Impression Trays PDF
Document Details
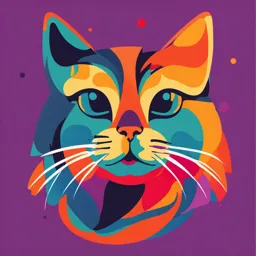
Uploaded by FuturisticOak6451
Alamein International University
Prof. Lucette Segaan
Tags
Summary
This document provides an overview of impression trays, including special trays, custom trays, and materials used in the creation of dental impressions. The content explains custom tray construction methods, advantages of custom trays, and presents different types of materials, such as thermoplastic and resins, used for custom tray construction. It also details the importance of the impression for creating accurate models and patient comfort during the procedure.
Full Transcript
Preclinical prosthodontics Impression Trays Special trays Prof. Lucette Segaan Prosthodontic department...
Preclinical prosthodontics Impression Trays Special trays Prof. Lucette Segaan Prosthodontic department 2-Custom Trays to a Great Final Impression Custom ( special) trays are constructed on the diagnostic cast prior to the final impression appointment. Patient Visit #2 Visit 2 Clinical Lab. procedure procedure Evaluation of final Border molding Boxing/Pouring Master casts impression trays Final impression Record Bases Occlusal Rims 2. Custom trays: (Special trays) Edentulous ridges show wide variations of shape and size. In the same patient the ridge shows different amount of resorption, so a stock tray can only fit such a ridge in a very arbitrary manner. Custom trays are made on preliminary casts (produced from a preliminary impression). They are designed to enable the dentist to make a more accurate and detailed impression than is possible with stock trays. Custom trays are constructed for a specific impression procedure for one patient and they are discarded after use. Advantages of custom trays: It fits accurately the arches of the patient. Less impression material is used. The bulk of the impression material is reduced and accordingly less dimensional changes will be expected and minimum tissue over compression. More comfortable to the patient. General Considerations: 1- Tray outline: The tray outline should follow specific anatomic landmarks, staying approximately 2 mm short of the vestibular depth. When making a final impression, the goal is to make an exact replica of the denture bearing area. (With maximum coverage of supporting tissues and minimal extension into movable tissues and muscle attachments). The impression must be able to be used to create a master cast that will exhibit the same characteristics as the denture bearing area. An exact replica of the tissues will create a denture/tissue interface with intimate contact throughout, which will result in excellent retention, stability, and support of the denture. Tray Extensions The desired extent of the tray should be drawn as an outline: - approximately 2 mm above the depth of the vestibules and muscle or frenulum attachments on the labial, buccal, and lingual. - posterior to the vibrating line on the maxillary arch and to the full extent to the retromylohyoid space on the mandibular arch. 2- Providing Spacer: Custom trays are sometimes provided with a spacer to ensure enough space between the tray and the tissues to allow an even thickness of impression material. The type of impression material used for the final impressions and impression technique determines whether a spacer is needed or not and the thickness of spacer to be used. When zinc oxide-eugenol impression paste is used, a close-fitting tray without spacer is required. When polysulfide rubber, or silicone impression material is used, a single layer of baseplate wax is required. When alginate or plaster are used as a final impression material, a spacer of double thickness of baseplate wax is desirable. When a wax spacer is used, three or four stops will be essential to ensure even thickness of impression material. Custom impression tray materials: ✓The special tray materials vary according to the type of impression technique selected. ✓The materials used should not warp in the mouth. ✓Metallic and plastic materials can be used for the construction of custom trays. Thermoplastic materials and resins are more commonly used for the construction of custom trays as they are easily and rapidly made. 1-Thermoplastic materials: a- Shellac base plate b- Modeling compound c- Hydroplastic tray material 2) Resins: a- self cure(cold cure) b- heat cure c- light cure d- plastic sheets 3- Modified stock trays Stock trays can be modified by cutting, bending, or adding. 4-old denture The old denture of the patient can be used as a custom tray as in case of making zinc oxide eugenol impression for relining of the dentures. 5-Metal Metallic custom trays are produced by casting or swaging methods which is time consuming and expensive. For this reason it is not used anymore. Methods of construction 1- Thermoplastic materials: a- Shellac base plate made from a resinous material that softens upon heating and hardens on cooling. Used when the impression is made from Plaster of Paris or alginate It comes in pink or brown colored sheets of two thicknesses, the single and the double thickness. The single is used for base plate construction, and the double is used to construct custom tray. Shellac base plate is supplied commercially in 2 forms, shaped to correspond to maxillary and mandibular arches. Before adapting the shellac base plate, the cast must be treated so that the material will not adhere to it. This may be done either by dusting the cast with talcum powder or by the application of light coat of vaseline. The shellac base plate is centered on the cast. The bunsen burner is inverted and the flame played on the surface of the shellac material. As the shellac material becomes softened, it will sag. It is then pressed firmly in place by the finger. After the preliminary adaptation is completed, the base plate is removed from the cast and borders are heated and excess is trimmed with scissors. You can also trim shellac by an acrylic bur. You can also roll the borders. The borders are heated, the edges are rolled on themselves so that the border is composed of double thickness. The base plate is returned to the cast and the borders readapted with a wet cotton roll. The borders are then smoothed. A handle can be made by softening a piece of the same material or adapting a wire and attaching it to the tray in such a manner to avoid lip interference. If alginate impression material is to be used, the tray should be perforated over its entire surface by drilling holes of approximately 1.5 mm diameter and spaced about 6 mm. b- Modeling compound Modeling compound is a thermoplastic material that is made either as a cakes or sticks. The cake form is used primarily as a tray material, whereas the stick form is used as an impression material. The tray material requires a higher heat to soften, does not record details accurately, and is rigid when it is hardened. In some techniques modeling compound impressions are used as custom trays after scraping 2-3 mm from the fitting surface and flanges of the impressions. o This custom tray is used for a plaster wash impression or zinc oxide eugenol paste lining as a final impression. o The advantage of this method is that it involves one less visit by the patient to the dentist’s office. c- Hydroplastic tray material: It is a single component resin, reaching an easy moldable consistency at 65-85 degrees C and hardens when placed under cool water. Excess material may be re-used by re-heating. It is supplied as small beads of material yellow, pink, or white. 2- Resins a) Self curing acrylic: Modified methyl methacrylates are the most widely used material for making custom trays. Advantages: 1- Easily constructed 2- More rigid than shellac base plate trays 3- More accurate and easily modified 4- Can accept border tracing material Construction 1-All undercuts on the cast are blocked out with base plate wax. 2-The exposed areas on the casts are coated with separating medium. 3-The acrylic resin powder and liquid are mixed according to the manufacturer’s instructions in a glass container. The consistency of the mix is checked periodically till it reaches the dough stage. 4- The dough is placed within a form container or two wet plastic sheets or glass slabs. It is patted out to form a wafer of uniform thickness. 5- The wafer of the tray material is lifted from the former and adapted to the cast with light finger pressure. Excessive pressure will cause thin areas in the tray. 6- A warm knife may be used to trim the soft material from around the borders of the cast. 7-Excess material is formed into a handle of the desired shape.The handle must be placed so that it will not interfere with any movement of the patient’s lips during impression procedures. 8-The casts and impression trays are set aside until material cures. The tray is removed from the cast by inserting a knife and gently lifting it from the cast. 9- Excess material beyond the outline is removed with a stone. Final trimming is done after curing. The tray may be polished and smoothed using polishing wheels and pumice or by the application of the tray material liquid rubbed on the tray surface before curing. b)Light-cured resins Visible light-cured resins exhibit dimensional stability immediately after curing, thus allowing immediate clinical use after fabrication. Research indicates that autopolymerizing acrylic resins should be fabricated 24 hours before the impression procedure. Draw with an indelible pencil the boundaries of the wax spacer, borders of the custom tray and the occlusal stops. Heat and adapt base plate wax to the diagnostic model to obtain a 2 to 4 mm thickness following the spacer outline. Occlusal stops of 2-4 mm sided square are made with a scalpel blade or a carver and positioned to provide a tripod-like stability. The light-cured material is applied over the spacer and carefully adapted to the tray outline. After adapting the material to the boundaries, the excess material is excised using a scalpel blade (No. 12), carver or wax knife. A central handle is shaped and contoured. The custom tray is placed in the light-curing unit and undergoes 2 polymerizations of 5 minutes each. The spacer wax is removed from the internal surface of the tray and placed in the light-curing unit for an additional 5 minutes to cure the interior surface. The posterior palatal seal area on the cast is not covered with the wax spacer. Additional stress can be placed at this area during impression making. The tray is evaluated on the diagnostic model and any sharp edges or irregularities are smoothed with a carbide bur. To improve retention of the impression material, perforations are made with a round head carbide bur. Completed visible light-cured custom tray c) Plastic sheets ❖Another method of making resin custom trays is through the use of a vacuum or pressure forming machine. ❖The material used is supplied by the manufacturer of the machine in the form of uniform clear plastic sheets. Heat curing resin can also be used for the construction of custom trays. Thank you