2 (LVL 2&3) 70 - POWER PLANT (RR Trent 700) POWER PLANT INSTALLATION D/O (3) Apr 16, 2013 Page 17 A330 RR Trent 700 TECHNICAL TRAINING MANUAL GCL13151 - GEHT0M0 - FM70D9000000071 B1/B2\_A330\_DIFF\_FR\_A320 REV. 1 DATE: 01.06.2019 DVIATION TRAINING SERVICES FOR TRAINING PURPOSES ONLY 17 POWER PLANT INSTALLATION D/O (3) IDG POWER CABLES TERMINAL BLOCK The IDG power cables are routed vertically at the rear of the LH fan case. They are connected to the aircraft cables through a terminal block located near the fan electrical interface panel. MECHANICAL & AVIONICS COURSE - T1+T2 (LVL 2&3) 70 - POWER PLANT (RR Trent 700) POWER PLANT INSTALLATION D/O (3) Apr 16, 2013 Page 18 A330 RR Trent 700 TECHNICAL TRAINING MANUAL GCL13151 - GEHT0M0 - FM70D9000000071 B1/B2\_A330\_DIFF\_FR\_A320 REV. 1 DATE: 01.06.2019 DVIATION TRAINING SERVICES FOR TRAINING PURPOSES ONLY 18 IDG POWER CABLES TERMINAL BLOCK MECHANICAL & AVIONICS COURSE - T1+T2 (LVL 2&3) 70 - POWER PLANT (RR Trent 700) POWER PLANT INSTALLATION D/O (3) Apr 16, 2013 Page 19 A330 RR Trent 700 TECHNICAL TRAINING MANUAL GCL13151 - GEHT0M0 - FM70D9000000071 B1/B2\_A330\_DIFF\_FR\_A320 REV. 1 DATE: 01.06.2019 DVIATION TRAINING SERVICES FOR TRAINING PURPOSES ONLY 19 POWER PLANT INSTALLATION D/O (3) EEC PROTECTION BOX ELECTRICAL CONNECTIONS The Engine Electronic Controller (EEC) protection box receives electrical connectors at the top RH corner to get the electrical connections to the EEC, the Overspeed Protection Unit (OPU) and the Power Control Unit (PCU). MECHANICAL & AVIONICS COURSE - T1+T2 (LVL 2&3) 70 - POWER PLANT (RR Trent 700) POWER PLANT INSTALLATION D/O (3) Apr 16, 2013 Page 20 A330 RR Trent 700 TECHNICAL TRAINING MANUAL GCL13151 - GEHT0M0 - FM70D9000000071 B1/B2\_A330\_DIFF\_FR\_A320 REV. 1 DATE: 01.06.2019 DVIATION TRAINING SERVICES FOR TRAINING PURPOSES ONLY 20 EEC PROTECTION BOX ELECTRICAL CONNECTIONS MECHANICAL & AVIONICS COURSE - T1+T2 (LVL 2&3) 70 - POWER PLANT (RR Trent 700) POWER PLANT INSTALLATION D/O (3) Apr 16, 2013 Page 21 A330 RR Trent 700 TECHNICAL TRAINING MANUAL GCL13151 - GEHT0M0 - FM70D9000000071 B1/B2\_A330\_DIFF\_FR\_A320 REV. 1 DATE: 01.06.2019 DVIATION TRAINING SERVICES FOR TRAINING PURPOSES ONLY 21 POWER PLANT INSTALLATION D/O (3) PNEUMATIC DUCTS CONNECTION The starter air duct is installed at the front of the LH fan case. It is connected to the pylon through an interface duct attached by two clamps. The connection of the engine bleed air system to the aircraft pneumatic system is done on the LH side of engine core through an interface duct attached by 2 clamps. MECHANICAL & AVIONICS COURSE - T1+T2 (LVL 2&3) 70 - POWER PLANT (RR Trent 700) POWER PLANT INSTALLATION D/O (3) Apr 16, 2013 Page 22 A330 RR Trent 700 TECHNICAL TRAINING MANUAL GCL13151 - GEHT0M0 - FM70D9000000071 B1/B2\_A330\_DIFF\_FR\_A320 REV. 1 DATE: 01.06.2019 DVIATION TRAINING SERVICES FOR TRAINING PURPOSES ONLY 22 PNEUMATIC DUCTS CONNECTION MECHANICAL & AVIONICS COURSE - T1+T2 (LVL 2&3) 70 - POWER PLANT (RR Trent 700) POWER PLANT INSTALLATION D/O (3) Apr 16, 2013 Page 23 A330 RR Trent 700 TECHNICAL TRAINING MANUAL GCL13151 - GEHT0M0 - FM70D9000000071 B1/B2\_A330\_DIFF\_FR\_A320 REV. 1 DATE: 01.06.2019 DVIATION TRAINING SERVICES FOR TRAINING PURPOSES ONLY 23 PNEUMATIC DUCTS CONNECTION MECHANICAL & AVIONICS COURSE - T1+T2 (LVL 2&3) 70 - POWER PLANT (RR Trent 700) POWER PLANT INSTALLATION D/O (3) Apr 16, 2013 Page 24 A330 RR Trent 700 TECHNICAL TRAINING MANUAL GCL13151 - GEHT0M0 - FM70D9000000071 B1/B2\_A330\_DIFF\_FR\_A320 REV. 1 DATE: 01.06.2019 DVIATION TRAINING SERVICES FOR TRAINING PURPOSES ONLY 24 This Page Intentionally Left Blank MECHANICAL & AVIONICS COURSE - T1+T2 (LVL 2&3) 70 - POWER PLANT (RR Trent 700) POWER PLANT INSTALLATION D/O (3) Apr 16, 2013 Page 25 A330 RR Trent 700 TECHNICAL TRAINING MANUAL GCL13151 - GEHT0M0 - FM70D9000000071 B1/B2\_A330\_DIFF\_FR\_A320 REV. 1 DATE: 01.06.2019 DVIATION TRAINING SERVICES FOR TRAINING PURPOSES ONLY 25 POWER PLANT INSTALLATION D/O (3) SYSTEM PYLON INTERFACES The following system connections are connected with the engine to the pylon interface, on the RH side: \- core zone fire extinguishing line, \- hydraulic reservoir pressurization air tube (engine 1 only), \- sense line connecting Pressure Regulating Valve (PRV) to Thermostat Solenoid (THS) of engine bleed air system. The sense lines connecting to the bleed Regulated Pressure (Pr) transducer and the Transferred Pressure (Pt) transducer interface with the pylon on the LH side. MECHANICAL & AVIONICS COURSE - T1+T2 (LVL 2&3) 70 - POWER PLANT (RR Trent 700) POWER PLANT INSTALLATION D/O (3) Apr 16, 2013 Page 26 A330 RR Trent 700 TECHNICAL TRAINING MANUAL GCL13151 - GEHT0M0 - FM70D9000000071 B1/B2\_A330\_DIFF\_FR\_A320 REV. 1 DATE: 01.06.2019 DVIATION TRAINING SERVICES FOR TRAINING PURPOSES ONLY 26 SYSTEM PYLON INTERFACES MECHANICAL & AVIONICS COURSE - T1+T2 (LVL 2&3) 70 - POWER PLANT (RR Trent 700) POWER PLANT INSTALLATION D/O (3) Apr 16, 2013 Page 27 A330 RR Trent 700 TECHNICAL TRAINING MANUAL GCL13151 - GEHT0M0 - FM70D9000000071 B1/B2\_A330\_DIFF\_FR\_A320 REV. 1 DATE: 01.06.2019 DVIATION TRAINING SERVICES FOR TRAINING PURPOSES ONLY 27 SYSTEM PYLON INTERFACES MECHANICAL & AVIONICS COURSE - T1+T2 (LVL 2&3) 70 - POWER PLANT (RR Trent 700) POWER PLANT INSTALLATION D/O (3) Apr 16, 2013 Page 28 A330 RR Trent 700 TECHNICAL TRAINING MANUAL GCL13151 - GEHT0M0 - FM70D9000000071 B1/B2\_A330\_DIFF\_FR\_A320 REV. 1 DATE: 01.06.2019 DVIATION TRAINING SERVICES FOR TRAINING PURPOSES ONLY 28 This Page Intentionally Left Blank MECHANICAL & AVIONICS COURSE - T1+T2 (LVL 2&3) 70 - POWER PLANT (RR Trent 700) POWER PLANT INSTALLATION D/O (3) Apr 16, 2013 Page 29 A330 RR Trent 700 TECHNICAL TRAINING MANUAL GCL13151 - GEHT0M0 - FM70D9000000071 B1/B2\_A330\_DIFF\_FR\_A320 REV. 1 DATE: 01.06.2019 DVIATION TRAINING SERVICES FOR TRAINING PURPOSES ONLY 29 NACELLE D/O (3) INLET COWL The inlet cowl is attached to the forward flange of the LP compressor case (fan case) and is de-iced. The air inlet cowl assembly is composed of: \- an inner and outer barrel, \- a rear bulkhead and, \- an intake cowl leading edge (lip) assembly which contains the forward bulkhead. The assembly also has: \- a thermal anti ice air outlet, \- a P20/T20 probe and access panel, \- a zone 1 cooling air inlet, \- a maintenance interphone jack, \- electronic unit protection box cooling ducts, \- and four hoisting points. MECHANICAL & AVIONICS COURSE - T1+T2 (LVL 2&3) 70 - POWER PLANT (RR Trent 700) NACELLE D/O (3) Apr 16, 2013 Page 30 A330 RR Trent 700 TECHNICAL TRAINING MANUAL GCL13151 - GEHT0M0 - FM70D8000000071 B1/B2\_A330\_DIFF\_FR\_A320 REV. 1 DATE: 01.06.2019 DVIATION TRAINING SERVICES FOR TRAINING PURPOSES ONLY 30 INLET COWL MECHANICAL & AVIONICS COURSE - T1+T2 (LVL 2&3) 70 - POWER PLANT (RR Trent 700) NACELLE D/O (3) Apr 16, 2013 Page 31 A330 RR Trent 700 TECHNICAL TRAINING MANUAL GCL13151 - GEHT0M0 - FM70D8000000071 B1/B2\_A330\_DIFF\_FR\_A320 REV. 1 DATE: 01.06.2019 DVIATION TRAINING SERVICES FOR TRAINING PURPOSES ONLY 31 NACELLE D/O (3) FAN COWL DOORS The fan cowls are attached by four hinges and secured together by four latches at the bottom to close around the LP compressor case. Two deflection restraints make sure that the front lower corners cannot droop below the nose cowl line. They can be opened during ground maintenance to give access to the components installed on the case and on the gearbox, and let the thrust reverser halves (C-Duct) be opened. Each fan cowl door is maintained open by means of two telescopic hold open rods. There are two hold open positions, 55 degrees and 44 degrees. The 55 degrees maximum open position gives the access to the pylon interfaces and upper accessories. The 44 degrees position gives access to other features. Each fan cowl door has various access doors and outlets. LEFT FAN COWL The left fan cowl has: \- the starter control valve, thrust reverser ground safety switch and anti ice valve access door, \- the Integrated Drive Generator (IDG) oil fill-sight glass and reset lever access door, \- and the IDG oil cooler air outlet. RIGHT FAN COWL The right fan cowl has: \- the oil fill sight-glass access door, \- a hydraulic filter contamination indicator and master Magnetic Chip Detector (MCD) access door, \- the Air Oil Heat Exchanger (AOHE) air outlet, \- the zone 1 airflow outlet, \- and the breather outlet mast. MECHANICAL & AVIONICS COURSE - T1+T2 (LVL 2&3) 70 - POWER PLANT (RR Trent 700) NACELLE D/O (3) Apr 16, 2013 Page 32 A330 RR Trent 700 TECHNICAL TRAINING MANUAL GCL13151 - GEHT0M0 - FM70D8000000071 B1/B2\_A330\_DIFF\_FR\_A320 REV. 1 DATE: 01.06.2019 DVIATION TRAINING SERVICES FOR TRAINING PURPOSES ONLY 32 FAN COWL DOORS - LEFT FAN COWL & RIGHT FAN COWL MECHANICAL & AVIONICS COURSE - T1+T2 (LVL 2&3) 70 - POWER PLANT (RR Trent 700) NACELLE D/O (3) Apr 16, 2013 Page 33 A330 RR Trent 700 TECHNICAL TRAINING MANUAL GCL13151 - GEHT0M0 - FM70D8000000071 B1/B2\_A330\_DIFF\_FR\_A320 REV. 1 DATE: 01.06.2019 DVIATION TRAINING SERVICES FOR TRAINING PURPOSES ONLY 33 NACELLE D/O (3) FAN COWL DOORS (continued) FAN COWL LATCHES The fan cowls are latched together along the bottom centerline by four latches. The RH fan cowl has four hook type latches that adjust in four keepers on the LH fan cowl. The keepers and the latches are installed into housings. Each keeper housing has one spigot and one bolt to be in contact with its related latch housing. The latch handles are visible when they are not properly engaged. They are flushing when they are correctly engaged. NOTE: Note: You must not open the fan cowls if wind speed is 60 MPH (96 KMH) or more. The fan cowl latches must be operated in the following sequence 1, 3, 2, 4 (numbered from the front to the rear) for locking and unlocking. MECHANICAL & AVIONICS COURSE - T1+T2 (LVL 2&3) 70 - POWER PLANT (RR Trent 700) NACELLE D/O (3) Apr 16, 2013 Page 34 A330 RR Trent 700 TECHNICAL TRAINING MANUAL GCL13151 - GEHT0M0 - FM70D8000000071 B1/B2\_A330\_DIFF\_FR\_A320 REV. 1 DATE: 01.06.2019 DVIATION TRAINING SERVICES FOR TRAINING PURPOSES ONLY 34 FAN COWL DOORS - FAN COWL LATCHES MECHANICAL & AVIONICS COURSE - T1+T2 (LVL 2&3) 70 - POWER PLANT (RR Trent 700) NACELLE D/O (3) Apr 16, 2013 Page 35 A330 RR Trent 700 TECHNICAL TRAINING MANUAL GCL13151 - GEHT0M0 - FM70D8000000071 B1/B2\_A330\_DIFF\_FR\_A320 REV. 1 DATE: 01.06.2019 DVIATION TRAINING SERVICES FOR TRAINING PURPOSES ONLY 35 NACELLE D/O (3) THRUST REVERSER ASSEMBLY The thrust reverser assembly has two halves (also called C-ducts) attached to the aircraft pylon with 5 hinges each and are latched together by means of 7 latches. When the C-ducts are closed, they make a cover over the core engine and form a smooth bypass duct from the LP compressor (fan) into the Common Nozzle Assembly (CNA). The thrust reverser assembly contains the mechanism for reversing the fan airflow during aircraft landing. Each thrust reverser half opens hydraulically by means of an actuator located underneath the engine pylon and is secured open with two hold open rods. Operation of the actuators requires a hand operated hydraulic pump. Each C-duct includes: \- a front frame, \- an inner fixed structure, \- an outer fixed structure, \- two pivoting doors. MECHANICAL & AVIONICS COURSE - T1+T2 (LVL 2&3) 70 - POWER PLANT (RR Trent 700) NACELLE D/O (3) Apr 16, 2013 Page 36 A330 RR Trent 700 TECHNICAL TRAINING MANUAL GCL13151 - GEHT0M0 - FM70D8000000071 B1/B2\_A330\_DIFF\_FR\_A320 REV. 1 DATE: 01.06.2019 DVIATION TRAINING SERVICES FOR TRAINING PURPOSES ONLY 36 THRUST REVERSER ASSEMBLY MECHANICAL & AVIONICS COURSE - T1+T2 (LVL 2&3) 70 - POWER PLANT (RR Trent 700) NACELLE D/O (3) Apr 16, 2013 Page 37 A330 RR Trent 700 TECHNICAL TRAINING MANUAL GCL13151 - GEHT0M0 - FM70D8000000071 B1/B2\_A330\_DIFF\_FR\_A320 REV. 1 DATE: 01.06.2019 DVIATION TRAINING SERVICES FOR TRAINING PURPOSES ONLY 37 NACELLE D/O (3) THRUST REVERSER ASSEMBLY (continued) THRUST REVERSER ASSEMBLY LATCHES The C-ducts are latched together with seven latches: \- The number 1 latch is mounted on the front frame and is operated by a remote lever. \- The number 2 to 7 latches are mounted on the 6 o\'clock beam. Latches 3 and 4 are the shear-pin type and are accessible through the latch access and overpressure relief doors. The latches 1, 2, 5, 6 and 7 are of hook type. A take-up device is installed between latches 3 and 4 that is used to pull the thrust reverser cowl doors together until you can fasten the latches easily. NOTE: Note: \- You must not open the C-ducts if wind speed is 46 MPH (73 KMH) or more. \- Before opening the C-ducts the thrust reverser must be deactivated. \- The take-up device must be operated before to release the latches. \- The opening sequence is latches number 2, 5, 6, 7, 1, 3, 4. \- The closing sequence is latches number 3, 4, 1, 7, 6, 5, 2. MECHANICAL & AVIONICS COURSE - T1+T2 (LVL 2&3) 70 - POWER PLANT (RR Trent 700) NACELLE D/O (3) Apr 16, 2013 Page 38 A330 RR Trent 700 TECHNICAL TRAINING MANUAL GCL13151 - GEHT0M0 - FM70D8000000071 B1/B2\_A330\_DIFF\_FR\_A320 REV. 1 DATE: 01.06.2019 DVIATION TRAINING SERVICES FOR TRAINING PURPOSES ONLY 38 THRUST REVERSER ASSEMBLY - THRUST REVERSER ASSEMBLY LATCHES MECHANICAL & AVIONICS COURSE - T1+T2 (LVL 2&3) 70 - POWER PLANT (RR Trent 700) NACELLE D/O (3) Apr 16, 2013 Page 39 A330 RR Trent 700 TECHNICAL TRAINING MANUAL GCL13151 - GEHT0M0 - FM70D8000000071 B1/B2\_A330\_DIFF\_FR\_A320 REV. 1 DATE: 01.06.2019 DVIATION TRAINING SERVICES FOR TRAINING PURPOSES ONLY 39 NACELLE D/O (3) COMMON NOZZLE ASSEMBLY The function of the Common Nozzle Assembly (CNA) is to mix the core engine exhaust with the LP compressor (fan) air. The CNA has the shape of a convergent duct which increases the velocity of the mixed gas and thus gives added thrust. The CNA is attached directly onto the LP turbine module of the engine. The CNA is an interchangeable assembly that has an inner and an outer duct assembly. The inner duct assembly is annular and is the primary exhaust nozzle around the core engine exhaust. The outer duct assembly is held by six aerodynamic struts attached to the inner duct assembly. If the CNA is replaced by an other CNA, which doesn\'t have the same nozzle EPR number, you can enter the new number with the Data Entry Plug (DEP). MECHANICAL & AVIONICS COURSE - T1+T2 (LVL 2&3) 70 - POWER PLANT (RR Trent 700) NACELLE D/O (3) Apr 16, 2013 Page 40 A330 RR Trent 700 TECHNICAL TRAINING MANUAL GCL13151 - GEHT0M0 - FM70D8000000071 B1/B2\_A330\_DIFF\_FR\_A320 REV. 1 DATE: 01.06.2019 DVIATION TRAINING SERVICES FOR TRAINING PURPOSES ONLY 40 COMMON NOZZLE ASSEMBLY MECHANICAL & AVIONICS COURSE - T1+T2 (LVL 2&3) 70 - POWER PLANT (RR Trent 700) NACELLE D/O (3) Apr 16, 2013 Page 41 A330 RR Trent 700 TECHNICAL TRAINING MANUAL GCL13151 - GEHT0M0 - FM70D8000000071 B1/B2\_A330\_DIFF\_FR\_A320 REV. 1 DATE: 01.06.2019 DVIATION TRAINING SERVICES FOR TRAINING PURPOSES ONLY 41 COMMON NOZZLE ASSEMBLY MECHANICAL & AVIONICS COURSE - T1+T2 (LVL 2&3) 70 - POWER PLANT (RR Trent 700) NACELLE D/O (3) Apr 16, 2013 Page 42 A330 RR Trent 700 TECHNICAL TRAINING MANUAL GCL13151 - GEHT0M0 - FM70D8000000071 B1/B2\_A330\_DIFF\_FR\_A320 REV. 1 DATE: 01.06.2019 DVIATION TRAINING SERVICES FOR TRAINING PURPOSES ONLY 42 This Page Intentionally Left Blank MECHANICAL & AVIONICS COURSE - T1+T2 (LVL 2&3) 70 - POWER PLANT (RR Trent 700) NACELLE D/O (3) Apr 16, 2013 Page 43 A330 RR Trent 700 TECHNICAL TRAINING MANUAL GCL13151 - GEHT0M0 - FM70D8000000071 B1/B2\_A330\_DIFF\_FR\_A320 REV. 1 DATE: 01.06.2019 DVIATION TRAINING SERVICES FOR TRAINING PURPOSES ONLY 43 NACELLE D/O (3) NACELLE ACCESS DOORS Various access doors and panels around the engine give access to maintenance and servicing purposes. These doors and panels are: \- P20/T20 probe access panel, \- hydraulic filter contamination indicator and master MCD access door, \- oil fill and sight glass access door, \- starter control valve and thrust reverser ground safety switch access door, \- IDG oil fill-sight glass and reset lever access door, \- pivot access panels, \- thrust reverser Rotational Variable Transducer (RVT) access panels, \- number 4 latch access panels. MECHANICAL & AVIONICS COURSE - T1+T2 (LVL 2&3) 70 - POWER PLANT (RR Trent 700) NACELLE D/O (3) Apr 16, 2013 Page 44 A330 RR Trent 700 TECHNICAL TRAINING MANUAL GCL13151 - GEHT0M0 - FM70D8000000071 B1/B2\_A330\_DIFF\_FR\_A320 REV. 1 DATE: 01.06.2019 DVIATION TRAINING SERVICES FOR TRAINING PURPOSES ONLY 44 NACELLE ACCESS DOORS MECHANICAL & AVIONICS COURSE - T1+T2 (LVL 2&3) 70 - POWER PLANT (RR Trent 700) NACELLE D/O (3) Apr 16, 2013 Page 45 A330 RR Trent 700 TECHNICAL TRAINING MANUAL GCL13151 - GEHT0M0 - FM70D8000000071 B1/B2\_A330\_DIFF\_FR\_A320 REV. 1 DATE: 01.06.2019 DVIATION TRAINING SERVICES FOR TRAINING PURPOSES ONLY 45 NACELLE D/O (3) C-DUCT OPERATION The opening mechanism is designed to hydraulically open and close the thrust reverser cowls. The thrust reverser opening mechanism is composed of: \- one actuator for each C-duct, \- two hold open rods for each C-duct. The pressure is supplied by the hydraulic hand pump to extend the actuator. Actuators are operated until the C-duct is fully open. Once the C-duct is fully open, the hold open rods are installed and the pressure is released. The hold open rods lock automatically and keep the C-ducts open. NOTE: Note: You must not open the thrust reverser cowls if wind speed is 46 MPH (73 KMH) or more. MECHANICAL & AVIONICS COURSE - T1+T2 (LVL 2&3) 70 - POWER PLANT (RR Trent 700) NACELLE D/O (3) Apr 16, 2013 Page 46 A330 RR Trent 700 TECHNICAL TRAINING MANUAL GCL13151 - GEHT0M0 - FM70D8000000071 B1/B2\_A330\_DIFF\_FR\_A320 REV. 1 DATE: 01.06.2019 DVIATION TRAINING SERVICES FOR TRAINING PURPOSES ONLY 46 C-DUCT OPERATION MECHANICAL & AVIONICS COURSE - T1+T2 (LVL 2&3) 70 - POWER PLANT (RR Trent 700) NACELLE D/O (3) Apr 16, 2013 Page 47 A330 RR Trent 700 TECHNICAL TRAINING MANUAL GCL13151 - GEHT0M0 - FM70D8000000071 B1/B2\_A330\_DIFF\_FR\_A320 REV. 1 DATE: 01.06.2019 DVIATION TRAINING SERVICES FOR TRAINING PURPOSES ONLY 47 ENGINE D/O (3) GENERAL The bare engine is an assembly of primary units, which are identified as modules. These modules can be independently replaced in shop and are specified as follows: \- Low Pressure (LP) compressor rotor, \- Intermediate Pressure (IP) compressor, \- intermediate case, \- High Pressure (HP) system (this includes the HP compressor, the combustion system and the HP turbine), \- IP turbine, \- external gearbox, \- LP compressor case, \- LP turbine. The engine direction of rotation is counterclockwise, the pressure ratio is 37.42:1 and the bypass ratio is 4.66:1. The weight of the dressed basic engine is 5107 kg (11259 lb) approximately. The engine has different thrust ratings according to different engine version. The engine hardware is the same and the thrust rating is defined through the Data Entry Plug (DEP). The DEP is installed and plugged into the Engine Electronic Controller (EEC). MECHANICAL & AVIONICS COURSE - T1+T2 (LVL 2&3) 70 - POWER PLANT (RR Trent 700) ENGINE D/O (3) Apr 16, 2013 Page 48 A330 RR Trent 700 TECHNICAL TRAINING MANUAL GCL13151 - GEHT0M0 - FM70D1000000071 B1/B2\_A330\_DIFF\_FR\_A320 REV. 1 DATE: 01.06.2019 DVIATION TRAINING SERVICES FOR TRAINING PURPOSES ONLY 48 GENERAL MECHANICAL & AVIONICS COURSE - T1+T2 (LVL 2&3) 70 - POWER PLANT (RR Trent 700) ENGINE D/O (3) Apr 16, 2013 Page 49 A330 RR Trent 700 TECHNICAL TRAINING MANUAL GCL13151 - GEHT0M0 - FM70D1000000071 B1/B2\_A330\_DIFF\_FR\_A320 REV. 1 DATE: 01.06.2019 DVIATION TRAINING SERVICES FOR TRAINING PURPOSES ONLY 49 ENGINE D/O (3) ENGINE ROTORS AND MODULES The three rotating assemblies include: \- the LP Compressor (fan) connected by a shaft to the LP turbine, \- the IP compressor connected by a shaft to the IP turbine, \- the HP compressor connected by a shaft to the HP turbine. Shafts are supported by ball and roller bearings. MECHANICAL & AVIONICS COURSE - T1+T2 (LVL 2&3) 70 - POWER PLANT (RR Trent 700) ENGINE D/O (3) Apr 16, 2013 Page 50 A330 RR Trent 700 TECHNICAL TRAINING MANUAL GCL13151 - GEHT0M0 - FM70D1000000071 B1/B2\_A330\_DIFF\_FR\_A320 REV. 1 DATE: 01.06.2019 DVIATION TRAINING SERVICES FOR TRAINING PURPOSES ONLY 50 ENGINE ROTORS AND MODULES MECHANICAL & AVIONICS COURSE - T1+T2 (LVL 2&3) 70 - POWER PLANT (RR Trent 700) ENGINE D/O (3) Apr 16, 2013 Page 51 A330 RR Trent 700 TECHNICAL TRAINING MANUAL GCL13151 - GEHT0M0 - FM70D1000000071 B1/B2\_A330\_DIFF\_FR\_A320 REV. 1 DATE: 01.06.2019 DVIATION TRAINING SERVICES FOR TRAINING PURPOSES ONLY 51 ENGINE D/O (3) ENGINE ROTORS AND MODULES (continued) LOW PRESSURE COMPRESSOR AND TURBINE The one stage LP compressor (fan) has 26 wide-chord type blades which are engaged in axial dovetail slots. Each fan blade is held in the disk by two shear keys. The LP compressor is located in the fan case. The fan case is made of two cylindrical cases, which are connected together with nuts and bolts. The front part of this assembly contains the LP compressor rotor and the rear part includes the Outlets Guide Vanes (OGVs). Attached to the outside of the rear part there are many system components, electrical harness and tubes. The LP compressor shaft connects the fan disk through a curvic coupling that gives the accurate location. The LP turbine has four disks which are bolted together to make a drum. The stage 3 disk acts as the drive arm and is attached to the turbine shaft with a curvic coupling. The LP turbine case supports the rear engine mount. MECHANICAL & AVIONICS COURSE - T1+T2 (LVL 2&3) 70 - POWER PLANT (RR Trent 700) ENGINE D/O (3) Apr 16, 2013 Page 52 A330 RR Trent 700 TECHNICAL TRAINING MANUAL GCL13151 - GEHT0M0 - FM70D1000000071 B1/B2\_A330\_DIFF\_FR\_A320 REV. 1 DATE: 01.06.2019 DVIATION TRAINING SERVICES FOR TRAINING PURPOSES ONLY 52 ENGINE ROTORS AND MODULES - LOW PRESSURE COMPRESSOR AND TURBINE MECHANICAL & AVIONICS COURSE - T1+T2 (LVL 2&3) 70 - POWER PLANT (RR Trent 700) ENGINE D/O (3) Apr 16, 2013 Page 53 A330 RR Trent 700 TECHNICAL TRAINING MANUAL GCL13151 - GEHT0M0 - FM70D1000000071 B1/B2\_A330\_DIFF\_FR\_A320 REV. 1 DATE: 01.06.2019 DVIATION TRAINING SERVICES FOR TRAINING PURPOSES ONLY 53 ENGINE D/O (3) ENGINE ROTORS AND MODULES (continued) INTERMEDIATE PRESSURE COMPRESSOR AND TURBINE The IP compressor rotor is an assembly of 8 titanium rotor disks welded together as one drum. The disks at stages 1 to 6 have axial dovetail slots into which the rotor blades are installed. At stages 7 and 8, the blades are installed in circumferential dovetail slots. The IP compressor case is divided into two semicircular half cases. The front part contains the Variable Inlet Guide Vanes (VIGVs), the two stages of Variable Stator Vanes (VSVs) and the associated actuating rings. The rear part contains stages 3 to 8 of the compressor stator vanes. The intermediate case is made from two cylindrical titanium casings welded together. The front part is installed around the rear part of the IP compressor case and the rear part around the front part of the HP compressor. The front part includes the engine front mount and the rear part includes ten structural vanes to which the internal gearbox housing is connected. The IP turbine is a single stage turbine assembly. At the hub of the disk a drive arm extends rearwards, and connects the IP turbine shaft and stub shaft by using taper bolts. The IP turbine shaft runs forward and is connected to the IP compressor stub shaft with helical splines. In front of the IP turbine there are 26 Nozzle Guide Vanes (NGVs) which are radially installed around the turbine case. Adjacent to the casing rear flange is a Turbine Case Cooling (TCC) air manifold and the location bosses for 11 thermocouples. MECHANICAL & AVIONICS COURSE - T1+T2 (LVL 2&3) 70 - POWER PLANT (RR Trent 700) ENGINE D/O (3) Apr 16, 2013 Page 54 A330 RR Trent 700 TECHNICAL TRAINING MANUAL GCL13151 - GEHT0M0 - FM70D1000000071 B1/B2\_A330\_DIFF\_FR\_A320 REV. 1 DATE: 01.06.2019 DVIATION TRAINING SERVICES FOR TRAINING PURPOSES ONLY 54 ENGINE ROTORS AND MODULES - INTERMEDIATE PRESSURE COMPRESSOR AND TURBINE MECHANICAL & AVIONICS COURSE - T1+T2 (LVL 2&3) 70 - POWER PLANT (RR Trent 700) ENGINE D/O (3) Apr 16, 2013 Page 55 A330 RR Trent 700 TECHNICAL TRAINING MANUAL GCL13151 - GEHT0M0 - FM70D1000000071 B1/B2\_A330\_DIFF\_FR\_A320 REV. 1 DATE: 01.06.2019 DVIATION TRAINING SERVICES FOR TRAINING PURPOSES ONLY 55 ENGINE D/O (3) ENGINE ROTORS AND MODULES (continued) HIGH PRESSURE COMPRESSOR, COMBUSTION CHAMBER AND TURBINE The HP system includes: \- the HP compressor, \- the combustion chamber, \- the HP turbine. The HP compressor rotor is a six-stage assembly of titanium disks welded together to make a drum. The first stage blades are installed in axial dovetail slots and are locked with retaining plates. Stage 2 to 6 are installed in circumferential dovetail slots and locked with special nut and screw assemblies. The HP compressor case is an assembly of 5 flanged cylindrical casings bolted together. The combustion chamber is fully annular and includes an inner and an outer combustion liners. 24 locations are provided to receive the fuel spray nozzles. There are also 2 igniter plugs installed through bosses in the combustion chamber outer case. There are 40 NGVs installed at the combustion chamber outlet which are held by a support ring and attached with bolts to the combustion inner case. The HP turbine is a single stage disk which is attached to the rear of the compressor drum with bolts. On the rear of the disk there is a flange that is attached to a stubshaft. The disk has firtree roots into which fit the turbine blades. MECHANICAL & AVIONICS COURSE - T1+T2 (LVL 2&3) 70 - POWER PLANT (RR Trent 700) ENGINE D/O (3) Apr 16, 2013 Page 56 A330 RR Trent 700 TECHNICAL TRAINING MANUAL GCL13151 - GEHT0M0 - FM70D1000000071 B1/B2\_A330\_DIFF\_FR\_A320 REV. 1 DATE: 01.06.2019 DVIATION TRAINING SERVICES FOR TRAINING PURPOSES ONLY 56 ENGINE ROTORS AND MODULES - HIGH PRESSURE COMPRESSOR, COMBUSTION CHAMBER AND TURBINE MECHANICAL & AVIONICS COURSE - T1+T2 (LVL 2&3) 70 - POWER PLANT (RR Trent 700) ENGINE D/O (3) Apr 16, 2013 Page 57 A330 RR Trent 700 TECHNICAL TRAINING MANUAL GCL13151 - GEHT0M0 - FM70D1000000071 B1/B2\_A330\_DIFF\_FR\_A320 REV. 1 DATE: 01.06.2019 DVIATION TRAINING SERVICES FOR TRAINING PURPOSES ONLY 57 ENGINE D/O (3) ENGINE ROTORS AND MODULES (continued) ENGINE BEARINGS Two types of bearings are used in this engine: \- roller bearings keep the shafts in the correct radial position, \- location thrust ball bearings for all three shafts are positioned in the internal gearbox. The LP and IP rotor assemblies are each supported by three bearings. The HP rotor is supported by two bearings. There are 4 bearing chambers: \- the front bearing chamber includes the LP and the IP roller bearings, \- internal gearbox bearing chamber includes the LP, IP and HP location bearings, \- HP/IP turbine bearing chamber includes the HP and IP turbine roller bearings, \- LP turbine bearing chamber includes the LP turbine roller bearing and the LP turbine spring pack bearing. Bearing chambers are sealed using IP and HP air and are isolated from other engine parts by labyrinth seals. MECHANICAL & AVIONICS COURSE - T1+T2 (LVL 2&3) 70 - POWER PLANT (RR Trent 700) ENGINE D/O (3) Apr 16, 2013 Page 58 A330 RR Trent 700 TECHNICAL TRAINING MANUAL GCL13151 - GEHT0M0 - FM70D1000000071 B1/B2\_A330\_DIFF\_FR\_A320 REV. 1 DATE: 01.06.2019 DVIATION TRAINING SERVICES FOR TRAINING PURPOSES ONLY 58 ENGINE ROTORS AND MODULES - ENGINE BEARINGS MECHANICAL & AVIONICS COURSE - T1+T2 (LVL 2&3) 70 - POWER PLANT (RR Trent 700) ENGINE D/O (3) Apr 16, 2013 Page 59 A330 RR Trent 700 TECHNICAL TRAINING MANUAL GCL13151 - GEHT0M0 - FM70D1000000071 B1/B2\_A330\_DIFF\_FR\_A320 REV. 1 DATE: 01.06.2019 DVIATION TRAINING SERVICES FOR TRAINING PURPOSES ONLY 59 ENGINE D/O (3) ACCESORY DRIVE SECTION The accessory drive section transmits mechanical power from the HP rotor to the accessory units installed on the external gearbox. The drive section is equipped with the following assemblies: \- an internal gearbox, \- an intermediate gearbox, \- an external gearbox drive shaft, \- an external gearbox module. MECHANICAL & AVIONICS COURSE - T1+T2 (LVL 2&3) 70 - POWER PLANT (RR Trent 700) ENGINE D/O (3) Apr 16, 2013 Page 60 A330 RR Trent 700 TECHNICAL TRAINING MANUAL GCL13151 - GEHT0M0 - FM70D1000000071 B1/B2\_A330\_DIFF\_FR\_A320 REV. 1 DATE: 01.06.2019 DVIATION TRAINING SERVICES FOR TRAINING PURPOSES ONLY 60 ACCESORY DRIVE SECTION MECHANICAL & AVIONICS COURSE - T1+T2 (LVL 2&3) 70 - POWER PLANT (RR Trent 700) ENGINE D/O (3) Apr 16, 2013 Page 61 A330 RR Trent 700 TECHNICAL TRAINING MANUAL GCL13151 - GEHT0M0 - FM70D1000000071 B1/B2\_A330\_DIFF\_FR\_A320 REV. 1 DATE: 01.06.2019 DVIATION TRAINING SERVICES FOR TRAINING PURPOSES ONLY 61 ENGINE D/O (3) ACCESORY DRIVE SECTION (continued) EXTERNAL GEARBOX MODULE The external gearbox module is an aluminum alloy casting. It is installed below the LP compressor case. The gearbox transmits power from the engine to drive the accessories mounted on the gearbox front and rear faces. During starting, the gearbox also transmits power from the air starter motor to the engine. The components installed on the forward face are: \- pneumatic starter, \- EEC dedicated alternator, \- centrifugal breather assembly, \- hydraulic pump number 1. The components installed on the rear face are: \- Integrated Drive Generator (IDG), \- input drive bevel gears, \- oil pump, \- fuel pump, \- hydraulic pump number 2. NOTE: Note: for maintenance purposes, hand turning of the HP rotor system is achieved through the centrifugal breather assembly. MECHANICAL & AVIONICS COURSE - T1+T2 (LVL 2&3) 70 - POWER PLANT (RR Trent 700) ENGINE D/O (3) Apr 16, 2013 Page 62 A330 RR Trent 700 TECHNICAL TRAINING MANUAL GCL13151 - GEHT0M0 - FM70D1000000071 B1/B2\_A330\_DIFF\_FR\_A320 REV. 1 DATE: 01.06.2019 DVIATION TRAINING SERVICES FOR TRAINING PURPOSES ONLY 62 ACCESORY DRIVE SECTION - EXTERNAL GEARBOX MODULE MECHANICAL & AVIONICS COURSE - T1+T2 (LVL 2&3) 70 - POWER PLANT (RR Trent 700) ENGINE D/O (3) Apr 16, 2013 Page 63 A330 RR Trent 700 TECHNICAL TRAINING MANUAL GCL13151 - GEHT0M0 - FM70D1000000071 B1/B2\_A330\_DIFF\_FR\_A320 REV. 1 DATE: 01.06.2019 DVIATION TRAINING SERVICES FOR TRAINING PURPOSES ONLY 63 ENGINE D/O (3) DRAINS SYSTEM The drains system has the following functions: \- To remove and discard fuel and/or oil if a leak occurs from an internal seal in specified primary components. The drains system can be used to monitor the condition of these seals. \- To remove and discard all unwanted liquids collected in the pylon, cowls and fairings. \- To collect unburned fuel from the combustion chamber following an engine shut down or a start procedure not completed. Leaks from the accessories are drained overboard via a drains mast. The items that are connected to the drains mast are: \- the Air Oil Heat Exchanger (AOHE), \- the hydraulic pump number 1, \- the hydraulic pump number 2, \- the LP/HP fuel pumps, \- the Fuel Metering Unit (FMU), \- the pneumatic starter, \- the IDG, \- the VSV actuators, \- the drain collector tank, and \- the oil tank. NOTE: Note: the two VSV actuators, the AOHE and the FMU are connected to the same drain outlet at the drains mast, as well as the IDG and the starter. But the drain tube from each actuator, the AOHE and the IDG have a sump for better source leak detection. Other tubes in the drains system remove unwanted fluids from the pylon primary structure, from the area behind the core fairings and from the LP turbine area. MECHANICAL & AVIONICS COURSE - T1+T2 (LVL 2&3) 70 - POWER PLANT (RR Trent 700) ENGINE D/O (3) Apr 16, 2013 Page 64 A330 RR Trent 700 TECHNICAL TRAINING MANUAL GCL13151 - GEHT0M0 - FM70D1000000071 B1/B2\_A330\_DIFF\_FR\_A320 REV. 1 DATE: 01.06.2019 DVIATION TRAINING SERVICES FOR TRAINING PURPOSES ONLY 64 DRAINS SYSTEM MECHANICAL & AVIONICS COURSE - T1+T2 (LVL 2&3) 70 - POWER PLANT (RR Trent 700) ENGINE D/O (3) Apr 16, 2013 Page 65 A330 RR Trent 700 TECHNICAL TRAINING MANUAL GCL13151 - GEHT0M0 - FM70D1000000071 B1/B2\_A330\_DIFF\_FR\_A320 REV. 1 DATE: 01.06.2019 DVIATION TRAINING SERVICES FOR TRAINING PURPOSES ONLY 65 ENGINE D/O (3) DRAINS SYSTEM (continued) DRAINS MAST The drains mast has six outlets for the routing of drained fluids overboard and is installed on the forward face of the external gearbox module adjacent to the collector tank. The related components from each drain outlet are identified on the side of the drains mast. MECHANICAL & AVIONICS COURSE - T1+T2 (LVL 2&3) 70 - POWER PLANT (RR Trent 700) ENGINE D/O (3) Apr 16, 2013 Page 66 A330 RR Trent 700 TECHNICAL TRAINING MANUAL GCL13151 - GEHT0M0 - FM70D1000000071 B1/B2\_A330\_DIFF\_FR\_A320 REV. 1 DATE: 01.06.2019 DVIATION TRAINING SERVICES FOR TRAINING PURPOSES ONLY 66 DRAINS SYSTEM - DRAINS MAST MECHANICAL & AVIONICS COURSE - T1+T2 (LVL 2&3) 70 - POWER PLANT (RR Trent 700) ENGINE D/O (3) Apr 16, 2013 Page 67 A330 RR Trent 700 TECHNICAL TRAINING MANUAL GCL13151 - GEHT0M0 - FM70D1000000071 B1/B2\_A330\_DIFF\_FR\_A320 REV. 1 DATE: 01.06.2019 DVIATION TRAINING SERVICES FOR TRAINING PURPOSES ONLY 67 ENGINE D/O (3) DRAINS SYSTEM (continued) DRAINS COLLECTOR TANK The drain system has also a drains collector tank / ejector assembly which is installed on the forward face of the external gearbox module and connected to the drains mast too. The tank collects excessive and unused fuel that drains from the fuel manifold when the engine is shut-down or after an engine start abort. The ejector sends the fuel back to the LP fuel system during engine start. If the tank is full, the fuel is discarded overboard via the drains mast. MECHANICAL & AVIONICS COURSE - T1+T2 (LVL 2&3) 70 - POWER PLANT (RR Trent 700) ENGINE D/O (3) Apr 16, 2013 Page 68 A330 RR Trent 700 TECHNICAL TRAINING MANUAL GCL13151 - GEHT0M0 - FM70D1000000071 B1/B2\_A330\_DIFF\_FR\_A320 REV. 1 DATE: 01.06.2019 DVIATION TRAINING SERVICES FOR TRAINING PURPOSES ONLY 68 DRAINS SYSTEM - DRAINS COLLECTOR TANK MECHANICAL & AVIONICS COURSE - T1+T2 (LVL 2&3) 70 - POWER PLANT (RR Trent 700) ENGINE D/O (3) Apr 16, 2013 Page 69 A330 RR Trent 700 TECHNICAL TRAINING MANUAL GCL13151 - GEHT0M0 - FM70D1000000071 B1/B2\_A330\_DIFF\_FR\_A320 REV. 1 DATE: 01.06.2019 DVIATION TRAINING SERVICES FOR TRAINING PURPOSES ONLY 69 ENGINE D/O (3) AERODYNAMIC STATIONS Engine parameters are measured at various stations throughout the engine. The stations can be described as follows: \- 0 In front of intake lip (atmospheric), \- 20 Inlet to LP compressor (fan) (P20/T20), \- 24 Inlet to IP compressor, \- 25 Inlet to HP compressor (P25\*/T25), \- 30 Exit from HP compressor (P30/T30), \- 40 Exit from combustion chamber, \- 50 Exit from LP turbine (P50), \- 160 Fan stream (by-pass) (P160\*). The Exhaust Gas Temperature (EGT) is measured at the inlet to the LP turbine, which corresponds to station 49.5. Eleven thermocouples are installed approximately equally around the engine within the LP1 turbine nozzle guide vanes and transmits EGT signal to the EEC.. MECHANICAL & AVIONICS COURSE - T1+T2 (LVL 2&3) 70 - POWER PLANT (RR Trent 700) ENGINE D/O (3) Apr 16, 2013 Page 70 A330 RR Trent 700 TECHNICAL TRAINING MANUAL GCL13151 - GEHT0M0 - FM70D1000000071 B1/B2\_A330\_DIFF\_FR\_A320 REV. 1 DATE: 01.06.2019 DVIATION TRAINING SERVICES FOR TRAINING PURPOSES ONLY 70 AERODYNAMIC STATIONS MECHANICAL & AVIONICS COURSE - T1+T2 (LVL 2&3) 70 - POWER PLANT (RR Trent 700) ENGINE D/O (3) Apr 16, 2013 Page 71 A330 RR Trent 700 TECHNICAL TRAINING MANUAL GCL13151 - GEHT0M0 - FM70D1000000071 B1/B2\_A330\_DIFF\_FR\_A320 REV. 1 DATE: 01.06.2019 DVIATION TRAINING SERVICES FOR TRAINING PURPOSES ONLY 71 AERODYNAMIC STATIONS MECHANICAL & AVIONICS COURSE - T1+T2 (LVL 2&3) 70 - POWER PLANT (RR Trent 700) ENGINE D/O (3) Apr 16, 2013 Page 72 A330 RR Trent 700 TECHNICAL TRAINING MANUAL GCL13151 - GEHT0M0 - FM70D1000000071 B1/B2\_A330\_DIFF\_FR\_A320 REV. 1 DATE: 01.06.2019 DVIATION TRAINING SERVICES FOR TRAINING PURPOSES ONLY 72 AERODYNAMIC STATIONS MECHANICAL & AVIONICS COURSE - T1+T2 (LVL 2&3) 70 - POWER PLANT (RR Trent 700) ENGINE D/O (3) Apr 16, 2013 Page 73 A330 RR Trent 700 TECHNICAL TRAINING MANUAL GCL13151 - GEHT0M0 - FM70D1000000071 B1/B2\_A330\_DIFF\_FR\_A320 REV. 1 DATE: 01.06.2019 DVIATION TRAINING SERVICES FOR TRAINING PURPOSES ONLY 73 ENGINE D/O (3) BORESCOPE ACCESS PORTS It is possible to visually examine the engine at different positions by the use of borescope equipment. There are 4 borescope access ports on the IP compressor case. They are located on the right side with access via the right thrust reverser half and right bottom gas generator fairing. The HP compressor has 4 borescope access ports. They are located on the compressor case, on the lower right hand side, with access via the right thrust half reverser. There are 8 combustion chamber access ports located radially around the combustion outer case. Three of these access ports are occupied by T30 thermocouples. The 2 igniter ports could be used as borescope ports. There are 2 access ports to view the HP turbine. They are both located on the lower right hand side of the core, one on the HP turbine case, the other on the IP turbine case. There are 2 access ports to view the IP turbine located on the lower right hand side of the core. The one on the IP turbine case lets the IP turbine blade leading edge be seen. The front access port on the LP turbine lets the IP turbine trailing edge be seen. There are 4 access ports on the LP turbine case, lower right hand side to view the LP turbine assembly. MECHANICAL & AVIONICS COURSE - T1+T2 (LVL 2&3) 70 - POWER PLANT (RR Trent 700) ENGINE D/O (3) Apr 16, 2013 Page 74 A330 RR Trent 700 TECHNICAL TRAINING MANUAL GCL13151 - GEHT0M0 - FM70D1000000071 B1/B2\_A330\_DIFF\_FR\_A320 REV. 1 DATE: 01.06.2019 DVIATION TRAINING SERVICES FOR TRAINING PURPOSES ONLY 74 BORESCOPE ACCESS PORTS MECHANICAL & AVIONICS COURSE - T1+T2 (LVL 2&3) 70 - POWER PLANT (RR Trent 700) ENGINE D/O (3) Apr 16, 2013 Page 75 A330 RR Trent 700 TECHNICAL TRAINING MANUAL GCL13151 - GEHT0M0 - FM70D1000000071 B1/B2\_A330\_DIFF\_FR\_A320 REV. 1 DATE: 01.06.2019 DVIATION TRAINING SERVICES FOR TRAINING PURPOSES ONLY 75 ENGINE FUEL SYSTEM D/O (3) GENERAL The engine fuel system is designed to supply metered fuel to the combustion chamber according to the engine power demand. The fuel system is also used to cool the engine oil and supply servo pressure to operate valves and actuators. The Engine Electronic Controller (EEC) controls the operation of the engine fuel system. The EEC also monitors the system for normal operation and ECAM fuel flow indication. MECHANICAL & AVIONICS COURSE - T1+T2 (LVL 2&3) 70 - POWER PLANT (RR Trent 700) ENGINE FUEL SYSTEM D/O (3) Apr 16, 2013 Page 76 A330 RR Trent 700 TECHNICAL TRAINING MANUAL GCL13151 - GEHT0M0 - FM70D3000000071 B1/B2\_A330\_DIFF\_FR\_A320 REV. 1 DATE: 01.06.2019 DVIATION TRAINING SERVICES FOR TRAINING PURPOSES ONLY 76 GENERAL MECHANICAL & AVIONICS COURSE - T1+T2 (LVL 2&3) 70 - POWER PLANT (RR Trent 700) ENGINE FUEL SYSTEM D/O (3) Apr 16, 2013 Page 77 A330 RR Trent 700 TECHNICAL TRAINING MANUAL GCL13151 - GEHT0M0 - FM70D3000000071 B1/B2\_A330\_DIFF\_FR\_A320 REV. 1 DATE: 01.06.2019 DVIATION TRAINING SERVICES FOR TRAINING PURPOSES ONLY 77 ENGINE FUEL SYSTEM D/O (3) GENERAL (continued) LOW PRESSURE FUEL The low pressure (LP) valve controls the fuel supply from the aircraft tanks to the engine fuel pump. The engine fuel pump includes an LP pump and an HP pump. Fuel from the tanks is initially supplied to the LP pump. From the LP fuel pump fuel is supplied to the Fuel Oil Heat Exchanger (FOHE) for fuel heating and oil cooling. Then the fuel goes through the LP fuel filter. HIGH PRESSURE FUEL The filtered LP fuel is returned to the high-pressure (HP) fuel pump. The HP fuel pump pressurizes the fuel and supplies the Fuel Metering Unit (FMU), the Variable Stator Vane (VSV) actuators and the Air Oil Heat Exchanger (AOHX) modulating valve. The FMU, which contains servo valves, is mounted below the fuel pump assembly. A metering valve in the FMU adjusts the fuel flow delivered to the combustion chamber. This fuel flow, from the FMU, successively goes through the fuel flow transmitter and the HP fuel filter before supplying the fuel manifolds and Fuel Spray Nozzles (FSNs). A Pressure Raising and Shut-Off Valve (PRSOV), installed inside the FMU downstream of the metering valve, starts or stops the fuel flow and keeps the fuel at a satisfactory pressure. An overspeed valve in the FMU can close the PRSOV in case of N1, N2 or LP turbine overspeed. CONTROL Before engine start, the MASTER switch is OFF, the LP valve and the PRSOV are closed. When the MASTER switch is set to ON, the LP valve opens and the EEC controls the PRSOV to open by. The EEC controls the fuel flow through the metering valve in response to the throttle control lever demand or to the auto thrust system command. Engine normal shut down is done by setting the MASTER switch on OFF which closes the LP valve and the PRSOV directly. The EEC can also close the PRSOV automatically in case of automatic start abort on ground. MONITORING For fuel system monitoring and ECAM indication, the EEC uses the following sensors: \- the fuel flow transmitter for fuel flow and fuel used indications, \- the LP fuel filter differential pressure switch for filter clogging indication, \- the fuel low pressure switch for fuel pressure monitoring. To monitor the metering valve and the PRSOV positions, the EEC uses sensors inside the FMU. MECHANICAL & AVIONICS COURSE - T1+T2 (LVL 2&3) 70 - POWER PLANT (RR Trent 700) ENGINE FUEL SYSTEM D/O (3) Apr 16, 2013 Page 78 A330 RR Trent 700 TECHNICAL TRAINING MANUAL GCL13151 - GEHT0M0 - FM70D3000000071 B1/B2\_A330\_DIFF\_FR\_A320 REV. 1 DATE: 01.06.2019 DVIATION TRAINING SERVICES FOR TRAINING PURPOSES ONLY 78 GENERAL - LOW PRESSURE FUEL \... MONITORING MECHANICAL & AVIONICS COURSE - T1+T2 (LVL 2&3) 70 - POWER PLANT (RR Trent 700) ENGINE FUEL SYSTEM D/O (3) Apr 16, 2013 Page 79 A330 RR Trent 700 TECHNICAL TRAINING MANUAL GCL13151 - GEHT0M0 - FM70D3000000071 B1/B2\_A330\_DIFF\_FR\_A320 REV. 1 DATE: 01.06.2019 DVIATION TRAINING SERVICES FOR TRAINING PURPOSES ONLY 79 ENGINE FUEL SYSTEM D/O (3) SYSTEM DESCRIPTION - FUEL PUMP ASSEMBLY The engine fuel pump assembly is driven from the external gearbox and is mounted on the gearbox rear face at the RH side. This assembly includes a LP pump, an HP pump and an HP pump relief valve. MECHANICAL & AVIONICS COURSE - T1+T2 (LVL 2&3) 70 - POWER PLANT (RR Trent 700) ENGINE FUEL SYSTEM D/O (3) Apr 16, 2013 Page 80 A330 RR Trent 700 TECHNICAL TRAINING MANUAL GCL13151 - GEHT0M0 - FM70D3000000071 B1/B2\_A330\_DIFF\_FR\_A320 REV. 1 DATE: 01.06.2019 DVIATION TRAINING SERVICES FOR TRAINING PURPOSES ONLY 80 SYSTEM DESCRIPTION - FUEL PUMP ASSEMBLY MECHANICAL & AVIONICS COURSE - T1+T2 (LVL 2&3) 70 - POWER PLANT (RR Trent 700) ENGINE FUEL SYSTEM D/O (3) Apr 16, 2013 Page 81 A330 RR Trent 700 TECHNICAL TRAINING MANUAL GCL13151 - GEHT0M0 - FM70D3000000071 B1/B2\_A330\_DIFF\_FR\_A320 REV. 1 DATE: 01.06.2019 DVIATION TRAINING SERVICES FOR TRAINING PURPOSES ONLY 81 ENGINE FUEL SYSTEM D/O (3) SYSTEM DESCRIPTION - LOW PRESSURE FUEL FLOW LP PUMP The LP pump has a single-stage centrifugal impeller with an axial inducer. The fuel from the tanks is delivered to the LP pump under aircraft boost pump pressure and the LP pump increases that pressure before supplying fuel to the HP pump. The LP pump behaves as a suction pump in case of a \"gravity feed\" situation (boost pumps failed). FOHE The Fuel Oil Heat Exchanger (FOHE) and the LP fuel filter are included in the same assembly and are installed on the RH side of the LP compressor case. The FOHE is installed in the upper part of the assembly. Its function is to both reduce the engine oil temperature and to prevent the icing of the moisture in the fuel. The fuel enters the FOHE at the upper part, flows through the inner core via a cluster of tubes, then directly supplies the LP fuel filter. The engine oil flows through the inner core via a stack of baffle plates. LP FUEL FILTER The LP fuel filter is installed in the lower part of the assembly. It is the primary filter in the distribution system. The filter element is disposable. A fuel drain plug is installed in the cap so that the case can be drained of fuel when the access to the filter is necessary. The LP fuel filter includes a fuel by-pass valve, a differential pressure ( P) switch and a fuel LP switch installed downstream of the filter. MECHANICAL & AVIONICS COURSE - T1+T2 (LVL 2&3) 70 - POWER PLANT (RR Trent 700) ENGINE FUEL SYSTEM D/O (3) Apr 16, 2013 Page 82 A330 RR Trent 700 TECHNICAL TRAINING MANUAL GCL13151 - GEHT0M0 - FM70D3000000071 B1/B2\_A330\_DIFF\_FR\_A320 REV. 1 DATE: 01.06.2019 DVIATION TRAINING SERVICES FOR TRAINING PURPOSES ONLY 82 SYSTEM DESCRIPTION - LOW PRESSURE FUEL FLOW - LP PUMP \... LP FUEL FILTER MECHANICAL & AVIONICS COURSE - T1+T2 (LVL 2&3) 70 - POWER PLANT (RR Trent 700) ENGINE FUEL SYSTEM D/O (3) Apr 16, 2013 Page 83 A330 RR Trent 700 TECHNICAL TRAINING MANUAL GCL13151 - GEHT0M0 - FM70D3000000071 B1/B2\_A330\_DIFF\_FR\_A320 REV. 1 DATE: 01.06.2019 DVIATION TRAINING SERVICES FOR TRAINING PURPOSES ONLY 83 ENGINE FUEL SYSTEM D/O (3) SYSTEM DESCRIPTION - HIGH PRESSURE FUEL HP PUMP The HP pump is a gear-type pump and is protected against overpressure by a relief valve. The fuel from the FOHE and the LP fuel filter, is supplied to the HP pump. The HP pump supplies the FMU with high-pressure fuel. The HP pump also re-circulates the excess spill flow from the metering valve. FUEL METERING UNIT - FMU The FMU is attached to the lower surface of the fuel pump assembly and has two internal fuel connections, one for the HP supply and the other for fuel spill. The main function of the FMU is to supply metered fuel to the nozzles for combustion. The FMU is the Line Replaceable Unit but it contains several different components. The FMU contains these components: \- the metering valve Torque Motor (TM), \- the fuel shut-off TM, \- the overspeed TM, \- the servo pressure regulator, \- fuel metering valve, \- PRSOV, \- the spill valve, \- the dump valve, \- the overspeed valve, \- PRSOV position microswitches, \- a metering valve position Linear Variable Differential Transducer (LVDT) sensor. The servo pressure regulator keeps the servo fuel pressure to the metering valve at a constant value more than LP return pressure. This is necessary for accurate control of the metering valve. The metering valve controls the rate of Fuel Flow (FF) for all operating conditions. The metering valve is hydraulically actuated and controlled by the metering valve TM. Metering valve position feedback for the control loop is sent to both channels of the EEC by a position resolver. The pressure drop and spill valve keeps a constant pressure difference across the metering valve. So it \'spills\' excess HP supply to the inlet of the HP fuel pump. PRSOV is downstream of the metering valve. The PRSOV is downstream of the metering valve. It keeps the metered fuel at a suitable pressure for operation, stops the fuel flow for engine shutdown and operates the dump valve. The PRSOV is opened by fuel pressure from the metering valve when the shut-off TM is de-energized. The ENGINE MASTER switch controls the shut-off TM. The shut-off TM is energized when the Master Switch is selected OFF. In case of automatic start abort on the ground, the EEC may also energize the shut-off TM. The dump valve lets most of the fuel in the fuel manifold drain into the drain collector tank at engine shutdown. It is closed during engine operation and opens as the PRSOV closes. The Overspeed Protection Unit (OPU) protects against N1 or N2 overspeed. If an overspeed condition is sensed, the OPU sends a signal to energize the overspeed TM. The overspeed valve then causes the PRSOV to close and shut down the engine. MECHANICAL & AVIONICS COURSE - T1+T2 (LVL 2&3) 70 - POWER PLANT (RR Trent 700) ENGINE FUEL SYSTEM D/O (3) Apr 16, 2013 Page 84 A330 RR Trent 700 TECHNICAL TRAINING MANUAL GCL13151 - GEHT0M0 - FM70D3000000071 B1/B2\_A330\_DIFF\_FR\_A320 REV. 1 DATE: 01.06.2019 DVIATION TRAINING SERVICES FOR TRAINING PURPOSES ONLY 84 SYSTEM DESCRIPTION - HIGH PRESSURE FUEL - HP PUMP & FUEL METERING UNIT - FMU MECHANICAL & AVIONICS COURSE - T1+T2 (LVL 2&3) 70 - POWER PLANT (RR Trent 700) ENGINE FUEL SYSTEM D/O (3) Apr 16, 2013 Page 85 A330 RR Trent 700 TECHNICAL TRAINING MANUAL GCL13151 - GEHT0M0 - FM70D3000000071 B1/B2\_A330\_DIFF\_FR\_A320 REV. 1 DATE: 01.06.2019 DVIATION TRAINING SERVICES FOR TRAINING PURPOSES ONLY 85 ENGINE FUEL SYSTEM D/O (3) SYSTEM DESCRIPTION - METERED FUEL FLOW After the FMU, the metered fuel flows through the fuel flow transmitter (FF XMTR) and the HP fuel is filtered before supplying the fuel manifold and 24 fuel spray nozzles. FUEL FLOW TRANSMITTER The fuel flow transmitter (FF XMTR) is installed on the rear LP compressor case at the bottom. It supplies electrical signals to the EEC, which are in proportion to the FF supplied to the combustion system. The EEC uses these signals to compute the fuel flow and the fuel used. The FF is shown on the EWD and the fuel used on the SD ENGINE and CRUISE pages. MECHANICAL & AVIONICS COURSE - T1+T2 (LVL 2&3) 70 - POWER PLANT (RR Trent 700) ENGINE FUEL SYSTEM D/O (3) Apr 16, 2013 Page 86 A330 RR Trent 700 TECHNICAL TRAINING MANUAL GCL13151 - GEHT0M0 - FM70D3000000071 B1/B2\_A330\_DIFF\_FR\_A320 REV. 1 DATE: 01.06.2019 DVIATION TRAINING SERVICES FOR TRAINING PURPOSES ONLY 86 SYSTEM DESCRIPTION - METERED FUEL FLOW - FUEL FLOW TRANSMITTER MECHANICAL & AVIONICS COURSE - T1+T2 (LVL 2&3) 70 - POWER PLANT (RR Trent 700) ENGINE FUEL SYSTEM D/O (3) Apr 16, 2013 Page 87 A330 RR Trent 700 TECHNICAL TRAINING MANUAL GCL13151 - GEHT0M0 - FM70D3000000071 B1/B2\_A330\_DIFF\_FR\_A320 REV. 1 DATE: 01.06.2019 DVIATION TRAINING SERVICES FOR TRAINING PURPOSES ONLY 87 ENGINE FUEL SYSTEM D/O (3) SYSTEM DESCRIPTION - METERED FUEL FLOW (continued) HP FUEL FILTER The HP fuel filter element can be cleaned of contamination and, if serviceable, can be used again. MECHANICAL & AVIONICS COURSE - T1+T2 (LVL 2&3) 70 - POWER PLANT (RR Trent 700) ENGINE FUEL SYSTEM D/O (3) Apr 16, 2013 Page 88 A330 RR Trent 700 TECHNICAL TRAINING MANUAL GCL13151 - GEHT0M0 - FM70D3000000071 B1/B2\_A330\_DIFF\_FR\_A320 REV. 1 DATE: 01.06.2019 DVIATION TRAINING SERVICES FOR TRAINING PURPOSES ONLY 88 SYSTEM DESCRIPTION - METERED FUEL FLOW - HP FUEL FILTER MECHANICAL & AVIONICS COURSE - T1+T2 (LVL 2&3) 70 - POWER PLANT (RR Trent 700) ENGINE FUEL SYSTEM D/O (3) Apr 16, 2013 Page 89 A330 RR Trent 700 TECHNICAL TRAINING MANUAL GCL13151 - GEHT0M0 - FM70D3000000071 B1/B2\_A330\_DIFF\_FR\_A320 REV. 1 DATE: 01.06.2019 DVIATION TRAINING SERVICES FOR TRAINING PURPOSES ONLY 89 ENGINE FUEL SYSTEM D/O (3) SYSTEM DESCRIPTION - METERED FUEL FLOW (continued) FUEL MANIFOLD The fuel manifold assembly equally supplies all 24 fuel spray nozzles. The manifold is split into 2 halves, each feeding 6 supply tubes. The 2 halves can be disconnected near the top and the bottom of the engine. Each supply tube is connected to an adjacent pair of fuel spray nozzles. MECHANICAL & AVIONICS COURSE - T1+T2 (LVL 2&3) 70 - POWER PLANT (RR Trent 700) ENGINE FUEL SYSTEM D/O (3) Apr 16, 2013 Page 90 A330 RR Trent 700 TECHNICAL TRAINING MANUAL GCL13151 - GEHT0M0 - FM70D3000000071 B1/B2\_A330\_DIFF\_FR\_A320 REV. 1 DATE: 01.06.2019 DVIATION TRAINING SERVICES FOR TRAINING PURPOSES ONLY 90 SYSTEM DESCRIPTION - METERED FUEL FLOW - FUEL MANIFOLD MECHANICAL & AVIONICS COURSE - T1+T2 (LVL 2&3) 70 - POWER PLANT (RR Trent 700) ENGINE FUEL SYSTEM D/O (3) Apr 16, 2013 Page 91 A330 RR Trent 700 TECHNICAL TRAINING MANUAL GCL13151 - GEHT0M0 - FM70D3000000071 B1/B2\_A330\_DIFF\_FR\_A320 REV. 1 DATE: 01.06.2019 DVIATION TRAINING SERVICES FOR TRAINING PURPOSES ONLY 91 ENGINE FUEL SYSTEM D/O (3) SYSTEM DESCRIPTION - METERED FUEL FLOW (continued) FUEL SPRAY NOZZLES The 24 fuel spray nozzles are installed at equal distance around the combustion outer case. There are 12 LH and 12 RH nozzles grouped in adjacent pairs to suit the supply tubes. The fuel flows into the inlet of the distributor weight assemblies. When there is sufficient fuel pressure at a nozzle, the weight in the assembly is pushed away from the inlet. Fuel then flows through the feed arm and rearward along a cavity in the nozzle head. At the end of the cavity, there are small holes, which supply the fuel in a circular direction across the swirl chamber outlet. Air at HP compressor outlet pressure (P30) flows into the swirl chamber in the nozzle head. The inner swirl vanes change the straight air flow into a circular air flow. This circular air flow is in the opposite direction to the circular fuel flow across the swirl chamber outlet, and helps to mix the fuel with the air satisfactorily. Air at P30 pressure also flows along the outer surface of the nozzle head, through the outer swirl vanes and into the combustion chamber. The outer swirl vanes change this straight air flow into a circular air flow. This circular air flow then mixes with the fuel/air mixture at the outlet of the swirl chamber to make a satisfactory spray. MECHANICAL & AVIONICS COURSE - T1+T2 (LVL 2&3) 70 - POWER PLANT (RR Trent 700) ENGINE FUEL SYSTEM D/O (3) Apr 16, 2013 Page 92 A330 RR Trent 700 TECHNICAL TRAINING MANUAL GCL13151 - GEHT0M0 - FM70D3000000071 B1/B2\_A330\_DIFF\_FR\_A320 REV. 1 DATE: 01.06.2019 DVIATION TRAINING SERVICES FOR TRAINING PURPOSES ONLY 92 SYSTEM DESCRIPTION - METERED FUEL FLOW - FUEL SPRAY NOZZLES MECHANICAL & AVIONICS COURSE - T1+T2 (LVL 2&3) 70 - POWER PLANT (RR Trent 700) ENGINE FUEL SYSTEM D/O (3) Apr 16, 2013 Page 93 A330 RR Trent 700 TECHNICAL TRAINING MANUAL GCL13151 - GEHT0M0 - FM70D3000000071 B1/B2\_A330\_DIFF\_FR\_A320 REV. 1 DATE: 01.06.2019 DVIATION TRAINING SERVICES FOR TRAINING PURPOSES ONLY 93 SYSTEM DESCRIPTION - METERED FUEL FLOW - FUEL SPRAY NOZZLES MECHANICAL & AVIONICS COURSE - T1+T2 (LVL 2&3) 70 - POWER PLANT (RR Trent 700) ENGINE FUEL SYSTEM D/O (3) Apr 16, 2013 Page 94 A330 RR Trent 700 TECHNICAL TRAINING MANUAL GCL13151 - GEHT0M0 - FM70D3000000071 B1/B2\_A330\_DIFF\_FR\_A320 REV. 1 DATE: 01.06.2019 DVIATION TRAINING SERVICES FOR TRAINING PURPOSES ONLY 94 This Page Intentionally Left Blank MECHANICAL & AVIONICS COURSE - T1+T2 (LVL 2&3) 70 - POWER PLANT (RR Trent 700) ENGINE FUEL SYSTEM D/O (3) Apr 16, 2013 Page 95 A330 RR Trent 700 TECHNICAL TRAINING MANUAL GCL13151 - GEHT0M0 - FM70D3000000071 B1/B2\_A330\_DIFF\_FR\_A320 REV. 1 DATE: 01.06.2019 DVIATION TRAINING SERVICES FOR TRAINING PURPOSES ONLY 95 ENGINE FUEL SYSTEM D/O (3) SYSTEM DESCRIPTION - METERED FUEL FLOW (continued) DRAIN TANK When the engine is shut down or after a failure to start, the fuel is drained from the manifold to the drain tank via the dump valve in the FMU. If, after a number of failed starts, the drain tank becomes full, the excess fuel is discharged through the drain mast. At engine start the LP fuel flows through the drain tank ejector pump, this causes a suction, which opens the non-return valve and drains the fuel from the drain tank. It then becomes part of the supply to the LP pump inlet. MECHANICAL & AVIONICS COURSE - T1+T2 (LVL 2&3) 70 - POWER PLANT (RR Trent 700) ENGINE FUEL SYSTEM D/O (3) Apr 16, 2013 Page 96 A330 RR Trent 700 TECHNICAL TRAINING MANUAL GCL13151 - GEHT0M0 - FM70D3000000071 B1/B2\_A330\_DIFF\_FR\_A320 REV. 1 DATE: 01.06.2019 DVIATION TRAINING SERVICES FOR TRAINING PURPOSES ONLY 96 SYSTEM DESCRIPTION - METERED FUEL FLOW - DRAIN TANK MECHANICAL & AVIONICS COURSE - T1+T2 (LVL 2&3) 70 - POWER PLANT (RR Trent 700) ENGINE FUEL SYSTEM D/O (3) Apr 16, 2013 Page 97 A330 RR Trent 700 TECHNICAL TRAINING MANUAL GCL13151 - GEHT0M0 - FM70D3000000071 B1/B2\_A330\_DIFF\_FR\_A320 REV. 1 DATE: 01.06.2019 DVIATION TRAINING SERVICES FOR TRAINING PURPOSES ONLY 97 ENGINE FUEL SYSTEM D/O (3) GENERAL OPERATION STARTING AND THRUST CONTROL During engine start, when the ENGine MASTER switch is selected ON, the LP fuel valve is commanded open via the master switch slave relay. At this time, the springs and shut-off valve servo pressure keep the PRSOV closed. The EEC manages the engine thrust by controlling the metering valve position via the electrical current supplied to the metering valve TM. The metering valve position is a function of the throttle control lever position or Throttle Resolver Angle (TRA) in manual thrust or a thrust command from the Autothrust System in automatic thrust control. The thrust command signal is routed through the Engine Interface and Vibration Monitoring Unit (EIVMU). As the metering valve opens, the metered fuel pressure increases and becomes greater than the PRSOV spring tension and opens the valve. Metered fuel is then supplied to the fuel spray nozzles through the fuel flow transmitter and the HP fuel filter. Two microswitches give the position of the PRSOV to the EEC. MECHANICAL & AVIONICS COURSE - T1+T2 (LVL 2&3) 70 - POWER PLANT (RR Trent 700) ENGINE FUEL SYSTEM D/O (3) Apr 16, 2013 Page 98 A330 RR Trent 700 TECHNICAL TRAINING MANUAL GCL13151 - GEHT0M0 - FM70D3000000071 B1/B2\_A330\_DIFF\_FR\_A320 REV. 1 DATE: 01.06.2019 DVIATION TRAINING SERVICES FOR TRAINING PURPOSES ONLY 98 GENERAL OPERATION - STARTING AND THRUST CONTROL MECHANICAL & AVIONICS COURSE - T1+T2 (LVL 2&3) 70 - POWER PLANT (RR Trent 700) ENGINE FUEL SYSTEM D/O (3) Apr 16, 2013 Page 99 A330 RR Trent 700 TECHNICAL TRAINING MANUAL GCL13151 - GEHT0M0 - FM70D3000000071 B1/B2\_A330\_DIFF\_FR\_A320 REV. 1 DATE: 01.06.2019 DVIATION TRAINING SERVICES FOR TRAINING PURPOSES ONLY 99 GENERAL OPERATION - STARTING AND THRUST CONTROL MECHANICAL & AVIONICS COURSE - T1+T2 (LVL 2&3) 70 - POWER PLANT (RR Trent 700) ENGINE FUEL SYSTEM D/O (3) Apr 16, 2013 Page 100 A330 RR Trent 700 TECHNICAL TRAINING MANUAL GCL13151 - GEHT0M0 - FM70D3000000071 B1/B2\_A330\_DIFF\_FR\_A320 REV. 1 DATE: 01.06.2019 DVIATION TRAINING SERVICES FOR TRAINING PURPOSES ONLY 100 GENERAL OPERATION - STARTING AND THRUST CONTROL MECHANICAL & AVIONICS COURSE - T1+T2 (LVL 2&3) 70 - POWER PLANT (RR Trent 700) ENGINE FUEL SYSTEM D/O (3) Apr 16, 2013 Page 101 A330 RR Trent 700 TECHNICAL TRAINING MANUAL GCL13151 - GEHT0M0 - FM70D3000000071 B1/B2\_A330\_DIFF\_FR\_A320 REV. 1 DATE: 01.06.2019 DVIATION TRAINING SERVICES FOR TRAINING PURPOSES ONLY 101 ENGINE FUEL SYSTEM D/O (3) GENERAL OPERATION (continued) SHUTDOWN During a normal engine shut down, when the ENGine MASTER switch is selected OFF, the fuel shut-off TM is directly controlled to close the PRSOV. This command overrides any EEC command to make sure that the operator always has the option to shut down the engine for any reason. The LP fuel valve also closes when the Master switch is selected OFF. The shut-off servo pressure helped by the spring force, hydraulically closes the PRSOV. When the PRSOV closes, the dump valve opens and the fuel is drained to the drain tank. The ENGine FIRE P/B also controls the LP fuel valve to the closed position in order to isolate the engine from the fuel tanks. The EEC receives a closed position signal from the PRSOV microswitches. MECHANICAL & AVIONICS COURSE - T1+T2 (LVL 2&3) 70 - POWER PLANT (RR Trent 700) ENGINE FUEL SYSTEM D/O (3) Apr 16, 2013 Page 102 A330 RR Trent 700 TECHNICAL TRAINING MANUAL GCL13151 - GEHT0M0 - FM70D3000000071 B1/B2\_A330\_DIFF\_FR\_A320 REV. 1 DATE: 01.06.2019 DVIATION TRAINING SERVICES FOR TRAINING PURPOSES ONLY 102 GENERAL OPERATION - SHUTDOWN MECHANICAL & AVIONICS COURSE - T1+T2 (LVL 2&3) 70 - POWER PLANT (RR Trent 700) ENGINE FUEL SYSTEM D/O (3) Apr 16, 2013 Page 103 A330 RR Trent 700 TECHNICAL TRAINING MANUAL GCL13151 - GEHT0M0 - FM70D3000000071 B1/B2\_A330\_DIFF\_FR\_A320 REV. 1 DATE: 01.06.2019 DVIATION TRAINING SERVICES FOR TRAINING PURPOSES ONLY 103 ENGINE FUEL SYSTEM D/O (3) GENERAL OPERATION (continued) MONITORING Impending fuel filter clogging is detected by the fuel filter differential pressure switch ( P), which sends a signal to the EEC. In the cockpit, an ECAM warning \"ENG FUEL FILTER CLOG\" is shown on the EWD and an amber \"CLOG\" indication appears close to the FUEL USED indication on the SD ENGINE page. A fuel low-pressure switch monitors the fuel pressure downstream of the LP fuel filter. The switch detects low fuel pressure and sends a signal to the EEC that will trigger the linked class 2 fault message. MECHANICAL & AVIONICS COURSE - T1+T2 (LVL 2&3) 70 - POWER PLANT (RR Trent 700) ENGINE FUEL SYSTEM D/O (3) Apr 16, 2013 Page 104 A330 RR Trent 700 TECHNICAL TRAINING MANUAL GCL13151 - GEHT0M0 - FM70D3000000071 B1/B2\_A330\_DIFF\_FR\_A320 REV. 1 DATE: 01.06.2019 DVIATION TRAINING SERVICES FOR TRAINING PURPOSES ONLY 104 GENERAL OPERATION - MONITORING MECHANICAL & AVIONICS COURSE - T1+T2 (LVL 2&3) 70 - POWER PLANT (RR Trent 700) ENGINE FUEL SYSTEM D/O (3) Apr 16, 2013 Page 105 A330 RR Trent 700 TECHNICAL TRAINING MANUAL GCL13151 - GEHT0M0 - FM70D3000000071 B1/B2\_A330\_DIFF\_FR\_A320 REV. 1 DATE: 01.06.2019 DVIATION TRAINING SERVICES FOR TRAINING PURPOSES ONLY 105 ENGINE LIMIT PROTECTION D/O (3) GENERAL Based on engine parameters, the Engine Electronic Controller (EEC) ensures limit protection for: \- N1, N2 and N3 shaft speeds. MECHANICAL & AVIONICS COURSE - T1+T2 (LVL 2&3) 70 - POWER PLANT (RR Trent 700) ENGINE LIMIT PROTECTION D/O (3) Apr 16, 2013 Page 106 A330 RR Trent 700 TECHNICAL TRAINING MANUAL GCL13151 - GEHT0M0 - FM70DB000000071 B1/B2\_A330\_DIFF\_FR\_A320 REV. 1 DATE: 01.06.2019 DVIATION TRAINING SERVICES FOR TRAINING PURPOSES ONLY 106 GENERAL MECHANICAL & AVIONICS COURSE - T1+T2 (LVL 2&3) 70 - POWER PLANT (RR Trent 700) ENGINE LIMIT PROTECTION D/O (3) Apr 16, 2013 Page 107 A330 RR Trent 700 TECHNICAL TRAINING MANUAL GCL13151 - GEHT0M0 - FM70DB000000071 B1/B2\_A330\_DIFF\_FR\_A320 REV. 1 DATE: 01.06.2019 DVIATION TRAINING SERVICES FOR TRAINING PURPOSES ONLY 107 ENGINE LIMIT PROTECTION D/O (3) OVERSPEED PROTECTION SYSTEM If an overspeed occurs and the EEC cannot detect it, the Rotor Overspeed protection System (ROS) automatically stops the engine. The ROS is an independent system from the EEC. In the unlikely event of a LP turbine shaft breakage, the LP Turbine Overspeed protection System (LPTOS) is designed to automatically shut down the engine. The LPTOS is an independent system to EEC, even if physically located in EEC (channel A part). The IP turbine is protected against overspeed and overheat by monitoring of the turbine cooling air temperature. The Overspeed Protection System (OPS) protects the ROS and LPTOS. The ROS protection is done by the Overspeed Protection Unit (OPU), which also ensures the selection of the corresponding compressor speed probes. The LPTOS protection is done by a dedicated circuit board located in the EEC channel A part. SPEED PROBE INSTALLATION There are three measuring stations corresponding to the measurement of: \- the LP Compressor speed, or N1C, \- the IP Compressor speed, or N2, \- the LP Turbine speed, or N1T. The measuring stations dedicated to N1C and N2 are installed in the front bearing housing. The measuring station dedicated to N1T is installed in the tail bearing housing. Each measuring station is composed of a phonic wheel and three inductive speed probes. The LP compressor and IP compressor speed probes outputs (N1C and N2) are sent to the OPU. The LP turbine speed probes outputs are sent to the independent LPTOS circuit board of the EEC. COMPRESSOR SPEED PROBE SELECTION The OPU has two channels: \- a N1 function channel which receives inputs from three N1C speed probes, \- a N2 function channel which receives inputs from three N2 speed probes. Each OPU channel selects two valid signals out of the three signals received from N1C or N2 speed probes. The N1C and N2 speed signals are then sent to both EEC channels for N1 and N2 monitoring and indicating. The third speed signal is only selected, as a spare signal, if a fault is detected with one of the speed probe signals initially selected. The N1C signals are also used by the LPTOS circuit board of the EEC for turbine overspeed detection. ROTOR OVERSPEED DETECTION In each OPU channel, the N1C or N2 selected signals are used for overspeed detection logics. Each OPU channel changes its N1C or N2 analog signal inputs to digital signals. These signals are then monitored by the overspeed detection logic circuit. In case of N1 or N2 severe overspeed detection, the corresponding OPU channel sends an electrical signal to the Overspeed Valve Torque Motor (TM) in the Fuel Metering Unit (FMU). The Overspeed Valve then closes the Pressure Raising and Shut Off Valve (PRSOV) to cut off the fuel supply from the FMU and thus to shut down the engine, independently of the normal shutdown control. LP TURBINE OVERSPEED DETECTION The independent LPTOS circuit board is installed in EEC channel A part. This circuit board has two overspeed logic circuits for LP turbine overspeed detection. MECHANICAL & AVIONICS COURSE - T1+T2 (LVL 2&3) 70 - POWER PLANT (RR Trent 700) ENGINE LIMIT PROTECTION D/O (3) Apr 16, 2013 Page 108 A330 RR Trent 700 TECHNICAL TRAINING MANUAL GCL13151 - GEHT0M0 - FM70DB000000071 B1/B2\_A330\_DIFF\_FR\_A320 REV. 1 DATE: 01.06.2019 DVIATION TRAINING SERVICES FOR TRAINING PURPOSES ONLY 108 The LPTOS circuit board receives the N1C signals from the OPU. One N1C signal is supplied to each logic circuit of the LPTOS. Three N1T signals are sent to the LPTOS circuit board directly from the corresponding speed probes. Each logic circuit of the LPTOS is supplied with one N1T signal. The third signal is only selected, as a spare signal, if a fault is detected with one of the speed probe signals initially selected. Each logic circuit continuously compares its LP turbine speed input with its LP compressor speed input. If the two logic circuits detect a specified speed difference between the LP turbine and LP compressor (in a specified time limit), a LP shaft breakage is diagnosed. In that case, the system immediately sends an electrical signal to the Overspeed Valve TM in the FMU. The Overspeed Valve then closes the PRSOV to cut off the fuel supply from the FMU and thus to shut down the engine, independently of the normal shutdown control. If one logic circuit (A or B) becomes defective, the LPTOS circuits are disarmed to prevent any incorrect operation of the system. OVERSPEED SYSTEM AUTO TEST The EEC does an automatic test of the LPTOS protection during every ground engine start (before light up). Test signal is cancelled almost immediately in order not to impact the starting sequence. The EEC receives PRSOV closure feedback from its two position switches. MECHANICAL & AVIONICS COURSE - T1+T2 (LVL 2&3) 70 - POWER PLANT (RR Trent 700) ENGINE LIMIT PROTECTION D/O (3) Apr 16, 2013 Page 109 A330 RR Trent 700 TECHNICAL TRAINING MANUAL GCL13151 - GEHT0M0 - FM70DB000000071 B1/B2\_A330\_DIFF\_FR\_A320 REV. 1 DATE: 01.06.2019 DVIATION TRAINING SERVICES FOR TRAINING PURPOSES ONLY 109 OVERSPEED PROTECTION SYSTEM - SPEED PROBE INSTALLATION \... OVERSPEED SYSTEM AUTO TEST MECHANICAL & AVIONICS COURSE - T1+T2 (LVL 2&3) 70 - POWER PLANT (RR Trent 700) ENGINE LIMIT PROTECTION D/O (3) Apr 16, 2013 Page 110 A330 RR Trent 700 TECHNICAL TRAINING MANUAL GCL13151 - GEHT0M0 - FM70DB000000071 B1/B2\_A330\_DIFF\_FR\_A320 REV. 1 DATE: 01.06.2019 DVIATION TRAINING SERVICES FOR TRAINING PURPOSES ONLY 110 This Page Intentionally Left Blank MECHANICAL & AVIONICS COURSE - T1+T2 (LVL 2&3) 70 - POWER PLANT (RR Trent 700) ENGINE LIMIT PROTECTION D/O (3) Apr 16, 2013 Page 111 A330 RR Trent 700 TECHNICAL TRAINING MANUAL GCL13151 - GEHT0M0 - FM70DB000000071 B1/B2\_A330\_DIFF\_FR\_A320 REV. 1 DATE: 01.06.2019 DVIATION TRAINING SERVICES FOR TRAINING PURPOSES ONLY 111 ENGINE LIMIT PROTECTION D/O (3) TURBINE OVERSPEED & OVERHEAT DETECTION SYSTEM The turbine overspeed & overheat detection system measures the temperature of the IP turbine disk cooling air, at both sides of the turbine disk. If the temperature at the front or the rear of the IP turbine rises above the specified limit, the EEC will reduce the engine thrust and trigger corresponding warning. DESCRIPTION The turbine overheat detection system includes 2 detector assemblies of the dual thermocouple type attached to the High Pressure (HP)/IP turbine case. There is one detector assembly located at the front of the IP turbine disk and one at the rear. The rear turbine overheat detector is installed through one of the LP stage 1 (LP1) nozzle guide vanes, the front turbine overheat detector is installed through one of the IP turbine nozzle guide vanes. Each detector assembly has two thermocouple elements: one sends a signal to channel A of the EEC, the other sends a signal to channel B. The voltage of each signal is proportional to the temperature sensed by its related thermocouple. OPERATION An overspeed and/or overheat condition is detected, if: \- both thermocouple elements in the same detector sense the overheat limit. \- one element senses an overheat limit and the other element in the same detector is faulty. If the temperature of the IP turbine disk cooling air reaches a specified limit, first the EEC automatically limits the engine thrust up to 55% of the maximum available thrust, and triggers the \"ENG1(2) THRUST LIMITED\" level 2 warning. If the temperature is still above the specified limit despite the power reduction, after five seconds the EEC will trigger the \"EN1(2) TURBINE OVHT\" level 3 warning, requesting to manually set the affected engine at idle power. If the warning persists, the engine must be shut down. MECHANICAL & AVIONICS COURSE - T1+T2 (LVL 2&3) 70 - POWER PLANT (RR Trent 700) ENGINE LIMIT PROTECTION D/O (3) Apr 16, 2013 Page 112 A330 RR Trent 700 TECHNICAL TRAINING MANUAL GCL13151 - GEHT0M0 - FM70DB000000071 B1/B2\_A330\_DIFF\_FR\_A320 REV. 1 DATE: 01.06.2019 DVIATION TRAINING SERVICES FOR TRAINING PURPOSES ONLY 112 TURBINE OVERSPEED & OVERHEAT DETECTION SYSTEM - DESCRIPTION & OPERATION MECHANICAL & AVIONICS COURSE - T1+T2 (LVL 2&3) 70 - POWER PLANT (RR Trent 700) ENGINE LIMIT PROTECTION D/O (3) Apr 16, 2013 Page 113 A330 RR Trent 700 TECHNICAL TRAINING MANUAL GCL13151 - GEHT0M0 - FM70DB000000071 B1/B2\_A330\_DIFF\_FR\_A320 REV. 1 DATE: 01.06.2019 DVIATION TRAINING SERVICES FOR TRAINING PURPOSES ONLY 113 TURBINE OVERSPEED & OVERHEAT DETECTION SYSTEM - DESCRIPTION & OPERATION MECHANICAL & AVIONICS COURSE - T1+T2 (LVL 2&3) 70 - POWER PLANT (RR Trent 700) ENGINE LIMIT PROTECTION D/O (3) Apr 16, 2013 Page 114 A330 RR Trent 700 TECHNICAL TRAINING MANUAL GCL13151 - GEHT0M0 - FM70DB000000071 B1/B2\_A330\_DIFF\_FR\_A320 REV. 1 DATE: 01.06.2019 DVIATION TRAINING SERVICES FOR TRAINING PURPOSES ONLY 114 This Page Intentionally Left Blank MECHANICAL & AVIONICS COURSE - T1+T2 (LVL 2&3) 70 - POWER PLANT (RR Trent 700) ENGINE LIMIT PROTECTION D/O (3) Apr 16, 2013 Page 115 A330 RR Trent 700 TECHNICAL TRAINING MANUAL GCL13151 - GEHT0M0 - FM70DB000000071 B1/B2\_A330\_DIFF\_FR\_A320 REV. 1 DATE: 01.06.2019 DVIATION TRAINING SERVICES FOR TRAINING PURPOSES ONLY 115 FADEC PRINCIPLE (3) GENERAL The Full Authority Digital Engine Control (FADEC) controls and monitors the engine and engine subsystems. It includes the Engine Electronic Controller (EEC), which is a dual channel computer, a Power Control Unit (PCU), an Overspeed Protection Unit (OPU) and a set of peripherals (control components, sensors) directly connected to it. The EEC, PCU and OPU are installed into a ventilated electronic-unit-protection box located on the fan case LH side. The EEC controls the engine thrust based on manual or automatic thrust demands and uses information from A/C systems, some centralized by an interface computer called the Engine Interface and Vibration Monitoring Unit (EIVMU), to optimize engine operation. MECHANICAL & AVIONICS COURSE - T1+T2 (LVL 2&3) 70 - POWER PLANT (RR Trent 700) FADEC PRINCIPLE (3) Apr 16, 2013 Page 116 A330 RR Trent 700 TECHNICAL TRAINING MANUAL GCL13151 - GEHT0M0 - FM70DJ000000071 B1/B2\_A330\_DIFF\_FR\_A320 REV. 1 DATE: 01.06.2019 DVIATION TRAINING SERVICES FOR TRAINING PURPOSES ONLY 116 GENERAL MECHANICAL & AVIONICS COURSE - T1+T2 (LVL 2&3) 70 - POWER PLANT (RR Trent 700) FADEC PRINCIPLE (3) Apr 16, 2013 Page 117 A330 RR Trent 700 TECHNICAL TRAINING MANUAL GCL13151 - GEHT0M0 - FM70DJ000000071 B1/B2\_A330\_DIFF\_FR\_A320 REV. 1 DATE: 01.06.2019 DVIATION TRAINING SERVICES FOR TRAINING PURPOSES ONLY 117 FADEC PRINCIPLE (3) FADEC DESIGN - ARCHITECTURE The EEC is a digital unit made of two independent and similar channels of operation. The two channels are identified as channel A and channel B. Each channel communicates with the other one. All the hardware is mounted in the same housing. Each channel receives inputs from the aircraft and from engine subsystem sensors, probes and switches. The signals from these devices are known as feedback signals. They are generally duplicated for channel A and B and \"close the loop\" on the EEC control functions. Each EEC channel is able to control engine subsystem torque motors and solenoids. Each channel also sends outputs to the aircraft. MECHANICAL & AVIONICS COURSE - T1+T2 (LVL 2&3) 70 - POWER PLANT (RR Trent 700) FADEC PRINCIPLE (3) Apr 16, 2013 Page 118 A330 RR Trent 700 TECHNICAL TRAINING MANUAL GCL13151 - GEHT0M0 - FM70DJ000000071 B1/B2\_A330\_DIFF\_FR\_A320 REV. 1 DATE: 01.06.2019 DVIATION TRAINING SERVICES FOR TRAINING PURPOSES ONLY 118 FADEC DESIGN - ARCHITECTURE MECHANICAL & AVIONICS COURSE - T1+T2 (LVL 2&3) 70 - POWER PLANT (RR Trent 700) FADEC PRINCIPLE (3) Apr 16, 2013 Page 119 A330 RR Trent 700 TECHNICAL TRAINING MANUAL GCL13151 - GEHT0M0 - FM70DJ000000071 B1/B2\_A330\_DIFF\_FR\_A320 REV. 1 DATE: 01.06.2019 DVIATION TRAINING SERVICES FOR TRAINING PURPOSES ONLY 119 FADEC PRINCIPLE (3) FADEC DESIGN - PROCESS Most FADEC operations are based on the same principle: as a response to a demand from the aircraft or from the EEC internal schedules. Taking into account input parameters from the aircraft and the engine parameter sensors, the EEC generates a command signal sent to an engine subsystem. The EEC makes sure that its command has been followed by monitoring the feedback from the engine subsystem sensors. The EEC also sends data to the aircraft. One channel controls (Active) while the other channel monitors (Standby). In case of an input failure, the control channel can access the inputs of the monitor channel through the inter-channel bus. This design keeps the active channel serviceable as long as possible. In case of failure of a control channel circuit, the control is given to the standby channel. Normally the EEC changes over the control between channel A and channel B at each power up. MECHANICAL & AVIONICS COURSE - T1+T2 (LVL 2&3) 70 - POWER PLANT (RR Trent 700) FADEC PRINCIPLE (3) Apr 16, 2013 Page 120 A330 RR Trent 700 TECHNICAL TRAINING MANUAL GCL13151 - GEHT0M0 - FM70DJ000000071 B1/B2\_A330\_DIFF\_FR\_A320 REV. 1 DATE: 01.06.2019 DVIATION TRAINING SERVICES FOR TRAINING PURPOSES ONLY 120 FADEC DESIGN - PROCESS MECHANICAL & AVIONICS COURSE - T1+T2 (LVL 2&3) 70 - POWER PLANT (RR Trent 700) FADEC PRINCIPLE (3) Apr 16, 2013 Page 121 A330 RR Trent 700 TECHNICAL TRAINING MANUAL GCL13151 - GEHT0M0 - FM70DJ000000071 B1/B2\_A330\_DIFF\_FR\_A320 REV. 1 DATE: 01.06.2019 DVIATION TRAINING SERVICES FOR TRAINING PURPOSES ONLY 121 FADEC PRINCIPLE (3) FADEC SUBSYSTEMS The FADEC incorporates three main subsystems: \- engine control, \- overspeed protection, \- power supply. NOTE: The subsystems are physically independent. ENGINE CONTROL The EEC controls and monitors various engine systems. The most important control function of the EEC is to control engine thrust. Based on manual or automatic thrust demand, the EEC controls fuel flow through the metering valve in the Fuel Metering Unit (FMU). The EEC controls the engine during the start sequence. The active channel controls the starter control valve and the PCU. The PCU controls the power supply for ignition. The EEC controls the airflow through the IP and HP compressors by means of the Variable Stator Vanes (VSVs) and the compressor handling bleed valves, in order to avoid surge and stall conditions. The EEC controls the Turbine Impingement Cooling (TIC) system, which is used to cool the turbine case and optimize the clearance between the turbine blade tips and the case to improve the turbine efficiency. The EEC keeps the oil temperature within limits by controlling the air modulating valve of the Air Oil Heat Exchanger (AOHE). The EEC controls the thrust reverser system operation through the use of the Isolation Control Unit (ICU) and the Direction Control Unit (DCU). The High Pressure Valve (HPV), supplying the aircraft pneumatic system, is electrically controlled to the closed position by the EEC following certain engine operating conditions. Several types of feedback components, such as sensors, switches, thermocouples, etc. are used by the EEC to monitor engine operation and to provide indications in the cockpit. OVERSPEED PROTECTION The OPU is designed to initiate an immediate engine shut down in case of Rotor OverSpeed (ROS) and/or Low Pressure Turbine OverSpeed (LP TOS) detection. The OPU monitors the N1 and N2 rotor speed. If either speed exceeds the ROS limit, the OPU cuts off the fuel supply through the FMU. The LP TOS protection is the function of an independent dedicated circuit board, installed in the EEC channel A. It compares the LP compressor speed with the LP turbine speed. In the unlikely event of an LP shaft breakage, the speed difference between the LP compressor and LP turbine is detected by the LP TOS protection circuit which cuts off the fuel supply through the FMU. POWER SUPPLY The electrical power supply to the EEC is controlled by the dual channel PCU. Each PCU channel independently supplies one EEC channel. When the engine is running, a dedicated alternator installed on and driven by the external gearbox, supplies electrical power to the EEC through the PCU. The dedicated alternator also supplies the OPU. However, for ground maintenance, engine starting or in case of loss of dedicated alternator power, an alternate stand-by power source is supplied to the EEC from the aircraft 115 VAC network. MECHANICAL & AVIONICS COURSE - T1+T2 (LVL 2&3) 70 - POWER PLANT (RR Trent 700) FADEC PRINCIPLE (3) Apr 16, 2013 Page 122 A330 RR Trent 700 TECHNICAL TRAINING MANUAL GCL13151 - GEHT0M0 - FM70DJ000000071 B1/B2\_A330\_DIFF\_FR\_A320 REV. 1 DATE: 01.06.2019 DVIATION TRAINING SERVICES FOR TRAINING PURPOSES ONLY 122 FADEC SUBSYSTEMS - ENGINE CONTROL \... POWER SUPPLY MECHANICAL & AVIONICS COURSE - T1+T2 (LVL 2&3) 70 - POWER PLANT (RR Trent 700) FADEC PRINCIPLE (3) Apr 16, 2013 Page 123 A330 RR Trent 700 TECHNICAL TRAINING MANUAL GCL13151 - GEHT0M0 - FM70DJ000000071 B1/B2\_A330\_DIFF\_FR\_A320 REV. 1 DATE: 01.06.2019 DVIATION TRAINING SERVICES FOR TRAINING PURPOSES ONLY 123 FADEC D/O (3) FADEC OPERATION The EEC is the primary component of the FADEC system. As such, the EEC is the interface between the aircraft and the engine. Aircraft computers and systems exchange data (control and monitoring signals) with both EEC channels. During engine operation, both channels exchange control and monitoring signals with the FMU and engine sub-systems. This module will detail the various EEC inputs and outputs on both the aircraft and engine sides. MECHANICAL & AVIONICS COURSE - T1+T2 (LVL 2&3) 70 - POWER PLANT (RR Trent 700) FADEC D/O (3) Apr 16, 2013 Page 124 A330 RR Trent 700 TECHNICAL TRAINING MANUAL GCL13151 - GEHT0M0 - FM70DA000000071 B1/B2\_A330\_DIFF\_FR\_A320 REV. 1 DATE: 01.06.2019 DVIATION TRAINING SERVICES FOR TRAINING PURPOSES ONLY 124 FADEC OPERATION MECHANICAL & AVIONICS COURSE - T1+T2 (LVL 2&3) 70 - POWER PLANT (RR Trent 700) FADEC D/O (3) Apr 16, 2013 Page 125 A330 RR Trent 700 TECHNICAL TRAINING MANUAL GCL13151 - GEHT0M0 - FM70DA000000071 B1/B2\_A330\_DIFF\_FR\_A320 REV. 1 DATE: 01.06.2019 DVIATION TRAINING SERVICES FOR TRAINING PURPOSES ONLY 125 FADEC D/O (3) EEC - ENGINE INTERFACE The EEC controls the engine thrust and several engine sub-systems for normal operation and for engine efficiency. Only one channel of the EEC is in control but either channel can control all the systems. Similarly, all of the feedback signals for sub-system control and monitoring are dual signals sent to both EEC channels. FUEL SYSTEM The EEC controls three Fuel Metering Unit (FMU) torque motors. These torque motors (TM) operate three internal FMU servo-valves: \- a fuel metering valve, which controls the rate of fuel flow delivered to the combustion chamber, \- a Pressure Raising and Shut-Off Valve (PRSOV) which starts and stops the fuel flow, \- an overspeed valve which closes the PRSOV, in case of an overspeed condition, to shut down the engine. Both EEC channels receive position feedback: \- two resolvers monitor the metering valve position, \- two microswitches monitor the PRSOV position. MECHANICAL & AVIONICS COURSE - T1+T2 (LVL 2&3) 70 - POWER PLANT (RR Trent 700) FADEC D/O (3) Apr 16, 2013 Page 126 A330 RR Trent 700 TECHNICAL TRAINING MANUAL GCL13151 - GEHT0M0 - FM70DA000000071 B1/B2\_A330\_DIFF\_FR\_A320 REV. 1 DATE: 01.06.2019 DVIATION TRAINING SERVICES FOR TRAINING PURPOSES ONLY 126 EEC - ENGINE INTERFACE - FUEL SYSTEM MECHANICAL & AVIONICS COURSE - T1+T2 (LVL 2&3) 70 - POWER PLANT (RR Trent 700) FADEC D/O (3) Apr 16, 2013 Page 127 A330 RR Trent 700 TECHNICAL TRAINING MANUAL GCL13151 - GEHT0M0 - FM70DA000000071 B1/B2\_A330\_DIFF\_FR\_A320 REV. 1 DATE: 01.06.2019 DVIATION TRAINING SERVICES FOR TRAINING PURPOSES ONLY 127 FADEC D/O (3) EEC - ENGINE INTERFACE (continued) ENGINE AIR SYSTEM Compressor bleed valves are located around the compressor. The valves are used to unload the compressors during start and transient operations to prevent surges and stalls. The EEC controls the operation of four IP bleed valves, and three HP bleed valves through the bleed valve controller. The controller is supplied with HP3 air (high pressure compressor stage 3) and contains the IP and HP bleed valve solenoids, When a solenoid is energized by the EEC channel A or B, HP3 air is supplied to the related bleed valve. Variable inlet guide vanes and the first 2 stages of stator vanes adjust the airflow through the IP compressor. The EEC controls the angular position of the variable vanes through the VSV control unit. A torque motor controlled servo-valve in the controller supplies high-pressured fuel to the VIGV/VSV actuators. The EEC receives feedback from LVDTs integrated in the actuators. The EEC controls the operation of the Turbine Impingement Cooling (TIC) valve by the TIC solenoid valve. There is no feedback of the TIC valve position. MECHANICAL & AVIONICS COURSE - T1+T2 (LVL 2&3) 70 - POWER PLANT (RR Trent 700) FADEC D/O (3) Apr 16, 2013 Page 128 A330 RR Trent 700 TECHNICAL TRAINING MANUAL GCL13151 - GEHT0M0 - FM70DA000000071 B1/B2\_A330\_DIFF\_FR\_A320 REV. 1 DATE: 01.06.2019 DVIATION TRAINING SERVICES FOR TRAINING PURPOSES ONLY 128 EEC - ENGINE INTERFACE - ENGINE AIR SYSTEM MECHANICAL & AVIONICS COURSE - T1+T2 (LVL 2&3) 70 - POWER PLANT (RR Trent 700) FADEC D/O (3) Apr 16, 2013 Page 129 A330 RR Trent 700 TECHNICAL TRAINING MANUAL GCL13151 - GEHT0M0 - FM70DA000000071 B1/B2\_A330\_DIFF\_FR\_A320 REV. 1 DATE: 01.06.2019 DVIATION TRAINING SERVICES FOR TRAINING PURPOSES ONLY 129 FADEC D/O (3) EEC - ENGINE INTERFACE (continued) THRUST REVERSER SYSTEM The EEC controls the hydraulic operation of the thrust reverser pivoting doors. To operate the thrust reverser, the EEC sends command signals to the Isolation Control Unit (ICU) and the Direction Control Unit (DCU). The ICU and DCU direct hydraulic pressure to unlock, deploy and stow the thrust reversers. The EEC receives feedback signals for control and monitoring from: \- the 4 Rotational Variable Transducers (RVTs), \- the 4 stow switches, \- the 4 tertiary lock position microswitches, \- the ICU pressure switch, \- the thrust reverser inhibit lever switch. MECHANICAL & AVIONICS COURSE - T1+T2 (LVL 2&3) 70 - POWER PLANT (RR Trent 700) FADEC D/O (3) Apr 16, 2013 Page 130 A330 RR Trent 700 TECHNICAL TRAINING MANUAL GCL13151 - GEHT0M0 - FM70DA000000071 B1/B2\_A330\_DIFF\_FR\_A320 REV. 1 DATE: 01.06.2019 DVIATION TRAINING SERVICES FOR TRAINING PURPOSES ONLY 130 EEC - ENGINE INTERFACE - THRUST REVERSER SYSTEM MECHANICAL & AVIONICS COURSE - T1+T2 (LVL 2&3) 70 - POWER PLANT (RR Trent 700) FADEC D/O (3) Apr 16, 2013 Page 131 A330 RR Trent 700 TECHNICAL TRAINING MANUAL GCL13151 - GEHT0M0 - FM70DA000000071 B1/B2\_A330\_DIFF\_FR\_A320 REV. 1 DATE: 01.06.2019 DVIATION TRAINING SERVICES FOR TRAINING PURPOSES ONLY 131 FADEC D/O (3) EEC - ENGINE INTERFACE (continued) AIRCRAFT PNEUMATIC SYSTEM In some operating conditions, the EEC controls the High Pressure Valve (HPV) closed by energizing the HPV dual-coil solenoid (Channel A or B control). MECHANICAL & AVIONICS COURSE - T1+T2 (LVL 2&3) 70 - POWER PLANT (RR Trent 700) FADEC D/O (3) Apr 16, 2013 Page 132 A330 RR Trent 700 TECHNICAL TRAINING MANUAL GCL13151 - GEHT0M0 - FM70DA000000071 B1/B2\_A330\_DIFF\_FR\_A320 REV. 1 DATE: 01.06.2019 DVIATION TRAINING SERVICES FOR TRAINING PURPOSES ONLY 132 EEC - ENGINE INTERFACE - AIRCRAFT PNEUMATIC SYSTEM MECHANICAL & AVIONICS COURSE - T1+T2 (LVL 2&3) 70 - POWER PLANT (RR Trent 700) FADEC D/O (3) Apr 16, 2013 Page 133 A330 RR Trent 700 TECHNICAL TRAINING MANUAL GCL13151 - GEHT0M0 - FM70DA000000071 B1/B2\_A330\_DIFF\_FR\_A320 REV. 1 DATE: 01.06.2019 DVIATION TRAINING SERVICES FOR TRAINING PURPOSES ONLY 133 FADEC D/O (3) EEC - ENGINE INTERFACE (continued) OIL SYSTEM As part of the engine heat management control, the EEC controls the operation of the Air Oil Heat Exchanger (AOHE) air modulating valve. A torque motor in the valve supplies servo fuel pressure to operate the valve. When the valve opens, LP air is ducted across the heat exchanger to decrease the oil temperature. The valve also has an LVDT for position feedback to the EEC. MECHANICAL & AVIONICS COURSE - T1+T2 (LVL 2&3) 70 - POWER PLANT (RR Trent 700) FADEC D/O (3) Apr 16, 2013 Page 134 A330 RR Trent 700 TECHNICAL TRAINING MANUAL GCL13151 - GEHT0M0 - FM70DA000000071 B1/B2\_A330\_DIFF\_FR\_A320 REV. 1 DATE: 01.06.2019 DVIATION TRAINING SERVICES FOR TRAINING PURPOSES ONLY 134 EEC - ENGINE INTERFACE - OIL SYSTEM MECHANICAL & AVIONICS COURSE - T1+T2 (LVL 2&3) 70 - POWER PLANT (RR Trent 700) FADEC D/O (3) Apr 16, 2013 Page 135 A330 RR Trent 700 TECHNICAL TRAINING MANUAL GCL13151 - GEHT0M0 - FM70DA000000071 B1/B2\_A330\_DIFF\_FR\_A320 REV. 1 DATE: 01.06.2019 DVIATION TRAINING SERVICES FOR TRAINING PURPOSES ONLY 135 FADEC D/O (3) EEC - ENGINE INTERFACE (continued) STARTING SYSTEM INPUTS/OUTPUTS The EEC electrically controls the operation of the starter control valve for automatic engine start, and manual engine start engine motoring. The EEC energ