Process .docx
Document Details
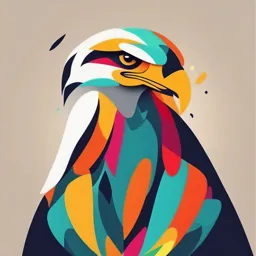
Uploaded by DevoutTanzanite4841
Full Transcript
Types of process measurement Point Measurement Detects the process variable at a predetermined point or value The input is a simple ON or OFF, 0 or 1, true or false Can be thought of as a digital system Continuous Measurement Detects the process variable within a range of all possible values at...
Types of process measurement Point Measurement Detects the process variable at a predetermined point or value The input is a simple ON or OFF, 0 or 1, true or false Can be thought of as a digital system Continuous Measurement Detects the process variable within a range of all possible values at all times Can be thought of as an analog system Direct or Invasive Measurement The measurement device will be in direct contact with the process May change process Source of contamination Indirect or Non-Invasive Measurement No contact, good for extreme processes Not as accurate as results are inferred or calculated Instrumentation Terminology Process – the system or “thing“ we want to measure and/or control. Manipulated Variable- The part of the process that is being adjusted by the final control element. Final Control Element: The last device the directly controls the manipulated variable. Usually, a control valve but could be a pump too. Primary Element: The sensor. The device that senses the process. Process Variable – the current measured condition of a process. E.g., the current temperature of your house as indicated by a thermometer. Set point – the desired setting of the process variable. Your thermostat is set for 20°C. Error – the difference between the setpoint and the process variable E.g., your furnace is set to keep your house at 20°C, but the process variable or current temperature is 17°C, so the error is 3°C. Range – It can be defined as the values of the lowest and highest readings it is designed to operate. A thermometer has a scale from −40°C to 100°C. So the range varies from −40°C to 100°C Zero – the lowest value that corresponds to the bottom or lowest limit of the process. Also called LRV (lower range value). Span – Is defined as the difference between the minimum to maximum range value. In the case of the thermometer, its scale goes from −40°C to 100°C. So its span is 140°C. Instrumentation Devices The purpose of instrumentation or process control is to, as the name implies, control a process through the act of measuring and changing that process. Devices are parts of the process control that perform this function. Sensors or elements Devices that measure the process. RTD’s, Paddle wheels, Orifice plates. Transmitters Devices that converts non-standard signals to standard instrumentation signals. Usually there is a sensor/element connected to a transmitter. Controllers Devices that controls the signal to an Actuator to cause the process to be maintained at a certain set-point. Transducers Devices that converts a standard instrumentation signals to a different standard instrumentation signal. 4-20mA to 3-15 psi. Actuators (Final Control Element) Devices that create changes in a process. Pumps, Control Valves. P&ID and ISA Symbols P&ID is the acronym for “Piping and Instrumentation Diagram. The (ISA) Instrumentation, systems and automation society is one of the leading trade and standards organization. The ISA S5.1, ISO 10628, and BS 5070 cover the standardization of P&ID symbols. The list is updated periodically. The P&ID is used by electricians (you), engineers, and operators to better understand the process and how the instrumentation is interconnected The list of diagrams is extensive and by no means is it feasible/reasonable to show you all of them. Those shown in this lecture are only the most common! Problem with high level probe Tank 315 ISA Symbols Individual Instruments To specify an individual instrument in the P&ID we use a circle that is also called a balloon. How they are drawn will help you locate the instrument. Tag numbers The design of the balloons help us understand where the device is located. But there is still more that needs to be added. We need to know what the process is, we need to know what the device is, and we need to know if the device has any additional functions like alarms. For this we add TAG numbers . We can have a lot of different instruments used in a process, so we have to be able to identify them. For this we use letters and numbers. The letters are called functional identifiers and the order they are in is very important. The first letter is always the process variable, for example a level process would be identified with a “L”. The second tells us what the device is, for example a “T” would be a transmitter. The next page shows a more complete list. You should note that you cannot substitute any of these letters. ISA S5.1 Identification Letters Note that the letter “Y” now represents a transducer!! Instrumentation signal lines So now we have taken the simple temperature process and replaced the pictures with balloons and with the addition of tags we also know what the devices are and any additional functions. But there is one bit of information left that we can get. How do they communicate. That is accomplished by creating different lines that run between the balloons. In order to connect the various devices in a control system together we need signal lines. The signals that are being transmitted could be pneumatic, hydraulic, electrical or some other medium. The lines we use must be designated as to the type of signal they are carrying. Solid bold line: Indicates the actual piping of the process. Solid thin line: Indicates a connection from the process to an instrument. Dashed line: Indicates a standard electrical signal. Usually 4-20 mA but could be voltage too. Solid w/ two diagonal marks: Indicates a standard pneumatic signal. 3-15 psi. These are the most common. But you can see that there are others too. ISA Symbols Valves P&ID P&ID legend Sample of industrial P&ID Resistive Temperature Detector (RTD) The most common RTDs used in industry are made from platinum. They are very stable and the most linear. Other materials such as Nickel, Balco and Copper can be used but have limitations due to nonlinearity and oxidation. The platinum RTD can come in either industrial grade or laboratory grade. Depending on the desired accuracy. Laboratory is about ±0.01 % at 0° C and industrial can be ±0.15 to ± 0.3%. Industrial RTD’s typically have a resistance of 100Ω at 0°C. There are 3 common designs of RTDs Thin film sensing element, wire wound element and coil element and can be a 2, 3 or 4 wire configuration. Resistive Temperature Detector (RTD) An RTD is a temperature device/sensor that will exhibit a positive change in resistance for a positive change in temperature. Therefore, an RTD also has a positive temperature coefficient. Positive coefficient = a rise in temp, an increase in resistance. This is an RTD. Negative coefficient = a rise in temp, a decrease in resistance. This is a Thermistor. Advantages & Limitations Advantages of Platinum RTDs: Stable for a long time. Accurate readings for a narrow temperature range. Disadvantages: Limited temperature ranges Initial higher cost Less rugged in certain processes, Vibration. The 2-wire RTD A simple 2-wire RTD is only used for short distances and where high accuracy isn’t necessary. Because you are adding the resistance in the leads to the resistance of the sensor. So a resistance reading of 123.4 would by found on the RTD chart to represent approx. 60 °C The 3-wire RTD The 3-wire RTD is the most common. Because you can subtract the lead resistance. An assumption is made that the resistance of the two leads across the resistance is the same. Comparing this to the two wire RTD from before we see that subtracting the lead resistance of 3.4Ω leaves use with 120 Ω. Looking at the chart we see its closer to 52°C so an 8 °C error using a 2-wire. Rt = R-RL Rt= 123.4 – 3.4 = 120 ohms. The 4-wire RTD The 4-wire RTD is used when very high accuracy is needed. With the 4-wire configuration, the instrument will pass a constant current (I) through the outer leads. The addition of the two additional leads makes it possible to eliminate errors due to change in lead wire resistance. This is because of a very high input impedance of the circuitry. Since there is no current flow there is no associated voltage drop in the lead wires from the RTD to the to the sensor input AB. This results in a measurement of the RTD only and the lead wires will have no effect on the reading. The voltage drop is measured across the inner leads AB. So from E = IR we learn the resistance of the element alone, with no effect from the lead wire resistance. Resistive Temperature Devices (Thermistors) Thermistors, derived from the term THERMaIly sensitive reslSTORS, are constructed from mixtures of metal oxides. They are available in 2 types, NTC (negative temperature coefficient) and PTC (positive temperature coefficient). The NTC thermistor is more commonly used. This means an increase in temp results in a decrease in resistance. A thermistor exhibits a large change in resistance to a small change in temperature and are usually very small. Communicating process information A standard instrumentation signal is used to represent a standard unit of measurement. For example, we can use a standard signal to represent temperature °C or level (feet). Standard Instrumentation Signals For a temperature transmitter to send a signal to another device (temperature controller), an agreed upon standard method of communications must be used. Common standard instrumentation signals: Voltage – 1 to 5V. Most common voltage. Instruments that receive a 4-20mA signal through a 250Ω resistor will produce 1- 5V. Drives can use 0-10 vdc. Other ranges, 1-10 Vdc Current – 4 -20 mA. Most common signal to eliminate line loss and to provide power to the transmitter. Pressure – 3 to 15 psi Rarely used. Leaks and condensation issues . Standard Signals Connections 4-20 mA. The most popular signal used in industry. Simple to connect, configure. Better for long distances. Not as susceptible to noise caused by electrical interference compared to voltage loops. Can only transmit one signal per loop. Wrong sized wire used and improper shielding methods (ground loop). Standard Signals 1-5 volts. Improper size or length of wire can cause a voltage drop causing a measurement error. Improper shielding to prevent EMI. Best for short distances. The controller below requires a 1-5 v signal. The transmitter sends a 4-20 mA signal. The controller measures the voltage drop across the 250 Ω resister as the current flows through it. We noticed standard signals lower range values (LRV) do not start at 0. Most standard signals have an elevated zero that is 1/4 times the value of the span. There are three reasons for this. The elevated zero can provide enough power to operate the devices such as transmitters which require about 3 mA to work The elevated zero can also indicate when we have a broken loop instead of a zero signal (0 mA instead of 4 mA etc.) Mechanical devices respond better with a signal that starts above zero. Looking at a transmitter. If the input has a range of (0°C LRV - 100°C URV) then the output must be 4ma LRV and 20mA URV. Zero °C relates to 4 mA ( both LRV’s) and 100 °C represents 20 mA ( both URV’s). The both input and output signals will be directly proportional to each other. The range of the (4 –20mA) will be proportional to the range of the process (0°C - 100°C) and must be calibrated to meet this. A transmitter must be calibrated to provide a linear signal converting a non- standard signal to a standard signal. Process Signal Calculations No doubt you are aware that math is an important part of the skilled electricians' tools. Basic electrical equations such as Ohms law E=I x R and Power P=E x I. Instrumentation has basic equations too: Pv−LRV %= Pspan x100 and PV= % 100 x Pspan + LRV From these basic formulas we can derive many other useful equations Process signal conversion There must be a specific order of operation when we solve equations. 5 + 7 x 4 - 2 = 46 or 19 or 31 The rules for the order of operations are: Solve brackets first. If equations contains more then 1 set, start from inner most. Solve exponents next Perform all multiplication and division from left to right Perform all addition and subtraction from left to right You can remember the order as BEDMAS Process signal conversion Using BEDMAS lets solve this equation. 5 + 7 x 4 -2 = There are no brackets or exponents. There is no division move to multiplication 5 + 7 x 4 -2 5+28 - 2 Last step is add and then subtract from left to right. 5+28 - 2 33-2 = 31 Process signal conversion Try another one with brackets (BEDMAS ) 80-5 x (4÷2+5) 80-5x(2+5) 80-5x7 80-35 45 Process signal conversion Next with exponent and with brackets (BEDMAS ) (3x10+ 52) +4 (3x10 +25)+ 4 (30+25) + 4 55+4 = 59 Process signal conversion Remember, an equation is simply a statement that is equal on both sides. What we do on one side, we must do the same to the other side. 6P+6= 24 6P+6-6=24-6 6P=18 6𝑃 18 = 6 6 P=18 6 P=3 Process signal conversion When we had to find the percentage of a single variable, we divided by the span to change to a decimal format and then multiplied by 100. To convert back we divide by 100. You got 20 out of 30 on a test. What is the percent? 20 = 0.667 x 100 = 66.67% 30 Going from the other direction: You got 66.67% on a test with 30 questions. How many did you get right? 66.67 100 x 30 = 20 But this was always assuming we started from zero. What if we don’t? Calculating Process and Signal Values First, we determine the % the process variable is at using the formula. 𝑃𝑟𝑜𝑐𝑒𝑠𝑠 𝑉𝑎𝑟𝑖𝑎𝑏𝑙𝑒 −𝐿𝑅𝑉 % = 𝑃𝑠𝑝𝑎𝑛 x 100 A compressor has a range of 120 psi to 300 psi. Span is 180 psi. A output is 4– 20mA and is calibrated so that 4mA (LRV) will represent 120 psi and 20mA (URV) will represent 300 psi. The pressure signal from the PE to the transmitter is 173 psi (PV). Find the mA output signal from the transmitter. Calculating Process and Signal Values Range of 120 psi to 300 psi. Span is 180 psi, LRV is 120 psi. Process variable (PV) is 173 psi. The proportional signal will be: %=𝑷𝑽 −𝑳𝑅𝑽 𝑷𝑠𝑝𝒂𝑛 x100 %= 173 −120=.2944 x (100) = 29.44 % 180 Now we know that 173 psi represents 29.44% of the range. Next, we can convert that to a signal. This is because the signal range is proportional to the temperature range. Can you recognize that this is the job of a transmitter? Converting a nonstandard signal (psi) to a standard signal. In this case a 4-20 mA signal. Calculating Process and Signal Values Second, we take the percentage and use it to calculate the correct standard signal % amount. Using Pv() = 4-20 mA signal mA= % 100 x Span + LRV 100 x 16mA+4mA mA = 29.44 100 x 16mA + 4mA= 8.71mA 3-15 psi signal psi = % 100 x 12psi+3psi psi = 29.44 100 x 12psi+3psi= 6.53psi Since standard instrumentation signals are proportional to each other they can be converted from one standard to another. Devices designed to do this are called transducers. Calculating Process and Signal Values Something Extra There is another way to calculate this. I think it is simpler Our Step #1 formula is converting the nonstandard signal input (°C) into a percent. Then step #2 we take the percent and calculate the output into the standard signal (mA). Why not combine the 2 formulas? %=𝑃𝑉 −𝐿𝑅𝑉 𝑃𝑠𝑝𝑎𝑛 x100 and Pv() % = 100 x Span + LRV Output= {𝑰𝑛𝑝𝑢𝑡 −𝑳𝑅𝑽𝒊𝑛𝑝𝑢𝑡 𝑠𝑝𝒂𝑛𝒊𝑛𝑝𝑢𝑡 }𝑆𝑝𝒂𝑛 𝑜𝑢𝑡𝑝𝑢𝑡 + 𝑳𝑅𝑽𝑜𝑢𝑡𝑝𝑢𝑡 Calculating Process and Signal Values What should the psi output signal be if the input range is 4-20mA and the PV is 13.6 mA. Transducer correct!!!! Output= {𝐼𝑛𝑝𝑢𝑡 −𝐿𝑅𝑉𝑖𝑛𝑝𝑢𝑡 𝑠𝑝𝑎𝑛𝑖𝑛𝑝𝑢𝑡 }𝑆𝑝𝑎𝑛 𝑜𝑢𝑡𝑝𝑢𝑡 + 𝐿𝑅𝑉𝑜𝑢𝑡𝑝𝑢𝑡 13.6𝑚𝐴−4𝑚𝐴 { 16𝑚𝐴 } 12psi +3 psi= 10.2 psi Review Thermocouple Concepts Introduction to HART Communication Thermocouples We know that when we measure a voltage, we are measuring a potential difference between two points. We need 2 dissimilar metals for a thermocouple! You cannot measure the Seebeck voltage on a single wire directly. If we use another conductor of the same metal to create the circuit, the second conductor will produce an identical Seebeck voltage to the first conductor. The voltages will cancel each other out so our voltage is 0 millivolts at the cold end. Thermocouples Manufacturers use different metals to construct thermocouples. The Seebeck coefficient of any given thermocouple material is the amount of voltage generated between the hot end and the cold end of each wire. The magnitude of the coefficient is based on the thermal electric properties of the wire. Conductors A&B are not made of the same metal. The metals have different Seebeck coefficients so there is a voltage difference at the cold end. Thermocouples If electrons move from the hot end to the cold end the Seebeck coefficient is negative. If the electrons move from cold to the hot end the Seebeck coefficient is positive. When the thermocouple hot junction is exposed to a process it will measure the process temperature. The wires are connected between the hot junction (measurement junction) and a measuring instrument. However, it is not at the hot junction where the differential voltage is developed. There must be a temperature gradient along the lead wires. This is where we will develop our Seebeck voltages. Thermocouples There are three thermal zones for our thermocouple. There is the uniformly hot zone, the thermal gradient zone and the uniformly cool zone. The Seebeck voltages are developed in the thermal gradient zone. The wires in the two uniform temperature zones cannot generate a voltage because they are at the same potential. Thermocouples But what will happen if the thermal gradient zone fluctuates? To obtain an accurate and stable temperature in the hot junction (measurement zone) we create a second junction called the cold junction (reference junction). We keep this junction at a known temperature 0° C. We have created a fixed/constant reference point! Cold Junction Compensation VJ1 =300 °C 16.327mV (Vtrue ) VJ2 =14.79mV(Vmeas) Temp VJ2 = 30°C = 1.537mV Notice the thermistor measuring the temperature at the desired junction J2. Notice the polarities!! The voltage created at this junction will be based on the ambient temperature and will be opposite in polarity to the thermocouples. The thermistor will add the correct amount of voltage to cancel this ambient temperature out and allow the meter to see the correct voltage 16.327-1.537+1.537. The VERY simplified formula is Vtrue=Vmeas+Vref. 16.327=14.79+1.537. This is what all temperature devices do. They Compensate for the temperature at its connection point. Cold Junction Compensation VJ1 =16.327mV (Vtrue ) VJ2 =14.79mV(Vmeas) Temp VJ2 = 30°C = 1.537mV What happens if we used copper cable instead of T/C cable? The reference junction J2 is no longer at the indicator but at the head of the T/C. This caused the reference junction J2 to completely shift position. When we use our meter to measure the mV at the junction VJ2 we read 14.79 mV. Because the reference or “cold junction” is not at 0°C but at the ambient temperature of 30°C which develops a voltage of 1.537 mV at an opposite polarity so 16.327-1.537=14.79 mV. If we didn’t account for the elevated Vref we mistakenly calculate the temperature to be approx. 272°C from the chart. J type chart Thermocouple plug and terminal block Types of Thermocouples and polarity Different combinations of natural and manmade alloys metals have been tried and tested and from that we have different types of thermocouples designated by letters. The different types of thermocouples have two conductors that are identified by colour. For example, “K” types is yellow and red while “J” type is white and red. You will notice that the colour red is in both and “for the most part” this is the same for all the common types of thermocouples in North America. The colour red will always be the negative. Thermocouple chart Hart Protocol The majority of the smart field devices installed today are Hart enabled. Simply put Hart (Highway Addressable Remote Transducer) is a global standard for sending and receiving digital information across analog wires between smart device and control or monitoring devices. The Hart protocol is a bidirectional communication protocol that provides data between intelligent field instruments and DCS/PLC or handheld communicators. The Hart makes use of Bells 202 Frequency Shift Keying (FSK) standard to superimpose digital information on the conventional 4-20 mA analog signal. Hart came about in the 1980’s and is based on the same technology as “Call display” on your phone. Hart simultaneously uses analog and digital communication. Communication HART Examples of the additional device information that is communicated using digital signal FSK (Frequency shift keying) which is superimposed on the analog signal are: Process Variable % Upper Range Value URV Lower Range Value LRV Units of measurement Device temperature Why do we care about HART? Intense competition in industries demands maximum output at minimum cost. That productivity push extends into the maintenance department. At the same time, regulations and quality standards are demanding more rigorous calibration plus extensive documentation. Yet maintenance expenses are being slashed to the minimum. Most plants have responded by replacing analog instrumentation with smart instruments. Smart describes any microprocessor-based field device. The microprocessor offers extra functionality, such as multiple sensor types, multiple measurement variables (e.g. flow rate and level), digital and temperature compensation. generally offer better accuracy, long-term stability, and reliability than conventional analog instruments. Most of these use the HART protocol. Functions of HART communicator: Provide identification details of the instrument being evaluated. The identification includes the type of instrument, sensor type, model #, etc. Can read or change name/tagging for each HART instrument. Can perform/identify diagnostic abnormalities of each HART instrument. Can adjust URV (Upper Range Value), LRV (Lower Range Value). The LRV and URV are the process variables that you choose to attach to the corresponding standard signal. The tank on each lab station is 0-30 inches. We do not want the tank to empty so we make our is our 4 mA. The highest we want is 24 inches. Twenty-four is our URV and our 20 mA. Functions of HART communicator Can monitor Variable Process values and signal values mA. Can be used to give the Auto-Manual Calibration command for the control valve. Can be used to determine Equal Percentage, Linear, and Quick Opening from the Control Valve. Can do signal injection for simulation. Device Calibration Smart fisher Valve/Positioner Hart Communication Communication When a transmitter is tested on the workshop bench, the transmitter will power up and do its functions while connected directly to a DC power supply with zero load in the loop (no resistor), except there will be no HART communications. HART comm will not function without at least 230 ohms in the loop. The reason for this has to do with an impedance across which the FSK HART signal can develop and be detected, because the DC power supply acts as a low pass filter. It basically filters out any ripple, your 1200-2200 Frequency. A workbench will require a 24 Vdc for something like calibration, but HART definitely requires a minimum loop resistance to communicate. Calibration is still required. Some have come to believe that the accuracy and stability of HART instruments, plus the presence of instrument diagnostics, have eliminated the need for calibration. False, regular performance verifications with a suitable reference standard, are necessary because regulations governing occupational safety, environmental protection, and consumer safety often require evidence of traceable calibration for process instrumentation. Quality programs, such as ISO 9000, dictate periodic calibration to recognized standards for all instruments that impact product quality. Calibration is still required The performance of instruments will changeover time with exposure of the transmitter and the primary sensing element to temperature, humidity, environmental pollutants and vibration. Regular performance checks can uncover problems not directly caused by the equipment such as plugged impulse lines, or pressure lines that have become filled with condensate. Or the wrong thermocouple type installed. Introduction to Level Measurement Level is simply the height that some material fills a container. Level measurement is an integral part of process control systems for inventory control, quality and safety. Level measurement is divided into two familiar types of detections. Point and Continuous level measurement. Level measurement can involve detecting the level of solids as well as liquid‘s. Level detection of solids can be more difficult than with liquids because solids will not take the shape of the vessel and can bridge the detection points (Primary Elements). In defining level measurement, we can say that : Level measurement is the act of detecting the interface or boundary between two media. Introduction to Level Measurement Another application of level measurement is the detection of liquid-to-liquid interfaces such as oil on top of water in a separator. The overall level remains constant but the location of the interface between the two liquids changes. Introduction to Level Measurement Accurate level measurement is a requirement of proper process control so that we can avoid: Waste from too little or too much material in a batching process. Spill hazards from over filling vessels with dangerous or flammable materials. Explosion hazards from overfilling and thus over pressurizing a vessel. Accurate inventory control. Quality control such as in food and drug manufacturing (iodine in salt) Point Measurement: Detects the interface at a predetermined point or level. The output from this is a simple ON or OFF, 0 or 1. Continuous Measurement Detects the interface within a range of all possible levels at all times. The output from this is an analog value, which is proportional to the detected level and is typically a 4-20mA current. This current signal can then be converted to represent various units such as height, percentage, volume and weight (mass). it is important to consider the sensor placement, as this will contribute to accuracy issues. How do we measure level When we measure level, it is accomplished using either Direct, Indirect, invasive or non-invasive methods. Direct (Invasive Measurement) Requires that the measuring device be in contact with the material to be measured. An example would be a float. Indirect (Non-invasive Measurement) Devices do not contact the material to be measured. Reasons include avoiding situations of contamination, hazardous material or ensuring accurate readings. Example: ultrasonic. Indirect The level is determined from a relationship of the pressure to the density and the specific gravity of the liquid. We use a variable other than level to measure and calculate the level. For example, the level can be calculated by the pressure at the bottom of the vessel. Texas City BP Refinery Accident Level Measurement Methods Visual Methods Rod gauge: A dipstick that is inserted into the material being measured that has some form of graduation marks to indicate level. Can be used as a reference to calibrate other devices. Direct / invasive and point measurement. Sight glass or tube: A transparent tube connect to the side of a vessel that has graduations marks to indicate level. Can be obscured by viscous and foamy substances. Considered noninvasive as it is part of the vessel and not defined as a primary element. Direct / noninvasive, continuous measurement Sight Glass This one is clean. Not been my experience. Float and Displacement Methods Buoyancy Method Float level indicator The float style is a round element the rides on the surface of a liquid. Examples: Magnetic reed switch Pointer on a graduated scale Mercury switch Variable resistor The larger the float, the lower the density of material to be measured Direct / invasive and point or continuous measurement Float and Displacement Methods Float system using reed switches How many floats do you see? What could each one represent? Displacement Method A displacement sensor is different from a float because it is weighted to remain partially or completely submerged. Based on Archimedes’ principle: A body immersed in a fluid will be buoyed up by a force equal to the weight of the fluid displaced. As the liquid level rises, due to Archimedes Principle a displacement sensor will lose apparent weight. More reliable than floats in turbulent, surging, frothy or foamy applications. Commonly use to measure levels in liquid-to- liquid interfaces such as condensation in fuel tanks Direct / invasive and continuous measurement Buoyancy Our mathematical equation for this principal is calculating the mass of the substance we are displacing. B = ρV B = buoyancy force (lbs) or the Mass of fluid. ρ = the weight density of the fluid (lbs/𝑓𝑡3 V = volume of the displaced fluid (ft3) Buoyancy Determine the buoyancy force on an object that displaces 5 ft3 of water at 20º C. Water density @ 20º C is 62.4 lb/ft3. Answer: B = ρ V B = 62.4 lb/ft3 X 5 ft3 B = 311.5 lbs Buoyancy Determine the volume of displaced water at 20º Celsius that an object displaces if it produces a buoyancy force of 936 lbs. Water density @ 20º Celsius is 62.4 lb/ft3. B=936 lbs, ρ = 62.4 lb/ft3 , V=? B = ρ V B V = ρ V = 936 lbs 62.4 lbs/ft3 = 15 ft3 Hydrostatic Pressure to find Level A column of liquid will exhibit pressure in direct relation to its height and density. (P=H x D) Hydrostatic head pressure is measured from the bottom of the tank, the level can now be determined by any changes in hydrostatic pressure. Hydrostatic Head Level Detector. A pressure transmitter calibrated to minimum and maximum range. LRV and URV Vessel must be open to the atmospheric pressure. Indirect / invasive, continuous measurement Hydrostatic Pressure Pressure (lb/ft2) = Height(ft) x Density(lb/ft3) Height = Pressure / Density Notice the units of pressure above? They are lbs/ft2 But we generally use lbs/in2 (psi) as the standard pressure units, so we must convert. Note 1psi = 144 lbs/ft2. How many inches are in 1 foot? 12”. Squaring gives you 12”x12”=144 inches 2 . So, 1 square foot has 144 square inches. If each little 1-inch square has 1 pound on it there must be 144 lbs on that square foot! Hydrostatic Pressure to find Level The head pressure in PSI for a column of water is 8.66lbs/in2, its density is 62.4lbs/ft3. What is the level in feet? Pressure=Height x Density Convert lbs/in2 to lbs/ft2 8.66 lbs/in2 x144= 1248 lb/ft2 𝑃𝑟𝑒𝑠𝑠𝑢𝑟𝑒=Height 𝐷𝑒𝑛𝑠𝑖𝑡𝑦 1248 lb/ft2 62.4 lbs /ft3 = 20 Ft Hydrostatic Pressure to find Level One of the simplest ways to measure liquid level is by using a pressure gauge. This is based on the principle that the hydraulic head or static pressure exerted by any liquid of a given density (or specific gravity) is directly proportional to the height above the point of measurement without any concern for the volume. When we look at water, we know that 27.72” of water is 1 psig. Another way to look at it 12 is 1 ft of water is 0.433 psig , so for every foot 27.72 of water there is 0.433 psig of pressure. But this is only considering water and we know there are many other fluids. We need to consider another factor and that is a fluids specific gravity. What’s Specific Gravity (SG)? It is a unitless number that is a ratio found from comparing an equal volume of weight (density) of a liquid to the same volume/weight of water. Water is 62.4 lbs/ft3. Water is always used as the standard. Gasoline has a density of 41.20 lb/ft3 so to find its SG 41.2 𝑙𝑏/𝑓𝑡3 we divide that by the density of water. 62.4 𝑙𝑏/𝑓𝑡3 =0.66 The SG of Gas is 0.66 and since water is the standard its SG is 1. Since gas is a smaller number (almost half) it means it is lighter than the water so will float on top. All liquids are compared to water. SG = X fluid density water density (62.4 𝒍𝒃 ) Hydrostatic Pressure to find Level You have seen the formula P= H x D, but we can use another formula too. P = K x h x sg Where K is the conversion factor 0.433, h is the height of the liquid (FT), sg is the specific gravity of the liquid. Hydrostatic Pressure to find Level What is the head pressure in PSI for a column of liquid 20 ft high and its density is 59.4 lbs/ft3? (P = K x h x sg) Remember to convert density to SG!!!!! 1) Pressure = 0.433 x 20 ft x 59.4 lbs/ft3 62.4 lbs/ft3 = 8.33 lbs/in2 Hydrostatic Pressure to find Level You can use either formula! What is the level in column displaying 10.33 psi on a gauge at its base and its density is 60lbs/ft3? (pressure=height x density) 𝒑𝑟𝑒𝑠𝑠𝑢𝑟𝑒 Height = 𝑑𝑒𝒏𝑠𝒊𝑡𝑦 1) convert lbs/in2 to lbs/ft2 = 10.33 psi x 144 = 1487.52 lbs/ft2 1487.52 lbs/ft2 60 lbs/ft3 = 24.79 ft Height = 𝒑𝑟𝑒𝑠𝑠𝑢𝑟𝑒 1) H = (𝑲 x 𝑠𝑔) OR 10.33 𝑝𝑠𝑖 (0.433 𝑥 60 = 24.79ft ) 62.4 Hydrostatic Pressure to find Level What is the level in a silo that is showing 55 psi on a gauge at it’s base? We know it’s SG is 0.92. P=K x H x sg Height = 𝒑𝑟𝑒𝑠𝑠𝑢𝑟𝑒 (𝑲 x 𝑠𝑔) 1) H = 55 𝑝𝑠𝑖 (0.433 𝑥 0.92) = 138.07ft Hydrostatic Pressure to find Level How high would the column of water be for 55 psi? Our formula is Pressure=Height x Density Convert 55 psi to psf, 55 x144=7920 lb/ft2 Density is 62.4 lb/ft3. Manipulate the formula Height= 7920 lb/ft2 62.4lb/ft3 = 126.9ft OR P=K x H x sg (what is sg for water? 1 ) Height = 𝒑𝑟𝑒𝑠𝑠𝑢𝑟𝑒 (𝑲 x 𝑠𝑔) 1) H = 55 𝑝𝑠𝑖 (0.433 𝑥 1) = 127ft Why would we care about hydrostatic pressure? Weight Method As we discussed before, we can use weight to calculate the level for solids and liquids. This is considered an indirect method . Mechanical Springs Springs are located under each leg of a vessel, or the vessel is suspended by them, and the springs are connected to an indicator device. Bathroom scales are and example. Weight Method Instead of Mechanical Springs we can use Load Cells Single point Load cell A load cell is a type of transducer, specifically a force transducer. They convert a force such as tension, compression, pressure, or torque into an electrical signal that can be measured and standardized. As the force applied to the load cell increases, the electrical signal changes proportionally. Load Cells Weight Method The load cells are located either at the base of the tank, under each leg, or above the tank with the tank suspended from them. They are very accurate. Load Cells Weight Method Tare weight is the empty vessel weight. Measured weight is the total weight of the vessel and its contents. Can be used for liquid or solid materials Indirect, non-invasive, continuous measurement Formulas Content Wt(lb) = Measured Wt (lb) – Tare Wt (lb) Volume (cubic feet) = Content Weight (lbs) Density (lbs/ft3) Level (feet) = Volume (cubic feet) Surface Area (square feet) Area=ur2 Question 1 A cylindrical tank has an area of 10 ft2 and a height of 8 ft. It has a tare weight of 1500 lbs. Wheat flour has a density of 37 lbs/ft3. What is the height (level) of wheat flour in the tank if the tank weighs a total of 3500lbs? What would the current signal be from the transmitter? Question 1 What is the approximate height of the Wheat flour in the tank? Area = 10 ft2 Content Wt (lb) = Measured Wt (lb) – Tare Wt (lb) Content weight = 3500lb – 1500 lb= 2000 lb Question 1 Volume (cubic feet) = Content Weight (lbs) Density (lbs/ft3) V = 2000 lb 37 lbs/ft3 V = 54.05 ft3 Question 1 Level (feet) = Volume (cubic feet) Surface Area (square feet) L = 54.05 ft3 10 ft L = 5.405 ft O/P signal = ( 5.405𝑓𝑡 −0 𝑓𝑡 8𝑓𝑡 )16 mA + 4mA = 14.81 mA Question 2 If we used Mercury instead of wheat, with a density of 848 lb/ft3, what would its height be? Question 2 What is the approximate height of the mercury in the tank? V = 2000lbs/848 lb/ft3 V = 2.36 ft3 L = 2.36 ft3/10 ft2 L = 0.23 ft yes that is about ¼ of a foot (3”)! Rotational Suppression Method Paddle Wheel Detector Typically used granular or powered materials Paddle rotates until materials restricts rotation Direct, invasive, point measurement Nuclear Level Measurement This type of level measurement is based on the weakening of gamma radiation as it penetrates materials. The radioactive isotope is installed in a container, also referred to as shielding, which emits the radiation only in one direction. The source container and the transmitter used to detect the radiation are mounted on opposite sides of a vessel or pipe. The higher the level of the process in the vessel the lower the intensity of the radiation received. For example, at 50% of the full range level, only half of the detector receives the radiation. Why and where would we use nuclear measurement? 14 Nuclear Level Measurement Electronic Sensors Ultrasonic Sensors Ultrasonic sound waves are transmitted, and the time required for the return echo is measured. The length of time determines the distance from the transceiver. No moving parts promote long life. Like sonar used for underwater depth detection but sound wave are above the human hearing range. Indirect, non-invasive, continuous measurement Electronic Sensors Radar Sensors Similar in principle to ultrasonic, but uses high frequency radio waves instead of sound Ideal for applications with poor conditions such as foamy materials Indirect, non-invasive, continuous measurement Electronic Sensors Conductive Probes Rods are suspended in an electrically conductive material and a circuit path will form between the rods Several rods can be used for multiple point levels Direct, invasive, point measurement. Electronic Sensors Capacitive Probes A rod is suspended in non-conductive material to be measured and the capacitance between the rod and the vessel wall is measured. As the material level rises, a decrease in capacitance will be measured. Indirect, invasive, continuous measurement. Differential Pressure Method Differential Pressure Level Detector Same as a hydrostatic pressure system but used with a sealed and pressurized tank. Differential pressure transmitter has two pressure ports: wet leg (high pressure, bottom of vessel) and a dry leg (low pressure, top of tank) Differential Pressure Method 21 DP Transmitter with Manifold D 22 Calibrating DB (in service) 23 Druck Pressure Calibrator 24 Differential Pressure Method Differential Pressure Method Differential Pressure Level Detector Measures the difference in pressure between the top of a pressurized tank, and the head pressure in the bottom of the tank. Placement of the transmitter is critical to the calibration of the transmitter. Indirect, invasive, continuous measurement Differential Pressure Formulas Differential Pressure = ΔP ΔP= High Pressure - Low Pressure Pressure = 0.433 x H x SG Differential Pressure Method Question: A pressurized tank 30‘ tall containing water has a wet leg pressure of 20psi and a dry leg pressure of 8psi. The weight density of the Hi-Quality water is 60.4 lb/ft3, what would the water level be in feet? Solution: Differential Pressure Method ΔP = Hl – LO = 20-8 = 12 psi SG= 𝑥 𝑑𝑒𝑛𝑠𝑖𝑡𝑦 62.4 60.4 = 62.4 ΔP =k*h*sg 12 H= 0.433 𝑥 0.968 =28.63ft Differential Pressure Method Same question BUT we have the level but not the dry leg pressure. A pressurized tank 30‘ tall containing water shows a wet leg pressure of 20psi with a level of 28.63 feet. If the weight density of the water is 60.4 lbs/ft3, what would the dry leg pressure be?? Solution: 60.4 Differential Pressure Method sg = = 1 62.4 ΔP =k*h*sg ΔP = 0.433 x 28.63ft x 0.968 = 12 psi ΔP = Hl – LO LO = 20psi – 12psi = 8psi Bubbler System The Bubbler System is one of the oldest types of level measurement. It is used for liquid and fine powders. It uses a dip tube with the open end located near the bottom of a vessel. Supply air pressure is adjusted to provide airflow into the tube and to a pressure transmitter. The supply is adjusted so that it will deliver a pressure that is slightly higher than the highest hydrostatic pressure that will be measured. Bubbler System Changes in level provide changes in head pressure, thus a change in backpressure in the bubbler supply. As the level increases the backpressure will increase, letting less airflow out the bottom of the tube. That means more pressure is applied to the D/P transmitter. regulator. Constant Differential Pressure Relay Bubbler system Indirect, invasive, continuous measurement Advantages: Not affected by foaming, conductivity, solids. Reliable because only part in contact with process is a tube. Self clean, Can be used for many different types of processes, such as slurries, corrosive, acidic or radioactive. Cost effective and relatively easy to configure Disadvantages: Essential to maintain a constant supply pressure. Hole in dip tube. Turbulent process will affect reading