Rectificado PDF
Document Details
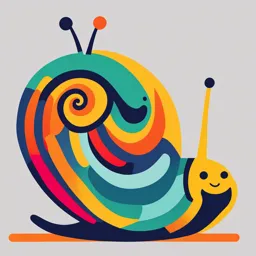
Uploaded by BestSellingSonnet
CEDE
Tags
Summary
Este documento describe diferentes tipos de rectificado en un proceso de mecanizado, incluyendo rectificado plano con muela frontal y tangencial, rectificado cilíndrico exterior e interior, y rectificado sin centro. Se explica la estructura de las rectificadoras y las características de las muelas, incluyendo sus tipos y dimensiones.
Full Transcript
Capítulo 22: Rectificado Fig. 1 Rectificadora plana tangencial. Introducción El rectificado es una operación de mecanizado realizada mediante el arranque de viruta gracias a una máquina llamada rectificadora (fig. 1). Este arranque de viruta se realiza mediante el giro de unas muelas abrasivas forma...
Capítulo 22: Rectificado Fig. 1 Rectificadora plana tangencial. Introducción El rectificado es una operación de mecanizado realizada mediante el arranque de viruta gracias a una máquina llamada rectificadora (fig. 1). Este arranque de viruta se realiza mediante el giro de unas muelas abrasivas formadas por una serie de granos de diferentes durezas y formas. La operación de rectificado se emplea únicamente para el acabado de piezas previamente mecanizadas, ya que las virutas que se consiguen arrancar con estas muelas son muy pequeñas. El rectificado se realiza sobre superficies de revolución o planas y se puede emplear para el mecanizado de piezas de gran dureza superficial como, por ejemplo, las piezas templadas. Clases de rectificadoras Estructura de una rectificadora De forma genérica diremos que las rectificadoras constan de una bancada, sobre la cual se sustenta la máquina, y de una mesa móvil donde se fijan las piezas. Las rectificadoras también poseen un cabezal portamuelas, que posibilita el movimiento de rotación de las muelas, y un cabezal portapiezas; este último solo existe en las rectificadoras cilíndricas y sirve para sujetar y hacer girar la pieza sobre su eje (fig. 2). 353 l a i c n e g n a t a n a l p a r o d a c i f i t c e R a c i r d n í l i c a r o d a c i f i t c e R e t n a r e g i r f e R s a l e lu a zm ea t br ao Cp Fig. 2 a l e u M e t n a t n o M s a l e lu a zm et a br ao Cp o t n u P s a lz e a i zp ea t br ao Cp l a n i d u t a r oi s r g e an M C o l l a n i d u t a r oi s r g e n ao M C l a d a c n a B a d a c n a B Clases de rectificado El movimiento de corte de la muela en una operación de rectificado; se produce al girar ésta sobre su eje a una velocidad elevada. También existen otros dos movimientos en este tipo de operaciones, el movimiento de avance, que lo realiza la pieza al desplazarse la mesa, y el movimiento de penetración, que es el llevado a cabo por la muela al desplazarse hacia la pieza. Dependiendo de estos factores, es decir, de la clase de superficie a rectificar y de la forma en que se realicen los movimientos previamente comentados, existen diferentes tipos de rectificados: - Rectificado plano con muela frontal: en este tipo de rectificado el eje que sustenta la muela es perpendicular a la superficie de la pieza a rectificar. La muela gira a una velocidad de corte indicada por el fabricante Vm, a medida que también se mueve axialmente en dirección a la pieza con un avance de penetración av, que se corresponde con la profundidad de pasada (figs. 3a y 3b). Fig. 3a av Fig. 3b Vm Muela Pieza - Rectificado plano con muela tangencial: este modelo de rectificado se caracteriza porque el plano a rectificar y el eje que sustenta a la muela son paralelos. La muela arranca la viruta por su periferia, lo que mejora la calidad del rectificado, ya que la superficie de contacto se reduce únicamente a una zona tangencial de la muela cilíndrica con la pieza. La muela dispone de un movimiento circular Vm y de un movimiento vertical av para aplicar la pasada. Por su lado, la pieza se mueve longitudinalmente con un avance vp, a la vez que se desplaza transversalmente at al término de cada pasada, teniendo en cuenta el ancho de la muela (figs. 4a y 4b). 354 Fig. 4b Fig. 4a av Muela Vm vp at - Rectificado cilíndrico exterior: se emplea para el rectificado de piezas de revolución; se caracteriza porque el eje de la pieza y el eje que sujeta la muela son paralelos. En este caso la muela describe un movimiento de rotación Vm y de uno transversal at que genera la profundidad de pasada. Por otra parte, la pieza gira sobre su eje con una velocidad vp, a la vez que dispone de otro movimiento longitudinal al, logrando que toda la pieza entre en contacto con la muela (figs. 5a y 5b). En el caso de que la pieza no sea cilíndrica, se orienta la generatriz de la misma hasta que quede paralela a la generatriz de la muela (fig. 6). Fig. 5b Fig. 5a vp Vm at al Fig. 6 355 - Rectificado cilíndrico interior: este rectificado mantiene todos los movimientos del rectificado cilíndrico exterior; la única diferencia se encuentra en la forma en la que están sustentadas la muela y la pieza. La muela se encuentra al aire, sobre un mango, y la pieza va sujeta de forma que su agujero quede libre para poder ser rectificado (fig. 7). Figs. 8a y 8b Fig. 7 vp at Vm Vm V'm Vp al al - Rectificado sin centro: se caracteriza porque la pieza va apoyada sobre una regla de gran dureza y aprisionada sobre dos muelas; una de ellas tiene su eje paralelo al de la pieza y el de la otra muela, más pequeña que la primera, está ligeramente inclinado con el fin de que mueva la pieza y la rectifique a lo largo de toda su longitud. Las dos muelas describen el mismo movimiento circular Vm; la pieza se mueve transversalmente con un avance al y también con un movimiento de rotación sobre su eje Vp. Los dos movimientos de la pieza son generados por la acción de las muelas (figs. 8a y 8b). - Rectificado de perfiles: este tipo de mecanizado requiere una preparación previa de la muela para que esta adquiera la forma de la superficie a mecanizar. Los movimientos característicos de este rectificado son: el de penetración av y el de giro sobre su eje de la muela vm. En las siguientes figuras se resume, de forma esquemática, los rectificados más habituales que vamos a poder desarrollar: Rectificado cilíndrico exterior Rectificado cilíndrico interior Dependiendo de la zona a rectificar, se empleará un portamuelas corto o largo Rectificado cilíndrico "interno - externo" Rectificado cónico "interno - externo" Es posible por el giro de la mesa o, si la pieza está montada al aire, orientando el cabezal donde se encuentre amarrada. 356 Rectificado cilíndrico y frontal Empleando una muela adecuada se puede logra un rectificado cilíndrico y frontal en un único amarre de la pieza. También existe la posibilidad de realizar un rectificado cónico o convexo, orientando el cabezal portamuelas. También se puede lograr girando adecuadamente el cabezal que sustenta la pieza. Rectificado plano tangencial Rectificado cilíndrico frontal Rectificado de ranuras La muela trabaja por su periferia, tangencialmente a la superficie de la pieza. Rectificado plano frontal Rectificado plano con muela de copa Se deberá utilizar una muela de forma, con un perfil adecuado. La pieza se deberá montar sobre cabezal divisor y contrapunto. Rectificado plano transversal Con este procedimiento es posible rectificar guías en forma de cola de milano, empleando una muela con la forma y dimensiones adecuadas. Características y tipos de muelas Las muelas (ruedas de amolar) son aglomerados de forma circular constituidos por granos de abrasivo con aristas vivas, que son los filos de corte. La disposición de los granos de abrasivo y la liga (aglomerante) definen la estructura de una muela concreta. Definimos los productos de abrasivo aglomerado (muelas) como herramientas de corte con múltiples aristas, gracias a los granos abrasivos, unidos entre sí por un producto sólido (aglomerante) que forma un cuerpo. Forma de las muelas: sus formas y tipos se definen según la norma UNE 16300-75. Nosotros estudiaremos las más utilizadas en la actualidad (figs. 9a y 9b): - Muela plana: tipo 1. Muela plana con escote: tipo 5. Muela plana con dos escotes: tipo 7. Muela de vaso: tipo 6. Muela de copa: tipo 11. Muela de plato: tipo 12. Muelas de centro embutido: tipo 27. 357 Fig. 9a Fig. 9b Distintos tipos de muelas. Tabla 10b Tabla 10a Dimensiones: Las dimensiones fundamentales de las muelas son tres: - E D Diámetro exterior “D”. Espesor o ancho de la muela “E”. Diámetro interior o del agujero “d”. mm mm mm Para evitar confusiones con las medidas de las muelas, se deberán escribir las tres dimensiones en el orden anteriormente indicado: Ø exterior x Espesor x Ø interior En las tablas 10a, 10b y 10c se indican las gamas de medidas nominales normalizadas. Tabla 10c mm 8 40 200 600 10 50 250 750 13 63 300 900 16 80 350 1060 20 25 100 400 125 450 1250 1500 32 150 500 d mm mm mm mm 0.6 4 25 160 0.8 5 32 200 1 6 40 250 1.25 8 1.6 10 2 13 50 315 63 400 80 500 2,5 16 100 — 3,2 20 125 — mm mm mm 1,6 20 2,5 4 6 10 50,8 25 76.2 32 127 40 152,4 — 203,2 13 — 304,8 16 — 508 Características: Las muelas se caracterizan principalmente por una serie de aspectos que también intervienen a la hora de designarlas: 1º El tipo y la naturaleza del abrasivo: son las sustancias naturales (minerales) o productos artificiales que componen los granos de la muela. Del tipo de abrasivo dependerá la dureza de la muela: - Corindón, Al2O3 (dureza 9, según la escala Mohs). Se utiliza para materiales tenaces como toda clase de aceros (excepto algún tipo de acero inoxidable), hierro dulce, fundición dulce y bronce tenaz. - Corindón artificial (dureza 9.25). Amuela con una acción cortante excepcionalmente fresca y rápida; se caracteriza por su adaptabilidad para amolar piezas de acero en estado blando o duro. 358 - Carburo de silicio, SiC (dureza 9.75). Se usa para materiales duros y frágiles, como hierro colado ordinario y en coquilla. También para materiales dúctiles muy blandos, tales como aluminio, latón, bronce blando, cobre, etc. - Diamante (dureza 10). Se emplea para amolar y cortar carburos cementados, materiales cerámicos, vidrio, cuarzo, granito, mármol y piedras para gemas. Se empleará la letra “A” para los abrasivos aluminosos y la letra “C” para los de carburo de silicio. 2º Grosor o tamaño del grano: el grosor del grano se designará por números que irán desde el 8, que indicará el tamaño más grueso, hasta el 1200, que marcará el grosor más fino. El tamaño del grano afecta a la cantidad de material levantado y a la rugosidad de acabado obtenida. Una combinación de mezclar dos tamaños de grano en la misma muela es útil para ciertas operaciones y se designa por una letra o cifra después del número del tamaño de grano. 3º Grado de dureza: es la fuerza (tenacidad) con la que el aglomerante retiene a los granos de abrasivo que forman la muela. Ésta será más dura cuanto más difícil les sea a los granos separarse durante el rectificado y más blanda cuando ocurra exactamente lo contrario. El grado de dureza depende del tamaño del grano, tipo de aglomerante, estructura y condiciones de funcionamiento; estas últimas alteran el grado efectivo o activo de la muela en uso. Por ejemplo, un tamaño fino de grano o una estructura densa hacen que el grado parezca más duro, mientras que la influencia de las condiciones de funcionamiento producen lo contrario. Se designa por una letra del alfabeto, siendo la A el grado más blando y la Z el más duro. 4º Estructura: es la relación cuantitativa existente entre los granos, la porosidad y el aglomerante que lleve la muela. Una estructura cerrada se designará por un número comprendido entre el 0 y el 3; será aquella cuyos granos están muy cercanos. Una muela con estructura abierta (de 7 a 12) es aquella que tiene una porosidad mayor, es decir, que los granos están más separados. En el medio existe otro tipo denominada estructura media (de 4 a 6) (fig. 11). Diremos que cuanto menor es el número que la designa más apretados estarán los granos del abrasivo. Una estructura abierta de una muela caracterizada por sus amplios espacios de aire proporciona una amplia holgura a la viruta y reduce al mínimo la carga o embotamiento, por lo que se recomienda su uso para materiales blandos, tenaces y dúctiles y para el rectificado de superficies ordinarias. Una estructura cerrada es recomendada para acabados superficiales rigurosos, puesto que lo cerrado de los granos hace menores las distancias entre los diminutos surcos producidos en la pieza, generando mejores acabados superficiales. Fig. 11 Estructura cerrada Estructura abierta Estructura porosa 5º Aglomerante: es una sustancia que actúa como pegamento entre los granos de abrasivo; existen diferentes tipos de aglomerante y se designan por una letra; los principales son: - Vitrificado o cerámico (V): es el más empleado (75% de las muelas); de naturaleza cerámica y se obtiene a altas temperaturas. Este tipo de aglomerante es muy poroso, lo que incrementa su capacidad abrasiva. Soporta con facilidad la fuerza centrifuga, aunque, resulta muy frágil a los choques mecánicos. La porosidad y resistencia de las ruedas permiten rebajar gran cantidad de material y su rigidez ayuda a hacer trabajos con gran precisión. Además, a este tipo de muelas, no les afectan los ácidos, el agua, los aceites, ni los cambios normales de la temperatura. - Resina sintética (B): se utiliza con frecuencia en muelas delgadas; también se puede usar en muelas que trabajan a velocidades muy altas. Tienen gran aplicación en talleres de fundición, así como en labores de recortado y amolado de roscas. - Caucho (R): se usa para muelas muy finas (con espesores de 0.2 mm), y que deben soportar grandes resistencias. Con estas muelas se trabajará a velocidades muy elevadas, para que la fuerza centrífuga mantenga el perfil. Se utilizan frecuentemente para desbarbar con amoladoras portátiles cuando el acabado es importante, como en soldaduras de acero inoxidable. - Goma laca (E): empleado en muelas para el acabado de hierro en coquilla o fundido y en rodillos de acero, levas de acero templado y pistones de aluminio. Estas muelas también van a poder presentar secciones muy delgadas, (hasta espesores de 0.9 mm), empleándolas en máquinas de corte abrasivo. 359 - Silicato (S): poco usado en el rectificado de precisión. Se emplea cuando deben mantenerse bajas las temperaturas durante el amolado, ya que con estas temperaturas de ella se desprenden más fácilmente los granos abrasivos, haciendo que la rueda tenga una acción más suave. También se utiliza en ruedas muy grandes para amolar herramientas de filo. Designación de las muelas Las muelas se identifican habitualmente conforme a la norma UNE 16-300-75. Esta designación implica una serie de símbolos, letras y números, que deben colocarse en un orden determinado (fig. 12), y que se exponen de forma resumida en la tabla 13. Tabla 13 0º 1º 2º 3º 4º 5º 6º TIPO DE ABRASIVO (Facultativo – Opcional) NATURALEZA DEL ABRASIVO TAMAÑO DEL GRANO GRADO ESTRUCTURA (Opcional) NATURALEZA DEL AGLOMERANTE TIPO DE AGLOMERANTE (Facultativo – Opcional) A - Abrasivos aluminosos Basto Blando Densa V 8, 10, 12, 14, 16, 20, 24. F, G, H, I, J, K. 0, 1, 2. Vitrificado Normal B 3, 4, 5, 6, 7, 8. Resina sintética Abierto R 9, 10, 11, 12, 14, etc. Caucho (Propio del fabricante) (Corindón) Medio 30, 36, 46, 54, 60, 70. Medio Fino L, M, N, O, P, Q. 80, 90, 100, 120, 150, 180. C - Carburo de Silicio Muy fino Duro 220, 240, 280, 320, 400, 500, 600, 800, 100, 1200 R, S, T. Nota: Los fabricantes podrán hacer seguir el número del grosor del grano por un símbolo que precise las combinaciones de grosores diferentes. (Propio del fabricante) E Goma laca S Silicato Tendremos presente que el fabricante podrá hacer preceder a la letra que designa la naturaleza del abrasivo un símbolo de su elección, precisando el tipo y origen del abrasivo en cuestión. Igualmente, podrá finalizar la designación indicando el tipo de aglomerante (fig. 14). Fig. 12 La designación completa de un producto abrasivo estará compuesta de las indicaciones de forma y dimensiones de la muela, así como las características de la naturaleza interna del producto. Ejemplo: Forma: Tipo 1; Dimensiones: 300x40x32; Especificaciones: 51A-36-L-5-V32 Es necesario recordar también la importancia de las prescripciones de seguridad relativas a la velocidad máxima de trabajo a la que podrá girar la muela. Por eso, esta indicación vendrá anotada en la misma muela o en una etiqueta que la acompañe. 360 Fig. 14 Empleo de las muelas Existen una serie de factores que deben tenerse en cuenta al seleccionar las especificaciones de una rueda de amolar; entre otros son: - - El tipo de material que se va a amolar y su dureza, ya que influyen directamente sobre el tipo de abrasivo, el tamaño del grano y el grado: o Se utilizará abrasivo tipo corindón para acero y aleaciones de acero, y abrasivo tipo carburo de silicio para metales no ferrosos, hierro fundido y materiales no metálicos. o Se emplearán granos bastos para materiales blandos y dúctiles, y granos finos para materiales duros y quebradizos. o Si son materiales fácilmente penetrables, se empleará grado duro; en cambio, si son materiales duros, utilizaremos ruedas de amolar de grado blando. La cantidad de material que se pretende rectificar, así como el acabado superficial requerido, influyen sobre todo en el tamaño del grano y en la elección del aglomerante: o Se emplearán granos bastos y aglomerante vitrificado para amolar material rápidamente. o Se usará aglomerante resinoide, de goma y de laca, así como granos finos, para acabados superficiales controlados. - El rectificado en seco o en húmedo influye directamente en la selección del grado de la muela, ya que un trabajo en húmedo permite usar una rueda de un grado superior, sin peligro de quemar la pieza. - La velocidad de la rueda influye en la selección del aglomerante. Se utilizarán velocidades menores para ruedas vitrificadas que para el resto, pero nunca se deberá sobrepasar la velocidad segura de funcionamiento que aconseja el fabricante. - El área de contacto en el amolado influye en la selección del tamaño del grano y del grado (mayor tamaño cuanto mayor área de contacto). Además, cuanto mayor sea el área de contacto, más dura deberá ser la rueda. - La rigurosidad de la labor de amolar influye en la selección del abrasivo, ya que, cuanto más tenaz, mejor precisión y rigurosidad de trabajo. No obstante se suele emplear genéricamente un abrasivo intermedio, tipo corindón, para tareas de precisión normal. Montaje de las muelas Para conseguir un buen rectificado es muy importante que las muelas estén montadas correctamente; para ello se deben tener en cuenta una serie de normas fáciles de comprender y de aplicar, para que el esmerilado sea lo más perfecto posible, a la vez que se eviten accidentes. Las normas son las siguientes: 1) Antes de montar la muela hay que asegurarse de que se adecue al trabajo que se va a realizar. 2) Se debe realizar la prueba de sonido, que consiste en golpear suavemente con un mazo la muela libremente suspendida; el resultado debe ser un sonido claro que nos indique que la muela no esconde fisuras internas. Las muelas con aglomerante resinoide no presentan sonoridad, pero tampoco tienen tendencia a agrietarse. 3) Debido a la constitución irregular en cuanto a la densidad de la muela, a defectos de excentricidad en los agujeros y a pequeños errores de paralelismo entre sus caras, es fundamental comprobar el correcto equilibrado antes de su montaje en máquina; al girar a gran velocidad durante su trabajo, cualquier descompensación podría provocar un grave accidente. Si utilizásemos una muela desequilibrada, se generarían vibraciones que se transmiten a la máquina y finalmente a la pieza y al proceso de rectificado. El resultado sería una pérdida de precisión en la operación, y, en casos extremos, incluso la rotura de la 361 muela, con el consiguiente riesgo que esto conlleva. Habitualmente, la operación de equilibrado se realiza en muelas que superen los 250mm de diámetro y se suele realizar con la ayuda de un aparato para el equilibrado estático y unos contrapesos móviles que presentan las bridas o platos portamuelas, normalmente en número par, (dos o cuatro). El proceso a seguir es el siguiente: se monta la muela en un mandril, haciendo reposar todo el conjunto en el aparato de equilibrado, que presenta dos rodillos totalmente horizontales. La rueda tenderá a girar, adquiriendo una posición determinada; en esta posición se moverán los contrapesos hasta colocarlos horizontalmente y se irán elevando progresivamente a la vez que se comprueba el giro de la muela sobre el útil. Cuando el conjunto quede estático significará que el equilibrado es correcto (figs. 15 y 16). Fig. 15 Fig. 16 4) La muela debe introducirse en su asiento, sin ser forzada ni con un excesivo juego; si esto último ocurre, se emplearían unos casquillos con el fin de eliminar el juego existente. 5) Las muelas se sujetan y son arrastradas con una brida cóncava a cada lado de la misma y cuyo diámetro debe ser al menos 1/3 del diámetro de la muela. 6) Entre las muelas y las bridas de sujeción deben ir situados unos discos de material elástico, con el fin de que el contacto entre ambas sea total. Habitualmente, las propias muelas ya van provistas de estos discos. 7) La fijación de la muela en la máquina se va a poder realizar de diversas formas. Así, encontraremos muelas que se montan directamente sobre el eje de la máquina mediante dos bridas y una tuerca (fig. 17). Cuando la muela es de un diámetro considerable, se suele colocar una chaveta para asegurar el giro solidario de la herramienta con el eje (fig. 17). Este sistema es empleado para diámetros de hasta aproximadamente 300mm. Para muelas muy grandes se suele realizar la fijación mediante un útil portamuelas. Cuando, por el contrario, tenemos muelas muy pequeñas pueden presentar un vástago propio para su fijación. Habitualmente se amarrarán a una pinza o plato de garras. 8) La tuerca de cierre no debe apretarse en exceso, revisando que no se afloja con el movimiento de la muela. 362 Fig. 17 Perfilado y afilado de las muelas El perfilado de las muelas se lleva a cabo cuando estas deben tener una forma específica para el rectificado de perfiles de ciertas piezas. Para realizarlo se suele emplear un útil de diamante. El afilado es una operación que sirve para mantener el perfil de las muelas rectas, para repasar la excentricidad y también para reavivarla. Reavivar la muela significa abrir sus poros eliminando los granos de abrasivo gastados, a la vez que hace que aparezcan unos nuevos con las aristas de corte intactas. Este proceso también elimina las virutas metálicas que se hayan podido quedar incrustadas en la muela durante el proceso de rectificado. Consejos para el afilado de muelas: - El afilado a mano es el menos aconsejable. Se suelen emplear perfiladores cuando haya que afilar o perfilar muelas pequeñas o con cierta precisión (fig. 18). Se utilizan las piedras de ajuste de muelas, llamadas comúnmente “escoria”, para reavivar las muelas convencionales y lograr recuperar las propiedades iniciales (fig. 19). Fig. 18 Perfilador de muelas. Fig.19 Reavivado de una muela de esmeril. - También se puede utilizar un perfilador con punta de diamante en un dispositivo de rectificar correctamente diseñado, que evite vibraciones. Cuando se empleen estos sistemas, las operaciones suelen realizarse automáticamente por la propia máquina acoplando el perfilador en un útil adecuado (figs. 20 y 21). - Para afilar la muela, se aconseja utilizar la misma velocidad que para rectificar, excepto cuando se rectifiquen roscas, para lo que se emplearán velocidades más elevadas. - Nunca se rectificará o afilará la muela sin antes hacerla funcionar previamente, para que los componentes alcancen la temperatura normal de trabajo. - Coloque el diamante (fig. 22), y comience siempre las pasadas desde el filo de la muela. Desplace siempre el diamante transversalmente de manera regular. Es aconsejable utilizar refrigerante en abundancia cuando afile. 363 Fig. 20 Perfilador de grano múltiple. Fig. 21 Disposición para el afilado de una muela en una rectificadora plana tangencial. Fig. 22 Proceso de afilado de muela en rectificadora cilíndrica Conservación de las muelas Es de suma importancia una correcta conservación de las muelas, con el fin de asegurar su perfecto estado y que cuando tengan que ser usadas funcionen correctamente, con las condiciones exigidas. El fabricante suele aconsejar unas pautas de almacenaje; en este apartado comentaremos unos criterios a tener en cuenta: - Las ruedas rectas y las de copa de menos de 150 mm han de almacenarse sobre sus filos en estantes y en un lugar seco, nunca en el suelo o en bancos, ya que en estos lugares es muy probable que se estropeen o se empapen de aceite y suciedad. - Las muelas rectas vitrificadas y de silicato de más de 150 mm deben amontonarse planas, con discos entre ellas de un material blando como puede ser cartón ondulado (fig. 23). - Las muelas aglomeradas con laca, goma o resina sintética deben almacenarse siempre planas para evitar su alabeo. Fig. 23 Precauciones en el uso de las muelas Para que un trabajo de rectificado se lleve a cabo con exactitud y sin ningún tipo de peligro para el operario que lo está realizando, es necesario tener en cuenta una serie de precauciones: 1) Antes de comenzar, comprobar que la muela se encuentra en correcto estado, que está perfectamente equilibrada y gira dentro de las revoluciones indicadas por su fabricante. 364 2) Realizar el contacto entre la muela y la pieza con extremada suavidad y precaución. Se empleará el tornillo micrométrico de avance para lograr la precisión de movimiento deseada en la aproximación de la muela. 3) Evitar que la presión existente entre la muela y la pieza sea muy alta. 4) Como criterio general se emplearán pasadas de desbaste de 3 - 5 centésimas y, para operaciones de conclusión o acabado, se podrán emplear pasadas de entre 0 y 3 micras. 5) Usar siempre la muela adecuada al trabajo que se va a realizar. 6) Unos instantes antes de empezar con el rectificado, poner la máquina en marcha para que todos sus órganos de movimiento cojan temperatura y no comiencen a trabajar en frío. 7) Como medida de seguridad, el operario evitará en todo momento ponerse en la zona de proyección de la maquina y utilizará gafas de protección. Como complemento de esta precaución, las maquinas deben estar provistas de unas pantallas de protección que cubran 270º de la superficie de proyección de la muela (fig. 24). Fig. 24 8) Se intentará utilizar toda la cara de trabajo de la muela con el fin de evitar que se desgaste irregularmente. 9) Si es posible, debe usarse abundante refrigeración; además, deberá estar dirigida al punto de contacto entre la muela y la pieza para evitar el calentamiento de la misma (fig. 25). En caso de que la maquina necesariamente tenga que trabajar en seco, se le instalara un sistema de aspiración. Fig. 25 Fig. 26 365 Refrigeración en el proceso de rectificado Durante el rectificado se alcanzan temperaturas elevadas, lo que produce tensiones internas, deformaciones, dilataciones, etc., en las piezas; para reducir estos efectos se empleará un refrigerante adecuado. Este líquido también posee propiedades limpiadoras para la muela, impidiendo que los poros se emboten y permitiendo que la muela pueda seguir haciendo su trabajo con eficacia. A la hora de usar refrigerante hay que tener una serie de precauciones: - Ha de ser usado en abundancia y aplicado sobre la superficie de contacto de la pieza y la muela, de modo que se lleve el calor tan pronto como se genere; no debe salpicar alrededor debido a la fuerza centrífuga producida por el rápido movimiento de la muela (fig. 26). - No se conectará la refrigeración de improvisto durante el proceso de rectificado, ya que se puede producir un choque térmico que podría llegar a agrietar la pieza e incluso a romper la muela. - Cuando se usa una muela que es muy porosa, conviene dejarla en funcionamiento durante unos instantes al término del trabajo para eliminar el posible liquido que pueda haber quedado dentro de ella, con el fin de evitar que se produzcan desequilibrios. Los líquidos que se emplean para el refrigerado en las operaciones de rectificado son muy variados, dependiendo del material que se está mecanizando; de forma genérica podemos decir que: - Para aceros, aleaciones ligeras y ciertos tipos de fundición se emplea taladrina (verde) con una emulsión del 10%. - Para otro tipo de fundiciones que se suelen rectificar en seco, se utiliza un sistema de aspiración adecuado. Es aconsejable limpiar los depósitos y filtros de la instalación al menos cada semana y siempre que se cambie de una muela basta a una fina. Limpiar al mismo tiempo la máquina, especialmente el interior de las protecciones de las muelas. Defectos más comunes del rectificado Los defectos que se pueden encontrar en el rectificado son muchos y de varios tipos, pero los más generales son los siguientes: - Grietas: se producen debido a la diferencia de temperatura existente entre la periferia de la pieza, (que está caliente debido al rozamiento con la muela y tiende a dilatarse), y el núcleo de la misa, que se encuentra frío e impide dicha dilatación de la periferia, lo que produce las grietas en su superficie. - Manchas de calentamiento: son zonas de color azulado que aparecen en la superficie de las piezas como consecuencia de la acción de la muela; se producen debido a un calentamiento excesivo de la superficie; ya sea por utilizar una velocidad muy alta o por otros motivos. El problema que generan estas manchas no es únicamente de apariencia, ya que estas zonas quemadas quedan ligeramente debilitadas y no en todos los casos es posible eliminarlas (fig. 27). - Facetas: son franjas irregulares que se producen en las piezas. Son causadas por vibraciones, irregularidades en la máquina, etc. La zona afectada sufre defectos superficiales que son apreciables a simple vista, frecuentemente con la reflexión de la luz. - Estrías: son marcas que aparecen en las piezas después de mecanizadas y son debidas a avances muy altos, suciedad en los refrigerantes, granos irregulares, etc. 366