Guidelines Regarding Electronic Interlocking Installation (2021) PDF
Document Details
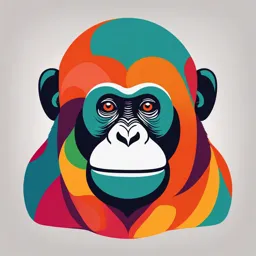
Uploaded by ImaginativePeachTree
STC/JHS
2021
Tags
Summary
These guidelines pertain to the installation of Electronic Interlocking systems within railway infrastructure. The document covers crucial aspects of power supply arrangements, communication protocols, and earthing procedures.
Full Transcript
**Subject** **Guidelines regarding Technical System Application Approval for Electronic** **Interlocking Installation** **Document No.** **STS/E/TAN/3012** **Date** **28.06.2021** Guidelines regarding installation of Electronic Interlocking ====================================================...
**Subject** **Guidelines regarding Technical System Application Approval for Electronic** **Interlocking Installation** **Document No.** **STS/E/TAN/3012** **Date** **28.06.2021** Guidelines regarding installation of Electronic Interlocking ============================================================ 1. **[Scope]** Suggestion: =========== a. The 110 volt DC supply from IPS room to EI rack shall be provided with duplicated cable with suitable gauge so as to ensure that voltage drop in cable shall not be more that 1.0 volt from integrated power supply (IPS). b. The DC-DC converters provided for Electronic Interlocking system shall be segregated for 'A' & 'B' systems along with segregation of cabling and termination for power supply up to DC-DC converters, for all the converters & shall be in N+1 configuration. It is advised that reliable DC-DC converters as advised by OEMs shall be considered for better reliability. (Tentative Power Supply Sketches are attached as Annexure --A1 & A2 ). c. The DC-DC converter shall be installed near to EI rack or in the EI rack itself to avoid the line drop. The line drop shall not be more than 0.5volt. d. The location of DC-DC converter shall be made in such a way that the 110V DC power supplies wires do not run and cut across other cables in the Electronic Interlocking room and this cable shall be treated as dirty cable and segregated from other clean wiring. e. Power supply for VDU PC/Panel processor module installed in the SM room shall be provided from 110V DC (from EI or IPS room) with duplicated cable arrangement. This shall have separate suitable DC-DC converter in N+1 configuration. f. 24 V or 110 V DC supply for fan shall be fed with separate external (from IPS) supply, which should be completely isolated from Electronic interlocking supply and same shall be provided with fuse. g. 230V AC supply for VDU Monitor shall be provided through separate inverter (Input voltage 24V DC nominal from IPS and output 230V AC, pure sine wave along with SPD) shall be provided at SM room with redundant arrangement. Inverter's 230V AC input cable shall be unplugged. Communication arrangement: ========================== a. The panel processor shall be preferably housed inside the control cum indication panel (CCIP) and shall be connected with EI on OFC cable in redundant manner in separate duct pipe to avoid failure due to cutting of optical fibre cable. b. It is advised that the EI to VDU, CPU to CPU (in case of distributed system), EI to Object Controller (in case of distributed system) & EI to Panel Processor Module connectivity shall be planned with OFC cable to avoid damage due to surge and lightening. The optical modem shall be of industrial grade with operating temperature range of 0 to 70oC. c. The communication line between the CPU's, CPU to PPM, CPU to OC and VDU shall be provided in the ring system (Redundant manner) to avoid failure due to loss of communication. The OFC and other network shall be provided with NMS (network Management System). Earthing arrangement: (For all EI's except Kyosan make K5BMC EI) ================================================================ a. Class A protection shall be ensured on top of the building. b. Copper tape (Bonding ring conductor) as per drawing mounted on insulated stand-off is provided to cover the maximum area in the Relay room, Power room & Equipment room and the connection to equipment shall be made at the nearest point. c. As far as possible, Railways shall make attempt to provide earthing in such a way that it can cover most part of the building. This is to ensure that earth resistance shall be less than 1ohm at the equipment. d. The buried earth conductor shown as copper can be of GI type to avoid theft. e. The interlinking of all Relay racks, as well as EI racks shall be ensured. f. All the cable trough and ladder shall be earthed properly. g. Provision of the relevant Surge Protection Device (SPD) for the power supplies used for Electronic Interlocking systems shall be ensured. During many cases, it was noticed that the proper earth connections in the SPDs was missing which renders SPD as functionless, hence, the same shall also be ensured. h. It shall be ensured that front and back doors of all cabinets using copper braid with shortest path to earth bus bar in equipment room. Data Logger Installation: ========================= a. The Data logger shall be commissioned prior to the commissioning of EI system with all the external relay contacts wired into data logger. b. Synchronization of the EI clock and data logger clock through CMU in network condition must be verified and certified at minimum Assistant officers\' level. c. The analog monitoring of output of DC-DC converter of EI shall be wired into data- logger for monitoring the healthiness of converter. Wiring Practice: ================ a. The input, output, data and power supply cable shall be routed indifferent cable troughs separated with a gap of minimum 6 to 8 inches. b. The input and output cables (RDSO approved) of EI shall be twisted to minimize EMI & EMC effect. c. The fuse terminals are to be fixed with proper fuse rating marking, fuse number and should be of indicative type. d. The lightening and surge protection devices shall be installed as per concerned Electronic Interlocking installation document. e. It is observed at many installations that wire ends are not properly crimped with correct size of lugs & loose connections are found at the terminals end. It is to be ensured and verified thoroughly at site minimum by Assistant officers\' level. f. Separation of 110V DC and other external power supply from the internal 12V/24V/50V DC power supply in the relay room by placing them in separate trough/ladder. g. Voltage monitoring cables to the data logger shall also be placed in a different trough which does not have any internal power supplies. Miscellaneous: ============== a. In terms of Railway Board's letter no. 2012/Sig/ASTS dated 03.05.2012, the application for technical system approval shall be forwarded through CSTE/Open line after due scrutiny and verification by Open line. b. As per Railway Board's letter no. 2010/Sig/SGF/EI (Ansaldo) dated 26.12.2012, in order to avoid failures due to reset, commissioning shall be planned with hot standby system only. c. The input and output details and logic shall be scrutinized and verified at minimum level of JAG officer before commissioning and certificate for the same shall be submitted to RDSO. d. The Factory Acceptance Test (FAT) shall be verified by Railway official (Open line/Construction) and Sample verification shall be done by minimum JAG officer during SAT(Site Acceptance Test) e. It is advised, for better reliability the guideline specification of embedded VDU as given in \"Technical Advisory Note No STS/E/TAN/3007 Ver. 1.0 Date 2.11.2012 may please be seen for guidance. f. It is observed that document submitted to ROSO for Technical system application approval are not verified & signed by authorized Railway officer (open line/construction). They are either signed by RVNL official or only by the firm official who are commissioning the Electronic interlocking installation, same shall not be accepted. g. The pre-commissioning checklist for concerned EI shall be thoroughly checked at the site at the minimum Assistant officers\' level jointly with the executing OEM. h. The quality and integrity of the installation remains complete responsibility of the OEM. The firm must provide an OEM certificate regarding this before commissioning of any installation, any deficiency pointed out later, shall be done free of cost by OEM, this shall be confirmed by OEM before commissioning.