Philippine Labor Sector Workplace Safety History PDF
Document Details
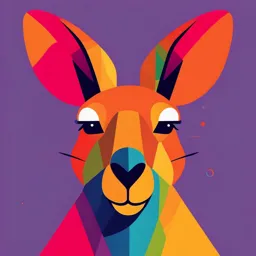
Uploaded by LovingStatistics
Sorsogon State University
Tags
Summary
This document provides a brief history of workplace safety promotion in the Philippine labor sector, highlighting key legislation and initiatives like the Union Obrera, Commonwealth Act No. 104, and Presidential Decree 442. It also discusses the 5S system, a workplace efficiency and waste reduction technique.
Full Transcript
***[REVIEWER IN OSH]*** **BRIEF HISTORY IN THE PROMOTION OF A HEALTHY AND SAFE WORKPLACE IN THE PHILIPPINE LABOR SECTOR.** **1902 - Unión Obrera Democrática Filipina** - \"to improve working conditions through protective labor legislation; locate work for the unemployed and assist their...
***[REVIEWER IN OSH]*** **BRIEF HISTORY IN THE PROMOTION OF A HEALTHY AND SAFE WORKPLACE IN THE PHILIPPINE LABOR SECTOR.** **1902 - Unión Obrera Democrática Filipina** - \"to improve working conditions through protective labor legislation; locate work for the unemployed and assist their families; provide free education for workers\' children; assist sick members and those in distress; and emancipate workers through saving and related projects. **1936 -- Commonwealth Act No. 104 -- First Industrial Safety Law** - An Act Authorizing the Secretary of Labor to Promulgate and Enforce Rules, Regulations, and Orders for the Safety of Persons Employed in Mines, Quarries, Metallurgical Operations and Other Enterprises **1974 - Presidential Decree 442 -- Labor Code of the Philippines** - As embodied in Article 162, Chapter II of Book IV of the Labor Code of the Philippines, *"The Secretary of Labor and Employment shall by appropriate orders set and enforce mandatory occupational safety and health standards* to eliminate or reduce occupational safety and health hazards in all work places and institute new and update existing programs to ensure safe and healthful working conditions in all places of employment" **1978-- Occupational Safety and Health Standards (YELLOW BOOK** - Formulated in 1978 - Adopted through the tested democratic machinery of tripartism - Considered as a landmark in Philippine labor and social legislation - Amended in 1989, to provide all establishments with better tool in promoting and maintaining a safe and healthful work environment. **2018 -- Republic Act 11058 "An Act Strengthening Compliance to Occupational Safety and Health Standards and Providing Penalties for the Violation Thereof"** - DOLE release Department Order 198-18 as the Implementing Rules and Regulations (IRR) of RA 11058 ***ENFORCEMENT AND ADMINISTRATION*** - The DOLE shall be responsible for the administration and enforcement of OSH laws in all workplaces. - Local Government Units may be authorized by the Secretary of DOLE to enforce safety and health standards within their respective jurisdiction. **TECHNICAL SAFETY INSPECTION** - Refers *to inspection for the purpose of safety determination of boilers, pressure vessels, internal combustion engines, electrical installations, elevators, hoisting and other equipment.* **GENERAL SAFETY AND HEALTH SAFETY INSPECTION** - Refers to *inspection of the work environment*, including the location and operation of machinery other than those covered by technical safety inspection, adequacy of work space, ventilation, lighting, conditions of work environment, handling, storage or work procedures, protection of facilities and other safety and health hazards in the workplace. **ART. 128 VISITORIAL AND ENFORCEMENT POWER** - The Secretary of Labor or his duly authorized representatives including labor regulation officers, *shall have access to employers records and premises any time of the day or night whenever work is undertaken therein,* the right to copy there from, to question any employee and investigate any fact, condition or matter which may be necessary to determine violations or which may aid in the enforcement of this code and of any labor law, wage order or rules and regulations issued pursuant there to. **5S SYSTEM** - The 5S system is a lean manufacturing tool that improves workplace efficiency and eliminates waste. There are five steps in the system, each starting with the letter S: - **Sort** - **Set in Order** - **Shine** - **Standardize** - **Sustain** 5S was created in Japan, and the original "S" terms were in Japanese, so English translations for each of the five steps may vary. The basic ideas and the connections between them are easy to understand, though. **Sort *Seiri* ([tidines]s)** -Remove unnecessary items from each area **Set in Order *Seiton* ([orderliness])** -Organize and identify storage for efficient use **Shine *Seiso* ([cleanliness]**) -Clean and inspect each area regularly **Standardize *Seiketsu* *(*[standardization]*)-*** Incorporate 5S into standard operating procedures **Sustain *Shitsuke* ([discipline])** -Assign responsibility, track progress, and continue the cycle Sustaining a 5S program can mean different things in different workplaces, but there are some elements that are common in successful programs. - **Management support** -- Without visible commitment from managers, the 5S processes won't stick around. Supervisors and managers should be involved in auditing the 5S work processes, and getting feedback from workers. - **Department tours** -- Bringing teams from one department to visit other departments will help familiarize the entire workforce with the processes of your facility. This type of "cross pollination" helps to spread good ideas, and inspires people to come up with new ways to improve the 5S implementation. - **Updated training** -- As time passes, there may be changes in your workplace, such as new equipment, new products, or new work rules. When this happens, revise your 5S work standards to accommodate those changes, and provide training on the new standards. - **Progress audits** -- The standards that are created in the 5S program should provide specific and measurable goals. - **Performance evaluations** -- Once you know your goals are reasonable, make performance part of each employee evaluation. **BUNOS S** (*SAFETY)* -with many lean programs, it's easy to focus only on those goals, and lose sight of the human factor. Worker safety is critical. That's why many facilities add another step to the 5S cycle, calling the result "6S" --- with Safety. Benefits of a 5S Program because 5S focuses on improving a workplace, and different workplaces may have little in common, it can be hard to predict the exact results of using the program. However, some benefits are almost always found: ***Better time usage*** - Getting rid of unwanted materials and organizing the important tools and supplies will eliminate clutter and confusion. Workers spend less time finding and retrieving what they need, and can be more productive instead. ***Less wasted space*** -- Eliminating unnecessary material stockpiles and consolidating tool storage will clear up room for more useful applications. Every square foot of floor space has a cost, and getting the most out of that investment will maximize your facility's profitability. ***Reduced injury rates*** -- Organizing work areas for efficiency and ease of use will reduce the movements needed for workers to do their jobs. Removing clutter and routinely cleaning up spills will eliminate trip hazards. As a result, workers will experience less fatigue and fewer injuries. ***Reduced equipment downtime*** -- When tools and equipment are kept clean, routinely inspected, and used in a standardized way, preventative maintenance is much easier, and major failures can often be prevented entirely. ***Improved consistency and quality*** -- Standardizing work processes will reduce variations and mistakes. By eliminating faults and failures, overall productivity can be dramatically improved. ***Heightened employee morale*** -- When 5S principles are used effectively, workers see that their input is valued, and their performance is recognized. This creates an environment where workers can feel pride in their work, and take an interest in improving their company. **UNSAFE ACTS/ CONDITIONS** ***UNSAFE ACTS*** - Mag first move - Titigan sya - Mag papansin - Magparinig sa FB ***UNSAFE CONDITIONS*** - D makatulog kakaiship shayo - Na pol shayo - Ngumingiti mag isha - Natutulala shayo - Kkunting dikit lang kinilig na - Nag aassume HOUSEKEEPING - The management and routine support activities of running and maintaining an organized physical institution occupied or used by people DUTIES AND RESPONSIBLITIES OF HOUSEKEEPER - Cleaning and reporting any safety hazards to the homeowner or manager in charge. MAIN PURPOSE OF HOUSEKEEPING - To maintain a high level of cleanliness and hygiene in the home **Elements of an effective housekeeping program** - **Maintenance** - e involves keeping buildings, equipment, and machinery in safe, efficient working order and in good repair. - **Dust and Dirt Removal -** Enclosures and exhaust ventilation systems may fail to collect dust, dirt and chips adequately. Vacuum cleaners are suitable for removing light dust and dirt that is not otherwise hazardous - **Employee Facilities** - Enclosures and exhaust ventilation systems may fail to collect dust, dirt and chips adequately. Vacuum cleaners are suitable for removing light dust and dirt that is not otherwise hazardous - **Surfaces** - *[Floors:]* Poor floor conditions are a leading cause of incidents so cleaning up spilled oil and other liquids at once is important. - *[Walls]*: Light-coloured walls reflect light while dirty or dark-coloured walls absorb light. Contrasting colours warn of physical hazards and mark obstructions such as pillars. - **Maintain Light Fixtures** - Dirty light fixtures reduce essential light levels. Clean light fixtures can improve lighting efficiency significantly. - **Aisles and Stairways** - Aisles should be wide enough to accommodate people and vehicles comfortably and safely. Aisle space allows for the movement of people, products and materials. Warning signs and mirrors can improve sight lines in blind corners. - **Spill Control -** The best way to control spills is to stop them before they happen. Regularly cleaning and maintaining machines and equipment is one way. Another is to use drip pans and guards where possible spills might occur - **Tools and Equipment** - Tools require suitable fixtures with marked locations to provide an orderly arrangement.