Polymer Basics PDF
Document Details
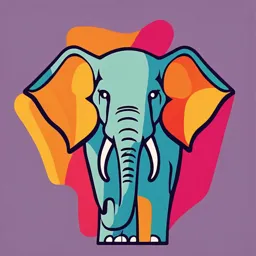
Uploaded by SalutaryConnemara2452
Tags
Summary
These lecture notes cover fundamental concepts in polymer science. Topics include polymer basics, classifications, morphology, and copolymer types. The material also delves into the properties of thermoplastics, thermosets, and factors influencing crystallinity. This is a good introduction for students.
Full Transcript
LECTURE 1 Introduction LECTURE 2 Polymer Basics Polymers are formed by polymerization of monomers Step growth every monomer can start polymerization thanks to an initiator Chain growth only few monomers can initiate growth but it goes extremely fast. Classification: synthetic...
LECTURE 1 Introduction LECTURE 2 Polymer Basics Polymers are formed by polymerization of monomers Step growth every monomer can start polymerization thanks to an initiator Chain growth only few monomers can initiate growth but it goes extremely fast. Classification: synthetic or semi-synthetic, often used in plastics. Additives are commonly incorporated. Applications: electronics, safety equipment, medical devices. Issues: production (plants/oil), usage (microplastics), and waste management (recycling/incineration/lanfill). Polymer Morphology Definition: Spatial arrangement of polymer chains (crystalline and amorphous regions) influencing mechanical, thermal, and optical properties. Types: Linear Polymers: Flexible, interactions via van der Waals and H-bonding. Branched Polymers: side chains off the main one. Lower density due to less packing. Cross-linked Polymers: Covalent bonds between chains (e.g., vulcanization of elastomers). Networked Polymers: Formed via physical or chemical interactions. Thermoplastics and Thermosets Thermoplastics: Can be melted and reshaped -> Easier to recycle because they don’t lose integrity when melted Thermosets: Decompose before melting (e.g., cured or cross-linked polymers). Copolymers Copolymers are polymers composed of two or more different monomers. The arrangement of these monomers along the polymer chain defines the type of copolymer: Random Copolymers: Monomers are distributed randomly along the chain. The sequence does not follow any specific order, leading to varied properties based on the monomers used. Alternating Copolymers: Monomers alternate in a regular pattern (e.g., A-B-A-B). This structure creates uniform properties derived from both monomers. Block Copolymers: Monomers are grouped into distinct segments (blocks). For example, one part of the chain consists entirely of monomer A, followed by a section of monomer B. Block copolymers often exhibit unique mechanical and physical properties due to phase separation between blocks. Graft Copolymers: A backbone polymer (e.g., monomer A) has side chains (grafts) of a different polymer (e.g., monomer B) attached. These structures are useful for modifying surface properties or creating specific functionalities Polymer Configuration and Conformation Configuration: Requires breaking covalent bonds Tacticity: atactic, isotactic, syndiotactic Chaining: Head-to-head, head-to-tail Isomers. Conformation: Shape changes via single bond rotation: random coil (amorphous), planar zig-zag (crystalline), helical (depends). Molecular Weight (MW) Importance: Determines polymer properties (e.g., mechanical strength, viscosity). Measures: Mn: Number average molecular weight. Mw: Weight average molecular weight. Mz: Z-average molecular weight. Dispersity (Đ): Ratio Mw/Mn, indicating the molecular weight distribution. Mv: Viscosity-average molecular weight -> obtained by extrapolating points from the Mark-Houwink Chain Entanglement Key to mechanical and viscoelastic properties. Parameters: Entanglement molecular weight (Me) -> distance between entanglements. Critical molecular weight (Mc ≈ 2 × Me) -> the bulkier the side group, the longer the chain has to be. Transition Temperatures Tg: Glass transition temperature (amorphous regions). Tm: Melting temperature (crystalline regions). Tc: Crystallization temperature (amorphous regions). Analysis Techniques GPC/SEC: Determines molecular weight distribution based on hydrodynamic volume –> calibration. Other Methods: Viscosimetry, ultracentrifugation, light scattering. Polymer Phases Polymers exhibit glassy, rubbery, crystalline, or melt phases. No vapor phase; decompose instead. LECTURE 3 Crystallinity in Polymers Discovery and Basics: Polymers cannot be 100% crystalline due to imperfections in their molecular arrangements. Typical degrees of crystallinity range from 30% to 80%, depending on polymer type. Requirements for Crystallization: Regular configurations (isotactic or syndiotactic) promote crystallization, while atactic polymers struggle. Symmetrical binding, e.g., head-to-tail configurations, favor crystal formation over head-to-head arrangements. Short and sparse side chains support crystallization; bulky or irregular ones impede it. Chains need intermediate flexibility; very rigid or highly flexible polymers cannot crystallize effectively. Crystal formation occurs when 𝑇𝑔 < 𝑇 < 𝑇𝑚. Factors Affecting Crystallinity: More regular copolymers have higher polymerization chances. A linear polymer generally has better chances at crystallizing. Strong inter- and intra-molecular forces (e.g., hydrogen bonds in polyamides) enhance crystallinity. Higher molecular weights generally promote crystallinity. Cooling rates, evaporation, and annealing conditions. Induced/spontaneous nucleation Structural Models: Fringed Micelle Model: Low crystallinity; crystals are dispersed within an amorphous matrix. Folded Chain Lamella Model: High crystallinity; chains fold into lamellar sheets, often creating ductile and tough materials. Crystal Types and Formation: Spherulites: o Formed by lamellae radiating from a central nucleus, interconnected by amorphous regions. o Found in many semi-crystalline polymers. Shish-kebab o Formed by an elongated middle portion (shish) and lamellar crystals perpendicularly organized around it (kebab) Enhancing Crystallinity: Controlled cooling from the melt (slower cooling enhances crystallinity). Annealing polymers at specific temperatures below their melting point. Using nucleating agents like metal salts of organic acids. Stretching polymers to orient chains and increase crystallinity. Crystallization Kinetics: Governed by the Avrami equation, which describes the rate and dimensionality of crystal growth. Crystallization temperature (𝑇𝑐) lies between 𝑇𝑔 and 𝑇𝑚; lower 𝑇𝑐 results in smaller but more numerous crystals. Analysis Methods: Differential Scanning Calorimetry (DSC): Instrument will measure the difference in the added heat to the pans as the temperature is kept the same between them Identifies thermal transitions like 𝑇𝑔, 𝑇𝑐, and 𝑇𝑚. Measures the heat required for melting or crystallization, revealing the degree of crystallinity. Dilatometry: Measures volume changes during phase transitions. X-ray Crystallography: Determines crystal structure and alignment. LECTURE 4 Glass Transition Temperature (𝑇𝑔) Definition and Behavior: Glassy State: Hard, rigid, and brittle, characterized by limited atomic motion (short-range vibrations and rotations). Rubbery State: Soft, flexible, with long-range rotational motion of chain segments (20–50 atoms). 𝑇𝑔 represents a temperature range between glassy and rubbery state, where chain segments gain coordinated motion, transitioning between these states. Key Influencing Factors: Higher 𝑀𝑤 increases 𝑇𝑔 due to decreased chain-end mobility. Chemical Structure: o Syndiotactic polymers have higher 𝑇𝑔 due to steric repulsion. o Stiff backbones elevate 𝑇𝑔. Side Chains: o Larger side groups increase 𝑇𝑔 by restricting chain movement. o Longer, flexible side chains act as plasticizers, lowering 𝑇𝑔 by increasing free volume. Intermolecular Forces: o Strong interactions (e.g., hydrogen bonds in poly(vinyl alcohol)) increase 𝑇𝑔. o Polar groups enhance packing, raising 𝑇𝑔. Cross-Linking forces chains closer together, reducing free volume and increasing 𝑇𝑔. Plasticizers soften the polymer by increasing free volume. Secondary Transitions: 𝛽 Transition: Motion of side groups or individual monomer units (e.g., phenyl rings in polycarbonates). 𝛾 Transition: Localized movements of small side or end groups (e.g., CH2 wagging in polyethylene). Polymer Blends Definition: Physical mixtures of polymers without covalent bonding. Types: Homologous Blends: Different molecular weights of the same polymer. Miscible Blends: Homogeneous at the molecular level with a single 𝑇𝑔. Immiscible Blends: Phase-separated with multiple 𝑇𝑔 values. Compatible Blends: Immiscible but exhibit uniform macroscopic properties due to interfacial interactions. Analysis: Miscibility determined via Differential Scanning Calorimetry (DSC). 1 𝑊1 𝑊2 Fox Equation: For miscible blends: = + W1, W2: weight fractions; 𝑇g,1, 𝑇g,2, 𝑇𝑔,𝑏𝑙𝑒𝑛𝑑 𝑇𝑔,1 𝑇𝑔,2 𝑇g,blend values of components). Applications: Form new materials with broad properties Adjust properties (e.g., strength, flexibility). Recycling and cost reduction by blending expensive resins with cheaper polymers. Plasticizers in blends lower 𝑇𝑔 for better processability, higher stability and less chances of leaching. LECTURE 5 Mechanical Properties of Polymers Types of Deforming Forces Tensile strength – Resistance to pulling forces. Compressive strength – Resistance to squashing forces. Shear strength – Resistance to sliding forces. Bending strength – Resistance to bending forces. Impact strength – Resistance to sudden forces. Creep & stress relaxation – Long-term deformation under constant stress. Hardness, friction, wear – Surface resistance to deformation and friction. Thermal Effects Heat deflection temperature – Temperature at which the polymer deforms under load. Softening temperature – The point at which the polymer softens. Thermal expansion – Change in size due to temperature changes. Failure Mechanisms in Polymers Types of Failure Ductile failure – Large deformation before breaking. Brittle failure – Little to no deformation before breaking. Crazing – Formation of small cracks that precede fracture. Common Failure Modes Creep failure – Gradual deformation over time under constant stress. Fatigue failure – Failure due to repeated stress cycles. Impact failure – Sudden fracture due to impact forces. Improving Failure Resistance with fibers, crosslinking, and polymer blending. Mechanical Testing of Polymers Common Mechanical Tests Tensile test – Measures stress-strain behavior. Compressive test – Measures resistance to compressive forces. Shear test – Determines response to parallel forces. Flexural test – Evaluates bending resistance. Impact test – Assesses toughness under sudden loads. Creep/deformation test – Examines long-term deformation under stress. Stress relaxation test – Determines how stress decreases over time under constant strain. Tensile Testing and Stress-Strain Behavior Procedure: A polymer sample is stretched until it breaks while measuring force and elongation. Output: Produces a stress-strain curve showing mechanical response. Key Terms Stress (σ) Force per unit cross-sectional area. 𝐹 Formula: σ = 𝐴 Unit: Pascal (Pa or N/m²). Strain (ε) Ratio of elongation to original length. ∆𝐿 Formula: 𝜖 = 𝐿0 Unitless. Young’s Modulus (E) 𝜎 A measure of stiffness, calculated from the slope of the stress-strain curve 𝐸 =. 𝜖 Higher modulus = more rigid material. Unit: Pascal (Pa). Factors Affecting Polymer Modulus 1. Temperature Below T𝑔 – Chains are rigid, modulus is high. At 𝑇𝑔 – Polymer softens, modulus decreases. Above 𝑇𝑔 – Rubber-like behavior, further modulus drop. Rubber plateau zone – Entangled chains restrict free movement. 2. Molecular Weight Higher molecular weight → More entanglements → Higher modulus above 𝑇𝑔. Below 𝑇𝑔 – Molecular weight has little effect as chains are immobile. 3. Crystallinity Higher crystallinity → Increased modulus due to rigid lamellae. Example: Polyethylene with different crystallinities shows different stiffness levels. 4. Crosslinking Increased crosslinking → Chains are locked in place → Higher modulus. Extreme crosslinking → Thermoset formation. 5. Frequency (Oscillating Analysis) 4. At low frequency/speed the chains have time to organize according to the stress. When frequency increases, entanglements affect more. 3. Chains are mobile but entanglements are not able to disentangle. 2. Chains lose their ability to ’follow’ the motion and segment motion is not fast enough. Modulus increasing. 1. Glassy state – chains are not mobile. Yielding and Plastic Deformation Yield Point: Stress at which 0.2% permanent strain occurs. Before yield point: Elastic deformation (returns to original shape). At yield point: Plastic deformation begins (permanent changes). Necking Formation of a localized thinner region. Occurs after the yield point. Stress increases in the necked region due to reduced cross-sectional area. Ductile vs. Brittle Behavior Ductile polymers: Stretch significantly before breaking. Brittle polymers: Fracture with little deformation. Crystalline polymers: Yielding starts in amorphous regions before crystals align. Mechanical Property Definitions Stiffness: Resistance to deformation (high modulus). Strength: Resistance to breaking under load. Brittleness: Tendency to fracture without deformation. Ductility: Ability to deform plastically before breaking. Toughness: Ability to absorb energy before fracture (area under stress-strain curve). LECTURE 6 Compressive Testing Definition: Measures material response under compression. Key Properties Measured: Compressive modulus – Stiffness under compression. Yield point – Stress level at which plastic deformation begins. Compressive strength – Maximum stress before failure. Thermoplastics Behavior: Excessive deformation before failure. Reported as stress at specific deformations (e.g., 1%, 2%, or 10%). Shear and Bending Properties Shear Testing: Measures material response to forces acting parallel to each other. Shearing forces distort the object rather than pulling or compressing it. Bending (Flexural) Testing: Important for beams, panels, and housings. Three-point bending: V-shaped deformation. Four-point bending: U-shaped deformation. Flexural modulus: Ratio of stress to strain (similar to Young’s modulus but for bending). Impact Strength and Toughness Definition: Ability to withstand sudden loads without fracturing. Testing Methods: Izod Test: Specimen placed vertically with notch facing striker. Charpy Test: Specimen placed horizontally with notch away from striker. Results Reported As: Energy (𝐹𝑟𝑎𝑐𝑡𝑢𝑟𝑒 𝑒𝑛𝑒𝑟𝑔𝑦 = 𝑚𝑔(ℎ0 − ℎ𝑓 )) absorbed per unit area (J/m²). Impact strength depends on specimen geometry. Long-Term Deformation: Creep & Stress Relaxation Creep: Definition: Time-dependent deformation under constant stress (below yield point). Stages: Primary Creep: Rapid initial deformation, then slows. Secondary Creep: Constant deformation rate. Tertiary Creep: Rapid deformation leading to failure (common at high stress or temperature). Temperature Dependence: Above 𝑇𝑔, chains can move past each other, increasing creep -> Higher temperature = faster creep. Creep Data Representation: Creep curve: Strain vs. time for different stress levels. Isometric curve (Stress Relaxation): Stress vs. time for constant strain. Isochronous curve: Stress vs. strain at different times. Creep Testing Procedure: 1. Heat specimen to required temperature. 2. Measure initial length. 3. Apply load quickly and without shock. 4. Record elongation over time (50+ readings recommended). Duration: 2,000 – 10,000 hours (accelerated testing at higher temperatures). Stress Relaxation Definition: Decrease in stress over time while strain remains constant. Occurs Due To: Delayed molecular movement. Reorganization of polymer chains. Hysteresis and Mullins Effect Hysteresis: Energy loss due to differences in loading/unloading behavior. The difference in areas under the curves represents energy loss through heat Seen in rubbers and elastomers. Important in tires and vibration-damping materials. Mullins Effect: Softening of elastomers under cyclic loads. Occurs when strain exceeds previous maximum. Leads to permanent changes in material properties. Surface Properties: Hardness, Friction, Wear Hardness: Resistance to local surface deformation (wear, cutting, machining). Testing Methods: Brinell Hardness Test (HB): Steel sphere indentation. Rockwell Hardness Test (HR): Indenter depth measurement. Vickers Hardness Test (HV): Diamond pyramid indentation (microhardness). Friction: Resistance to sliding between surfaces. Key Factors: Adhesion (dominant in smooth surfaces, low speeds). Deformation (dominant in rough surfaces, high speeds). Wear: Loss of material due to surface interaction. Types: Adhesive wear: Small particles detach due to surface adhesion. Frictional heating wear: Excess heat causes local melting and damage. Minimizing Wear: High-molecular-weight polymers. Internal lubricants (e.g., PTFE). Reinforcing fillers (glass, carbon fibers) – but can increase friction. Summary of Key Concepts Deformation and Testing: Polymers undergo elastic deformation first, then plastic deformation (yielding). Ductile polymers: Exhibit necking and large plastic deformation. Brittle polymers: Fail suddenly without plastic deformation. Tough materials: Absorb more energy before failure. Deformation Influences: Temperature: Softens polymers, increases deformation. Frequency/Speed: Faster loading increases stiffness. LECTURE 7 Thermal Properties of Polymers Key Temperatures: Melting Temperature (𝑇𝑚) – Transition from solid to liquid (crystalline polymers). Glass Transition Temperature (𝑇𝑔) – Transition from glassy to rubbery state (amorphous polymers). Crystallization Temperature (𝑇𝑐) – Temperature where a polymer crystallizes from the melt. Heat Deflection Temperature (HDT) Definition: The highest temperature at which a polymer can withstand a specific load without significant deformation. Also Known As: Heat Distortion Temperature (HDTUL), Deflection Temperature Under Load (DTUL). Test Procedure: 1. Sample immersed in silicone oil bath. 2. Temperature of oil increased gradually. 3. Load applied. 4. Deflection temperature recorded at 0.25 mm. HDT vs. 𝑇𝑔 or 𝑇𝑚: 𝑇𝑔 describes chain mobility, while HDT measures structural stiffness under load. Effect of Additives: Reinforcements (e.g., fibers) → Increase HDT (stiffer material). Plasticizers → Decrease HDT (increase flexibility). Fillers → Varied effect on HDT but do not affect 𝑇𝑔. Softening Temperature: Vicat Softening Temperature (VST) Definition: Temperature at which a 1 mm² indenter penetrates a polymer sample by 1 mm under a specific force. Key Differences from HDT: Vicat measures softening, while HDT measures structural deflection under load. HDT is more influenced by composite structure than Vicat. Thermal Expansion Definition: The tendency of a polymer to expand when heated. Measured as the coefficient of thermal expansion (linear, areal, or volumetric). ∆𝐿 Formula: 𝛼 = 𝐿0 ∙∆𝑇 α = Coefficient of thermal expansion (unit: 1/𝐾). Δ𝐿 = Change in length. 𝐿0 = Original length. Δ𝑇 = Temperature change. Factors Affecting Thermal Expansion: Higher bond energy → Lower expansion (e.g., high-melting-point materials expand less). Polymers expand 2–20 times more than metals. Crosslinking and high crystallinity reduce expansion. Mechanical Failure of Polymers Major Failure Modes: Excessive Deformation: Large strain without breaking (e.g., rubber-like materials). Ductile Failure: Yielding occurs before fracture. Brittle Failure: Sudden fracture with little deformation. Crazing: Formation of microvoids in glassy polymers under tensile stress (not a crack but may lead to failure). Ductile vs. Brittle Failure Ductile Failure: Polymer undergoes large-scale plastic deformation before breaking. Yielding marks the onset of failure. Example: PVC in pressurized tubing. Brittle Failure: Fracture occurs with minimal deformation. Happens at stress concentrations (e.g., cracks, impurities, large filler particles). No prior warning before failure. Smaller cracks or higher surface energy → More resistance to fracture. Crazing: Occurs for glassy polymers in excessive tensile stress before yielding (below Tg). Often occurs in highly strained locations during bending. Microcavities with highly oriented polymers in fibrillar shape which bridge the cavity surfaces. Crazes are not cracks and can continue to sustain loads after they are formed. Fatigue Failure Definition: Crack growth due to cyclic loading. Process: 1. Crack initiates due to repeated stress. 2. Crack propagates slowly with each stress cycle. 3. Final failure is brittle when the remaining material cannot bear the load. 4. Fatigue failure occurs at stress levels much lower than immediate failure loads. Factors Affecting Fatigue: Amplitude and frequency of stress cycles. Component size and shape. Material properties and environmental conditions. Crack density and pre-existing flaws. Prevention of Mechanical Failures 1. Design Considerations Avoid stress concentrators (e.g., notches, sharp corners, sudden thickness changes). Use Finite Element Method (FEM) simulations to analyze stress distribution. Design components below yield stress limits. 2. Material Selection Choose materials based on: Mechanical properties. Temperature resistance. Chemical stability (oxidants, solvents). Ductility is the most important factor in preventing brittle failure. 3. Material Modification Toughening with rubber phases: Copolymerization or direct blending. Rubber inclusion lowers yield strength but increases ductility. Example: High-impact polystyrene (HIPS). LECTURE 8 Introduction to Rheology Definition: Rheology is the science of how liquids flow and solids deform. Rheometry: Experimental methods to measure rheological properties. Viscosity (η) Definition: Resistance of a material to shearing forces. Follows Newton’s law: τ = ηγ o τ = Shear stress (Pa). o η = Viscosity (Pa·s). o γ = Shear rate (1/s). Key Factors Affecting Viscosity: o Temperature: Higher temp → Lower viscosity. o Pressure: Higher pressure → Higher viscosity. o Time: Some materials show viscosity changes over time. o Molecular weight: Higher MW → Higher viscosity. o Additives (e.g., fillers, lubricants): Can increase or decrease viscosity. Newtonian vs. Non-Newtonian Fluids Newtonian Fluids (Ideal Behavior) Viscosity is constant, regardless of shear rate. No elastic properties (purely viscous). Non-Newtonian Fluids (Real-World Behavior) Viscosity changes with shear rate. Polymeric materials are non-Newtonian and exhibit viscoelasticity: o Elastic behavior (energy storage). o Viscous behavior (energy dissipation). Time-Independent Flows Shear Thinning (Pseudoplasticity) o Definition: Viscosity decreases with increasing shear rate. o Cause: Polymer chains uncoil and align with the flow. o Examples: ▪ Ketchup: Flows easily when shaken. ▪ Polymer melts: Easier to process at high shear rates. o Effect on Processing: ▪ Allows processing of large molecules at lower temperatures. ▪ Leads to easier extrusion and injection molding. Shear Thickening (Dilatancy) o Definition: Viscosity increases with increasing shear rate. o Cause: Particles become disorganized, increasing resistance. o Examples: ▪ Cornstarch in water ("Oobleck"). ▪ Wet sand on the beach. o Can cause processing problems if viscosity increases too much. Time-Dependent Flows 1. Thixotropy Definition: Viscosity decreases over time under constant shear stress. Example: Paint – becomes thinner when stirred but thickens when left undisturbed. 2. Rheopexy Definition: Viscosity increases over time under constant shear stress. Example: Synovial fluid (joint lubrication) – becomes stiffer under continuous movement. Real Thixotropy/Rheopexy: Reversible viscosity changes (e.g., paint). Apparent Thixotropy/Rheopexy: Irreversible changes (e.g., crosslinking or evaporation). LECTURE 9 Bingham Model & Yield Stress Bingham Fluids: Materials that behave as a solid at low stress but flow like a liquid above a threshold (yield stress). Flow Equation (Bingham Model): τ = τ0 +ηpl γ o τ0 = Yield stress. o ηpl = Plastic viscosity (constant beyond yield stress). Benefits of Bingham Flow Prevents phase separation. Reduces sedimentation and flocculation. Improves stability and shelf-life of emulsions and suspensions. Types of Non-Newtonian Flows (Expanded) 1. Shear Thinning (Pseudoplasticity): o Viscosity decreases with shear rate. o Example: Paint, polymer melts. 2. Shear Thickening (Dilatancy): o Viscosity increases with shear rate. o Example: Cornstarch in water, wet sand. 3. Bingham Flow: o Fluid only flows after yield stress is exceeded. o Example: Toothpaste. 4. Bingham Pseudoplastic: o Yield stress + shear thinning behavior. 5. Bingham Dilatant: o Yield stress + shear thickening behavior. 4. Rheological Effects in Polymers Kaye Effect A shear-thinning liquid "bounces" when poured. Why? A thin layer of reduced viscosity forms where the liquid meets itself. Weissenberg Effect Fluid climbs a rotating rod instead of moving outward. Why? Sheared polymer chains seek lower energy states (stretching chains lowers the energy), pulling material upwards. Barus Effect (Die Swell) Polymers expand after exiting a narrow opening. Why? Chains relax and regain entangled state after high shear. Significance: Important in extrusion processes. Molecular Weight & Viscosity Relationship Zero-Shear Viscosity (η0): o Viscosity measured at very low shear rates. o Used to estimate molecular weight and polymer stability. o Formula: 𝜂0 = 𝑘 ∙ 𝑀𝑤𝛼 ▪ α ≈ 3.4 for polymers over Mwc (Critical MW), 1 for polymer under. ▪ K is a temperature dependant constant. Flow Behavior of Polymer Melts Three Key Regions in Flow Curve: 1. First Newtonian Region: Low shear rate, viscosity constant. 2. Power Law Region: Shear thinning behavior as polymer chains align. 3. Second Newtonian Region: At very high shear rates, viscosity stabilizes. Types of Viscosity Measurements: 1. Dynamic Viscosity (η): Measured under applied shear. 2. Apparent Viscosity (ηapp): Instantaneous viscosity in non-Newtonian fluids. 3. Kinematic Viscosity (ν): Ratio of dynamic viscosity to density. 4. Zero-Shear Viscosity (η0): Extrapolated viscosity at very low shear rate. 5. Complex viscosity η*: Complex modulus divided by the angular frequency, acquired when doing angular frequency 6. Relative viscosity ηrel or ηr: Specific viscosity divided by concentration. 7. Inherent viscosity ηinh Used for determination of intrinsic viscosity 8. Intrinsic viscosity, [η]: Obtained by extrapolating the reduced and inherent viscosity at different concentrations to the (infinitely dilute) zero-concentration. Mark-Houwink Equation Relates intrinsic viscosity to molecular weight: [η] =K Mα o [η] = Intrinsic viscosity. o K, α = Constants specific to polymer-solvent system. o M = Molecular weight. LECTURE 10 Rheological Measurement Methods Rheology is measured using various instruments depending on fluid properties. Different methods measure viscosity, elasticity, and flow behavior. Common Measurement Techniques: Ostwald Viscometer (U-Tube) o Measures kinematic viscosity based on gravity-driven flow. o Pros: Quick, cheap, simple. o Cons: No shear rate control, unsuitable for highly viscous or structured liquids. Ubbelohde Viscometer o Similar to Ostwald but includes a third arm to level pressure, making measurements independent of sample volume. o Pros: More precise than Ostwald. o Cons: Still no control over shear rate. Melt Flow Indexer (MFI) o Measures mass (g) of polymer extruded in 10 minutes under controlled temperature and weight. o Pros: Fast, easy, industry standard. o Cons: Single shear rate, poor for detailed viscosity analysis. Capillary Viscometer o Similar to MFI but varies flow pressure, allowing variable shear rate testing. o Pros: High shear rates, relevant for polymer processing. o Cons: Requires multiple measurements for full viscosity profile. Brookfield Viscometer o Measures viscosity using a rotating spindle. o Pros: Common in quality control. o Cons: Limited data, not suitable for complex fluids. Cylindrical Rheometers (Searle & Couette) o Two-cylinder system: Inner or outer cylinder rotates to control shear rate. o Pros: Uniform shear rate, accurate viscosity measurement. o Cons: Possible secondary flows affecting accuracy. Cone & Plate Rheometer o Uses a small cone rotating on a flat plate to ensure constant shear rate. o Pros: Small sample size, good heat control. o Cons: Limited to low shear rates, unsuitable for suspensions. Parallel Plate Rheometer o Two plates with variable gap distance. o Pros: Handles particle suspensions, good for low shear rate studies. o Cons: Non-uniform shear distribution. Watch out for wall slip -> might be treated by crosshatched pattern on the plates. Advanced Rheological Techniques 1. Rotational Rheometer Measures flow and deformation by rotating a sample under controlled stress. Used for: Polymers, gels, emulsions. 2. Dynamic Mechanical Analysis (DMA) Measures elastic and viscous properties under oscillating stress. Key advantage: Can test solids, films, fibers, and viscous fluids. 3. Oscillating Rheometry (DMA) Applies sinusoidal strain and measures storage & loss modulus. Key Parameters: o Storage modulus (G′ or E’): Measures elastic response (energy stored). o Loss modulus (G′′ or E’’): Measures viscous response (energy dissipated as heat). o Phase angle (δ): Defines the balance between elasticity (0°) and viscosity (90°). o Loss tangent (tan δ): Damping coefficient: tan δ = G′′/G′ ▪ Tan δ > 1 → Viscous behavior dominates. ▪ Tan δ < 1 → Elastic behavior dominates. Key Concepts in Oscillating Rheology 1. Storage & Loss Modulus High G′ (Storage Modulus): Solid-like behavior. High G′′ (Loss Modulus): Liquid-like behavior. 2. Cross-Over Point The temperature or frequency where G′=G′′ Gel point: When G’ = G’’, indicating transition from liquid-like to solid-like behavior. Vitrification: The slowing of cure rate as the material becomes too viscous for bulk reaction to continue. 3. Time-Temperature Superposition Used to extend measurement range by shifting curves along the time/frequency axis. Based on Arrhenius equation (high T range) or WLF equation (T near Tg). Not applicable for semicrystalline polymers, blends, or temperature-sensitive materials. LECTURE 11 Oscillating analysis measurement Techniques Amplitude sweep: Determines the Linear Viscoelastic Region (LVR) where the material behaves elastically. Frequency sweep: Examines how viscoelastic properties vary with frequency. Temperature ramp: Analyzes temperature dependence of viscoelastic behavior. Time ramp: Observes changes over time, useful for studying degradation or cross-linking. Cox-Merz Rule Steady-state shear viscosity at a given shear rate ≈ complex viscosity at the same frequency. Valid for: Polymer melts, concentrated/semi-dilute solutions. Not applicable for: Cross-linked systems, particulate suspensions. Deborah Number (De) Determines whether a material behaves as solid-like or liquid-like. Formula is De = tc /tp tc = relaxation time tg = observation time o De > 1: Elastic response.