Quality Assurance and Management Module 1 Notes PDF
Document Details
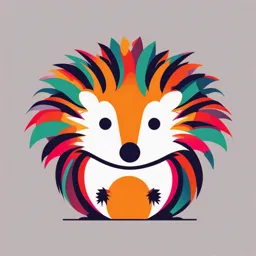
Uploaded by DesirousVampire
Sushant University
Tags
Related
- Quality Assurance and Total Quality Management CA2 PDF
- Quality Assurance and Total Quality Management PDF
- Quality Assurance and Management Module 1 Notes PDF
- Quality Control 1 - Introduction to Quality Control and Total Quality System PDF
- Total Quality Management in Curriculum PDF
- Healthcare Quality Management (MCQ11212) PDF
Summary
This document describes various quality management concepts, including Total Quality Management (TQM), Lean Management, Six Sigma, and the PDSA Cycle. It also examines quality standards like ISO 9001, GMP, and GCP, and discusses quality improvement tools such as Root Cause Analysis and Pareto Charts.
Full Transcript
**Quality Assurance and Management (Module 1 Notes)** **1. Introduction:** - **Quality Assurance (QA):** QA involves systematic processes to ensure that products and services meet specified quality standards and requirements. It focuses on preventing defects and ensuring the quality...
**Quality Assurance and Management (Module 1 Notes)** **1. Introduction:** - **Quality Assurance (QA):** QA involves systematic processes to ensure that products and services meet specified quality standards and requirements. It focuses on preventing defects and ensuring the quality of outputs through planned and systematic activities. - **Quality Management (QM):** QM encompasses all activities related to maintaining and improving the quality of products or services. It includes QA, quality control (QC), and continuous quality improvement (CQI) efforts to enhance performance and customer satisfaction. **2. Quality Improvement Approaches:** - **Total Quality Management (TQM):** An organization-wide approach to embedding a culture of quality at all levels, focusing on long-term success through customer satisfaction and continuous improvement. - **Lean Management:** Focuses on eliminating waste and improving efficiency by streamlining processes and enhancing value for customers. - **Six Sigma:** A data-driven approach to improving quality by identifying and removing causes of defects and variability in processes. It uses statistical methods and follows a structured methodology (DMAIC: Define, Measure, Analyze, Improve, Control). - **Plan-Do-Study-Act (PDSA) Cycle:** An iterative, four-step model for improving processes and outcomes. It involves planning a change, implementing it, studying the results, and acting on what is learned. - **Kaizen:** A Japanese term meaning \"continuous improvement.\" It emphasizes incremental changes and employee involvement to improve processes and eliminate inefficiencies. **3. Standards and Norms:** - **ISO 9001:** An international standard specifying requirements for a quality management system (QMS). It focuses on meeting customer expectations and regulatory requirements and enhancing customer satisfaction. - **Good Manufacturing Practice (GMP):** Standards ensuring that products are consistently produced and controlled according to quality standards. GMP is crucial for industries such as pharmaceuticals and food production. - **Good Clinical Practice (GCP):** A set of standards for designing, conducting, and reporting clinical trials to ensure the safety and rights of trial participants and the integrity of trial data. - **Accreditation Standards:** Industry-specific standards set by accreditation bodies (e.g., NABH for healthcare facilities, NABL for laboratories) to ensure compliance with quality and safety criteria. **4. Quality Improvement Tools:** - **Root Cause Analysis (RCA):** A method used to identify the underlying causes of problems or defects. Techniques include Fishbone Diagram (Ishikawa) and 5 Whys. - **Pareto Chart:** A bar graph that represents the frequency or size of problems in descending order, based on the Pareto Principle (80/20 rule), which identifies the most significant factors affecting quality. - **Flowchart:** A visual representation of a process, used to identify steps, inputs, and outputs. It helps in understanding and analyzing workflows and spotting inefficiencies. - **Control Charts:** Graphs used to monitor the performance of processes over time. They help in identifying variations and determining if a process is in a state of statistical control. - **Fishbone Diagram:** Also known as Ishikawa or cause-and-effect diagram, it helps identify potential causes of a problem by categorizing them into groups such as people, processes, materials, and environment. - **Histogram:** A graphical representation of the distribution of numerical data. It helps in understanding the frequency and distribution of data points. **NABH (National Accreditation Board for Hospitals and Healthcare Providers)** **1. Overview:** - **Purpose:** NABH provides accreditation to hospitals and healthcare organizations to ensure quality, safety, and effectiveness in patient care. - **Objective:** To improve healthcare services by setting standards that healthcare organizations must adhere to for accreditation. **2. Key Standards and Areas:** - **Patient Care and Safety:** - **Patient Rights and Education:** Ensuring patient rights are respected, including informed consent, privacy, and access to medical information. - **Patient Safety:** Implementing protocols to prevent harm, such as infection control practices and error reporting systems. - **Infection Control:** - **Standards:** Guidelines for maintaining cleanliness, sterilization, and handling of infectious materials to prevent healthcare-associated infections. - **Quality Management:** - **Continuous Quality Improvement (CQI):** Establishing processes for monitoring, evaluating, and improving quality of care through regular audits and feedback mechanisms. - **Facility Management:** - **Infrastructure:** Requirements for maintaining a safe and hygienic environment, including proper facility management, waste disposal, and maintenance of equipment. - **Human Resources:** - **Staff Training:** Ensuring ongoing training and professional development for healthcare staff to maintain high standards of care. **3. Accreditation Process:** - **Application:** Healthcare organizations apply for NABH accreditation. - **Assessment:** An evaluation team assesses compliance with NABH standards through inspections and reviews. - **Certification:** If standards are met, accreditation is granted. Organizations must undergo periodic re-evaluation to maintain accreditation. **NABL (National Accreditation Board for Testing and Calibration Laboratories)** **1. Overview:** - **Purpose:** NABL provides accreditation to testing and calibration laboratories to ensure they meet international standards of quality and reliability. - **Objective:** To enhance the quality of laboratory services by setting benchmarks for performance and accuracy. **2. Key Standards and Areas:** - **General Requirements:** - **Quality Management Systems:** Laboratories must implement and maintain a robust quality management system to ensure accurate and reliable test results. - **Personnel Competence:** Ensuring that laboratory personnel are qualified, trained, and competent in their roles. - **Technical Requirements:** - **Test Methods and Validations:** Laboratories must use validated methods and ensure the accuracy and reliability of test results through regular calibrations and validations. - **Equipment Calibration:** Regular calibration and maintenance of equipment to ensure precision and accuracy in testing and measurements. - **Accreditation Scope:** - **Scope of Accreditation:** Laboratories must define and operate within their scope of accreditation, detailing the tests and calibrations they are certified to perform. - **Documentation and Records:** - **Record Keeping:** Maintaining comprehensive records of tests, calibrations, and quality control processes to demonstrate compliance with NABL standards. **3. Accreditation Process:** - **Application:** Laboratories apply for NABL accreditation and provide evidence of compliance with NABL standards. - **Assessment:** An evaluation team conducts an on-site assessment to verify adherence to standards and review laboratory practices. - **Certification:** Accreditation is granted based on successful assessment. Laboratories must undergo periodic reassessments to retain accreditation.