Diesel Engine Theory PDF
Document Details
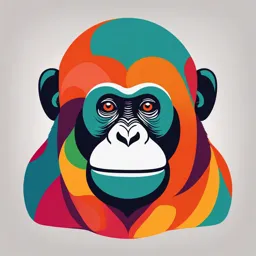
Uploaded by ImaginativePeachTree
STC/JHS
Tags
Summary
This document provides an introduction to diesel engine theory, focusing on the four-stroke and two-stroke operating cycles. It covers essential concepts like general engine arrangement and model types.
Full Transcript
c c c c c c c G G c c c c c c c c Diesel Engine Theory G c c c Introduction c In this chapter we will look at the diesel engine beginning with a review of the four stroke and two stroke...
c c c c c c c G G c c c c c c c c Diesel Engine Theory G c c c Introduction c In this chapter we will look at the diesel engine beginning with a review of the four stroke and two stroke operating cycles. In this chapter we will continue with: c c ElectrMotive general engine arrangement; model types (8,12,16, and 20 cylinders,); c 567,645and 710 Diesel internal pressure zones (crankcase, airbox, and top deck,) Engines are all G "twostroke" serial number locations and system engines. G In the next chapter we will cover the individual components in detail. c G Engine Operating Cycles c The General Motors diesel engine utilizes a two stroke operating cycle. c This means that for one engine cylinder to generate a power pulse, it requires two strokes of the piston, one upwards stroke and one downwards stroke. The easiest way to c present this cycle is by first comparing it to the four stroke cycle used in most other diesel engines. c 'G c c - IT5 Locomotive Training Series Student Text 2-1 a e 3 - Four Stroke Engine Construction Fuel Injector 3 Most four stroke diesel engines share a Intake Exhaust similar construction (Figure 2.1). Valve Valve 3 3 The cylinder is closed on the top by the cylinder head and sealed on the bottom 3 by the moveable piston and piston rings. Intake and exhaust valves located in the Cylinder + 13 cylinder head allow the flow of gases into and out of the cylinder as required. 3 The crankshaft eccentric and the. Piston 3 connecting rod translate the up and down motion of the piston to a rotary motion on 13 the shaft. 3 Crankshaft 1c3 3 3 3 Figure 2.1 Four Stroke Construction 3 3 - Four Stroke Engine Intake Stroke 1" 3 3 The four stroke cycle begins with the Fresh air enters intake stroke (Figure 2.2). Cylinder 3 through The rotary motion of the crankshaft Intake valve 3 causes the piston in the cylinder to move 3 downwards, increasing the volume of the cylinder. As the volume of the cylinder 3 increases, the pressure decreases below atmospheric pressure. 3 Lg Fresh air at the higher pressure rushes into the cylinder through the open intake u) valve to fill the cylinder. This provides a new charge of oxygen,for the combustion of the 3 fuel. 3 As the piston approaches the bottom 3 of the stroke (BottomDead Center or BDC), the intake valve closes to seal the cylinder. 3 The piston now begins to move upwards on the compression stroke. Figure 2.2 Intake Stroke I 2J I2-2 Electro-Motive Model 567,645 & 710 Series Diesel Engines c c G G c Four Stroke Engine - Compression c Stroke c As the piston moves upwards on the c compression stroke (Figure 2.3), the volume of the sealed cylinder is reduced and causes the pressure G in the cylinder to rapidly increase. The reduction in cylinder volume is usually expressed as the c compression ratio. This ratio is the difference between the cylinder volume with the piston at c Bottom Dead Center (BDC) and cylinder volume c with the piston at Top Dead Center (TDC). Diesel engines commonly have compression ratios c between 16:l and 20:l. c It is a property of gases, that as the pressure is c increased the temperature also increases. It is this rapid increase in temperature that provides the heat c necessary to ignite the fuel. c c Four Stroke Engine - Power Stroke Figure 2.3 Compression Stroke c a The piston moves upwards on the c compression stroke increasing cylinder pressure and Fuel enters Cylinder through Injector temperature. Near the top of this stroke, fuel is c sprayed into the cylinder by the fuel injector. c The fuel is atomized by the injector so that it will mix easily and completely with the hot air. The high c cylinder temperature ignites the fuel and air mixture and combustion begins. c The heat produced by the burning fuel and air c mixture causes a further rapid increase in cylinder c pressure. As the piston passes through Top Dead Center and begins a downward motion, the increased c cylinder pressure pushes the piston down. The force acting downwards on the piston is many times greater G than the force required to initially compress the air. c This force is transferred through the connecting rod to the crankshaft. It is through the actions of the c cylinder assembly that the latent energy contained in the fuel is released and converted into a useable c mechanical force. c c G c Figure 2.4 Power Stroke c - ITS Locomotive Training Series Student Text 2-3 a c 3 I) 3 3 I) Four Stroke Engine - Exhaust Stroke Burnt Gases “u) pushed out Before the combustion process Exhaust Valve 3 can be repeated, the cylinder must be 3 purged of the burnt gases and refilled with a fresh air charge. 3 Just before the piston reaches the G, bottom of the power stroke, the exhaust valve is opened to vent the 3 pressure contained in the cylinder. 3 The piston passes Bottom Dead Center and moves upwards on the 3 exhaust stroke. The motion of the piston moving upwards reduces the 3 volume of the cylinder and increases 4 the pressure. 3 Since the exhaust valve is open, the burnt gases flow outwards to the atmosphere through the valve. ‘t 6Jb When the piston has reached Top 3 Dead Center, the exhaust valve closes, 3 the intake valve opens, and the cylinder is ready to begin the next Figure 2.5 Exhaust Stroke 3 intake stroke. 3 3 Four Stroke Engine - Conclusion d In order for the four stroke engine to produce one power stroke, four distinct piston movements are required: 3 13 intake (piston moves downwards) compression (piston moves upwards) 3 power (piston moves downwards) 3 exhaust (piston moves upwards) 3 The crankshaft must turn two complete revolutions to produce these for motions. Therefore each cylinder of a four stroke engine will produce one power u stroke every other revolution of the crankshaft. The valve operating mechanism 3 (usually a camshaft) will operate at one half of crankshaft speed in a four stroke engine. 3 u) The energy generated on the power stroke is transferred to the crankshaft and then to the devices powered by the engine. Some of the energy produced is 4 absorbed by the heavy flywheel, usually mounted on the rear of the crank. This energy is released as momentum to carry the engine through the exhaust, )3 intake, and compression strokes. Ld 2-4 Electro-Motive Model 567, 645 & 710 Series Diesel Engines 0 c3 c c G G c Two Stroke Engine - Fuel Injector c Construction I c There are a great many different c designs for two stroke (or cycle) engines; this text will deal only with the design (air pump) c similar to the one used on the General Motors diesel engines. c; As in the four stroke engine, the G cylinder assembly is sealed at the top by c the cylinder head, and at the bottom by the piston and piston rings. Fuel is c injected in a similar manner by a fuel injector located in the cylinder head. c There are however several very c important differences. Instead of utilizing an intake valve located in the c cylinder head, a row of ports, or openings, have been located in the lower G portion of the cylinder wall. These ports c are surrounded by a chamber known commonly as the airbox. c Figure 2.6 Two Stroke Engine Constnrction Fresh air is pumped into this G chamber by an air pump, or blower, for use in combustion. G c Two Stroke Engine - c Scavenging (Start) c The two stroke engine uses a c different method of introducing a fresh air charge into the cylinder than the four G stroke engine. Rotation of the crankshaft causes the mechanically coupled air c pump to force fresh air into the airbox c that surrounds the air ports on the lower cylinder walls. c With the piston at the bottom of c the stroke, this fresh air enters the ~ 1 cylinder through the ports. As the c exhaust valves are also open at this time, c the air moves upwards through the cylinder, and exits through the c open valves. IG Figure 2.7 Scavenging (Start) c (, ITS LocomotiveTraining Series - Student Text 2-5 a G 3 I$ 3 The air ports are angled slightly from the center line of the cylinder causing the air to swirl in the cylinder as it moves upwards. Thus the cylinder is completely purged 3 and filled with fresh air. This action is called scavenging. 3 3 - Two Stroke Engine Scavenging 09 (Fin ish) 0 The crankshaft rotates, moving the piston 3 upwards in the cylinder. The upwards piston movement blocks the flow of fresh air through 3 the liner ports, and forces a small amount of air out the exhaust valves. Any remaining exhaust 3 from the previous power stroke is completely removed from the cylinder by this action. 3 3 The exhaust valves then close to seal the cylinder and allow compression of the air. 3 Figure 2.8 Scavenging (Finish) Two Stroke Engine - Compression After the exhaust valves have closed, the piston moves upwards compressing the air in the cylinder. As in the four stroke engine when the air is compressed, the temperature and pressure rise. However, compression in a two stroke engine differs slightly in that the initial cylinder pressure is slightly higher because of the air pump, and the effective stroke is much shorter. 3 cl) u) u) u) +a# Figure 2.9 Compression Stroke Ab 3 2-6 Electro-Motive Model 567,645 & 710 Series Diesel Engines L Two Stroke Engine - Injection Fuel Injection begins just before TDC The injection of fuel into the cylinder of the two stroke engine is handled in the same manner as the four stroke engine. r\s the piston nears Top Dead Center (TDC)the fuel injector delivers an atomized spray of fuel into the cylinder. The fuel combines with the air and is ignited by the high temperature. Rotation of the crankshaft carries the piston past TDC as the fuel begins to combust with the air. Figure 2.10 Injection Stroke Two Stroke Engine - Power Combustion of the fuel and air causes the pressure in the cylinder to rise rapidly. This pressure expands in all directions, pushing the piston downwards with a greater force than it took to initially compress the air. As in the four stroke engine, this force on the piston is converted into a rotary mo- tion on the crankshaft, providing a useable mechanical force. Figure2.11 Power Stroke IlS Locomotive Training Series - Student Text 2-7 3 Two Stroke Engine Exhaust- nr-in hb The piston travels downwards on the power stroke until a point just before w, the air ports are uncovered. The exhaust valves open to vent cylinder pressure 3 to atmosphere. 3 By opening the exhaust valves 3 slightly before the air ports, a flow of gasses is started through the valves and 3 cylinder pressure is reduced below that 3 of the airbox. By reducing cylinder pressure in this way a back flow of gas d (backfire) into the airbox is prevented. 131 Cylinder pressure continues to r) reduce until the air ports are opened by the piston. At this time the fresh air from 3 the airbox is allowed to enter and scavenge the cylinder to begin the Ls cycle again. 4 Figure 2.12 Exhaust Stroke 3 3 - Two Stroke Engine Conclusion 3 Conversion of the heat energy contained in the fuel is essentially done the same I$ way in both the two and four stroke engines. However where the four stroke engine requires two revolutions of the crankshaft to deliver one power impulse, the two stroke 3 engine will deliver one power impulse every crankshaft revolution. u) The power impulses in the two stroke engine are of a less magnitude than a four stoke due to the reduced effective compression and power strokes. d ul 2-8 Electro-Motive Model 567,645 & 710 Series Diesel Engines c c c c G Review c The four stroke engine cycle consists of intake, compression, power, G and exhaust. c Fuel is injected into a closed cylinder containing compressed air at a c temperature high enough to ignite the fuel. c The pressure increase in the cylinder due to the expanding gases forces the piston downwards inducing a turning motion on the crankshaft. c. c The four stroke engine requires two complete revolutions of the crankshaft to produce one power impulse. c The two stroke engine uses air ports located around the lower portion of the c cylinder liner instead of intake valves to admit fresh air into the cylinder. L Fresh air supplied by an air pump is used for combustion and to purge c (scavenge) the cylinder of exhaust gases. c The two stroke engine requires one complete revolution of the crankshaft to produce one power impulse. c;. c G L G c c G c L c c c c c c; c c c ITS LocomotiveTraining Series - Student Text 2-9 I c 3 3 3 General Engine Arrangement 3 The two stroke General Motors diesel engine is a It Narrow 'V' type design 3 consisting of two banks (or rows) of engine cylinders arranged with an angle of 45 0 between them. Opposing cylinders share a common crankshaft eccentric (throw)using 3 a "fork and blade" connecting rod design. This design allows for a close distance between cylinders, and the narrow "V", keeps the overall engine width to a minimum. The engine 3 is available in 8, 12, 16, and 20 cylinder models, depending on the desired horsepower output. The 3 45" compact nature of this engine makes it particularly Between Banks 3 suited to railroad locomotives and marine installations where size is a major consideration. 3 The rear of the engine is usually called the 3 flywheel end since this is where the main gen- erator is driven from. Depending on equipment 3 and horsepower, it may also be termed the blower r$ or turbo end because combustion air is supplied through the rear of the engine by either a mec- 3 hanical air blower or a turbocharger. Ls The camshaft gear train and auxiliary 3 generator drive are located on the rear of the engine. Engine rotation is left hand, or anti- 3 clockwise as viewed from the rear facing towards the front. 3 3 Figure 2.13 CM Engine - 3 Rear View c*, The front end of the engine is commonly referred to as the governor end as this is the mounting location of this device. The water pumps, lube oil pumps, and the pump 3 drive gears are also located on the front of the engine. All oil, fuel, and cooling water 3 connections for the engine are made on the front end. Since the size and type of pumps may vary according to engine horsepower and engine application, the front is sometimes hb referred to as the accessory end. A drive connection is available on the front end of the crankshaft for accessory items such as air compressors, additional pumps, or mechanically 3 driven blowers. lu) Right Bank 3 d 3 Generator Drive bid 3 Left Bank J b& Figure 2.14 Engine Configuration L) I2-10 Electro-Motive Model 567.645 & 710 Series Diesel Engines c c c G G Engine orientation is established from the rear of the engine looking forward. c The engine banks are termed left and right as viewed from the rear of the engine looking forward. The cylinders are numbered sequentially from front to rear beginning G with the right bank. Cylinder number one is always located on the right front corner of the engine. G c In the illustration of a twelve cylinder engine Figure 2.14, the cylinders on the right bank are numbered one thru six; the cylinders on the left bank are numbered seven c thru twelve. O n a sixteen cylinder engine the cylinders on the right bank are numbered one thru eight beginning with the right front; the cylinders on the left bank are cfl numbered nine thru sixteen beginning with the left front. c Cylinder number one on all engines is at TDC when the flywheel pointer reads 0". c The cylinder mated to number one will be at TDC 45" later because of the layout of the cylinder banks. Therefore, paired engine cylinders, such as number one and seven on c the twelve cylinder model, always fire 45" apart. c O n the eight cylinder engine, a power pulse is generated every 45" of crankshaft c rotation (360" I 8 cyl = 45"). The sixteen cylinder engine generates a power pulse every 22 1/2" of crankshaft rotation (360" I 16 cyI = 22 I/2").These two engines have a c "Balanced" firing order since the pulses are evenly distributed through out one crankshaft revolution. c G The twelve and twenty cylinder models have an "Unbalanced" firing order. To balance these engines is not possible with a 45" vee. For example, the twelve cylinder c model would require a power pulse every 30" (360" I 12 cyl = 30"). This is not possible since opposing cylinders are 45" apart. The "Pairs" of cylinders are distributed through c out the revolution based on experience and computer simulation to give the best performance for the twelve and twenty cylinder models. An Injector Timing tag is c located at the rear corner of the engine for use when doing engine adjustments. c NOTE: c Always consult your Engine Maintenance Manual for the correct firing order and timing for the engine being serviced ! c c The exhaust system is located on the top of the engine between the cylinder banks. c For engines equipped with mechanical blowers, the exhaust is collected in the manifold and allowed to vent to atmosphere. O n higher horsepower engines equipped with c turbochargers, the exhaust is collected in the manifold and sent through the turbine before escaping to atmosphere. c G c c c c c I ~ ~~ ~ ~ ~~ ITS Locomotive Training Series - Student Text c 2-11 t 3 L) 3 3 3 Review 3 The GM diesel engine is a 45" "narrow V" design. 3 Engine layout is determined from the rear of the engine facing forward. 3 The combustion air supply (bloweror turbo), camshaft gear train, and generator 3 drives are located on the rear of the engine. 3 The engine consists of two banks (or rows) of cylinders, the left bank and the right bank. 3 64 The cylinders are numbered from front to rear, beginning with the right front cylinder. 3 Opposing cylinders are always timed 45" apart. 3 3 The front end of the engine is also called the governor or accessory end. io) The governor, water pumps, and lube oil pumps are located on the front of the engine. 'Ir) I$ All fuel, oil, and cooling water connections are made at the front of the engine. 3 The exhaust system is mounted to the top of the engine between the cylinder banks. 3 3 lo) 4 1c3 Ls 3 3 3 3 3 3 3 3 2-12 ElectroMotiveModel 567, 645 & 710 Series Diesel Engines LJ LA ~ c c G G c Internal Pressure Divisions G The GM diesel engine is divided into two distinct pressure zones; positive pressure G (above atmospheric pressure);and negative pressure (be2ow atmospheric pressure). G (I, Positive Pressure c The airbox area of the c engine is always at a positive pressure as compared to c atmosphere. The positive pressure is required to force the c air into the cylinders through Positive Pressure the liner air ports. The in c flowing air must have sufficient c pressure to push through the cylinder and force the burnt c gases out the exhaust valves. Unlike the four stroke engine, G there is no intake stroke to draw c fresh air into the cylinder, nor an exhaust stroke to expel the c burnt gases. Figure 2.15 Positive Pressure Zone 6 ci The positive air pressure in the airbox is sometimes referred to as the boost c pressure. The amount of boost pressure on a mechanical blower equipped engine is directly proportional to the speed of the blower (engine speed). O n turbo equipped c engines, the boost depends not only on engine speed, but also the amount of fuel consumed by the engine, as the turbo relies on waste heat energy in the exhaust c to operate. c c Negative Pressure c Most engines use a crankcase c ventilation system to prevent the buildup of combustible gases in the crankcase. c The eductor system on the GM engine is designed to keep the crankcase at a G negative pressure whenever the engine is running. Blower equipped engines draw G the crankcase vapours through an oil G separator into the blower inlet. Turbo equipped engine use an eductor c (venturi) tube in the exhaust stack to draw the vapours through the oil c separator and expel them to atmosphere. Figure 2.16 Negutive Pressure Zone G c - ITS Locomotive Training Series Student Text 2-13 I c;..... _- ~..... ~. 3 3 I The oil separator is designed to trap and recover small oil droplets carried out of the engine with the vapours. 3; The top deck area of the engine is common to the engine sump through oil drain tubes, and the entire assembly is kept at the negative pressure. The reduction of pressure is dependant on engine speed and engine condition. As engine speed is increased, the vapour withdrawn is also increased. Leakage on engine covers and seals or excessive piston ring leakage (blowby) will affect the ability of the system to maintain the negative pressure. Serial Numbers To facilitate parts identification most major components and assemblies are Refer to section "0"of stamped with a part number and a unique serial number. In order to maintain the G M the Engine engine and ensure correct parts replacement, it is necessary to understand the system Maintenance used for serial numbers. Section 0 of the Engine Maintenance Manual identifies most Manual. 3 parts that carry serial numbers and where the number is located. 3 The following example shows the type of information typically found on the Serial I Number & Identification plate found on the right bank of the crankcase. 31 a) model designation 31 b) date of manufacture (or remanufacture) c) location of manufacture d) production sequence number ELECTRO-MOTIVE DIVISION GENERAL MOTORS CORPORATION LAGRANGE, IL 60526 MODEL NO. SERIAL NO. l - 2 3 4 s 6 i 8 9 io Figure 2.17 Engine ldentification Plate I2-14 ~~ ~ Electro-Motive Model 567, 645 & 710 Series Diesel Engines c c c c e The specific breakdown of the data is as follows: G (1) Number of cylinders ( 8, 12,16, or 20) G c (2) Cubic inch displacement per cylinder ( 567,645, or 710) (9291.4, 10,569.6, 11,634.8)-CM3 c (3)(4)Application ( 567A thru E, 645 E thru F, 710 G) c E Railroad engine blower equipped c El Industrial engine blower equipped c E2 E3 Marine engine blower equipped (without strainer housing) Railroad engine turbocharged c E4 Industrial power generator E5 Marine engine turbocharged (without struiner housing) c E6 Marine engine blower equipped (with strainer housing) E7 Marine engine turbocharged (with strainer housing) c E8 Drill rig engine blower equipped c E9 El0 Drill rig engine turbocharged Industrial engine turbocharged c; (5) New Generation Fuel Economy Engine (designated B or C ) c c (6) (7) Year produced Month produced ( A thru M, Z is skipped due to confusion) c (8) Engine history c 1 New manufacture c 2 Remanufactured trade in c 3 4 UTEX (unit exchange) Repair and return c (9) Location of production G c 1 LaGrange, 11. 2 not used c 3 Hazelwood, Mo. (no longer used) 4 Vendoritem c 5 Halethorpe, Md. (turbo) 6 Commerce, Ca. (turbo) c 7 Jacksonville, F1. e (10) Production sequence number G In addition to the engine itself, all major components and assemblies carry a serial G number. While it is possible for two parts to have identical serial numbers, it is not G possible for two parts to have both the same serial number and the same part number. For example, while you may have a cylinder head and a cylinder liner with the same c serial numbers, it is impossible to have two cylinder heads with the same serial numbers. G c ITS Locomotive Training Series -Student Text 2-15 a c I 3 ;... ,.... 3 Review The diesel engine and all major components and assemblies are identified with part numbers and unique serial numbers. 3 3 The serial number provides a history of the engine or component including date and location of manufacture. 31 The diesel engine identification tag is located on the right bank of the engine It is not possible to have two identical parts with the same serial number. The first two digits of the serial number indicate the year of production. Months of manufacture are expressed as A thru M; I is excluded due to confusion. The last three digits of the serial number indicate the production sequence number. 2-16 Electro-MotiveModel 567,645 & 710 Series Diesel Engines