UNIT V Corrosion Sciences PDF
Document Details
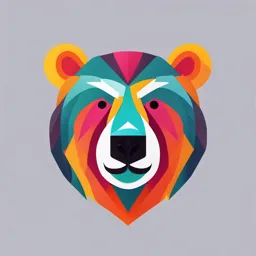
Uploaded by MotivatedAcer3145
Tulsiramji Gaikwad Patil College of Engineering and Technology
Tags
Summary
This document is a unit on Corrosion Sciences from a college. It covers the introduction, effects, consequences, and various mechanisms behind corrosion. It discusses the theories and provides examples.
Full Transcript
Tulsiramji Gaikwad-Patil College of Engineering and Technology Wardha Road, Nagpur-441 108 + NAAC A Accredited & An Autonomous Institute Approved by AICTE ,New Delhi, Govt.of M...
Tulsiramji Gaikwad-Patil College of Engineering and Technology Wardha Road, Nagpur-441 108 + NAAC A Accredited & An Autonomous Institute Approved by AICTE ,New Delhi, Govt.of Maharashtra & Affiliated to RTM Nagpur Department of Science & Humanities UNIT V CORROSION SCIENCES Introduction Almost all metals used in engineering exist in nature in combined forms such as oxides, carbonates, sulfides, chlorides, or silicates, known as minerals or ores. The process of extracting metals from their ores or minerals is referred to as extractive metallurgy. During the extraction of metals from these minerals, a considerable amount of energy is required. This energy consumption indicates that the metal has a higher energy state than the mineral or compound form. Energy + Metallic Compounds Pure Metal Fig 5.1: Corrosion and Extraction Process Just like water flows to the lowest level, all natural processes tend toward the lowest possible energy states. Thus, metals in their higher energy state (unstable) tend to revert back to their stable natural combined state of lower energy in the environment. The greater the amount of energy required for the extraction of metal, the greater the extent of corrosion. Corrosion is defined as the undesired destruction of materials through chemical or electrochemical reactions with their surroundings, originating from the surface. It is a natural process and can be considered as the reverse process of metallurgy. Metals have a tendency to revert from their higher energy state (unstable) to a stable lower energy state. According to the basics of thermodynamics, corrosion cannot be completely prevented but only slowed down. For example, iron and steel have a natural tendency to combine with other chemical compounds to return to their lowest energy states. To achieve this, iron and steel frequently combine with oxygen and water, both of which are present in most natural environments, forming hydrated iron oxides (rust). This is similar in chemical composition to the original iron ore. Illustrates the corrosion life cycle of a steel product. This illustration shows the energy transition from metallic compounds to pure metal and back to metallic compounds through the processes of extraction and corrosion. The Effects of Corrosion The effects of corrosion in our daily lives are both direct and indirect. At home, corrosion is readily recognized on automobile body panels, charcoal grills, outdoor furniture, and metal tools. Preventative maintenance, such as painting, protects such items from corrosion. For example, a principle reason to replace automobile radiator coolant every 12 to 18 months is to replenish the corrosion inhibitor that controls corrosion of the cooling system. Tulsiramji Gaikwad-Patil College of Engineering and Technology Wardha Road, Nagpur-441 108 + NAAC A Accredited & An Autonomous Institute Approved by AICTE ,New Delhi, Govt.of Maharashtra & Affiliated to RTM Nagpur Department of Science & Humanities Corrosion protection is built into all major household appliances such as water heaters, furnaces, ranges, washers, and dryers. Of far more serious consequence is how corrosion affects our lives during travel from home to work or school. The corrosion of reinforcing bars (rebar) in concrete can proceed out of sight and suddenly (or seemingly) result in failure of a section of highway, the collapse of electrical towers, buildings, parking structures, bridges, etc., leading to significant repair costs and endangering public safety. For instance, the sudden collapse due to corrosion fatigue of the Silver Bridge over the Ohio River at Point Pleasant, OH in 1967 resulted in the loss of 46 lives and millions of dollars. Fig 5.2: The corrosion cycle of steel Perhaps most dangerous of all is corrosion that occurs in major industrial plants, such as electrical power plants or chemical processing plants. Plant shutdowns can and do occur as a result of corrosion. This is just one of its many direct and indirect consequences. (Fig 5.2) Consequences of Corrosion Some important consequences of corrosion are summarized below: 1. Plant shutdowns: Shutdown of nuclear plants, process plants, power plants, and refineries may cause severe problems for industry and consumers. 2. Loss of products: Leaking containers, storage tanks, water and oil transportation lines, and fuel tanks cause significant loss of product and may generate severe accidents and hazards. It is well known that at least 25% of water is lost by leakage. 3. Loss of efficiency: Insulation of heat exchanger tubing and pipelines by corrosion products reduces heat transfer and piping capacity. 4. Contamination: Corrosion products may contaminate chemicals, pharmaceuticals, dyes, packaged goods, etc., with dire consequences for consumers. 5. Nuclear hazards: The Chernobyl disaster is a continuing example of the transport of radioactive corrosion products in water, causing deaths to human, animal, and biological life. Tulsiramji Gaikwad-Patil College of Engineering and Technology Wardha Road, Nagpur-441 108 + NAAC A Accredited & An Autonomous Institute Approved by AICTE ,New Delhi, Govt.of Maharashtra & Affiliated to RTM Nagpur Department of Science & Humanities The magnitude of corrosion depends upon the sensitivity of a particular metal or alloy to a specific environment. For instance, copper corrodes rapidly in the presence of ammonia, which is a serious problem in agricultural areas. Many historical statues made from bronze have been destroyed by ammonia released from fertilizers. Environmental conditioning offers one method of controlling corrosion, such as the use of inhibitors and oil transmission pipelines. Breakdown of Spending on Corrosion The petroleum, chemical, petrochemical, construction, manufacturing, pulp and paper, and transportation (railroad, automotive, and aerospace) industries are the largest contributors to corrosion expenditure. The cost of corrosion differs from country to country. For instance, in the USA, the transportation sector is the largest sector contributing to corrosion after public utilities, whereas in the oil-producing countries, such as the Arabian Gulf countries, petroleum and petrochemical industries are the largest contributors to expenditure. In the oil sector, drilling poses severe hazards to equipment in the form of hydrogen-induced cracking and hydrogen sulfide cracking. The direct cost of corrosion to the aircraft industry exceeds 2.2 billion US dollars. Corrosion has a serious impact on defense equipment. In the Gulf War, a serious problem of rotor blade damage in helicopters was caused by the desert sand. The thickness of the blade was damaged to a concerning extent in some instances. Desert erosion-corrosion offered a new challenge to corrosion scientists and engineers. The storage of defense equipment is a serious matter. Humidity is the biggest killer of defense hardware. Storage of defense equipment demands minimal humidity, scanty rainfall, alkaline soil, no dust storms, no marine environment, and minimal dust particles. Factors Influencing Corrosion The rate and extent of corrosion depend on the nature of the metal and the corroding environment. Nature of Metal a) Electrode potential or position in the galvanic series: Metals with higher electrode potentials do not corrode easily and are known as noble metals, such as gold, platinum, and silver. In contrast, metals with lower electrode potentials readily undergo corrosion, like zinc, magnesium, and aluminum. When two metals are in contact with each other, a higher difference in electrode potentials results in greater corrosion. For example, the potential difference between iron and copper is 0.78V, which is more than the potential difference between iron and tin (0.3V). Therefore, iron corrodes faster when in contact with copper than with tin. To avoid galvanic corrosion, the use of dissimilar metals should be avoided wherever possible. For instance, bolts and nuts or screws and washers should be made of the same metal or alloy. The Galvanic Series provides information on predicting the corrosion behavior of metals and alloys in specific environmental conditions. It arranges the oxidation potential of metals in decreasing order of activity. Tulsiramji Gaikwad-Patil College of Engineering and Technology Wardha Road, Nagpur-441 108 + NAAC A Accredited & An Autonomous Institute Approved by AICTE ,New Delhi, Govt.of Maharashtra & Affiliated to RTM Nagpur Department of Science & Humanities b) Purity of metal: Impurities such as Pb, Fe, or C in Zn metal increase the corrosion of zinc due to the formation of local electrochemical cells where Zn acts as the anode and impurities act as the cathode. Thus, the rate and extent of corrosion increase with increasing concentration of impurities in the metal. c) Physical state of metal: The physical state of metals, such as grain size, crystal orientation, and stresses, affects the rate of corrosion. Smaller grain size leads to greater solubility and increased corrosion. In pure metals under stress, atoms at boundaries have different electrode potentials than those in bulk, making the boundaries anodic and prone to corrosion. d) Ratio of cathodic to anodic region: The rate of corrosion is influenced by the relative size of cathodic to anodic areas. A small anode and large cathodic region lead to a high corrosion rate. When the cathodic region is larger, electrons are rapidly consumed at the cathode, enhancing the anodic reaction and increasing the overall rate of corrosion. For example, tin plating on iron with exposed small anodic surfaces leads to intense localized corrosion. e) Nature of the corrosion product: Corrosion products like metal oxides may act as protective films if they are insoluble and non-porous, preventing further corrosion. Metals like aluminum, chromium, and titanium form protective films, making them passive and resistant to further corrosion. In contrast, metals like iron, zinc, and magnesium form non-protective films and are highly susceptible to continuous corrosion. f) Solubility of corrosion product: In electrochemical corrosion, corrosion proceeds faster when the solubility of the corrosion product is high. Insoluble corrosion products act as barriers, decreasing the corrosion rate. g) Hydrogen overvoltage: Metals with lower hydrogen overvoltage on their surface are more susceptible to corrosion when the cathodic reaction involves hydrogen evolution. Lower hydrogen overvoltage facilitates hydrogen gas liberation, accelerating the cathodic reaction and, in turn, the anodic reaction, increasing the rate of corrosion. Nature of the Corroding Environment a) Temperature: As the temperature of the environment increases, the reaction rate also increases, accelerating corrosion due to the increased conductance of the medium and diffusion rate. In some cases, a rise in temperature decreases passivity, leading to an increased corrosion rate, such as in caustic embrittlement in high-pressure boilers. b) pH of the medium: Acidic solutions are generally more corrosive than neutral or alkaline solutions. Exceptions include amphoteric metals like aluminum, zinc, and lead, which form complex ions in alkaline solutions, making them resistant to corrosion. For other metals, the corrosion rate increases with acidity. c) Effect of oxidants: Oxidizing agents can increase or decrease corrosion rates. Dissolved oxygen in water systems like boilers and heat exchangers supports cathodic reactions, promoting corrosion. Metals like aluminum and magnesium form thin oxide films in oxidizing Tulsiramji Gaikwad-Patil College of Engineering and Technology Wardha Road, Nagpur-441 108 + NAAC A Accredited & An Autonomous Institute Approved by AICTE ,New Delhi, Govt.of Maharashtra & Affiliated to RTM Nagpur Department of Science & Humanities environments, rendering them passive. Conversely, Monel metal corrodes rapidly in the presence of air, while stainless steel corrodes in the absence of air. d) Humidity of air: Critical humidity is the relative humidity above which the atmospheric corrosion rate of a metal increases sharply. In humid atmospheres, gases like CO₂ and O₂, along with vapors, furnish water to the electrolyte, establishing electrochemical corrosion cells. Rainwater can wash away protective oxide films, enhancing atmospheric attack. e) Presence of impurities in the atmosphere: Industrial atmospheres contain corrosive gases like O₂, H₂S, SO₂, and fumes like HCl and H₂SO₄. These gases and fumes increase the acidity and electrical conductivity of the liquid in contact with the metal surface, accelerating electrochemical corrosion. f) Presence of suspended particles in the atmosphere: Suspended particles can be chemically active or inactive. Chemically active particles like NaCl and (NH₄)₂SO₄ absorb moisture and act as strong electrolytes, enhancing corrosion. Chemically inactive particles like charcoal adsorb sulfur gases and moisture, slowly increasing corrosion rates. g) Nature of ions present in the medium: Anions like silicates form insoluble reaction products, decreasing corrosion by depositing on metal surfaces. Anions like chloride ions destroy protective surface films, exposing metal surfaces to fresh corrosion. Cations like NH₄⁺ ions increase the corrosion of many metals, including iron. Traces of metals like Cu in mine water accelerate the corrosion of iron pipes. Theories of Corrosion Theories explaining the mechanisms of corrosion are essential to understand how and why metals degrade in various environments. Two primary theories are the chemical and electrochemical theories of corrosion, which describe the processes occurring based on the surrounding environment. Chemical Theory of Corrosion (Dry or Direct Chemical Attack or Atmospheric Corrosion) This theory posits that corrosion occurs due to the direct reaction of atmospheric gases, such as oxygen, halogens (Cl₂, Br₂, I₂), SO₂, and H₂S, with the metal. In this process, a solid film of the corrosion product typically forms on the metal's surface, which can protect the metal from further corrosion. The extent of corrosion depends on the metal's chemical affinity towards the reactive gas, with oxygen being the most common corrosive agent. Types of Chemical Corrosion 1. Oxidation Corrosion (Reaction with Oxygen) o Mechanism: Some metals directly react with oxygen in the absence of moisture. For example, alkali and alkaline earth metals form oxides at room Tulsiramji Gaikwad-Patil College of Engineering and Technology Wardha Road, Nagpur-441 108 + NAAC A Accredited & An Autonomous Institute Approved by AICTE ,New Delhi, Govt.of Maharashtra & Affiliated to RTM Nagpur Department of Science & Humanities temperature, while other metals may require higher temperatures. Noble metals like gold and platinum are resistant to oxidation. o Reaction: 2M → 2Mn+ + 2ne− (De-electronation or oxidation) nO2 + 2ne− → 2nO2− (Electronation or reduction) Net reaction: 2M + nO2 → 2Mn+ + 2nO2− → 2MnO (Metal oxide) o Oxide Film: The metal oxide layer that forms can be protective or non- protective depending on its properties. The Pilling-Bedworth Rule helps determine the nature of the oxide layer: ▪ Stable Oxide Film: Oxides of Pb, Al, and Sn form stable, tightly adhering films that inhibit further corrosion. The Pilling-Bedworth Ratio (P.B. Ratio) for protective films is: P.B. Ratio ≥ 1 ▪ Unstable Oxide Film: When the oxide film is unstable, it decomposes back into the metal, making oxidation corrosion impossible. Noble metals like Au, Ag, and Pt form unstable oxides. ▪ Non-Protective Oxide Film: If the oxide volume is insufficient to cover the metal surface completely (P.B. Ratio ≤ 1), the oxide film will be porous, allowing continued corrosion. Pilling-Bedworth Rule The Pilling-Bedworth Rule is a guideline used to predict the protectiveness of an oxide layer formed on the surface of a metal during oxidation. It relates the volume of the oxide formed to the volume of the metal consumed in the oxidation process. According to the Pilling-Bedworth Rule: P.B. Ratio (Pilling-Bedworth Ratio): It is the ratio of the volume of the oxide formed to the volume of the metal consumed. Volume of the oxide P.B. Ratio = Volume of the metal consumed Implications of the Pilling-Bedworth Ratio 1. Protective Oxide Layer (Non-Porous) o If the P.B. Ratio is greater than or equal to 1 (P.B. Ratio≥1), the oxide layer formed is non-porous and protective. Tulsiramji Gaikwad-Patil College of Engineering and Technology Wardha Road, Nagpur-441 108 + NAAC A Accredited & An Autonomous Institute Approved by AICTE ,New Delhi, Govt.of Maharashtra & Affiliated to RTM Nagpur Department of Science & Humanities o This means the oxide occupies at least as much volume as the metal it replaces, forming a continuous, adherent layer that covers the metal surface and prevents further oxidation. o Examples: Aluminum (Al), Iron (Fe), Nickel (Ni), Chromium (Cr). 2. Non-Protective Oxide Layer (Porous) o If the P.B. Ratio is less than 1 (P.B. Ratio