PKSC 8220 Exam 1 Slides PDF: Green Chemistry and Sustainable Materials
Document Details
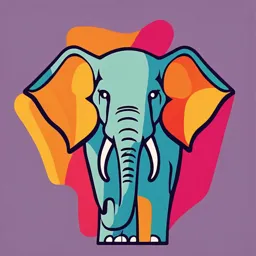
Uploaded by LoyalAntigorite9220
Clemson University
Tags
Related
Summary
These slides cover advanced methods in sustainable materials, focusing on green chemistry principles, metrics, and renewable raw materials. The lectures discuss waste prevention, efficiency, and the 12 principles of green chemistry, along with examples and case studies. Topics include the E factor, atom economy, solvent selection, and the use of natural sources for material synthesis.
Full Transcript
Advanced Methods in Sustainable Materials Lecture 1: Green Chemistry and Metrics Historical Context of Green Chemistry 1970s the EPA is formed, primary concern is with monitoring pollutants using “end-of-pipe” analysis Polychlorinated biphenyls (PCBs), Ch...
Advanced Methods in Sustainable Materials Lecture 1: Green Chemistry and Metrics Historical Context of Green Chemistry 1970s the EPA is formed, primary concern is with monitoring pollutants using “end-of-pipe” analysis Polychlorinated biphenyls (PCBs), Chlorinated fluorocarbons (CFCs), and heavy metals Still considered a “soft science” U.S. Pollution Prevention Act of 1990 Beginning of pollution prevention, rather than monitoring and treatment Chemistry as the solution, rather than the problem “Green Chemistry” and “Minimum Impact Chemistry” used in 1991, described as “benign by design chemistry” With initiation of Green Chemistry Institute and Green Chemistry Challenge Award in mid 90’s, the term Green Chemistry became codified in the 12 Principles by Anastas and Warner in 1998. From: R. Sheldon. https://pubs.acs.org/doi/10.1021/acssuschemeng.7b03505 12 Principles of Green Chemistry by Anastas and Warner, 1998 1. It is better to prevent waste than to treat or clean up waste after it is formed. 2. Synthetic methods should be designed to maximize the incorporation of all materials used in the process into the final product. 3. Wherever practicable, synthetic methodologies should be designed to use and generate substances that possess little or no toxicity to human health and the environment. 4. Chemical products should be designed to preserve efficiency of function while reducing toxicity. 5. The use of auxiliary substances (e.g. solvents, separation agents, etc) should be made unnecessary wherever possible and, innocuous when used. 6. Energy requirements should be recognized for their environmental and economic impacts and should be minimized. Synthetic methods should be conducted at ambient temperature and pressure. 7. A raw material of feedstock should be renewable rather depleting wherever technically and economically practicable. 8. Unnecessary derivatization (blocking group, protection/deprotection, temporary modification of physical/chemical processes) should be avoided whenever possible. 9. Catalytic reagents (as selective as possible) are superior to stoichiometric reagents. 10.Chemical products should be designed so that at the end of their function they do not persist in the environment and break down into innocuous degradation products. 11.Analytical methodologies need to be further developed to allow for real-time, in-process monitoring and control prior to the formation of hazardous substances. 12.Substances and the form of a substance used in a chemical process should be chosen so as to minimize the potential for chemical accidents, including releases, explosions and fires. From: https://www.sheldon.nl/Principles.aspx. P. T. Anastas and J. C. Warner, Green Chemistry ; Theory and Practice, Oxford University Press, Oxford, 1998. Summarized 12 Principles 1. Waste prevention not remediation 7. Renewable rather than depleting raw material 2. Atom efficiency 8. Shorter synthesis (avoid derivatization) 3. Less hazardous/toxic materials 9. Catalytic rather than stoichiometric reagents 4. Safer products by design 10. Design products for degradation 5. Innocuous solvents and auxiliaries 11. Analytical methods for pollution prevention 6. Energy efficient by design 12. Inherently safer processes R. Sheldon, https://pubs.acs.org/doi/10.1021/acssuschemeng.7b03505 Origins of Green Chemistry Roger Sheldon (www.sheldon.nl) is a recognized authority on Green Chemistry and widely known for developing the E factor concept for assessing the environmental impact of chemical processes. He is currently Distinguished Professor of Biocatalysis Engineering at the University of the Witwatersrand (SA). He authored several books on catalysis, more than 460 papers, and 55 granted patents. He was Co-Chair of the 1999 Gordon Research Conference on Green Chemistry. Among other awards, he was a co- recipient of a Presidential Green Chemistry Challenge Award in 2006 and received the RSC 2010 Green Chemistry Award and the Biocat2010 lifetime achievement award for his important and lasting contributions to biocatalysis. He was elected a Fellow of the Royal Society in 2015. https://pubs.acs.org/doi/10.1021/acssuschemeng.7b03505 Example: Pharmaceutical Synthesis Initial metrics for the efficiency of reactions relied upon the ATOM ECOMONY, defined as molecular weight of the product / molecular weight of reactants. Issues with Atom Economy (AE) Doesn’t account for actual amounts used – AE predicts 20kg of waste and 40 kg is actually produced TNT is highly explosive and dangerous Chromium is a cancer- causing reagent Introduction of the “E” factor E = Waste Mass / Product Mass Table 1. E Factors in the Chemical Industry Industry Sector Tonnage E Factor (kg waste/kg product) Oil refining 106–108 100 What is included as waste? Waste water / solvents? Initial methods considered 10% solvent loss, did not consider the waste-water that was generated AE vs. E Atom Economy E Factor Can be calculated without Uses actual amount of waste experiments – very useful generated preliminary survey Does not need to monitor individual steps, just total Assumes exact stoichiometric amount of waste and product ratios of reactants and products Can be calculated for single Does not consider solvents and process or entire manufacturing auxiliary chemicals site Ideal value is 0. No waste. Simple (sEF) and Complete (cEF) E Factors Because many solvents are recycled and waste-water is often reused, it is sometime difficult to determine the exact amount of waste produced. sEF does not consider water or solvents in calculation cEF includes all solvents and water with no recycling consideration Real E Factor will reside somewhere between these two Other Sustainability Metrics either relying on E factor or Atom Economy Boundary Conditions for E Factor It is easy to improve E factors by purchasing a chemical produced off-site Initial E Factors were simply a “gate-to-gate” calculation Need to define starting point as “commodity-type, commercially available raw material” Importance of including all steps in manufacturing process Chemical (1) was initially used as a starting point to determine an E factor of 6.4 However, (1) is also a manufactured chemical, including its steps brings E factor to 13.8. Class Exercise Calculate the following for your own research project: 1. E Factor 2. Atom Economy 3. PMI 4. MP 5. CE Quantifying Toxicity How can the toxicity / benign nature of chemicals be introduced with E factor or AE? Environmental Quotient: “EQ” Q Values given for chemicals from 1 – 1000 Salt would have a value of “1” where heavy metals may be 100 – 1000 Scores take into consideration safety, health and environmental factors EATOS Example: Environmental Assessment Tool for Organic Synthesis (EATOS) Downloadable at: http://www.metzger.chemie.uni-oldenburg.de/eatos/english.htm Uses Mass Index and E Factor to quantify efficiency Mass index S−1=Σ Raw materials [kg]/Product [kg] Environmental factor E=Σ Waste [kg]/Product [kg] Secondly, applies Specific Potential Environmental Impact (PEI) value to each chemical used (range from 1-10) Environmental Impact (EI) of reactants and products are assessed Eissen and Metzger: https://chemistry-europe.onlinelibrary.wiley.com/doi/full/10.1002/1521-3765(20020816)8:16%3C3580::AID-CHEM3580%3E3.0.CO;2- J?getft_integrator=acs&utm_source=acs S-1 = Raw material (kg) / Product (kg) Example EATOS Calculation E = Waste (kg) / Product (kg) 4 Different pathways to the same product are analyzed At first glance, wouldn’t (d) be most efficient? EATOS result shows path (a) requires 39 kg of raw materials (S-1 ) and 38 kg of waste (E factor) to produce 1 kg of product Path (c) has values of 3 for (S-1 ) and 2 for (E) respectively. Potential Environmental Impact (PEI) Reaction a,b,d have 50% of impacts due to solvent used Reaction “c” is a solventless reaction Points to importance of solvents used during synthesis Solvents in Green Chemistry Issues with Using Solvents: Often used in large excess (> 10X mass of actual product) Toxicity to human health Toxicity to environment Many evaporate at low temperatures, contaminating atmosphere Difficulty separating from water Difficulty recycling in manufacturing system GlaskoSmithKline Solvent Selection Tool Measures solvents on a 1-10 scale based on the following factors: 1. Incineration score: most waste solvents are incinerated to destroy toxic compounds. Measurement made on toxic emissions and amount of energy needed for incineration (water miscibility) 2. Recycling score: How easily can it be separated and dried from water? Explosion and safety also considered. 3. Bio-treatment score: how well can the solvent be treated in aeration tanks, how much is released to air, how easily does the solvent enter aqueous systems GlaskoSmithKline Solvent Selection Tool 4. Volatile Organic Carbon score: how easily can the solvent be lost / spilled/ evaporate to environment 5. Environmental Impact: a. Air: Photochemical ozone creation potential b. Aqueous: toxicity against aquatic species, chronic toxicity, biodegradation 6. Health: a. Exposure potential: occupational exposure limits b. Health hazard score: uses Global Harmonized System (GHS) Hazard and Precautionary risk phrases GHS Phrases Decision Tree for Health Hazards Genetic defects, cancerous, damage to unborn child or fertility is given lowest rating (1-4) Next lowest ratings given to fatal solvents (4-10) Best ratings given to “harmful” statements and those with no statements (7-10) Advanced Methods in Sustainable Materials Lecture 2: Harnessing Renewable Raw Materials Natural Sources of Material Synthesis Castor Bean Jatropha Seed Mahua Seed Karanja Seed Perilla Seed Starch Animal Fats Non-Edible Sources for Biopolymers Animal Processing Corn Stover Chitosan Tannins / Wood Resins Polyhydroxyalkonates Crustacean Shells Tree Bark Bacteria Cellulose / Lignin 2 CO2 Capture – Algae / Seaweed Inedible Vegetable Oils Microcrystalline Cellulose Castor, Perilla Starch-based Materials Carbohydrate-based Polymers Mycelium, Mushroom- based Materials Agriculture By-products: Industrial By-products: Lignin, Shells, Hulls, Bagasse, Stover Distiller Grains, Glycerol https://www.ecovative.com/airmycelium/ Department of Energy Bioproducts and Carbon Reduction Plan ▪ Department of energy sets goal to displace 90% of current plastics with biobased or recyclable by design polymers ▪ Paris climate agreement: Need a 43% reduction in emissions by 2030 and net zero by 2050 to curb 1.5 degree increase in global warming Typical Petroleum Refinery / Chemical Production Process ▪ Petroleum has been so successful as an industry due to the myriad of products created in Fractional Distillation Process ▪ In addition to oils, fuels, and asphalt, Naptha is further refined to Benzene, Toluene, and Xylene (BTX), which is the raw material for most chemicals used in the world today. ▪ To compete with the traditional petroleum-derived process, a similar refinery concept must be developed with biomass where “platform chemicals” (like BTX) are produced that can lead to other products and materials. http://www.lydenoil.com/lyden/fractional_distillation Vegetable Oils Have a triglyceride structure Can be broken down by transesterification Chain liberated from the triglyceride are referred to as fatty acids Fatty acids have “unsaturated” groups that can be manipulated Each natural oil source has different content of unsaturated groups Unsaturated groups used to introduce different functionality to fatty acids Vegetable Oil Derived Polymers Veg. Oil Description Ref. Tropical deciduous tree, seeds used in skin care, Mahua oil detergents and soaps Non Edible Temperate shrub / tree used in lubricants, oils, fuels, Castor oil paints, inks, polymers Drought resistant shrub / tree used for soap, diesel fuel, Jatropha oil traditional medicine Karanja oil Local Indian tree with few value added applications Perilla oil Traditional Chinese plant used in medicine and therapies. Commercial Bio-epoxies exist, high omega-3 fatty acid Linseed oil nutritional value Fourth highest worldwide production of vegetable oil, Sunflower oil mainly used for cooking Cotton seed oil Used for animal fodder, cooking oil, lubricant Edible One of the cheapest vegetable oils with many uses in food Corn oil chemistry and ethanol production Used in biodiesel production, cooking oil, and 2nd highest Canola oil world production of protein meal Largest production volume, commercial Bio-epoxies exist Soybean oil yet exhibit low mechanical and thermal properties [25,27] 7 What is transesterification? A reaction where one oxygenated compound replaces another at the site of an ester group. https://www.e-education.psu.edu/egee439/node/684 Having a familiar with these groups (especially those in blue and green) will be very helpful as we discuss different types of polymers and reactions in this course. at Saturated Monounsaturated Polyunsaturated Unsaturated Content Animal Fats Lard % 40.8 % 43.8 % 9.6 Duck Fat 33.2 49.3 12.9 Butter 54.0 19.8 2.6 Vegetable oils Coconut oil 85.2 6.6 1.7 Palm oil 45.3 41.6 8.3 Cottonseed oil 25.5 21.3 48.1 Wheat Germ oil 18.8 15.9 60.7 Soya oil 14.5 3.2 56.5 Olive oil 14.0 69.7 11.2 Corn oil 12.7 24.7 57.8 Grapeseed oil 11.0 16.0 72.0 Sunflower oil 11.9 20.2 63.0 Safflower oil 10.2 12.6 72.1 Remember these: Oleic: 1 Double bond Hemp oil 10.0 15.0 75.0 Linoleic: 2 Double Bonds Canola/Rapeseed Oil 5.3 64.3 24.8 Linolenic: 3 Double bonds Rice Bran oil 20.0 47.0 33.0 Avocado oil 20.0 65.4 15.5 Walnut oil 15.0 1.0 84.0 https://www.sciencedirect.com/science/article/pii/S0926669018305569 https://savantes.org/news-and-articles/cooking-and-using-olive-oil/72-fatty-acid-ratios Epoxidation Reactions The goal of epoxidation reactions is normally to achieve the highest epoxy content without Epoxidized Soybean Oil is not an industrially side reactions that lead to “ring opening” produced chemical in the polymer industry Ring opening lowers epoxy content and introduces other chemical groups https://link.springer.com/article/10.1007/s13233-015-3154-6?fromPaywallRec=false https://www.sciencedirect.com/science/article/pii/S0926669018305569 Other reactions with epoxies The epoxy group is often reacted with another compound to create monomers for different kinds of polymer synthesis Amines can be used for curing agents, polyamides, polyimines Carboxylic acids can be used for esters or polyamides Hydroxyl groups can be used in polyurethanes, esters, and other polymers Industrial applications: Soap and Biodiesel Manufacturing of Soap: The Saponification Reaction Manufacturing of Biodiesel: FAME = Fatty Acid Methyl Ester A major industrial source of glycerol (or glycerin) is the transesterification of triglycerides Industrial applications: Castor Oil and polymers The 10-carbon chain of sebacic acid comes from castor oil and is used to make a series of polyamides such as PA 11, PA 10,10, 6,10 etc. Biobased Polyamides from Casto Oil https://www.sciencedirect.com/science/article/abs/pii/S2589597423002277 Industrial applications: Polyurethane Foams Standard method of producing Polyurethane Diisocyanate Polyol Polyurethane Suspected Carcinogen (Cat. 2A) Ford Motor Co. initially innovated the soy- Acute Toxicity (Cat. 2) oil polyurethane by replacing up to 30% of the polyol portion of the polymer Respiratory Sensitizer (Cat. 1) Eye/Skin Irritant (Cat. 2) Sometimes you want ring opening…. Formic Acid Sulfuric Acid Sulfuric Acid Hydrogen Peroxide Ethylene Glycol Avg. OH content [mg Source Avg. Yield (%) KOH/g] Soybean Polyol 77.9 246.8 Cottonseed Oil - 15.9 Cottonseed Polyol 82.9 202.8 Algae Oil - 3.7 Algae Polyol 82.5 63.0 Distilled Pyrolyzed 66.4 111.9 Cottonseed Pyrolyzed 53.6 148.4 Cottonseed Polyol Pawar, M., Kadam, A., Yemul, O., Thamke, V., & Kodam, K. (2016). Biodegradable bioepoxy resins based on epoxidized natural oil (cottonseed & algae) cured with citric and tartaric acids through solution polymerization: A renewable approach. Industrial Crops and Products, 89, 434–447. Clemente, T. E., & Cahoon, E. B. (2009). Soybean oil: genetic approaches for modification of functionality and total content. Plant physiology, 151(3), 1030–1040. Skowyra, M., Falguera, V., Azman, N. A., Segovia, F., & Almajano, M. P. (2014). The Effect of Perilla frutescens Extract on the Oxidative Stability of Model Food Emulsions. Antioxidants (Basel, Switzerland), 3(1), 38–54. 17 Kousaalya, A. B., Beyene, S. D., Gopal, V., Ayalew, B., & Pilla, S. (2018). Green epoxy synthesized from Perilla frutescens: A study on epoxidation and oxirane cleavage kinetics of high-linolenic oil. Industrial Crops and Products, 123, 25–34 Research Applications: Cottonseed and Algae Oil 0% 10% 30% 50% 50% 50% Polyol Replacement Cottonseed Oil Polyol Replacement replacement with Algae Oil Polyol with raw oil Replacing the traditional polyol with the oil-based polyol created difficulties surrounding 1. Reactivity – different OH content and molecular structures and 2. Viscosity: thicker vegetable oil polyols made it difficult for the foam to rise to normal heights Measuring hydroxyl content The acetylation method for determining hydroxyl content is Acetylated described under ASTM E222 Acetic Anhydride Hydroxyl group Requires pyridine solvent and boiling for ~ 2hrs Measure the By seeing how Excess acetic acid is titrated to amount of this much of this is determine the amount of hydroxyl produced groups that were acetylated Other methods based on silylation of hydroxyl groups and using FTIR to integrate the peak at 1250 cm-1 can also be used. Example Calculation 20 grams of a vegetable oil polyol was added to 100 ml of a 1 M acetic acid solution in pyridine. The solution was boiled to acetylate the hydroxyl groups of the polyol and was subsequently titrated with 0.5 M sodium hydroxide. A blank solutions was also completed to establish a baseline. If the sample required 200 ml of sodium hydroxide to reach the endpoint and the blank required 15 ml, what is the concentration of hydroxyl groups in millimoles / g (mmol/g) ? - Concentration (mmol/g) = (A – B) x 0.5 / W - A = ml of titrated sample - B = ml of titrated blank - 0.5 = concentration of titrating agent - W = weight of sample added - OH Value is often presented in terms of mg KOH/g. To get this value, multiply concentration (in mmol/g, calculated above) by 56.1. This value is the equivalent amount of KOH needed to reach the same OH amount in your sample. Dimer Fatty Acids Dimer acids are formed from combining 2 fatty acids at unsaturated points in their chain Dimer diamines can be formed by converting the carboxylic acid group to an amine group Dimerized compounds give flexibility, elasticity, water resistance, adhesion, and toughness to polymers Can be added to replace a portion of more traditional reagents to increase flexibility of products Fun with Chemistry – creating Non- isocyanate polyurethanes Glycerol Carbonate Dimethylcarbonate Fatty acid Polyol 1,2-Diol Cyclocarbonate Using alternative chemistry to make polyurethanes without isocyanates Diamine Curing Agent Designing a Study Often times, a well-designed study will gain a higher impact journal than good results Good results, presented with poor figures and explanation, will most likely not gain high consideration It is important to remember that research is aimed at increasing knowledge of a previously unknown problem, system, or product Designing a well-thought-out study often provides more information than just presenting good results Describing the interesting scientific aspects can often make a paper much better Polyamide Precursor Design Diacid Sebacic Acid (SA) Adipic Acid (AA) Fatty Acid Dimer Diamine PR-SA PR-AA Diamine (PR) Tm = 92°C Tm = 100°C 100% Biobased Polyamide HMDA-SA HMDA-AA Precursors Hexamethylene (PA 6,10) (PA 6,6) Diamine (HMDA) Tm = 223°C Tm = 269°C HMDA50-SA HMDA25-AA 50% HMDA + 50% PR 25% HMDA + 75% PR Tm = 177°C Tm = 163 °C 1/13/2025 24 Properties targeted Bio-content Viscosity / melt-strength of polymers Low water adsorption Reactivity with other biobased fillers (lignin) Reaction with Lignin Plant-based Plastics 1/13/2025 26 Rheological advantage of lignin-derived PAs Polymers at 30% lignin loading show 3-5 order of magnitude increase in melt strength over traditional PA6,6 and PA6,12 Enhanced bead strength predicted for lignin-derived materials facilitating the use of modern thermal processing equipment. Traditional PAs suffer from low melt viscosity leading to difficulties in extrusion and thermoforming techniques 1/13/2025 27 Water Adsorption Sample Water Adsorption (wt%) PR-SA 0.51 ± 0.21 Biobased polyamides show low water adsorption addressing another PR-SA-30% Lignin 1.62 ± 0.23 important characteristic of nylons PA6,6 3.21 ± 0.30 High water adsorption PA6,12 1.53 ± 0.81 Low water adsorption Water Adsorption ASTM D570 Traditional Polyamides suffer high water adsorption at amide sites in polymer chain Additional H-bonding after ring opening reaction mitigates against water adsorption 1/13/2025 28 Mechanical Properties Mechanical properties of the new materials are not excellent However, a rational explanation of the results can be had based on the design of Ultimate Tensile Strength Strain at Break Modulus experiments Thus, new knowledge is Sample (MPa) (% Elongation) (MPa) given on this system PRSA-blank 11.2 ± 1.0 33.8 ±26.3 130.4 ± 30.1 PRSA-C.M. 12.4 ± 0.3 7.9 ± 1.1 262.1 ± 31.0 PRSA-15% 11.3 ± 0.6 26.7 ± 7.6 147.3 ± 16.2 using widely available PRSA-30% 13.2 ± 1.2 18.3 ± 10.1 184.4 ± 22.3 raw materials PRSA-30% C.M. 15.0 ± 1.5 6.1 ± 1.4 453.8 ± 83.0 Introduction to Lignocellulosic Biomass Lignocellulosic Biomass Is the Most Accessible and Abundant Source of Carbon on Earth33 15 – 25 % Lignin 20 – 35 % Hemicellulose 30-50 % Cellulose Cellulose Hemicellulose Linear polymer chains of D-glucopyranosyl Less ordered, branched polysaccharides with Carbohydrates suffer units stacked in parallel43 orders of magnitude fewer DOP.43,44 from poor processability, Most hydrophilic component with lowest solubility as well as poor Used in transparent films and coatings for thermal properties44 thermal and mechanical screens and packaging44 properties due to Crystalline structure restricts development Addition of high molecular weight plasticizers needed to create materials with sufficient structural rigidity.40 of thermoplastic materials44 toughness or flexibility44 30 Lignin Structure and Functionality Free ortho position on phenolic ring32 Aliphatic and phenolic hydroxyl groups32 Aromatic backbone providing structural strength and rigidity32 Β-O-4 linkage allows depolymerization33 31 Introduction to Lignin Lignin is considered a heterogeneous, crosslinked, natural polymer Contains the most amount of renewable aromatic carbon (carbon available in a ring) on earth Is the “glue” that holds together cellulose and hemicellulose, is what makes trunks and branches of trees strong Is very difficult to process and make available with the same kind of consistency as cellulose is for paper Different tree sources, different pulping techniques, different parts of the tree all produce different kinds of lignin Is very high molecular weight (~ 5000 – 10,000 g/mol), difficult to dissolve, slow to react, prone to side reactions Variation in Lignin Properties OH value Aliphatic Aromatic Total Mw Mn PDI C.A. Thiol (mg OH OH OH KOH/g) Softwood Kraft 6231 1232 6.10 2.17 3.49 0.31 0.48 6.33 355 Kraft, organosolv, and soda are S.D. (n=4) 1210 551 3.16 0.36 0.59 0.09 0.20 0.70 44 different pulping properties Hardwood Organosolv 6153 1273 4.93 2.46 3.12 0.47 6.04 339 Aliphatic OH refers to hydroxyl S.D. (n=3) 3291 651 1.74 1.59 0.80 0.25 1.33 74 groups on linear carbon chains Wheat / Grass Aromatic OH refers to hydroxyl 4183 679 8.63 1.43 3.36 0.98 5.76 323 Soda Lignin groups on an aromatic or ring - S.D. (n=3) 869 414 7.10 0.30 0.57 0.60 1.00 176 group Lignosulfates 68786 10124 7.26 -- -- -- -- -- S.D. (n=3) 19621 5239 1.61 -- -- -- -- -- Petroleum Derived Functionalization Reference Lignin Material? ? Diisocyanates ? Harmful Solvents ? Toxicity Profile of Diisocyanates7 Luo et al. 2018 Suspected Carcinogen Duong et al. 2014 (Cat. 2A) Pohjanletao et al. 2014 Acute Toxicity (Cat. 2) Bai-Liang Xue et al. 2014 Hayati et al. 2018 Respiratory Sensitizer (Cat. 1) Chung et al. 2012 Eye/Skin Irritant (Cat. 2) Laurichesse et al. 2014 Gomez-Fernandez et al. 2017 Hatakeyama et al. 2002 Cinelli et al. 2013 + Liu et al. 2013 Lee et al. 2015 Is there a green route to Oulame et al. 2015 polyurethane synthesis without the use of toxic diisocyanates? Chen et al. 2015 Lignin-derived Polyurethanes 34 How to create a Previous Approach by Salanti et al. lignin-based NIPU? NIPU = non-isocyanate PU Previous research showed an inability to produce a material capable of undergoing mechanical testing Research Gap: How can lignin be used for a high performing NIPU material? Hypothesis: Dimer diamines may provide flexibility and mitigate the brittle nature of lignin https://pubs.rsc.org/en/content/articlelanding/2017/ra/c7ra03416d New approach by Sternberg et al. The addition of the dimer diamine created a set of materials that demonstrated interesting properties: shape memory, foaming ability, decent tensile strength - However, the foam properties were only applicable to high density, rigid foams, almost 10X heavier than commercial materials. Non-isocyanate Polyurethane Foam 100% Biobased Foam Non-toxic Organic Carbonates ASTM 6866: Glycerol Carbonate Radiocarbon Analysis Unmodified Kraft Lignin Dimethyl Carbonate Pulping Vegetable Oil-based Woody Biomass Curing Agent Cellulose (30-50%) Lignin (15-35%) Hemicellulose (25-35%) Sternberg, J. & Pilla, S. Green Chem. 20, 6922–6935 (2020) Pilla, Srikanth; Sternberg J. Non-Isocyanate Polyurethanes from Biobased Polyols. USA; 63/034,584, 2020. Additional Biobased Source to Impart Flexibility Castor Oil Triglyceride Inedible Castor Beans – Used in Commercially Available Sebacic Acid from Castor Oil many cosmetic and medicinal applications Sebacic Cyclocarbonate Synthesized in our Lab Extended linear segments with Castor oil- based component The addition of the linear segments from castor oil modified the viscosity of the mixture allowing much higher rise heights of the foams, and Extended linear soft segments between rigid lignin centers increased their soft, flexible nature Decreased crosslinking Between Lignin through copolymerization of Sebacic CC and diamine How Does It Perform? Rigid Flexible Property Rigid PU Flexible PU Lignin-NIPU Lignin-NIPU Density (kg/m3) 60-100 200 30-100 60-70 Compression Strength 100 130 3-13 5-20 (kPa) Thermal Stability (T5%) 300 300 240-250 240 Burn Rate 8 mm/sec 0.55 mm/sec 1.2 mm/sec 0.71 mm/sec Where else can lignin be used? The easiest use for lignin is to add directly as a filler / crosslinking agent Lignin cannot be added in high concentrations due to its low compatibility with most polymer systems Two major schemes for “functionalizing” lignin: 1. Grafting from: to use lignin as the start of a new polymer chain 2. Grafting to: creating polymer chains outside of lignin and attaching after the fact Fractionating lignin to lower molecular weight Since lignin exists as a dispersion of different molecular weight fractions, solvent extraction is often used to concentrate a specific molecular weight range for different applications Lower molecular weight fractions will dissolve in select solvents while higher molecular weight fractions stay in the solid state The lower molecular weight fraction can be filtered off Can be expensive to employ industrially as a large portion of lignin goes unused. Now its your turn…. Presentations due Monday 11/20 Plan for 10 minutes Pick a renewable material: Vegetable oils, lignin, chitin, cellulose, starch, biocarbon, algae, others…. Outline: 1. Introduce the title, authors, and main idea 2. What research gap are they targeting? What has been done in the past and how is what they are doing new? 3. Describe the materials that are used and the synthetic scheme, what properties are they targeting? 4. Describe how the properties relate back to the materials they are using 5. Describe the downsides to their results, how does it compare to traditional materials and what future work needs to be done? Advanced Methods in Sustainable Materials Lecture 3: Renewable Materials Chitin and Chitosan Most widely occurring biopolymer after cellulose Compare with lignin? Found in crustaceans, insects, fungi Shrimp and crabs used most commercially, also lobster, crayfish, oysters Shells typically have 20-30% Chitin, although lobsters shells can be up to 70% 40-50% of Crustacean mass (ie. Shrimp, crabs, lobster) harvested for human consumption become waste (i.e shells), most thrown back into the ocean https://www.sciencedirect.com/science/article/pii/S0141813020351631 Chitin and Chitosan Structure Chitin is the naturally occurring substance in crustaceans and other sources Chitin is identified by the “acetyl” groups attached to the backbone Chitosan is formed by removing (partially) these acetyl groups to form free amine groups Amine groups are important for water solubility and other chemical properties https://www.frontiersin.org/journals/cellular-and-infection- microbiology/articles/10.3389/fcimb.2021.643953/full Deacetylation The most common characteristic to report about Chitosan is the extent of deacetylation – the removal of acetyl groups from Chitin Most commercial Chitosan has deacetylation values of 70-90% Most common method is use of sodium hydroxide (NaOH), although other methods exist The change in molecular weight is also important – Chitin ranges from 10’s kDa to 100’s kDa https://www.sciencedirect.com/science/article/pii/S0141813020351631 Chitosan Applications High degrees of deacetylation makes chitosan less flexible and transparent but also makes it more soluble in water – better at film formation Crosslinking agents are often added to create a polymer gel, dried to form a film Processing Solution casting is the most often used technique for creating materials for research, however, this technique is not applicable for commercial manufacturing More viable routes would include blending, or spray coating Interaction between the negative charges on chitin and positive charges on cellulose have been cited to provide positive interactions for barrier materials Film Production Process Combining Materials Materials for chitosan Casting and pectin films were combined using heat and Drying mechanical stirring Chitosan and pectin film solutions were cast onto leveled glass plates Films were left to dry in laboratory oven until reaching a moisture content of approximately 20% Hardiman, Mchugh, Cooksey Data Film Production Process Chitosan Film Pectin Film Hardiman, Mchugh, Cooksey Data Barrier properties of Chitosan The high degree of crystallinity of Chitosan makes it a good candidate for films designed for high barrier properties: Water, Oxygen, CO2 Water barrier properties highly depend on degree of deacetylation (DA) - low degree of DA typically have better water barrier properties due to hydrophilicity of amine group pH also affects the activity of the amine group and interaction with bacteria and water Main routes to improve barrier properties: 1. Combine with other materials (i.e. nanocellulose), 2. Coat in multiple layers, 3. Blend with other polymers, 4. Alignment of particles to create a more “tortuous path” Modeling barrier properties P, p are permeability coefficients of filler / polymer (L/W) is aspect ratio of filler Φ is volume fraction (concentration) of filler in polymer Higher aspect ratio, greater volume fraction linked to better barrier properties (Lower P/p) Addition of Chitosan to cellulose nanocrystals, nanoclay, metal oxide particles, and other cellulose materials have been combined by solution mixing, or blending to improve properties in either neat films or blends https://link.springer.com/article/10.1007/s42247-020-00147-5 Barrier properties of Films Water Vapor: 19 – 28,000 Oxygen: 0.2 – 18.5 https://topas.com/tech-center/performance-data/barrier-general/ Multilayer films Layer-by-layer assembly is most common application method Includes dipping, spraying, or spinning Improvement in properties seen on PLA and PET, normally 5-10 layers of chitosan applied Coating performance Water vapor: 1.2 – 74 Oxygen: 2 - 1157 Antimicrobial properties Films of chitosan can be edible, coating foods with a barrier to microbial attack Films limit oxygen permeation to food, lowering aerobic microorganisms' ability to thrive Positive charge at amine can open cell wall of bacteria, causing cell death Can form barrier around bacteria cells, limiting exchange of necessary nutrients Low molecular weight can enter cell nucleus and inhibit DNA translation of cells https://www.sciencedirect.com/science/article/pii/S1466856420302927 Spot on Lawn Results - Chitosan Film Sample Inhibition Additional Zone Inhibition Chitosan 8.58 mm Zone only Control 1.5% Chitosan 2% 8.80 mm Zone only Chitosan 9.57 mm Zone only 2.5% Chitosan 2.5% Hardiman, Mchugh, Cooksey Data Extruded PLA/Starch/Chitosan films 40/5 and 40/10 refer to 40% starch and 5 or 10% Chitosan Growth curves of microorganisms found in fresh meat slowed with composite films However, the mechanical properties also decreased Bie et al. https://www.sciencedirect.com/science/article/pii/S0144861713006875 Recyclability Chitosan-based coatings showed high re-pulpability with similar properties to first generation paper Image shows fibers washed in water (b) and acetic acid (c) FTIR (d) was used to monitor the amine peak at 1550 cm-1 to demonstrate the removal of chitosan coating Tensile strength (e) was similar among uncoating and coated samples after repulping https://www.sciencedirect.com/science/article/pii/S0141813022028951#:~:text=Full%2Dbiobased%20chitosan%2Dde rived%20coating,excellent%20recyclability%20but%20also%20biodegradability. Recyclability? Depending on their solubility in water, chitosan films could be recycled in general recycling stream Other methods include dissolution in sulfuric acid to regenerate films, or Fiber-based composites incorporation of recycled fibers in composites https://www.sciencedirect.com/science/article/pii/S0144861720304306?via%3Dihub https://www.sciencedirect.com/science/article/pii/S0950061817320135 Biodegradability Controlled aerobic composting at 58oC. 90% biodegradation needed to be considered “compostable” 70% cellulose biodegradation after 45 days to validate test Hardiman, Mchugh, Cooksey Data Plasticizers in polymer films Plasticizers are added to many polymers to enhance their toughness, processability, and elasticity Several ways of explaining how plasticizers work are described here The main point is that plasticizers enhance movement of the polymer chains, allowing them to be more flexible and elastic (i.e. adsorb more energy without fracture) Glycerol as plasticizer Traditional plasticizers are based on the use of phthalates and bisphenols which are endocrine disrupters and toxic Glycerol’s structure enables its use as plasticizer due to its hydroxyl groups that can disrupt hydrogen bonding in polymers, lessening the rigidity of polymer networks Glycerol is biobased and benign, satisfying the requirements of green chemistry Glycerol can be used in many hydrophilic polyesters and starches such as PLA, polyvinyl alcohol, cellulose acetate etc. Example of chitosan films and glycerol Chitosan Film - 1.5% Chitosan Material Amount Water 300 mL Acetic Acid 3 mL (1% v/v) Glycerol 1.80 mL (0.75% v/v) Chitosan 4.572 g (1.5 % w/v) Glycerol effect on properties Mechanical properties: Tensile strength is lowered, elongation at break is increased Thermal properties: Glass transition temperature is lowered, polymer chains move more freely Water Vapor Permeability: Glycerol is hydrophilic and adsorbs water from the air, increasing the plasticization effect but also leading to high permeability values Addition of plasticizers typically transition failure mechanisms away from brittle fracture towards ductile fracture Brittle vs. Ductile Materials Brittle materials show rapid onset of breaking point with little elongation, typically have smooth surfaces after fracture Ductile materials have significant elongation before break, fractured surfaces typically show rough fibrils of extended material Plasticizers facilitate the transition to ductile behavior by improving the mobility of polymer chains http://www.ltas-cm3.ulg.ac.be/FractureMechanics/overview_P3.html Glycerol in other polymer synthesis Glycerol is tri- functional, creating the ability for crosslinked and hyperbranched systems Other more typical condensation polymers such as polyesters and Polyurethanes are also possible Glycerol has a high hydroxyl value: 1823 mg KOH/g https://www.sciencedirect.com/science/article/pii/S1381514820304041 Biochar / activated carbon Highly porous carbon Agricultural Refuse materials made through high Shells / hulls Forestry Residue Manure temperature pyrolysis Pyrolysis is a technique that heats samples to high temperature (~ 500 – 1000oC) in the absence of oxygen The absence of oxygen results in release of volatile compounds and some carbon, creating pores throughout the Thermal Treatment structure Thermal / Chemical The enhanced porosity of the Treatment materials are able to adsorb a large range of compounds making them valuable in water purification, gas adsorption, and as electrode materials for electronic applications. Applications of Biochar Applied as a filler to both polyolefin and condensation polymers Increases impact resistance, flexural strength, tensile strength Can be used to create conductive polymers, and electromagnetic (EM) shielding materials EM shielding is achieved by the conductivity of the biochar, which either dissipates or reflects the unwanted radiation https://www.mdpi.com/2073-4360/14/12/2506# Important Properties of biochar Surface area and pore volume are measured through a surface area analzyer that uses adsorption of nitrogen on the surface of pores throughout the biochar structure Surface area is calculated using Brunauer-Emmett- Teller (BET) theory Surface area is described in m2/g, biochar is typically somewhere between 1 – 200 m2/g where as activated carbon can be up to 3000 m2/g Pores are categorized as Micro: < 2 nm Meso: 2 – 50 nm Macro: > 50 nm Point of zero charge (Pzc) is pH where there are an equal number of positive and negative charges on biochar Is important when used to adsorb toxin from water as charged molecules will be repelled Example Properties of Activated Carbons DFT DFT Vtotal BET Material Vmicro Vmeso+macro (cm³/g) pHPZC m²/g Type (cm³/g) (cm³/g) (P/Po=0.98) Calgon WPL 964 0.35 0.36 0.64 5.6 Coal Aqua Nuchar 1,703 0.32 0.95 1.48 6.5 Wood Calgon F400 1,070 0.29 0.07 0.54 7.8 Bituminous Coal Norit20B 918 0.30 0.06 0.45 9.5 Bituminous Coal S32 2,844 1.08 0.36 1.46 10.4 Soyhull Adsorption Performance of Heavy Metals Cost / commercial valuation Compression Force Deflection of Biochar Polyurethane Foams Density(kg/ C.S. at t=0s C.S. at % carbon % Difference m3 ) (KPa) t=60s(KPa) 0 60.35±4.94 9.87±0.21 7.52±0.2 76% 1 61.12±3.64 11.04±1.41 8.48±0.96 77% 5 61.63±2.23 10.81±0.43 8.35±0.14 77% 10 64.92±4.18 13.81±1.58 9.92±0.94 72% 20 76.99±13.53 32.47±6.24 21.65±4.25 67% Burn Rate of Biochar PU Foams % Burn rate After burn Cotton Ignited Observation carbon (mm/s) (s) (Y/N) Fully burned - Nothing 0 1.22 31.22 N left Fully burned - Nothing 1 1.23 19.97 N left Fully burned - Char 5 0.87 39.06 N remains Fully burned - Char 10 0.76 55.81 Y remains Fully burned - Char 20 0.61 71.77 N remains https://www.amade-tech.com/guide-on-ul94-horizontal-vertical-burning-flammability-test/ Polymer Synthesis "I am inclined to think that the development of polymerization is perhaps the biggest thing that chemistry has done, where it has had the biggest effect on everyday life” —Lord Todd, 1980 Ethylene Polyethylene CH = CH [–CH – CH –]n 2 2 Magic ? 2 2 Polymer Synthesis HISTORICAL CONTEXT My dear chap, give up your ideas on big molecules. There are no organic molecules with a molecular weight of more than 5000. Just clean up your products and they will crystallize and reveal themselves as low molecular weight compounds. —Advice given to Hermann Staudinger. Historical Context 1920 – STAUDINGER; The macromolecular hypothesis 1926 - CHARLES STINE; Initiates a program of fundamental research at du Pont, hires Carothers LATE 1920's - CAROTHERS; Set out to prove the existence of macromolecules by systematically building them from small molecules using well known chemistry Polymer Synthesis – Classification Carothers suggested that most polymers could be classified into two broad categories according to the mechanism of polymerization; Condensation Addition These categories were broadened to include Step-growth Chain-growth Why do Molecules React ? The whole question of sustainability is summed up in this graph. Why is that an overstatement? What role do catalysts play? How is energy generated in the real world? How does this graph depict that? What role does energy play in sustainability? Arrhenius Equation and Activation Energy Linear Form Thermodynamics of reactions are modeled by the Arrhenius equation. This equation allows for the determination of activation energy by plotting the linear form of the equation: ln k vs. 1/T Activation energy can even be calculated for melt transitions https://iopscience.iop.org/article/10.1088/1742-6596/1045/1/012040/pdf Types of Reactions Broader Category O O Named: Step Growth Condensation H2N–(CH2)6–NH2 + HO–C–(CH2)4–C–OH Polymers Nylon 6,6 Addition CH2 CH2 Polyethylene Broader Category Named: Chain Growth Polymers O Ring opening C Nylon 6 N H What is the difference between Step-growth and Chain-growth polymerization reactions? Step growth polymerization Step growth polymerization occurs by the formation of dimes, trimers and oligomers that then combine to form higher molecular weight species Features 1-Stoichiometric equivalence of functional groups 2.-Growth occurs throughout the matrix 3-There is the rapid loss of the monomer species 4-The molecular weight slowly increases throughout the reaction 5-The same mechanism operate throughout the reaction 6-The polymerization rate decreases as the number of functional group decreases 7-No initiator is required to start the reaction And so on….. 1st step 2nd step Chain growth polymerization Chain growth polymerization occurs by the addition of monomer after monomer to the end of growing chains Features 1- Monomers remain after long reaction times 2-The molecular weight of the polymer are increase rapidly 3-The polymerization rate initially increases and then become constant 4-An initiator is required to start the reaction 5- Most often occurs in radical initiated reactions Chain polymerization reaction consists of three stages 1- Initiation 2- Propagation 3-Termination Chain growth polymerization Radical initiated polymerization Free radical Initiation The formation of a free radical enables the reaction with a subsequent double Propagation bond, leading to chain growth and the creation of another free radical to continue the reaction Termination I Termination occurs when two free radicals combine, eliminating the creation of further free radicals on the chain Condensation Reactions O Reversible O Reaction! CH3–C–OH + CH3–CH2–OH CH3–C–O–CH2–CH3 + H2O Acetic Acid Ethanol Ethyl Acetate Additional Product Ester linkage Step Growth Polymerization occurs by the combination of larger and larger fragments of the growing polymer (contrary to chain growth where monomers are always added to the end of polymer chains). Is water always the byproduct of condensation reactions? Some of the possible byproducts of condensation reaction are: water, hydrogen chloride, methanol, or acetic acid Condensation Polymerization Nucleophile Electrophile + H2O Polyamides or nylons: reaction of diamine and dicarboxylic acid The reactivity of condensation polymers can be described by: - Nucleophiles (N, O, or other elements with extra elections) - Electrophiles (almost always carbon double bonded to oxygen, making the carbon deficient of electrons and able to react with N, or O, of another molecule) Condensation Polymerization Nylon 6,6 is the most widely produced polyamide due to its favorable balance of strength and toughness To create high molecular weight nylons, a 1:1 stoichiometry of monomers is needed – this is achieved through creating salts that polymerized Other technique for creating Nylon Is a molecule of water always split out? O O H2N–(CH2)6–NH2 + Cl–C–(CH2)4–C–Cl Hexamethylene Diamine Adipoyl Chloride O O H2N–(CH2)6–N–C–(CH2)4–C–OH + HCl – H Amide Group Chlorinated compounds are used to make the molecule super-reactive (a “super” electrophile). Normally this reaction would occur around 200C to overcome the activation energy, but as a chloride, it can be done at room temperature. Condensation Polymerization: Polyesters Polyester: reaction of diol and dicarboxylic acid As with Nylons, water needs to be removed from the reaction in order to allow the reaction to proceed toward high molecular weight. - The reaction is reversable, so water present in the reaction can cause the chain to break apart. Condensation Polymerization Sometimes these reactions are not so straightforward – the production of PET involves multiple steps where esterification reactions continue to build high molecular weight polymers Completed under high vacuum to remove ethylene glycol Condensation Polymerization Polyurethanes are created through the reaction of an isocyanate (NCO) and diol / polyol. (No water is released!) These polymers are often synthesized with a foaming agent to create polyurethane foams Additional Reactions with Polyurethanes Water is often used as a foaming agent because it reacts with isocyanates to create carbon dioxide and a urea molecule, fortifying the polymer structure Additional Reactions with Polyurethanes Excess isocyanate can react with newly formed urethane or urea chains, or react with itself to form rigid segments The amount of isocyanate used can be adjusted to increase the hard segment composition of polyurethanes, creating more rigid materials. Condensation Polymerization: Polycarbonates and PF Resins Polycarbonates are typically synthesized from the toxic precursor phosgene and have a repeating carbonate functional group Phenol-formaldehyde resins (or Novolacs) were one of the first polymers produced. The multifunctional nature of phenol creates crosslinked networks. - However, phenol and formaldehyde are not green or friendly Looking closer….. Polycarbonate Reaction Polycarbonates and PF PF Resin Reaction Resins are another example of using electrophilic C=O groups. Condensation Polymerization: Epoxies Bisphenol-A (BPA) is the most common epoxy used commercially Epoxy group but has come under scrutiny as a reproductive toxin and probable carcinogen “BPA” Component Curing of epoxies can occur through amines, anhydrides and others, often creating crosslinked networks Sukanto et al. https://www.degruyter.com/document/doi/10.1515/eng-2021-0078/html Categorizing the toxicity of polymers by synthetic path – Ranking system Categorizing the toxicity of polymers by synthetic path – Ranking system Hazard Levels V and IV are “phase out” and “risk reduction” identified by Swedish Chemicals Agency Levels I-III are assembled from the Global Harmonized System (GHS) Each hazard grad differs by a power of 10 (1, 10, 100, 1000 etc.) Categorizing the toxicity of polymers by synthetic path – Results Summarizing Results, taking out duplicates Polymer Rank Polyurethane 1 PAN 2 PVC 5 Epoxies 8 ABS 10 PS 14 PF 16 UPE 18 PC 19 PMMA 22 PA 33 EPS (Styrofoam) 34 LDPE 36 PP 37 Average degree of polymerization The number-average degree of polymerization Xn is given as the total number of monomer molecules (No) initially present divided by the total number of molecules (N) present at time t, Xn = No / N = [ M ]o / [ M ] The concentration [M] at any time given by : [M]o - [M]o (P) = [M]o (1- P ) Which makes: Xn = 1 / 1 – P This relationship is the Carother's Equation. P = extent of the reaction = the fraction of conversion (fraction of A or B functional groups Example that has reacted at time t ) If monomer conversion is 99% what is the average degree of polymerization Xn ? Xn = 1 / (1 – P) = 1 / (1 - 0.99) = 100 Consider small increases in monomer conversion: If P =99.5 % Xn = 1 / 1 - 0.995 = 200 If P =99.6 % Xn = 1 / 1 - 0.996 = 250 Mn as a function of conversion of monomers Large molecular weights are only achieved when a high degree of monomer conversion is attained. Branched-chain polymer Branched polymers contain molecules having a linear backbone with branches emanating randomly from it For this, the monomer must have capability to grow in multiple directions i.e. a functionality >2 o r Network or gel polymer Network or gel polymers are crosslinked polymers that contain short side chains (cross links) that connect different polymer chains into a “network” Gel polymers are a type of crosslinked material that does not dissolve in a solvent, but swells by incorporating molecules of the solvent into its own matrix Branching and Network Formation Hyperbranched Polymers and Dendrimers More Network Formation Networks can also be made by taking linear polymer chains and linking them using covalent bonds. We call this crosslinking Crosslinking in packaging applications Covalent linking of edible films using Crosslinking using ionic interaction Crosslinking using radical formation biopolymer feedstocks (chitin, between cations (+) and oxygenated and covalent linking between cations cellulose, alginate etc..) compounds (-) in biopolymers in polyolefins (PE, PP) https://www.sciencedirect.com/science/article/pii/S240584401936685X https://www.sciencedirect.com/science/article/pii/S0268005X18302698 https://www.scielo.br/j/mr/a/FFTLTF9zPX7X8BVvxntjfMv/?lang=en Applications of crosslinked PE Crosslinking provides better energy absorption (i.e. shock, compression) and thermal resistance. Is used in thermal insulation (wires / cables) foams, and containers https://youtu.be/sHCOv00kDu0 https://4spepublications.onlinelibrary.wiley.com/doi/full/10.1002/pen.26049 Network Formation by Cross-Linking An example of cross linking is the reaction of natural rubber or poly(isoprene) with sulfur in the vulcanization process The double bonds present in isoprene are reactive toward sulfur providing the opportunity for crosslinking Ramos-Ballesteros et al. DOI- 10.1002/9783527819249.ch7 Measuring crosslinking density Dynamic Mechanical Analysis: can be used by Solvent measuring the modulus of the “rubbery plateau”, condenses and drips more on this later in the semester Gel Content: Pick a solvent that is known to dissolve Sample chamber the polymer resin before crosslinking, then measure the amount that dissolves after crosslinking The difference is the amount that crosslinks, and does not dissolve Solvent Soxhlet extraction evaporate s Use continual solvent extraction to measure crosslinked content, similar to gel content Solvent evaporates under heat, then drips onto sample When the chamber fills past the #6 point, a siphon exists that drains the sample chamber and the process starts again Networks - Summary We can make networks by; Linking together small multi-functional monomers Branching, star formation, network formation Crosslinking already formed chains Ionic interactions, covalent linking, Note; you can change properties dramatically by changing the crosslinking density Think of the difference between a rubber band and a rubber tire Radical Polymerization of Polypropylene Initiation Propagation Termination Termination occurs when the free radical from two chains react, forming a bond, and ending the free radical propagation process Short Chain Branching in Polyethylene CH2–CH2 ~~~CH2–CH CH2 CH H 2 Formation of short chain branches in polyethylene CH2–CH2 Reaction is often called “back- ~~~CH2–CH CH2 biting” since the free radical CH2H circles back to react at the middle of the chain CH2 CH2 C4H9 C4H9 ~~~CH2–CH–CH2–CH2 ~~~CH2–CH–CH2–CH2–CH2–CH2 CH2 CH2 Many commercial polymers are synthesized by free-radical Free-radical polymerization polymerization Polytetrafluoroethyene – PTFE (Teflon) Polystyrene – Styrofoam Polyvinyl chloride – PVC Why are polyolefins typically so cheap, energy efficient, and non-toxic? 1. Gas-phase reactions – reactions done in the gas phase have very little waste, higher conversion rates, and easy processing 2. Catalysts – new developments in catalysts increase the efficiency and productivity of manufacturing 3. Simple chemicals design: small amount of oxygenated groups, simple reactivity, few side reactions Polyolefin Catalysts in the last century 1990’s Metallocenes s g res 1960’s P ro Metal oxide i cal olog Z/N Catalysts n ech T A modern Exxon plant 1940’s ICI-LDPE 1920’s Every 25 years or so, there appears to be a “quantum jump” Staudinger in polyolefin technology. Metallocene catalysts are considered by many to be one such revolution in polymer science. They have been referred to as“designer” catalysts, because of their ability to (co)polymerize an incredible variety of polyolefins with different microstructures, molecular weights and reproducible distributions of molecular weight and branching. Ziegler-Natta Catalysts CH2 CH2 CHR CHR Cl Cl Cl Cl CH2 + Ti CHR Ti Cl Cl CH2 Vacant Orbital Cl Cl CHR Insertion by the monometallic mechanism Polyolefin Energy Demand / GHG’s Top graphs represent values per kg of polymer Bottom graphs represent cumulative values per year Energy demand comes primarily from chemical feedstocks GHG emissions come mainly from electrical requirements Lower two graphs show actual production uses and associated energy and emissions GP: General Purpose IM: Injection Molded Nicholson et al. https://www.cell.com/joule/pdf/S2542-4351(20)30626-7.pdf Polyester Energy and GHG Demand Top graphs represent values per kg of polymer Bottom graphs represent cumulative va