Production Cycle PDF
Document Details
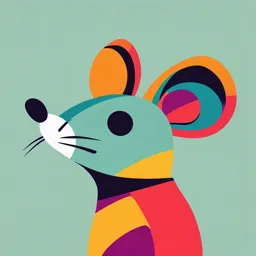
Uploaded by DazzlingLeopard384
UM Tagum College
Tags
Summary
This document outlines the production cycle. The production cycle describes all of the stages involved in turning raw materials into final products. These steps are crucial for manufacturing and operations management.
Full Transcript
PRODUCTION CYCLE Auditing in Specialized Industries PRODUCTION CYCLE: TYPICAL ACTIVITIES Planning Production of Determination Cost Goods and of Goods Sold Services Planning Sales Forecasts Production activities start with a sa...
PRODUCTION CYCLE Auditing in Specialized Industries PRODUCTION CYCLE: TYPICAL ACTIVITIES Planning Production of Determination Cost Goods and of Goods Sold Services Planning Sales Forecasts Production activities start with a sales forecast, a marketing projection of product sales, based on past performance and marketing initiatives. Based on this forecast and other pertinent factors, the production planner can determine both the type and the quantity of products that need to be produced to meet anticipated demand and can schedule the products in a production plan. Planning Production Planning The goal of production planning is to provide a schedule for manufacturing, called the production plan, so that quality products will be available at the appropriate time for the lowest cost. In addition, production planners must integrate corporate strategies such as long-range plans and just in-time (JIT) inventory management. Planning Production Planning Job of the Production Planner Creates a production plan Identify the total quantity of raw materials necessary for production based on the production plan and the bill of materials Planning Production Planning Job of the Production Planner Uses the raw material inventory status report to determine whether enough raw materials are in stock to complete production. Must also be aware of labor requirements. Production of Goods and Services Production Once the production plan has been finalized, it is generally shared with managers in the sales/marketing department, production department, and possibly human resources who may be required to “sign off” as evidence of their approval of the plan. Production of Goods and Services Inventory Control As the time for production nears, the production planner issues a production order to the appropriate production personnel including inventory control and production managers. Inventory control will receive a materials requisition or materials transfer ticket that authorizes inventory to release raw materials and supplies to production. Determination Cost of Goods Sold Cost Accounting When production is completed, production orders and the related records of materials and labor used are sent to the cost accounting department. Cost accounting generally records finished goods at standard costs. All materials, supplies, labor, and overhead that go into the product must be measured based on the bill of materials and accumulated into the production cost. Determination Cost of Goods Sold Cost Accounting The cost accounting department produces analyses of actual cost per unit, standard cost, and variances. Cost accounting also may determine the overhead allocation to production in general, to production orders, and to finished units. Control Considerations Production orders should contain a list of materials and their quantities, and they should be approved by a production planner/scheduler. Material should not be issued to the production floor without an authorized material requisition. Control Considerations Material requisitions should be compared in the cost accounting department with the list of materials on the production orders, and the production operator and the materials inventory storekeeper should sign the materials requisitions. All material requisitions should be accounted for. Material requisitioned is used in production, is unusable (scrap), or excess material returned to raw material inventory. Control Considerations Documentation for material returned to raw material inventory should accompany the returned items with a copy going to inventory control for use in adjusting the perpetual raw material inventory. Production supervisors should sign (or review if the time is kept electronically) labor time records on jobs, and the cost accounting department should reconcile these cost amounts with the labor report from the payroll department. Control Considerations The production supervisor and finished goods inventory custodian should review production reports of finished units and then forward them to cost accounting. Inventory should be periodically counted with the counts agreed to perpetual inventory records.