Composite Production Forming Process (Open Mould) PDF
Document Details
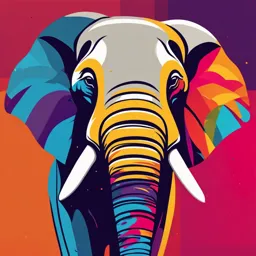
Uploaded by PanoramicSerpentine4424
Kolej Kemahiran Tinggi MARA Masjid Tanah
2024
Tags
Related
- Composite Production Forming Process (Open Mould) PDF
- Composite Production Forming Process (Open Mould) PDF
- Composite Material Preparation - Level 2 PDF
- Lecture 21 - Composite Materials (FRPs) PDF
- Composite Materials 50-Item Questionnaire PDF
- Fachwissen Duroplaste Formenbau mit Faser-Verbund-Kunststoffen PDF
Summary
This document is a set of slides detailing various aspects of composite material production, focusing on the forming process using open molds. It covers topics such as materials category, composite process, curing agents, release agents, and safety requirements. The information is organized into sections that provide definitions, examples and requirements, making it a useful guide for those working in the field of composite manufacturing.
Full Transcript
C03 : COMPOSITE PRODUCTION FORMING PROCESS (OPEN MOULD) DIP. OF INDUSTRY IN AEROSPACE COMPOSITE MANUFACTURING IMC 10473 COMPOSITE PRODUCT FORMING (OPEN MOULD) v COMPETENCY UNIT 1 CHECK PRODUCT FORMING PROCESS (OPEN MOULD) REQUIREMENTS Job Order Information...
C03 : COMPOSITE PRODUCTION FORMING PROCESS (OPEN MOULD) DIP. OF INDUSTRY IN AEROSPACE COMPOSITE MANUFACTURING IMC 10473 COMPOSITE PRODUCT FORMING (OPEN MOULD) v COMPETENCY UNIT 1 CHECK PRODUCT FORMING PROCESS (OPEN MOULD) REQUIREMENTS Job Order Information Product specification/part/drawing/customer product/limit/master sample Color Delivery date Quantity Production Documents Production Schedule Material Requisition Notes (MRN) Materials Request Voucher Materials Category 1. Direct (Raw Materials) i. Fiber ii. Resin iii. Gelcoat iv. Core materials v. Release Agent (Wax) vi. Curing Agent (MEKP) vii. Filler (CaCO3) 2. Indirect i. Bagging Materials ii. Sealant tape 3. Consumable i. Cleaning Solvent (Acetone) ii. Brush / Roller iii. Spatula / Stick iv. Cup / Dipper / Bucket v. Cotton Rag Composite Process OPEN MOULD CLOSE MOULD CONTINUES Techniques Techniques Techniques 1. Hand Lay-UP 1. Press Process 1. Filament Winding i. Wet Lay-Up 2. RTM Process Process ii. Prepreg 2. Pultrusion Process (Dry Lay-Up) 2. Spray-Up Infusion Technique 3. Vacuum Bagging (Wet Lay-Up and Dry Lay-Up) Curing Agent Curing is a chemical process employed in polymer chemistry and process engineering that produces the toughening or hardening of a polymer material by cross-linking of polymer chains. It is strongly associated with the production of thermosetting polymers. Curing Agent Curing agents and crosslinking agents: Polyester Resin Catalyst - is an organic peroxide such as methyl ethyl ketone peroxide (MEKP) and used for room temperature cured processes. - For heat-cured molding, benzoyl peroxide is added to the resin. - As an Initiator : substance which start a chain reaction. Promoter / - such as cobalt naphthenate is used when polyester Accelerator triggered by heat, peroxides convert to a reactive state (exhibiting free radicals), causing the unsaturated resin to react (cross-link) and become solid. Reaction by: Percentage (%) – 0.5% to 3.0 % Curing Agent Curing agents and crosslinking agents: Epoxy Resin Hardeners - Hardener, often an amine, is used to cure the epoxy by an ‘addition reaction’ where both materials take place in the chemical reaction - The chemistry of this reaction means that there are usually two epoxy sites binding to each amine site. This forms a complex three-dimensional molecular structure. Reaction by: Ratio Refer to CDS/TDS/MSDS Release Agent A release agent (also mold release agent, release coating, or mold release coating) is a chemical used to prevent other materials from bonding to surfaces. It can provide a solution in processes involving mold release, die-cast release, plastic release, adhesive release, and tire and web release. A release agent is simply a coating that is applied to a surface to stop the material being moulded (usually a plastic) from sticking Release Agent Release Agent Requirements : Guaranteed release Quick and easy to apply Low cost / part High quality finish Low defect rate No processing problems Ability to release a wide range of materials Release Agent Sacrificial Internal Semi-Permanent ▪ Products are applied to ▪ Internal release agents ▪ Cross-linking (curing) the mould surface. are added to the polymer systems ▪ Release by cohesive prior to moulding. ▪ Hard, thin, dry films (not failure, i.e. they act ▪ During the moulding greasy) sacrificially. process they migrate to ▪ Bond to mould surface ▪ Transfer to released the mould surface where ▪ Low mould build-up surface they act sacrificially. ▪ Multiple releases per ▪ Need frequent re- ▪ Can be inefficient on application application, typically their own and may cause ▪ Low cost / part released; every cycle part failure / bonding high product cost Silicones, Waxes, problems. ▪ Minimal transfer / no PTFE (Teflon), Soaps ▪ Similar chemistry to part cleaning required Sacrificial release agent Silicones, Waxes, Phosphates, Soaps Release Agent Sacrificial Internal Semi-Permanent ▪ Sacrificial coatings ▪ Mix or add into matrix ▪ A semi-permanent must be applied system release agent does not before every cycle of a need to be reapplied for molding operation and every cycle of a molding are therefore operation and even considered more labor works better when it is intensive. not over-applied to the mold surface. Cleaning Solvent - Solvents are used to remove uncured resins from spray equipment, rollers, brushes, tools, and finished surfaces. - For cleaning purpose / cleaning agents - Typical solvents used include: i. Acetone ii. methanol iii. methyl ethyl ketone (MEK) iv. toluene v. xylene Core Materials - Core materials are used extensively throughout the composites industry to fabricate stiff and yet lightweight composites products. Balsa Foam Honeycomb Documentation for Recording/References Tools / Equipment Operating Manual Mould / Tooling Labels Operation Check Sheet / Checklist Safety Requirements Personal Protective Equipment (PPE) Utilization Machine Safety (Sensor, Safety Guard) Safety Practices / Precaution Notices Display COMPETENCY UNIT 2 PREPARE PRODUCT FORMING PROCESS (OPEN MOULD) WORKS REQUIREMENTS Type of Tools / Equipments 1. Hand tools A hand tool is any tool that is powered by hand rather than a motor. Type of Tools / Equipments Accessories Backing Structure The backing is a mix of a selected resin for providing support as to tool backing at its operating temperatures and pressures; and a mix of very small, larger low, and large higher aspect fibers that are combined to form a lattice. Type of Tools / Equipments Ancillary Sealant Tape Bagging Film Acetone Mould / Tooling 1. Availability 2. Part number 3. Serviceable sticker Hand tools, Equipment & Open Mould Functionality and Operability Functionality of Hand Tools To remove the part from mould tool Technique to remove the part depend on the design of tool. Hand tools, Equipment & Open Mould Functionality and Operability Plastic Wedges Handy plastic scraper and spreader set that's great for applying body puty, spreading filler or removing decals without harming your finish Hand tools, Equipment & Open Mould Functionality and Operability Plastic mallet It is a tool of preference for wood workers using chisels with plastic, metal, or wooden handles, as they give a softened strike with a positive drive. It is the most commonly used mallet Hand tools, Equipment & Open Mould Functionality and Operability Allen Key Type of Personal Protective Equipment Glove Choose the right glove according to type of pollution (toxic) and assignment (condition of work area): Rubber: paint spraying or degreasing. Leather: heat resistant. Cloth/Nylon: work required handgrip. Latex: electrical insulation work. PVC: chemical handling. Type of Personal Protective Equipment Apron Choose proper clothes for proper job. Type of Personal Protective Equipment Googgles Protection against flying particle, chemical splash, heat (radiation) or welding activity. Choose the right goggle to suit for the task that needs to be carried out. Type of Personal Protective Equipment Safety Shoes Come in different type according to work area. For example: Constructive construction: static charge protection. Non ferrous construction: friction spark protection. Very important when entering production section or heavy workload area. Type of Personal Protective Equipment Safety Mask A mask is a flexible pad held over the nose and mouth by elastic or rubber straps to protect against dusts encountered during construction or cleaning activities. “Respirator” A respirator is a device designed to protect the wearer from inhaling hazardous atmospheres, including particulate matter such as dusts and airborne microorganisms, as well as hazardous fumes, vapours and gases. Refreshment!! 1. List of production documents. Production Schedule Material Requisition Notes (MRN) Materials Request Voucher 2. Give an example of DIRECT, INDIRECT & CONSUMABLE. DIRECT INDIRECT CONSUMABLES i. Fiber i. Bagging Materials i. Cleaning Solvent (Acetone) ii. Resin ii. Sealant tape ii. Brush / Roller iii. Gelcoat iii. Breather iii. Spatula / Stick iv. Core materials iv. Cup / Dipper / Bucket v. Release Agent (Wax) v. Cotton Rag vi. Curing Agent (MEKP) vii. Filler (CaCO3) Refreshment!! 3. Give an example of OPEN MOULD and CLOSE MOULD process. OPEN MOULD CLOSE MOULD 1. Hand Lay-UP 1. Press Process i. Wet Lay-Up 2. RTM Process ii. Prepreg (Dry Lay-Up) 3. Vacuum Infusion 2. Spray-Up 3. Vacuum Bagging (Wet Lay-Up and Dry Lay- Up) Refreshment!! 4. What the definition and name of catalyst for polyester resin? Catalyst is an organic peroxide such as methyl ethyl ketone peroxide (MEKP) and used for room temperature cured processes. 5. State the release agent requirements. Release Agent Requirements : Guaranteed release Quick and easy to apply Low cost / part High quality finish Low defect rate No processing problems Ability to release a wide range of materials THANK YOU !