Introduction to Quality Service in Tourism and Hospitality PDF
Document Details
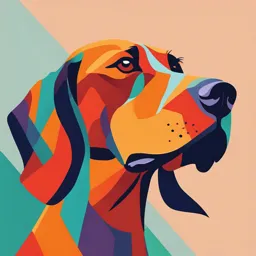
Uploaded by StateOfTheArtHawthorn4198
Tags
Related
- Quality Service Management in Tourism and Hospitality PDF
- Quality Service Management in Tourism & Hospitality PDF
- Quality Service Management in Tourism and Hospitality PDF
- QSM Lesson 1 & 2 PDF
- Unit 1: Overview of Quality Service PDF
- Introduction to Total Quality Management in Hospitality and Tourism Industry PDF
Summary
This document provides an introduction to quality service management in tourism and hospitality. It covers definitions, dimensions of quality (like reliability and empathy), and Total Quality Management (TQM) strategies and different approaches. The document also highlights the contributions of quality management pioneers, like Shewhart, Deming, and Juran. It includes a discussion on how to create a fishbone diagram.
Full Transcript
INTRODUCTION TO QUALITY SERVICE IN TOURISM AND HOSPITALITY GTHMULDV – QUALITY SERICE MANAGEMENT IN TOURISM AND HOSPITALITY Learning Objectives At the end of this chapter, the student must be able to: 1. Define and explain what Total Quality Management...
INTRODUCTION TO QUALITY SERVICE IN TOURISM AND HOSPITALITY GTHMULDV – QUALITY SERICE MANAGEMENT IN TOURISM AND HOSPITALITY Learning Objectives At the end of this chapter, the student must be able to: 1. Define and explain what Total Quality Management (TQM) is; 2. Explain the concepts of quality and its relation to management; 3. Outline the different dimensions of quality; and 4. Analyze the different contributions made by pioneers in total quality and service management. Dimensions of TSQM Reliability- is the ability to perform the promised service dependably and accurately. Customers want to count on the businesses they buy from; that’s at the heart of this dimension. Dimensions of TSQM Empathy- is the caring, individualized attention the firm provides its customers. Showing empathy to customers means ensuring your company showcases your care. Training employees on providing excellent and empathetic service where smiles and engaging conversation occur regularly can help you exceed expectations. Customers want to feel like they’re more than a transaction; they want to build a relationship with your business. Even if you have the best product or services, you can still fall short of their expectations. Dimensions of TSQM Assurance- is employees' knowledge and ability to convey trust and confidence. Dimensions of TSQM Responsiveness- the willingness to help customers and provide prompt service; it lets your customers know you’re listening to them and working actively to solve their problems. Dimensions of TSQM Tangibility- the appearance of physical facilities, equipment, personnel, and communication materials. Customers expect clean and professional facilities and shops, employees who look groomed and neat, and well-written and designed materials such as menus, websites, and signs. Attention to appearance can indicate that your company takes customer comfort seriously. TQM Strategies & Approach TQM Element Approach- Kaizen Approach (Continuous improvement)- your company’s go al or objective when following this approach is continuous improvement by development of products and services. Guru Approach- you are following one specific person or leader when it comes to decision making. Organizational Model Approach- you are following the organizational chart, there is a hierarchy to be followed. TQM Strategies & Approach The Japanese Total Quality Approach- Japanese are known to be perfectionist. This approach is process-oriented, effort-driven, long-term, gradual, practically painless, emphasizes the importance of an organization's people, and works best when companies can accommodate slow-growth strategies. TQM Strategies & Approach The Award Criteria Approach- you are following the company’s operations based on the award that you want to achieve. Shangri-La Hotel Six Sigma- refers to a statistical measure of how far a process deviates from perfection. A process that operates at six sigma has a failure rate of only 0. 00034%, which means it produces virtually no defects. Applicable to healthcare, finance, manufacturing industries. ISO 9001- It helps organizations of all sizes and sectors to improve their performance, meet customer expectations and demonstrate their commitment to quality. Its requirements define how to establish, implement, maintain, and continually improve a quality management system (QMS). Lean Manufacturing- is a methodology that focuses on minimizing waste within manufacturing systems while simultaneously maximizing productivity. Waste is seen as anything that customers do not believe adds value and are not willing to pay for. 1. Walter A. Shewhart An American physicist, engineer and statistician. He is also known as the Father of Statistical Quality Control and also related to the Shewhart cycle. 2. William Edwards Deming ⭐ An American engineer. statistician, professor, author, and management consultant. ⭐ He championed the work of Walter Shewhart, including statistical process control, operational definitions, and what Deming called the "Shewhart cycle" which had evolved into Plan-Do-Study-Act (PDSA). 3. Joseph M. Juran He made many contributions to the field of quality management in his more than 70 active working years. His book. Quality Control Handbook, is a classic reference quality engineers. He revolutionized the Japanese philosophy on quality management and in no small way worked to help shape Japan's economy into the industrial leader it is today. Dr. 3. Joseph M. Juran ⭐ Duran was the first to incorporate the human aspect of quality management which is referred to as Total Quality Management(TQM). ⭐ He illustrated this concept in "Juran trilogy," a cross-functional management approach, constituted of three managerial processes: quality planning, quality control, and quality improvement. 4. Philip B. Crosby ⭐ He was a businessman and author who contributed to management theory and quality management practices. ⭐ He initiated the Zero Defects program at the Martin Company. As the quality control manager of the Pershing missile program. ⭐ Crosby was credited with a twenty-five percent (25%) reduction in the overall rejection rate and a thirty percent (30%) reduction in 4. Philip B. Crosby 4. Philip B. Crosby DIRFT- Doing it right the first time 1. Quality must be viewed as conformance to specifications. 2. Quality should be achieved through the prevention of defects rather than inspection after the production process is complete. 3. Production workers should be granted the authority and responsibility to ensure that quality goods or services are produced at every step of the process. 4. Managers need to demonstrate that a higher standard of performance can lead to perfection -to zero defects. 5. Quality should be measured by the price of nonconformity. 5. Armand V. Feigenbaum He was an American quality control expert and businessman. He devis the concept of Total Quality Control cr- Qc) which inspired Total Quality Management (TQM). 5. Armand V. Feigenbaum Hidden Plant The elements of total quality to enable a totally customer focus (internal and external) Quality is the customers perception of what quality is, not what a company thinks it is. Quality and cost are the same not different. Quality is an individual and team commitment. Quality and innovation are interrelated and mutually beneficial. Managing Quality is managing the business. 5. Armand V. Feigenbaum Quality is a principal. Quality is not a temporary or quick fix but a continuous process of improvement. Productivity gained by cost effective demonstrably beneficial Quality investment. Implement Quality by encompassing suppliers and customers in the system. 6. Kaoru Ishikawa He is notable for rejuvenating the norm in the workplace. He always believed that quality should not stop in reinventing a product alone. He was one of the few people who believed that delivering quality does not stop in purchasing the product; it goes beyond the transaction itself. 6. Kaoru Ishikawa Thus, he highlighted and reinvented the concept of customer service, giving us the concept of after-sale service and warranty. He was also the one who coined the "Ishikawa" or "fishbone“ diagram that highlights the cause and effect of the activities and processes while in constant search of quality in operations. Steps to Create a Fishbone Diagram 1.Define the Problem: Clearly identify the problem or issue you want to address in the tourism sector. 2. Draw the Basic Structure: Draw a horizontal line to represent the "fish's spine." This is where you will write the problem statement. Draw a box at the left end of the line to represent the "fish's head." This is where you will write the problem. Steps to Create a Fishbone Diagram 3. Identify Major Cause Categories: Brainstorm the primary factors that could contribute to the problem. In tourism, these often include: Draw main lines branching off from the spine, one for each major category. 4. Brainstorm Specific Causes: For each major cause category, brainstorm specific factors that could contribute to the problem. Draw smaller lines branching off from the main lines to represent these specific causes. 5. Identify Root Causes: Analyze the diagram to identify the root causes of the problem. These are the underlying issues that contribute to multiple specific causes. Example Example Activity 1. Make a group consisting of 5 members. 2. In a piece of paper, make a simple fishbone diagram about “Low Hotel Guest Satisfaction” 3. Write at least 6 main causes and 2 minor causes for each major cause. 4. This activity is worth 50 points. Criteria Exceeds Meets Expectation Below Expectation Poor Expectation (10) (8) (7) (5) Content & Clearly states theClearly states thePartially states the Does not state the Development problem and severalproblem and factorsproblem and factors problem or factors factors contributingcontributing to contributing to contributing to to problem. problem. problem. problem. Categories Includes at least two Includes at least oneIncludes three to Includes less than items in at least sixitem in at least fivefour categories. three categories. categories(i.e. categories(i.e. People, Processes,People, Processes, etc) etc). Organization Diagram isDiagram isDiagram is Diagram is organized, logical,organized and easyunorganized and incomplete. and easy to follow. to follow. difficult to follow. End of Presentation