Strength of Materials PDF
Document Details
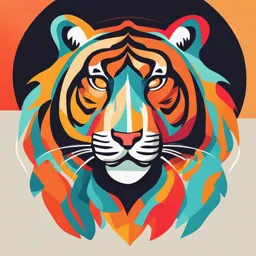
Uploaded by InvigoratingMatrix
University of Mines and Technology
Tags
Related
- Strength of Materials Pictorial Booklet-4 PDF
- Mechanics of Materials, Seventh Edition PDF
- Strength Of Materials PDF
- Royal University of Bhutan TSM 202: Strength of Material Lecture 1.2 PDF
- 22306 Strength of Materials Sample Question Paper - AE/ME/PG/PT/FG - 2022 Summer (PDF)
- Strength of Materials Notes PDF
Summary
This document introduces the fundamental concepts of stress and strain in structural and solid body mechanics. It covers tension, compression, bending, and twisting, and explains how forces acting on a body cause structural deformations. It emphasizes the importance of stress analysis in the design of mechanical components and structures.
Full Transcript
CHAPTER ONE SIMPLE STRESS AND STRAIN 1.1 INTRODUCTION Structural and solid body mechanics is concerned with analysing the effects of applied loads. These are external to the material of the structure or body and result in internal react...
CHAPTER ONE SIMPLE STRESS AND STRAIN 1.1 INTRODUCTION Structural and solid body mechanics is concerned with analysing the effects of applied loads. These are external to the material of the structure or body and result in internal reacting forces, together with deformations or displacements conforming to the principles of Newtonian Mechanics. The strength of a material is defined largely by the internal stress or intensities or force in the material. Thus the concern of this subject will be internal effects of forces acting on the body. The bodies themselves will no longer be considered to be perfectly rigid as was assumed in statics, instead the calculation of deformation of various bodies under a variety loads will be one of primary concern. Usually, the objectives of our analysis will be the determination of stress, strains and deflections produced by the loads. If these quantities can be found for all values of load then we will have a complete picture of the mechanical behaviour of the body. Knowledge of these stresses is essential to the safe design of a machine, an aircraft or any type of structure. Most of these practical structures consist of a complex arrangement of many component members. The detail stress analysis is a difficult task even when the loading conditions are simple. The problem is further complicated because the loads experienced by a structure are variable and sometimes unpredictable. Forces acting on the body result in four basic deformations or displacements of structure or solid bodies and these are tension, compression, bending and twisting. 1.2 Tension and Compression (Direct Stresses). The fundamental concepts of stress and strain can be illustrated by considering a straight metal bar loaded at its ends by collinear (or axial) forces P coinciding and acting through the centroid of each cross – section as shown in Figure 1-1. a P P a Fig. 1-1 Bar in tension 1 The axial forces produce a uniform stretching of the bar, hence the bar is said to be in tension. To investigate the internal stress produced in the bar by the axial force we make an imaginary cut at the section a-a. This section is taken perpendicular to the longitudinal axis of the bar hence it is known as cross section. a P P a σ We now isolate the right part of the bar as a free- body. The tensile load P acts at the right hand end of the free body. At the other end are forces representing the hatching of the removed part of the bar or the part that remains. These forces are continuously distributed over the cross-section. The intensity of these forces (Force /Area) is called stress and is represented by σ (sigma). Assuming that the load has a uniform distribution over the cross-section, then it is readily seen that its resultant is equal to the intensity σ x area of cross section of the bar. From the equilibrium of the body shown, the resultant must be equal in magnitude and opposite in direction to the applied load P, hence σ = P/A Units: Nm-2 (Pascal) where σ = stress P = applied load, A = cross-sectional area. The above equation is the equation for uniform stress in an axially loaded bar of arbitrary cross- sectional shape. When the bar is stretched by a force P, the resulting stresses are tensile. If the forces are reversed in direction at each end of the bar i.e directed towards the bar, the bar is said to be in a state of compression and the resulting stresses are compressive stresses (Figure 1-2). P P Fig. 1-2 Bar in compression Tensile and compressive stresses are together referred to as Direct or Normal (Perpendicular) stresses. They are referred to as normal stresses because the stresses act in a direction perpendicular to the cut surface. Customarily, tensile stresses are defined to be positive and the compressive stresses to be negative. It is important to realise that the stress equation gives the average normal stress acting on the cross-sectional area. With concentrated loads or where the material being loaded changes 2 in shape i.e. a hole through the bar, then the stress will generally not be the same over each segment of the cross section. The maximum stress will depend on the bar’s geometry and the type of discontinuity. Tables and graphs are available which enable stress concentration factor K to be determined. The maximum stress is then being K times the average stress. Example 1.1 A steel bar of rectangular cross-section 25 mm x 20 mm carries an axial tensile load of 3 kN. Estimate the average tensile stress in the cross-section. Example 1.2 A steel bolt 25 mm in diameter carries a load of 4 kN in tension. Estimate the tensile stress of the section A and at the screw section B when the diameter of the thread is 20 mm. 1.3 Strain L δ P P L+δ Fig 1-3 An axially loaded bar undergoes a change in length becoming longer when in tension and shorter when in compression. The change in length can be denoted by δ (delta), Figure 1-3, for the bar in tension. This elongation is the cumulative result of the stretching of the material throughout the length of the bar. Now assuming that the material is the same everywhere in the bar then, if we consider half of the bar, it will have an elongation equal to δ/2. Similarly, if we consider a unit length of the bar, it will have an elongation of 1/L times the total elongation δ. In this manner we arrive at the concept of elongation per unit length or strain and it is denoted by ε (Epsilon) and is given by the equation: ε = δ/ L. where δ = elongation (change in length) L = original/ initial length ε = strain. 3 Strain is a measure of the deformation produced in the member by the load. Direct stresses produce a change in length in the direction of the stress. The above definition of strain is useful only for small distortions in which the extension δ is small compared to the original length L. It is however, adequate for most engineering problems where values of strain are of order of 0.001. If the bar is in tension the strain is called a tensile strain representing an elongation or stretching of the material. If the bar is in compression the strain and the bar shortens. Tensile strain is taken as positive and the compressive, negative. The strain ε is call Axial or Normal strain because it is associated with normal stresses. Normal strain is a dimensionless quantity since it is a ratio of two lengths and hence has no units. Example 1.3 A cylindrical block of concrete is 300 mm long and has a circular cross section of 100 mm in diameter. It carries a total compressive load of 67 kN and under this load contracts 0.2 mm. Estimate the compressive stress and the compressive strain. Example 1.4 A bar with a rectangular cross section 20 mm x 40 mm and length L = 2.8 m is subjected to an axial tensile force of 70 kN. The measured elongation of the bar δ is 1.2 mm. Calculate the tensile stress and the strain in the bar. 4 1.4 Tensile Test (Stress –Strain Diagrams) Mild Steel or low carbon steel σ High Ductility D B C E A ε Cold drawn or heat treated steel Low Ductility σ ε σ Brittle (High Carbon Steel) ε 5 The mechanical properties of materials used in engineering are determined by tests performed on small specimens of the material. These tests are conducted in material- testing laboratories equipped with testing machines capable of loading the specimens in a variety of ways including static and dynamic loading in tension and compression. Most common material test is the tensile test, in which tensile loads are applied to the ends of a cylindrical specimen. As the specimen is pulled, the load P is measured and recorded either automatically or by reading from the dial gauge. The elongation over the gauge length is measured simultaneously with the load, usually by mechanical gauges or extensometers. The load is applied very slowly. The axial stress in the test specimen is calculated by dividing the load P by the cross-sectional area A. When the initial area of the bar is used in this calculation, the resulting stress is called the Nominal Stress (Conventional or Engineering Stress). More exact value of the axial stress known as the true stress can be calculated by using the actual area of the bar, which can become significantly less than the initial area for some materials. The average axial strain in the bar is found from the measured elongation δ between the gauge marks by dividing δ by the gauge length L. If the initial gauge length is used then the nominal strain is obtained. If the actual is used in calculating the strain, the true strain or natural strain is obtained. After performing tension and the compression test in determining the stress and strain of various magnitudes of a load, the plot of stress versus strain diagram can be made. Such a diagram is a characteristic of the material and conveys important information about the mechanical properties and types of behaviour of the material. The stress – strain diagram for typical mild steel (low carbon steel) in tension is shown in Figure 1-4. σ E′ D Ultimate Stress B C A Fracture E Yield Stress Limit of Prop. O ε Elasticity Perfectly Strain Necking Plastic Hardening Fig 1-4 Stress- strain diagram for typical mild-steel Strains are plotted on the horizontal axis and stresses on the vertical axis. The diagram begins with a straight line from O to A. In this region, the stress and strain are directly proportional and the behaviour of the material is said to be linear. Beyond point A, the linear relationship between 6 stress and strain no longer exists, although the material may still be in the elastic state, in the sense that, if the load were removed, the strain also would return to zero. Hence A is the proportional limit and B the elastic limit. With an increase in load beyond the proportional limit, the strain begins to increase more rapidly for each increment in stress. The stress – strain curve has a smaller and smaller slope, until at point B, the curve becomes horizontal. Beginning at this point, considerable elongation occurs with no noticeable increase in tensile force from B to C in the diagram. This phenomenon is known as yielding of the material and the stress at point B is called the Yield Stress. From B to C the material becomes perfectly plastic which means the material can deform without an increase in the applied load. The elongation of the mild steel specimen in a perfectly plastic region is typically 10 – 15 times the elongation that occurs between the onset of loading and the proportional limit. After undergoing the large straining that occurred during yielding in the region BC the steel begins to strain harden. During strain hardening the material undergoes changes in its atomic and crystalline structure, resulting in increase resistant of the material to further deformation. Thus, additional elongation requires an increase in tensile load and the stress – strain diagram has a positive slope from C to D. The load eventually reaches its maximum value and the corresponding stress at point D is called the Ultimate Stress. Further stretching of the bar is actually accompanied by a reduction in the load and fracture finally occurs at a point such as E. Lateral contraction of the specimen occurs when it is stretched resulting in a decrease of the cross sectional area. If the actual cross sectional area of the narrow part of the neck is used to calculate the stress, the true stress –strain curve will follow the dashed line CE′. In the vicinity of the ultimate stress, the reduction in area of one bar becomes visible. A pronounced necking of the bar occurs. Brittle Material is one showing relatively little elongation at fracture in the tensile test i.e. they fail in tension at relatively low values of strain. Examples are: Concrete, Stone, Cast Iron, Ceramic Materials Ductile Material is one that undergoes large strains before failure, thus stretch appreciably before breaking. Examples are: Mild steel, Copper, Aluminium, Magnesium, Manganese, Brass (Zn Cu), Bronze (Zn S) 1.4.1 Proof Stresses When a material such as aluminium does not have an obvious yield point and yet undergoes large straining after the proportional limit is exceeded, an arbitrary yield stress may be determined by the proof stress or off –set method. 7 A line is drawn on the stress-strain diagram parallel to the initial linear part of the curve but is offset by some standard amount of strain, such as 0.002 (0.2 %). The intersection of the offset line and the stress-strain curve defines the yield stress. This stress is also known as Proof Stress. The 0.1 % proof stress (say) is the stress required to produce a permanent strain of 0.001 on removal of the stress. σ 0.2% Proof Stress 0.1% Proof Stress 0.002 off set 0.001 0.002 0.003 0.004 ε Fig. 1-5 Proof Stress Determination Ductility and Brittleness The capacity for being drawn out plastically before breaking is called the ductility of the material and is measured by the following two quantities; - Percentage elongation and percentage reduction in area (contraction). PERCENTAGE ELONGATION is defined as: L f Lo x 100 % Lo where Lf – Distance between the gauge marks at fracture. Lo – Original gauge length. PERCENTAGE REDUCTION is defined as: Ao A f x 100 % Ao where Af – final area of the fracture section Ao – Original cross-sectional area. 8 A material is generally classified as brittle if the percentage elongation is less than 5 in a gauge length of 50 mm. 1.4.2 Factor of Safety When designing a structure a safety factor has to be taken into account in order to ensure the working stresses keep within safe limits. It has been pointed out that stress is calculated from knowledge of the magnitude and position of application of the load, the dimensions of the member, and the properties of the material. In practice none of these factors is known exactly, and possible errors arise from various sources. In spite of all these approximations and assumptions, a body of theory has been developed which in many cases can be shown to agree with experimental results within a reasonable margin of error, and forms the basis for sound design. The maximum permissible stress, or working stress or design stress, is determined from a consideration of the above factors, taking into account the social and economic consequences of failure, and the factor of safety is normally defined as the ratio between the failure stress and the working stress. Failure Stress Factor of Safety = Working Stress To avoid failure, the following conditions must be satisfied. Maximum Induced Stress ≤ Allowable Stress The allowable stress can be obtained easily if the material proper ties and the desired safety factor are known. For ductile materials subjected to static loading, the allowable stress is often defined as: Yield Stress Allowable Stress = Factor of Safety For those ductile materials with no well-defined yield stress, the allowable stress is defined as: Pr oof Stress Allowable Stress = Factor of Safety 9 For brittle materials it is often defined as: Ultimate Stress Allowable Stress = Factor of Safety 1.4.3 Relationship between Stress and Strain (Hooke’s Law) Within the elastic region, there is a linear relationship between stress and strain. The linear relationship between stress and strain for a bar in simple tension or compression can be expressed as: σ = Eε where σ – stress ε – strain E – constant of proportionality known as Modulus of Elasticity or Young’s Modulus for the material The above equation is commonly known as Hooke’s law. Deductions: σ = Eε σ = P/A ε = δ/L E = σ/ε E = PL Aδ or δ = PL/AE Also, F = kx F/x = k Implying, P/ δ = k = AE/L The modulus of elasticity is the slope of the stress – strain diagram in the linearly elastic region (within the proportional limit) and its value depends upon the particular material being used. The unit of E is N/m2. 10 Typical Values of E 200 GPa (steel) 70 GPa (aluminium) 11 GPa (wood) Example 1.5 A tensile test is carried out on a bar of mild steel of diameter 20mm. The bar yields under a load of 8 kN. It attains a maximum load of 15 kN and breaks finally at a load of 7 kN. Estimate: (i) the tensile stress at the yield point. (ii) the ultimate stress. (iii) the average stress at the breaking point if the diameter of the neck is10 mm. Example 1.6 A concrete cube 150 mm x 150 mm x 150 mm is loaded in a compression-testing machine. If the compressive force acting normal to one face of the cube is 250 kN, calculate the compressive stress in the concrete. 1.5 Stresses in Composite Bars A composite bar may be defined as a bar made up of two or more different materials, joined together in such a manner that the system extends or contracts as one unit, equally when subjected to tension or compression. The extension or contraction of the bar being equal, the strain is also equal. The total external load on the bar is equal to the sum of the loads carried by the different material. Consider a composite bar made of two different materials in Figure 1-6. 1 2 L P Fig. 1-6 Stresses in Composite Bars Let P1 = load carried by bar 1, A1 its cross sectional area, σ1 stress produced in the bar and E1 its elastic modulus. P2, A2, σ2, and E2 are corresponding values of bar 2. P is the total load on the composite bar, L, length of the bar and δ elongation of the composite bar. 11 P = P1 + P2 = σ1A1 + σ2A2 δ1 = P1L/A1E1 , δ2 = P2L/A2E2 since δ1 = δ2 P1L/A1E1 = P2L/A2E2 -------------------- (*) A1 E1 or P 1 = P2 x A2E2 Therefore, A1 E1 P =P1 + P2 = P2 x + P2 A2E2 A2E2 And P2 = P x A1 E1 A 2 E 2 Similarly, A1 E1 P1 = P x A1 E1 A 2 E 2 Also from (*), E1 E2 σ1 = x σ2 and σ2 = x σ1 E2 E1 These equations can be used to find out loads and stresses produced in different bars. 12 1.6 Poisson’s Ratio (ν) When a bar is loaded in tension, the axial elongation is accompanied by a lateral contraction (normal to the direction of the applied load), Figure 1-7, in which the dashed lines represent the shape before loading and solid lines give the shape after loading. The lateral strain is proportional to the axial strain in the linear elastic range. The ratio of the strain in the lateral direction to the strain in the axial direction is known as Poisson’s ratio, and is denoted by ν (xu). P P Fig. 1-7 Axial elongation and lateral contraction of a bar in tension Lateral strain , y ν =– Axial strain , x The minus sign is because when one strain is tensile the other is compressive. y ν =– x or εy = – νεx or εy = νεx The lateral strain εy is also given as εy = ∆d/d or ∆t/t where d and t are diameter and thickness respectively of a material. The lateral strain represents a decrease in width (negative strain) and the axial strain represent elongation (positive strain). For compression, the opposite situation occurs with the bar becoming shorter (negative axial strain) and wider (positive lateral strain). Therefore the Poisson’s ratio has a positive value for most materials. Poisson’s ratio ranges from 0.25 to 0.35 for many metals. 0.3 is commonly used for metals. Concrete has values from 0.1 to 0.2, and cork approximately 0.0. The theoretical maximum value is 0.5. 13 1.7 Volume Change Because the dimensions of the bar in tension or compression are changed when the load is applied, the volume of the bar also changes. The change in volume can be calculated from the axial and lateral strains. The unit volume change ℮ is defined as: the change in volume, ∆v Original volume, vo V ℮= Vo But ∆v is given as; ∆v = Vf – Vo = Vo (1 – 2ν) E Hence ℮= (1– 2ν) E = ε (1– 2ν) If there are stresses σx, σy and σz acting in each of the three coordinate directions, then ( x y z ) ℮= (1– 2ν) E The quantity ℮ is also known as Dilatation or Volumetric Strain. As the bar is loaded along each of the three coordinate axes, the total strains in the bar in the respective directions will be given as; 1 x ( x y z ) E 1 y ( y x z ) E 1 z ( z x y ) E If the body is subjected to three mutually perpendicular stresses of equal intensity (σx = σy = σz = σ), then the ratio of the direct stress (σ) to the corresponding volumetric strain (e) is known as Bulk Modulus. It is usually denoted by K. Direct Stress K = Volumetric Strain 14 = V Vo The Bulk Modulus is related to Modulus of Elasticity (E) as; E K = 3(1 2 ) Example 1.7 A bar of circular cross-section is loaded by tensile forces P = 85 kN. The bar has length L = 3.0 m and diameter, D = 30 mm. It is made of aluminum with Modulus of Elasticity E = 70 GPa and Poisson’s ratio, ν = 1/3. Calculate the elongation δ, the decrease in diameter ∆d, and the increase in volume ∆V of the bar. Assume the proportional limit of the material is not exceeded. Example 1.8 A steel pipe of length L = 1.2 m, outside diameter d2 = 150 mm, and inside diameter d1 = 110 mm is compressed by and axial force P = 620 kN. The material has modulus of elasticity E = 200 GPa and Poisson’s ratio ν = 0.3. Determine the following quantities for the pipe: (a) the shortening δ (b) the lateral strain (c) the increase ∆d2 in the outer diameter and the increase ∆d1 in the inner diameter (d) the increase ∆t in the wall thickness (e) the increase ∆V in the volume of the material and, (f) the dilation ℮. 15 1.8 Strain Energy As a tensile specimen extends under load, the forces applied to the ends of the test specimen move through small distances. These forces perform work in stretching the bar. To evaluate the work done by the load we use the load deflection diagram. Load P ∆P1 L P1 δ1 δ1+ dδ1 δ Elongation Fig. 1.8 Load – deflection diagram for a bar Consider a bar of length, L subjected to a variable tensile force P. The bar gradually elongates as the load is applied eventually reaching its maximum elongation δ at the same time the load reaches it full value P. Thereafter the load remains at a constant value. During the loading process, the load moves through the distance δ. Let us denote by P1, any value of the load between zero and the maximum value P; the corresponding elongation of the bar is denoted by δ1. Then an increment ΔP1, in the load will produce and increment dδ1 in the elongation. The area of the shaded strip represents the work done by P1 during this incremental elongation P1dδ1. The total work done, W by the load as its value P1, varies from zero to the maximum value P and as δ1 varies from zero to the maximum elongation δ, is the summation of all such elemental strips: W = ∫ Pdδ I.e. The work done by the load is equal to the area under the load deflection curve. The application of the load produces strains in the bar. The effect of these strains is to increase the energy level of the bar. If the limit of proportionality of the material is not exceeded, the work done in extending the bar is stored as strain energy, which is directly recoverable on the removal of the load. Hence the strain energy is defined as the energy absorbed by the bar during the loading process. The strain energy is denoted by U and is equal to the work done by the load provided no energy is added or subtracted in the form of heat. 16 U = W = ∫ P1dδ1 ----------------- (I) The strain energy is sometimes referred to as internal work to distinguish it from external work, W. PL δ= ----------------------- (a) EA Rearranging (a), we have; EA P= ----------------------- (b) L Substituting equation (b) into ( I ), gives U = W = ∫ (δEA/L) dδ EA L = d EA 2 U= ----------------------- (I*) 2L In terms of P, P2L U= ----------------------- (I**) 2EA In terms of σ, 2 AL U= ----------------------- (I***) 2E In terms of ε, E 2 AL U= ----------------------- (I****) 2 AL = V is the original volume of the bar so that the strain energy per unit volume (u) is given by; 2 u= ------------------------ (K) 2E The strain energy per unit volume of a material is also called the strain energy density or Resilience. The resilience of a material is its capacity to absorb potential energy within the elastic range. The strain energy density is equal to the area under the stress– strain curve from the origin to the point on the curve representing the stress σ and the strain ε. The strain energy density when the material is stressed to the proportional limit is called the Modulus of Resilience and is denoted by ur. It is found by substituting the proportional limit stress σPL into the equation (K) and this gives; 17 ur PL 2 —— (Modulus of Resilience) 2E Note: The Modulus of Resilience is equal to the area under the stress – strain curve up to the proportional limit. Toughness: It refers to the ability of the material to absorb energy without fracturing. Hence the Modulus of Toughness (ut ) is the strain energy density when the material is stressed to the point of failure. It is equal to the area under the stress-strain curve. Example 1.9 Calculate the strain energy of the bolt shown in the figure below under a tensile load of 10 kN. Show that the strain energy is increased, for the same maximum stress by turning down the shank of the bolt to the root diameter. 50 mm 25 mm 10 kN 10 kN 16.6mm 20 mm Take E = 205000 N/mm2. Example 1.10 A round bar having the length L but different shapes is shown below. The bar has diameter d over one-fifth of its length and 2d elsewhere. It is subjected to axial load P. Find the strain energy stored in the bar. 2d L d L/5 P 18 Problems 1 1.1 Figure 1.1 shows one end of a beam resting upon a bearing pad made of a rubber compound and which is 250 mm square in plan area. If the vertical reaction at the end of the beam is 3000 kN, calculate the compressive stress in the bearing pad. [Ans: – 48.0 N/mm2] 250 mm Fig. 1.1 1.2 A metal bar ABC having two different cross-sectional areas is loaded by an axial force P (Figure 1.2). Parts AB and BC are circular in cross-section with diameters 50 mm and 38 mm, respectively. If normal stress in part AB is 40 MPa, what is the normal stress σBC in part BC? [Ans: 69.3 MPa] Fig. 1.2 1.3 Calculate the compressive stress σc in the piston rod (Figure 1.3) when a force P = 40 N is applied to the brake pedal. (Note that the line of action of the force P is parallel to the piston rod. Also the diameter of the piston rod is 5 mm, and the other dimensions shown in the figure are measured perpendicular to the line of action of the force P.) [Ans: 11.2 MPa] Fig. 1.3 19 1.4 A compression member 0.3 m long has a rectangular cross section 150 mm by 100 mm. It passes through a slot in a rigid block as shown in Figure 1.4 such that there is complete restraint in the x direction. Therefore no change of dimension can take place in the x direction. There is however no restriction of movement in the y direction. If a load of 3800 kN is applied to the member as shown. Calculate: (i) the stress in the x direction (ii) the strain in the z direction (iii) the strain in the y direction Assume that E = 200 kN/mm2 and Poisson’s ratio ν = 0.3. [Ans: – 76.0 N/mm2, – 1.153 x 10-3, 0.494 x 10-3] Fig. 1.4 1.5 A specimen of a metharcrylate plastic is tested in tension at room temperature (Figure 1.5), producing the stress-strain data listed in the accompanying table. Plot the stress – strain curve and determine the proportional limit, modulus of elasticity and yield stress at 0.2 % offset. Is the material ductile or brittle? [Ans: σpl ≈ 47 MPa, E ≈ 2.4 GPa, σy ≈ 53 MPa, Brittle] Stress-strain Data for 1.5 Stress (MPa) Strain 8.0 0.0032 17.5 0.0073 25.6 0.0111 31.1 0.0129 39.8 0.0163 44.0 0.0184 Fig. 1.5 48.2 0.0209 53.9 0.0260 58.1 0.0331 62.0 0.0429 62.1 fracture 20 1.6 A high -strength steel wire, 3.2 mm diameter, stretches 35 mm when a 15 m length of it is stretched by a force of 3800 N. (a) What is the modulus of elasticity E of the steel? (b) If the diameter of the wire decreases by 0.0022 mm, what is Poisson’s ratio? (c) What is the unit volume change for steel? [Ans: 202.8 GPa, 0.3, 932 x 10-6 (increase)] 1.7 A prismatic bar is loaded in tension by axial forces. Find Poisson’s ratio for the material if the ratio of the unit volume change to the unit change in cross-sectional area is equal to – 2/3. [Ans: 3/10] 1.8 A flexible string of length Ls = 1.4 m is fastened to supports at points A and B (Figure 1.8). Points A and B are at different elevations, with B being lower than A. The horizontal distance L between the supports equals 1.2 m. A load P hangs from a small roller that slides without friction along the string until it comes to rest in the equilibrium position at C. If the string has a breaking strength F = 160 N, and if a factor of safety S = 2.5 is required, what is the allowable load P? [Ans: 65.9 N] L A B C P Fig. 1.8 1.9 A bar 3 m long is made of two bars, one of copper having E = 105 GN/m2 and the other of steel having E = 210 GN/m2. Each bar is 25 mm broad and 12.5 mm thick. This compound bar is stretched by a load of 50 kN. Find the increase in length of the compound bar and the stress produced in the steel and copper. The length of copper as well as steel is 3 m each. [Ans: 1.52 mm, 106 MPa, 53 MPa] 21 CHAPTER TWO AXIALLY LOADED SPRINGS/ BARS This chapter is devoted to the behaviour of axially loaded members, which are structural elements having straight longitudinal axes and carrying only axial forces (tensile or compressive). Their cross-sections may be solid, hollow or tubular or thin-walled and open. 2.1 Displacement of Axially Loaded Members An axially loaded spring is analogous to a bar in tension. Consider a spring axially loaded by a force P. P Under the action of the force, P, the spring elongates by an amount δ so that its total length becomes (L+ δ), where L is the original length. The spring constant, K is given as; K = P/ δ The compliance of the spring is the reciprocal of the spring constant or the deflection produced by a load of unit value and is given as f = δ/P The terms stiffness and flexibility are commonly used rather than spring constant and compliance in structural analysis. The stiffness, K of an axially loaded bar below is defined as force required to produce a unit deflection, hence stiffness of the bar, K is; P EA K= L P The flexibility, f is defined as the deflection given to a unit load. Thus the flexibility of an axially loaded bar is L f= EA A prismatic bar of length L is loaded in tension by axial forces P as shown in Figure 2.1. The uniform stress is given by the equation σ = P/A and the axial strain is ε = δ/ L. Assuming Hooke’s law is being obeyed then σ = Eε. The above expressions are combined to give the following equation for the elongation of the bar: 22 PL δ= EA L δ P P Fig. 2.1 Axially loaded bar in tension Thus when a prismatic bar of linearly elastic material is loaded only at the ends, we can obtain its change in length from the above equation. Suppose, that a prismatic bar is loaded by one or more axial loads acting at intermediate points along the axis of the bar Figure 2.2 and 2.3. A P1 a P1 A B b a C P2 B P2 c b D P3 C Fig. 2.2, 2.3 Bar with intermediate axial loads/ Bar consisting of prismatic bars We can determine the axial force in each part of the bar (that is in part AB, BC, and CD, say, by statics). We then calculate the elongation or shortening of each part separately. Finally, the changes in lengths can be added algebraically to obtain the total elongation. This method can be used if the bar consists of several prismatic segments, each having different axial forces, different dimensions, and different materials. The change in length may be obtained from the equation n Pi L i δ= E A i 1 i i In which the subscript i is a numbering index for the various segments of the bar. Note especially that Pi is not an external load but is the internal axial force in segment i. If either the axial force or cross-sectional area varies continuously along the axis of the bar, the above equation is not suitable. Instead the elongation can be found by considering a differential element of the bar, obtaining an expression for its elongation and then integrating over the length of the bar. 23 Consider a tapered bar shown in Figure 2.4(a). The bar is subjected to a continuously distributed load, as shown by the arrows in the Figure. A B A C B P P L x dx Fig. 2.4a Fig. 2.4b A continuous axial load of this kind may be produced by centrifugal forces, magnetic forces or the weight of a bar hanging vertically. Now consider any intermediate cross-section C, at a distance x from the left- hand end (Figure 2.4b). The internal axial force P(x) acting at this section may be determined from static equilibrium using part of the bar AC or CB as a free body. Thus the force P(x) is known in terms of x. Also the cross-sectional area A(x) at section C may be expressed as a function of x. Next we consider an element of the bar of length dx at section C, the elongation dδ of this element may be obtained as follows; P( x )dx dδ = EA( x ) The elongation of the entire bar is obtained by integrating over the length L as; P( x )dx δ = d EA(x) This same procedure is applied to a prismatic bar hanging vertically under its own weight, Figure 2.5. A x dx L B Fig. 2.5 A bar hanging vertically under its own weight The elongation of the entire bar AB is given as; P( x)dx δ= EA 24 Example 2.1 A steel bar 2.5 m long has circular cross-section of diameter d1 = 20 mm over one-half of its length and diameter d2 = 13 mm over the other half. (a) How much will the bar elongate under a tensile load P = 22 kN? (b) If the same volume of the material is made into a bar of constant diameter d and length 2.5 m, what will be the elongation under the same load P? (Assume E = 210 GPa). d1= 20 mm d2 = 13 mm P P = 22 kN 1.25 m 1.25 m Example 2.2 A steel bar AD (see figure) has a cross-sectional area of 260 mm2 and is loaded by forces P1 = 12 kN, P2 = 8 kN, and P3 = 6 kN. The lengths of the segments of the bar are a = 1.5 m, b = 0.6 m, and c = 0.9 m. (a) Assuming that the modulus of elasticity E = 210 GPa, calculate the change in length δ of the bar. Does the bar elongate or shorten? (b) By what amount P should the load P3 be increased so that end D of the bar does not move when the loads are applied? P1 P2 P3 A B C D a b c 25 2.2 Statically Indeterminate Structures/ Bars In the preceding section we deal with axially loaded bars and other simple structures that could be analysed by static equilibrium. Such structures are classified as statically determinate. For many structures, however, the equations of static equilibrium alone are not sufficient for the calculation of axial forces and reactions in the members; these structures are called statically indeterminate. Structures of this type can be analysed by supplementing the equilibrium equations with additional equations pertaining to the displacement of the structure. Consider a prismatic bar AB of cross-sectional area A attached to rigid supports at both ends and axially loaded by a force P at an intermediate point C (Figure 2.6a). From the free-body diagram Figure 2.6b, the reactions RA and RB cannot be found by statics alone, because only one equation of equilibrium is available. RA A A P a P C C L b B B RB Fig. 2.6a Fig. 2.6b ∑Fvert = 0 RA + RB − P = 0 --------------------- (1) We need an additional equation to be able to solve for the two unknowns. This equation is obtained based on the observation that a bar with both ends fixed does not change in length. That is δAB = 0. --------------------------- (2) This also means that the total change in length of the bar caused by the three forces is zero. This equation is called Compatibility Equation expressing the fact that the change in length of the bar must be compatible with the conditions at the supports. Considering Figure 2.6b, the changes in lengths of the upper and lower segments of the bar are respectively, R Aa R Bb δAC = and δCB = − EA EA 26 where the minus sign indicates a shortening of the bar. Equation (2) now becomes: R Aa R b δAB = δAC + δCB = B 0 EA EA Or R Aa R Bb 0 ---------- (3) EA EA We now solve simultaneously equations (1) and (3) to get; Pb Pa RA = and RB = L L With the reactions known, all other forces and displacement equations can be found. Stresses in the two segments of the bar can also be found directly from the internal axial forces. Note: The analysis of structurally indeterminate structures involves setting up and solving equations of equilibrium and equations of compatibility. Example 2.3 The axially loaded bar ABCD shown in the figure is held between rigid supports. The bar has cross-sectional area Ao from A to C and 2Ao from C to D. (a) Obtain formulars for the reactions RA and RD at the ends of the bar. (b) Determine the displacement δB and δC at points B and C respectively. Ao 2Ao P A B C D L/4 L/4 L/2 27 2.3 Strain Energy The strain energy of an axially loaded bar of a linearly elastic material is given as P2L U= ---------------------- (1) 2EA For linearly elastic spring the strain energy is obtained by replacing the stiffness EA/L of the prismatic bar by the stiffness k of the spring, and is given as; P2 U= 2K The total strain energy U of a bar consisting of several segments is equal to the sum of strain energies of the individual segments. Considering Figure 2.7, the total strain energy is the strain energy of segment AB plus the strain energy of segment BC. A P1 B C P2 Fig. 2.7 Bar consisting of prismatic segments having different cross-sectional areas and different axial forces Therefore for a bar of any prismatic segment and constant internal axial force within each segment, and made up of different materials, the total strain energy is given as; n Pi2 L i U= i 1 2E i A i in which Pi is the axial force acting in segment i and Li, Ei and Ai are properties of segment i. For a non-prismatic bar – Figure 2.8 with continuously varying axial force, equation (1) is applied to a differential element shown in the figure and integrating along the length of the bar gives the strain energy of the bar as; P( x ) 2 dx L U= 0 2EA( x ) 28 P(x) and A(x) are the axial force and cross-sectional area at distance x from the end of the bar. A dx L B P Fig. 2.8 Non-prismatic bar with varying axial force The same procedure is applied to a bar hanging vertically under its own weight. For such a bar – Figure 2.9, the strain energy is also given as; P( x ) 2 dx L U= 0 2EA( x ) x L dx Fig. 2.9 Bar hanging vertically under its own weight Example 2.4 The bar ABC shown in the figure is loaded by a force P acting at end C and by a force Q acting at the midpoint B. The bar has constant axial rigidity EA. (a) Determine the strain energy U1 of the bar when the force P acts alone (Q = 0). (b) Determine the strain energy U2 when the force Q acts alone (P = 0). 29 (c) Determine the strain energy U when the forces P and Q act simultaneously upon the bar. Q P A L/2 B L/2 C Example 2.5 Determine the strain energy stored in a bar suspended from one end due to its own weight. Assume linear elastic behaviour. 2.4 Pre-Stress or Strain (Initial Stress) Sometimes, it happens that before any load is applied to any part of a machine or structure, it is already in state of stress. For example, the bolts holding down the heads of the cylinder of a steam engine are put into tension by tightening up the units. The same applied to the bolt in a flanged coupling of a steam pipe, or the big end bolts of the connecting rod. In some cases, relative rigidity of the bodies has to taken into account while in others it is not taken into account. For example in the case of a cylinder head, there will be little deformation, under the pressure, of nuts compared with the deformation of the bolts, so that the head can be treated as rigid and the stress in the bolt when there is steam in the cylinder will be the same as the initial stress before steam come to the cylinder. On the other hand, in dealing with flanged joints, the elasticity of the packing must be considered. Any tension applied to the joints will be taken up partly by extra tension in the bolt and partly by reduced compression in the packing. 30 Problems 2 2.1 A high strength steel rod with diameter d = 25 mm and modulus of elasticity E = 200 GPa must transmit a tensile load P = 134 kN. a) If the length L of the rod is 1 m, what is its final length? b) What is the ratio of the length of the rod to the increase in length? c) If the increase in length is limited to 3.8 mm, what is the maximum load Pmax that can be permitted? d P P L [1.00136m, 735, 373.4] 2.2 A prismatic bar AD is subjected to loads P1, P2, and P3 acting at points B, C, and D, respectively, as shown in the figure. Each segment of the bar is 500 mm long. The bar has cross-sectional area A = 900 mm2 and is made of copper with E = 120 GPa. a) Determine the displacement δD at the free end of the bar. b) What should be the load P3 if it is desired to reduce the displacement at end D to half of its original value? P1 = 13 kN P2 = 13 kN P3 = 50 kN A 500 mm B 500 mm C 500 mm D [0.755 mm, 22.8 kN] 2.3 A bar ACB having two different cross-sectional areas A1 and A2 is held between rigid supports at A and B. A load P acts at point C, which is distance b1 from end A and b2 from end B. a) Obtain formulars for the reactions RA and RB at supports A and B, respectively due to load P. b) Obtain a formular for the downward displacement δC of point C. 31 AP A1 b1 C A2 b2 B b 2 A1P b1 A 2 P b1 b 2 P [RA = , RB = , δC = ] b1 A 2 b 2 A 1 b1 A 2 b 2 A 1 E ( b1 A 2 b 2 A 1 ) 2.4 A bar AD of length L, cross-sectional area A, and modulus of elasticity E is subjected to loads 5P, 3P, and P acting at points B, C, and D, respectively. Segments AB, BC, and CD have lengths L/6, L/2, and L/3, respectively. a) Obtain a formular for the strain energy U of the bar. b) Calculate the strain energy if P = 21 kN, L = 1.2 m, A = 1,780 mm 2, and the material is aluminium with E = 72 GPa. 5P 3P P A B C D L/6 L/2 L/3 23P 2 L [U = , 8 kJ] 12EA 2.5 Determine the strain energy in a bar suspended from one end if in addition to its own weight, it supports a load P at the lower end. 32 2.6 The truss ABC shown in the figure supports a horizontal load P 1 = 9 kN and a vertical load P2 = 18 kN. Both bars have cross-sectional area A = 1,290 mm2 and are made of steel with E = 210 GPa. a) Determine the strain energy U1 of the truss when the load P1 acts alone (P2 = 0). b) Determine the strain energy U2 when the load P2 acts alone (P1 = 0). c) Determine the strain energy U when both loads act simultaneously. A 813 mm C B P1 = 9 kN P2 = 18 kN 1524 mm [U1 = 5.69 J, U2 = 191.62 J, U = 155.55 J] 33 CHAPTER 3 TEMPERATURE AND SHEAR STRESSES 3.1 Temperature Stresses External loads are not the only sources of stresses and strains in a structure. When the temperature of a body is raised or lowered the material expands or contracts. If the expansion and contraction is wholly or partially restricted stresses and strains are set up in the structure. Consider a long bar AB of a material – Figure 3.1 at a temperature θo. The bar is now subjected to an increase ∆θ in temperature. A B Fig. 3.1 A bar of material subjected to an increase in temperature As the bar is unrestrained, when it is heated, every element of the material will undergo thermal strains in all directions resulting in increase in the dimensions of the bar. If A is taken as the reference point and side AB maintained its original position, the block will have the shape shown by the dashed lines. For most homogeneous structural materials if the temperature changes the uniform thermal strains εt undergone by the materials is seen to be proportional to the temperature change ∆θ. The strain is thus give as εt = α (∆θ) ---------------------- (1) α is a property of the material known as the coefficient of thermal expansion or coefficient of linear expansivity. α has unit of 1/K or 1/ oC. Conventionally the thermal strain resulting from expansion is taken to be positive and that resulting from contraction is taken to be negative. If the expansion of the bar is prevented, it is as if the bar is compressed to its original shape and dimensions above. The compressive strain is given by equation 1 above. The corresponding stress is; σ = Eε = α E (∆θ) By a similar argument the tensile stress set up in a constrained bar subjected to a temperature difference ∆θ is given as σ = α E (∆θ) It is assumed that the material remains elastic. 34 3.1.1 Change in Length of Unrestrained Bar Consider a prismatic bar of length L (Figure 3.2) subjected to a temperature difference ∆θ. δt is the elongation of the bar due to the temperature change ∆θ. ∆θ L δt Fig. 3.2 Increase in length of a prismatic bar subjected to temperature change ∆θ. If the bar is homogeneous and isotropic and the temperature increase is uniform throughout the bar, the increase in length δt is given by δt = εtL = α (∆θ) L Thus the change in any dimensions of the bar can be obtained by multiplying the original dimensions by the thermal strain. For a bar of length L subjected to a temperature increase ∆θ, the increase in length is δ t and therefore the final length Lf becomes, Lf = L + δt = L + α (∆θ) L = L [1 + α (∆θ)] Example 3.1 A steel bar of length 200 mm is at a temperature of 10 oC. If the material properties are; E = 210 GPa and α = 12 x 10-6/K. Find: i The thermal strain induced in the bar ii The new length of the bar when it is heated to 23 oC. Example 3.2 A 150 mm diameter steam pipe is laid in a trench at a temperature of 13oC. When steam passes through the pipe, its temperature rises to 120oC; (a) What is the increase ∆d in the diameter of the pipe if the pipe is free to expand in all directions? (b) What is the axial stress σ in the pipe if the trench restrains the pipe so that it lengthens only one-third as much as it would if it could expand freely? (Note: The pipe is made of steel with modulus of elasticity E = 200 GPa and coefficient of thermal expansion α = 12 x 10-6 /oC.) 35 3.1.2 Statically Indeterminate Bars In the previous discussion the bars and structures considered are free to expand or contract. There are, however, certain structures that can be restrained and depending on their character and nature of the temperature changes may or may not develop temperature stresses. The analysis of statically indeterminate structures that develop temperature stresses is analysed by establishing equilibrium equations, compatibility equations- temperature displacement relations together with force- displacement relations. Consider a prismatic bar AB (Figure 3.3a) of linear elastic material, rigidly constrained at the two ends and subjected to a temperature difference of ∆θ. Figure 3.3b is a free-body diagram of Figure 3.3a and 3.3c, 3.3d are the increase and the decrease in the length of the bar due to temperature change ∆θ and external load RA respectively. RA RA A A A δt A δRA ∆θ L L ∆θ B B B B RB Fig. 3.3a Fig. 3.3b Fig. 3.3c Fig. 3.3d As the temperature is raised the bar tends to elongate but is restrained by the supports A and B. Consequently reactions RA and RB are developed at the supports and the bar is subjected to compressive stresses. Considering Figure 3.3b, the equilibrium equation is determined as; ΣFvert = 0, RA – RB = 0 --------------- (1) The compatibility equation is given as; δAB = 0 In Figure 3.3c, when only the temperature change is acting, the bar elongates by an amount δt. In Figure 3.3d when only the reaction RA acts the bar shortens by an amount δRA. The compatibility equation then becomes δAB = δt – δRA = 0 R AL = α (∆θ) L – 0 --------- (2) EA 36 Solving equations (1) and (2) gives RA = RB = EAα (∆θ) From which the thermal stresses σt can be obtained. RA RB I.e. σt = = E α (∆θ) A B Example 3.3 A composite bar made up of aluminum bar and steel bar, is firmly held between two unyielding supports as shown in figure below. B Steel C A Aluminium 200 kN 1000 mm2 1500 mm2 100 mm 150 mm An axial load of 200 kN is applied at B at 47 0C. Find the stress in each material, when the temperature is 97 0C. Take Ea = 70 GPa; Es = 210 GPa; αa = 24 x 10-6/ 0C and αs =12 x 10-6/ 0C. 3.1.3 Creep of Materials under Sustained Stresses At ordinary temperatures, most metals will sustain stresses below the limit of proportionality for long periods without showing additional measurable strains. At these temperatures metals deform continuously when stressed above the elastic range. This process of continuous inelastic strain is called creep. At high temperatures metals lose some of their elastic properties and creep under constant stress takes place more rapidly. Strain Primary Secondary Tertiary c a b Fracture εo Instantaneously Plastic Time Fig. 3.4 Creep Curve for a Material in the Inelastic Range 37 When a tensile specimen of a metal is tested at a high temperature under a constant load, the strain assumes instantaneously some values εo; if the initial strain is in the inelastic range of the material then creep takes place under constant stress. At first, the creep rate is fairly rapid but diminishes until a point (b) is reached on the strain –time curve. The point ‘b’ is a point of inflexion in this curve, and continued application of the load increases the creep rate until fracture of the specimen occurred at ‘c’. 3.1.4 Fatigue under Repeated Stresses When a material is subjected to repeated tensile stresses within the elastic range, it is found that the material tires and fractures rather suddenly after a large but finite number of repetitions of stress; the material is said to fatigue. σ 50 Endurance Limit 40 Medium strength 30 Titanium alloy 20 Mild Steel 10 Aluminium light alloy 104 105 106 107 108 109 No. of cycles to failure Fig. 3.5 Forms of the stress-endurance curve for steel, aluminium light alloy and titanium alloy. The endurance to fatigue at a given stress level is the number of complete cycles of loading to that stress level required to bring about fracture of the materials. Failure of the material after a large number of cycles of tensile stress occurs with little or no permanent set. Fractures show the characteristics of brittle materials. Fatigue is primarily a problem of repeated tensile stresses; this is due, probably, to the fact that microscopic cracks in a material can propagate more easily when the material is stressed in tension. In the case of steels, it is found that there is a critical stress called the endurance limit below which fluctuating stresses cannot cause a fatigue failure. Titanium alloys show a similar phenomenon. No such endurance limit has been found for other non-ferrous metals and other materials. 38 3.2 Shearing Stresses A part from the direct stresses (tensile and compressive stresses), and thermal stresses, there is another type of stress which plays a vital role in the behaviour of the materials and structures, especially metals. This stress acts parallel or tangential to a surface. Consider a thin block of a material, which is glued to a table. Suppose a thin plate is now glued to the upper surface of the block (Figure 3.6). Thin plate P A B Block of material Fig. 3.6 A block glued to a table on top of which is glued a thin plate If a horizontal force P is applied to the plate, the plate will tend to slide along the top of the block of the material, and the block itself will tend to slide along the table. So that, provided the glued surfaces remain intact, the table resists the sliding of the block, and the block resists the sliding of the plate on its upper surface. This is equivalent to applying two equal and opposite parallel forces not in the same line to two parts of a structure. There is a tendency for one part of the body to slide over or shear from the other part across any section. Assuming the block is to be divided by any imaginary horizontal plane such as AB, the part of the block above this plane will be trying to slide over the part below the plane. The material on each side of this plane is said to be subjected to a shearing action, the stresses arising from these actions are called Shearing Stresses. Shear stress is denoted by the symbol τ (thaw), and shearing stress on any surface is defined as the intensity of shearing force tangential to the surface. The average shear stress is obtained by dividing the total shear force V by the area A over which it acts. V τ= A In many cases, the shear force is not distributed uniformly over the section; if δV is the shear force on any elemental area δA of a section, the shear stress on that elemental area is; lim V τ= A 0 A Shear stress arises in many practical problems. For example, Figure 3.7 (a) shows two flat plates held together by a single rivet and carries a tensile force P. 39 P a b P Fig. 3.7 (a) A rivet in a single shear We imagine the rivet divided into two portions by the plane ab, then the upper half of the rivet is tending to slide over the lower half, and a shearing is set up in the plane ab. The shearing takes place at one cross-section of the rivet. The rivet is therefore said to be in a single shear. Figure 3.7 (b) shows three flat plates held together by a single rivet and carry a tensile force P. P/2 a b c d P P/2 Fig. 3.7 (b) A rivet in double shear In the above diagram, shearing takes place over two cross-sections of the rivet. That is in plane ab and in plane cd. The rivet is therefore said to be in double shear. Example 3.3 A punch of diameter 19 mm is used to punch a hole in a 6 mm steel plate. A force P= 116 kN is required. What are the average shear stress in the plate and the average compressive stress in the punch? Example 3.4 Three steel plates are held together by a (sixteen) 16 mm diameter rivet. If the load transmitted is 5 kN, estimate the shear stress in the rivet. 2.5 kN a b c d 5 kN 2.5 kN 40 3.2.1 Complementary Shearing Stress Consider now the equilibrium of one of the elementary blocks of a rectangular block in a state of shear – Figure 3.8. τyx τxy b τxy τyx a Fig. 3.8 An elementary block in a state of shear Let τyx be the shear stress on the horizontal face of the element and τxy, be the shear stress on the vertical faces of the element. Suppose ‘a’ is the length of the element and ‘b’ its height and that it has unit breath. The total shear force on the upper and lower faces is then aτyx while the total shear forces on the end faces bτxy, so that for rotational equilibrium; aτyx b = bτxy a or τyx = τxy This implies that whenever there is a shearing stress over a plane passing through a given line, there must be an equal complementary shearing stress on a plane perpendicular to the given plane and passing through the given line. The direction of the two shearing stresses must be either both towards or both away from the line of intersection of the two planes in which they act. NOTE: In direct stress there is a change in volume but in shear there is no change in volume. An element subjected to shear stresses only is said to be in pure shear. 41 3.3 Shear Strain τ γ τ Consider a rectangular block of material, subjected to shear stresses τ in one plane. The shearing stresses distort the rectangular face of the block into a parallelogram as shown above. If the right angles at the corners of the faces change by amounts γ, then γ is the shear strain. The shear strain γ can be defined as the change in the right angle. S I G N C O N VE N T I O N The shear stress acting on a positive face of an element is positive if it acts in the direction of one of the coordinate axes and negative if it acts in the negative direction of the axis. The shear stress acting on a negative face of an element is positive if it acts in the negative direction of an axis, and negative if it acts in the positive direction of an axis. Positive shear stress Negative shear stress The sign convention for shear strain is related to that of shear stresses. Shear strain in an element is positive when the angle between two positive or (two negative) faces is reduced. The strain is negative when the angle between two positive or (two negative) faces is increased. Positive shear strain Negative shear strain 42 NOTE: A face is said to be positive if it has its outward normal directed in the positive direction of a coordinate axis. The opposite faces are negative faces. +ve face y – ve face +ve face x – ve face 3.4 Relationship between Shear Stress and Shear Strain The τ versus γ diagram is similar in shape to the σ versus ε diagram. For many materials the initial part of the shear stress–strain diagram is a straight line. Within the linear elastic region, the shear stress and shear strain are directly proportional. That is; τ=Gγ where G is the shearing modulus of elasticity (Modulus of Rigidity). G is the ratio of the shear stress to the shear strain, and it is also the slope of the linear portion of the shear stress- strain diagram. E G is related to E as: G 2 1 3.5 Shear Strain Energy For a member in pure shear the shear strain energy is given as; 1 U= G γ2 x Volume of the material 2 The shear strain per unit volume also known as the Shear Resilience is given as; 1 U= G γ2 2 43 3.6 Bearing Stresses A localized compressive stress at the surface of contact between two members of a machine part that are relatively at rest is known as bearing stress. It is used in the design of riveted joints, knuckle joints et ce tera. F d t F The bearing stress between the two members is given as; F b dtn t = plate thickness d = rivet diameter n = number of rivet per pitch length Example 3.5 A 15-mm-diameter steel rod AB is fitted to a round hole near end C of the wooden member CD. For the loading shown, determine: (i) The maximum average normal stress in the wood, (ii) The distance b for which the average shearing stress is 500 kPa on the surface indicated by the dashed lines, (iii) The average bearing stress in the wood. 44 Problems 3 3.1 Find the minimum size of a hole that can be punched in a 20 mm thick mild steel plate having ultimate shear strength of 300 N/mm2. The maximum permissible compressive stress in the punch material is 1200 N/mm2. [20 mm] 3.2 A block of wood is tested in direct shear using the loading frame and test specimen shown in the figure. The load P produces shear in the specimen along plane AB. The height h of plane AB is 50 mm and its width (perpendicular to the plane of the drawing) is 100 mm. If the load P = 16 kN, what is the average shear stress τaver in the wood? P = 16 kN Testing frame A h = 50 mm B [3.2 MPa] 3.3 A solid circular bar of aluminum fits inside a tube of copper having the same length (Figure Q3.3). The outside diameter of the copper tube is 50 mm and the inside diameter is 45 mm. The diameter of the aluminum bar is 42 mm. At each end of the assembly, a metal pin of 8 mm diameter goes through both bars at right angles to the axis. Find the average shear stress in the pins if the temperature is raised 20 oC. (For aluminum, Ea = 70GPa and αa = 23 x 10-6 /oC; for copper, Ec = 120 GPa and αc = 17 x 10-6 /oC). Pin Copper tube Aluminum bar Fig. Q3.3 [36.6 MPa] 45 3.4 A plastic bar ACB having two different solid circular cross sections is held between rigid supports as shown in Figure Q3.4. The diameters in the left- and right- hand parts are 50 mm and 76 mm respectively. The corresponding lengths are 230 mm and 300 mm. Also, the modulus of elasticity E is 6 GPa, and the coefficient of thermal expansion α is 100 x 10-6 /oC. The bar is subjected to a uniform temperature increase of 50 oC. Calculate the following quantities: (a) The compressive force P in the bar; (b) The maximum compressive stress σc; and (c) The displacement δc of the point C. 50 mm 76 mm A C B 230 mm 300 mm Fig. Q3.4 [86.885 kN; 44.26 MPa; – 0.544 mm (to the left)] 3.5 A flexible connection consisting of rubber pads (thickness t = 10 mm) bonded to steel plates is shown in Figure Q3.5. The pads are 200 mm long and 150 mm wide. (a) Find the average shear strain γaver in the rubber if the force P = 15 kN and the shear modulus for the rubber is G = 800 kPa. (b) Find the relative horizontal displacement δ between the interior plate and the outer plates. 200 mm X Rubber pad P/2 P P/2 X Rubber pad 150 mm t = 10 mm t = 10 mm Section X-X Fig. Q3.5 [0.313; 3.13 mm] 46 CHAPTER 4 CENTROIDS AND MOMENT OF INERTIA 4.1 Centroids of Shapes A body or structure consists of parts each subjected to its own weight force. These forces are vertical and parallel to each other. These forces may be replaced by a single vertical resultant of magnitude equal to the total weight of the body and acting at the centre of gravity of the body. This section is, therefore, concerned with locating the portion of the centre of gravity or centroids of plane areas or geometric figures. 4.1.1 Centroids of Areas by Integration To obtain formulas for locating of centtroids, we consider an irregular shaped plate of material of uniform thickness and having centre of gravity at C. We take the coordinate axes intersecting at point O as shown. y x C dA y y x O x δA is a differential element of area having coordinates x and y from y and x axes respectively. Let A be the total area of the irregular shape, that is A = dA First moment of area with respect to the x and y axes are defined as Qx = ydA , Qy = xdA For the whole figure, we can write _ Qx = y dA ; Qy = x dA 47 x= xdA xdA = -------------------- (a) dA A y= ydA ydA = ------------------- (b) dA A Equations (a) and (b) are the formulas used in obtaining the coordinates of the centroids of geometric figures. In general, the coordinates x and ȳ may be positive or negative depending upon the position of the centroid with respect to the reference axes. Example 4.1 Find the centroid of the triangle shown below y h O x b A table of centroids for a variety of shapes is given in some text books and handbooks. Some examples are shown below. y y y r c c h c r x x x b b For the above figures the centroids coincide with the geometric centres. 48 y y y y 34r y 34r r c r cr c x x x x=0 x= d 2 y 34r ; x= 4r For semi-circles For a quarter circle 3 4.1.2 Centroid of Composite Areas Composite area is the one made up of a number of simple areas. To determine its centroid, composite area is general divided into two or more simple component areas each area having a familiar geometric shape. The centroid of the composite area is then found by the following principle: About any axis, the moment of area equals the algebraic sum of the moment of its component areas. If the composite area is divided into n equal parts and the area of the ith part is Ai, then n n n A = Ai ; Qx = y i A i ; x Qy = i Ai i 1 i 1 i 1 Where x i and y i are the coordinates of the centroids of the ith part with respect to the y and x axes respectively. The coordinates of the centroid of the composite area are then; n n Qy x i Ai i 1 Q y i 1 i Ai x n , y x n A A A A i i i 1 i 1 49 4.1.3 Symmetric Areas In most cases obtaining areas of geometric shapes becomes less of a work when the area is symmetric about certain axes. Actually if an area is symmetric about an axis, the centroid must lie on that axis. For the single symmetric areas shown below the centroid must lie on the x-axis which is the line of symmetry and therefore only one coordinate must be calculated to locate the centroid. y y x x X-axis is the symmetry Y-axis is the symmetry If an area has two axes of symmetry the position of the centroid is located by inspection and it lies at the point of intersection of the two axes. y y x x Both x and y are axes of symmetry If an area is symmetric about a point (centre of symmetry) such that every line drawn through that point contacts the area in a symmetrical manner, the centroid of such an area coincides with the centre of symmetry and can be located by inspection. y y C x C x 50 Note: 1. In general the coordinates x and y may be positive or negative depending on the location of the centroid with respect to the coordinate axes. 2. When a composite area is divided into two parts, the centroid C of the entire area lies on the line joining the centroids C1 and C2 of the two parts. See the figure below. y A1 C1 y x x C2 A2 3. For composite areas with absence of areas or with holes or notches or cutouts, they are treated by subtraction or as negative areas. Example 4.2 Determine the position of the centroid C of the area below. y 100 mm 12 mm 100 mm 12 mm x 51 Example 4.3 Find the centroid of the figure below. y r=2m 10 mm x 20 mm 4.2 Moment Of Inertia The second moment of area is known as the moment of inertia. It is the sum of the product of the elemental areas and the square of their distances from the reference axis to its centroid. It is denoted by letter I. For elemental area dA, y dA x 2 2 Ix = ; Iy = dA When