Principles of Industrial Maintenance PDF
Document Details
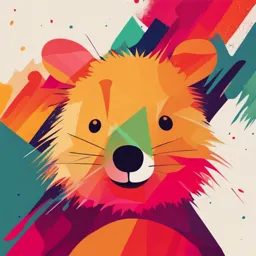
Uploaded by FortunateRisingAction
Edith Cowan University
2018
Dr Ana Vafadar
Tags
Related
- Purple Book (Guide for Controlling ACM in Buildings) Part 4 PDF
- On-load tap-changer VACUTAP® VV Maintenance Manual WA 241/05 PDF
- OHS 5S 7S PDF
- Wagon Maintenance Manual PDF
- Safety Refresher Training Manual PDF (Southern Petrochemical Industries Corporation Ltd)
- R.D. 773/1997 Utilización de Equipos de Protección Individual PDF
Summary
This document is a lecture on principles of industrial maintenance. It covers case studies, such as the Piper Alpha oil platform and F-111 deseal and reseal maintenance, to explore occupational hazards and aircraft maintenance errors. It also provides an introduction to the Occupational Health and Safety (OHS) framework in Australia, and discusses safety performance measures. The document is from Edith Cowan University in 2018.
Full Transcript
Course materials provided for personal study only and subject to the disclaimer on the ECU website http://www.ecu.edu.au/supplemental/disclaimer Principles of Industrial Maintenance...
Course materials provided for personal study only and subject to the disclaimer on the ECU website http://www.ecu.edu.au/supplemental/disclaimer Principles of Industrial Maintenance Lecturer: Dr Ana Vafadar [email protected] This lecture Coverage in this lecture will be largely derived from … Richardson, S. (1995). Piper alpha: the event. IChemE Loss Prevention Bulletin. 122, 3-6. Richardson, S. (1995). Piper alpha: the event. IChemE Loss Prevention Bulletin. 123, 3-8. Department of Defence [n.d.]. Air force to put people first following inquiry. Department of Veterans Affairs [n.d.]. Background to the development of Study of Health Outcomes in Aircraft Maintenance Personnel (SHOAMP). Lind, S., & Nenonen, S. (2008). Occupational risks in industrial maintenance. Journal of Quality in Maintenance Engineering, 14, Issue 2, 194-204. Hobbs, A., & Williamson, A. (2003). Associations between errors and contributing factors in aircraft maintenance. Human Factors, 45, 186-201. Robinson, R. M., Francis, G., Hersan, A., Kanga, M., Robinson, J., Stoks, F., & Wallis, J.(2008). Risk & reliability: an introductory text (7th ed). Melbourne: R2A Pty Ltd. (ISBN 9780958524155) Content from other sources will be indicated where applicable This lecture – the plan This lecture material is largely based on … Case studies Piper-Alpha oil platform (Richardson, 1995) F-111 deseal and reseal maintenance (Dept of Veterans Affairs, Dept of Defence, Australia) Occupational hazards during (on-site) industrial maintenance (Lind & Nenonen, 2008) Aircraft maintenance errors and their contributing factors (Hobbs & Williamson, 2003) OH&S (CHP 16) (Robinson et al, 2008) Brief introduction to the OHS framework (in Australia) This lecture in a nutshell This lecture will basically … Highlight potential relationship between maintenance operations and safety related issues. To achieve this, several case studies will be used. Themes covered include: The role of maintenance work permits and wider operational awareness for the status of maintenance work. Case: Piper Alpha oil platform explosion (UK) Potential exposure to harmful substances during maintenance operations. Case: F-111 deseal/reseal operations (Australia) Identifying major occupational hazards during industrial maintenance. Case: Database of incidents (Finland) The relationship between aircraft maintenance errors and their contributing factors. Case: Study into data base of (CASA licensed) maintenance professionals and a large group of unlicensed airline mechanics (Australia) Provide an insight into Occupational Health and Safety Safety & Maintenance Slide 5 Source: https://www.thechemicalengineer.com Case:Piper Alpha oil platform Source: Richardson (1995, Issue 122) Location of platform is North Sea (UK) Piper oilfield, ~193km north east of Aberdeen (Scotland) Piper oilfield, deep water (~140m) Platform (initially) exported oil only Later gas condensate was also incorporated (propane) Total oil export: ~10% of UK North Sea output Total gas export: ~0.6% of UK North Sea output Evening of 6th July 1988 explosions occurred Flames estimated to have reached 200meters Fire extinguished only on 29 July 1988 Human life losses 166 (on day) and 1 later in hospital. Most of the platform collapsed into the sea including the main (four story) accommodation module. Financial losses £2000million Richardson, S. (1995). Piper alpha - the event. IChemE Loss Prevention Bulletin. 122, 3-6. Principles of Industrial Maintenance Edith Cowan University 2018 Safety & Maintenance Slide 6 Case:Piper Alpha oil platform Refer to figures in the original Source: Richardson (1995, Issue 122) article(s) for schematics showing pump configurations. Causes (probable) … quoted from Richardson: In trying to establish the cause of the disaster, considerable difficulties were encountered because so little physical evidence remained and there were so few survivors who could give essential information … The most probable original cause almost certainly lay in the condensate separation and injection area … On the evening of 6 July 1988, injection pump A was isolated for maintenance of its motor drive coupling. In addition, its safety valve was removed for maintenance and a blind flange almost certainly fitted in its place. The flange was not, however, leak-tested or pressure-tested. When pump B tripped at about 21.45, the operators initially sought to restart it. They were not successful in this endeavour: pump B kept tripping… The evidence suggests that what they in fact did was to try and restart pump A. They would have been aware that pump A was out of commission for maintenance – but that maintenance had not yet started and the problem with pump A was not essentially serious. Because of the way in which work permits were organised on Piper, it is almost certain that the operators would have not been aware that the safety valve for pump A was missing … The most probable thing that happened next is that the condensate, after flowing extremely rapidly into the pump [i.e., pump A] and then into it safety valve line, leaked at the flange fitted in place of the safety valve (Richardson, 1995, p. 5-6) Principles of Industrial Maintenance Edith Cowan University 2018 Safety & Maintenance Slide 7 Case:Piper Alpha oil platform Source: Richardson (1995, Issue 122) Causes (probable) … quoted from Richardson:... The most likely scenario … is that the blind flange was incompletely tightened. The evidence of gas alarms noted by the surviving control room operator and the strength of the initial explosion suggests that the leakage hole had an area of about 50 square millimetres. … 50 square millimetres corresponds to lifting of the flange by only about 0.15 millimetres … Perhaps 90 kilogrammes of condensate would have escaped over a period of around 30 seconds. (Richardson, 1995, pg 6). Source: Richardson (1995, Issue 123) Lessons A follow-up article by Richardson (1995, Issue 123) summarised that the accident had lessons to be learned. These included: design, plan (equipment) isolation, operational procedures, communication (and its breakdown) and evacuations. There were also lessons to be learned in Maintenance and work permits. Richardson, S. (1995). Piper alpha - the lessons. IChemE Loss Prevention Bulletin. 123, 3-8. Principles of Industrial Maintenance Edith Cowan University 2018 F-111 aircraft. Image: Dept of Defence , Australia http://www.defence.gov.au/media/download/2008/aug/20080808/index.htm Safety & Maintenance Case: F-111 deseal and reseal maintenance Source: Dept of Veterans Affairs (Australian Government) Royal Australian Air Force (RAAF) receives F-111 aircraft from US Fuel tanks chemically sealed Sealant degrades with time Need to remove damaged sealant and place new sealant (deseal/reseal) Timelines of Deseal/Reseal Started in Australia Oct 1977 Concluded 2000 Source: Dept of Defence (Australian Government) F-111 fuel tanks Airplanes do not have ‘bladders’ to hold fuel Instead, spaces within fuselage act as integral fuel storage tanks Spaces need to be sealed for integrity Safety & Maintenance Case:F-111 deseal and reseal maintenance Source: Dept of Defence (Australian Government) Maintenance Work (deseal/reseal) “ … each aircraft was subject to RAAF maintenance workers entering the fuel tanks, setting up apparatus to spray a softening agent (SR51), laboriously removing the sealant by hand and then preparing the surface for new sealant. This sealant consisted of two coats of a putty-like substance which had to be applied by hand. In all of this, RAAF staff had to wear protective clothing as the chemicals and sealant were known to be toxic” F-111 aircraft. Image: Dept of Defence , Australia http://www.defence.gov.au/media/download/2008/aug/20080808/index.htm Safety & Maintenance Case:F-111 deseal and reseal maintenance Source: Dept of Veterans Affairs (Australian Government) RAAF Board of inquiry “A RAAF Board of Inquiry found that since 1977, some 400 ADF personnel and civilians had suffered health effects, allegedly because of the chemicals and solvents used while working on the F-111 Deseal/Reseal fuel tank maintenance programs”. Study of Health Outcomes in Aircraft Maintenance Personnel (SHOAMP) Commissioned in 2001, completed and declared Oct 2004. Findings … “The study concluded that, on the balance of probabilities, there was an increased risk of cancer associated with having participated in the F-111 Deseal/Reseal program” Source: Dept of Defence (Australian Government) Media Release “The Board’s [Board of Inquiry] principal finding is that the health symptoms that DSRS [Deseal Reseal] workers currently experience or demonstrate are reasonably attributable to their earlier exposure. It is on this basis that the Board estimates there to be in excess of 400 workers who have suffered long-term damage to their health” Safety & Maintenance Case:F-111 deseal and reseal maintenance Source: Dept of Defence (Australian Government) Media Release “The Board found that there were a number of systemic failures, described in the Report as the ‘causal pathways to the outcome’. The Air Force medical service was seen as failing in particular by the low priority given to occupational medicine. A second factor identified as an immediate cause was the relative powerlessness of maintenance workers. Complaints were effectively ignored” “At the level of immediate causes, exposure to toxic chemicals was the main focus of the Inquiry. Exposure was possible, the Board found, as the Air Force was relying totally on personal protective equipment (PPE) to protect its workers from the many hazards involved in working with toxic substances in confined spaces” “Given the reliance on personal protective equipment, problems arose with the appropriateness of protective equipment for the tasks at hand, the availability and control of that equipment through the supply network, and the failure of some workers to wear the equipment, coupled with an inadequate compliance system” “A final failure, and in some respects, most fundamental of all failures, was that of the chain of command to operate optimally …” Safety & Maintenance Slide 13 Case: Occupational hazards during (on-site) industrial maintenance Source: Lind & Nenonen (2008) Two pathways of investigation utilised in this study: First: Public databases of maintenance incidents (Finland) Severe accident reports (1994-2004): total: 90 persons Fatal accidents (1985-2004): total: 37 persons All data reported related to full-time maintenance workers Second: Risk assessment surveys...Conducted in companies to identify hazards, estimate their likelihood of occurrence and what the expected consequences might be. Companies surveyed: Three companies (15 sites) Two of these companies are maintenance service providers The other company is a machine manufacturer, with after sales service This makes all these companies essentially render maintenance services in others work sites (similar to a sub-contracting work to customers). Lind, S., & Nenonen, S. (2008). Occupational risks in industrial maintenance. Journal of Quality in Maintenance Engineering, 14, Issue 2, 194-204. Principles of Industrial Maintenance Edith Cowan University 2018 Safety & Maintenance Slide 14 Case:Occupational hazards during (on-site) industrial maintenance Source: Lind & Nenonen (2008) Accident data: Common causes of severe injury and fatal incidents Severe accident Fatality Total Crushing or entrapment 39% 27% 36% Falls 21% 27% 23% Falling items 12% 15% 13% Electricity 7% 6% 7% Splashing of dangerous substances 6% 0% 4% Touching or entanglement 3% 3% 3% Suffocation or poisoning 0% 9% 2% Others 12% 12% 12% Principles of Industrial Maintenance Edith Cowan University 2018 Safety & Maintenance Slide 15 Case:Occupational hazards during (on-site) industrial maintenance Source: Lind & Nenonen (2008) Accident data: Factors contributing to severe injury and fatal incidents Severe accident Fatality Total Working on machine in motion 25% 15% 24% Dangerous work practices 11% 48% 21% Ignoring instructions and rules 18% 13% 16% Machine malfunctions 10% 15% 11% Inappropriate walking or working surface 14% 0% 10% Human Error 9% 4% 7% Hurried work 9% 4% 7% Others …% …% …% Principles of Industrial Maintenance Edith Cowan University 2018 Safety & Maintenance Slide 16 Case:Occupational hazards during (on-site) industrial maintenance Source: Lind & Nenonen (2008) On site risk assessments: mostly under three headings Ergonomic associated risks: poor ergonomics during maintenance operations Lack of worker awareness of appropriate work postures or methods Machines and processes not designed with maintenance in view Work environment risks Work that needs to be done outdoors (weather, seasonal effects, travel to site) Planning and scheduling should ideally take this into account Workplace tidiness and cleanliness Risks of injury Slips, trips, climbing and falls (all affected by seasonal variations too: cold, hot, light levels) Principles of Industrial Maintenance Edith Cowan University 2018 Safety & Maintenance Slide 17 Case:Occupational hazards during (on-site) industrial maintenance Source: Lind & Nenonen (2008) Remarks from this study … “The occupational safety of workers is the duty of management also while workers are on unfamiliar sites. Sites may be stable or temporary. Thus, safety management must be flexible and constantly take into account changing work environments. Also on stable sites maintenance crew members may change, e.g. due to varying work loads. The time for work planning (including safety planning) may also be limited. This may be problematic, especially on new sites and in the case of new maintenance tasks”. Promoting safety from this study … Maintenance crew personnel should have relevant safety related information. Workers should be instructed on safe work methods before working independently at customer work sites. Work should be appropriately planned and workers should be advised on conducting independent identifications of potential hazards. Work conditions need to be taken into account so as to promote working in a safe manner. Principles of Industrial Maintenance Edith Cowan University 2018 Safety & Maintenance Slide 18 Case:Aircraft maintenance errors and their contributing factors Source: Hobbs & Williamson (2003) A study into the potential links between specific maintenance work errors and the factors that contribute to them was conducted by Hobbs and Williamson (2003). If these causing factors are identified, accidents might be averted. Questionnaires: those surveyed Total of 4,900 aircraft maintenance personnel (holders of CASA issued maintenance licenses) About 300 mechanics (unlicensed) who work for airlines in Australia. Response rate of respondents: 28% Principles of Industrial Maintenance Edith Cowan University 2018 Safety & Maintenance Slide 19 Case:Aircraft maintenance errors and their contributing factors Source: Hobbs & Williamson (2003) Maintenance related errors on aircraft are serious: Major accidents might result Financial repercussions due to flight delays or cancellations Maintenance work on aircraft can potentially be subject to errors, arising from: Inadequately designed maintenance documentation Communication breakdown Inadequate supervision Time pressures Shift type work Environmental conditions (extremes) Unlike errors that are caused by aircrew (flight personnel), errors made by maintenance personnel can remain unnoticed (dormant) for longer times. This makes tracking their causes more difficult. Unlike aircrew (pilots) or traffic controllers, maintenance personnel do not find themselves being subject to voice recording. This also complicates subsequent investigation. Hobbs, A., & Williamson, A. (2003). Associations between errors and contributing factors in aircraft maintenance. Human Factors, 45, 186-201. Principles of Industrial Maintenance Edith Cowan University 2018 Safety & Maintenance Slide 20 Case:Aircraft maintenance errors and their contributing factors Source: Hobbs & Williamson (2003) Questionnaires: Analysis of the outcomes Some of the highest reported occurrences which were attributable to maintenance personnel errors were Systems operated unsafely during maintenance 13% Read “Nature of the Installations that were incomplete 8% Occurrences” in the Contact between maintenance workers and hazards 7% article on pg 192. Incorrect assembly processes or locations 7% Towing event 7% Questionnaires: Events contributing to occurrences To better understand the factors which lead to occurrences taking place, the highest contributing factors were found to be … Memory lapses 20.1% Violations 17.2% The single highest reason used to explain why these events took place was attributable to pressure (23.5%). Principles of Industrial Maintenance Edith Cowan University 2018 Safety & Maintenance Slide 21 Introduction to OHS frameworks (Robinson et al, 2008) In the Australian context, Occupational Health and Safety (OHS) is subject to regulation by the states and territories. These states and territories are responsible for drafting and enforcement of OHS laws. OHS laws take the form of acts and regulations. Each state and territory will have specific OHS Acts OHS Acts provide for the structure and responsibilities of how to achieve OHS goals. Main objectives of OHS legislation: To ensure safety, health and the welfare of working individuals Elimination of risks that can affect the health and safety in the workplace. Extend duty (duty of care) to persons who also occupy the workplace (other than the employees). Retailers … also have duty to customers Educational institutions … also have duty to students Robinson, R. M., Francis, G., Hersan, A., Kanga, M., Robinson, J., Stoks, F., & Wallis, J.(2008). Risk & reliability: an introductory text (7th ed). Melbourne: R2A Pty Ltd.. Principles of Industrial Maintenance Edith Cowan University 2018 Safety & Maintenance Slide 22 Introductionto OHS frameworks (Robinson et al, 2008) Regulations are also drafted to support the OHS Acts Regulations provide more detail on what kind of steps must be applied for the control of specific hazards, and who should undertake these steps. Examples: Asbestos regulations Noise regulations Regulations may be supported by codes of practice Codes of practice “are basically ‘how to comply’ documents with a lot of useful advice on assessment and control” (Robinson et al, 2008, pg. 179) Other steps in the legal framework include: National standards (drafted by the National Occupational Health and Safety Commission, NOHSC) Codes, standards and guidance notes issued by authorities, professional bodies and industry associations. Principles of Industrial Maintenance Edith Cowan University 2018 Safety & Maintenance Slide 23 Introduction to OHS frameworks (Robinson et al, 2008) Compliance: “mandatory” OHS Acts OHS Regulations Codes of Practice Standards (Australian, NOHSC) Industry standards or guidance notes Compliance: “… generally not mandatory unless the document is called up by an act or regulation. However codes and Australian standards can be used as evidence in court to demonstrate what could have been done, that is, a form of good/best practice” (Robinson et al, 2008, pg 180) Adapted/modified from figure on pg 180: Robinson et al (2008) Principles of Industrial Maintenance Edith Cowan University 2018 Safety & Maintenance Slide 24 Introduction to OHS frameworks (Robinson et al, 2008) Breaches, Penalties and interventions Breaches: might mean the imposition of fines. Improvement Notices: employers are required by this to undertake specific steps within specific time periods. Prohibition Notices: cessation of work until such a time by which specific remedial actions are applied. Principles of Industrial Maintenance Edith Cowan University 2018 Safety & Maintenance Slide 25 Introduction to OHS frameworks (Robinson et al, 2008) Controlling risks “The legislation requires that risk control must be based upon the Hierarchy of Controls which is typically, in order of most to least preferred: Elimination Substitution Isolation Engineering controls Administrative controls Personal protective equipment and clothing There are small variations to this in other states/territories. Because of the legislative requirement to carry out risk assessments, which must be documented to prove that they have been conducted, this can result in an extremely large list of controls that need to be implemented” (Robinson et al, 2008, pg 182) Principles of Industrial Maintenance Edith Cowan University 2018 Safety & Maintenance Introductionto OHS frameworks @ General hierarchy of hazard control (at ECU) and their descriptions Most Elimination: is the first choice and this is a permanent solution and should be preferred attempted in the first instance. Substitution: if elimination is not possible the next preferred option involves replacing the hazard by one of lower risk. Isolation (enclose the hazard): this choice is to isolate the hazard so that people do not come in contact with it. Engineering: controls involve physical barriers or structural changes to the environment or process. Administrative: controls reduce hazard by altering procedures and providing instructions. eg: (i) Written Safe Operating Procedures. (ii) Job rotation to restrict hours worked on difficult jobs. Least (iii) Staff trained in the correct operating procedures. preferred Personal protective equipment: last resort or temporary treatment to deal with the hazard, where the hazard cannot be removed or reduced by any other means, eg: (i) Handling of chemicals – gloves, safety glasses, aprons. (ii) Protecting eyes from flying particles. (iii) Protecting feet – safety boots. Hazard and Risk Management Guidelines (ECU). Retrieved January, 12, 2010 from http://www.hr.ecu.edu.au/osh/resource/Risk%20Management%20For%20Risk%20Assess%20Procedure%20R1.doc Safety & Maintenance Introductionto OHS frameworks @ General hierarchy of hazard control (at ECU) and their descriptions “There is a legal requirement to address each of the control criteria from elimination through to personal protective equipment and to substantiate and document why each criteria is not reasonably practicable for the solution of the hazard” “Administration and the use of personal protective equipment are the lowest priority on the list of controls. These treatments should NOT be relied on as the primary means of risk control. The higher option in the control priorities must have been exhausted. These treatments require management, enforcement, and commitment, together with behavioural modification.” Hazard and Risk Management Guidelines, ECU (pg 9-10) Hazard and Risk Management Guidelines (ECU). Retrieved January, 12, 2010 from http://www.hr.ecu.edu.au/osh/resource/Risk%20Management%20For%20Risk%20Assess%20Procedure%20R1.doc Safety & Maintenance Slide 28 Introduction to OHS frameworks (Robinson et al, 2008) Safety performance measures Some indicators might be used to assess risks and reliability (associated with safety). Such indicators may be expressed over different periods (daily, weekly, monthly, annually). These include: Fatalities (total numbers and the frequency of occurrence) Injuries (total numbers, severity and the frequency of occurrence) Statutory breaches (number and severity) Days gained or delayed (especially for projects and contracts) Dollars (gained or lost) Availability (% time operating). Principles of Industrial Maintenance Edith Cowan University 2018 Safety & Maintenance Slide 29 Tasks (self study materials) There are a number of required Audio Visual items and readings which constitute part of the content for this lecture. Information included in this lecture is only a summary of the articles cited. Access the original sources of information and read these please. Self study reading list has been posted on the Blackboard under Learning Materials tab in the module 7 folder. Piper Alpha (1 video) RAAF F-111 (2 articles) Incident data base in Finland (1 article) Principles of Industrial Maintenance Edith Cowan University 2018 Component Life Time Slide 30 Thank you Principles of Industrial Maintenance Edith Cowan University 2018