Definitions of Quality by Quality Gurus PDF
Document Details
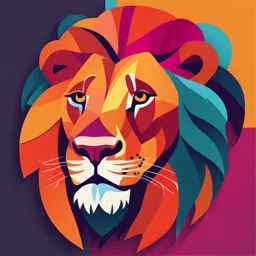
Uploaded by PleasantGhost
Tags
Related
- Revista de la Universidad de La Salle (2009) - Historia, Evolución e Importancia para la Competitividad - PDF
- Different Definitions of Quality by Quality Gurus (PDF)
- Lesson 1 - Introduction to Quality PDF
- Chapter 3: Gurus of Total Quality Management PDF
- Lesson 1: Introduction to Total Quality Management PDF
- Chapter 2 Quality Theory PDF
Summary
This document provides various definitions of quality from different quality gurus. It also covers topics like translating voice of customer (VOC) to requirements and different types of statistics.
Full Transcript
DIFFERENT DEFINITIONS OF QUALITY BY QUALITY GURUS NAME DEFINITION “Quality is defined from the customer’s point of Deming view as anything that enhances their satisfaction”...
DIFFERENT DEFINITIONS OF QUALITY BY QUALITY GURUS NAME DEFINITION “Quality is defined from the customer’s point of Deming view as anything that enhances their satisfaction” “Fitness for use. Those product features which Juran meet the needs of customers & thereby provide product satisfaction. Freedom from deficiencies.” “The totality of features and characteristics of a ASQ product or service that bear on its ability to satisfy stated or implied needs” “Quality is defined as knowledge of agents that COPC would enable them to provide accurate & consistent solution to the customer at the very first attempt” “Degree to which a set of inherent characteristics ISO of a product or service, fulfill requirements” Copyright © 2018 Advanced Innovation Group Pro Excellence | All Rights Reserved DIFFERENT DEFINITIONS OF QUALITY BY QUALITY GURUS Simply stated, quality comes from meeting customer expectations. This occurs as a result of four activities: Understanding customer requirements Designing products & services that satisfy those requirements Developing processes that are capable of producing those products & services Controlling & managing those processes so they consistently delivery to their capabilities Copyright © 2018 Advanced Innovation Group Pro Excellence | All Rights Reserved TRANSLATE VOC TO REQUIREMENTS (STEPS) TOPIC: VOC TO REQUIREMENTS (STEPS) Critical to Quality (CTQ) Voice of Customer Critical Customer Criteria (Requirement / (Verbatim) (Need) Performance) Write excerpt from Take the exact voice of customers verbatim Write the customer’s need customer showcasing the in measurable terms customer’s need Steps to Translate VOC to Requirements: 1. Take the exact voice of customer & update in column 1 “Voice of Customer (Verbatim)” 2. Write in column 2 the excerpt from customers verbatim showcasing the customer’s need 3. Write the customer’s needs in measurable terms Copyright © 2018 Advanced Innovation Group Pro Excellence | All Rights Reserved CAUSE- SOLUTION MATRIX TOPIC: CAUSE-SOLUTION MATRIX Copyright © 2018 Advanced Innovation Group Pro Excellence | All Rights Reserved WHAT IS STATISTICS? TOPIC: WHAT IS STATISTICS? Statistics is a way to get information from data Statistics is a tool to create new understanding from a set of numbers. Statistics can be better understood under two branches: 1. Descriptive Statistics 2. Inferential Statistics Copyright © 2018 Advanced Innovation Group Pro Excellence | All Rights Reserved WHAT IS INFERENTIAL STATISTICS? TOPIC: WHAT IS INFERENTIAL STATISTICS? Inferential statistics is a set of methods used to draw conclusions or inferences about characteristics of populations based on data from a sample Population: A complete set of data “N” Sample: A subset of data representing the population “n” Copyright © 2018 Advanced Innovation Group Pro Excellence | All Rights Reserved WHAT IS DESCRIPTIVE STATISTICS? TOPIC: WHAT IS DESCRIPTIVE STATISTICS? Descriptive Statistics is a method of organizing, and presenting data in a convenient and informative way. The actual method used depends on what information we would like to extract. Copyright © 2018 Advanced Innovation Group Pro Excellence | All Rights Reserved PROCESS FOCUS: BASELINE, ENTITLEMENT & BENCHMARK TOPIC: PROCESS FOCUS Process Baseline: It is the average, long-term performance level of a process when all the input variables in the process are running in an unconstrained fashion Process Entitlement: It is the best case, short-term performance level of a process when all the input variables in the process are centered and in-control Process Benchmark: It is the performance level of the process deemed by comparison to the best process possible It takes us to the best that anyone has ever done. In practical terms this means researching and finding the best that has ever been in the industry Copyright © 2018 Advanced Innovation Group Pro Excellence | All Rights Reserved THE DMAIC ROADMAP TOPIC: DMAIC ROADMAP & TOOLKITS – AN OVERVIEW Copyright © 2018 Advanced Innovation Group Pro Excellence | All Rights Reserved THE DMAIC ROADMAP TOPIC: DEFINE PHASE OVERVIEW Copyright © 2018 Advanced Innovation Group Pro Excellence | All Rights Reserved THE DMAIC ROADMAP TOPIC: MEASURE PHASE OVERVIEW Copyright © 2018 Advanced Innovation Group Pro Excellence | All Rights Reserved THE DMAIC ROADMAP TOPIC: ANALYZE PHASE OVERVIEW Copyright © 2018 Advanced Innovation Group Pro Excellence | All Rights Reserved THE DMAIC ROADMAP TOPIC: IMPROVE PHASE OVERVIEW Copyright © 2018 Advanced Innovation Group Pro Excellence | All Rights Reserved THE DMAIC ROADMAP TOPIC: CONTROL PHASE OVERVIEW Copyright © 2018 Advanced Innovation Group Pro Excellence | All Rights Reserved THE DMAIC ROADMAP TOPIC: DMAIC TOOLKITS Copyright © 2018 Advanced Innovation Group Pro Excellence | All Rights Reserved DEFINE YOUR CUSTOMERS TOPIC: DEFINE YOUR CUSTOMERS A customer is the one who buys your products or services. He is the one who receives the process output. Customers can be classified as: OR Copyright © 2018 Advanced Innovation Group Pro Excellence | All Rights Reserved VOICE OF CUSTOMER (VOC) TOPIC: METHODS TO CAPTURE VOC VOC methodology can be used to capture customer needs. It helps capture these needs through stated verbatim comments. Distinct customer categories (AICPS): VOC Capture Methods include: Surveys Interviews Focus Groups Suggestions Observations Copyright © 2018 Advanced Innovation Group Pro Excellence | All Rights Reserved AFFINITY DIAGRAM TOPIC: AFFINITY DIAGRAM Affinity diagram is a tool that gathers large amount of language data (i.e. ideas, opinions, issues) and organizes them into groupings based on their natural relationship Example of an Affinity Diagram Copyright © 2018 Advanced Innovation Group Pro Excellence | All Rights Reserved AFFINITY DIAGRAM TOPIC: STEPS TO CREATE AN AFFINITY DIAGRAM Copyright © 2018 Advanced Innovation Group Pro Excellence | All Rights Reserved TRANSLATING NEEDS TO REQUIREMENTS TOPIC: TRANSLATING NEEDS TO REQUIREMENTS Copyright © 2018 Advanced Innovation Group Pro Excellence | All Rights Reserved KANO ANALYSIS TOPIC: WHAT IS KANO ANALYSIS? Kano Analysis helps you to analyze customer requirements and prioritize them in the order of importance for the customer. There are three Kano Categories: Dissatisfiers or Basic Needs (the Must-Be’s): These are expected features or characteristics These needs are typically unspoken If not fulfilled, the customer will be highly dissatisfied Satisfiers or Performance Needs (One-Dimensional Needs): These are the standard characteristics of products/services They increase/decrease satisfaction levels by their degree of presence These needs are typically spoken Delighters or Excitement Needs: These are unexpected features that impress your customers They help your company earn the right recognition These needs are typically unspoken Copyright © 2018 Advanced Innovation Group Pro Excellence | All Rights Reserved STEPS TO CONSTRUCT A KANO ANALYSIS TOPIC: STEPS TO CONSTRUCT A KANO ANALYSIS? 1. Classify the requirements as: Must-Be’s One-Dimensional Delighters 2. Finish the Kano Diagram by adding specific requirements to the specific classifications on the diagram 3. Prioritize the requirement Kano Analysis Grid Copyright © 2018 Advanced Innovation Group Pro Excellence | All Rights Reserved CTQ DRILL DOWN TREE TOPIC: WHAT IS A CTQ DRILL DOWN TREE? A CTQ Drill Down Tree links Project “Y” to Business “Y” Bounds the project well to make it more manageable Used when requirements are to be converted to metrics CTQ DRILL DOWN TREE EXAMPLE Copyright © 2018 Advanced Innovation Group Pro Excellence | All Rights Reserved BUSINESS CASE TOPIC: WHAT IS A BUSINESS CASE? A business case helps to understand how the project is linked with the overall business objectives. Why should the project be done? Why should it be done now and not later? What are the risks associated with not doing it? Which of the business objectives does it address? What is the financial impact (if any)? Copyright © 2018 Advanced Innovation Group Pro Excellence | All Rights Reserved PROBLEM STATEMENT TOPIC: WHAT IS A PROBLEM STATEMENT? A problem statement should quantitatively describe the pain in the current process. It should address 4 critical components: A problem statement should NOT: Assign a Cause or Blame Include a solution Copyright © 2018 Advanced Innovation Group Pro Excellence | All Rights Reserved GOAL STATEMENT TOPIC: WHAT IS A GOAL STATEMENT? A goal statement defines the improvement the team is seeking to accomplish A goal statement starts with a verb Should not presume a cause or include a solution Has a deadline Is actionable and sets the focus Is SMART: Copyright © 2018 Advanced Innovation Group Pro Excellence | All Rights Reserved SCOPE STATEMENT TOPIC: WHAT IS A SCOPE STATEMENT? A project scope helps us to understand the start and end-point for the process and also gives an insight on Project constraints and dimensions Types of Scoping: SCOPE CREEP: Incorrect scoping or changing the scope regularly is termed as “Scope Creep” Seek an understanding of your project scope at the beginning of the project Scope must not change unless there is a valid business justification Copyright © 2018 Advanced Innovation Group Pro Excellence | All Rights Reserved SELECTING YOUR PROJECT TEAM TOPIC: SELECTING YOUR PROJECT TEAM The project roles include: Copyright © 2018 Advanced Innovation Group Pro Excellence | All Rights Reserved SELECTING YOUR PROJECT TEAM TOPIC: DO’S AND DON’T’S OF SELECTING & MANAGING A PROJECT TEAM Do’s of selecting & managing project team Copyright © 2018 Advanced Innovation Group Pro Excellence | All Rights Reserved SELECTING YOUR PROJECT TEAM TOPIC: DO’S AND DON’T’S OF SELECTING & MANAGING A PROJECT TEAM Dont’s of selecting & managing project team Copyright © 2018 Advanced Innovation Group Pro Excellence | All Rights Reserved PROFICIENCY HACK: PROJECT CHARTER TOPIC: PROFICIENCY HACK: PROJECT CHARTER 1. When writing a problem statement, do not forget to add all of the four components: What is the Problem? Since when/where is the problem occurring? What is the magnitude of the problem? What are the consequences if we do not rectify the problem now 2. Write your project charter in a layman language It should be jargon free Simple Understandable and Key points should be discussed in a crisp and clear manner 3. The business case, problem statement and the goal statement should never include a cause or a blame and a solution 4. Treat the project charter as a living document Copyright © 2018 Advanced Innovation Group Pro Excellence | All Rights Reserved PROJECT ACCEPTABILITY & INTRODUCTION TO CAP TOPIC: PROJECT ACCEPTABILITY Effectiveness of a solution = Quality of a Solution * Acceptability of the Solution E = Q*A 100%[E] = 20%[Q]*80%[A] Improvements bring about change and it is a commonly known fact that change is always resisted It is important for all of us to realize that just finding a solution to the problem is not good enough The identified solution should be understood and implemented It is important to create a “shared-need” as early as possible in your project journey as it helps in: Copyright © 2018 Advanced Innovation Group Pro Excellence | All Rights Reserved PROJECT ACCEPTABILITY & INTRODUCTION TO CAP TOPIC: PROJECT ACCEPTABILITY The key benefits are: Copyright © 2018 Advanced Innovation Group Pro Excellence | All Rights Reserved CHANGE ACCELERATION PROCESS (CAP) TOPIC: CHANGE ACCELERATION PROCESS (CAP) Which are the different CAP tools? ARMI Stakeholder Analysis RACI Elevator Speech Threat vs. Opportunity Matrix Communications Plan Copyright © 2018 Advanced Innovation Group Pro Excellence | All Rights Reserved WHAT IS ARMI? TOPIC: WHAT IS ARMI? ARMI is a CAP tool used to assess each person’s role in the project during various phases of the project Copyright © 2018 Advanced Innovation Group Pro Excellence | All Rights Reserved WHAT IS RACI? TOPIC: WHAT IS RACI? The RACI matrix is used to assess key stakeholder roles and responsibilities for the area under study. It stands for: Copyright © 2018 Advanced Innovation Group Pro Excellence | All Rights Reserved THREAT VS. OPPORTUNITY MATRIX TOPIC: WHAT IS THREAT VS. OPPORTUNITY MATRIX? Simple 2X2 grid Captures threats and opportunities Helps you seek buy-in from project stakeholders Helps provide a clear picture of why should this project be done now? EXAMPLE: THREAT VS. OPPORTUNITY MATRIX Copyright © 2018 Advanced Innovation Group Pro Excellence | All Rights Reserved STAKEHOLDER ANALYSIS TOPIC: WHAT IS STAKEHOLDER ANALYSIS? A process of identifying those people and functions that will be impacted by a change Identifies each stakeholder’s position regarding the change Also identifies strategies and plans to address those positions Stakeholders refers to seniors as well as team members of your project WHEN IS STAKEHOLDER ANALYSIS USED? Should be conducted early in the DMAIC process Results of this tool can influence the project’s charter & scope Should be revisited and revised throughout the DMAIC journey WHY IS A STAKEHOLDER ANALYSIS USED? Because best technical solutions won’t help if it can’t be successfully implemented Individuals may have different motivations for wanting a change to succeed or fail These individual motivations can be influenced by using stakeholder analysis Copyright © 2018 Advanced Innovation Group Pro Excellence | All Rights Reserved STAKEHOLDER ANALYSIS TOPIC: EXAMPLE – STAKEHOLDER ANALYSIS Copyright © 2018 Advanced Innovation Group Pro Excellence | All Rights Reserved ELEVATOR SPEECH TOPIC: WHAT IS AN ELEVATOR SPEECH? Short 30-60 seconds business pitch Its meant to represent the amount of time you’d have if you were stuck in an elevator with someone riding from the bottom of the building to the top Targeted to your audience Not more than 30-60 seconds long Simple, compelling and has less than 100 words It answers questions such as: o What is the situation or the issue? o Why is that a problem? o What do you plan to accomplish? o How big a difference do you hope to make? o How will you know (measure)? Helps in getting you the support and commitment of key stakeholders Copyright © 2018 Advanced Innovation Group Pro Excellence | All Rights Reserved ELEVATOR SPEECH TOPIC: EXAMPLE: ELEVATOR SPEECH? “Did you know that customer satisfaction is the number one issue for most of the existing businesses in our organization? Their issue is not that the performance of our business processes has deteriorated, it’s that the other organizations have, with the help of technology, raised the standards of servicing their customers. I know that if we focus on improving the customer satisfaction with a slightly heightened focus on technology, it would help us service our customers the same way our competitors are servicing them. As a result, we will continue to remain number 01 in our chosen area of expertise and we will also reduce the operating cost not just for this location, but for all the locations of our organization.” DON’TS WHILE DELIVERING AN ELEVATOR SPEECH You should not speak too fast Don’t use highly technical terms, acronyms or slangs Don’t beat around the bush, stay focused Don’t sound robotic Copyright © 2018 Advanced Innovation Group Pro Excellence | All Rights Reserved PROCESS MAPPING TOPIC: PROCESS MAPPING OVERVIEW What is Process Mapping? Graphic display of steps, events and operations that constitute a process Create using the combined knowledge of all people associated with the process In step 03, you will create a SIPOC What is a SIPOC? SIPOC is also termed as a Macro As Is Process Map Copyright © 2018 Advanced Innovation Group Pro Excellence | All Rights Reserved WHAT IS A SIPOC? TOPIC: SIPOC EXAMPLE Copyright © 2018 Advanced Innovation Group Pro Excellence | All Rights Reserved STEPS TO CREATE PROCESS MAPPING TOPIC: STEPS TO CREATE A SIPOC DIAGRAM Copyright © 2018 Advanced Innovation Group Pro Excellence | All Rights Reserved EFFECTIVE VS. EFFICIENCY MEASURES TOPIC: EFFECTIVE MEASURES VS. EFFICIENCY MEASURES Copyright © 2018 Advanced Innovation Group Pro Excellence | All Rights Reserved COST OF POOR QUALITY (COPQ) TOPIC: COST OF POOR QUALITY (COPQ) Copyright © 2018 Advanced Innovation Group Pro Excellence | All Rights Reserved 8 WASTES TOPIC: WHAT IS WASTE? Anything other than minimum amount of information, equipment, materials and effort absolutely required to add value to a product or service There are 8 different types of waste Copyright © 2018 Advanced Innovation Group Pro Excellence | All Rights Reserved 8 WASTES TOPIC: 8 TYPES OF WASTES WASTE OF DEFECTS: Defects are rejects that require additional time, resources and money to fix Defects are also called rework as they lead to more work To identify defects, you should look for: o Errors o Not in Good Order Transactions o Missing information o Rework loops o Breaks WASTE OF OVER PRODUCTION: Producing too much or too soon Examples of Over Production o When more information is being requested than required o When efforts are not aligned with risk, complexity or customer needs o When automation is poorly applied in your business process Copyright © 2018 Advanced Innovation Group Pro Excellence | All Rights Reserved 8 WASTES TOPIC: 8 TYPES OF WASTES WASTE OF WAITING: Occurs whenever work has to stop for some reason This may be due to: o Next person in line is overwhelmed o Something broke down o You are waiting for approval o You have run out of something Examples of Waiting: o When you observe idle time o When someone is waiting for information o When you see overfull inboxes pending to be addressed WASTE OF NON-UTILIZED SKILLS: This is also termed as “Waste of Intellect” Examples of Waste due to non-utilized skills o Look for significant portion of expert time “wasted” on low value activities o Lack of team work o Lack of training o Narrowly defined jobs and expectations Copyright © 2018 Advanced Innovation Group Pro Excellence | All Rights Reserved 8 WASTES TOPIC: 8 TYPES OF WASTES WASTE OF TRANSFER (TRANSPORTATION): This is waste from moving things around or work transferring across platforms or teams, mostly non- essential transportation To identify defects, you should look for: o Excessive back and forth, repeated follow-ups o Movement from location to location, building to building, etc WASTE OF INVENTORY: Work stuck in email boxes not being processed, idle financial or fixed assets To identify defects, you should look for: o Bottlenecks leading to “staging” areas for work in progress o Idle or underutilized equipment Copyright © 2018 Advanced Innovation Group Pro Excellence | All Rights Reserved 8 WASTES TOPIC: 8 TYPES OF WASTES WASTE OF MOTION It is inefficient placement of resources creating motion To identify defects, you should look for: o Inefficient placement of office resources o Physical distance between workstations o Poor housekeeping WASTE OF EXCESS PROCESSING: It is additional processing of transactions To identify defects, you should look for: o Similar information being captured in several places o Large variations in time to do similar tasks o Unnecessary approvals Copyright © 2018 Advanced Innovation Group Pro Excellence | All Rights Reserved 8 WASTES TOPIC: WHAT IS DOWNTIME? D Waste of Defects O Waste of Over-Production W Waste of Waiting N Waste of Non-Utilized Skills T Waste of Transfer I Waste of Inventory M Waste of Motion E Waste of Excess Processing Copyright © 2018 Advanced Innovation Group Pro Excellence | All Rights Reserved WHAT ARE PROCESS MAPS? TOPIC: WHAT ARE PROCESS MAPS? Most powerful mapping tool Displays step-by-step process activities Helps identify roles and responsibilities Identifies dependencies and bottlenecks Helps understand the interaction between the process & technology requirements Copyright © 2018 Advanced Innovation Group Pro Excellence | All Rights Reserved COMMONLY USED PROCESS MAPPING SYMBOLS TOPIC: COMMONLY USED PROCESS MAPPING SYMBOLS SYMBOL DESCRIPTION & USAGE Indicates where the process starts and stops Terminal Activity Describes the actual work task that occurs at that point in the process It generally is best to include only one task in each Activity activity symbol Displays a question that has several optional answers/flows that lead away from the diamond Answers can be simple “Yes”or “No” or specifically described choices Answers are labeled on connector lines Decision Connects any two steps and shows the path or direction of the process Connector Copyright © 2018 Advanced Innovation Group Pro Excellence | All Rights Reserved COMMONLY USED PROCESS MAPPING SYMBOLS TOPIC: COMMONLY USED PROCESS MAPPING SYMBOLS SYMBOL DESCRIPTION & USAGE Identifies when the process comes to a temporary halt Also identifies what has to happen before the Delay process resumes Indicates that a written document is prepared or used at that step of the process; the name of the document appears in the symbol Document Shows that a database is associated with this step Database Indicates when something goes into storage for some period of time; it contains a brief description of what is stored and for how long Storage Copyright © 2018 Advanced Innovation Group Pro Excellence | All Rights Reserved COMMONLY USED PROCESS MAPPING SYMBOLS TOPIC: COMMONLY USED PROCESS MAPPING SYMBOLS SYMBOL DESCRIPTION & USAGE Indicates a pre-defined process Predefined Process Copyright © 2018 Advanced Innovation Group Pro Excellence | All Rights Reserved STEPS TO CREATE A PROCESS MAP TOPIC: STEPS TO CREATE A PROCESS MAP Step 01. Assemble the right team Step 02. Select and prepare the room Step 03. Set the agenda for the meeting Step 04. Create the map Step 05. Document issues, disconnects, opportunities and process measures Step 06. Validate the map Copyright © 2018 Advanced Innovation Group Pro Excellence | All Rights Reserved STEPS TO CREATE A PROCESS MAP TOPIC: KEY QUESTIONS TO EVALUATE YOUR PROCESS MAP Are there lots of paper and manual processes? Are there many layers of review and approval? Are there high error rates and significant rework? Low self-service success rates Are people dependent on “tribal” knowledge rather than documentation, manuals and tools to enable process steps? Is the first contact resolution low? Are customer complaints very high? Are contact center agent complaints and their turn-over high? Copyright © 2018 Advanced Innovation Group Pro Excellence | All Rights Reserved DIFFERENT TYPES OF PROCESS MAPS TOPIC: PROCESS FLOWCHART TOPIC: DEPLOYMENT FLOWCHART Copyright © 2018 Advanced Innovation Group Pro Excellence | All Rights Reserved DIFFERENT TYPES OF PROCESS MAPS TOPIC: ALTERNATE PATH FLOWCHART Copyright © 2018 Advanced Innovation Group Pro Excellence | All Rights Reserved DO’S & DON’TS OF CREATING A PROCESS MAP TOPIC: DO’S AND DON'TS OF CREATING A PROCESS MAP Copyright © 2018 Advanced Innovation Group Pro Excellence | All Rights Reserved WHAT ARE VALUE STREAM MAPS? TOPIC: WHAT ARE VALUE STREAM MAPS? A Value Stream Map is a lean technique used to document, analyze and improve the flow of information or materials required to produce a product or service for a customer. Review the flow of System of symbols Identify and process steps and to depict various eliminate waste information from work activities and origin to delivery information flows Process map is the work that Value stream map is the work should ideally happen on the that actually happens on the floor floor Non-Value Added Essential Non- Value Added Work Work Value Added Work Value Added Time Process Cycle Efficiency Total Time Copyright © 2018 Advanced Innovation Group Pro Excellence | All Rights Reserved VSM ICONS TOPIC: VSM ICONS Customer / Process Kaizen Operator Burst Supplier Icon Flow Timeline Go & See Electronic Flow Production Kanban Signal Kanban Inventory Shipments Push Arrow FIFO Copyright © 2018 Advanced Innovation Group Pro Excellence | All Rights Reserved STEPS TO CREATE A VALUE STREAM MAP TOPIC: STEPS TO CREATE A VALUE STREAM MAP Step 01: Identify the start and end points of your value stream map First step: Customer calls the pizza outlet on the phone Last Step: Pizza is delivered to the customer Copyright © 2018 Advanced Innovation Group Pro Excellence | All Rights Reserved STEPS TO CREATE A VALUE STREAM MAP TOPIC: STEPS TO CREATE A VALUE STREAM MAP Step 02: Document the process steps Add activity boxes to show all the steps involved In the corner of each activity box, a small circle indicates how many operators complete the step in the process Below each activity box, include a data box for your analysis: o Cycle Time (C/T): the time to complete each activity o Change-over time (C/O): the time to switch the product type o Uptime: the % of time the machine is up and running o Yield: the % of parts that pass inspection Copyright © 2018 Advanced Innovation Group Pro Excellence | All Rights Reserved STEPS TO CREATE A VALUE STREAM MAP TOPIC: STEPS TO CREATE A VALUE STREAM MAP Step 03: Add inventory and wait times Connect start and end points and the activity boxes with arrows to show the entire process flow In between each stage, use inventory triangles to mark the number of parts you have in work in progress (WIP) at the end of each step Copyright © 2018 Advanced Innovation Group Pro Excellence | All Rights Reserved STEPS TO CREATE A VALUE STREAM MAP TOPIC: STEPS TO CREATE A VALUE STREAM MAP Step 04: Draw information flow Add a production control box to represent central coordination Place lines of communication – you can add notes about the type of data exchanged, the frequency of exchange, or the media used Straight lines show manual communication, such as memos, printed reports, or in-person conversations Copyright © 2018 Advanced Innovation Group Pro Excellence | All Rights Reserved STEPS TO CREATE A VALUE STREAM MAP TOPIC: STEPS TO CREATE A VALUE STREAM MAP Step 05: Create timeline The timeline has 3 levels: value added step, essential non-value added step and non-value added step Timeline also includes data boxes that combine all of this information: o Total cycle time: total cycle time of the process o Value added time: total value added time of the process o Process cycle efficiency: it is the percentage of value added time out of the total cycle time Copyright © 2018 Advanced Innovation Group Pro Excellence | All Rights Reserved WHAT IS TAKE TIME? TOPIC: WHAT IS TAKT TIME? Time needed to produce one unit of a product to meet customer requirements Ta where, T stands for Takt Time Ta stands for Net Available Time T = Td is the total customer demand (units Td produced per day) Establishes the pace German word for of the process needed Shows where the flow “Drum beat” to meet customer is uneven demand Takt time can be calculated after creating high level, functional process maps, and value stream maps Copyright © 2018 Advanced Innovation Group Pro Excellence | All Rights Reserved DIFFERENT DATA TYPES TOPIC: DIFFERENT DATA TYPES Copyright © 2018 Advanced Innovation Group Pro Excellence | All Rights Reserved WHAT IS XY MATRIX? TOPIC: WHAT IS XY MATRIX? XY Matrix allow team members to: Document the outputs that are critical to business Map the inputs that affect those outputs Mutually agree on which inputs will affect those outputs the most Copyright © 2018 Advanced Innovation Group Pro Excellence | All Rights Reserved STEPS TO CREATE XY MATRIX TOPIC: STEPS TO CREATE XY MATRIX Step 01: Participants review all available information prior to the session Copyright © 2018 Advanced Innovation Group Pro Excellence | All Rights Reserved STEPS TO CREATE XY MATRIX TOPIC: STEPS TO CREATE XY MATRIX Step 02: The participants lists the output variables (Y’s) in the XY Matrix Copyright © 2018 Advanced Innovation Group Pro Excellence | All Rights Reserved STEPS TO CREATE XY MATRIX TOPIC: STEPS TO CREATE XY MATRIX Step 03: The participants will rate each output in terms of its significance Copyright © 2018 Advanced Innovation Group Pro Excellence | All Rights Reserved STEPS TO CREATE XY MATRIX TOPIC: STEPS TO CREATE XY MATRIX Step 04: The participants will brainstorm potential inputs (X’s) that can impact the various Y’s Copyright © 2018 Advanced Innovation Group Pro Excellence | All Rights Reserved STEPS TO CREATE XY MATRIX TOPIC: STEPS TO CREATE XY MATRIX Step 05: Participants rate the effect of each X on each Y Copyright © 2018 Advanced Innovation Group Pro Excellence | All Rights Reserved STEPS TO CREATE XY MATRIX TOPIC: STEPS TO CREATE XY MATRIX Step 06: You will calculate the overall score and % Copyright © 2018 Advanced Innovation Group Pro Excellence | All Rights Reserved STEPS TO CREATE XY MATRIX TOPIC: STEPS TO CREATE XY MATRIX Step 07: You will use the rating to prioritize data collection for the project Copyright © 2018 Advanced Innovation Group Pro Excellence | All Rights Reserved SAMPLING AND SAMPLING TECHNIQUES TOPIC: SAMPLING AND SAMPLING TECHNIQUES Sampling is the process of collecting only a portion of the data that is available or could be available, and drawing conclusions about the total population. This is known as statistical inference. Sampling is done when: Collecting all the Data collection can You are measuring a data is impractical be a destructive high-volume or too costly process process Benefits include: Allows for more meaningful data Saves time and money to be collected than might otherwise be available Copyright © 2018 Advanced Innovation Group Pro Excellence | All Rights Reserved SIMPLE RANDOM SAMPLING TOPIC: SIMPLE RANDOM SAMPLING Simple random sampling is a method of sampling in which every unit has equal chance of being selected. Copyright © 2018 Advanced Innovation Group Pro Excellence | All Rights Reserved STRATIFIED RANDOM SAMPLING TOPIC: STRATIFIED RANDOM SAMPLING Stratified random sampling is a method of sampling in which subsets or groups are created and then units are picked randomly. Copyright © 2018 Advanced Innovation Group Pro Excellence | All Rights Reserved SYSTEMATIC SAMPLING TOPIC: SYSTEMATIC SAMPLING Systematic sampling is a method of sampling in which every nth unit is selected from the population. Copyright © 2018 Advanced Innovation Group Pro Excellence | All Rights Reserved CLUSTER SAMPLING TOPIC: CLUSTER SAMPLING Cluster sampling is a method of sampling in which clusters are sampled every nth time. Copyright © 2018 Advanced Innovation Group Pro Excellence | All Rights Reserved SAMPLE SIZE FORMULA TOPIC: SAMPLE SIZE FORMULA Sample size formula for Continuous Data n = sample size s = standard deviation d = margin of error 1.96 = 95% Confidence Sample size formula for Discrete Data n = sample size d = margin of error p = proportion defective 1.96 = 95% Confidence Copyright © 2018 Advanced Innovation Group Pro Excellence | All Rights Reserved MEASUREMENT SYSTEM ANALYSIS – COMPONENTS OF VARIATION TOPIC: MSA – COMPONENTS OF VARIATION Copyright © 2018 Advanced Innovation Group Pro Excellence | All Rights Reserved MEASUREMENT SYSTEM ERRORS TOPIC: MEASUREMENT SYSTEM ERRORS - REPEATABILITY Repeatability is the variation in measurement when a person measures the same unit repeatedly with the same measuring tool. Copyright © 2018 Advanced Innovation Group Pro Excellence | All Rights Reserved MEASUREMENT SYSTEM ERRORS TOPIC: MEASUREMENT SYSTEM ERRORS - REPRODUCIBILITY Reproducibility is the variation in measurement when two or more persons measure the same unit using the same measuring gage. Copyright © 2018 Advanced Innovation Group Pro Excellence | All Rights Reserved MEASUREMENT SYSTEM ERRORS TOPIC: MEASUREMENT SYSTEM ERRORS - ACCURACY Accuracy is the difference between the average of observed values and the actual. Copyright © 2018 Advanced Innovation Group Pro Excellence | All Rights Reserved SPECIAL CAUSE PATTERNS OF A RUN CHART TOPIC: SPECIAL CAUSE PATTERNS OF A RUN CHART RUN CHART – SAME VALUE PLOT A run chart having seven or more points with same value in a sequence indicates bias in the process Measurement Medi an Time Copyright © 2018 Advanced Innovation Group Pro Excellence | All Rights Reserved SPECIAL CAUSE PATTERNS OF A RUN CHART TOPIC: SPECIAL CAUSE PATTERNS OF A RUN CHART RUN CHART – CLUSTERING PLOT Such a plot has a lot of data points next to each other on one side of the median and the same way on the side of the median over time and indicates a periodic shift in process average due to lot-to-lot or setup variability; Also known as too few runs plot Median Measurement Time Copyright © 2018 Advanced Innovation Group Pro Excellence | All Rights Reserved SPECIAL CAUSE PATTERNS OF A RUN CHART TOPIC: SPECIAL CAUSE PATTERNS OF A RUN CHART RUN CHART – MIXTURES PLOT Such a plot has an absence of points near the center line with a sequence of fourteen or more points in a row alternating up and down; indicates a bias or systematic sampling from different sources or processes; Also known as cycle or too many runs plot Copyright © 2018 Advanced Innovation Group Pro Excellence | All Rights Reserved SPECIAL CAUSE PATTERNS OF A RUN CHART TOPIC: SPECIAL CAUSE PATTERNS OF A RUN CHART RUN CHART – OSCILLATIONS PLOT Such a plot has data points constantly fluctuating up and down rapidly around the median and indicates that the process is not steady or stable Copyright © 2018 Advanced Innovation Group Pro Excellence | All Rights Reserved SPECIAL CAUSE PATTERNS OF A RUN CHART TOPIC: SPECIAL CAUSE PATTERNS OF A RUN CHART RUN CHART – TREND PLOT Such a plot has a sequence of seven or more data points continuously increasing or decreasing and indicates a gradual increase or decrease trend in the data measurement methods Copyright © 2018 Advanced Innovation Group Pro Excellence | All Rights Reserved SPECIAL CAUSE PATTERNS OF A RUN CHART TOPIC: SPECIAL CAUSE PATTERNS OF A RUN CHART RUN CHART – SHIFT PLOT Such a plot has a sequence of eight or more points on the same side of the median and indicates a gradual shift in the process Copyright © 2018 Advanced Innovation Group Pro Excellence | All Rights Reserved STEPS TO CREATE A RUN CHART ON MINITAB TOPIC: STEPS TO CREATE A RUN CHART ON MINITAB Open the excel sheet Turn Around Time.xlsx Choose Stat > Quality Tools > Run Chart In Single column, enter TAT In Subgroup size, enter 1. Click OK Copyright © 2018 Advanced Innovation Group Pro Excellence | All Rights Reserved WHAT IS NORMAL DISTRIBUTION? TOPIC: WHAT IS NORMAL DISTRIBUTION? This is one of the most widely used distribution Copyright © 2018 Advanced Innovation Group Pro Excellence | All Rights Reserved WHAT IS NORMAL DISTRIBUTION? TOPIC: WHAT IS NORMAL DISTRIBUTION? Example of data that is not normal Copyright © 2018 Advanced Innovation Group Pro Excellence | All Rights Reserved WHAT IS NORMAL DISTRIBUTION? TOPIC: WHAT IS NORMAL DISTRIBUTION? Characteristics of a Normal Curve Copyright © 2018 Advanced Innovation Group Pro Excellence | All Rights Reserved WHAT IS NORMAL DISTRIBUTION? TOPIC: WHAT IS NORMAL DISTRIBUTION? Is it advisable to work with Normal Data? Yes, Normal data is preferred over non-normal data Copyright © 2018 Advanced Innovation Group Pro Excellence | All Rights Reserved HOW TO CHECK NORMALITY ON MINITAB? TOPIC: STEPS TO PERFORM A NORMALITY TEST ON MINITAB Open the excel sheet Turn Around Time.xlsx Copy and paste the data in Minitab Choose Stat > Basic Statistics > Normality Test In Variable, enter TAT Click OK Copyright © 2018 Advanced Innovation Group Pro Excellence | All Rights Reserved WHAT IS CLASSIC YIELD, FIRST PASS YIELD & ROLLED THROUGHPUT YIELD? TOPIC: WHAT IS CLASSIC YIELD, FIRST PASS YIELD & ROLLED THROUGHPUT YIELD? 𝑁𝑁𝑁𝑁𝑁𝑁𝑁𝑁𝑁𝑁𝑁𝑁 𝑜𝑜𝑜𝑜 𝑔𝑔𝑔𝑔𝑔𝑔𝑔𝑔 𝑝𝑝𝑝𝑝𝑝𝑝𝑝𝑝𝑝𝑝 𝑎𝑎𝑎𝑎 𝑡𝑡𝑡𝑡𝑡 𝑒𝑒𝑒𝑒𝑒𝑒 𝑜𝑜𝑜𝑜 𝑡𝑡𝑡𝑡𝑡 𝑝𝑝𝑝𝑝𝑝𝑝𝑝𝑝𝑝𝑝𝑝𝑝𝑝𝑝 𝐶𝐶𝐶𝐶𝐶𝐶𝐶𝐶𝐶𝐶𝐶𝐶𝐶𝐶 𝑌𝑌𝑌𝑌𝑌𝑌𝑌𝑌𝑌𝑌 = 𝑌𝑌 = 𝑇𝑇𝑇𝑇𝑇𝑇𝑇𝑇𝑇𝑇 𝑛𝑛𝑛𝑛𝑛𝑛𝑛𝑛𝑛𝑛𝑛𝑛 𝑜𝑜𝑜𝑜 𝑝𝑝𝑝𝑝𝑝𝑝𝑝𝑝𝑝𝑝 𝑠𝑠𝑠𝑠𝑠𝑠𝑠𝑠𝑠𝑠𝑠𝑠𝑠𝑠 𝑤𝑤𝑤𝑤𝑤𝑤𝑤 𝑁𝑁𝑁𝑁𝑁𝑁𝑁𝑁𝑁𝑁𝑁𝑁 𝑜𝑜𝑜𝑜 𝑔𝑔𝑔𝑔𝑔𝑔𝑔𝑔 𝑝𝑝𝑝𝑝𝑝𝑝𝑝𝑝𝑝𝑝 𝑎𝑎𝑎𝑎 𝑡𝑡𝑡𝑡𝑡 𝑒𝑒𝑒𝑒𝑒𝑒 𝑡𝑡𝑡𝑡𝑡𝑡𝑡 𝑚𝑚𝑚𝑚𝑚𝑚𝑚𝑚 𝑖𝑖𝑖𝑖 𝑡𝑡𝑡𝑡𝑡𝑡𝑡𝑡𝑡𝑡𝑡𝑡 𝑤𝑤𝑤𝑤𝑤𝑤𝑤𝑤𝑤𝑤𝑤𝑤𝑤 𝑟𝑟𝑟𝑟𝑟𝑟𝑟𝑟𝑟𝑟𝑟𝑟 𝐹𝐹𝐹𝐹𝐹𝐹𝐹𝐹𝐹𝐹 𝑃𝑃𝑃𝑃𝑃𝑃𝑃𝑃 𝑌𝑌𝑌𝑌𝑌𝑌𝑌𝑌𝑌𝑌 = 𝑌𝑌𝑌𝑌𝑌𝑌 = 𝑇𝑇𝑇𝑇𝑇𝑇𝑇𝑇𝑇𝑇 𝑛𝑛𝑛𝑛𝑛𝑛𝑛𝑛𝑛𝑛𝑛𝑛 𝑜𝑜𝑜𝑜 𝑝𝑝𝑝𝑝𝑝𝑝𝑝𝑝𝑝𝑝 𝑠𝑠𝑠𝑠𝑠𝑠𝑠𝑠𝑠𝑠𝑠𝑠𝑠𝑠 𝑤𝑤𝑤𝑤𝑤𝑤𝑤 𝑅𝑅𝑅𝑅𝑅𝑅𝑅𝑅𝑅𝑅𝑅𝑅 𝑇𝑇𝑇𝑇𝑇𝑇𝑇𝑇𝑇𝑇𝑇𝑇𝑇𝑇𝑇𝑇𝑇𝑇 𝑌𝑌𝑌𝑌𝑌𝑌𝑌𝑌𝑌𝑌 = 𝐹𝐹𝐹𝐹𝐹𝐹𝐹𝐹𝐹𝐹 𝑃𝑃𝑃𝑃𝑃𝑃𝑃𝑃 𝑌𝑌𝑌𝑌𝑌𝑌𝑌𝑌𝑌𝑌 1 ∗ 𝐹𝐹𝐹𝐹𝐹𝐹𝐹𝐹𝐹𝐹 𝑃𝑃𝑃𝑃𝑃𝑃𝑃𝑃 𝑌𝑌𝑌𝑌𝑌𝑌𝑌𝑌𝑌𝑌 2 ∗ … ∗ 𝐹𝐹𝐹𝐹𝐹𝐹𝐹𝐹𝐹𝐹 𝑃𝑃𝑃𝑃𝑃𝑃𝑃𝑃 𝑌𝑌𝑌𝑌𝑌𝑌𝑌𝑌𝑌𝑌 𝑛𝑛 Copyright © 2018 Advanced Innovation Group Pro Excellence | All Rights Reserved WHAT IS SIGMA SHIFT? TOPIC: WHAT IS SIGMA SHIFT? ZST = 1.5 + ZLT where ZST is short term sigma and ZLT is long term sigma Copyright © 2018 Advanced Innovation Group Pro Excellence | All Rights Reserved INTRODUCTION TO DUDO TOPIC: INTRODUCTION TO DUDO DUDO stands for Defects, Units, Defectives and Opportunity for Errors. Here are the definitions: What is a Unit? An Item being processed What is a Defect? Failure to meet a customer Requirement or a Performance standard What is an Opportunity? Any product / service characteristics which is measured to a standard What is Defective? A unit that has s defect Copyright © 2018 Advanced Innovation Group Pro Excellence | All Rights Reserved CALCULATE PROCESS CAPABILITY FOR DISCRETE DATA TOPIC: STEPS TO CALCULATE PROCESS CAPABILITY FOR DISCRETE DATA Copyright © 2018 Advanced Innovation Group Pro Excellence | All Rights Reserved PROCESS SIGMA CALCULATION – CONTINUOUS DATA TOPIC: STEPS FOR CALCULATING PROCESS SIGMA – CONTINUOUS DATA Open the excel sheet Turn Around Time.xlsx Choose Stat > Quality Tools > Capability Analysis > Normal In Single column, enter TAT In Subgroup size, enter 1. In Upper Specification Limit, enter 4. Click OK Copyright © 2018 Advanced Innovation Group Pro Excellence | All Rights Reserved WHAT IS BRAINSTORMING? TOPIC: WHAT IS BRAINSTORMING? Brainstorming is an idea generation tool It is an individual or a group method to generated ideas, increase creative efficacy and find solutions to problems Helps identify trivial many root causes Brainstorming encourages creativity, involves everyone, generates excitement and energy, and separates people from the ideas they suggest Use brainstorming whenever creative ideas are sought This tool can be used in each of the DMAIC phases Copyright © 2018 Advanced Innovation Group Pro Excellence | All Rights Reserved GENERAL BRAINSTORMING GUIDELINES TOPIC: GENERAL BRAINSTORMING GUIDELINES Copyright © 2018 Advanced Innovation Group Pro Excellence | All Rights Reserved GENERAL BRAINSTORMING GUIDELINES TOPIC: PROS AND CONS OF BRAINSTORMING WHAT’S GOOD ABOUT IT? WHAT’S BAD ABOUT IT? ADDRESSES EVERYONE’S CAN BE SLOW TO GET THROUGH REQUIREMENTS TYPICALLY HAVE ONLY ONE GETS ALL CURRENT OPTIONS ON OPPORTUNITY WITH THE TEAM THE TABLE TAKES MORE RESOURCES UP FRONT CONTRIBUTES TO CONSENSUS & (MORE PARTICIPANTS) BUY-IN HELPS TAKE PERSONALITIES OUT OF THE PROCESS CAPTURES DESIGN KNOWLEDGE PROVIDES STRUCTURE FOR PARTICIPANTS PROMOTES UNIQUE IDEAS AND OFFERS VALIDATION Copyright © 2018 Advanced Innovation Group Pro Excellence | All Rights Reserved GENERAL BRAINSTORMING GUIDELINES TOPIC: 7 TIPS TO CONDUCT EFFECTIVE BRAINSTORMING Establish the need for a Don’t allow participants to deviate brainstorming from the topic Ensure dominating participants are Ensure everyone participates in the effectively managed discussion Don’t engage in evaluating Any crazy idea is welcome viability of the idea Genuinely appreciate and thank everyone for their contributions at the end of the session Copyright © 2018 Advanced Innovation Group Pro Excellence | All Rights Reserved WHAT IS A FISHBONE DIAGRAM? TOPIC: WHAT IS A FISHBONE DIAGRAM? It is called a fishbone diagram because a completed diagram resembles the skeleton of a fish Also known as a Cause and Effect or Ishikawa diagram Helps identify trivial many root causes Helps you associate & represent causes for an effect or problem in one diagram Helps you structure a brainstorming session by segregating causes for an effect or problem under predetermined categories Avoids overlooking possible root cause(s) of an effect or problem Identify possible causes for an effect or a problem To keep the team focused on the causes of the problem, rather than the symptoms To identify the root cause(s) from the underlying reported symptoms Copyright © 2018 Advanced Innovation Group Pro Excellence | All Rights Reserved FISHBONE DIAGRAM EXAMPLE TOPIC: FISHBONE DIAGRAM EXAMPLE Copyright © 2018 Advanced Innovation Group Pro Excellence | All Rights Reserved STEPS TO CREATE A FISHBONE DIAGRAM TOPIC: STEPS TO CREATE A FISHBONE DIAGRAM 1. Decide the major categories for causes 2. One option: the 5M’s o Machines o Manpower o Methods o Materials o Mother nature 3. Identify the most important causes 4. Ask why? 5 times to determine the probable root causes 5. Brainstorm for more ideas in those categories that contain fewer items 6. Perform another iteration to determine root causes if necessary Copyright © 2018 Advanced Innovation Group Pro Excellence | All Rights Reserved WHAT IS 5 WHY ANALYSIS TECHNIQUE? TOPIC: WHAT IS 5 WHY ANALYSIS TECHNIQUE? 5 whys is an iterative probing technique to get to the root cause(s) of an effect or a problem The answer to the first “why” uncovers another reason and generates another “why”. It often takes five “whys” to arrive at the root cause(s) of the problem Helps identify trivial many root causes It’s a simple probing technique Helps team collectively reach root cause(s) Determines the relationship between the different root causes of a problem One of the simplest tools, easy to complete with no statistical analysis required Determine the cause & effect relationship of a problem You want to get to the root cause(s) of an effect or problem without using statistical analysis You want to uncover root cause(s) Copyright © 2018 Advanced Innovation Group Pro Excellence | All Rights Reserved 5 WHY ANALYSIS EXAMPLE TOPIC: 5 WHY ANALYSIS EXAMPLE 01 TOPIC: 5 WHY ANALYSIS EXAMPLE 02 Copyright © 2018 Advanced Innovation Group Pro Excellence | All Rights Reserved STEPS TO CREATE A FISHBONE DIAGRAM TOPIC: STEPS TO PERFORM 5 WHY ANALYSIS 1. Define the problem for which you are trying to identify the root cause. Insert the statement you wish to interrogate 2. Keep on asking “why” until the team agrees they have reached the root cause, or the answer provided does not have a further “why” (note this might be after 4 whys or after more than 5) 3. Once the root cause has been identified, highlight it 4. Develop a corrective action and assign responsibility for action 5. Add the date when the action gets complete Copyright © 2018 Advanced Innovation Group Pro Excellence | All Rights Reserved STEPS TO CREATE A PARETO CHART ON MINITAB TOPIC: STEPS TO CREATE A PARETO CHART ON MINITAB Open the excel sheet Pareto Chart_Class Exercise.xlsx Choose Stat > Quality Tools > Pareto Chart In Defects or Attribute Data in, enter Defects In Frequencies in, enter Counts. Click OK Copyright © 2018 Advanced Innovation Group Pro Excellence | All Rights Reserved WHAT IS A BOX PLOT? TOPIC: WHAT IS A BOX PLOT? The box plot is a graphical display that simultaneously displays several important features of the data, such as its central tendency, variability, departure from symmetry and identification of observations that lie unusually far from the bulk of the data. Box: The box represents the middle 50% values of the process data Median: The center line of the box is called the median. It represents the point for which 50% of the data points are above and 50% are below the line. Q1, Q3: Q1 represents the point for which 75% of the data points are above and 25% are below the line. While Q3 represents the point for which 25% of the data are above and 75% are below the line. Aestrix: Aestrix represents an outlier and is a point which is more than 1.5 times the inter-quartile range i.e. Q3-Q1 in the data (I hope you remember our discussion on Quartiles in the Introduction Phase) Lines: the vertical lines represent a whisker which joins Q1 or Q3 with the farthest data-point but other than an outlier. Copyright © 2018 Advanced Innovation Group Pro Excellence | All Rights Reserved STEPS TO CREATE A BOX PLOT TOPIC: STEPS TO CREATE A BOX PLOT Open the excel sheet Box Plot_Class Exercise.xlsx Choose Graph > Boxplot Under One Y, choose With Groups. Click OK In Graph Variables, enter TAT In Categorical variables for grouping (1-4, outermost first), enter Team Click Scale and click Reference Lines In Show reference lines at Y (value scale) positions, enter 40 Click OK and Click OK Copyright © 2018 Advanced Innovation Group Pro Excellence | All Rights Reserved WHAT IS A SCATTERPLOT? TOPIC: WHAT IS A SCATTERPLOT? Is a powerful visual tool used to display relationships or associations between two variables, cause and effect, and so on The independent variable corresponds to the x axis, or horizontal axis The dependent variable corresponds to the y axis, or vertical axis The pattern identifies whether there is any positive or negative correlation, or no correlation Copyright © 2018 Advanced Innovation Group Pro Excellence | All Rights Reserved STEPS TO CREATE A SCATTERPLOT TOPIC: STEPS TO CREATE A SCATTERPLOT Open the excel sheet Scatterplot_Class Exercise.xlsx Choose Graph > Scatterplot Choose Simple, then click OK Under Y variables, enter Job Knowledge Test Score Under X variables, enter Tenure Click OK Copyright © 2018 Advanced Innovation Group Pro Excellence | All Rights Reserved WHAT IS MULTI-VOTING? TOPIC: WHAT IS MULTI-VOTING? Gather all your subject matter experts and key project members in the conference room List all the trivial many X’s either on the board or on a projector screen, so they are visible to everyone List the objective of the discussion Take the first brainstorming root-cause and ask every member to rate the impact of that root-cause on the Y variable on a scale of 1 to 10 Repeat this rating for every X listed in the table Calculate the score by adding all the individual ratings Sort the score in descending order Copyright © 2018 Advanced Innovation Group Pro Excellence | All Rights Reserved MULTI-VOTING EXAMPLE TOPIC: MULTI-VOTING EXAMPLE Copyright © 2018 Advanced Innovation Group Pro Excellence | All Rights Reserved WHAT IS A CONTROL IMPACT MATRIX? TOPIC: WHAT IS A CONTROL IMPACT MATRIX? A prioritization tool that is used in conjunction with brainstorming Prioritization is done based on factors (or causes) that are in your control and the impact (or extent) of the factor on the problem Copyright © 2018 Advanced Innovation Group Pro Excellence | All Rights Reserved STEPS TO CONSTRUCT A CONTROL IMPACT MATRIX TOPIC: STEPS TO CONSTRUCT A CONTROL IMPACT MATRIX Gather the subject matter experts and necessary project members together Pick-up one root-cause at a time and discuss whether the root-cause is in control or out of control Identify whether the root cause has a high, medium or low impact on the problem Continue this step for all the identified root-causes Priorities those root-causes that are in-control and medium to high impact on the problem Copyright © 2018 Advanced Innovation Group Pro Excellence | All Rights Reserved HYPOTHESIS TESTING TOPIC: HYPOTHESIS TESTING Hypothesis testing tells us whether there exists statistically significant difference between the data sets for us to consider the to represent different distribution Copyright © 2018 Advanced Innovation Group Pro Excellence | All Rights Reserved HYPOTHESIS TESTING TOPIC: HYPOTHESIS TESTING Copyright © 2018 Advanced Innovation Group Pro Excellence | All Rights Reserved STEPS IN HYPOTHESIS TESTING TOPIC: STEPS IN HYPOTHESIS TESTING Copyright © 2018 Advanced Innovation Group Pro Excellence | All Rights Reserved STEP 01. IDENTIFY THE HYPOTHESIS TESTS TOPIC: STEP 01. IDENTIFY THE HYPOTHESIS TESTS Copyright © 2018 Advanced Innovation Group Pro Excellence | All Rights Reserved ADVANCED LEARNING: IDENTIFY DIFFERENT HYPOTHESIS TESTS TOPIC: ADVANCED LEARNING: IDENTIFY DIFFERENT HYPOTHESIS TESTS Copyright © 2018 Advanced Innovation Group Pro Excellence | All Rights Reserved HOW DO YOU WRITE THE NULL & ALTERNATIVE HYPOTHESIS? TOPIC: HOW DO YOU WRITE THE NULL & ALTERNATIVE HYPOTHESIS? SCENARIO 01 Copyright © 2018 Advanced Innovation Group Pro Excellence | All Rights Reserved HOW DO YOU WRITE THE NULL & ALTERNATIVE HYPOTHESIS? SCENARIO 02 SCENARIO 03 Copyright © 2018 Advanced Innovation Group Pro Excellence | All Rights Reserved HOW DO YOU WRITE THE NULL & ALTERNATIVE HYPOTHESIS? KEY POINTS TO REMEMBER Copyright © 2018 Advanced Innovation Group Pro Excellence | All Rights Reserved 1-SAMPLE T TEST ON MINITAB TOPIC: 1-SAMPLE T TEST ON MINITAB Open the excel sheet 1-Sample t test.XLSX Copy and paste the data of worksheet Example 1 Choose Stat > Basic Statistics > 1-Sample t In Samples in columns, enter Speed of Vehicle Check Perform hypothesis test. In Hypothesized mean, enter 40 Click Options. Click on the dropdown that says Alternative and select Greater than Click OK in each dialog box “With 95% confidence, it is concluded that the speed of the vehicle is NOT significantly greater than 40 kmph.” Copyright © 2018 Advanced Innovation Group Pro Excellence | All Rights Reserved 2-SAMPLE T TEST ON MINITAB TOPIC: 2-SAMPLE T TEST ON MINITAB Open the excel sheet 2-Sample t test.XLSX Copy and paste the data of worksheet Choose Stat > Basic Statistics > 2-Sample t Choose Samples in different columns In First, enter Financial Loss –Team A In Second, enter Financial Loss –Team B Click Options, click on the dropdown that says Alternative and select Greater Than. Click OK. Check Assume equal variances. Click OK “With 95% confidence, it is concluded that the financial loss of the projects executed by Team A is significantly higher than the financial loss of the projects executed by team B.” Copyright © 2018 Advanced Innovation Group Pro Excellence | All Rights Reserved PAIRED T TEST ON MINITAB TOPIC: PAIRED T TEST ON MINITAB Open the excel sheet Paired t test.XLSX Copy and paste the data of worksheet Choose Stat > Basic Statistics > Paired t Choose Samples in columns In First Sample, enter Mileage – Shell Oil In Second Sample, enter Mileage – Castrol Oil Click Options, click on the dropdown that says Alternative and select Not Equal. Click OK in each dialog box “With 95% confidence, it is concluded that the mileage of the cars with Shell Engine oil is significantly different than the mileage of the cars with Castrol engine oil” Copyright © 2018 Advanced Innovation Group Pro Excellence | All Rights Reserved ONE-WAY ANOVA ON MINITAB TOPIC: ONE-WAY ANOVA ON MINITAB Open the excel sheet One-Way ANOVA.XLSX Copy and paste the data of worksheet Choose Stat > ANOVA > One-Way (Unstacked) In Responses in Separate Columns, enter Accuracy – Team A, Accuracy – Team B, Accuracy – Team C, Accuracy – Team D Click OK “With 95% confidence, it is concluded that the accuracy score of at least one of the four teams is significantly different.” Copyright © 2018 Advanced Innovation Group Pro Excellence | All Rights Reserved 1-VARIANCE TEST ON MINITAB TOPIC: 1-VARIANCE TEST ON MINITAB Open the excel sheet 1-Variance test.XLSX Copy and paste the data of worksheet Choose Stat > Basic Statistics > 1 Variance Under Data, choose Samples in columns In Columns, enter Speed of Vehicle (kmph) Check Perform hypothesis test and choose Hypothesized Standard Deviation In Value, enter 10 Click Options. Under Alternative, choose greater than Click OK in each dialog box “With 95% confidence, it is concluded that the standard deviation of the data for speed of vehicle is not significantly greater than 10.” Copyright © 2018 Advanced Innovation Group Pro Excellence | All Rights Reserved 2-VARIANCE TEST ON MINITAB TOPIC: 2-VARIANCE TEST ON MINITAB Open the excel sheet 2-Variance test.XLSX Copy and paste the data of worksheet Choose Stat > Basic Statistics > 2 Variances Under Data, choose Samples in different columns In First, enter KTS – Team 01 In Second, enter KTS – Team 02 Click Options Click the dropdown under Hypothesized ratio and select Variance 1 / Variance 2 Confirm that the Alternative Hypothesis is set to Not Equal Click OK in each dialog box “With 95% confidence, it is concluded that the variance in the Knowledge Test Scores of Team 1 and Team 2 is significantly different.” Copyright © 2018 Advanced Innovation Group Pro Excellence | All Rights Reserved TEST OF EQUAL VARIANCES ON MINITAB TOPIC: TEST OF EQUAL VARIANCES ON MINITAB Open the excel sheet Test of Equal Variances.XLSX Copy and paste the data of worksheet Choose Stat > ANOVA > Test of Equal Variances In Response, enter Project Loss (in millions) In Factors, enter Month Click OK “With 95% confidence, it is concluded that the variance in financial project loss for each month is significantly different.” Copyright © 2018 Advanced Innovation Group Pro Excellence | All Rights Reserved 1-SAMPLE SIGN TEST ON MINITAB TOPIC: 1-SAMPLE SIGN TEST ON MINITAB Open the excel sheet 1-Sample Sign Test.XLSX Copy and paste the data of worksheet Choose Stat > Nonparametrics > 1-Sample Sign In Variables, enter Speed of Vehicle (kmph) Choose Test Median, enter 40 In Alternative, choose Greater than Click OK “With 95% confidence, it is concluded that the median speed of the vehicle is not significantly greater than 40 kmph.” Copyright © 2018 Advanced Innovation Group Pro Excellence | All Rights Reserved MANN-WHITNEY TEST ON MINITAB TOPIC: MANN-WHITNEY ON MINITAB Open the excel sheet Mann-Whitney Test.XLSX Copy and paste the data of worksheet Choose Stat > Nonparametrics > Mann-Whitney In First Sample, enter Median Thickness – Batch 01 In Second Sample, enter Median Thickness – Batch 02 Click OK “With 95% confidence, it is concluded that the median thickness of monitors in batch 01 is not significantly different than the median thickness of monitors in batch 02.” Copyright © 2018 Advanced Innovation Group Pro Excellence | All Rights Reserved MOOD’S MEDIAN TEST ON MINITAB TOPIC: MOOD’S MEDIAN TEST ON MINITAB Open the excel sheet Mood’s Median Test.XLSX Copy and paste the data of worksheet Choose Stat > Nonparametrics > Mood’s Median Test In Response, enter TAT In Factor, enter Shift Click OK “With 95% confidence, it is concluded that at least one of the shifts has a significantly different median TAT.” Copyright © 2018 Advanced Innovation Group Pro Excellence | All Rights Reserved WHAT IS CORRELATION COEFFICIENT? TOPIC: WHAT IS CORRELATION COEFFICIENT? The Correlation Coefficient, r, is Provides the strength and also known as Pearson’s relationship between Y and X Correlation Coefficient variables A +ve r value indicates a positive Values of r range between -1 and correlation; a –ve r value indicates +1 a negative correlation r value close to zero indicates no relationship between X and Y variables Copyright © 2018 Advanced Innovation Group Pro Excellence | All Rights Reserved WHAT IS CORRELATION COEFFICIENT? TOPIC: DIFFERENT r VALUES r = +1 Perfect +ve Correlation r = +0.8 to +1 Strong +ve Correlation r = +0.2 to +0.8 Possible +ve Correlation r = +0.2 to -0.2 No Correlation r = -0.2 to -0.8 Possible –ve Correlation r = -0.8 to -1 Strong –ve Correlation r = -1 Perfect –ve Correlation Copyright © 2018 Advanced Innovation Group Pro Excellence | All Rights Reserved CORRELATION ANALYSIS ON MINITAB TOPIC: CORRELATION ANALYSIS ON MINITAB Open the excel sheet Correlation Analysis.XLSX Copy and paste the data of worksheet Choose Stat > Basic Statistics > Correlation In Variables, enter AHT Financial Loss Click OK “AHT is one of the critical factors that significantly impacts the financial loss for the process.” Copyright © 2018 Advanced Innovation Group Pro Excellence | All Rights Reserved WHAT IS REGRESSION ANALYSIS? TOPIC: WHAT IS REGRESSION ANALYSIS? Regression Analysis helps you identify a Regression Equation Helps you predict performance of Y based on performance of X Regression Analysis can be performed when both X & Y variables are continuous The Regression equation is: Y = mx + b where Y is the predicted value, given the value of x X is the independent variable b is the y-intercept for the straight line and m is the slope of the straight line Copyright © 2018 Advanced Innovation Group Pro Excellence | All Rights Reserved REGRESSION ANALYSIS ON MINITAB TOPIC: REGRESSION ANALYSIS ON MINITAB Open the excel sheet Regression Analysis.XLSX Copy and paste the data of worksheet Choose Stat > Regression > Fitted Line Plot In Response (Y), enter Financial Loss In Predictor (X), enter AHT Under Type of Regression Model, choose Linear Click OK This equation can be used to predict Y based on the performance of X. An important point to note is that the R-square (adjusted) value is a little over 7%. So the confidence level in this regression equation is only 7%. Copyright © 2018 Advanced Innovation Group Pro Excellence | All Rights Reserved CHI-SQUARE TEST ON MINITAB TOPIC: CHI-SQUARE TEST ON MINITAB Open the excel sheet Chi-Square Test.XLSX Copy and paste the data of worksheet Choose Stat > Tables > Chi-Square Test (Two-Way Table in Worksheet) In Columns containing the table, enter Slight, Moderate, A Lot Click OK “With 95% confidence, it is concluded that the smoking status of individuals is not dependent upon gender.” Copyright © 2018 Advanced Innovation Group Pro Excellence | All Rights Reserved 1-PROPORTION TEST ON MINITAB TOPIC: 1-PROPORTION TEST ON MINITAB Choose Stat > Basic Statistics > 1-Proportion Choose Summarized data In Number of Events, enter 129. In Number of trials, enter 421 Check Perform Hypothesis Test. In Hypothesized proportion, enter 0.56 Click Options. Under Alternative, choose Greater than Click OK in each dialog box “With 95% confidence, the proportion of passed audits is not significantly greater than the passed audits target of 56%.” Copyright © 2018 Advanced Innovation Group Pro Excellence | All Rights Reserved 2-PROPORTION TEST ON MINITAB TOPIC: 2-PROPORTION TEST ON MINITAB Choose Stat > Basic Statistics > 2-Proportion Choose Summarized data In First Sample, under Events, enter 129. Under Trials, enter 421 In Second Sample, under Events, enter 300. Under Trials, enter 652 Click OK “With 95% confidence, the proportion of passed audits of team 01 is significantly different than the proportion of passed audits of team 02.” Copyright © 2018 Advanced Innovation Group Pro Excellence | All Rights Reserved HYPOTHESIS TESTING ERRORS TOPIC: HYPOTHESIS TESTING ERRORS Type I Error – P (Reject Ho when Ho is true) = α Type II Error - P (Accept Ho when Ho is false) = β Copyright © 2018 Advanced Innovation Group Pro Excellence | All Rights Reserved WHAT IS BENCHMARKING? TOPIC: WHAT IS BENCHMARKING? Comparison of the current state with outstanding processes or products Comparison may be within the same company or it could be external Use of these comparisons is termed as BENCHMARKING Helps set new targets and find new ways to achieve them Especially helpful when the team has run out of new ideas TOPIC: WHAT ARE THE FOUR STEPS OF BENCHMARKING? Analyze your process Know your competition & industry leaders Study them & incorporate best of the best Gain superiority Copyright © 2018 Advanced Innovation Group Pro Excellence | All Rights Reserved WHAT IS BENCHMARKING? TOPIC: TYPES OF BENCHMARKING? INTERNAL BENCHMARKING Provides easy access to other departments within the same company. Search for exceptional performance is often limited by the company’s culture, norms, and history COMPETITIVE BENCHMARKING Forces an organization to take an external perspective. Focusing on industry practices may limit opportunities to achieve high levels of performance, particularly if a given industry is not known for its quality FUNCTIONAL BENCHMARKING Compares similar functions, typically outside the organization’s industry, and provides ample opportunities to seek out benchmarking partners Copyright © 2018 Advanced Innovation Group Pro Excellence | All Rights Reserved WHAT IS BENCHMARKING? TOPIC: TYPES OF BENCHMARKING? COLLABORATIVE BENCHMARKING Refers to the cooperation between various functions or organizations to achieve benchmarking results Collaborative benchmarking may permit access to specific benchmarking partners that may not exist with the other types of benchmarking Copyright © 2018 Advanced Innovation Group Pro Excellence | All Rights Reserved WHAT IS BENCHMARKING? TOPIC: BENCHMARKING TIPS: THE DO’S Select projects tied to strategic goals & objectives Obtain management commitment Get support & involvement of process owners Benchmark core processes Ensure your process maps are in-place before beginning to benchmark Do plenty of research Research companies you visit before you go and reciprocate Debrief your benchmarking team Copyright © 2018 Advanced Innovation Group Pro Excellence | All Rights Reserved WHAT IS BENCHMARKING? TOPIC: BENCHMARKING TIPS: THE DONT’S Don’t benchmark just to say you benchmarked the process Don’t expect a high return on investment when you are benchmarking non-core processes Don’t benchmark without sufficient support and buy-in Don’t expect to benchmark another’s process without a thorough understanding of your own Don’t trust what you cannot measure Don’t think that you can get a big return without some investment of resources Don’t forget to research internet or any public domains Don’t ask for information that you will not be willing to share Don’t over-control the team Copyright © 2018 Advanced Innovation Group Pro Excellence | All Rights Reserved WHAT IS BRAINWRITING? TOPIC: WHAT IS BRAINWRITING? Copyright © 2018 Advanced Innovation Group Pro Excellence | All Rights Reserved WHAT IS ASSUMPTION BUSTING? TOPIC: WHAT IS ASSUMPTION BUSTING? Assumption Busting as a technique is used to trace back from the current performance problems to identify rules and then surface underlying assumptions. TOPIC: STEPS FOR ASSUMPTION BUSTING? Copyright © 2018 Advanced Innovation Group Pro Excellence | All Rights Reserved WHAT IS MODIFIED BRAINSTORMING TECHNIQUES? TOPIC: WHAT ARE MODIFIED BRAINSTORMING TECHNIQUES? A modified brainstorming technique makes some basic and/or simple amendments to the “regular” creative brainstorming in order to help expand the number and quality of ideas. Copyright © 2018 Advanced Innovation Group Pro Excellence | All Rights Reserved WHAT IS 5S? TOPIC: WHAT IS 5S? 5S is a workplace organization method that can help improve the efficiency and management of operations Applying the 5S steps (that is, Sort [Seiri], Straighten [Seiton], Shine [Seiso], Standardize [Seiketsu], and Sustain [Shitsuke]) reduce problems arising from poor housekeeping or organization Copyright © 2018 Advanced Innovation Group Pro Excellence | All Rights Reserved WHAT IS GENERIC PULL OR PULL SYSTEM? TOPIC: WHAT IS GENERIC PULL OR PULL SYSTEM? Pull systems manage scheduling and work flow so that overproduction and excess inventories are eliminated TOPIC: EFFICIENCIES THAT LEAD TO PULL SYSTEM? Copyright © 2018 Advanced Innovation Group Pro Excellence | All Rights Reserved SOLUTION SELECTION MATRIX TOPIC: SOLUTION SELECTION MATRIX The solution selection matrix is used to evaluate and rank proposed solutions against agreed criteria Effectiveness of the Cost & associated Any inherent Risks in Solution Efforts the Solution Allow team members to agree on the criteria that are critical to solution selection Provides a more objective assessment of the proposed improvement ideas Copyright © 2018 Advanced Innovation Group Pro Excellence | All Rights Reserved SOLUTION SELECTION MATRIX TOPIC: STEPS FOR SOLUTION SELECTION MATRIX 1. Review all available information 2. Confirm the decision factors 3. Rate each factor in terms of its significance 4. List proposed solutions 5. Rate each of the proposed solutions against each decision factor 6. Calculate the overall rating and percentage 7. Use the ratings to prioritize solutions Copyright © 2018 Advanced Innovation Group Pro Excellence | All Rights Reserved WHAT IS A PILOT? TOPIC: WHAT IS A PILOT? IS A TEST OF A PROPOSED SOLUTION(S) IS TYPICALLY PERFORMED ON A SMALL SCALE GIVES DATA ABOUT EXPECTED RESULTS AND EXPOSES ISSUES Reduces the risk of a Allows teams to Allows you to validate failed implementation improve a solution results Is essential to gain a buy-in and to create a momentum Copyright © 2018 Advanced Innovation Group Pro Excellence | All Rights Reserved KEY STEPS TO IMPLEMENT A PILOT TOPIC: KEY STEPS TO IMPLEMENT A PILOT CREATE A PILOT PLAN ENSURE STRONG LEADERSHIP SUPPORT COMMUNICATE THE PLAN TO KEY STAKEHOLDERS TRAIN THE PILOT GROUP IMPLEMENT THE PILOT COLLECT AND ANALYZE FEEDBACK DIAGNOSE GAPS AND REVISE SOLUTIONS AND IMPLEMENT THE SOLUTION Copyright © 2018 Advanced Innovation Group Pro Excellence | All Rights Reserved KEY STEPS TO IMPLEMENT A PILOT TOPIC: TIPS TO BE SUCCESSFUL IN YOUR PILOT STUDY MAKE CAREFUL OBSERVATION OF ALL ACTIVITIES, EFFECTS, AND INTERACTIONS ACTIVELY MANAGE YOUR IMPLEMENTATION PLAN CONTINUE THE PILOT LONG ENOUGH USE APPLICABLE STATISTICAL TOOLS CELEBRATE SUCCESS COMMUNICATE SMALL VICTORIES IMPROVE ON THE DESIGN OFTEN THE PILOT WILL UNCOVER ADDITIONAL OPPORTUNITIES FOR IMPROVEMENT Copyright © 2018 Advanced Innovation Group Pro Excellence | All Rights Reserved WHAT IS MISTAKE- PROOFING? TOPIC: WHAT IS MISTAKE-PROOFING? JAPANESE TERM FOR ERROR PROOFING: A METHOD USED TO PREVENT ERRORS SHUTDOWN CONTROL WARNING SHUTDOWN OR STOP A ELIMINATE THE PROACTIVELY NOTIFY THE PROCESS IMMEDIATELY ON OCCURRENCE OF FAILURE OCCURRENCE OF FAILURE OCCURRENCE OF A IN A PROCESS BEFORE IT OCCURS FAILURE Copyright © 2018 Advanced Innovation Group Pro Excellence | All Rights Reserved WHAT IS AN FMEA? TOPIC: WHAT IS AN FMEA? ACRONYM FOR FAILURE MODE & EFFECT ANALYSIS MOST WIDELY USED TOOL IDENTIFIES PROBABLE FAILURE MODES FOR THE PRODUCT/PROCESS RPN HELPS CREATE SUITABLE ACTION PLANS TO CONTAIN RISK USED AS A LIVING DOCUMENT THAT HELPS BUILD ROBUSTNESS Copyright © 2018 Advanced Innovation Group Pro Excellence | All Rights Reserved WHAT IS AN IMPLEMENTATION PLAN? TOPIC: WHAT IS AN IMPLEMENTATION PLAN? TO BE COMPLETED BEFORE YOU PROCEED ACTION IMPLEMENTATION ON THE SHOP FLOOR KEY ELEMENTS FOR A FULL SCALE IMPLEMENTATION ARE: IMPLEMENTATION PILOT LEARNINGS IMPLEMENTATION OBJECTIVES? INCORPORATED? MILESTONES? INFLUENCE IMPLEMENTATION RESOURCE NEEDS? STRATEGY? BUDGET? Copyright © 2018 Advanced Innovation Group Pro Excellence | All Rights Reserved VALIDATE THE COST BENEFIT TOPIC: VALIDATE THE COST BENEFIT IN THE DEFINE PHASE, THE COST BENEFIT ANALYSIS WAS CALCULATED THERE IS A POSSIBILITY THAT THE COST BENEFIT ANALYSIS MAY HAVE UNDERGONE CHANGES IT IS IMPORTANT TO CONFIRM THE COST BENEFIT ANALYSIS RESULTS AS YOU ARE ENDING THE SIX SIGMA PROJECT JOURNEY STEPS INCLUDE: REACH THE OPERATIONAL / APPROACH THE FUNCTIONAL TEAM FINANCE TEAM AND VALIDATION TO CONFIRM IF ANY CONFIRM ALL COMPLETE VARIABLES ARE CALCULATIONS CHANGED Copyright © 2018 Advanced Innovation Group Pro Excellence | All Rights Reserved VISUAL MANAGEMENT BOARDS (VMB’S) TOPIC: WHAT ARE VISUAL MANAGEMENT BOARDS (VMB’S)? LARGE DISPLAY BOARDS DISPLAYS METRICS, STATUS OF IMPROVEMENT INITIATIVES & ACTIONS HELP DRIVE PERFORMANCE, EMPOWERS YOUR EMPLOYEE, IMPROVES ACCOUNTABILITY SUPPOSED TO BE USED CONSISTENTLY ACROSS ALL OF YOUR TEAMS USE IT AS AN INPUT DURING DAILY OR WEEKLY HUDDLES Copyright © 2018 Advanced Innovation Group Pro Excellence | All Rights Reserved TEAM HUDDLES TOPIC: WHAT IS A TEAM HUDDLE? SHORT GATHERINGS AROUND TEAM VMB’S; PROVIDES FOCUS ON WHAT IS WORKING WELL; CREATES A SENSE OF UNITY, CONNECTION & ALIGNMENT CLARIFIES EXPECTATIONS & PROVIDES FEEDBACK; FOSTERS A POSITIVE TEAM CULTURE HOLD A TEAM HUDDLE AT A CONSISTENT TIME & PLACE EACH DAY; SHOULD NOT EXCEED 15 MINUTES & IDEALLY HELD FACE-TO-FACE TIPS TO HOLD SUCCESSFUL TEAM HUDDLES: STAND UP! BE SURE VMB IS UPDATED PRIOR TO THE HUDDLE SHARE ACHIEVEMENTS, CURRENT ACTIVITIES AND ANY CHALLENGES, ALONG WITH ACTION PLANS TO RESOLVE THEM FOCUS ON MEASURES – WHAT CHANGED? WHY? INVOLVE ALL TEAM MEMBERS IN THE CONVERSATION TAKE MORE COMPLEX ISSUES OFFLINE AS AN ACTION ITEM FROM THE HUDDLE. USE A “PARKING LOT” TO CAPTURE THESE WITHOUT DERAILING THE REST OF THE CONVERSATION Copyright © 2018 Advanced Innovation Group Pro Excellence | All Rights Reserved STANDARD OPERATING PROCEDURES (SOP’S) TOPIC: WHAT ARE SOP’S? WRITTEN INSTRUCTIONS INTENDED TO DESCRIBE HOW TO PERFORM TASKS TO ACHIEVE SPECIFIC RESULTS INCLUDE BENCHMARKS & MEASURES INCLUDE INPUTS, SYSTEMS, OUTPUTS, PROCESS STEPS, HAND-OFFS, CONTROLS, ETC SHOULD FOLLOW A PRESCRIBED STANDARD AND BE HELD CENTRALLY AND ACCESSIBLE BY ALL STAFF DEFINE THE WAY PERSONNEL ARE REQUIRED TO PERFORM A SPECIFIC TASK FACILITATE REDUCTION OF PROCESS VARIATION DEFINE EXPECTED QUALITY & EFFICIENCY TARGETS REDUCE OPERATIONAL RISKS USED DAILY; UPDATED AFTER ANY CHANGE IS CONSIDERED OR IMPLEMENTED USED AS AN INPUT TO ANALYZE PROCESSES; ALSO USED AS A TRAINING AID Copyright © 2018 Advanced Innovation Group Pro Excellence | All Rights Reserved GO GEMBA TOPIC: WHAT IS GO GEMBA? MEANS “THE REAL PLACE”. ITS WHERE THE WORK HAPPENS REFERS TO PHYSICALLY GOING TO THAT LOCATION USED TO IDENTIFY CROSS FUNCTIONAL PROBLEMS AND NEW CUSTOMER REQUIREMENTS USED TO SIMULATE INNOVATIVE IDEAS INVOLVING TEAM MEMBERS WHO ARE DOING THE REAL WORK GEMBA IS EXECUTED BY MANAGERS. QUESTIONS THAT YOU MAY ASK DURING PROCESS WALK: WHERE IS YOUR VMB? WHAT IS THE OBJECTIVE OF YOUR TEAM? WHAT IS THE PURPOSE OF THIS PROCESS? WHO IS RESPONSIBLE FOR IT? WHAT ARE YOUR PERFORMANCE MEASURES? HOW MUCH RE-WORK DO YOU SEE? WHY IS THAT? WHAT IS WORKING WELL? WHAT COULD YOU CHANGE ABOUT THE PROCESS? DO EMPLOYEES HAVE THE RIGHT SKILL SETS AND TOOLS TO PERFORM THEIR WORK? WHERE ARE THE SOPS? ARE THEY HELPFUL? WHEN WERE THEY LAST UPDATED? THE OBJECTIVE OF GO GEMBA IS NOT TO SCARE THE TEAM MEMBERS BY ASKING QUESTIONS Copyright © 2018 Advanced Innovation Group Pro Excellence | All Rights Reserved CONTROL CHARTS TOPIC: WHAT ARE CONTROL CHARTS? HELPS TRACK PROCESS AND PRODUCT PARAMETERS OVER TIME REFERRED TO AS STATISTICAL PROCESS CONTROL (SPC) USED TO ANALYZE AND CONTROL PROCESS PERFORMANCE IDENTIFIES & EVALUATES VARIATION IN IMPLEMENTED PROCESS IMPROVEMENTS ARE SENSITIVE TO SMALL CHANGES OVER TIME USE A CONTROL CHART TO MONITOR PROCESS & OUTPUT METRICS OVER TIME ESPECIALLY USEFUL WHEN A PROCESS HAS CHANGED Copyright © 2018 Advanced Innovation Group Pro Excellence | All Rights Reserved CONTROL LIMITS VS. SPECIFICATION LIMITS TOPIC: CONTROL LIMITS VS. SPECIFICATION LIMITS Copyright © 2018 Advanced Innovation Group Pro Excellence | All Rights Reserved SEVEN INDICATORS OF AN OUT OF CONTROL PROCESS TOPIC: SEVEN INDICATORS OF AN OUT OF CONTROL PROCESS UCL A B C Average C B A LCL One Point Or More Points Fall Outside Of The Control Limits UCL A B C Average C B A LCL Seven Consecutive Points Steadily Increasing Or Decreasing Copyright © 2018 Advanced Innovation Group Pro Excellence | All Rights Reserved SEVEN INDICATORS OF AN OUT OF CONTROL PROCESS TOPIC: SEVEN INDICATORS OF AN OUT OF CONTROL PROCESS UCL A B C Average C B A LCL Eight Consecutive Points On One Side Of The Average UCL A B C Average C B A LCL Fourteen Consecutive Points In An Up And Down Pattern Copyright © 2018 Advanced Innovation Group Pro Excellence | All Rights Reserved SEVEN INDICATORS OF AN OUT OF CONTROL PROCESS TOPIC: SEVEN INDICATORS OF AN OUT OF CONTROL PROCESS UCL A B C Average C B A LCL Two Out Of Three Consecutive Points In Zone A Or Beyond UCL A B C Average C B A LCL Four Out Of Five Consecutive Points In a Row In Zone B Or Beyond Copyright © 2018 Advanced Innovation Group Pro Excellence | All Rights Reserved SEVEN INDICATORS OF AN OUT OF CONTROL PROCESS TOPIC: SEVEN INDICATORS OF AN OUT OF CONTROL PROCESS UCL A B C Average C B A LCL Fifteen Consecutive Points In Zone C Copyright © 2018 Advanced Innovation Group Pro Excellence | All Rights Reserved CONTROL CHART SELECTION TOPIC: CONTROL CHART SELECTION CONTINUOUS DATA o FOR CONTINUOUS DATA WE CAN MEASURE THE AVERAGE AND THE VARIATION, THUS X BAR AND R (RANGE) OR X BAR AND S (STANDARD DEVIATION) CAN BE USED ATTRIBUTE DATA o DETERMINE WHAT ARE WE MEASURING – DEFECTS OR DEFECTIVES o IN CASE WE ARE CAPTURING DEFECTIVE DATA THEN DETERMINE IF WE ARE SAMPLING FOR SUBGROUP OF EQUAL SAMPLE SIZE OR NOT o IN CASE IF WE ARE CAPTURING DATA FOR DEFECTS THEN DETERMINE IF THE OPPORTUNITY FOR THE DEFECTS ARE THE SAME FOR EACH SUBGROUP OR NOT. o BASED ON THE ABOVE SELECT THE APPROPRIATE CHART Copyright © 2018 Advanced Innovation Group Pro Excellence | All Rights Reserved CONTROL CHART SELECTION TOPIC: CONTROL CHART SELECTION Copyright © 2018 Advanced Innovation Group Pro Excellence | All Rights Reserved I-MR CHART ON MINITAB TOPIC: I-MR CHART ON MINITAB Open the worksheet I-MR Chart and copy data into Minitab Choose Stat > Control Charts > Variables Charts for Individuals > I-MR In Variables, enter Accuracy Score Click I-MR Options, then click the Tests tab Choose Perform all tests for special causes, then click OK in each dialog box Copyright © 2018 Advanced Innovation Group Pro Excellence | All Rights Reserved X-BAR R CHART ON MINITAB TOPIC: X BAR R CHART ON MINITAB Open the excel sheet X bar R Chart and copy the data to Minitab Choose Stat > Control Charts > Variables Charts for Subgroups > Xbar-R Choose All observations for a chart are in one column, then enter AHT In Subgroup sizes, enter Reading. Click OK Copyright © 2018 Advanced Innovation Group Pro Excellence | All Rights Reserved X-BAR S CHART ON MINITAB TOPIC: X BAR S CHART ON MINITAB Open the excel sheet X bar S Chart and copy the data to Minitab Choose Stat > Control Charts > Variables Charts for Subgroups > Xbar-S Choose All observations for a chart are in one column, then enter Test Score In Subgroup sizes, enter Reading. Click OK Copyright © 2018 Advanced Innovation Group Pro Excellence | All Rights Reserved NP CHART ON MINITAB TOPIC: NP CHART ON MINITAB Open the excel sheet np Chart and copy the data to Minitab Choose Stat > Control Charts > Attributes Chart > NP In Variables, enter Defectives Found In Subgroup sizes, enter 200. Click OK Copyright © 2018 Advanced Innovation Group Pro Excellence | All Rights Reserved P CHART ON MINITAB TOPIC: P CHART ON MINITAB Open the excel sheet p Chart and copy the data to Minitab Choose Stat > Control Charts > Attributes Chart > P In Variables, enter Defectives Found In Subgroup sizes, enter No of Transactions Monitored. Click OK Copyright © 2018 Advanced Innovation Group Pro Excellence | All Rights Reserved C CHART ON MINITAB TOPIC: C CHART ON MINITAB Open the excel sheet c Chart and copy the data to Minitab Choose Stat > Control Charts > Attributes Chart > C In Variables, enter Defects Found Click OK Copyright © 2018 Advanced Innovation Group Pro Excellence | All Rights Reserved U CHART ON MINITAB TOPIC: U CHART ON MINITAB Open the excel sheet u Chart and copy the data to Minitab Choose Stat > Control Charts > Attributes Chart > U In Variables, enter Defects Found In Subgroup Sizes, enter No of opportunity for defects Click OK Copyright © 2018 Advanced Innovation Group Pro Excellence | All Rights Reserved