Open Vs Closed Circuit Hydraulic Transmission PDF
Document Details
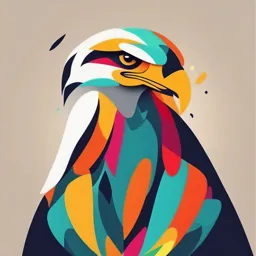
Uploaded by AdjustableSymbolism
2022
Tags
Related
- Leccion 2 Transmision y Actuacion_RIA_handout PDF
- Torque Measurement Notes PDF
- Trabajo Final del Curso: GuÃa de Reusabilidad de Componentes Mecánica Automotriz PDF
- Daegan Sample Test PDF
- City & Guilds Level 2 Technical Certificate in Land-based Engineering Sample External Test PDF
- Hydraulic Systems PDF
Summary
This document provides an overview of open and closed circuit hydraulic transmission systems. It details the differences in functionality and the efficiency advantages of closed-loop systems. Diagrams of various conditions of transmission are included.
Full Transcript
Open Vs. Closed Circuit Warranty Service Partner…………………….. Level 200 © 2022 Danfoss. All rights reserved.. Open Vs. Closed Circuit Open Circuit Closed Circuit Open Circuit – This is a si...
Open Vs. Closed Circuit Warranty Service Partner…………………….. Level 200 © 2022 Danfoss. All rights reserved.. Open Vs. Closed Circuit Open Circuit Closed Circuit Open Circuit – This is a simplified version of Closed circuit - is commonly called a open circuit transmission circuit. Fluid goes from the pump to Fluid goes for the pump to the actuator and the motor and from the motor back to tank in a from the actuator to the reservoir. It is the closed loop fashion. Closed circuits are most most common type circuit used today for commonly used in propel applications auxiliary functions. 2 © 2022 Danfoss. All rights reserved.. How does closed circuit pump controls help conserve power/energy? Closed circuit applications are inherently efficient. Pump displacement is changed instead of diverting flow Pressure rises or falls to meet load demand The ability to control the displacement eliminates the waste experienced in open circuit systems. Therefore, the type of control has little effect on the efficiency of the basic circuit. 3 © 2022 Danfoss. All rights reserved.. Closed Circuit & Open Loop Control Open loop means no electronic feedback. The things that reduce circuit efficiencies would be charge pressure on the return side, case pressure and line inefficiencies. 4 © 2022 Danfoss. All rights reserved.. Closed Circuit, Closed Loop The electronic loop is closed so you have feedback for speed control. Closed loop provides more accurate speed control and the controller can change the displacement of the pump. 5 © 2022 Danfoss. All rights reserved.. Transmission Circuit This is what goes into a typical closed-circuit system. All the valves, the pump, motor, filter, reservoir and cooler are included in a closed- 6 circuit system. © 2022 Danfoss. All rights reserved.. Transmission Circuit - Neutral The closed circuit (loop) hydrostatic transmission is considered to be in neutral when there is no output flow being generated by the variable displacement pump as its shaft, internal components, and charge pump are being driven. Therefore, with no flow available to the motor, the pump is at rest with no transmission output. Because of the variable displacement pump is being driven continuously, several functions must be maintained. 7 © 2022 Danfoss. All rights reserved.. Transmission Circuit - Transient As you energize the solenoid the control spool will move allowing charge pump flow to pass through the controller and in the servo piston allowing the swash plate to move thus stroking the rotating group. 8 © 2022 Danfoss. All rights reserved.. Transmission Circuit - Forward As the control lever is slowly moved forward the vehicle starts a forward movement. As the camplate begins to move, the piston assemblies start to reciprocate in the piston block. As the control lever continues a forward movement, the cam angle increases, the pistons reciprocate further, more oil is being pumped, and the speed of the vehicle is increased 9 © 2022 Danfoss. All rights reserved.. Transmission Circuit - Transient Transitioning back to neutral 10 © 2022 Danfoss. All rights reserved.. Transmission Circuit - Back to Neutral 11 © 2022 Danfoss. All rights reserved.. Transmission Circuit - Transient As you energize the opposite solenoid the control spool will allow charge flow to move the rotating group in the reverse direction. 12 © 2022 Danfoss. All rights reserved.. Transmission Circuit - Reverse When the control lever is slowly moved to the reverse position, the vehicle starts a reverse movement (Figure 4). As the camplate begins to move, the piston assemblies start to reciprocate in the piston block. As the control lever continues a reverse movement, the cam angle increases, the pistons reciprocate further, more oil is being pumped, and the speed of the vehicle is increased. 13 © 2022 Danfoss. All rights reserved.. Transmission Circuit - Transient 14 © 2022 Danfoss. All rights reserved.. Transmission Circuit - Neutral 15 © 2022 Danfoss. All rights reserved.. Transmission Circuit - Electronic Displacement Control Swash plate sensors, speed sensors and a proportional control can be added to a closed-circuit system for electronic displacement control. 16 © 2022 Danfoss. All rights reserved.. Transmission Circuit - Electronic Displacement Control The solenoids are energized to change displacement. 17 © 2022 Danfoss. All rights reserved.. Transmission Circuit - Stall Condition This figure shows the camplate in the full forward position with the relief valve cross relieving. The function of the system relief valve is to relieve the pressure side of the system of excessive high pressure when the vehicle encounters a heavy load or stalls out. When the maximum pressure exists and surrounds the closed loop system relief valve, it starts to open internally. Due to high pressure, the large spring in the relief valve compresses and opens an orifice allowing oil to bypass and take a pressure drop. The opposite relief valve serving as a check valve opens and allows the oil to flow to the intake side of the pump 18 © 2022 Danfoss. All rights reserved.. Transmission Circuit - Stall Condition Cross port relief valves are there to clip spikes so if the system hits the relief valve setting for extended periods of time the system can overheat and potentially cause catastrophic failure 19 © 2022 Danfoss. All rights reserved.. Transmission Circuit - Stall Condition 20 © 2022 Danfoss. All rights reserved.. Transmission Circuit - Stall Condition The main closed loop will also require protection from possible excessive system pressures. This is accomplished by the addition of two pilot operated high pressure relief valves. Two valves are required, as they are used on a bi-directional system. Again, application dictates preset relief valve settings. In most cases, but not all, both relief valve settings will have the same valve setting. 21 © 2022 Danfoss. All rights reserved.. Transmission Circuit - Pressure Over-Ride Valves IPOR (Internal pressure override control) is an option that is sometimes used to prevent the continuous operation of the system high pressure relief valves. The IPOR valve setting is normally 500 psi lower than the system high pressure relief valves. 22 © 2022 Danfoss. All rights reserved.. Transmission Circuit - Pressure Over-Ride Valves The IPOR valve is spring biased to the closed position. System pressure is monitored in both directions so when system pressure exceeds the spring setting of the POR it opens up allowing pressure to move the servo piston toward the neutral postilion. Once the pressure is reduced to a value lower than the POR spring setting the servo piston will bring the swash plate back to its original position allow the transmission to stroke. 23 © 2022 Danfoss. All rights reserved.. Transmission Circuit - Pressure Over-Ride Valves 24 © 2022 Danfoss. All rights reserved.. Transmission Circuit - Pressure Over-Ride Valves 25 © 2022 Danfoss. All rights reserved.. Product Overview Service Information: These products are preset at the factory for optimum performance. Disassembling critical items would destroy these settings. It is therefore essential that any valve requiring mechanical or electronic repair be returned to the nearest Eaton repair center. The products will be refurbished as necessary and retested to specification before return. Field repair is restricted to the replacement of the external seals only. 26 © 2022 Danfoss. All rights reserved..