Safety and Risk Management PDF
Document Details
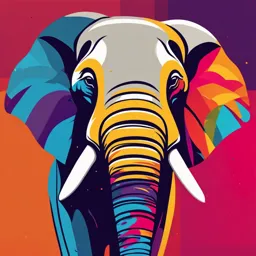
Uploaded by SnazzyImpressionism
King Abdulaziz University
Abdulmohsen Alsalman & Bashar Farsi
Tags
Summary
This document details safety and risk management strategies for a healthcare environment. The document explores common workplace hazards, risk management methods, including specific area concerns and disaster preparedness procedures. It also includes employee training and preparedness.
Full Transcript
SAFETY AND RISK MANAGEMENT Abdulmohsen Alsalman & Bashar Farsi Outline 1) Introduction. 2) Risk Management. 3) Common Workplace safety hazards. 4) General Physical Hazards. 5) Area-Specific safety concerns. 6) Disaster Preparedness. 7) Employee Information and Tr...
SAFETY AND RISK MANAGEMENT Abdulmohsen Alsalman & Bashar Farsi Outline 1) Introduction. 2) Risk Management. 3) Common Workplace safety hazards. 4) General Physical Hazards. 5) Area-Specific safety concerns. 6) Disaster Preparedness. 7) Employee Information and Training. 8) Employee Preparedness. 9) Conclusion. 1) Introduction - Safety is no.tnedicca statement couldn't be more true - Healthcare professionals are responsible for keeping patients, employees and visitors free from injury. - Safety requires ongoing education, safeguards, proper planning and the combined implementation of safety systems to: Reduce risks. Prevent injury. Save lives. Overview - The Central Service (CS) decontamination area is a perfect example of how safety systems and due diligence is essential for ensuring safety. - Employees are educated in biohazard safety and must follow specific regulations, such as those established by the Occupational Safety and Health Administration (OSHA).yrujni fo ksir eht ecuder ot , - We will identify common risks found in the CS work areas and discuss ways to minimize the risk of injury. 2) Risk Management What is Risk Management? - It is a method used to: Assess the risks fo a specific activit. Develop programs to reduce that risk. Involves injury prevention. Claims management.)stiuswal fo noitneverp dna esnefed ,tnemelttes eht( - Healthcare facilities must effectively manage injury prevention for patients and employees as part of a risk management program. Element of risk management/ Assessment ï‚§ Identify the risk ( fire, biological, electrical, fall, slip and trip) ï‚§ Identify the people who might be effected (employees, visitors, patients) ï‚§ Evaluate the risk (high - moderate - low) (Likelihood X severity) ï‚§ Record the findings (current control measures + required mitigation plan) ï‚§ Review regularly to ensure the effectiveness Additional slide Sample Risk Assessment Matrix Likelihood Impact (Severity) Score Rating Description Score Rating Description Fatality (ies). 5 Extreme Permanent Personal 5 Alomost Certain More than 5 times yearly. Disability (total or partial) Few occurrences yearly (e.g., Permanent Personal 4 Likely 4 High 2 to 5 times). Disability (total or partial). Restricted duty Injury. 3 Possible Once each year. 3 Moderate Requires hospitalization. Injury requires medical 2 Unlikely Every 1 to 2 years. 2 Low treatment or first aid. Every 3 or occur in most Minor cut or pain, 1 Rare 1 Minor circumstances more years headache, backache, etc Additional slide Sample Risk Assessment Matrix Risk Assessment Matrix Extreme (5) 5 10 15 20 25 High (4) 4 8 12 16 20 Impact Moderate (3) 3 6 9 12 15 Low (2) 2 4 6 8 10 Minor (1) 1 2 3 4 5 Likelihood Rare (1) Unlikely (2) Possible (3) Likely (4) Alomost Certain (5) Additional slide Sample of Risk Assessment Register RISK ASSESSMENT Likelihood of Impact of Additional Control Measures (if required) Occurance Harm RISK Activity / Process / People Details of SN Date Hazard Consequences LEVEL Risk Rating Task Affected Existing Control BR=L*I 1, 2, 3, 4, 5 1, 2, 3, 4, 5 EL SB EN AD PPE Using papers, Paper cuts, Office No Major 1 16/6/2022 Office work staplers and other 2 1 2 Training Injured hands, Employees Concern stationary items Maintaing Proper Office No Major 2 16/6/2022 Office Lighting Eye Strain Vision Problems 1 2 2 Light Levels Employees Concern (Min 500 lux) Moving files, Manual Handling, Back Pain Injury, Office No Major 3 16/6/2022 equipment and Dropping of 2 1 2 Training Foot Injury Employees Concern systems equipment and files Using of Desktop Decrease in clear Office No Major 4 16/6/2022 Computer / Laptops Eye Strain vision or eye sight, 2 1 2 No Employees Concern for Office Work Head Aches Using of Desktop Improper Back pain, Office Provision of Periodic 5 16/6/2022 Computer / Laptops Arrangement of 2 2 4 Employee Training on Ergonomic Workstation, Hand inujuries Employees Ergonomic Chairs Monitoring for Office Work work area Additional slide Risk Management (Cont.) - The Joint Commission (TJC) seitilicaf erachtlaeh taht eriuqer taht ytirohtua na , teem yeht taht erusne ot serudecorp tnemelpmi dna polevedminimum safety standards: Prevent accidents and/or injuries. Ensure accurate reporting. Follow up to help prevent similar incidents. Risk Management (Cont.) - After a situation is examined dna hazards or unsafe practices have been discovered taht erusne lennosrep tnemeganam ksir ,corrective actions are taken - To improve systems, behaviors and/or physical conditions to help prevent employee and patient accidents and injuries. as well as the manufacturer's Instructions for Use (IFU), standards and regulations, and CS technicians support patient safety. To determine best and effective control measures in order to reduce or remove the exposures to hazards. Additional slide 3) Common Workplace Safety Hazards Common Workplace safety hazards - All jobs involve some risks. - The key to working safely:ot si tnemnorivne krow yna ni Understand those risks. Take appropriate steps to minimize them. - CS technicians must : Understand potential hazards. Pay close attention in work areas within and sometimes outside of their department. Common Workplace safety hazards (Cont.) - The belief that "an accident or injury will never happen to me" creates a false sense of security that results in many injuries each yea. - Following safety protocols and incorporating them into all work practices is necessary for preventing injuries and accidents. Central Service Occupational Hazards - Types of occupational hazards : Physical hazards. Biological hazards. Chemical hazards. - Some of those occupational hazards can be present in all areastnemtraped eht fo and other hazards may be confined to a specific work area. 1 - Physical Safety Hazards: - It may be caused by the environment dna the tasks performed within that environment, Due to the nature of the tasks performed, there are many potential physical hazards in the CS department. - Physical hazards :edulcni yam Wet floors. Cluttered walkways. Heavy carts. Sharp instruments. Fire. 2- Biological Safety Hazards: - Biological safety hazards (infectious waste dna blood borne pathogens nac ) nemtraped eht fo aera yna ni dnuof eb yllaitnetop - The main area of concern :sdrazah lacigoloib rof The decontamination area. 3 - Chemical Safety Hazards: - It may be found throughout eht work area. - For example: Solutions used in the decontamination area Sterilants used in the sterilization area Some patient care products may pose chemical hazards within the department. - The risk of injury from all of these hazards can be minimized by safety protocols that will be discussed in the upcoming slides. 4) General Physical Hazards General Physical Hazards - General physical hazards include those related to: Ergonomics. Slips and falls. Electrical and Safety. Sharps. 1 -Ergonomic Concerns: - Ergonomics : it is the process of changing work or working conditions to reduce physical stress. - CS technicians - are exposed to many ergonomic stress factors, such as : repetitive motion. lifting and pushing. Video https://youtu.be/naCBsggzx3U Ergonomic hazards - YouTube 1 -Ergonomic Concerns: (Cont.) - Ergonomic stressors that employees may encounter include : ï‚§ Force-Heavy lifting. ï‚§ Manipulating equipment ï‚§ Instrument sets. ï‚§ Repetition: Using the same motion, or series of motions, continuously or frequently 1 -Ergonomic Concerns: (Cont.) ï‚§ Awkward positions: Assuming positions that place stress on the body, such as reaching or twisting while lifting. ï‚§ Vibration :Rapid oscillation of the body or a body part. ï‚§ Contact stress continuous pressure between the body and a sharp edge. 1 -Ergonomic Concerns: (Cont.).8 Exposure to these stressors can cause numerous problems:gnidulcni , Ligament sprains. Joint and tendon inflammation. Pinched nerves. Herniated spinal discs. Other injuries. 1 -Ergonomic Concerns: (Cont.) - How can employee reduce cimonogre fo sksir eht injury ? 1. Training:ot seeyolpme pleh nac Recognize the signs and symptoms of injuries, so they can respond to them. Report potential problems. Recognize jobs/tasks that have ergonomic stressor. 1. Stretching before work. 2. Shifting position. 3. Learning and practicing good body mechanics. 1 -Ergonomic Concerns: (Cont.).5 breaking up repetitive activities..6 Proper lifting and pushing movements: When loading and unloading carts from dumbwaiters or elevators, or receiving a cart into the department, it is essential to check the weight on the cart before attempting to move it..7 Ensuring that the wheels are straight, and that they will roll over door spaces or uneven edges is also important, as is unloading some items to lighten the cart if it is too heavy to move easily. 2- Slip and Fall Concerns: - Both are always a concern in the CS department. - Mobile equipment and ever-present wet floors increase fall risks Workplace safety - slips, trips & falls - YouTube 2- Slip and Fall Concerns: (Cont.) - To reduce:sksir eht Mobile equipment should be parked away from common traffic areas. Areas that often have wet floors, such as in the decontamination area, around the cart wash exits, and washer unload areas, must be kept as dry as possible, and spills should be wiped immediately. Non-slip footwear should be worn and attention should be given to slippery floors. Signage, such as the wet floor alerts people to the potential hazard. 3- Electrical Safety Concerns: - Burns and shocks from electric equipment can result if safe handling precautions are not observed. 3- Electrical Safety Concerns: (Cont.) - To reduce eht risks: ï‚§ Carefully check all electrical cords to ensure they are intact, with no breaks in the insulation. ï‚§ Electrical cords on mobile equipment run a greater risk of being kinked or run over by rolling carts which can make the equipment unsafe. 3- Electrical Safety Concerns: (Cont.) ï‚§ All plugs on electrical equipment must be three-pronged and grounded, and all electrical outlets must accommodate these plugs. ï‚§ Inspecting electrical cords for breaks and plugs for bent prongs is a responsibility of CS technicians. ï‚§ Identifying and reporting a potential hazard during cleaning or delivery can prevent injuries to patients and staff. 4- Sharps Concerns: - Cuts and puncture injuries from sharps can happen in any area of the CS department. - Sharp instruments can break the skin's surface and produce puncture wounds, lacerations and abrasions. - If the injury occurs in the decontamination area, these injuries can result in exposure to disease. 4- Sharps Concerns: (Cont.) - Some general precautions to prevent sharps injuries include : Handling all sharps with care. Not grasping several objects at the same time. Ensuring that sharp ends point away from any part of one's body during transport. Placing all disposable sharps, such as needles and blades, in the appropriate sharps container. 5- General Chemical Hazards: - Although most chemicals used in CS are found in the decontamination area , ni dnuof eb yam sdrazah lacimehcother areas - Splashing chemicals is a common cause of eye injuries. 5- General Chemical Hazards: (Cont.) - To reduce:sksir eht The use of eye protection deriuqer si because of splashing chemicals which is a common cause of eye injuries. Eye wash stations era also required in areas where chemical injuries are a concern. 6- Hazardous Substance Concerns: - Each state categorizes certain chemicals and substances as hazardous. Video https://youtu.be/dzX6IaPPmiw 6- Hazardous Substance Concerns: (Cont.) - To reduce the risks: ï‚§ Each CS department should have an easily accessible ,understandable dna , current list of all hazardous substances ï‚§ Most facilities have a comprehensive computerized hazardous chemical list. ï‚§ If employees are required to perform known hazardous tasks, it is important that they understand the safety procedures developed for that task. 6- Hazardous Substance Concerns: ï‚§ Prior to performing such tasks, employees must be given information about the hazards to which they may be exposed. This information should include: Hazards identification. Require PPE. Recommended safety measures. Emergency response procedures. ï‚§ Employers should take measures to minimize hazards to employees. These could include: Increased area ventilation. Respirators. Presence of other employees to assist. The rehearsal of emergency procedures. Safety Data Sheets (SDS) - Formerly called material safety data sheet (MSDS). - It contains important information about product materials and properties that employees must know to work safely with any given product. - SDS are developed and provided by the manufacturer of the product, and they are specific for each product. Safety Data Sheets (SDS) (Cont.) - SDS contain at least information of the following : 1. Product identification Product name, manufacturer's name, address and telephone number, product item number (manufacturer's identification) and synonym names. 2. List of hazardous ingredients. 3. Health hazard data Effects of overexposure. 4. Emergency and first-aid procedures. 5. Spill or leak procedures, spill management and waste disposal methods. Safety Data Sheets (SDS) (Cont.) - SDS contain:noitamrofni gniwollof eht tsael ta 6. Physical data : Vapor pressure. Evaporation rate. Solubility in water. Freezing and boiling points. Specific gravity. Acidity (pH). Vapor density. Appearance and odor. Safety Data Sheets (SDS) (Cont.) - SDS also contain: 7. Fire and explosion information: Flash point. Flammable units. Extinguishing media. Special fire fighting procedures. Unusual fire and explosion hazards. Safety Data Sheets (SDS) (Cont.) - SDS also contain: 8. Reactivity data : Stability. Incompatibility. Hazardous decomposition products. Conditions contributing to hazardous polymerization. Safety Data Sheets (SDS) (Cont.) - SDS also contain:.9 Storage recommendations: Incompatible materials and storage temperatures..10 Protection information and control measures..11 Special precautions. Sample SDS MSDSSafetySheet.pdf (ozonesolutions.com) Employee Monitoring - To prevent potential health hazards to workers, OSHA has established permissible exposure limits (PELS) for many chemicals used in sterilant and disinfectant formulations. These include: Ethylene oxide (EtO). Hydrogen peroxide (H,O,). Ozone.),0( Others. Employee Monitoring (Cont.) - Glutaraldehyde is a chemical commonly used in CS as a high-level disinfectant. - The National Institute for Occupational Safety and Health (NIOSH) recommends that exposure to glutaraldehyde eb under 0.2 parts per million (ppm) time weighted average over an eight-hour work shift. - The American Conference of Governmental Industrial Hygienists (ACGIH) recommends a ceiling value of 0.05 ppm, which should not be exceeded at any time. Employee Monitoring (Cont.) - Healthcare facilities are required by OSHA to : Provide adequate ventilation systems. Establish safe work operating procedures. Provide PPE. Implement other methods to ensure that occupational exposure limits are not exceeded in the workplace. Fire and Explosions - The presence of large volumes of combustible materials and flammable substances poses unique risks. - The large combustible materials loading, storing and disposal could be dangerous. Fire and Explosions (Cont.) - When these materials burn, large quantities of highly toxic smoke are produced. Even with hospital compartmentalization features that limit the spread of smoke and fire, a high-risk situation occurs, therefore, healthcare fire safety programs must include: Minimization of the combustible load. Fire response plans. Early detection. Containment of the fire and combustible products. Extinguishment. Evacuation plans. Fire and Explosions (Cont.) - Fire Response Plan Every healthcare facility requires a comprehensive fire response plan and each staff member in every department must know his/her specific role in these plans. - The fire safety emphasis should begin at the time of new employee orientation and should continue with ongoing training. Fire and Explosions (Cont.) - Every healthcare facility is required to have and maintain: Sprinkler systems. Smoke detectors. Fire extinguishers. Audible alarms to warn and protect staff and patients. Workplace Violence - According to OSHA, approximately 2 million people are the victims of workplace violence Each year. - All employees should: Pay attention to possible warning signs Immediately report any direct threats of violence or retaliation to management. Note behavior, statements or attitudes that are unusual, threatening or disconcerting. 5) Area-Specific Safety Concerns Area-Specific Safety Concerns - There are safety concerns that are common in specific work areas within the CS department. - Must personnel notifying about the need for PPE in the decontamination area. Soiled Receiving and Decontamination Areas - Safety tips:edulcni saera noitanimatnoced dna gniviecer delios ni gnikrow nehw 1. Never reach into a basin or container holding contaminated objects, unless the objects in the basin are clearly visible. ï‚§ Use a sponge forceps to grasp the object or pour out any solution that prohibits visual examination (to be able to properly see the objects) ï‚§ Remove objects from basins or containers one at a time. ï‚§ Never use foaming detergents when handling contaminated instruments in the decontamination sink, as the foam can prevent visualization of sharp objects. 1. Never reach into trash containers or sharps containers. Soiled Receiving and Decontamination Areas (Cont.).3 Use extreme caution when disarming scalpel blades. Do not attempt to do so without training. Never disarm by hand. Always use a needle holder or tool specifically designed to remove blades..4 When processing reusable sharps, separate them from other instruments and position them in a manner that protects anyone who may handle them..5 Follow the manufacturer's recommendations for safe use of chemicals. Always wear recommended PPE to protect all skin surfaces. and mucous membranes from chemical burns. Soiled Receiving and Decontamination Areas (Cont.).6 Follow the manufacturer's recommendations for safe operation of cleaning and testing equipment..7 Use caution when walking, and inspect the floor for slippery surfaces. Utilize mats and non-skid footwear..8 Sinks and other working surfaces should be at levels to afford easy access , and to reduce back and arm strain. Preparation and Sterilization Areas - Safety tips:edulcni saera noitazilirets dna noitaraperp ni gnikrow nehw 1. Move sterilizer carts to low/no traffic or other designated areas, so co-workers will be less likely to come in contact with hot carts. 2. Use thermal insulated gloves when handling steam sterilizer carts, washer baskets and other objects subjected to high temperatures. 3. Keep sterilizer doors closed when not loading or unloading the chamber to protect co- workers from coming in contact with the hot inner door. 4. Use caution when using heat sealers. Keep away from heated components. Be sure to follow the manufacturer's instructions. Preparation and Sterilization Areas.5 Be cautious when using a cutting edge to prepare paper/plastic packs..6 Be cautious when testing instruments for sharpness..7 When lifting instrument sets, use the larger muscles in legs and arms. Hold the item as close to the body as possible without actually touching the body..8 Follow procedures for using and disposing of biological indicators..9 Ensure that proper signs and labels are posted to warn of hot surfaces or other hazard. Supply Receiving, Breakout and Storage Areas Adequate storage space and traffic access must be available to ensure a safe and efficient supply receiving area , Supply storage and shelving units must be secure and steady. Shelves should be arranged to facilitate maximum space efficiency and allow employees easy access to supplies. Heavy materials and items used most frequently should be placed on middle shelves to enable them to be easily and safely accessed by employees. Supply Receiving, Breakout and Storage Areas Lighter, infrequently- used items should be placed on higher shelves. Employees should use appropriate equipment (e.g., steps, stands and ladders) to safely reach upper shelves. Climbing on shelves is not acceptable. Procedures for the safe operation of dollies, hand trucks or carts to handle bulk materials must be available, and employees must be trained to consistently comply with them. Supply Receiving, Breakout and Storage Areas (Cont.) Closed trash containers should be available to properly dispose of unwanted materials. Containers for the appropriate storage of hazardous or flammable materials must be readily available to avoid exposure to hazardous substances. Employees working in this area must also follow proper procedures when disposing of and removing hazardous materials. SDS must be available for reference where these substances are used. Disaster Preparedness Disaster Preparedness - Disaster preparedness is an important component of the CS safety system. - Each facility has developed a comprehensive response plan for : 1. An internal disaster yrujni ro mrah esuac ot laitnetop eht htiw noitautis yna si yam seitilitu fo ssol eht erehw ro seeyolpme ytilicaf erachtlaeh eht ot.snoitarepo latnemtraped tcapmi yllacitsard - Examples: A hazardous chemical spill or leak. Loss of power or failure of a utility, such as water, electricity or steam. Disaster Preparedness (Cont.).2 An external disaster ytilicaf eht edistuo seitivitca hcihw ni noitautis a si tcapmi departmental or facility operations. - Examples that may necessitate activation of the external disaster plan include: earthquakes. floods. hurricanes. other events that result in large numbers of seriously injured patients being sent to the facility. - When an external disaster occurs, the entire facility is placed on alert and personnel from each department are expected to perform tasks, based on the situations present. Disaster Plans - Elements of a CS disaster plan typically include: - An emergency call list slaudividni yek eht dna ,ytirohtua fo senil eht gniniltuo hcae rof reffid yam esehT :etoN.sretsasid fo sepyt cfiiceps ni defiiton eb ot.retsasid fo epyt - Protocols.seilppus ycnegreme fo yreviled dna tnemhsinelper yrotnevni rof eht rof elbisnopser era lennosrep tnemtraped noitubirtsid ylppus ,yllausU rof aera na ot reviled lliw ,retsasid fo semit ni ,dna seilppus fo ecnanetniam.erac tneitap ycnegreme - Posted evacuation plans and practice drills taht erusne ot seeyolpme rof.ksir ta si ytefas rieht fi tnemtraped eht evael ot syaw evitanretla wonk yeht Biological Disasters - Many healthcare facilities have added biological incidents to their disaster plans. - As with other types of disasters, CS technicians should know their role. - Close communication with the Infection Prevention department is critical in this type of disaster. Biological Disasters (Cont.) - CS departments should utilize appropriate resources such as : The Centers for Disease Control and Prevention-pu rof )vog.cdc.www ;CDC(.staerht lacigoloib gnigreme gnidrager noitamrofni etad -ot The World Health Organization edivorp osla nac )gro.ohw.www ;OHW(.ecnadiug Coordination eht yb detcapmi saera lla dna noitneverP noitcefnI neewteb disaster is very important. EMPLOYEE Accidents and Injures - Even significant efforts to emphasize safety and accident prevention cannot eliminate all employee accidents, and CS technicians can still be injured on the job. - If an injury occurs, it must be: 1. Documented. 2. Reported to the appropriate administrative personnel, in compliance with OSHA regulations for healthcare facilities. PATIENT Accidents and Injures - CS professionals have responsibilities to help prevent patient injuries , accidents and infections. - They do so as they perform the important tasks of: Decontaminating. Inspecting. Testing. Assembling. Packaging. Sterilizing. Aseptic handling of sterile items. Delivering items according to established procedures. PATIENT Accidents and Injures (Cont.) - When their job is done correctly, risk to the patient is greatly reduced. - When a patient incident occurs, it must be promptly investigated dna documented. - Any practices or physical conditions within the facility that can cause a patient injury must also be investigated dna reported. - All healthcare workers ot yltpmorp sdrazah ro secitcarp efasnu troper tsum.ecnerrucer rieht tneverp dna stnedicca eziminim Employee Information and Training Employee Information and Training - No safety and risk management system can be successful without employee involvement. - Each employee must understand their role and responsibilities in maintaining a safe environment. - This requires education for all staff at all levels of experience. - All new CS employees should attend a health and safety orientation provided by the facility to become familiar with hazards and safety practices throughout the facility. Employee Information and Training (Cont.) - They should also attend a department-specific orientation that focuses on, at least, the following: An overview of the requirements contained in the hazard communication regulations, including employees' rights under the regulations. Notification of employees about any operations in their work area where hazardous substances are present. Employee Information and Training (Cont.) - A department-specific orientation:no sesucof osla Location and availability of written hazard communication program information. Physical and health effects of any hazardous substances they may encounter. Methods and observation techniques used to determine the presence or release of hazardous substances in the work area. Employee Information and Training (Cont.) - A department-specific orientation:no sesucof osla Strategies to lessen or prevent exposure to these hazardous substances through safe control and work practices, and use of PPE. Steps the department has taken to lessen or prevent exposure to these substances. Employee Information and Training (Cont.) - A department-specific orientation:no sesucof osla Instructions on how to read labels and review SDS to obtain appropriate hazard information. Disaster and fire plans, and the role of the Cs department in their development and implementation. Employee Information and Training (Cont.) - A department-specific orientation:no sesucof osla Emergency spill procedures. Employee Preparedness Employee Preparedness - An important factor in safety and risk management is employee awareness and preparedness. - Every employee should approach each shift and each task with 2 questions in mind: 1. "What can I do to ensure my safety and the safety of those in the facility "? 2. "What do I need to know to respond if I am faced with an emergency "? Employee Preparedness (Cont.) - Some strategies to help ensure emergency preparedness:edulcni Be familiar with safety policies. Ask questions if specific information is not understood. Be familiar with the chemicals used. Know how to handle them safely and what to do in the event of an emergency. Know how to work safely around equipment. Understand the hazards and know where emergency shut-off buttons are located. Employee Preparedness (Cont.) - Some strategies to help ensure emergency preparedness:edulcni osla Be familiar with evacuation routes, the location of fire extinguishers and fire alarm boxes. Leave each area safe. Wipe up spills, prevent trip hazards and do not cross contaminate. Maintain a safe environment at all times. Pay attention to detail. Report anything that threat- ens the safety and well-being of those in the facility. Employee Preparedness (Cont.) - The success of any safety system is dependent upon the individuals who work within that system. - Creating and maintaining a culture of safety reduces the risk for everyone. Conclusion - Central Service (CS) technicians play an important role in every healthcare facility's safety program. - It is important to know the expectations and be able to perform efficiently and calmly during any type of situation that may arise. - For the safety of patients, visitors, other employees and departmental staff, training and safety drills must be taken seriously, as should the adoption of safe work habits that help ensure preparedness for any unplanned emergency.