Powerplant.docx
Document Details
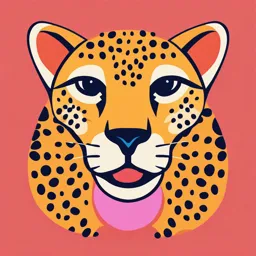
Uploaded by PhenomenalNumber
Full Transcript
Powarplant 2A-71-10: General Arrangement General: (See Figure 1.Powerplant GeneralArrangement.) The BR725 is the third engine in the series of BR700's, all derived from a common core; containing a Rolls-Royce technology annular combustion chamber, atwo-stage shrouded High-Pressure Turbine(HPT) wi...
Powarplant 2A-71-10: General Arrangement General: (See Figure 1.Powerplant GeneralArrangement.) The BR725 is the third engine in the series of BR700's, all derived from a common core; containing a Rolls-Royce technology annular combustion chamber, atwo-stage shrouded High-Pressure Turbine(HPT) with modulated clearance control and a new three-stage Low-Pressure Turbine (LPT) with high lift blading. The engine designation BR700-725A1-12 refers to the powerplant for use on the Gulfstream G650ER aircraft. The BR725 engine is equipped with a 50 inch swept fan for improved flow, efficiency and noise and is designed to have a higher thrust-to-weight ratio, a lower Specific Fuel Consumption (SFC) and significanUy longer maintenance intervals. The engine is a high bypass ratio turbofan with Low Pressure (LP) and High Pressure (HP) compressors driven by turbines through coaxial shafts. All air entering the engine air intake passes through the LP compressor (fan) and is then divided into the two mainflows; the fan (cold) stream and the core (hot) stream.The cold stream air passes through the fan Outlet Guide Vanes (OGVs) along the structural bypass duct, through the forced mixer: the core airflow also passes through the forced mixer and a combined air stream is exhausted to the atmosphere through a common nozzle. The turbines and exhaust are designed for minimal noise production. The HP compressor has ten 1O stages of rotor blading forcing the core airflow into a low-emission annular combustion chamber incorporating 20 fuel spray nozzles through which fuel is supplied accordingto the engine control system demand. All engine operation is controlled by a Full Authority Digital Engine Control (FADEC) mounted at the twelve o'clock position on each engine core. The FADEC is powered by a self-contained generator, but can use aircraft direct current (DC) if the generator fails. The FADEC is electrically linked to the cockpit power levers and switches and communicates with all three Modular Avionics Units (MAUs) and three Air Data Systems (ADSs) over ARINC 429 data buses. Engine Data: Configuration: Singlewide chord, 50 inch diameter, 24 blade fan Ten stage HP compressor Two stage HP turbine Annular combustion chamber Three stage LP turbine Exhaust section Full Authority Digital Engine Control (FADEC) Clockwise rotation (as viewed from rear, both shafts) Ratings (Takeoff At ISA Sea Level, Static): Thrust - 16,900 lb @ SL, 86°F Flat Rating - ISA + 15"C Pressure Ratio - 29.9:1 Bypass Ratio - 4.18:1 Mass Flow - 478 lb I sec Dimensions: Length - 203 in Fan Diameter - 50.0 in Basic Weight - 4,760 lb 100% Shaft Speeds: LP - 7,000 RPM HP - 15,898 RPM b. Subsections Within this Section: This section is divided into the following subsections: 2A-71-20: Nacelle Arrangement 2A-71-30: Mechanical Accessories Limitations: Primary Operating Limits: The following limitations exist for the BMW/Rolls Royce BR700-725A1-12 engines: Condition MAX LP (%) MAX.HP (%) MAX TGT Time Limit Ground Start <1> - - 1oo·c Momentary Airstart (Relight) - - 850"C Momentary Takeoff(2l 102.8 100.0 900"C 5 Minutes Maximum Continuous 102.8 98.7 885"C Unrestricted Maximum Overspeed 104.3 101.3 - 20 Seconds Maximum Overtemperature - - 920"C 20 Seconds Reverse Thrust <3! <"> 78.1 - - 30 Seconds (1) Maximum TGT prior to ground start is 150"C. (2) The use of takeoff ratingislimited to five minutes all engines operatingor ten minutes inthe event of an engine failure. (3) Static operation of thrust reversers is limited to 30% LP maximum. <4> Maximum reverse thrust must be selected only at airplane speeds above 60 knots. Engine Ground Start: A ground start can be initiated at altitudes from -2000 feet up to 15,000 feet. Maximum crosswind component for engine ground start is 30 knots. Maximum tailwind component for engine ground start is 20 knots. Engine Airstart: The preferred method of engine airstart is an automatic airstart. Manual starter assisted and windmill airstarts are also permitted. Takeoff Power: Minimum acceptable power for takeoff is shown in Airplane Flight Manual I Performance I Field Length Limited Performance I Takeoff Performance. Takeoff in the Alternate Control (LP) Mode is prohibited. Static Ground Run: Static operation above idle is limited to a crosswind component of less than 25 knots and/or a tailwind component of less than 20 knots. Figure 1.Powerplant General Arrangement LP COMPRESSOR Bl.ADES LPCOMPRESSOR ROTOR Bl.ADES CASEASSEMll..Y AOCE.S90RY GEARSOX TIL.-001118D 2A-71-20: Nacelle Arrangement 1. General Description: The engine nacelle assembly (see Figure 2. Nacelle Components) is an aerodynamic enclosure for the enginethat ducts fan stage airaround and past the engine core (to provide engine thrust) and cools the combustion section and engine exhaust gases. Each nacelle houses the engine fire detection loops and provides the mounting surface for the engine thrust reversers. The nacelles are composed of cowlings and doors that may be opened to facilitate engine maintenance and servicing. Each nacelle includes the following components: Inlet Cowl Upper and Lower Cowl Doors Fixed Cowl Structure Fire Detection I Protection System Note Nacelle components are not interchangeable between left and right engines. Description of Subsystems, Units and Components: Inlet Cowl: The forward section of the engine inlet cowl is manufactured of aluminum alloy (primary assembly) mounted to an aluminum bulkhead. This D-shaped structure provides a smooth contour to the front edge of the inlet cowl. In this hollow D section there is a titanium spray ring which is attached to the forward bulkhead. Warm air from the 5th stage HP compressor is directed through this ring. See 2A-30-30: Cowl Anti-Ice System for a discussion of the cowl anti-icing system. Upper and Lower Cowl Doors: (See Figure 3. Upper and Lower Engine Cowl Doors.) General: The upper cowl is made from carbon composite and provides protection to the upper half of the engine. It is installed between the aft edge of the inlet cowl and the forward edge of the thrust reverser. Along the inboard edge of the cowl there are two hinges and three hook receivers which attach it to the fixed cowl.The cowl opens on the hinges to give access to the upper engine components. The cowl is kept closed with five latches which are installed along the mating edges of the upper and lower cowls. There are door restraint latches on the forward and aft edges of the upper cowl. These prevent accidental movement of the upper cowl to the open position when the lower cowl is open.When the upper cowl is opened or closed, the rate of movement is controlled by two damper hold-open rods. The hold-open rods form part of the damper rods. The cowl is held open with these two rods, which are attached to its inner surface and the inlet are of the Thrust Reverser Unit (TRU). There is also a device on the forward edge of the upper cowl to ensure the cowl closes in the correct position.As the cowl closes, the device engages with a receptacle on the inlet cowl and aligns the upper cowl correctly. The lower cowl is also made of carbon composite and gives protection to the lower half of the engine. It is installed between the aft edge of the inlet cowl and the forward edge of the thrust reverser. Along the inboard edge of the cowl there are two hinges and three hook receivers which attach it to the fixed cowl.The cowl opens on the hinges to give access to the lower engine components. An electrical harness is connected to microswitches at the hinges to give an indication if the door is not closed correctly. The cowl is kept closed with fivelatches which are installed along the mating edges of the upper and lower cowls. When the IO'Ner cowl is opened or dosed, the rate of movement is controlled by two dampening hold-open rods. The cowl is also held open with these hold-open rods, which are attached to its inner surface and the inlet I TRU. When the cowl is held open, personnel can sit in the cowl door to do maintenance tasks. There is also a device on the forward edge of the lower cowl to ensure the cowl doses in the correct position. As the cowl doses, the device engages with a receptacle on theinlet cowl andaligns the lower cowl correctly. The lower cowl has an aluminum draindish, which lets unwanted fuel and oil drain overboard.On the left lower cowl and right hand apron, there is a small door which gives access to the oillevel sight glass. - -C-a-ut-io-n- - AIRCRAFT APU HOT EXHAUST GASES WILL DAMAGE THE RIGHT HAND ENGINE LOWER COWL DOOR IF THE APU IS OPERATED WITH THIS COWL DOOR OPEN. (a) Opening and Closing of Upper and Lower Cowl Doors: Note It is recommended that the cowl doors opening I closing procedures are carried out by two people. Note The fan cowl doors have mechanical dampers that are permanently attached to all the doors to assist in opening and dosing. However, these dampers should notbe reliedonwithout supporting the weight of the doors. Note Both doors must be supported by the front and rear hold-open rods when opened. Note The upper fan cowl door cannot beopened without the lower fan cowl door being opened fully. Note The lower doors can be used as a seat to aid working on the lower inboard area of the engine, but only when supported by hold-open struts. The door is designed to support two maintenance personnelwith a toolbox (maximumweight of 400 pounds). On the inboard side, each door is attached to the fixed cowl by two hinges and three hooks. On the outboard side, the doors align with each one another and are fastened together by five latches. The doors are unique to their particular left or right hand installations and therefore, are not interchangeable. Both the upper and lower doors are of carbon fiber composite construction and have some common features such as two dampening hold open rods, two opening dampers, hinges and latches. The upper door also incorporates safety latches to prevent the upper door opening in highwind conditions when the lower door is opened. The fan case, bypass duct mounted accessories and gearbox can be accessed by opening both of the cowl doors. The followingbriefly describes howto open and close the cowl doors. For a detailed procedure, refer to the Aircraft Maintenance Manual (AMM). Note The door latches are numbered 1to 5, No. 1at the front. Follow all safety requirements. Release the tension on all five latches, in the following sequence: 15 2 4 3 Manually support the weight of the lower door and disengage all five latches Unlatch the upper cowl door restraint latches Open the upper cowl door and support with both hold-open struts Ensure the mechanically-damped hold-open rods are locked before enteringthelower fan cowl door. VVhen closing the doors, ensure the latches are closed in the reverse sequence: 3 4 2 5 1 Cowl Access Panels and Doors: The cowl access panels and doors (see Figure 4. Nacelle Access Doors, Drains and Exhausts) allow access to various system components for maintenance, ventilation air for cooling I vapor removal and venting of air I gas exhaust overboard. Hinged access doors allow quick and easy access to the Thermal Anti-Ice (TAl) valve and Starter Air Valve (SAV) (both are considered pressure relief doors) and the oillevel sight gage. Elimination of fluid accumulation is provided via holes along the bottom of the cowl. Fuelflow transmitter access for the left engine is through a fixed panel built into the fixed cowl structure above the pylon. On the right engine, access is obtained by opening the cowl door. Components associated with the Thrust Reverser (TR) system are located on the exhaust unit assembly and are accessible through removable panels located on the top, bottom and outboard sides of the thrust reverser. (One exception is the inboard primary lock that is located under an access panel on top of the pylon.) Fixed Cowl Structure: The fD<ed cowl acts as a support for the cowl doors and as a continuation of the nacelle external surface between the pylon and the upper and lower cowl doors.The fD<ed cowl mounts against the outboard face of the pylon and is not interchangeable between the left and right nacelles. The forward and aft engine mounts, the thrust strut and various engine systems go through the fixed cowl to the airaaft. The forward engine mount is contained in a titanium firebox which is attached to the inner surface of the fixed cowl. There is a seal on the firebox edges which touches the intermediate case. The aft engine mount and the thrust strut go through fireproof silicon rubber boots which are attached to the fD<ed cowl. Fireproof seals also provide protection to the bleed air duct, the precooler air duct and the generator cables. There are various bulkhead connectors for fuel, remote oil fill and fire extinguishing systems. The bulkhead also incorporates isolated panels for hydraulic and electrical connectors. On the right fixed cowl only, a small door allows access to the oil level sight glass and oilfilter. Fire Detection I Protection System: (See Figure 5. Engine Fire Zones and Figure 6. Fire Extinguishing Layout.) Note For additional information on the fire protection system and related components, see 2A-26-00 2A-26-00: Fire Protection. Fire Zones: The BR725 engine is comprised of the following two Fire Zones: Zone 1(Accessories): Zone 1is the annular space extending radially from the engine Bypass Duct (BPD) to the circumference formed by the fixed cowl I apron and the fan cowl doors and extends in the longitudinal directionfrom the aft bulkhead of theinlet cowl tothe forward bulkhead of the TRU. This zone contains the majority of engine accessories including: Fuel,oil and hydraulic lines Accessories gearbox Engine oil pump FADEC system Hydro-Mechanical Unit (HMU) Air Turbine Starter (ATS) OEM Provided Data Powerplant Revision 13 20233-23 2A-71-00: B of 22 Starter Air Valve (SAV) and ducting HP Stage 5 and 8 bleed valves and ducting Cowl Anti-ice valve and ducting 40 KVA Integrated Drive Generator (IDG) Electronic Engine Controller (EEC) Zone 2 (Core): Zone 2 is bounded in the radial direction by the engine casings and the core fairing access panels (which form the bypass duct inner surface) and in the axial directions, by the intercase, the splitter fairing (including splitter tray) and the aft firewall. Line Replaceable Units (LRUs) installed within Zone 2 include: Variable Stator Vane 0-JSV) Actuator (actuated by fuel servo pressure) Overspeed Shutoff Unit (OSU) Bleed Valve Solenoid Block (BVSB) Fuel and oillines and HP compressor bleed off-takes Thermal Switches: Pylon heat sensing thermal switches, with a set point of 250°F are installed at the following four locations in both left and right hand pylons: Adjacent to the rear engine mount links and the precooler inlet fan air connection On the rib immediately downstream of the precooler On the next aft rib, immediately downstream of the fan air valve Behind the precooler exhaust duct, in the vicinity of the AGB breather duct aft flexible boot If any one of the switches detect an overheat condition, a 11;Iit'$j1 t::mi (warning) CAS message will be displayed. The associated engine bleed air supply and Environmental Control System (ECS) pack may be isolated to determine if the overtemperature condition is the result of a bleed air leak. Conversely, a pylon overheat condition combined with a powerplant overheat I fire condition may be the result of a combustor case bum-through event requiring an aircrew-commanded engine shutdown. Fire Seals: The fire seals are made of fireproof flexible-rubber material. Most of the fire seals are installed to components that go through the fixed cowl to the airframe. These indude the forward and aft engine mounts, the thrust strut and LP and HP air ducts. The firebox is attached to the inner surface of the fixed cowl and contains the engineforward mount-beam. There is an opening in the rear face of the firebox which has a short metal circular duct that points rearwards. The front end of the thrust strut goes through the duct into the firebox for connection to the forward mount. A silicon rubber boot seals this interface and is held with one damp on the duct and one clamp on the thrust strut. The other end of the thrust strut goes through an opening in the fixed cowl which is also sealed with a silicon rubber boot. This boot is attached to the fixed cowl with bolts and a clamp holds it to the thrust strut. The opening in the fixed cowl for the engine aft mount is also sealed with a silicon rubber boot. This boot has two openings in the shape of short sleeves. Each of these sleeves is installed on one of the links of the aft mount and is held with a clamp. The boot also has a flange which is attached to the fixed cowl with bolts. At the rear of the fixed cowl there is a silicon rubber boot which includes a retaining strip. The boot is attached to the ECS air duct in the pylon with a clamp. The strip is attached to the fixed cowl with bolts to hold the boot in position and seal the opening. The precooler air duct, which supplies fan airthrough the fixed cowl, also goes through a silicon rubber boot. This is attached to the fixed cowl with bolts to hold the boot in position and seal the opening. A damp holds the boot to the duct in the pylon. The function of the fixed cowling fire seals is to preventthe flow of fire and provide component protection at the fixed cowling penetration points. Most of the fire seals are attached to components that penetrate the fixed cowlingto the airframe. These indudetheforward and aft engine mount areas, the thrust andjury struts, precooler duct and the ECS dud. Controls and Indications: Crew Alerting System (CAS) Messages: The following CAS messages are associated with the nacelle: Area Monitored CAS Message Pylon Area IIii m; :{warning) Engine Access [Left Engine] Engine Access [Right Engine] External Air External Power Forward Cowl [Left Engine] Forward Cowl [Right Engine] Fuel Drain Valve [Left Wing] Fuel Drain Valve [Right Wing] Fuel Hopper Drain [Left Wing] Fuel Hopper Drain [Right Wing] Fuel Service Ldg Gear Maintenance Nose Wheel Well Oxygen Service Radome Security Tail Compartment waste Service water Service Wheel Well [Left Main Gear] Wheel Well [Right Main Gear] fi§ti$1•$ {advisory) Limitations: Flight Manual Limitations: There are no limitations established for the nacelle at the time of this writing. Other Limitations: Lower Cowl Door Weight Limit: The lower cowl door, when supported by the hold open struts, has a maximum weight capacity of 400 pounds (i.e., two maintenance personnel and a toolbox). Maximum Wind Velocity (When Opening Cowl Doors): The maximum wind speed for opening cowl doors is 13 knots (15 miles per hour). Maximum Wind Velocity (With Cowl Doors Open and Locked): Cowl doors are designed to withstand wind speeds of up to 60 knots (69 miles-per-hour), in any direction, when proper1y secured (front and rear dampener hold-open rods). Figure 2. Nacelle Components UPPER COWi.DOOR i IN.ETCOWL Tll.--001453 Figure 3. Upper and Lower Engine Cowl Doors UPPER COWL DOOR LOWER COWL DOOR DETAIL A TIL-002315 Figure 4. Nacelle Access Doors,Drains and Exhausts LEFT 1)ENGINE OUTBD --FWD_j STARTER.AIR VALVE (SAV)ACCESS THERMAL ANTICE(TAI) ACCEaa VENT EXHAIJST RIGHT (Na.2) ENGINE TIL-002311 Figure 5. Engine Fire Zones ZONE 1 This zone is annular space extending radially from the engine bypass duct to the circumference formed by the fixed cowl apron and fan cowl doors, and extends in a longitudinal direction from the aft bulkhead of the inlet cowl to the forward bulkhead of the thrust reverser unit. ZONE 1(ACCESSORIES) ZONE2 This zone contains the majority of engine accessories including: Fuel, oil end hydraulic lines Accessories gearbox Engine oil pump FullAuthority Digital Engine Control (FADEC) system Hydro-Mechanical Unit (HMU) Air Turbine Starter (ATS) Starter Air Valve (SAV) and ducting HP Stage 5 and 8 bleed valves end ducting Cowl Anti-Ice Valve (CAV) end ducting 40Kva Integrated Drive Generator (IDG) Electronic Engine Controller (EEC) ZONE 2 (CORE FIRE ZONE) TIL-002307 Figura 6. Fire Extinguishing Layout TIL-008476A 2A-71-30: Mechanical Accessories GeneralDescription: In addition to furnishing thrust to power the aircraft, aircraft engine operation provides an energy source for other aircraft and engine systems. High-pressure air at elevated temperatures generated by the engine compressor section is used to supply pneumatic power to the aircraft air conditioning and pressurization system, provide a means to prevent ice formation onthe aircraft wings and engine air intake cowl andfurnishes energy to operate the air-driven engine starter during cross-bleed starts with the pneumatic supply manifold isolation valve open.The pressure levels of air withinthe engine compressor can be reduced to ensure engine operational stability, prevent engine power surges and protect the engine against flameout. The rotational energy of each engine powers a gearbox that supplies the motive force for operating the hydraulic pump, an electrical generator, the engine fuel pump and oil pump and the dedicated generator of the Full Authority Digital Engine Control (FADEC). Description of Subsystems, Units and Components: Engine Pneumatic Bleed System: (See Figure 7. Bleeds System Simplified Block Diagram and Figure 8. Cabin Air System -Component Locations.) High-pressure engine compressor air at elevated temperatures is supplied to aircraft systems through a common duct connected to valves located at the 5th and 8th stage of the engine High-Pressure (HP) compressor. At normal power settings, the pressure and temperature of the air drawn from the 5th stage ofthe HP compressor air is sufficient to meet system requirements. If the engine is operating alow power settings as during a prolonged descent, air of increased temperatureand pressurewill beextracted fromthe 8th HP compressor stage to satisfy requirements.A check valve in the common duct prevents 81h stage airfrom entering into the 5th stage of the compressor and disrupting airflow through the engine. The operation of the 5th stage and 8th stage bleed valves is regulated by the Bleed Air Controller (BAC) of each engine. The BAC also maintains the temperature of the engine bleed air supply at a constant level by operating the bleed air precooler. The precooler is an air-to-air heat exchanger that uses cool ambient air extracted from the engineair inlet at the Low-Pressure (LP) fan stage. The fan stage air circulates within the interior of the precooler to reduce the temperature of the 5th stage and 8111 stage bleed air that passes through the precooler. The BAC opens and closes the supply valve from the engine fan stage to maintain engine bleed air at 400°F for normal operations. If higher temperature air is required for wing anti-icing or if an engine fails and cannot supply bleed air, the BAC increases the regulated temperature of the air supply to 500°F by passingless fan stage air through the precooler. An independent 5th stage bleed valve supplies warm air to the engine intake cowling to prevent the formation of ice. The bleed valve is controlled by the L COWL and R COVIii... anti-ice switches on the cockpit overhead panel. The switches may be used to electrically select the bleed valve open to provide ice protection or to enable the aircraft ice detectors to control the operation of the valve. Additional ice protection for the engine is provided mechanically by the rubber tip on the spinner of the fan stage compressor. The spinner tip is made of a soft elastic rubber compound designed to distort at the high centrifugal forces generated by engine rotation in order to dispel any ice buildup. A complete description of the systems powered by engine compressor air is found in 2A-21-00: 2A-21-00: Air Conditioning, 2A-30-00: 2A-30-00: Ice and Rain Protection, and 2A-36-00: 2A-36-00: Pneumatics. Three additional air bleed valves located on the 5111 stage of the HP compressor operate in conjunction with an additional 8th stage valve to modulate engine performance. The valves are referred to as engine handling bleed valves. The operation of all four valves is controlled by the FADEC. During engine starting, the bleed valves are open to promote engine acceleration. The FADEC doses the valves sequentially as engine rpm inaeases to a normal setting of 100%. The FADEC will also selectively open the bleed valves if an engine surge is detected or if water (rain) is sensed enteringthe engine intake. Note If indement weather is detected, continuous ignition (CONT IGN) is automatically selected ON by the FADEC. Engine Accessory Gearbox: The rotationalforce of the enginesis usedto provide the mechanical drive for aircraft system components mounted on the accessory gearbox. The gearbox is attached to the engine exterior and connected to the HP compressor through a driveshaft. The gearbox reduces engine rpm to a lower speed in order to power the following components: Integrated Drive Generator (IDG) Fuel Pump and Metering Unit OilPump Hydraulic Pump FADEC Generator The accessory gearbox also provides mounting and mechanical connection to the engine for the pneumatically-driven engine starter. Controls and Indications: The engine mechanical accessories have no controls independent of the powered systems. See the following sections for specific controls and indications: 2A-21-00: 2A-21-00: Air Conditioning 2A-30-00: 2A-30-00: Ice and Rain Protection 2A-36-00: 2A-36-00: Pneumatics 2A-80-10: Engine Starting System Limitations: There are no limitations established for the mechanical accessories at the time of this writing. Figure 7. Bleeds System Simplified Block Diagram --- I 3 ,.,.,_. F""' - -- = - -1= = = - - - - .J BtEm - -r f11-- - -- _-:-= - == i--:b""' I ,.,.,_. I -- - 3 ""' TIL-001638A Figure 8. CabinAir System -Component Locations FAN AIR OFFTAKE APRON INTERFACE STAGE S OFFTAKE AIR TURBINE STARTER DUCT ANTl ICE VALVE DUCT AIR STARTER VALVE HIGH PRESSURE (8TH STAGE) SHUTOFF VALVE TIL-002316