Print_EN_GRIDCON iTAP PDF - Maintenance Manual
Document Details
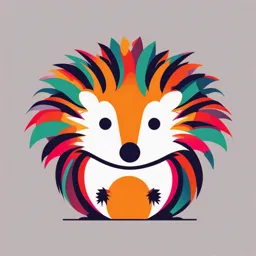
Uploaded by ValuableSugilite
Pink University
Tags
Related
- OILTAP® M On-load Tap-Changer Installation & Commissioning Instructions PDF
- On-Load Tap Changer Type R and RM Inspection Instructions (PDF)
- VACUTAP® VM 300 On-load tap-changer Operating Instructions PDF
- OILTAP® R On-load Tap-Changer Installation and Commissioning Instructions PDF
- VACUTAP® VV® On-load tap-changer Operating Instructions PDF
- On-load tap-changer VACUTAP® VV Maintenance Manual WA 241/05 PDF
Summary
This document provides a comprehensive guide on the maintenance and servicing of GRIDCON iTAP equipment, specifically focusing on step-by-step procedures, parts replacement, and safety guidelines.
Full Transcript
Table of contents Table of contents 1 Introduction......................................................................................................................... 2 2 Step-by-Step....................................................................................................
Table of contents Table of contents 1 Introduction......................................................................................................................... 2 2 Step-by-Step....................................................................................................................... 3 2.1 Tests and condition-based parts replacement at each maintenance................................................. 3 2.2 Parts replacement after fixed number of tap-change operations intervals......................................... 3 2.3 One-time retrofit and modifications..................................................................................................... 3 2.3.1 Until 28 July, 2016 - Replacing micro-switches in tap-change supervisory control............................................... 3 3 Assemblies.......................................................................................................................... 6 3.1 General............................................................................................................................................... 6 3.1.1 Replacing GRIDCON® iTAP® motor-drive unit with ECOTAP® VPD® MD&C.................................................... 6 3.2 Contact system, switching element.................................................................................................. 22 3.3 Energy accumulator, gearbox........................................................................................................... 22 3.4 Supporting cylinder/supporting bars, coupling shaft, switching column............................................ 22 3.4.1 Until 28 July, 2016 - Replacing micro-switches in tap-change supervisory control............................................. 22 3.5 Transition impedance and protective circuit..................................................................................... 25 3.6 Control, contactors and micro-switches............................................................................................ 25 3.6.1 Software update CPU......................................................................................................................................... 25 3.6.2 Until 28 July, 2016 - Replacing micro-switches in tap-change supervisory control............................................. 44 3.6.3 Safety notices for current and power measurement card replacement.............................................................. 46 EN 1 1 Introduction 1 Introduction NOTICE Risk of personal damage or injury, damage to property or mal- function. If work is performed by insufficiently qualified personnel and/or safety in- structions are not observed, there is a risk of personal damage or injury, damage to property or malfunction. ► Safety, hazard and other information included in the MR operating in- structions for the relevant on-load tap-changer type must be observed! ► Please read the instructions carefully before starting work. ► The realization of the instructions below requires profound knowledge and experience that correspond to the knowledge acquired during a train- ing at MR about maintenance of the relevant on-load tap-changer type. ► It is absolutely necessary that the diverter switch insert (or selector switch insert, respectively) has been removed. 2 EN 2 Step-by-Step 2 Step-by-Step 2.1 Tests and condition-based parts replacement at each maintenance 2.2 Parts replacement after fixed number of tap-change operations intervals 2.3 One-time retrofit and modifications 2.3.1 Until 28 July, 2016 - Replacing micro-switches in tap-change supervisory control The instruction describe when and under which conditions the micro- switches in the tap-change supervisory control have to be replaced. The re- placement can normally be performed in less than one hour. Replacement criterion Up to 28 July 2016, the contact material of micro-switches S80/S81 in the tap-change supervisory control consisted of silver (figure 2). Since 29 July 2016, the contact material of the micro-switches consists of sil- ver-nickel, galvanized with gold (figure 1). When performing a service assignment on a GRIDCON® iTAP®, the old- version micro-switches have to be replaced with microswitches of the new version. If micro-switches of the new version are already installed, they have to be replaced only in the event of failure. The OPS is responsible to provide the necessary parts via SETERSATZ in advance. Preparatory work Before starting work, de-energize the control cabinet of the on-load tap- changer type GRIDCON® iTAP® using the F1 miniature circuit breaker. To perform work, the drive motor of the tap changer on the transformer cover must be accessible. If necessary, the facility operator must disconnect and ground the transformer on all poles. EN 3 2 Step-by-Step DANGER Electric shock! Risk of fatal injury due to electrical voltage. Always observe the following safety regulations when working in or on electrical equipment. ► Disconnect the equipment. ► Provide safeguard to prevent unintentional restart. ► Make sure all poles are de-energized. ► Ground and short-circuit. ► Cover adjacent, energized parts or put barriers. Distinctive feature Micro-switch current version (figure 1). Contact material: AgNi gal. Au Figure 1: Fig. 2 Current micro-switch Micro-switch old version (figure 2). Contact material: Ag Figure 2: Fig. 2 Old micro-switch Automatic adjustment and test tap-change operations Carry out automatic adjustment as specified in Operating Instructions 4288748 "On-Load Tap-Changer GRIDCON® iTAP®", section 10.3. When you have performed adjustment successfully, perform trial tap-change oper- ations across the entire regulating range and ensure correct function of the tap changer. Energize the control cabinet of the on-load tap-changer GRIDCON® iTAP® again using the F1 miniature circuit breaker, and then start automatic adjust- ment and function test. Depending on the facility design, it can be necessary to energize the transformer without load. 4 EN 2 Step-by-Step NOTICE! If the transformer is energized, it may not be possible to switch to each operating position without leaving the allowed voltage bandwidth. In that case, do not perform homing. Limit trial tap-change operations to an ad- equate range of operating positions. If the control indicates an error, perform homing. In that case, do a risk assessment if it is possible with the trans- former being energized. Installation direction of micro-switches Installation notes Fitting washer alignment Locking with Torque: 1 Nm DELO ML 5428 Locking with DELO ML 5428 EN 5 3 Assemblies 1 2 3 4 5 6 7 8 9 10 3 Assemblies A B AB Text box 4x Text box 1 2 3 4 5 6 7 8 9 10 11 12 13 3.1 General 14 15 16 17 18 19 20 Text box Text box 8 M8 x 20 30 Nm Text box 3.1.1 Replacing GRIDCON® iTAP® motor-drive unit with ECOTAP® VPD® MD&C This section describes the replacement of the motor-drive unit GRIDCON® iTAP® with the motor-drive unit ECOTAP® 6 cm VPD® MD&C. This measure must be performed in case of a defective GRIDCON® iTAP® motor or con- trol cabinet. Before: GRIDCON® iTAP® motor and motor plate GRIDCON® iTAP® sealing module After: ECOTAP® VPD® motor cover ECOTAP® VPD® sealing module with sealing flange and indication gear Adapter plate GRIDCON® iTAP® sealing module Figure 3: Overview GRIDCON® iTAP® motor and ECOTAP® VPD® motor 6 EN 3 Assemblies Figure 4: Hand wheel and tap position indicator GRIDCON® iTAP® These instructions do not describe the installation and commissioning of the control unit. This information can be found in the operating instructions of the motor-drive unit ECOTAP® VPD® MD&C. Preparatory work To perform work, the motor-drive unit of the OLTC on the transformer cover must be accessible. The facility operator must disconnect and ground the transformer on all poles. The supply voltage and any available signal volt- ages of the GRIDCON® iTAP® control cabinet must be disconnected. The on-load tap-changer GRIDCON® iTAP® must be in operating position 5. DANGER Electric shock! Risk of fatal injury due to electrical voltage. Always observe the following safety regulations when working in or on electrical equipment. ► Disconnect the equipment. ► Provide safeguard to prevent unintentional restart. ► Make sure all poles are de-energized. ► Ground and short-circuit. ► Cover adjacent, energized parts or put barriers. Removal EN 7 A B AB Text b Text b 1 2 3 4 5 67 8 9 10 Text box 8 M8 x 20 30 Nm 3 Assemblies 6 cm Arial 9, normal Remove cables for motor control and micro-switches S80/81 between motor- drive unit and control cabinet. Figure 5: Removing cable in control cabinet Remove 1 grounding screw M8 x 16 together with cable. Figure 6: Removing grounding screw with cable 8 EN 3 Assemblies Open 4 M6 x 35 cylinder head bolts. Remove motor-drive unit incl. motor plate from the sealing module. Figure 7: Opening screw connection of the motor on the sealing module Remove GRIDCON® iTAP® motor incl. motor plate from the sealing mod- ule. Loosen hex. head bolts 4 M3 x 16 of micro-switches and remove micro- switch S80/S81 from the sealing module. Figure 8: Removing micro-switches S80 and S81 At the control cabinet GRIDCON® iTAP, label all cables attached by the cus- tomer and disconnect them. Disassemble the control cabinet. Installation Remove flat sealing from GRIDCON® iTAP® sealing module. Clean sealing surface and insert new sealing. EN 9 1 2 3 4 5 67 8 9 10 Text box 4x Text box A B AB 1 2 3 4 5 67 8 9 10 Text box 8 M8 x 20 30 Nm 3 Assemblies 6 cm Install adapter plate to GRIDCON® iTAP® sealing module and tighten 4 cylinder head bolts M6 x 25 incl. locking washers to 8 Nm. Insert sealing into groove of adapter plate. 1 2 3 4 5 67 8 9 10 Text box 4x Text box A B AB Adapter plate 1 2 3 4 5 67 8 9 10 Text box 8 M8 x 20 30 Nm Figure 9: Installing adapter plate to GRIDCON® iTAP® sealing module 6 cm Open hex. head bolts M6 x 30 and remove ECOTAP® VPD® motor cover Arial 9, normal with motor from the sealing module. Remove adapter for manual activation from the ECOTAP® VPD® sealing module. ECOTAP® VPD® motor cover Figure 10: Remove ECOTAP® VPD® motor cover with motor from the sealing module. Make sure that the indication gear of the ECOTAP® VPD® sealing module shows the same operating position as the on-load tap-changer GRIDCON® iTAP®, visible in the inspection window in the transformer cover. If the oper- ating positions are not identical, move the on-load tap-changer GRIDCON® iTAP® into the respective operating position by means of hand wheel. 10 EN A B AB Text b Text b 1 2 3 4 5 67 8 9 10 Text box 8 M8 x 20 30 Nm 3 Assemblies 6 cm Arial 9, normal The adjusting triangles on the cam disk and micro-switch carrier plate in the ECOTAP® VPD® sealing module must be equal. Micro-switch carrier plate 1 2 3 4 5 67 8 9 10 Text box 4x Text box A B AB 1 2 3 4 5 67 8 9 10 Text box 8 M8 x 20 30 Nm Cam disk Arial 9, normal Figure 11: Position of adjusting triangles cam 6 disk cmto micro-switch carrier plate Insert feather key into groove of drive shaft ECOTAP® VPD® sealing mod- ule. Feather key Drive shaft Figure 12: Feather key of drive shaft ECOTAP® VPD® Align feather key of drive shaft of sealing module ECOTAP® VPD® to the groove of the drive shaft of the GRIDCON® iTAP® sealing module. EN 11 3 Assemblies NOTICE! At this time, the drive shaft can freely move in relation to the cam disk. 1 2 3 4 5 6 7 8 9 10 A B AB Text box 4x Text box 1 2 3 4 5 6 7 8 9 10 Figure 13: Aligning drive shaft sealing flange drive 11 12 13 14 15 16 17 18 19 20 Text box Text box 8 M8 x 20 30 Nm Place sealing flange of ECOTAP® VPD® sealing module on adapter plate and tighten hex. head bolts M6 x 25 sealing ring to 6 Nm. The adjusting triangles on the cam disk and micro-switch carrier plate in the ECOTAP® VPD® sealing module must still be equal. Align cam disk, as necessary. 6 cm Arial Place adjustment template on Unicode sealing 9, normal flange of ECOTAP® VPD® sealing module. Adjustment template Sealing flange Figure 14: Placing adjustment template on sealing module Install direction indicator on adapter for manual operation. Insert adapter for manual operation with direction indicator in the drive shaft of the ECOTAP® VPD® sealing module. 12 EN A B AB Text box 4x Text box 1 2 3 4 5 6 7 8 9 10 11 12 13 14 15 16 17 18 19 20 Text box Text box 8 M8 x 20 30 Nm 3 Assemblies 6 cm NOTICE! The position of the direction indicator in relation to the adapter for Arial Unicode 9, normal manual operation must no longer be changed. Adapter for manual activation 1 2 3 4 5 6 7 8 9 10 Direction indicator A B AB Text box 4x Text box 1 2 3 4 5 6 7 8 9 10 11 12 13 14 15 16 17 18 19 20 Text box Text box 8 M8 x 20 30 Nm Figure 15: Inserting direction indicator with adapter for manual operation. Rotate adapter for manual operation in counterclockwise direction using ap- propriate tools (size 10) until the mechanical end position blocking of the on- load tap-changer GRIDCON® iTAP® is reached. 6 cm NOTICE! The position of the cam disk in the ECOTAP® VPD® sealing Arial Unicode 9, normal flange must not be changed anymore. Rotate 360° per tap. 1 2 3 4 5 6 7 8 9 10 A B AB Text box 4x Text box 1 2 3 4 5 6 7 8 9 10 11 12 13 14 15 16 17 18 19 20 Text box Text box 8 M8 x 20 30 Nm Figure 16: Rotating in counterclockwise direction to end position blocking Mark position of the direction indicator 6 cm on the adjusting template at the posi- tion of the mechanical end position blocking of the on-load tap-changer Arial Unicode 9, normal GRIDCON® iTAP® while rotating in counterclockwise direction. Figure 17: Marking end position while rotating in counterclockwise direction EN 13 1 2 3 4 5 6 7 8 9 10 A B AB Text box 4x Text box 1 2 3 4 5 6 7 8 9 10 3 Assemblies 11 12 13 14 15 16 17 18 19 20 Text box Text box 8 M8 x 20 30 Nm Rotate adapter for manual operation in clockwise direction until the other mechanical end position blocking of the on-load tap-changer GRIDCON® iTAP® is reached. Mark position of6 the cm direction indicator on the adjusting template at the position of the mechanical end position blocking of the on- Arial Unicode 9, normal load tap-changer GRIDCON® iTAP® while rotating in clockwise direction. 1 2 3 4 5 6 7 8 9 10 A B AB Text box 4x Text box 1 2 3 4 5 6 7 8 9 10 Figure 18: Marking end position while rotating in clockwise direction 11 12 13 14 15 16 17 18 19 20 Text box Text box 8 M8 x 20 30 Nm Operate on-load tap-changer GRIDCON® iTAP® back into adjustment posi- tion of the indication gear of the ECOTAP® VPD® sealing module by rotat- ing the adapter for manual operation. To center the on-load tap-changer GRIDCON® iTAP®, rotate the adapter for manual operation in clockwise direction until the torque has noticeably in- creased (opening of vacuum interrupters 6 cm MSV1). Mark the position of the di- rection indicator on the adjustment template. The tap position indicator of the on-load tap-changer GRIDCON® iTAP® must not be changed. 1 2 3 4 5 6 7 8 9 10 A B AB Text box 4x Text box 1 2 3 4 5 6 7 8 9 10 Mark for tightening torque 11 12 13 14 15 16 17 18 19 20 Text box Text box 8 M8 x 20 30 Nm drive shaft in clockwise direction Figure 19: Mark rotation drive shaft in clockwise direction Rotate the adapter for manual operation 6 cm in counterclockwise direction until the torque has noticeably increased (opening of vacuum interrupters MSV2). Mark the position of the direction indicator on the adjustment template. Mark for tightening torque drive shaft in counterclockwise direction Figure 20: Mark rotation drive shaft in counterclockwise direction 14 EN 1 2 3 4 5 6 7 8 9 10 A B AB Text box 4x Text box 1 2 3 4 5 6 7 8 9 10 11 12 13 14 15 16 17 18 19 20 Text box 8 M8 x 20 30 Nm 3 Assemblies Rotate adapter for manual operation6 cmin such a way that the direction indica- tor is aligned in the center between the marks with increased torque (open- ing of vacuum interrupters MSV1 and MSV2). Direction indicator in the center between α marks α Figure 21: Direction indicator in the center between marks 1 2 3 4 5 6 7 8 9 10 Remove adapter for manualA operation B AB with direction indicator from the 4x drive Text box Text box 1 2 3 4 5 6 7 8 9 10 shaft of the ECOTAP® VPD® sealing module. 11 12 13 14 15 16 17 The 18 position Textdrive 19 20of the box shaft Text box 8 M8 x Re- 20 NOTICE! must not be changed anymore! 30 Nm move adjustment template. Check that the on-load tap-changer GRIDCON® iTAP® and the indication gear of the ECOTAP® VPD® sealing module are in the same position. Check alignment of adjusting triangle on cam disk to adjusting triangle on micro-switch carrier plate of the ECOTAP® 6 cm VPD® sealing module. In case the position does not match, carefully turn the cam disk in such a way that Arial Unicode 9, normal the drive shaft position does not change. Cam disk Adjusting triangles Micro-switch carrier plate Figure 22: Alignment cam disk to micro-switch carrier plate EN 15 1 2 3 4 5 67 8 9 10 Text box 4x Text box A B AB 1 2 3 4 5 67 8 9 10 Text box 8 M8 x 20 30 Nm 3 Assemblies Tighten ECOTAP® VPD® cam disk with 6 cmcounter washer by means of 3 cylinder head bolts M4 x 20 twice until hand-tight. The adapter for manual operation can be used against unintentional rotation of the drive shaft ECOTAP® VPD® sealing module. Cam disk Cylindrical bolt 1 2 3 4 5 6 7 8 9 10 Figure 23: Bolt connection cam disk A B AB Text box 4x Text box 1 2 3 4 5 6 7 8 9 10 Place the adjustment template on the ECOTAP® VPD® to check that the mechanical 11 12 13 14 15 16 17 end18 position 19 20 blocking of Text the indication box 8 ECOTAP® gear in the M8 x 20 30 Nm VPD® sealing module is reached before the mechanical end position block- ing of the on-load tap-changer GRIDCON® iTAP®. Insert adapter for manual operation with direction indicator in the drive shaft of the ECOTAP® VPD® sealing flange. Rotate in clockwise direction (in di- rection of operating position 1) until the mechanical end position blocking is activated. Distance between marks6 end cm position blocking indication gear ECOTAP® VPD® sealing module and end position blocking on-load tap- Arial Unicode 9, normal > 10 ° changer GRIDCON® iTAP® must be > 10°. 1 2 3 4 5 6 7 8 9 10 End position blocking A B AB Text box 4x Text box 1 2 3 4 5 6 7 8 9 10 indication gear 11 12 13 14 15 16 17 18 19 20 Text box Text box 8 M8 x 20 30 Nm > 10 ° End position blocking on-load tap-changer Figure 24: Checking mechanical end blocking position indication gear in direction of operating position 1 6 cm NOTICE! The distance between neighboring scale marks on the adjustment Arial Unicode 9, normal template is 5°. Scale mark Figure 25: Distance scale marks adjustment template 5° 16 EN 1 2 3 4 5 6 7 8 9 10 A B AB Text box 4x Text box 1 2 3 4 5 6 7 8 9 10 3 Assemblies 11 12 13 14 15 16 17 18 19 20 Text box 8 M8 x 20 30 Nm Rotate adapter for manual operation with direction indicator in counterclock- wise direction (in direction of operating position 9) until the mechanical end position blocking is activated. Distance 6 cm between marks end position blocking indication gear ECOTAP® VPD® sealing module and end position blocking Arial Unicode 9, normal > 10 ° on-load tap-changer GRIDCON® iTAP® must be > 10°. End position blocking on-load tap-changer > 10 ° End position blocking indication gear Figure 26: Checking mechanical end blocking position indication gear in direction of operating position 9 1 2 3 4 5 7 8 9 10 6 In case the distance of one end position is