Lean Systems and Supply Chain - Unit 4
Document Details
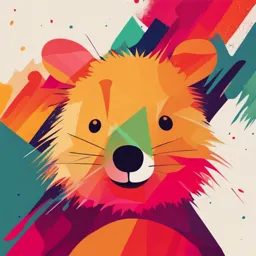
Uploaded by Sennin
Seth K. Nkrumah
Tags
Summary
This document appears to be a presentation focusing on Unit 4: Lean Systems, covering topics such as defining lean, discussing the principles and metrics of lean, and explaining the 7 wastes of lean. It also covers the concepts of a lean supply chain and draws upon the Toyota Production System(TPS).
Full Transcript
ISD 469: (PLANNING AND CONTROL SYSTEMS FOR SUPPLY CHAIN) Dr. Seth K. Nkrumah (SCIS-KSB) UNIT 4: LEAN SYSTEMS Overview What is Lean Principles and metrics of lean 7 wastes of lean Concepts of a Lean Supply Chain What is Lean? A set of tools to reduce waste ?...
ISD 469: (PLANNING AND CONTROL SYSTEMS FOR SUPPLY CHAIN) Dr. Seth K. Nkrumah (SCIS-KSB) UNIT 4: LEAN SYSTEMS Overview What is Lean Principles and metrics of lean 7 wastes of lean Concepts of a Lean Supply Chain What is Lean? A set of tools to reduce waste ? A proactive approach to manufacturing that focuses on; providing value to the customer by identifying and producing products the customer wants. Developing processes that enable customer demand to pull production, rather than the manufacturer pushing products to the customer. A philosophy based on lead-time reduction from customer order to delivery ? A state of mind ? An organizational methodology designed to create a learning organization ? An operational model based on continuous improvement ? What is Lean? Lean is concerned with delivering more value for the business and it’s customers by increasing the velocity of throughput and minimizing wasteful practices by balancing process flow. Lean is a Business Philosophy, not a technique. What is Lean? “Lean is much more than techniques. It is a way of thinking - a whole systems approach that creates a culture in which everyone in the organization continuously improves their processes and production.“ Jim Wolmack A definition for Lean A systematic approach to identifying and eliminating waste(non-value-added activities) through continuous improvement by flowing the service at the pull of the customer in pursuit of perfection‘ Lean is a Business Philosophy, not a technique. Origins of Lean Although there are many quoted origins for many of the founding concepts behind lean production, most people recognize the Toyota Production System (TPS) as initially bringing together all of the essential ingredients required to implement a complete lean manufacturing process. The term ‘lean’ was originally coined following an MIT automotive study and the book that followed that study. That book was the landmark ‘The Machine that Changed the World’ by Womak and Jones in 1988. Five Principles of Lean…used to drive continuous improvements. 1. Define Value 2. Value Stream 3. Flow 4. Pull 5. Perfection Five Principles of Lean…used to drive continuous improvements. 1. Define Value – Specify what creates value from the customers perspective– not individual firms, functions or departments 2. Value Stream – Identify the value stream for each product/service (The Value Stream is the combination of all the steps necessary to design, order,& produce the product/service) 3. Flow – Create continuous flow in the Value Stream (Take actions to eliminate interruptions, detours and waiting) (from Lean Thinking, Womack and Jones, 1996) Five Principles of Lean…used to drive continuous improvements. 4. Pull – Only produce to customer demand (demands the implementation of just-in time systems) 5. Perfection – Relentlessly pursue continuous improvement removing successive layers of waste as they are uncovered. (from Lean Thinking, Womack and Jones, 1996) Five Principles of Lean Wastes of Lean Waste can be defined as any aspect of an activity, task or process that adds no value to the final product or service Categorizing waste allows us to quantify it and make it tangible Waste is a symptom rather than a root cause of the problem. It points to problems within the system A rule of thumb is to expect that 40-60% of what we do adds no value. Identification and Elimination of Waste Philosophy Waste exists in all work and at all levels in the organization. Identification and elimination of waste is the central focus of a lean system. Successful implementation requires that ALL employees must be trained to identify and eliminate waste from their work. The 7 Wastes of Lean 1. Waiting 2. Overproduction 3. Unnecessary processing 4. Inventories 5. Unnecessary movement 6. Unnecessary transport 7. Defects/Rework These wastes were identified by Toyota engineers Taiichi Ohno and Shigeo Shingo in developing the Toyota Production System (TPS) Waste of Waiting Definition: Cola Idle time between operations or events Characteristics: Causes: Person Waiting for Machine Inconsistent Work Methods Long Machine Change Over Machine Waiting for Person Times Person Waiting for Person Poor Machine/Person Lack of Concern for Effectiveness Equipment Breakdowns Lack of Proper Machine Unplanned Equipment Poor Preventative Maintenance Downtime Program Can you identify waiting waste in your work place? Waste of Overproduction Definition: Producing more than the customer requires. Causes: Producing faster than the customer Lack of Communication requires it. Low Uptimes/Insufficient P.M. Lack of Consistent Characteristics: Schedules Inventory Stockpiles Focus on Expectation Unbalanced Material Flow (Forecasted Sales) Versus Customer Demand Extra Racks (Consumption) Extra Resources Complex Inventory Management Massive Rework Campaigns Waste of Overproduction Waste of Rework Definitions: Not meeting customer expectations the “first” time Characteristics: Extra Human Resources to Causes: Inspect, Rework, or Repair Missed Shipments/Deliveries Incapable Processes Operator Control Error Poor Customer/Supplier Insufficient Training Relations Inadequate Tools/Equipment Lower Profits Due to Rework, High Inventory Level Scrap, Organization Becomes Reactive (Firefighting vs. Prevention Orientation) Can you identify Rework in your work place? Waste of Rework Waste of Motion Definition: Any movement of people or machines which does not add value to the product/service. Characteristics: Causes: Looking to Find Tools Equipment, Office & Plant Excessive Layout Reaching/Bending Lack of Work Place Organization Machines/Material too Far Apart (Walk Time) Poor Machine/People Shuttle Conveyors Between Effectiveness Equipment to Carry Parts Inconsistent Work Methods Can you identify motion Confusing Motionwaste within your Workwork place? Large Batch Sizes Waste of Motion Waste of Processing Definition: Occurs when people or effort add no value to a product/service. Enhancements which are transparent to the customers, or work which could be combined with another purpose. Processing when the process is flawed. Waste of Processing Characteristics: Causes: Lack of Clear Customer New Technology Used Specifications Inappropriately Endless Refinement Decision making at Redundant Approvals Inappropriate Levels Machines In the Line Ineffective Policies and That Rejects Good Parts Procedures Lack of Customer Input Concerning Requirements Can you identify processing waste in your work place? Waste of Inventory, a Major Paradigm Before, Inventory was declared an asset by financial people. Now it is a Waste. Waste of Inventory Definition: Any supply in excess of customer requirements necessary to produce goods or services just in time. Characteristics: Causes: Slow Response to Incapable Processes Changes Uncontrolled Bottlenecks Extra Space on Receiving Long Change Over Time Dock Incapable Suppliers Management Decisions Large Store Areas Local Optimization FILO Instead of FIFO Inaccurate Forecasting Material With Out Dated Systems Shelf life Can you identify inventory waste in your Months Worth of Supplies work place? Waste of Inventory Waste of Transportation Definition: Wasted effort to transport materials, parts, or finished goods into or out of storage, or between processes. Causes: Characteristics: Large Lot Processing Additional Pallet Movement Inconsistent Schedules Multiple Storage Locations Long Change Over Times Incorrect Inventory Counts Lack of Work Place Opportunity for Damage/Floor Organization Loss Improper Facility Layout Costly, Inflexible Conveyors Lack of Demand Driven and Fork Lifts Manufacturing System Can you identify transportation waste in your work place? Waste of Intellect Definition: Any failure to utilize the time and talents of the people. Causes: Characteristics: Status Quo Never Challenged Lack of Employee Lack of Accountability Involvement Lack of Team Activities Poor Morale Can you identify intellectual waste in your work place? 3 Critical Metrics of Lean (1) When considering the typical gains for a lean conversion, think in terms of the three critical metrics: Quality, Delivery, and Cost 3 Critical Metrics of Lean (2) Quality: Ensure a defect free product/service with low process variation. Defect Reduction Product Development Time reduction Delivery: Deliver the amount the customer wanted, when they want it. Lead-time reduction Set-up time reduction Work in Process reduction 3 Critical Metrics of Lean (3) Cost: Provide services/products at the lowest cost. This will provide protection in a commodity environment.(implement necessary actions to assume a cost leadership strategy) Productivity/Process Improvement Scrap reduction Floor Space reduction Value chain analysis and optimization Capital Expenditure reduction Lean Supply Chain Critical wastes that a Lean Supply Chain looks to eliminate: Delays from issuing purchase orders to initiate parts flow Redundant and unnecessary receiving and inspections Delays and wasted motion of getting parts from supplier to floor location Unnecessary inventories Defective products Lean Supply Chain A lean supply chain looks to deliver: Systematic price reductions and competitive pricing strategies Continual lead time reduction Continual quality improvement Reduced product handling Win-Win agreements Lean Supply Chain Characteristics of Lean Suppliers Few Nearby (if possible) Repeat business/Longer Term Agreements Analysis to enable desirable suppliers to become or stay price competitive Logistics: Frequent Deliveries/Smaller Quantities Exact Quantities Consumption initiates deliveries Deliveries directly to the point of use Perfect Parts Concurrent product design practices THANKS 36