Supply Chain Management: Principles, Strategies, and Ethics PDF
Document Details
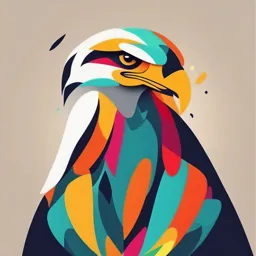
Uploaded by SuppleSard5035
Tags
Related
- HF - Supply Chain Strategic Application PDF
- Strategic Logistics Management 3rd Edition PDF
- Supply Chain Management: Strategy, Planning, and Operation PDF
- Supply Chain Management Midterm Study Guide PDF
- Supply Chain Management: Strategy, Planning, and Operation - 5th Edition PDF
- Supply Chain Coordination - Planning and Control Systems
Summary
This document provides an overview of supply chain management, discussing its core principles, functions, and the strategic coordination of business activities. It covers logistics, SCM, the supply chain flow, ethical considerations, and the importance of competitive strategies. Relevant keywords include supply chain management, logistics, strategic fit, and business strategy.
Full Transcript
CHAPTER 1: UNDERSTANDING SUPPLY CHAIN 3.​ MANUFACTURING A supply chain is the sequence of It facilitates the transfer and organizations-their facilities, functions, and transformation of raw mat...
CHAPTER 1: UNDERSTANDING SUPPLY CHAIN 3.​ MANUFACTURING A supply chain is the sequence of It facilitates the transfer and organizations-their facilities, functions, and transformation of raw materials into activities that are involved in producing and finished products delivering a product or service. 4.​ DISTRIBUTION A management system within The sequence begins with basic suppliers of logistics that is focused on order raw materials and extends all the way to the fulfillment throughout distribution final customer. channels 5.​ RETAIL LOCATION Facilities include: It manages the entire supply chain Warehouse of retail organizations Factories 6.​ CUSTOMER Processing centers The individuals or organizations Distribution that purchase and use a product or centers service Retails outlets Offices. LOGISTICS It is the part of a supply chain involved Functions and activities include: with the forward and reverse flow of goods, Forecasting services, cash, and information. Purchasing Inventory Management Logistics management includes Informati tion Management management of inbound and outbound Quality Assurance transportation, material handling, Scheduling warehousing, inventory, order fulfillment and Production distribution, third-party logistics, and reverse Distribution logistics (the return of goods from Delivery customers). Customer Service SCM vs. Logistics Supply Chain Management is the SCM sets the strategy and directs strategic coordination of business functions daily logistical activities that happen in within a business organization. factories, warehouses, local shipping centers and other facilities. Logistics is an SUPPLY CHAIN MANAGEMENT FLOW aspect of the supply chain that stores or 1.​ RAW MATERIALS delivers finished goods or services to the The basic material from which a customer. product is made. 2.​ SUPPLIER SCM covers all the activities involved An entity that provides good and in sourcing, producing, delivering, and services to another organization. returning goods and services. SCM also involves managing the relationships with scanning of goods at receiving docks, in suppliers, intermediaries, and customers. warehouses, and on retail shelves. This The objective of SCM is to optimize the eliminates errors and greatly speeds up efficiency, effectiveness, and the process. responsiveness of the supply chain, creating value for both the customer and the Important benefits of SCM business. ​ Better collaboration with suppliers. ​ Better quality control Logistics is a subset of SCM that ​ Shipping optimization focuses on the movement and storage of ​ Reduced inventary and overhead goods and services. within the supply chain. costs. It includes activities such as transportation, ​ Improved risk mitigation warehousing, inventory management, ​ Stronger cash flow. packaging, and distribution. Logistics ensures that the right products are in the Ethics and Supply Chain right place at the right time, meeting the There are many examples of unethical customer's needs and expectations. behavior involving supply chains. Logistics also takes care of the reverse flow It includies: of goods and services, such as returns, ​ Bribing government or company repairs, and recycling. officials to secure permits or favorable status. LOGISTICS ​ "Exporting smokestacks" to developing countries. Incoming and Outgoing Shipments Overseeing the shipment of Incoming Ethics and Supply Chain and outgoing goods comes under the heading of traffic management. Computer ​ Claiming a "green" supply chain tracking of shipments often helps to when in reality the level of green is maintain knowledge of the current status of only minimal green shipments as well as to provide other ​ Ignoring health, safety and up-to-date information on costs and environmental standards. schedules. ​ Violating basic right al workers. Tracking Goods: RFID Every company should develop an ethical Radio frequency identification (RFID) supply chain code to guide behavior. is a technology that uses radio waves to identify objects, such as goods in supply A major risk of unethical behavior is that chains. This is done through the use of an when such behavior is exposed in the RFID tag that is attached to an object. media, consumers tend to blame the major company or brand in the supply chain Tracking Goods: RFID associated with the ethical infractions. RFID tags can be attached to pallets, cases, or individual items. RFID eliminates PROCUREMENT the need for manual counting and bar-code The purchasing department of an organization by buyers or customers) with organization is responsible for obtaining the their resources and capabilities. materials, parts, supplies, and services needed to produce a product or provide a COMPETITIVE AND SUPPLY CHAIN service. STRATEGIES The duties of purchasing are identifying Competitive Strategy: a set of policies and sources of supply, negotiating contracts, procedures that a business uses to gain a maintaining a database of suppliers, competitive advantage in the market. obtaining goods and services that meet or exceed operations requirements in a timely Product Development Strategy: relies on and cost-efficient manner, and managing developing new products or modifying suppliers. existing products so they appear new, and offering those products to current or new The Purchasing Cycle markets The purchasing cycle begins wito a request from within the organization to Marketing and Sales Strategy: specifies purchase matera equipment, supplies, or how the market will be segmented and other items from outside the organization. product positioned, priced, and promoted. The cycle ends when the purchasing your plan for reaching, engaging, and department notified that a shipment has converting target prospects into profitable been received in satisfactory.condition, customers The main steps in the cycle are: 1. Purchasing receives the requisition 2. Purchasing selectsa supplier 3. Purchasing places the order with a vendor 4. Monitoring orders 5. Receiving orders Michael Porter's generic strategies are a CHAPTER 2: ACHIEVING STRATEGIC FIT valuable framework for identifying a suitable IN A SUPPLY CHAIN segment to acquire a strategic advantage in Strategic fit means the supply chain every Industry. and competitive strategies must have a common goal. It refers to consistency Competitive and Supply Chain Strategies between the competitive strategy of meeting Having a competitive strategy is most customers' needs and demands and the important when a company has a strategy of responding efficiently within its competitive marketplace and several similar supply chain capabilities. products are available for consumers. This Strategic fit means meeting the strategy helps you create a defensive organizational external environment position in your industry, along with (requirements or demands to the generating a superior return on investment. COST FOCUS STRATEGY This strategy involves trying to offer the lowest price, but it attempts to target a FOUR TYPES OF COMPETITIVE unique market segment with specific STRATEGIES preferences and needs. When a company implements a cost ​ COST LEADERSHIP STRATEGY focus strategy, it can establish brand ​ DIFFERENTIATION LEADERSHIP awareness more easily within a specific geographic market. STRATEGY A Cost Focus Strategy is when an ​ COST FOCUS STRATEGY organization tries to attract potential ​ DIFFERENTIATION FOCUS customers solely based on pricing. For example, A bar or restaurant that STRATEGY attempts to improve table turnaround time (catering to more customers who remain for COST LEADERSHIP STRATEGY a shorter time rather than welcoming people A cost leadership strategy keeps to sit for longer hours) prices for products and services lower than competitors to encourage DIFFERENTIATION FOCUS STRATEGY customers to purchase the lower-priced Focused differentiation allows you to products to save money. target one or all market segments and The business projects itself as the provide custom products for each. cheapest manufacturer or provider of a For example, Coca-Cola, with its Diet, particular product or commodity in a canned, and bottled colas is a focused competition. differentiation strategy example that serves Some cost leadership examples include three distinct market segments. McDonald's, Walmart, Ryan Air, Primark and IKEA Competitive and Supply Chain Strategies DIFFERENTIATION LEADERSHIP Supply Chain Strategy: STRATEGY determines the nature of material Businesses may use the differentiation procurement, transportation of materials, leadership strategy to differentiate their manufacture of product or creation of products from competitors by service, distribution of product emphasizing special features of their the overarching plan that an products. This strategy might involve the organization uses to manage the flow of design or function of a product. goods and services, from sourcing raw Differentiation strategy allows a materials to delivering products to company to compete in the market with customers. something other than lower prices. For example, a candy company may The Value Chain: Linking Supply Chain differentiate its candy by improving the taste and Business Strategy or using healthier ingredients. A value chain is used to describe Dimension describing the supply chain activities it takes to create a product is supply chain responsiveness from start to finish (e.g., design, production, distribution). Supply chain responsiveness ability to 1.​ New Product adapt quickly 2.​ Marketing & Sales respond to wide ranges of quantities 3.​ Operations demanded meet short lead times 4.​ Distribution handle a large variety of products 5.​ Service build highly innovative products meet a very high service level Value chain also refers to the full Supply chain efficiency: cost of making lifecycle of a product or process, and delivering the product to the customer including material sourcing, production, Increasing responsiveness results in consumption and disposal/recycling higher costs that lower efficiency processes. Step 3: Achieving Strategic Fit Achieving Strategic Fit Step 3 is to ensure that what the supply chain does well, is consistent with target Step 1: Understanding the customer and customer's needs. supply chain uncertainty Step 2: Understanding the supply chain Other Issues Affecting Strategic Fit Step 3: Achieving strategic fit Multiple products and customer segments Step 1: Understanding the Customer and Product life cycle Supply Chain Uncertainty Identify the needs of the customer Competitive changes over time segment being served Quantity of product needed in each lot Response time customers will tolerate Variety of products needed Chapter 3: Supply Chain Drivers and Service level required Metrics Price of the product Supply chain metrics Desired rate of innovation in the product Overall attribute of customer demand -​ are performance indicators used by Demand uncertainty: the external businesses to assess and optimize factors that cause demand to the efficiency and productivity of unexpectedly increase or decrease. various supply chain processes. Implied demand uncertainty: resulting uncertainty for only the portion of the FINANCIAL MEASURES demand that the supply chain plans to -​ It is the measures taken for gauging satisfy different fixed and operational costs related to a supply chain. Step 2: Understanding the Supply Chain How does the firm best meet demand? -​ It indicates the company's strategy. Drivers of Supply Chain Performance implementation, and execution are The supply chain management drivers contributing to bottom-line were the main focus that motivates supply Improvement. chain sustainability.It influences the performance of the supply chain. Such -​ The key objective to be achieved is drivers include facility, transportation, to maximize the revenue by information, inventory, sourcing, and maintaining low supply chain costs. pricing. FINANCIAL MEASURES OF ​ Supply chain drivers enable a PERFORMANCE balance between responsiveness to From a shareholder perspective, return the customer and efficiency in on equity (ROE) is the main summary supply chain that allows the measure of a firm's performance company to be competitive in its Return on equity (ROE) chosen strategic arena -​ is the measure of a company's net ​ FACILITIES - The physical locations income divided by its shareholders' in the supply chain network where equity. ROE is a gauge of a product is stored, assembled or corporation's profitability and how fabricated. efficiently it generates those profits. ​ INVENTORY - All raw materials, work in progress, and finished goods Return on assets (ROA) within a supply chain. -​ measures the return earned on each ​ TRANSPORTATION - Moving amount invested by the firm in Inventory from point to point of the assets. Assets are owned by an supply chain. individual. company, or organization ​ INFORMATION - Data and analysis -​ Return on assets is a profitability concerning facilities. Inventory, ratio that provides how much transportation, costs, prices, and profit a company can generate customers throughout the supply from its assets. chain. ​ SOURCING- Who will perform a Accounts payable turnover (APT) particular supply chain activity. -​ An important ratio that defines ​ PRICING- How much a firm will financial leverage charge for the goods and services -​ The accounts payable turnover that it makes available in the supply measures how quickly a business chain. makes payments to creditors and suppliers that extend lines of credit.