Printing Systems 1 PDF 2024-2025
Document Details
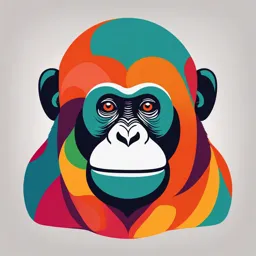
Uploaded by BrightestFarce
Helwan University
2025
Mahmoud Farouk Elfeky
Tags
Summary
This document provides an overview of printing technologies, including both conventional and non-impact methods. It details printing processes and systems, with diagrams and explanations of various printing techniques. The document also covers pre-press and post-press operations.
Full Transcript
Faculty of Applied Arts Media Design and Graphics Printing Systems 1 Prof. Dr. Mahmoud Farouk Elfeky Prof. of Security Prints Designing and Production Printing, Publishing and Packaging Dept. Faculty of Applied Arts – Helwan University 2024-2025 ...
Faculty of Applied Arts Media Design and Graphics Printing Systems 1 Prof. Dr. Mahmoud Farouk Elfeky Prof. of Security Prints Designing and Production Printing, Publishing and Packaging Dept. Faculty of Applied Arts – Helwan University 2024-2025 Printing Technology Current printing technologies are based on a wealth of inventions. The discoveries made in the engineering sciences, information technology, physics, and chemistry have left their mark on the development of printing technologies. In recent years it is computer and information technology that have had the most lasting impact on the printing industry and printing technologies, and this trend is continuing. An overview of printing technologies is given in figure 1 Printing Technologies Conventional Printing Non-Impact Printing (with master) (masterless) Screen Letterpress (incl. Electro- Lithography Gravure photography Ionography Magnetography Ink Jet Thermography Photography Printing flexographic printing) Waterless Drop on Offset Offset Continuous Demand Sublimation Transfer Ink Powder Liquid Magnetic Liquid Hot-melt Color donor Color (liquid) toner toner toner ink ink (ribbon/foil) sensitive coating Production flow Sheet or Web (substrate) Originals Prepress Press Postpress Printed product A distinction is made between technologies requiring a master, conventional procedures, and so- called non-impact printing (NIP) technologies which do not require a printing plate. Printing technologies requiring a printing plate are technologies like lithography (offset), gravure, letterpress, and screen printing. The most common NIP technologies are electrophotography and ink jet. As can be seen in figure 1, all printing technologies have the task of transferring information to a substrate (i. e., paper in sheet or web form). The execution of this task requires the prepress phase for procedure specific preparation of the printing process as well as the finishing phase for fabrication of the end product. Printing Technologies with a Printing Master Printing technologies with a master are also referred to as conventional printing technologies. The printing plate is the information carrying medium. This information is generated on the printing substrate by the partial surface transfer of ink. All information is denoted by image elements (transferred ink) and non-image elements (no ink). To enable continuous color tone values to be reproduced in print, such as from photographic originals, the original has to be broken up into extremely small dots (screen dots) that vary in size or are at various distances from each other. This process is called screening. The main function of screening is to generate halftone values, which are intended to simulate the continuous tonal gradation, ending with the conversion of gray images into binary images. Such screening is necessary because most printing technologies operate on a binary system and can therefore only perform one of two actions, namely to transfer ink (in an evenly distributed layer) or not to transfer ink. Printing Technologies without a Master (NIP Technologies) An overview of the various printing technologies, sub-divided into conventional printing technologies (with master) and non-impact printing technologies (masterless). Printing technologies, which do not require a stable, physical, fixed image carrier and can, in principle, generate a different printed page print per print. This type of process is referred to as non-impact printing (NIP technology). The term non-impact is based on early digitally controlled printing systems where computing centers would often print out data using dot matrix printers. If printing systems based on non-impact technologies are to be used, a full description of the printed product is required in digital form. Which operations must be carried out in prepress in order to prepare the entire printed page with text, graphics, and illustrations (pictures) in digital form for single or multicolor printing. Printing Process: Printing is described as the process of transferring ink onto paper (or another substrate) via a printing plate. In the course of the centuries many different printing technologies have been developed and these can be divided into four main technologies according to the type of image carrier used. Database Printed product Consumer, Customer Information Sources Plate, Printed Originals etc. pages Customer, Printing Agency, Prepress Postpress Distributor Process Publisher Data Data Data Data Film, Plate, etc. Paper, Ink, etc. Material, etc. Production flow Storage Consumables Supplier Definition of the Most Important Terms Relating to Printing Technology: Printing is a reproduction process in which printing ink is applied to a printing substrate in order to transmit information (images, graphics, text) in a repeatable form using an image carrying medium (e.g., a printing plate). The printing plate or image carrier (master) is the tool (material) by which ink is transferred to the printing substrate or an intermediate carrier for the reproduction of text, graphics and/or images. One printing plate usually generates many prints. The ink is the colored substance that is applied to the printing substrate during printing. The printing substrate is the material receiving the print. The printing press is the equipment with which the printing process is performed. Printing Systems: Letterpress (Relief) Printing. Here, the printing elements (letters, lines, dots, etc.) are raised. When the printing plate is inked, the ink adheres to the raised (printing) parts and is then transferred under pressure onto the printing substrate. The main examples of this printing technology are letterpress which, until a few decades ago, was the dominant printing technology and flexography which, by the middle of this century, had started to be used more and more in packaging printing. With traditional letterpress printing a hard metal printing plate (lead) is used and in flexography a flexible, soft rubber or plastic plate is employed. Gravure Printing. Here, the printing elements are recessed. The gravure cylinder surface is covered with low viscosity ink (“flooded”) and then passed under a doctor blade which removes all the excessive ink, leaving ink only in the recesses. The printing material is pressed onto the cylinder surface and takes up the ink from the recesses. The main examples of gravure printing are rotogravure printing and, in the area of arts and crafts, copperplate engraving and die-stamping (also security printing). Lithography. Here, printing and non-printing elements are at the same planographic level but are usually made from different materials (e.g., aluminum and polymer coating) with different chemical and physical surface properties. During printing, the non-printing elements are usually made ink-repellent first (by wetting) and the plate is then inked so that the ink is taken up only by the printing areas. The main example of lithography is offset printing, which is today the dominant printing technology. Offset printing is an indirect\ printing technology, that is, the ink is first transferred to an intermediate carrier (rubber blanket) and from there onto the substrate. Screen Printing. Here, the printing plate consists of a fine mesh (e.g., nylon). The non-printing elements of the mesh are blocked by a coating (stencil). As with gravure printing, the screen plate is covered with ink and a squeegee (blade) is passed over it. Through the pressure of the squeegee the ink is pushed through the screen onto the substrate lying below. In addition to the image carrier, each of these printing technologies require a back pressure element which presses the substrate onto the image carrier to transfer the ink. Gutenberg’s press, an adapted wine screw-type press, worked on the principle of “plane to plane”, that is, the image carrier and the back pressure element were flat. Middle- and large-sized letterpress machines of the nineteenth and twentieth centuries worked on the principle of “plane against cylinder”, i.e., with a flat image carrier and a back cylinder which rolls on the image carrier. The currently dominant technologies of offset printing, as well as gravure printing and flexography, work entirely on the principle of “cylinder against cylinder” to achieve entirely rotating motion sequences in the printing unit. Only in this way is it possible to achieve the production speeds expected today of 5000 up to 100000 impressions per hour. Multicolor printing presses, where several printing units are located one after the other, are largely constructed on the cylinder/cylinder basis. The four classic (conventional) printing technologies have one thing in common: the image carriers (masters) have a physically stable structure and are therefore not variable, that is to say, with the same image carrier it is possible to reproduce the same image in high quality many times. Beginning in the middle of the twentieth century several technologies have been developed that are known today as “non-impact printing technologies” (NIP technology). With these technologies, the printing plate is newly imaged for each printed copy (e.g., electrophotography) or the ink is directly transferred (without a plate or image carrier) onto the substrate (e.g., ink jet). One page after another can then be printed with a different content – even if there are limitations with respect to quality and productivity. Until a few years ago the non-impact technology was no alternative to conventional printing technologies as far as either quality, speed of production or cost were concerned. However, in recent years in particular, electrophotographic printing has been greatly improved and has therefore become a genuine alternative in some print media market sectors. This is particularly true of low volume printworks and jobs involving variable data and/or information (such as mailings), since the image can easily be completely changed for each copy. Prepress Operations Why is Prepress Important? Think about a book, magazine, catalog, brochure, postcard, poster, or any other printed item you might encounter on a daily basis. Each one originated as a creative idea…a vision someone had in their mind. At some point, the text and images that composed this vision were recreated using electronic pixels. With the aid of design software, the original idea was transformed into a digital file that could be viewed and manipulated on a computer screen. Now, here's the important question: How does something that exists in a digital format (such as a PDF file) transition into the physical product of ink on paper? The answer is Prepress. The production flow involved in the production of print media comprises the stages of prepress, the actual printing process (press) itself, and finishing (post-press). These individual production stages are connected by the flow of materials, such as printing plates between prepress and press and printed sheets between press and post-press. Interconnection between the production stages has become increasingly marked by the data flow. The content, layout, and form of the printed product are based on information in the form of originals and also particularly on data. However, it is to a large extent determined by the conception of the print medium in text, graphics, and pictures, the representational form of the contents, that is, by layout, typography, and graphic design. Prepress This term refers to the process which includes all the steps which are carried out before the actual printing, the transferring of information onto paper or another substrate. There are two types of prepress: 1) Traditional and 2) Digital. A Traditional prepress is divided into three areas: composition, that is, recording text, formatting text, and pagination; reproduction of pictures and graphics, and particularly color separations for multicolor printing; assembly and platemaking, i. e., the assembly of text, picture, and graphic elements into complete pages, (page layout/make-up), from pages to print sheets, and also the making of the printing plate as the vehicle of information in the printing press. A digital prepress machine accepts information electronically and transforms the data onto a printing plate which is ultimately used to transfer your files onto paper while on press. Using an experienced prepress team can be a significant time saver, especially if you used a graphic designer to create artwork in the correct format. Different file sizes, output needs, and file types can all slow down the printing process, but utilizing a trained prepress technician results in efficient file output quickly and efficiently. Steps in the Process When you produce a business card, magazine, or any type of artwork and send it to a printer, the prepress department takes charge of checking it to make sure it’s ready to be printed without any issues, such as color distortions or size-related problems. Modern prepress and reprographic professionals usually separate their duties into four stages: The First Stage: Pre-Flighting Preflighting is a term borrowed from the aviation industry that refers to the series of inspections and system checks performed on an aircraft prior to take off. In printing, Preflighting refers to the process of reviewing a digital artwork file to verify it has all the elements and formatting necessary to produce high-quality printed output. Preflighting is an essential part of the prepress process because it is much better to find and correct any file issues as early as possible, before they lead to costly mistakes like remaking printing plates or reprinting an entire job. Preflighting occurs soon after a printing order is received. The accompanying artwork file is forwarded to the prepress department where an experienced graphics specialist reviews it. In addition to a visual inspection, the file is sent through Preflighting software to identify any technical issues that might prevent it from printing properly. Preflighting detects potential problems with colors, fonts, images, bleeds, margins, spacing, and a host of other issues that could negatively affect the production run. Any concerns found during the preflight process are remedied before the artwork file can advance to the second prepress stage - the Raster Image Processor. The Second Stage: Raster Image Processor (RIP) After the artwork file passes the Preflight stage, it is then processed with specialized software known as the Raster Image Processor. RIP analyzes the data within the artwork file and translates it into the format needed to accurately reproduce the file layout on a printing press. Artwork files are created from various layers of overlapping information - text, images, shadowing, color blends, etc. The RIP software flattens the layers of information within a file to create a single layer. It then analyzes the colors of the file and uses this information to create grids of tiny dots. Though you may not realize it, commercial full-color printing is created from thousands of miniscule cyan, magenta, yellow, and black ink dots. These individual ink dots cannot be detected with the naked eye, but they are visible under heavy magnification. Printing presses apply these four colors of ink dots to the paper one after the other, where they intermingle to create what our eyes perceive as full color images. Because the printing press applies the four ink colors to the paper one at a time, the RIP software separates the artwork file into four unique color files (cyan, magenta, yellow, and black) so that the printing press can lay down these four colors individually. If the project will be produced on a Digital press, these color-separated files will be transmitted directly to the press when it is time to produce the project. If the project is to be produced on an Offset press, the color-separated files will be sent to a plate making device so that physical printing plates can be created for each of the four ink colors. The Third Stage: Creating a Proof The third stage of the prepress process involves forwarding a Proof to the client, or their graphic designer, for approval. A Proof is a representation of how the project will appear once printed. Proofing is an important stage because it ensures the client and the printing company are in agreement about the desired outcome. Also, should any issues be found at this stage, there is still an opportunity for changes to be made to the file before it goes to print. There are two basic types of proofs - soft proofs and hard proofs. A Soft Proof refers to an electronic file that displays on a computer screen. Usually created as a PDF file, soft proofs are the most widely used type of proof. Soft proofs are very convenient because they can be emailed, either as an attachment or as a clickable link that will display the proof file. The ease of sharing a soft proof streamlines the approval process, which allows the project to be placed on the production schedule sooner. A Hard Proof refers to a proof that exists in physical form. Hard proofs are basically a one-off version of a print project, so they can sometimes be expensive to produce. Also, hard proofs will need to be mailed or shipped, which can add cost and time to the project. For these reasons, Hard proofs are generally reserved for projects that are color critical or have more involved physical features, such as complex folding or a detailed construction method. A benefit of using a hard copy proof is that it can often be printed on the actual paper, cardstock, or other substrate specified for the project. This allows the thickness and texture of the piece to be inspected in addition to the layout. Once proofs are approved by the client, the project is entered into the production schedule. Projects that will be printed on a Digital press are pretty much ready to go after the proofing stage. On the other hand, Offset projects will require one additional step before they will be press ready - the creation of printing plates. The Fourth Stage: Printing Plates (for Offset Presses) After the proof has been approved, the project is ready to be produced on a printing press. If the project is to be produced on a digital printing press, the pre-press process is pretty much complete. This is because the graphics file can be electronically transferred directly to the digital press for output without the need for printing plates. However, if the project is to be produced on an offset press, it will need printing plates. In this case, the final stage of the pre-press process is the creation of printing plates. Printing plates are made from plastic, rubber, metal, paper, and other materials. At this point, the actual run begins, bringing an end to the prepress process. From there, the printer lets the press do its job. The plates are mounted on a large cylinder. As each plate cylinder rotates, it receives a metered amount of ink. The plate cylinder contacts another rotating cylinder that is wrapped with a rubber blanket. The inked image on the plate cylinder offsets to the blanket cylinder. The blanket cylinder, with the aid of an impression cylinder, then offsets the ink to the paper. Each rotation of the plate cylinder applies a fresh layer of ink to the blanket and the process repeats. Also, each ink color used on the project has its own set of printing plates and cylinders, so impressions are being made for each ink color as the paper, or other substrate, travels through the press. Letterpress Printing A common feature of all letterpress processes is the fact that the printing elements of the plate are raised above the nonprinting elements. The printing elements that are at the same height (image areas) are coated with a layer of ink of constant thickness by the application rollers. It is a mechanical technology in which a relatively high pressure is required to transfer the highly viscous, pasty ink to the paper via the hard printing elements. Primarily, and simply put, letterpress printing involves the placement of individual moveable type into a chase, or a bed, that is then inked, before the paper is then pressed into the letters (hence the name letterpress) to create an impression on the paper. The letterpress printing technique is used with the following printing systems: Book printing, Flexographic printing, Letterset. Book printing Book printing is the oldest letterpress printing technology. As a result of Gutenberg’s inspired discovery in the middle of the fifteenth century of how to produce individual, moveable type from lead alloy, it became possible to reproduce type elements economically and quickly, and thereby to reproduce books by printing. The importance of letterpress printing has diminished in recent decades, mainly because of the expense of producing printing plates. The following printing principles are applied in book printing: Plane-Plane: Platen press. Plane-Cylinder: Flatbed cylinder printing. Cylinder-Cylinder: Rotary printing. Letterpress was originally carried out on platen presses, in which the paper is pressed against the flat, inked form by a flat platen; later, the platen was replaced by a roller in the flat-bed cylinder press; still later, the printing form (plate) was wrapped around one cylinder and the paper was passed between this cylinder and a second, creating a rotary press. Printing plates for platen printing and flatbed cylinder printing consist almost of several fixed, rigid, flat individual component parts. Semicircular cast lead plates (stereos) or flexible plastic plates, so called wash-off printing plates, are suitable for rotary printing. Hot metal composition and photocomposition are suitable for the production of printing plates for text in book printing. The variety of printing plates and printing-plate components that can be used is characteristic of letterpress printing consist of various materials such as lead alloys, zinc, copper, and photopolymer plastics, and, in art printing, wood and linoleum. Prints produced using the letterpress technology can be recognized by an accumulation of ink at the edges. Letterpress can produce work of high quality at high speed, but it requires much time to adjust the press for varying thicknesses of type, engravings, and plates. Because of the time needed to make letterpress plates and to prepare the press, many newspapers have changed to offset printing. To combat this trend, letterpress printers have developed printing plates made from a photosensitive plastic sheet that can be mounted on metal. Flexographic Printing In the last several decades, a modified letterpress printing method, flexography, has become increasingly more prevalent, especially in the packaging industry, for printing on the most varied materials. The term “flexography” was introduced at the beginning of the 1950s (it was previously known as “Aniline Printing”). Unlike letterpress printing, flexography uses low viscosity inks that is transferred to the printing plate via a roller that is evenly screened with cells, the so-called screen roller/anilox roller (screen width 200–600 lines/cm, ceramic or hardchromed metal surface). The rubber or plastic plate is attached to the printing plate cylinder, which are soft, flexible printing plates (compared to book printing plates) and the pressure applied between plate cylinder and substrate is low (“Kiss Printing”). letterpress printing flexography printing Ink is transferred to the printing substrate by the pressure of the impression cylinder. The use of a blade (together with the ink supply system) on the screen roller has a stabilizing effect on the printing process resulting from even filling of the cells on the screen roller. With the rubber plates, only a low to moderate printing quality of solid motifs and rough line drawings could be achieved. Letterset In letterset printing, the image of the letterpress plate (stable, hard letterpress plate) is transferred to the paper via an intermediate carrier (a cylinder covered with a blanket) – that is by indirect letterpress printing. It is still used in certain special fields, packaging printing in particular. By analogy with the offset printing process as an indirect lithographic technology, letterset printing could also be called offset letterpress printing technology – but to avoid misunderstandings, the term lithographic offset printing would need to be used rather than the term offset printing. Letterpress Printing (Process and Applications): Letterpress is the oldest of the traditional printing techniques and remained the only important one from the time of Gutenberg (1400 – 1468), Johannes Gutenberg, who invented the printing press in (15thcentury) is a German inventor and designer, brought the technique of letterpress printing to Europe, until the development of lithography late in the 18th century and, especially, offset lithography early in the 20th. The fundamental disadvantages of letterpress printing compared to offset printing are the expensive printing plate, the costly makeready of the printing plate, the limited print quality and the limit of production speed. Letterpress was the invention that made the mass-production of books and newspapers possible and made books economically viable for both publishers and readers. In Gutenberg’s time, he used metal alloys and hand molding to cast the type. Gutenberg and his printing press are also responsible for what’s known as the Gutenberg Bible, as he was the first person to print a version of the Bible. Gutenberg’s earliest printing process isn’t well known, but it is thought that typesetting each plate would take hours, then they had to ink the type, print, hang up the sheets, and much more. Letterpress printing was the predominant book-printing process. For four centuries it was also the predominant printing technology for posters, announcements, printed matter for churches, government and businesses, single- or two-page local news-sheets, and daily and weekly newspapers, as well as several simple print jobs. In the beginning, the letterpress printing process would be all done by hand. With someone carefully placing all the letters individually into the plate and inking the plates once in order. Printing is by a relief image plate. The relief (print) areas receive a film of high viscosity ink and under a controlled pressure known as the ‘impression,’ the image is transferred direct from the plate to the substrate. At the top of the unit, you can see the ink reservoir known as the ink duct, which distributes a controlled amount of ink to the inking distribution rollers. These distribution rollers rotate and oscillate from side to side, breaking down the ink film and ensuring that correct ink film weight ink is deposited on the printing plates with each revolution of the press. The substrate being printed travels between the rotating plate cylinder and the impression cylinder and the printing pressure is adjusted by increasing or decreasing the plate cylinder pressure to the substrate. Careful balance of pressure between plate and impression roll is crucial as it determines the print quality. Too much impression creates a squashed or halo effect and too little impression creates missing dots and poor print. In order to achieve a good ink film transfer and a sharp image, the pressure between the printing plates and the impression cylinder or flatbed requires a very careful setting. A skilled operator will vary the hardness of the impression roll ensuring that the plate to substrate contact is a ‘kiss’ touch. Designs carved on wood blocks combine with movable letters of wood or metal. These elements are positioned backwards, and locked into a frame, or “chase,” secured in a printing press, and inked. The paper is pressed onto the inked type to obtain an impression that is right-reading. Posters with more than one color require separate forms for each color. Each application of additional color requires a new pass of the paper through the press. What is it primarily used for? Due to the letterpress printing process makes the print look very vintage and “old school”, the printing process is used for printing on gift cards and cards. Also forms, labels, lottery tickets, security papers, telephone books, and paperbacks. Letterpress was also used for newspaper web printing. A few newspaper rotaries are still in use both for direct and indirect printing (letterset, with blanket cylinder). The last newspaper letterpress printing presses were delivered in the 1980s. The letterpress printers are also used by a lot of private persons as a hobby since it is easy to get a very low-cost set-up that can be used for printing hobby projects. The printing process can often also be used for embossed printing. Letterpress printing is often used for printing serial numbers, barcodes, and design elements of covers. How does it work? Letterpress printing does use printing plates, and they are probably the most essential part due to they are the ones transferring the ink onto the object that needs to be printed. 1. The printing plates are made by first turning the graphics into a litho film using a film processor. 2. Then the litho film photography is put over the plates and put into the platemaker machine where they are covered with a vacuum sheet. 3. The platemaker machine then exposes the plates and litho film for UV lighting to transfer the graphics on to the printing plates. 4. The plates are then cleaned with water, and they are then cooled off. In the end, they are again exposed to UV light to harden them and make them stable for the printing process. Letterpress printing does normally only make the print in one color, since the printing plates only can carry one color at a time. So, if the graphics have more than one color in it, the printing plates would need to be shifted and the paper with the print would need to cool off. If the system does not have any cooling mechanism, so they would normally have to cool off by waiting. This often slows the production process a lot, why it normally is printed in one color. Letterpress printing can both use CMYK and Pantone color, but it is mostly Pantone colors used since the colors are added one at a time. The colors are either added directly to the rollers or to a flat iron plate, where the roller rolls over to receive the ink. The rollers’ jobs are to make sure that the printing has enough ink at all times, and they do that by rolling over the printing plate after it has printed one object. So, the process works by the printing plate being pressed onto the objects that need printing, and then in between the next press, the rollers roll over the printing plate to add more ink to ensure the right amount of ink is added to the object. The object just needs to cool off after the ink has been added and then it is ready to use. Imaging The Letterpress Plate: The imaging of photopolymer plates is done by exposing the polymer to a UV light source through a film negative. The film and plate are positioned in contact with one another and placed in a vacuum sealed unit to ensure full and even contact. Exposure units may be flat or rotary. If the plate is for flatbed application, then the exposure is done flat, but if the plate is for rotary use, then it is done in a rotary unit. This is necessary because allowance has to be made for the distortion factor that is created by the curvature of the printing cylinder. UV light is then applied and the image area is polymerized and hardens leaving the unexposed area still soft, which can then be removed. The washing/brushing process is done in a washing unit and the removal of the non-image area can be achieved with direct sprays, pads, or a rotating brush and sprayed with clean warm water. The brush must be soft to avoid damaging the plate surface. The plate is then dried using warm air and a second post cure exposure is given to the plate to ensure the polymer is fully hardened. CTP (Computer to Plate) Imaging: Letterpress plate imaging is also done using CtP (Computer to Plate) direct ablation. This is a process which uses specially formulated letterpress plates coated with a black ablation layer which means that the letterpress plate can be imaged directly via a digitally driven laser which is controlled from a computer file. The hard, metal-reinforced letterpress plates are coated with a black ablation layer that is evaporated by laser and removed by suction from the parts to be printed. The plates are then cured with UV light, washed out, dried and post-exposed. Letterpress Print Cylinders: In the flexographic, letterpress and litho processes the printing plate is located on the print cylinders. The cylinder needs to have accurate and even contact with the inking rollers and the surface of the substrate. The print cylinders should run perfectly true with an accuracy of ±0.025 mm ensuring that the pressure on the adjacent rollers is constant. Accurate measurement should be made when the press has been running for a short period to allow the running parts to warm up. Plate Mounting: Before mounting the printing plate the print cylinder surfaces should be thoroughly cleaned to ensure a clean, uncontaminated surface. A contaminated cylinder surface will cause problems with the print quality. Foreign particles trapped between the surfaces of the print cylinder, the mounting tape and the back of the printing plate and any grease or oily residue will affect the adhesion power of the mounting tape causing plate lift during the print run. Double sided filmic adhesive tape is used to fix the printing plate to the printing cylinder. Letterpress Inks And Drying Systems: Paste inks are used for both flatbed and rotary letterpress systems. The ink has a high viscosity and is therefore very similar to offset litho inks (often referred to as a short ink). The letterpress plate has a hard surface and this ensures a good ink film transfer to the substrate being printed. The majority of letterpress label presses are equipped with ultraviolet (UV) curing systems and the UV ink is especially formulated to cure rapidly. Advantages and Disadvantages of Letterpress Printing: Advantages: Good color density Extended plate life Good printing of type and solids and sharp edge definition No ink and water balance problems Suitable for sheet-fed and web-fed printing Good legibility of text even on uncoated papers Disadvantages Limited tonal reproduction Minimum printable dot (3-5%) Relatively high printing plate costs Poor tonal reproduction when compared with offset litho Relatively coarse screen rulings have to be used for tonal reproductions